Операция может выполняться за одну или несколько установок детали. Установкой называют часть операции, выполняемой при одном закреплении детали. Например, опиливание детали с одной стороны, а затем после перестановки и закрепления ее с другой стороны является одной операцией, выполненной за две установки.
Позицией называется каждое из различных положений детали относительно станка и режущего инструмента при одной ее установке (не считая перемещений, связанных с рабочими движениями детали или инструмента). Операция может быть выполнена за один или несколько переходов.
Переходом называется часть операции по обработке одной поверхности (или нескольких одновременно), выполняемая без изменения режущего инструмента и режима работы станка. Опиливание плоскости какого-либо изделия сначала напильником с крупной насечкой, а потом с более мелкой составит два перехода. Одновременное сверление и зенкерование отверстий является также одним переходом.
Проходом называется часть перехода, охватывающая все действия, связанные со снятием одного слоя металла без изменения инструмента, поверхности обработки и режима резания станка. Каждый переход или проход включает в себя, кроме процесса снятия стружки, относящиеся к ним рабочие приемы.
Приемом называют законченное действие рабочего из числа необходимых для выполнения операции или ее подготовки; например, установка и снятие детали, измерение ее, пуск и остановка станка и т. п.
Наименьшая возможная по времени часть рабочего приема, которая является отдельным, но законченным движением рабочего, называется элементом приема.
Различают еще один элемент работы — установку. Установка — положение, приданное детали в тисках или на станке после ее зажима с целью подвергнуть деталь установке.
5.2. Порядок разработки технологического процесса
5.3. Выбор режущего и измерительного инструмента и приспособлений
Контрольные вопросы
Раздел II
Глава 6
6.1. Общие сведения о резании металлов
Позицией называется каждое из различных положений детали относительно станка и режущего инструмента при одной ее установке (не считая перемещений, связанных с рабочими движениями детали или инструмента). Операция может быть выполнена за один или несколько переходов.
Переходом называется часть операции по обработке одной поверхности (или нескольких одновременно), выполняемая без изменения режущего инструмента и режима работы станка. Опиливание плоскости какого-либо изделия сначала напильником с крупной насечкой, а потом с более мелкой составит два перехода. Одновременное сверление и зенкерование отверстий является также одним переходом.
Проходом называется часть перехода, охватывающая все действия, связанные со снятием одного слоя металла без изменения инструмента, поверхности обработки и режима резания станка. Каждый переход или проход включает в себя, кроме процесса снятия стружки, относящиеся к ним рабочие приемы.
Приемом называют законченное действие рабочего из числа необходимых для выполнения операции или ее подготовки; например, установка и снятие детали, измерение ее, пуск и остановка станка и т. п.
Наименьшая возможная по времени часть рабочего приема, которая является отдельным, но законченным движением рабочего, называется элементом приема.
Различают еще один элемент работы — установку. Установка — положение, приданное детали в тисках или на станке после ее зажима с целью подвергнуть деталь установке.
5.2. Порядок разработки технологического процесса
На выбор разработки технологического процесса изготовления деталей в машиностроении влияют вид заготовок, материал детали, ее конструкции и размеры, а также обеспечение наименьшего расхода металла, степень приближения размеров и формы заготовки к размерам и форме детали.
Для изготовления детали используют различные заготовки:
1) отливки из чугуна, стали и сплавов цветных металлов;
2) поковки, полученные свободной ковкой, горячей штамповкой и холодной штамповкой (из листа);
3) сортовые материалы круглого и квадратного сечения полученные прокатом;
4) заготовки из металлокерамики и пластмасс.
Базы и их выбор. Термин «база» происходит от греческого слова «базис» — основание. Базами называют поверхности, от которых задаются размеры, ведется установка и контроль при обработке и сборке детали. Различают основные типы баз: конструкторские, технологические и сборочные.
Конструкторскими базами называют поверхности или оси определяющие положение детали относительно других деталей в машине при сборке. Две взаимно перпендикулярные оси, которые совмещают ось отверстия корпуса с осями отверстий кондукторных втулок приспособления, являются конструкторскими базами детали.
Технологическими базами называют поверхности, определяющие положения детали при ее установке на станке или в приспособлении. Технологические базы подразделяются на установочные и измерительные.
