Страница:
Предисловие
Все процессы, связанные с производством и потреблением любых продуктов, утилизацией отходов, непременно содержат операции по перемещению каких-либо предметов в пространстве, по погрузке-разгрузке.
Соблюдению правил безопасного производства специальных работ (земляных, сварочных, строительных и т. п.) посвящено много исследований, и этот вопрос имеет достаточно широкое освещение в литературе.
Необходимость настоящей публикации вызвана прежде всего тем, что процессы, о безопасном осуществлении которых пойдет речь, действительно имеют массовый характер и будут полезны для всех отраслей, разрабатывающих нормы безопасности различных операций. Кроме того, большинство погрузочно-разгрузочных работ, особенно в агропромышленном комплексе, осуществляется с массовыми грузами. Зачастую эта работа однообразная и утомительная. Эти факторы накладывают определенные требования к охране труда при их проведении. Как известно, из-за того что перемещение большинства грузов осуществляется на значительные расстояния (0,1 — 10,0 км) в течение длительного периода времени 60 — 300 дней, сельскохозяйственное производство называют «транспортным поневоле».
По степени механизации погрузочно-разгрузочные работы можно разделить (классифицировать) следующим образом: ручные, механизированные и автоматические.
Ручные работы — перемещение груза осуществляется вручную или с помощью оборудования, управляемого за счет энергии рабочего. Данные виды работ отличаются значительной мышечной активностью.
Механизированно-ручные работы — энергия рабочего используется только для того, чтобы зацепить, отцепить груз, а само перемещение производится краном, транспортером.
Механизированные работы — энергия рабочего используется только для управления энергией самого оборудования.
Автоматические работы — осуществляются без участия человека.
Погрузо-разгрузочное оборудование, устройства, машины имеют свою довольно обширную классификацию (рис. 1).
По сравнению с разгрузкой, погрузка — более трудоемкая операция, так как при этом происходит подъем груза. Для этого создано значительное количество машин, установок. Разгрузка — это, как правило, перемещение с большей высоты на меньшую, естественно, что энергозатрат при этом меньше и количество машин менее разнообразно.
Рис. 1. Классификация погрузочно-разгрузочного оборудования
Соблюдению правил безопасного производства специальных работ (земляных, сварочных, строительных и т. п.) посвящено много исследований, и этот вопрос имеет достаточно широкое освещение в литературе.
Необходимость настоящей публикации вызвана прежде всего тем, что процессы, о безопасном осуществлении которых пойдет речь, действительно имеют массовый характер и будут полезны для всех отраслей, разрабатывающих нормы безопасности различных операций. Кроме того, большинство погрузочно-разгрузочных работ, особенно в агропромышленном комплексе, осуществляется с массовыми грузами. Зачастую эта работа однообразная и утомительная. Эти факторы накладывают определенные требования к охране труда при их проведении. Как известно, из-за того что перемещение большинства грузов осуществляется на значительные расстояния (0,1 — 10,0 км) в течение длительного периода времени 60 — 300 дней, сельскохозяйственное производство называют «транспортным поневоле».
По степени механизации погрузочно-разгрузочные работы можно разделить (классифицировать) следующим образом: ручные, механизированные и автоматические.
Ручные работы — перемещение груза осуществляется вручную или с помощью оборудования, управляемого за счет энергии рабочего. Данные виды работ отличаются значительной мышечной активностью.
Механизированно-ручные работы — энергия рабочего используется только для того, чтобы зацепить, отцепить груз, а само перемещение производится краном, транспортером.
Механизированные работы — энергия рабочего используется только для управления энергией самого оборудования.
Автоматические работы — осуществляются без участия человека.
Погрузо-разгрузочное оборудование, устройства, машины имеют свою довольно обширную классификацию (рис. 1).
По сравнению с разгрузкой, погрузка — более трудоемкая операция, так как при этом происходит подъем груза. Для этого создано значительное количество машин, установок. Разгрузка — это, как правило, перемещение с большей высоты на меньшую, естественно, что энергозатрат при этом меньше и количество машин менее разнообразно.
