Страница:
Иногда для создания прочных поковок с низкой температурой каления берут магниевые и титановые сплавы. Но технологически изготовить из них поковку намного сложнее, чем из стали или бронзы, так как необходимо очень точно соблюдать температурный режим.
Техника ковки
Техника ковки
Теперь рассмотрим процесс ковки. Хотя существует и холодная ковка, основные операции кузнец проводит именно с горячим железом. Разогревают его в горне. Это не такое уж простое дело, как может показаться.
Способов и приемов ковки множество, но все их можно свести к нескольким основным операциям. Это осадка и высадка, протяжка или вытяжка, рубка, прошивка или пробивка отверстий, гибка, закручивание, отделка (выглаживание), нанесение рисунка, набивка фактуры и рельефа, кузнечная сварка.
Для начального нагрева холодного горна необходимо очистить очаг от золы и шлака, продуть фурму. Затем засыпать в очаг небольшой слой угля, следя за тем, чтобы отверстия фурмы оставались свободными, поверх него – древесную стружку или пропитанную керосином ветошь. Поджечь ветошь или стружку, засыпать сверху второй слой угля и начать слабо поддувать воздух в фурму. Когда уголь разгорится, добавить еще топлива и плавно увеличить подачу воздуха.
Уголь в горне спекается в корку, под которой и развивается необходимая высокая температура. Для разогрева заготовки зарывают ее целиком или нужную часть в горячие угли подальше от фурмы (чтобы между металлом и фурмой постоянно был слой раскаленного угля) и засыпают свежим углем. Корка образует спекшийся свод, который должен всегда быть целым. Время от времени подгребают от краев очага к центру свежий уголь и слегка обрызгивают его водой. Если угли под коркой выгорели и образовалась большая полость, разрушают свод и подгребают свежий уголь; вскоре образуется новая корка. Заготовку периодически поворачивают для равномерного нагрева.
Регулируют поддув так, чтобы пламя было нейтральным, невысоким, слегка коптящим. Избыток воздуха (высокое дутье) вызывает перегрев металла и оплавление кромок. Кроме того, образуется окалина, которая приводит к потерям (угару) металла, снижает качество и затрудняет дальнейшую обработку заготовки. Избыточный или неоправданно долгий разогрев заготовки приводит к пережогу металла, он становится хрупким, при ударе рассыпается на части.
Хорошая ковкость появляется после достижения температурного промежутка, который для каждого металла свой. Нагревать заготовки чаще всего приходится до ковочной температуры, которая для разных видов стали составляет от 1200 до 1250 °C.
Определение степени нагрева осуществляется с помощью специальных приборов – термопаров и пирометров. Но в условиях обычной кузницы проще и вернее определять ее на глаз. На разных степенях каления металлы окрашиваются в разные цвета, которые при остывании меняются в обратном порядке.
При дневном освещении в тени температуры нагрева соответствуют следующим цветам:
– 530–580 °C – темно-коричневый;
– 580–650 °C – красно-коричневый;
– 650–730 °C – темно-красный;
– 730–780 °C – вишневый;
– 780–830 °C – светло-вишневый;
– 830–900 °C – красный;
– 900–1050 °C – светло-красный;
– 1050–1150 °C – соломенно-желтый;
– 1150–1250 °C – лимонно-желтый;
– 1250–1400 °C – ослепительно белый.
Обычно ковку начинают при 1100° C и заканчивают при 700 °C. Следует помнить о том, что при длительном нагреве углерод стали выгорает прежде всего с поверхности. Если надо закалить изделие после ковки, долго греть заготовку нельзя. Лучше увеличить температуру в очаге горна.
Нижняя граница ковки должна превышать отметку 723 °C, выше которой кристаллическая решетка металла меняет свою структуру на гранецентрированную кубическую. В этом состоянии сталь имеет наибольшую пластичность.
Определение верхней границы ковки зависит от температуры плавления: она должна быть на 100–150 °C ниже последней. При превышении этого предела начинается резкое увеличение размеров зерен металла, что приводит к уменьшению пластических свойств. Такой дефект называется перегревом. Его можно устранить, проведя дополнительную ковку, после которой зернистость уменьшается, и подвергнув металл повторной термической обработке.
Нагрев до более высоких температур в горне приводит к тому, что материал начинает плавиться, вследствие чего большое количество углерода и других газов проникает в его нижние слои. Там происходит активное окисление, которое в кузнечном деле называется пережогом. Связь между зернами нарушается, и металл навсегда теряет пластичность.
Нагревание сплавов следует производить в строго ограниченном температурном промежутке, который определяется свойствами материала. Он обозначается буквами Тн и Тк – температура начала и конца ковки.
При приближении к Тк у металла устанавливается мелкозернистая структура, которая обеспечивает высокую пластичность, поэтому при нагревании его стремятся доводить до этой температуры. Такой режим позволяет дольше ковать изделие. Но, с другой стороны, при долгом повышении температуры с поверхности начинает выгорать углерод. Деталь после этого будет очень трудно закалить. Поэтому режим следует выбирать заранее, с учетом поставленной задачи.
Интервал, в котором можно проводить ковку, у разных марок стали различный. Самый широкий (до 500 °C) имеют малоуглеродистые сорта стали, что позволяет обрабатывать их в течение длительного промежутка времени без дополнительного нагрева. Чем выше содержание углерода, тем этот промежуток меньше.
Другие металлы, например алюминий, имеют более низкий температурный интервал обработки. Для сплава ВД17 он составляет 400–470 °C.
Во время ковки металл постепенно остывает и с трудом поддается деформации. Поэтому останавливать процесс надо уже при достижении температуры, которая на 20–30 °C выше Тк.
Табл. 5 содержит информацию о температурных интервалах некоторых марок стали.