Установочными базами называют поверхности, по которым деталь устанавливается и ориентируется при обработке. При разметке установочной базой является поверхность, по которой заготовку устанавливают на разметочную плиту. При обработке в тисках установочными базами будут поверхности, по которым ведется закрепление детали. При обработке на станке заготовку закрепляют на столе или в приспособлении. Установочной базой при этом будет та поверхность, по которой ориентируют деталь. Установочные базы могут быть черновыми и чистовыми.
Черновая база — необработанная поверхность, используемая для первой установки заготовки.
Чистовые базы — обработанные поверхности, по которым устанавливают деталь для окончательной обработки.
Измерительными базами называют поверхности, от которых ведется отсчет размеров при измерении детали.
Сборочными базами называют поверхности, по которым детали присоединяются к другим деталям, определяющим ее положение в узле или машине.
Базы выбирают следующим образом. В качестве черновой базы принимают поверхность, которая должна остаться необработанной в готовой детали; такая базировка обеспечит правильное взаимное расположение обработанных поверхностей относительно необрабатываемой. После выполнения этого условия черновые базы должны быть заменены чистовыми — обработанными базами Основное назначение черновых базирующих поверхностей сводится к обеспечению правильной ориентации детали при выполнении первой механической обработки — создании чистовых баз. Вначале обрабатывается поверхность, относительно которой чертежом задана координация большего числа других поверхностей. Поверхности, принимаемые за чистовые базы, должны обеспечить жесткое крепление заготовки, позволяющее производить обработку изделия с образованием с стружки большого сечения. При точной обработке следует принимать за чистовую базу основные поверхности детали. Установочная база должна иметь достаточную протяженность для обеспечения устойчивости детали при ее обработке. Следует стремиться выполнять, по возможности, все операции (кроме первой), используя одну установочную базу. Измерительная база должна быть выбрана так, чтобы было удобно и просто выполнять процесс измерений. Целесообразно совмещать технологическую и измерительную базу со сборочной, тогда погрешности при обработке и при контроле детали будут наименьшими.
Припуском называется слой материала, снимаемый с заготовки для получения окончательно обработанной поверхности детали. Припуск представляет собой разницу между параметрами заготовки и размером готовой детали. Поверхности, которые механически не обрабатываются припусков не имеют. Применение прогрессивных способов изготовления заготовок (штамповка на ковочных прессах, прецизионное литье, чеканка, литье под давлением) позволяет уменьшить припуски, повысить производительность обработки резанием и снизить расход металла. Припуски подразделяются на общие и межоперационные. Общим припуском называется слой металла, который необходимо удалить с заготовки на всех операциях для получения готовой детали. Межоперационным припуском называется слой металла, который удаляется на данной операции, в результате выполнения которой получают поверхность заданного размера и чистоты. Значения припусков в зависимости от вида обработки приводятся в таблицах. Недостаточный припуск затрудняет и удорожает обработку, а большой припуск приводит к непроизводительной затрате времени и снижает производительность. Величины межоперационных припусков устанавливаются в зависимости от характера производства (массовое, серийное и индивидуальное), принятого технологического процесса, формы деталей, материала и технических требований.
Размер припуска должен быть минимальным, но достаточным для получения заданной точности, надлежащей чистоты поверхности н размеров детали. Припуски под шабрение вследствие трудоемкости этой операции должны быть минимальными.
Технологический процесс, разработанный заводским или цеховым технологическим отделом, записывается в документ, называемый технологической картой. Она служит основой для планирования и распределения работы в цехе и на заводе, а также исходным документом для подготовки производства, снабжения необходимыми материалами, заготовками. При серийном производстве технологическая карта является основным документом. На заводах применяются различные формы технологических карт, но независимо от формы каждая технологическая карта содержит следующие данные: наименование изделия, чертеж, материал, технические требования, номера операций в определенной последовательности, наименование и содержание операций и переходов, наименование оборудования приспособлений, измерительного, режущего и вспомогательного инструментов.
На заводах крупносерийного и массового производства разрабатывают операционные карты. В них записывают данные о порядке обработки при выполнении только одной операции, предусмотренной технологическим процессом. В такой карте указывается название детали и операции, приводятся эскизы, проставляются те размеры, допуски и классы чистоты, которые должны быть получены на данной операции, наименование инструментов и приспособлений, могут указываться положения инструментов, баз и зажимов.