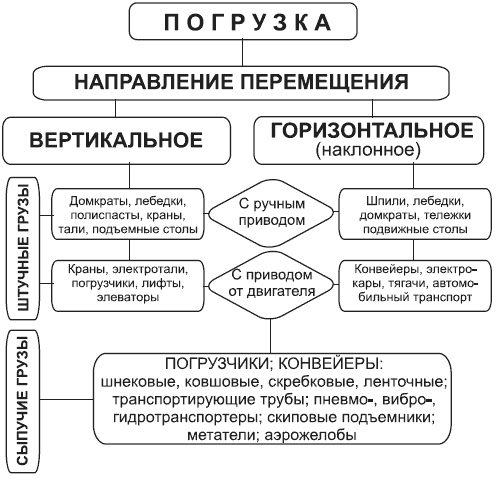
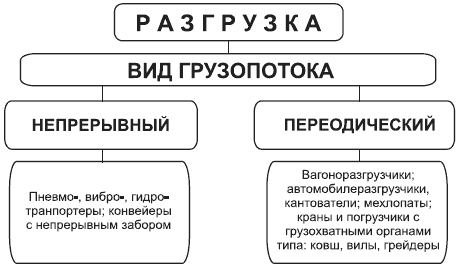
1. Ручная погрузка и разгрузка
Выполнять вручную погрузочно-разгрузочные работы допускается только при небольших объемах работ с грузами незначительной массы.
Для мужчин старше 18 лет допустима работа с грузом массой не более 50 кг, для женщин — не более 10 кг, при перемещении его на расстояние не далее 15 м и высоту до 3 м. Законодательством запрещается привлекать к погрузочно-разгрузочным работам подростков в возрасте до 16 лет. Для подростков мужского пола в возрасте до 18 лет масса переносимого груза не должна превышать 20 кг. Мужчины старше 18 лет могут переносить грузы на носилках на расстояние не более 80 м. При перемещении груза массой более 50 кг операции по подъему груза на спину грузчика и опусканию должны производиться с помощью других рабочих.
При перемещении груза по наклонной плоскости необходимо использовать различные приспособления: сходни, трапы, мостки. В случае подъема по наклонной плоскости на высоту до 1,5 м используют сходни (рис. 1.1, а). При перемещении груза на высоту более 1,5 м трапы оборудуют поручнями (рис. 1.1, б). Ширину сходней, трапов (l) при одностороннем движении делают не менее 0,8 м, двухстороннем — не менее 1,5 м. Уклон установки сходней, трапов должен быть минимальным, не более 1: 3. Расстояние между рабочими, поднимающимися по сходням, должно быть не менее 6 м.
При погрузке-разгрузке барабанов, бочек и т. п. возможно использование слег. Слеги (рис. 1.1, в) делают обычно из круглых бревен диаметром тонкого конца не менее 150 мм. В этом случае на толстом конце бревна укрепляют металлические крючья. А тонкий конусный конец оковывают, окольцовывают листовой сталью толщиной 1,5–2,0 мм.
Все рабочие, исполняющие погрузку-разгрузку, должны быть одеты в спецодежду, рукавицы, а при необходимости использовать индивидуальные средства защиты (очки, противогазы). Одежда и обувь каждого рабочего должны быть соответствующего размера, аккуратно застегнуты и не иметь болтающихся концов завязок.
Рис. 1.1. Сходни (а), трапы (б) и слеги (в).
Для мужчин старше 18 лет допустима работа с грузом массой не более 50 кг, для женщин — не более 10 кг, при перемещении его на расстояние не далее 15 м и высоту до 3 м. Законодательством запрещается привлекать к погрузочно-разгрузочным работам подростков в возрасте до 16 лет. Для подростков мужского пола в возрасте до 18 лет масса переносимого груза не должна превышать 20 кг. Мужчины старше 18 лет могут переносить грузы на носилках на расстояние не более 80 м. При перемещении груза массой более 50 кг операции по подъему груза на спину грузчика и опусканию должны производиться с помощью других рабочих.
При перемещении груза по наклонной плоскости необходимо использовать различные приспособления: сходни, трапы, мостки. В случае подъема по наклонной плоскости на высоту до 1,5 м используют сходни (рис. 1.1, а). При перемещении груза на высоту более 1,5 м трапы оборудуют поручнями (рис. 1.1, б). Ширину сходней, трапов (l) при одностороннем движении делают не менее 0,8 м, двухстороннем — не менее 1,5 м. Уклон установки сходней, трапов должен быть минимальным, не более 1: 3. Расстояние между рабочими, поднимающимися по сходням, должно быть не менее 6 м.