Определение времени нагрева зависит от многих факторов. Не рекомендуется брать заготовки слишком большого диаметра, так как на полное прогревание требуется слишком много времени, за которое образуется большой слой окалины. В то же время, если слишком поспешить, то внутренние слои не приобретут достаточной пластичности и могут потрескаться.
Скорость нагрева зависит также от сечения заготовки. Быстрее нагреваются круглые детали, медленнее – квадратные. У изделий большего сечения разница почти отсутствует. Нагрев в горне, заправленном древесным углем, круглой заготовки диаметром 10–20 мм происходит за 2–4 минуты, а квадратной – за 3–5 минут.
Если размеры больше 30 мм, то время увеличивается до 8–15 минут, а у заготовок диаметром до 50 мм нагрев занимает до 25 минут.
Поскольку каменный уголь дает меньшее количество тепла, то нагревать на нем деталь придется немного дольше. Для того, чтобы получить гарантированно ровный прогрев, поковки рекомендуется выдерживать в огне в течение срока, больше требуемого на 25 %.
Как известно, содержащая меньшее количество углерода сталь более пластична.
При отжиге сталь более высокой марки нагревается в горне при температуре 650–720 °C, что соответствует темно-красному цвету каления, в течение 2–3 часов.
Регулировать режим ковки можно интенсивностью поддува. Периодически уровень накала надо проверять, охлаждение и перегрев одинаково нежелательны.
По прошествии нужного времени горн выключают и заготовке дают постепенно остыть. Чем медленнее будет происходить этот процесс, тем пластичнее станет металл. Если отжиг проводится на древесном угле, то можно закопать заготовку в золу и оставить в таком виде на несколько часов.
С повышением температуры окисление становится более интенсивным, особенно после 900 °C. Образование окалины гораздо сильнее при избытке воздуха, наличие которого определяется по коротким прозрачным языкам пламени. Ее верхний слой, называемый шубой, частично предохраняет металл от дальнейшего окисления.
Параллельно происходит выделение углерода из верхних слоев материала, вследствие чего металл становится менее прочным и хуже закаливается.
У заготовок большого размера часть газа из внутренних слоев переходит во внешние, и металл немного восстанавливает свою пластичность.
В условиях кузницы полностью защитить поковку от образования окалины невозможно. Для уменьшения этого процесса применяют скоростной нагрев, однако делать это можно не во всех случаях.
Следует также отметить, что образование окалины происходит не только во время нагревания, но и в течение ковки. Поэтому при переносе надо следить за тем, чтобы слой «шубы» не осыпался.
Обрабатывая металл на наковальне, окалину удаляют только с тех частей, которые подвергаются деформации. У заготовок из малоуглеродистых сталей нагар легко удаляется ударами ручника.
Перед тем как положить заготовку в горн, на нее наносят специальные обмазки. Они не только защищают металл, но и являются хорошим смазывающим материалом, снижающим время нагрева и увеличивающим пластичность металла.
Простой способ защиты от окалины мелких изделий из инструментальной стали, например чеканов, напильников и т. п., – нагревать их внутри герметично закрытой трубы.
Если прокаливается только часть заготовки, необходимо следить за тем, чтобы весь подлежащий обработке участок был одного цвета. В противном случае поковка требуемой формы не получится.
Важно следить за режимом поддува: он должен быть равномерным и давать необходимую для того или иного процесса температуру.
Часто при неправильном нагреве на поверхности металла возникают трещины. Работы с поделочной сталью, как правило, обходятся без них, поскольку данные сорта обладают широким температурным интервалом ковки.
Глубокие поперечные трещины появляются вследствие слишком быстрого нагрева заготовки, когда внутренние слои остаются еще холодными. Наиболее часто трещины образуются на поверхности, они возникают из-за того, что металл остыл до температуры, которая ниже Тк. Если при ударах молотом заготовка раскалывается на несколько частей, то это свидетельствует о пережоге стали.
Начинающему мастеру следует особенно тщательно следить за соблюдением температурного режима ковки и нагрева. Рекомендуется до начала серьезной работы потренироваться на черновых заготовках, то есть не имеющих еще правильной формы.
Для того чтобы поковка не раздавалась в ширину и вытягивалась в нужном направлении, применяют желобчатые (седлообразные) наковальни и шпераки, а также ручьи кузнечной плиты-формы. Если нужна круглая заготовка или заготовка с гранями, применяют обжимки (рис. 144).
Рис. 144. Использование обжимки при вытяжке.
Они не только вытянут заготовку в длину, но и выгладят ее, придав нужное сечение. Поворачивая заготовку вокруг продольной оси (для получении граней – на определенный угол), надо ударять кувалдой по обжимке и постепенно передвигать заготовку вперед. Если необходимо получить всю поковку или отдельный участок в виде пластины (например, при ковке лепестков, листьев в растительном орнаменте), заготовку или ее часть расплющивают (разгоняют). При этом площадь увеличивается за счет уменьшения толщины.
Расплющивать можно кувалдой или ручником на наковальне. Если необходимо раздать металл быстрее, надо воспользоваться раскаткой с полукруглыми рабочими поверхностями. Сила удара в таком случае будет сосредоточена на небольшом участке, и металл раздастся равномерно во все стороны.
Для выполнения нескольких последовательных операций существует правило: независимо от задуманного результата в процессе протяжки заготовка сначала куется квадратного сечения, затем она уменьшается до нужных размеров и только потом ей придается нужная форма.
На рис. 145 показана очередность переходов при ковке различных сечений.
Рис. 145. Последовательность переходов при ковке различных сечений: а – квадратное сечение из круглого; б – квадратное из квадратного; в – круглое из круглого; г – круглое из квадратного.
Она выполняется с помощью раскатки, которая разгоняет металл в разные стороны. Последовательным перемещением инструмента создают широкую ребристую поверхность нужных размеров, потом выравнивают ее гладилками до требуемой толщины (рис. 146).