Инструкционно — технологической карте приводятся дополнительные указания о выполнении операции.
В единичном и мелкосерийном производстве составляют маршрутно-технологическую карту. Она выполняется либо на специальных бланках, либо на обороте чертежа детали. В этой карте указываются наименования всех цехов, участков, где должна обрабатываться заготовка; данные об оборудовании и приспособлениях; перечисляются все операции: разряд работы, норма времени и иногда количество обрабатываемых заготовок и размер партии. Маршрутные карты чаще всего применяются в инструментальных цехах заводов, где инструмент изготовляется небольшими партиями.
При разработке технологической документации предусматривают применение новой прогрессивной технологии, автоматизацию и новые средства механизации.
Режим выполнения установленного технологического процесса, оформленного в виде технологических карт, называется технологической дисциплиной. Соблюдение технологической дисциплины является основным условием, обеспечивающим выпуск высококачественной продукции, высокую производительность труда, уменьшение брака и снижение себестоимости изделий. Технологическая дисциплина требует от всех рабочих, мастеров и инженеров обеспечения строжайшего выполнения операций технологического процесса и выпуска продукции согласно требованиям технических условий и государственных стандартов. Тем не менее, это не значит, что технологический процесс не может быть изменен. Наоборот, технология любого производства должка совершенствоваться так, чтобы непрерывно росла производительность труда, снижалась себестоимость продукции, и улучшалось ее качество. Соблюдение технологической дисциплины не должна противоречить проявлению идей новаторства, применению наиболее рациональных приемов труда и передовой технологии, которые организованно внедряются в производство через существующие на всех заводах бюро рационализации и изобретательства. Но все изменения в технологические карты имеют право вносить только работники технологической службы предприятия. Поэтому произвольное изменение технологии рабочим, мастером и т. д. является нарушением технологической дисциплины.
Для изготовления детали используют различные заготовки:
1) отливки из чугуна, стали и сплавов цветных металлов;
2) поковки, полученные свободной ковкой, горячей штамповкой и холодной штамповкой (из листа);
3) сортовые материалы круглого и квадратного сечения полученные прокатом;
4) заготовки из металлокерамики и пластмасс.
Базы и их выбор. Термин «база» происходит от греческого слова «базис» — основание. Базами называют поверхности, от которых задаются размеры, ведется установка и контроль при обработке и сборке детали. Различают основные типы баз: конструкторские, технологические и сборочные.
Конструкторскими базами называют поверхности или оси определяющие положение детали относительно других деталей в машине при сборке. Две взаимно перпендикулярные оси, которые совмещают ось отверстия корпуса с осями отверстий кондукторных втулок приспособления, являются конструкторскими базами детали.
Технологическими базами называют поверхности, определяющие положения детали при ее установке на станке или в приспособлении. Технологические базы подразделяются на установочные и измерительные.
Установочными базами называют поверхности, по которым деталь устанавливается и ориентируется при обработке. При разметке установочной базой является поверхность, по которой заготовку устанавливают на разметочную плиту. При обработке в тисках установочными базами будут поверхности, по которым ведется закрепление детали. При обработке на станке заготовку закрепляют на столе или в приспособлении. Установочной базой при этом будет та поверхность, по которой ориентируют деталь. Установочные базы могут быть черновыми и чистовыми.
Черновая база — необработанная поверхность, используемая для первой установки заготовки.
Чистовые базы — обработанные поверхности, по которым устанавливают деталь для окончательной обработки.
Измерительными базами называют поверхности, от которых ведется отсчет размеров при измерении детали.
Сборочными базами называют поверхности, по которым детали присоединяются к другим деталям, определяющим ее положение в узле или машине.