При погрузке-разгрузке барабанов, бочек и т. п. возможно использование слег. Слеги (рис. 1.1, в) делают обычно из круглых бревен диаметром тонкого конца не менее 150 мм. В этом случае на толстом конце бревна укрепляют металлические крючья. А тонкий конусный конец оковывают, окольцовывают листовой сталью толщиной 1,5–2,0 мм.
Все рабочие, исполняющие погрузку-разгрузку, должны быть одеты в спецодежду, рукавицы, а при необходимости использовать индивидуальные средства защиты (очки, противогазы). Одежда и обувь каждого рабочего должны быть соответствующего размера, аккуратно застегнуты и не иметь болтающихся концов завязок.
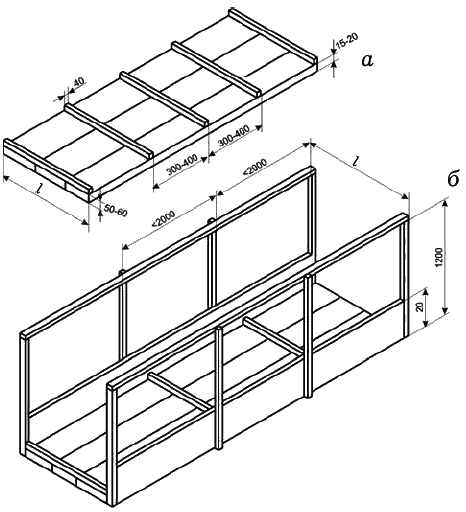
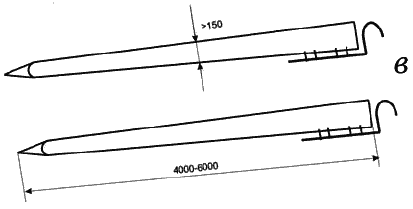
2. Погрузка с использованием простых механизмов
Производство погрузочных и разгрузочных работ зачастую невозможно без использования простых механизмов и устройств с ручным приводом. Это обусловлено и тем, что погрузку (или разгрузку), особенно штучных грузов, приходится осуществлять в тесных, неудобных условиях, внутри складов, зданий, где нельзя применять грузоподъемные или транспортирующие устройства с электроприводом. А в случае если расстояние перемещения груза превышает 15 м, рабочий обязан это сделать только при представлении ему транспортных механизмов или простейших приспособлений для перемещения груза: тачки, тележки, вагонетки (рис. 2.1).
Рис. 2.1. Тележка ручная
Общим требованием, предъявляемым к ручным тележкам всех типов, является их минимальная масса. Центр масс груза должен быть расположен по возможности ниже, ближе к оси колеса, что ослабляет опрокидывающее усилие, действующее на тяговые рукоятки тележки.
Наиболее распространено использование лебедок, талей, полиспастов и домкратов. Эти механизмы функционируют за счет энергии рабочего, компактны и способны развивать усилия до 100 кН. Механизмы в данных устройствах исполнены так, что при этом получается большой выигрыш в силе, а скорости исполнительных органов механизма столь же значимо уменьшаются.
Лебедки. Лебедки предназначены для подъема, опускания, оттягивания висящего оборудования и перетаскивания. По правилам Гостехнадзора лебедки должны обеспечивать надежное удерживание поднятого оборудования. Чаще используют лебедки с барабаном, конструкция которых приведена на рис. 2.2.
Рис. 2.2. Лебедки ручные: а — с барабаном; б — рычажная; 1 — рукоятка; 2 — большое зубчатое колесо; 3 — стяжной болт; 4 — щека; 5 — барабан; 6 — храповое колесо с собачкой; 7, 11 — крюк; 8 — рукоятка прямого хода; 9 — корпус лебедки; 10 — рукоятка обратного хода; 12 — канат; 13 — катушка
Щека 4 на лебедке с барабаном (рис. 2.2, а) скреплена болтами 3. Вращение от рукоятки 1 передается барабану 5 через зубчатые передачи. Поднятый груз удерживается храповым колесом 6. Окружная скорость барабана лебедки незначительна — v ≈ 0,01 м/с. В монтажных работах недопустимо использование лебедок с фрикционными передачами.