Рис. 146. Разгонка плоской пластины.
Рис. 147. Примеры вытяжки с оправкой: а – протяжка на оправке; б – раскатка.
В процессе вытяжки поковку надо постоянно поворачивать вокруг оси (при работе с квадратной оправкой – на 90°).
Для увеличения наружного и внутреннего диаметров колец, обручей и т. п. металл раздают на оправке. Для этого надо осадить и прошить заготовку или взять готовое изделие и надеть его на цилиндрическую оправку. Оба выступающих конца оправки уложить на подставку, ударами молота раздать металл, постепенно поворачивая заготовку. Диаметр изделия увеличивается за счет утончения стенок. Готовые кольца можно раздать на конической оправке, поставленной в вертикальное положение.
Раскатка увеличивает диаметр кольцевой заготовки протяжкой стенок полосы. Ее применяют для изготовления бесшовных колец высокой прочности (рис 147, б).
Проводят эту операцию на роге кувалдой или используют верхники вогнутой формы. Если кольцо сделано из полосы с продольным распределением волокон, то поперечная деформация незначительна, а расширение идет целиком по периметру. На заключительном этапе делают выглаживание.
Рис. 148. Формообразующие операции осадки: а – осадка цилиндрической заготовки; б – высадка верхней части заготовки; в – высадка нижней части заготовки; г – высадка средней части заготовки.
Осадка (рис. 148, а) нужна для уменьшения длины заготовки за счет увеличения толщины (поперечного сечения). Если осадка производится только на отдельных участках заготовки (на концах или в середине), то такая операция называется высадкой (рис. 148, б, в, г).
Осадку применяют для утолщения изделия по всей длине, высадку – для получения отдельных утолщений, при ковке декоративных элементов (узлов, ягод и т. п.), шляпок гвоздей и т. д.
Высадка в середине стержня или полосы проводится также перед изгибанием под углом 90°. Это необходимо для восполнения недостающего металла, иначе в месте перегиба толщина поковки сильно уменьшается.
Когда требуется высадить середину длинной заготовки, ни один из вышеперечисленных способов не подходит. Пруток надо изогнуть в форме буквы Z выше места деформации и наносить удары по изгибу. После выполнения операции заготовку выпрямляют.
Осадка применяется как предварительная операция перед прошивкой при изготовлении колец, трубок и других пустотелых изделий.
Для осадки или высадки нагревают поковку или высаживаемый участок в горне. Если длина заготовки или нагретого участка превосходит диаметр (толщину) не более чем в 2–2,5 раза, а сама поковка относительно короткая, то ставят поковку вертикально на наковальню и бьют ручником или кувалдой по верхнему концу.
Длинные изделия или участки при таком способе осадки могут изогнуться, поэтому их надо положить на наковальню, зажать клещами и осаживать молотом или ручником.
Существует также способ осадки поковки за счет ее собственного веса: для этого зажимают нагретую поковку в клещах и бьют торцом о наковальню. Но необходимо помнить, что обычно такая осадка применяется для небольших изделий.
Чтобы утолщение распространялось только в нужную сторону, заготовку после высадки куют соответствующим образом. Если высадка оказалась недостаточной, процесс повторяют. Для придания желаемой формы утолщению пользуются обжимками, подбойками и т. п.
Фигурную высадку выполняют с помощью гвоздильни. Пруток в этом случае помещают в отверстие наковальни, необходимый по длине конец оставляют снаружи и деформируют ударами кувалды.
Можно высаживать заготовку в тисках. При этом надо помнить, что нагретая часть в тисках охлаждается быстрее. Этот способ используется тогда, когда необходимо получить четкий переход от осаженной части к стержню.
Рис. 149. Разделительные операции: а – обрубка с помошью зубила; б – обрубка с помошью зубила и подвески; в – продольная разрубка; г – разрубка отщепов в тисках; д – вырубка или просечка.
Для рубки заготовку нагревают до темно-красного цвета, кладут на наковальню, наставляют кузнечное зубило и сильно бьют по нему молотом (рис. 149, а). Перерубив заготовку на 3/4, переворачивают ее и отрубают окончательно. Толстые поковки перерубаются с помощью зубила и подсечки (рис. 149, б), полосы – с помощью подсечки без зубила. Подсечку вставляют в отверстие наковальни, сверху кладут полосу и наносят удар кувалдой. Нельзя прорубать металл насквозь, потому что можно повредить острые части инструмента. Для окончательного перерубания надо использовать незакаленную площадку у основания рога наковальни или подложить полосу мягкой стали (рис. 149, в). Чтобы лезвия зубила и подсечки не схватывались с горячим металлом и не выкрашивались, перед рубкой необходимо протереть их ветошью, смоченной машинным маслом.
Разновидностями рубки являются разрубка, обрубка (обсечка), вырубка. При разрубке (рис. 149, г) заготовку надрубают, оставляя прочно соединенной на каком-то участке. В художественной ковке этот прием широко применяется, при этом надрубленные зубцы отгибают, вытягивают, расплющивают и т. д., превращая в завитки, листья и цветы на общей ветке, дополнительные (поперечные) зубцы ограды по эскизу и велению фантазии.
Обрубка – это отделение металла по внешнему контуру. Вырубка (рис. 149, д) – удаление части металла по внутреннему контуру, применяемое при создании ажурных изделий или отверстий сложной формы и больших размеров. Для вырубки по сложному контуру применяется специальный инструмент – кузнечный топор (секач) с угловой или полукруглой формой лезвия.
Пробивку проводят на кольце с толстыми стенками, которое устанавливают на наличнике наковальни. Сверху кладут заготовку тем местом, в котором будет пробиваться отверстие.