Базы выбирают следующим образом. В качестве черновой базы принимают поверхность, которая должна остаться необработанной в готовой детали; такая базировка обеспечит правильное взаимное расположение обработанных поверхностей относительно необрабатываемой. После выполнения этого условия черновые базы должны быть заменены чистовыми — обработанными базами Основное назначение черновых базирующих поверхностей сводится к обеспечению правильной ориентации детали при выполнении первой механической обработки — создании чистовых баз. Вначале обрабатывается поверхность, относительно которой чертежом задана координация большего числа других поверхностей. Поверхности, принимаемые за чистовые базы, должны обеспечить жесткое крепление заготовки, позволяющее производить обработку изделия с образованием с стружки большого сечения. При точной обработке следует принимать за чистовую базу основные поверхности детали. Установочная база должна иметь достаточную протяженность для обеспечения устойчивости детали при ее обработке. Следует стремиться выполнять, по возможности, все операции (кроме первой), используя одну установочную базу. Измерительная база должна быть выбрана так, чтобы было удобно и просто выполнять процесс измерений. Целесообразно совмещать технологическую и измерительную базу со сборочной, тогда погрешности при обработке и при контроле детали будут наименьшими.
Припуском называется слой материала, снимаемый с заготовки для получения окончательно обработанной поверхности детали. Припуск представляет собой разницу между параметрами заготовки и размером готовой детали. Поверхности, которые механически не обрабатываются припусков не имеют. Применение прогрессивных способов изготовления заготовок (штамповка на ковочных прессах, прецизионное литье, чеканка, литье под давлением) позволяет уменьшить припуски, повысить производительность обработки резанием и снизить расход металла. Припуски подразделяются на общие и межоперационные. Общим припуском называется слой металла, который необходимо удалить с заготовки на всех операциях для получения готовой детали. Межоперационным припуском называется слой металла, который удаляется на данной операции, в результате выполнения которой получают поверхность заданного размера и чистоты. Значения припусков в зависимости от вида обработки приводятся в таблицах. Недостаточный припуск затрудняет и удорожает обработку, а большой припуск приводит к непроизводительной затрате времени и снижает производительность. Величины межоперационных припусков устанавливаются в зависимости от характера производства (массовое, серийное и индивидуальное), принятого технологического процесса, формы деталей, материала и технических требований.
Размер припуска должен быть минимальным, но достаточным для получения заданной точности, надлежащей чистоты поверхности н размеров детали. Припуски под шабрение вследствие трудоемкости этой операции должны быть минимальными.
Технологический процесс, разработанный заводским или цеховым технологическим отделом, записывается в документ, называемый технологической картой. Она служит основой для планирования и распределения работы в цехе и на заводе, а также исходным документом для подготовки производства, снабжения необходимыми материалами, заготовками. При серийном производстве технологическая карта является основным документом. На заводах применяются различные формы технологических карт, но независимо от формы каждая технологическая карта содержит следующие данные: наименование изделия, чертеж, материал, технические требования, номера операций в определенной последовательности, наименование и содержание операций и переходов, наименование оборудования приспособлений, измерительного, режущего и вспомогательного инструментов.
На заводах крупносерийного и массового производства разрабатывают операционные карты. В них записывают данные о порядке обработки при выполнении только одной операции, предусмотренной технологическим процессом. В такой карте указывается название детали и операции, приводятся эскизы, проставляются те размеры, допуски и классы чистоты, которые должны быть получены на данной операции, наименование инструментов и приспособлений, могут указываться положения инструментов, баз и зажимов.
Инструкционно — технологической карте приводятся дополнительные указания о выполнении операции.
В единичном и мелкосерийном производстве составляют маршрутно-технологическую карту. Она выполняется либо на специальных бланках, либо на обороте чертежа детали. В этой карте указываются наименования всех цехов, участков, где должна обрабатываться заготовка; данные об оборудовании и приспособлениях; перечисляются все операции: разряд работы, норма времени и иногда количество обрабатываемых заготовок и размер партии. Маршрутные карты чаще всего применяются в инструментальных цехах заводов, где инструмент изготовляется небольшими партиями.
При разработке технологической документации предусматривают применение новой прогрессивной технологии, автоматизацию и новые средства механизации.