Ручные рычажные лебедки (рис. 2.2, б) используют на работах, связанных с подъемом и перемещением оборудования. В корпусе 9 лебедки находится тяговый механизм. Крюком 11 лебедку крепят к перемещаемому элементу, а крюком 7 — к неподвижной опоре якорю. При закреплении лебедки канат 12 сматывается с катушки 13. Канат перемещают сквозь механизм лебедки с помощью рукоятки 8 переднего хода, а возвращают с помощью рукоятки 10 заднего хода.
Рис. 2.3. Закрепления лебедок за колонну, стену и ригель: 1 — лебедка; 2 — колонна; 3 — подкладки; 4 — стена; 5 — ригель; 6 — отводный блок
Рис. 2.4. Якоря: а — свайный; б — горизонтальный; в — винтовой; г — наземный; 1 — свая (бревно); 2 — горизонтальные бревна; 3 — засыпка; 4 — бетонный блок; 5 — винтовая лопасть; 6 — стержень; 7 — упор; 8 — ригель; 9 — шипы
При выполнении работ лебедки должны быть закреплены от смещения. Для этого используют элементы строительных сооружений: колонны (рис. 2.3), ригели, стены или специальные анкерные устройства — якоря. Якоря заглубленные (рис. 2.4, а, б, г) выполняют вертикальными (рис. 2.4, а, в), горизонтальными (рис. 2.4, б). Деревянный якорь из бревна диаметром 180–300 мм забивают на глубину 1,5 м. Такие якоря воспринимают усилие 10–20 кН. Забивка свай — трудоемкая работа, поэтому их применяют ограниченно. Винтовой якорь (рис. 2.4, в) состоит из стержня, на котором установлен шарнирно ригель 8, один конец которого соединен с упором, а к другому крепится тяговый канат. За счет упора 7 на стержень якоря действует только вертикальное усилие. Винтовые якоря применяют при усилии 3, 5, 10 кН, а они могут быть использованы многократно.
Для восприятия усилий, направленных под разным углом, применяют горизонтальный якорь (рис. 2.4, б). Для этого 3–4 бревна скрепляют хомутом, который через косынку связывается с тягой. Для предохранения тяги от смятия устанавливают дополнительное бревно.
В наземном якоре (рис. 2.4, г) к раме приварено несколько шипов, часть из которых может охватывать бетонные блоки, врытые в грунт, а другие могут быть просто заглублены в землю. В случае если грунт неплотный, то засыпают слой крупного песка или щебня. На наземные якоря укладывают железобетонные блоки, в зависимости от количества последних изменяется усилие, которое воспринимается таким якорем. Крепление оттяжки, полиспаста к наземному якорю осуществляют в середине рамы.
Рис. 2.5. Схемы фиксации лебедки
Для подбора анкера и силы тяжести контргруза (железобетонных блоков) выполняют расчет. При определении усилия (F), которое должен обеспечить якорь, препятствующий только горизонтальному смещению лебедки (рис. 2.5, а), используют зависимость:
f — коэффициент трения, равный 0,3–0,5;
FЛg — сила тяжести лебедки;
F — необходимое тяговое усилие.
В случае если необходимо определить массу контргруза, препятствующего опрокидыванию (рис. 2.5, б), пользуются зависимостью:
F0 — сила тяжести контргруза;
k=1,2–2,0 — коэффициент запаса устойчивости.
Тали — это подвесные лебедки, используемые для подъема, удержания, опускания оборудования. В случае если таль устанавливают на тележке, передвигающейся по монорельсу, то это устройство называется тельфер.
В качестве тягового органа у талей используют не канат, а цепь, что позволяет обходиться без барабана и делает подъемный механизм более компактным и легким. По конструкции наиболее распространены червячные и шестеренчатые тали (рис. 2.6). Применение тормоза обязательно как в шестеренчатых, так и червячных талях. Скорость подъема груза у талей незначительна v ≈ 0,01 м/с.
Шпили используют только для горизонтального перемещения (рис. 2.7). Основным элементом этого механизма является небольшой барабан — шпиль.
В качестве тягового органа используется канат, который на шпиле не закрепляется, укладывается рядом в бухту. Канат сцепляется с барабаном возникающей силой трения между поверхностью барабана и несколькими витками.
Необходимый для создания тягового усилия F крутящий момент на валу шпиля определится из выражения:
Fp — усилие рабочего, удерживающего канат от проскальзывания.