Прошивень берут чуть меньшего размера, чем диаметр кольца. Слабыми ударами его вгоняют в металл, который выдавливают в кольцо с другой стороны. Чтобы отверстие получилось ровным, края прошивня должны быть острыми, а зазор между ним и кольцом очень небольшим.
Отверстия диаметром до 30 мм делаются пробойниками с различным сечением рабочей части. Ими пользуются в паре с гвоздильней и кузнечной плитой, подбирая требуемые фасонные отверстия.
Работать пробойниками очень удобно, так как они имеют конические сужения к обоим концам. Это позволяет легко вынимать инструмент из отверстия или проталкивать его в отверстие.
После пробивания отверстия поверхность около него несколько деформируется. Заготовку правят легкими ударами ручника или используют гладилки.
Во время прошивания отверстия импульс от ударов распространяется не только строго вниз, но и немного в стороны. Чем больше диаметр инструмента, тем больше форма заготовки прогибается внутрь. Поэтому прошивку осуществляют в самом начале обработки изделия в несколько этапов по разным схемам.
Открытую прошивку выполняют на рабочей плоскости наковальни. Пробойник погружают на 2/3 в глубину металла, затем изделие переворачивают на другую сторону и легкими ударами выбивают оставшуюся часть. При закрытой прошивке место заготовки, в котором будет пробиваться отверстие, располагают над круглым отверстием наковальни. От ударов по пробойнику металл выдавливается с другой стороны (рис. 150).
Рис. 150. Прошивка отверстия пробойником.
Инструмент погружают примерно на 1/2 глубины металла, затем заготовку вынимают и, не отнимая пробойника, делают легкий удар, чтобы точно обозначить место с другой стороны. Затем поковку переворачивают, ставят над отверстием и выбивают прошивнем металлическую пробку.
Во время работы инструмент рекомендуется немного покачивать после каждого удара. В противном случае он застревает и требуются большие усилия, чтобы продвигать его дальше.
При прошивке глубоких отверстий пробойник необходимо периодически погружать в воду, так как иначе он сам может начать деформироваться. К тому же охлажденный он дает усадку и легче проходит в отверстие.
Другой способ обезопасить инструменты – насыпать в образующееся отверстие немного угольного порошка. При работе он будет гореть, а образовавшиеся газы будут выполнять роль смазывающего вещества и предотвращать взаимодействие металлов.
У отверстий, выполненных с помощью пробивки, сужение направлено к нижнему краю, а максимальная ширина соответствует наибольшему сечению прошивня. У тех же, которые сделаны пробойником, сужение идет к центру и внешние отверстия имеют диаметр, соответствующий сечению погруженной в металл части инструмента. Это следует учитывать при выборе размера пробойника.
При раздаче тонкие стенки детали могут выпучиваться за внешние границы. Чтобы устранить этот дефект, в отверстие вставляют стержень такого же диаметра, кладут заготовку горизонтально на наковальню и делают осадку выступа.
Инструмент при выбивании отверстий располагают вертикально, первые удары наносят слабо, чтобы наметить место и создать направление деформации.
Способов и приемов ковки множество, но все их можно свести к нескольким основным операциям. Это осадка и высадка, протяжка или вытяжка, рубка, прошивка или пробивка отверстий, гибка, закручивание, отделка (выглаживание), нанесение рисунка, набивка фактуры и рельефа, кузнечная сварка.
Нагрев металлов
Этот процесс начинается с розжига и топки горна.Для начального нагрева холодного горна необходимо очистить очаг от золы и шлака, продуть фурму. Затем засыпать в очаг небольшой слой угля, следя за тем, чтобы отверстия фурмы оставались свободными, поверх него – древесную стружку или пропитанную керосином ветошь. Поджечь ветошь или стружку, засыпать сверху второй слой угля и начать слабо поддувать воздух в фурму. Когда уголь разгорится, добавить еще топлива и плавно увеличить подачу воздуха.
Уголь в горне спекается в корку, под которой и развивается необходимая высокая температура. Для разогрева заготовки зарывают ее целиком или нужную часть в горячие угли подальше от фурмы (чтобы между металлом и фурмой постоянно был слой раскаленного угля) и засыпают свежим углем. Корка образует спекшийся свод, который должен всегда быть целым. Время от времени подгребают от краев очага к центру свежий уголь и слегка обрызгивают его водой. Если угли под коркой выгорели и образовалась большая полость, разрушают свод и подгребают свежий уголь; вскоре образуется новая корка. Заготовку периодически поворачивают для равномерного нагрева.
Регулируют поддув так, чтобы пламя было нейтральным, невысоким, слегка коптящим. Избыток воздуха (высокое дутье) вызывает перегрев металла и оплавление кромок. Кроме того, образуется окалина, которая приводит к потерям (угару) металла, снижает качество и затрудняет дальнейшую обработку заготовки. Избыточный или неоправданно долгий разогрев заготовки приводит к пережогу металла, он становится хрупким, при ударе рассыпается на части.
Хорошая ковкость появляется после достижения температурного промежутка, который для каждого металла свой. Нагревать заготовки чаще всего приходится до ковочной температуры, которая для разных видов стали составляет от 1200 до 1250 °C.
Определение степени нагрева осуществляется с помощью специальных приборов – термопаров и пирометров. Но в условиях обычной кузницы проще и вернее определять ее на глаз. На разных степенях каления металлы окрашиваются в разные цвета, которые при остывании меняются в обратном порядке.
При дневном освещении в тени температуры нагрева соответствуют следующим цветам:
– 530–580 °C – темно-коричневый;
– 580–650 °C – красно-коричневый;
– 650–730 °C – темно-красный;
– 730–780 °C – вишневый;
– 780–830 °C – светло-вишневый;
– 830–900 °C – красный;
– 900–1050 °C – светло-красный;
– 1050–1150 °C – соломенно-желтый;
– 1150–1250 °C – лимонно-желтый;
– 1250–1400 °C – ослепительно белый.