Режим выполнения установленного технологического процесса, оформленного в виде технологических карт, называется технологической дисциплиной. Соблюдение технологической дисциплины является основным условием, обеспечивающим выпуск высококачественной продукции, высокую производительность труда, уменьшение брака и снижение себестоимости изделий. Технологическая дисциплина требует от всех рабочих, мастеров и инженеров обеспечения строжайшего выполнения операций технологического процесса и выпуска продукции согласно требованиям технических условий и государственных стандартов. Тем не менее, это не значит, что технологический процесс не может быть изменен. Наоборот, технология любого производства должка совершенствоваться так, чтобы непрерывно росла производительность труда, снижалась себестоимость продукции, и улучшалось ее качество. Соблюдение технологической дисциплины не должна противоречить проявлению идей новаторства, применению наиболее рациональных приемов труда и передовой технологии, которые организованно внедряются в производство через существующие на всех заводах бюро рационализации и изобретательства. Но все изменения в технологические карты имеют право вносить только работники технологической службы предприятия. Поэтому произвольное изменение технологии рабочим, мастером и т. д. является нарушением технологической дисциплины.
5.3. Выбор режущего и измерительного инструмента и приспособлений
Правильный выбор режущего и измерительного инструмента и приспособлений оказывает существенное влияние на качество производимых изделий в машиностроении.
Выбор приспособлений зависит от ряда факторов — от характера обработки, механических свойств обрабатываемого материала, геометрических форм поверхности обработки, размеров детали, выбранных баз и других условий. Приспособления делятся на две группы: универсальные и специальные. К числу универсальных приспособлений относятся слесарные и машинные тиски, сверлильные патроны, струбцины и т. д. Специальные приспособления применяют в том случае, когда нельзя использовать универсальные приспособления, а также при обработке большого количества одинаковых деталей, т. е. в массовом производстве, так как затраты в этом случае на изготовление специальных приспособлений быстро возмещаются.
Режущий инструмент выбирают так, чтобы обеспечить заданную форму, чистоту и точность обрабатываемой поверхности; при этом учитывают размер и механические свойства обрабатываемой детали, программу выпуска. В первую очередь стремятся выбрать стандартизованные и нормализованные инструменты. В редких случаях применяются специальные режущие инструменты.
При выборе измерительных инструментов прежде всего нужно руководствоваться соответствием точности показания данного инструмента техническим условиям на обработку детали. Предпочтение отдается универсальным инструментам. Принимают во внимание удобство измерения инструментом и затраты времени на измерение.
Выбор приспособлений зависит от ряда факторов — от характера обработки, механических свойств обрабатываемого материала, геометрических форм поверхности обработки, размеров детали, выбранных баз и других условий. Приспособления делятся на две группы: универсальные и специальные. К числу универсальных приспособлений относятся слесарные и машинные тиски, сверлильные патроны, струбцины и т. д. Специальные приспособления применяют в том случае, когда нельзя использовать универсальные приспособления, а также при обработке большого количества одинаковых деталей, т. е. в массовом производстве, так как затраты в этом случае на изготовление специальных приспособлений быстро возмещаются.
Режущий инструмент выбирают так, чтобы обеспечить заданную форму, чистоту и точность обрабатываемой поверхности; при этом учитывают размер и механические свойства обрабатываемой детали, программу выпуска. В первую очередь стремятся выбрать стандартизованные и нормализованные инструменты. В редких случаях применяются специальные режущие инструменты.
При выборе измерительных инструментов прежде всего нужно руководствоваться соответствием точности показания данного инструмента техническим условиям на обработку детали. Предпочтение отдается универсальным инструментам. Принимают во внимание удобство измерения инструментом и затраты времени на измерение.
Контрольные вопросы
1. Какие типы производства существующие в машиностроении вы знаете?
2. Дайте краткую характеристику каждому типу производства.
3. Какие виды цехов вы знаете?
4. Дайте определение производственного процесса.
5. Охарактеризуйте основные части производственного процесса.
6. Назовите последовательность разработки технологического процесса.
7. Что обозначает термин «база детали», какой она бывает?
8. Дайте определение припуска и назовите его основные виды.
9. Назовите основные виды технической документации, необходимой для производства изделий в машиностроении.
10. На чем основывается выбор режущего, измерительного инструмента и приспособлений при изготовлении деталей?
2. Дайте краткую характеристику каждому типу производства.
3. Какие виды цехов вы знаете?
4. Дайте определение производственного процесса.
5. Охарактеризуйте основные части производственного процесса.
6. Назовите последовательность разработки технологического процесса.
7. Что обозначает термин «база детали», какой она бывает?
8. Дайте определение припуска и назовите его основные виды.