Рис. 2.6. Тали: а — шестеренчатые; б — червячные
Рис. 2.7. Шпиль
Имеем F = 2T/(D+0,5dk)+Fp, т. е. для увеличения тягового усилия F выгодно использовать шпили малого диаметра.
Шпили делают вогнутыми для того, чтобы канат под действием сдвигающей силы (F × sin φ) преодолевал силу трения (f × F × cos φ) каната о барабан и устанавливался на минимальном диаметре (φ — угол между касательной к вогнутой кривой и вертикальной осью).
Полиспасты. Полиспасты — наиболее простейшие механизмы подъема. Могут использоваться самостоятельно или как средство, увеличивающее тяговое усилие лебедки, тали (рис. 2.8). Полиспаст — система подвижных и неподвижных блоков, соединенных гибкой связью. Полиспасты запасовывают канатами при расположении блоков в рабочем положении или плашмя на полу.
Рис. 2.8. Примеры использования лебедки с полиспастами
Основной характеристикой полиспастов является кратность (Uп), определяемая как отношение числа ветвей, на которых висит груз (Z), к числу ветвей, наматываемых на барабан (ZH) лебедки. Полиспаст, приведенный на рис. 2.9, в, имеет кратность:
При эксплуатации полиспастов допустимо отклонение сбегающей ветви от оси ручья на угол не более 6°. В противном случае канат может выйти из ручья блока.
Рис. 2.9. Монтажные полиспасты
Домкраты — переносимые, передвижные устройства для подъема, удержания, опускания оборудования. Домкраты некоторых типов обеспечивают и горизонтальное перемещение.
Домкраты по конструктивному исполнению разделяются на винтовые, реечные, гидравлические (рис. 2.10).
Рис. 2.10. Домкраты: а — винтовой; б, в — реечные; г — гидравлический; 1, 7 — стойка; 2 — гайка; 3 — винт; 4, 8 — пята; 5 — рукоятка; 6 — храповик; 9 — цепь; 10, 11, 14 — звездочки; 12 — выдвижная секция; 13 — шестерня; 15 — корпус; 16 — червячное колесо; 17 — червяк; 18 — насос; 19 — поршень
Область применения различных домкратов характеризуется примерно следующей схемой (рис. 2.11).
Рис. 2.11. Область применения домкратов
Домкраты испытывают раз в год, для чего при максимально выдвинутом подъемном устройстве их загружают на 110 % в течение 10 мин. Новые гидравлические домкраты испытывают под нагрузкой в 125 %, при этом через 10 минут падение давления не должно быть более 5 %.
Винтовые домкраты — наиболее простые по конструкции (рис. 2.10). Домкрат состоит из корпуса 1 с закрепленной в нем гайкой 2. Винт 3 с опорной головкой 4 имеет трапецеидальную или прямоугольную резьбу и вращается рукоятью 5 с храповым механизмом 6.
Для перемещения груза с помощью винтового домкрата необходимо приложить усилие на рукоятке, равное:
f — коэффициент трения на торце винта;
dc — средний диаметр опорного торца винта;
d2 — средний диаметр резьбы;
l — длина рукоятки;
α — угол подъема винтовой линии;
φ — угол трения.
Очевидно, что самопроизвольно груз не опустится, в случае если угол подъема винтовой линии будет меньше угла трения. Поэтому для обеспечения самоторможения в винтовых домкратах угол подъема — около 4°, что меньше угла трения: около 6° при f ≈ 0,1.
Однако данное преимущество обуславливает и недостаток винтовых домкратов — низкий КПД (0,3…0,4), который определяется как:
р — шаг винта (путь силы тяжести груза за один оборот винта);
2π×l — длина окружности, описываемая концом рукоятки (путь силы рабочего за один оборот винта).
При работе с винтовыми домкратами следует соблюдать следующие правила:
1) устанавливать домкрат строго под центром груза, так как винт домкрата рассчитан только на центральное сжатие и при неправильной установке может легко согнуться;
2) не увеличивать длину рукоятки домкрата путем надевания на нее отрезков труб или каким-либо другим способом, так как тогда домкрат будет развивать силу большую, чем может выдержать поперечное сечение винта;
3) под домкраты рекомендуется устанавливать прокладки, увеличивающие их опорную поверхность, что обеспечивает надежность работы.