Режимы нагрева
Правильный режим нагрева имеет большое значение для качественной последующей обработки. Обязательно нужно учитывать температурный интервал, верно определять время нагрева заготовки, чтобы не допустить пережигания или недокала.Обычно ковку начинают при 1100° C и заканчивают при 700 °C. Следует помнить о том, что при длительном нагреве углерод стали выгорает прежде всего с поверхности. Если надо закалить изделие после ковки, долго греть заготовку нельзя. Лучше увеличить температуру в очаге горна.
Нижняя граница ковки должна превышать отметку 723 °C, выше которой кристаллическая решетка металла меняет свою структуру на гранецентрированную кубическую. В этом состоянии сталь имеет наибольшую пластичность.
Определение верхней границы ковки зависит от температуры плавления: она должна быть на 100–150 °C ниже последней. При превышении этого предела начинается резкое увеличение размеров зерен металла, что приводит к уменьшению пластических свойств. Такой дефект называется перегревом. Его можно устранить, проведя дополнительную ковку, после которой зернистость уменьшается, и подвергнув металл повторной термической обработке.
Нагрев до более высоких температур в горне приводит к тому, что материал начинает плавиться, вследствие чего большое количество углерода и других газов проникает в его нижние слои. Там происходит активное окисление, которое в кузнечном деле называется пережогом. Связь между зернами нарушается, и металл навсегда теряет пластичность.
Нагревание сплавов следует производить в строго ограниченном температурном промежутке, который определяется свойствами материала. Он обозначается буквами Тн и Тк – температура начала и конца ковки.
При приближении к Тк у металла устанавливается мелкозернистая структура, которая обеспечивает высокую пластичность, поэтому при нагревании его стремятся доводить до этой температуры. Такой режим позволяет дольше ковать изделие. Но, с другой стороны, при долгом повышении температуры с поверхности начинает выгорать углерод. Деталь после этого будет очень трудно закалить. Поэтому режим следует выбирать заранее, с учетом поставленной задачи.
Интервал, в котором можно проводить ковку, у разных марок стали различный. Самый широкий (до 500 °C) имеют малоуглеродистые сорта стали, что позволяет обрабатывать их в течение длительного промежутка времени без дополнительного нагрева. Чем выше содержание углерода, тем этот промежуток меньше.
Другие металлы, например алюминий, имеют более низкий температурный интервал обработки. Для сплава ВД17 он составляет 400–470 °C.
Во время ковки металл постепенно остывает и с трудом поддается деформации. Поэтому останавливать процесс надо уже при достижении температуры, которая на 20–30 °C выше Тк.
Табл. 5 содержит информацию о температурных интервалах некоторых марок стали.
Таблица 5. Температурные интервалы ковки
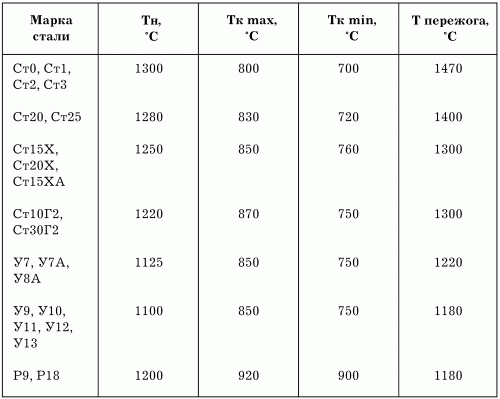
Скорость нагрева зависит также от сечения заготовки. Быстрее нагреваются круглые детали, медленнее – квадратные. У изделий большего сечения разница почти отсутствует. Нагрев в горне, заправленном древесным углем, круглой заготовки диаметром 10–20 мм происходит за 2–4 минуты, а квадратной – за 3–5 минут.
Если размеры больше 30 мм, то время увеличивается до 8–15 минут, а у заготовок диаметром до 50 мм нагрев занимает до 25 минут.
Поскольку каменный уголь дает меньшее количество тепла, то нагревать на нем деталь придется немного дольше. Для того, чтобы получить гарантированно ровный прогрев, поковки рекомендуется выдерживать в огне в течение срока, больше требуемого на 25 %.
Отжиг
Очень часто для выполнения художественных изделий требуется пластичная поделочная сталь, а под рукой оказалась только инструментальная. Как поступить в таком случае? Ковкость металла можно повысить, проведя отжиг.Как известно, содержащая меньшее количество углерода сталь более пластична.
При отжиге сталь более высокой марки нагревается в горне при температуре 650–720 °C, что соответствует темно-красному цвету каления, в течение 2–3 часов.
Регулировать режим ковки можно интенсивностью поддува. Периодически уровень накала надо проверять, охлаждение и перегрев одинаково нежелательны.
По прошествии нужного времени горн выключают и заготовке дают постепенно остыть. Чем медленнее будет происходить этот процесс, тем пластичнее станет металл. Если отжиг проводится на древесном угле, то можно закопать заготовку в золу и оставить в таком виде на несколько часов.
Окалина
При нагревании стальных изделий на поверхности образуется слой оксидов железа, называемый в кузнечном деле окалиной. Пластичность металла после ее появления заметно снижается.С повышением температуры окисление становится более интенсивным, особенно после 900 °C. Образование окалины гораздо сильнее при избытке воздуха, наличие которого определяется по коротким прозрачным языкам пламени. Ее верхний слой, называемый шубой, частично предохраняет металл от дальнейшего окисления.
Параллельно происходит выделение углерода из верхних слоев материала, вследствие чего металл становится менее прочным и хуже закаливается.
У заготовок большого размера часть газа из внутренних слоев переходит во внешние, и металл немного восстанавливает свою пластичность.