9. Назовите основные виды технической документации, необходимой для производства изделий в машиностроении.
10. На чем основывается выбор режущего, измерительного инструмента и приспособлений при изготовлении деталей?
Раздел II
Основы резания металлов на металлорежущих станках
Глава 6
Процесс механической обработки металла резанием
6.1. Общие сведения о резании металлов
Обработка металлов резанием — это процесс срезания режущим инструментом с поверхностей заготовки слоя металла в виде стружки для получения необходимой геометрической формы, точности размеров, взаиморасположения и шероховатости поверхностей детали.
Заготовками для механических цехов служат прокат (круглый, квадратный, полосовой, трубы и т. д.), поковки, штамповки и отливки. Заготовки, поступающие в механические цехи, имеют припуск на обработку резанием. Припуск зависит от ряда факторов: размеров, формы и конструктивных особенностей изготовляемой детали, вида заготовки, масштабов производства (числа изготавливаемых деталей) и др. Припуск на сторону для штамповок составляет 1,5–7 мм, для поковок — 2,5–20, для отливок (в земляные формы) — 3–30 мм.
К основным методам обработки металлов резанием относятся точение (рис. 6.1а), сверление (рис. 6.1б), фрезерование (рис. 6.1в), строгание (рис. 6.1 г) и шлифование (рис. 6.1д). Из них наиболее распространенным и изученным методом с точки зрения теории резания металлов считается точение, у которого много общего со всеми другими методами механической обработки металлов, поэтому правильное понимание этого процесса облегчает изучение всех других методов обработки резанием.
Рис. 6.1. Схемы основных методов обработки материалов резанием:
а — точение; б — сверление; в — фрезерование; г — строгание; д — шлифование
I — главное движение; II — движение подачи
Чтобы с заготовки срезать слой металла, необходимо режущему инструменту и заготовке сообщить относительные движения. Инструмент и заготовку устанавливают и закрепляют в рабочих органах станков, обеспечивающих эти относительные движения: в шпинделе, на столе, в револьверной головке и т. д. Движения рабочих органов станков делят на движения резания, установочные и вспомогательные. Движения, которые обеспечивают срезание с заготовки слоя металла или вызывают изменение состояния обработанной поверхности заготовки, называют движениями резания. К ним относят главное движение и движение подачи.
За главное движение принимают то движение, которое определяет скорость деформирования и отделения стружки. За движение подачи принимают то движение, которое обеспечивает непрерывность врезания режущей кромки инструмента в материал заготовки. Эти движения могут быть непрерывными или прерывистыми, а по своему характеру вращательными, поступательными, возвратно-поступательными и т. д. Скорость главного движения обозначают v, величину подачи — s.
Движения, обеспечивающие взаимное расположение инструмента и заготовки для срезания с нее определенного слоя материала, называют установочными. К вспомогательным движениям относят транспортирование заготовки, закрепление заготовок и инструмента, быстрые перемещения рабочих органов станка на холостом ходу, переключение скоростей резания и подачи и т. п.
При токарной обработке (рис. 6.1а) главное движение резания I — вращение обрабатываемой детали, движение подачи II — движение резца. При строгании (рис. 6.1 г) главное движение I — перемещение резца относительно детали или детали относительно резца, что физически равноценно; движение подачи II — перемещение обрабатываемой детали на двойной ход резца в направлении, перпендикулярном к главному движению. При фрезеровании (рис. 6.1в) главное движение I определяется вращением фрезы, а движение II — движением подачи. При сверлении (рис. 6.1б) главное движение I — вращение сверла; движение подачи II — перемещение сверла в осевом направлении. При шлифовании (рис. 6.1д) главное движение I — вращение круга; движение подачи II — продольное или поперечное перемещение детали.
Главное движение по величине значительно больше движения подачи. Вспомогательные движения — установочные перемещения суппортов, задней бабки, поворот резцедержателя, перемещение траверсы и др.
При обработке резанием на детали различают обрабатываемую 1 (рис. 6.2) и обработанную 3 поверхности, поверхность резания 2.
Обрабатываемая поверхность — поверхность, с которой снимается стружка.
Обработанная поверхность — поверхность, полученная после снятия стружки.