Реечные домкраты выполняются с несколько меньшей грузоподъемностью, чем винтовые. Но минимальная высота, начиная с которой возможен подъем, у таких домкратов — 60–70 мм. Принципиальная схема реечного домкрата и существующие конструктивные решения приведены на рис. 2.10, б, в. Разновидностью реечно-зубчатых домкратов являются цепные домкраты.
Домкрат, показанный на рис. 2.10, в, имеет пустотелую опорную стойку 7 квадратного сечения и выдвижную секцию 12 такого же сечения с грузовой площадкой. Внутри секции к ее верхнему и нижнему концам прикреплена втулочно-роликовая цепь 9, которая огибает холостые 10 и 11 и приводную 14 звездочки привода, смонтированного в корпусе 15. Вращение звездочек 14 сообщается через червячное колесо 16 и червяк 17. В зависимости от направления вращения вала червяка звездочка 14 перемещает цепь, а вместе с ней и выдвижную секцию 12 вверх или вниз. На конце вала червяка имеется хвостовик для установки рукоятки ручного привода. В корпусе реечного домкрата расположена выдвижная зубчатая рейка, на верхнем конце которой установлена головка-подхват, а нижний конец загнут и образует лапу для подъема низко расположенных грузов. Грузоподъемность домкрата при подъеме груза лапой меньше на 40–50 %, чем при подъеме верхним концом. Рейка поднимается и опускается вращением рукоятки 5, которая может быть связана с рейкой одной или несколькими передачами.
Коэффициент полезного действия для реечного домкрата составляет 0,6–0,8 и определяется как:
где s = πdш/u — ход рейки при передаточном отношении uu между вращаемой рабочим рукояткой и валом шестерни, входящей в зацепление с рейкой.
Подъемное усилие реечного домкрата равно:
откуда следует, что для увеличения данного усилия следует уменьшать диаметр шестерни (dш), входящей в зацепление с рейкой. С этой целью число зубьев шестерни zш делают минимальным и равным 4.
Все реечные домкраты по правилам Гостехнадзора должны иметь безопасные рукоятки, т. е. должны иметь устройства, предотвращающие опасное для обслуживающего персонала произвольное вращение рукоятки под действием силы тяжести груза.
К безопасным относится рукоятка, сконструированная по типу дискового грузоупорного тормоза с размыкающимися поверхностями трения, которые замыкаются грузом (рис. 2.12).
Рис. 2.12. Схема безопасной рукоятки лебедки: 1 — диск-втулка; 2 — храповое колесо; 3 — собачка; 4 — диск; 5 — вал; 6 — ручка
На валу 5 закреплена на шпонке резьбовая втулка с диском 1. Второй диск 4 представляет собой гайку с рукояткой 6. Между этими дисками находится храповое колесо с собачкой 3. Храповое колесо свободно сидит на втулке диска 1. Резьба на втулке диска 1 направлена так, что при вращении рукоятки по часовой стрелке (при подъеме груза) гайка перемещается влево и зажимает храповое колесо 2 между дисками 1 и 4. Благодаря соответствующему направлению зубьев храпового колеса диски и храповое колесо могут свободно вращаться при подъеме груза. По окончании подъема груз останавливается, так как храповое колесо удерживается от обратного вращения собачкой 3, а диски 1 и 4 сцеплены с храповым колесом силами трения (грузовой момент как при подъеме, так и при спуске направлен в одну и ту же сторону).
Для спуска груза необходимо вращать рукоятку против часовой стрелки. Так как вал 5 и диск 1 закреплены от осевого смещения, то диск 4 будет перемещаться по резьбе вправо до тех пор, пока момент трения между дисками и храповым колесом станет недостаточным для удержания диска от вращения под действием силы тяжести груза. При этом груз начнет опускаться. Свободное опускание груза продолжается до тех пор, пока угловая скорость диска 1 не превысит угловой скорости вращения рукоятки. Тогда втулка диска 1 опять начнет передвигаться по резьбе и перемещать диск 4 влево, увеличивая момент трения между дисками и храповым колесом и прекращая их относительное перемещение. Это относительное перемещение переходит в непрерывное скольжение дисков 1 и 4 по храповому колесу 2, при котором груз опускается со скоростью, не превышающей соответствующей окружной скорости рукоятки.
Гидравлический домкрат — устройства (рис. 2.10, г), в которых жидкость подается под давлением насосом с ручным приводом и из цилиндра выдвигается поршень, осуществляющий подъем груза. Гидравлические домкраты компактны, плавно поднимают груз, имеют высокий КПД (0,7–0,8). В качестве рабочей жидкости в домкратах используется индустриальное масло 12.