В условиях кузницы полностью защитить поковку от образования окалины невозможно. Для уменьшения этого процесса применяют скоростной нагрев, однако делать это можно не во всех случаях.
Следует также отметить, что образование окалины происходит не только во время нагревания, но и в течение ковки. Поэтому при переносе надо следить за тем, чтобы слой «шубы» не осыпался.
Обрабатывая металл на наковальне, окалину удаляют только с тех частей, которые подвергаются деформации. У заготовок из малоуглеродистых сталей нагар легко удаляется ударами ручника.
Перед тем как положить заготовку в горн, на нее наносят специальные обмазки. Они не только защищают металл, но и являются хорошим смазывающим материалом, снижающим время нагрева и увеличивающим пластичность металла.
Простой способ защиты от окалины мелких изделий из инструментальной стали, например чеканов, напильников и т. п., – нагревать их внутри герметично закрытой трубы.
Дефекты нагрева
При недогреве, который появляется при неправильно выбранном тепловом режиме или плохой поддувке, разные части заготовки во время ковки деформируются неодинаково. Это вызывает перекос и образование трещин.Если прокаливается только часть заготовки, необходимо следить за тем, чтобы весь подлежащий обработке участок был одного цвета. В противном случае поковка требуемой формы не получится.
Важно следить за режимом поддува: он должен быть равномерным и давать необходимую для того или иного процесса температуру.
Часто при неправильном нагреве на поверхности металла возникают трещины. Работы с поделочной сталью, как правило, обходятся без них, поскольку данные сорта обладают широким температурным интервалом ковки.
Глубокие поперечные трещины появляются вследствие слишком быстрого нагрева заготовки, когда внутренние слои остаются еще холодными. Наиболее часто трещины образуются на поверхности, они возникают из-за того, что металл остыл до температуры, которая ниже Тк. Если при ударах молотом заготовка раскалывается на несколько частей, то это свидетельствует о пережоге стали.
Начинающему мастеру следует особенно тщательно следить за соблюдением температурного режима ковки и нагрева. Рекомендуется до начала серьезной работы потренироваться на черновых заготовках, то есть не имеющих еще правильной формы.
Вытяжка
Вытяжка или протяжка – увеличение длины заготовки за счет поперечного сечения. Чаще всего возникает необходимость отковать из куска металла прут или полосу определенного сечения. Для этого надо взять раскаленную заготовку и положить ее на наковальню. Удерживая поковку клещами, наносят по всей длине удары узким бойком молота. Бить надо быстро и часто, за один нагрев отковывая как можно больший участок. Затем заготовку вновь нагревают, поворачивают на 90° и повторяют операцию.Для того чтобы поковка не раздавалась в ширину и вытягивалась в нужном направлении, применяют желобчатые (седлообразные) наковальни и шпераки, а также ручьи кузнечной плиты-формы. Если нужна круглая заготовка или заготовка с гранями, применяют обжимки (рис. 144).
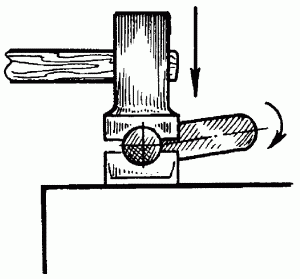
Они не только вытянут заготовку в длину, но и выгладят ее, придав нужное сечение. Поворачивая заготовку вокруг продольной оси (для получении граней – на определенный угол), надо ударять кувалдой по обжимке и постепенно передвигать заготовку вперед. Если необходимо получить всю поковку или отдельный участок в виде пластины (например, при ковке лепестков, листьев в растительном орнаменте), заготовку или ее часть расплющивают (разгоняют). При этом площадь увеличивается за счет уменьшения толщины.
Расплющивать можно кувалдой или ручником на наковальне. Если необходимо раздать металл быстрее, надо воспользоваться раскаткой с полукруглыми рабочими поверхностями. Сила удара в таком случае будет сосредоточена на небольшом участке, и металл раздастся равномерно во все стороны.
Вытяжка с переходами
Чаще всего, чтобы выполнить протяжку с большим перепадом размеров, ее проводят в несколько этапов, в промежутке выполняя кантовку. Такая последовательность операций называется переходом. Наиболее удобная последовательность переходов: несколько протяжек с последующей кантовкой на 90°, затем на 45° и закругление с помощью обжимок, раскаток и других специальных инструментов.Для выполнения нескольких последовательных операций существует правило: независимо от задуманного результата в процессе протяжки заготовка сначала куется квадратного сечения, затем она уменьшается до нужных размеров и только потом ей придается нужная форма.
На рис. 145 показана очередность переходов при ковке различных сечений.
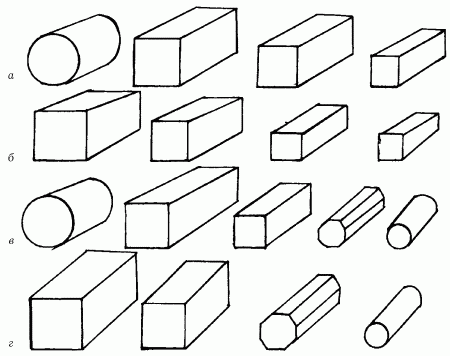
Разгонка
Одной из разновидностей протяжки, часто используемой в художественной ковке, является разгонка, или изготовление пластины из заготовки большего сечения.Она выполняется с помощью раскатки, которая разгоняет металл в разные стороны. Последовательным перемещением инструмента создают широкую ребристую поверхность нужных размеров, потом выравнивают ее гладилками до требуемой толщины (рис. 146).