Поверхность резания — поверхность, образуемая режущей кромкой резца в результате движений резания. Такая поверхность служит переходной между обработанной и обрабатываемой поверхностями.
Углы режущих инструментов наиболее часто определяют в статической системе координат с началом в рассматриваемой точке режущей кромки резца, ориентированной по направлению скорости главного движения резания. Для этого устанавливают исходные плоскости: основную и рабочую плоскости, плоскость резания.
Основная плоскость — плоскость, проведенная через рассматриваемую точку режущей кромки перпендикулярно к направлению скорости главного движения v.
Плоскость резания — плоскость, касательная к режущей кромке в рассматриваемой точке и перпендикулярная к основной плоскости.
Рабочая плоскость — плоскость, в которой расположены направления скоростей главного движения v и движения подачи vs (рис. 6.2). Скорость результирующего движения резания обозначена ve. При установке резца по центру детали основная плоскость параллельна плоскости основания резца.
Рис. 6.2. Поверхности и плоскости при обработке резцом:
1 и 3 — обрабатываемая и обработанная поверхности; 2 — поверхность резания; 4 и 6 — основная и рабочая плоскости; 5 и 7 — плоскости резания и основания резца
Пространственную конструктивную форму любой детали определяет сочетание различных поверхностей. Для облегчения обработки заготовки конструктор стремится использовать следующие геометрические поверхности: плоские, круговые цилиндрические и конические, шаровые, торовые, геликоидные и др. Любая геометрическая поверхность представляет собой совокупность последовательных положений (следов) одной производящей линии, называемой образующей, движущейся по другой производящей линии, называемой направляющей. Например, для образования круговой цилиндрической поверхности необходимо прямую линию (образующую) перемещать по окружности (направляющей).
При обработке поверхностей на металлорежущих станках образующие и направляющие линии в большинстве случаев являются воображаемыми. Они воспроизводятся во времени комбинацией движений заготовки и инструмента, скорости которых строго согласованы между собой. Движения резания являются также формообразующими движениями. Механическая обработка заготовок деталей машин реализует в основном четыре метода формообразования поверхностей. Рассмотрим их на конкретных примерах.
Заготовками для механических цехов служат прокат (круглый, квадратный, полосовой, трубы и т. д.), поковки, штамповки и отливки. Заготовки, поступающие в механические цехи, имеют припуск на обработку резанием. Припуск зависит от ряда факторов: размеров, формы и конструктивных особенностей изготовляемой детали, вида заготовки, масштабов производства (числа изготавливаемых деталей) и др. Припуск на сторону для штамповок составляет 1,5–7 мм, для поковок — 2,5–20, для отливок (в земляные формы) — 3–30 мм.
К основным методам обработки металлов резанием относятся точение (рис. 6.1а), сверление (рис. 6.1б), фрезерование (рис. 6.1в), строгание (рис. 6.1 г) и шлифование (рис. 6.1д). Из них наиболее распространенным и изученным методом с точки зрения теории резания металлов считается точение, у которого много общего со всеми другими методами механической обработки металлов, поэтому правильное понимание этого процесса облегчает изучение всех других методов обработки резанием.
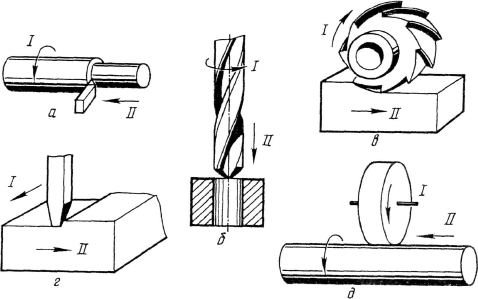
а — точение; б — сверление; в — фрезерование; г — строгание; д — шлифование
I — главное движение; II — движение подачи
Чтобы с заготовки срезать слой металла, необходимо режущему инструменту и заготовке сообщить относительные движения. Инструмент и заготовку устанавливают и закрепляют в рабочих органах станков, обеспечивающих эти относительные движения: в шпинделе, на столе, в револьверной головке и т. д. Движения рабочих органов станков делят на движения резания, установочные и вспомогательные. Движения, которые обеспечивают срезание с заготовки слоя металла или вызывают изменение состояния обработанной поверхности заготовки, называют движениями резания. К ним относят главное движение и движение подачи.
За главное движение принимают то движение, которое определяет скорость деформирования и отделения стружки. За движение подачи принимают то движение, которое обеспечивает непрерывность врезания режущей кромки инструмента в материал заготовки. Эти движения могут быть непрерывными или прерывистыми, а по своему характеру вращательными, поступательными, возвратно-поступательными и т. д. Скорость главного движения обозначают v, величину подачи — s.
Движения, обеспечивающие взаимное расположение инструмента и заготовки для срезания с нее определенного слоя материала, называют установочными. К вспомогательным движениям относят транспортирование заготовки, закрепление заготовок и инструмента, быстрые перемещения рабочих органов станка на холостом ходу, переключение скоростей резания и подачи и т. п.
При токарной обработке (рис. 6.1а) главное движение резания I — вращение обрабатываемой детали, движение подачи II — движение резца. При строгании (рис. 6.1 г) главное движение I — перемещение резца относительно детали или детали относительно резца, что физически равноценно; движение подачи II — перемещение обрабатываемой детали на двойной ход резца в направлении, перпендикулярном к главному движению. При фрезеровании (рис. 6.1в) главное движение I определяется вращением фрезы, а движение II — движением подачи. При сверлении (рис. 6.1б) главное движение I — вращение сверла; движение подачи II — перемещение сверла в осевом направлении. При шлифовании (рис. 6.1д) главное движение I — вращение круга; движение подачи II — продольное или поперечное перемещение детали.
Главное движение по величине значительно больше движения подачи. Вспомогательные движения — установочные перемещения суппортов, задней бабки, поворот резцедержателя, перемещение траверсы и др.
При обработке резанием на детали различают обрабатываемую 1 (рис. 6.2) и обработанную 3 поверхности, поверхность резания 2.
Обрабатываемая поверхность — поверхность, с которой снимается стружка.
Обработанная поверхность — поверхность, полученная после снятия стружки.
Поверхность резания — поверхность, образуемая режущей кромкой резца в результате движений резания. Такая поверхность служит переходной между обработанной и обрабатываемой поверхностями.
Углы режущих инструментов наиболее часто определяют в статической системе координат с началом в рассматриваемой точке режущей кромки резца, ориентированной по направлению скорости главного движения резания. Для этого устанавливают исходные плоскости: основную и рабочую плоскости, плоскость резания.
Основная плоскость — плоскость, проведенная через рассматриваемую точку режущей кромки перпендикулярно к направлению скорости главного движения v.
Плоскость резания — плоскость, касательная к режущей кромке в рассматриваемой точке и перпендикулярная к основной плоскости.
Рабочая плоскость — плоскость, в которой расположены направления скоростей главного движения v и движения подачи vs (рис. 6.2). Скорость результирующего движения резания обозначена ve. При установке резца по центру детали основная плоскость параллельна плоскости основания резца.
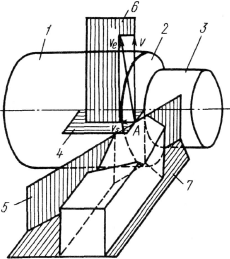
1 и 3 — обрабатываемая и обработанная поверхности; 2 — поверхность резания; 4 и 6 — основная и рабочая плоскости; 5 и 7 — плоскости резания и основания резца
Пространственную конструктивную форму любой детали определяет сочетание различных поверхностей. Для облегчения обработки заготовки конструктор стремится использовать следующие геометрические поверхности: плоские, круговые цилиндрические и конические, шаровые, торовые, геликоидные и др. Любая геометрическая поверхность представляет собой совокупность последовательных положений (следов) одной производящей линии, называемой образующей, движущейся по другой производящей линии, называемой направляющей. Например, для образования круговой цилиндрической поверхности необходимо прямую линию (образующую) перемещать по окружности (направляющей).
При обработке поверхностей на металлорежущих станках образующие и направляющие линии в большинстве случаев являются воображаемыми. Они воспроизводятся во времени комбинацией движений заготовки и инструмента, скорости которых строго согласованы между собой. Движения резания являются также формообразующими движениями. Механическая обработка заготовок деталей машин реализует в основном четыре метода формообразования поверхностей. Рассмотрим их на конкретных примерах.
Конец бесплатного ознакомительного фрагмента