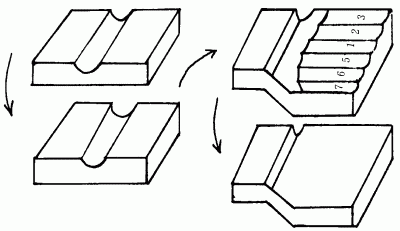
Протяжка на оправке и раскатка
Если необходимо увеличить длину толстостенной трубки или другой пустотелой заготовки при уменьшении ее толщины, надо применять вытяжку с оправкой. Оправку (она круглая или квадратная, обычно слегка коническая или пирамидальная для облегчения снятия заготовки) вставляют в поковку, саму поковку размещают в соответствующих обжимках (рис. 147, а).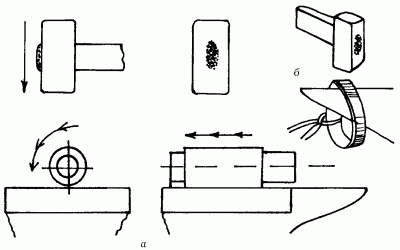
В процессе вытяжки поковку надо постоянно поворачивать вокруг оси (при работе с квадратной оправкой – на 90°).
Для увеличения наружного и внутреннего диаметров колец, обручей и т. п. металл раздают на оправке. Для этого надо осадить и прошить заготовку или взять готовое изделие и надеть его на цилиндрическую оправку. Оба выступающих конца оправки уложить на подставку, ударами молота раздать металл, постепенно поворачивая заготовку. Диаметр изделия увеличивается за счет утончения стенок. Готовые кольца можно раздать на конической оправке, поставленной в вертикальное положение.
Раскатка увеличивает диаметр кольцевой заготовки протяжкой стенок полосы. Ее применяют для изготовления бесшовных колец высокой прочности (рис 147, б).
Проводят эту операцию на роге кувалдой или используют верхники вогнутой формы. Если кольцо сделано из полосы с продольным распределением волокон, то поперечная деформация незначительна, а расширение идет целиком по периметру. На заключительном этапе делают выглаживание.
Осадка
Осадкой называется увеличение площади поперечного сечения детали за счет уменьшения длины. Эта операция обратна вытяжке (рис. 148).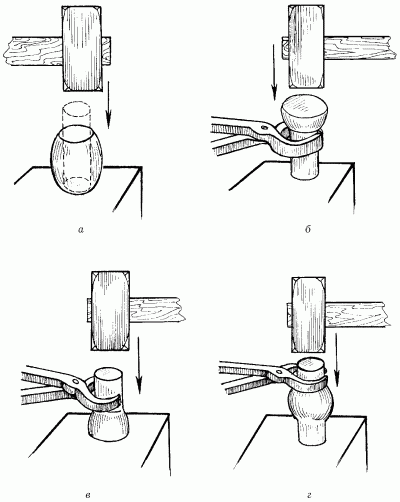
Осадка (рис. 148, а) нужна для уменьшения длины заготовки за счет увеличения толщины (поперечного сечения). Если осадка производится только на отдельных участках заготовки (на концах или в середине), то такая операция называется высадкой (рис. 148, б, в, г).
Осадку применяют для утолщения изделия по всей длине, высадку – для получения отдельных утолщений, при ковке декоративных элементов (узлов, ягод и т. п.), шляпок гвоздей и т. д.
Высадка в середине стержня или полосы проводится также перед изгибанием под углом 90°. Это необходимо для восполнения недостающего металла, иначе в месте перегиба толщина поковки сильно уменьшается.
Когда требуется высадить середину длинной заготовки, ни один из вышеперечисленных способов не подходит. Пруток надо изогнуть в форме буквы Z выше места деформации и наносить удары по изгибу. После выполнения операции заготовку выпрямляют.
Осадка применяется как предварительная операция перед прошивкой при изготовлении колец, трубок и других пустотелых изделий.
Для осадки или высадки нагревают поковку или высаживаемый участок в горне. Если длина заготовки или нагретого участка превосходит диаметр (толщину) не более чем в 2–2,5 раза, а сама поковка относительно короткая, то ставят поковку вертикально на наковальню и бьют ручником или кувалдой по верхнему концу.
Длинные изделия или участки при таком способе осадки могут изогнуться, поэтому их надо положить на наковальню, зажать клещами и осаживать молотом или ручником.
Существует также способ осадки поковки за счет ее собственного веса: для этого зажимают нагретую поковку в клещах и бьют торцом о наковальню. Но необходимо помнить, что обычно такая осадка применяется для небольших изделий.
Чтобы утолщение распространялось только в нужную сторону, заготовку после высадки куют соответствующим образом. Если высадка оказалась недостаточной, процесс повторяют. Для придания желаемой формы утолщению пользуются обжимками, подбойками и т. п.
Фигурную высадку выполняют с помощью гвоздильни. Пруток в этом случае помещают в отверстие наковальни, необходимый по длине конец оставляют снаружи и деформируют ударами кувалды.
Можно высаживать заготовку в тисках. При этом надо помнить, что нагретая часть в тисках охлаждается быстрее. Этот способ используется тогда, когда необходимо получить четкий переход от осаженной части к стержню.
Рубка
Рубкой называется разделение заготовки на части. Для этого используется зубило, разнообразные подложки и кувалда (рис. 149).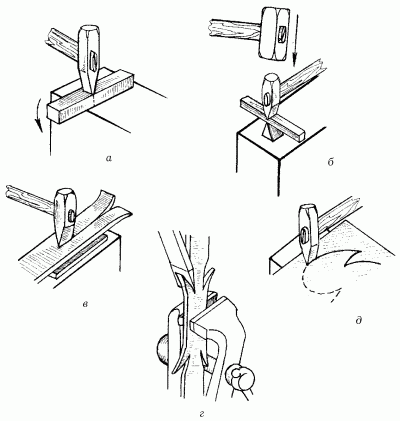
Для рубки заготовку нагревают до темно-красного цвета, кладут на наковальню, наставляют кузнечное зубило и сильно бьют по нему молотом (рис. 149, а). Перерубив заготовку на 3/4, переворачивают ее и отрубают окончательно. Толстые поковки перерубаются с помощью зубила и подсечки (рис. 149, б), полосы – с помощью подсечки без зубила. Подсечку вставляют в отверстие наковальни, сверху кладут полосу и наносят удар кувалдой. Нельзя прорубать металл насквозь, потому что можно повредить острые части инструмента. Для окончательного перерубания надо использовать незакаленную площадку у основания рога наковальни или подложить полосу мягкой стали (рис. 149, в). Чтобы лезвия зубила и подсечки не схватывались с горячим металлом и не выкрашивались, перед рубкой необходимо протереть их ветошью, смоченной машинным маслом.
Разновидностями рубки являются разрубка, обрубка (обсечка), вырубка. При разрубке (рис. 149, г) заготовку надрубают, оставляя прочно соединенной на каком-то участке. В художественной ковке этот прием широко применяется, при этом надрубленные зубцы отгибают, вытягивают, расплющивают и т. д., превращая в завитки, листья и цветы на общей ветке, дополнительные (поперечные) зубцы ограды по эскизу и велению фантазии.
Обрубка – это отделение металла по внешнему контуру. Вырубка (рис. 149, д) – удаление части металла по внутреннему контуру, применяемое при создании ажурных изделий или отверстий сложной формы и больших размеров. Для вырубки по сложному контуру применяется специальный инструмент – кузнечный топор (секач) с угловой или полукруглой формой лезвия.
Выбивание отверстий
В кузнице, не применяя сверлильного станка, можно делать сквозные отверстия или углубления с помощью пробойников. Существует два способа выбивания отверстий.Пробивка
Это один из способов изготовления отверстий, при котором металл отделяется от заготовки. Ее проводят при высокой температуре пробойником, если отверстие небольшого диаметра, и с помощью специальных прошивней.Пробивку проводят на кольце с толстыми стенками, которое устанавливают на наличнике наковальни. Сверху кладут заготовку тем местом, в котором будет пробиваться отверстие.
Прошивень берут чуть меньшего размера, чем диаметр кольца. Слабыми ударами его вгоняют в металл, который выдавливают в кольцо с другой стороны. Чтобы отверстие получилось ровным, края прошивня должны быть острыми, а зазор между ним и кольцом очень небольшим.
Отверстия диаметром до 30 мм делаются пробойниками с различным сечением рабочей части. Ими пользуются в паре с гвоздильней и кузнечной плитой, подбирая требуемые фасонные отверстия.
Работать пробойниками очень удобно, так как они имеют конические сужения к обоим концам. Это позволяет легко вынимать инструмент из отверстия или проталкивать его в отверстие.
После пробивания отверстия поверхность около него несколько деформируется. Заготовку правят легкими ударами ручника или используют гладилки.
Прошивка
Если пробивка отверстия производится за счет выдавливания металла, то при прошивке он раздается в стороны, пропуская инструмент. Чаще всего этот способ является подготовительным этапом для пробивания.Во время прошивания отверстия импульс от ударов распространяется не только строго вниз, но и немного в стороны. Чем больше диаметр инструмента, тем больше форма заготовки прогибается внутрь. Поэтому прошивку осуществляют в самом начале обработки изделия в несколько этапов по разным схемам.
Открытую прошивку выполняют на рабочей плоскости наковальни. Пробойник погружают на 2/3 в глубину металла, затем изделие переворачивают на другую сторону и легкими ударами выбивают оставшуюся часть. При закрытой прошивке место заготовки, в котором будет пробиваться отверстие, располагают над круглым отверстием наковальни. От ударов по пробойнику металл выдавливается с другой стороны (рис. 150).
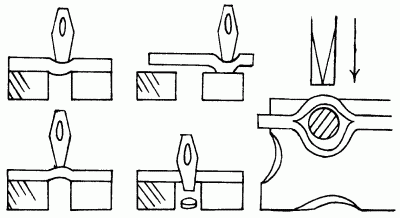
Инструмент погружают примерно на 1/2 глубины металла, затем заготовку вынимают и, не отнимая пробойника, делают легкий удар, чтобы точно обозначить место с другой стороны. Затем поковку переворачивают, ставят над отверстием и выбивают прошивнем металлическую пробку.
Во время работы инструмент рекомендуется немного покачивать после каждого удара. В противном случае он застревает и требуются большие усилия, чтобы продвигать его дальше.
При прошивке глубоких отверстий пробойник необходимо периодически погружать в воду, так как иначе он сам может начать деформироваться. К тому же охлажденный он дает усадку и легче проходит в отверстие.
Другой способ обезопасить инструменты – насыпать в образующееся отверстие немного угольного порошка. При работе он будет гореть, а образовавшиеся газы будут выполнять роль смазывающего вещества и предотвращать взаимодействие металлов.
Раздача
При прошивке и пробивке образуются отверстия, края которых имеют коническое сужение. Для исправления этого дефекта используют бочкообразные оправки, которые проталкивают сквозь отверстие. При этом стенки вдавливаются внутрь, и отверстие получается правильной цилиндрической формы.У отверстий, выполненных с помощью пробивки, сужение направлено к нижнему краю, а максимальная ширина соответствует наибольшему сечению прошивня. У тех же, которые сделаны пробойником, сужение идет к центру и внешние отверстия имеют диаметр, соответствующий сечению погруженной в металл части инструмента. Это следует учитывать при выборе размера пробойника.
При раздаче тонкие стенки детали могут выпучиваться за внешние границы. Чтобы устранить этот дефект, в отверстие вставляют стержень такого же диаметра, кладут заготовку горизонтально на наковальню и делают осадку выступа.
Инструмент при выбивании отверстий располагают вертикально, первые удары наносят слабо, чтобы наметить место и создать направление деформации.