Рис. 2.13. Схема гидравлического домкрата: 1 — насос; 2 — плунжер (поршень); 3 — всасывающий клапан; 4 — нагнетательный клапан; 5 — спускной клапан; 6 — предохранительный клапан; 7 — манометр; 8 — цилиндр домкрата; 9 — основной поршень
Схема гидравлического домкрата приведена на рис. 2.13. Все домкраты имеют всасывающий, нагнетательный и спускной клапаны. Отдельные домкраты могут быть оснащены предохранительным клапаном, манометром для контроля за давлением (или развиваемым усилием). В свое время получили распространение домкраты «Перпетуум» (рис. 2.14), у которых под действием давления жидкости поднимается цилиндр, и домкраты завода «Ленинская кузница», у которых поднимается поршень. Для подъема груза на большую высоту домкратами типа «Перпетуум» необходимо использование брусьев (шпал). Схема работы домкрата показана на рис. 2.15.
Рис. 2.14. Гидравлические домкраты: а — завода «Ленинская кузница», б — «Перпетуум»; 1 — резервуар домкрата; 2 — плунжер; 3 — цилиндр; 4 — поршень; 5 — отверстие для подачи жидкостей под крышку цилиндра; 6 — манжеты; 7 — направляющий шток; 8 — возвратная пружина; 9 — ось рукоятки; 10 — рукоятка; 11 — толкатель плунжера; 12 — ручка для переноса домкрата; 13 — всасывающий клапан; 14 — нагнетательный клапан
В общем случае для подъема груза домкратами на высоту, превышающую их ход, используют способ ступенчатого подъема. Вначале грузовые площадки домкратов взаимодействуют с упорами на грузе. Подъем производится за несколько повторяющихся циклов: первый цикл — под домкраты устанавливают прокладки и аппарат поднимают на ход домкрата; второй цикл — под аппарат подкладывают прокладки из шпал, а поршни домкратов опускают; третий цикл — под домкраты устанавливают новый ряд прокладок и снова поднимают аппарат; четвертый цикл и так далее — последовательно выполняют описанные операции, пока аппарат не окажется на необходимой высоте.
Рис. 2.15. Схема работы домкрата при подъеме на большую высоту
Коэффициент полезного действия гидравлического домкрата определяется как:
где (d/D)²×ln — ход поршня за одно качание рукоятки ручного насоса.
Скорость подъема груза:
k = 0,9–0,95 — коэффициент, учитывающий утечки рабочей жидкости через уплотнения.
Давление жидкости в домкратах обычно в пределах 30–40 МПа, это обусловлено следующим. За счет рукоятки сила, которую прикладывает рабочий, увеличивается на плунжере насоса в l/l1 раз и становится равной Fp×l/l1, при диаметре плунжера d давление жидкости будет:
Если принимать рекомендуемые практикой значения параметров: Fp = 150…200 Н; l = 200…400 мм; d = 10…200 мм;
l1=l/(15…20), то получим p = 10…40 МПа.
Правила эксплуатации гидравлических домкратов:
1) домкраты следует устанавливать на плотное основание с тем, чтобы при подъеме не могло возникнуть перекосов, которые приводят к заеданию поршня;
2) для предотвращения аварий в случае внезапного оседания домкрата или прорыва манжеты между неподвижной частью домкрата и поднимаемым грузом следует укладывать специальные прокладки (полукольца);
3) не разрешается работать домкратом с неисправным манометром.
Специальные средства. Производство работ зачастую невозможно при использовании только штатных инвентарных средств и приспособлений. Из-за стесненных условий, отсутствия более совершенных грузоподъемных механизмов используют средства, изготовленные обычно на монтажной площадке.
Монтажные треноги (рис. 2.16) могут быть использованы при одноразовой погрузке или разгрузке упакованного груза или оборудования. Необходимые расчеты проводятся в следующей последовательности. Определяют:
Высоту ноги треноги H = (hФ + hЗ + ho + hC + hП + hОГ)/cos δ,
где hОГ ≈ 0,5–1,0 м — высота оголовка треноги;
hП — высота полиспаста в стянутом состоянии;
hС — высота строп;
hО — высота оборудования;
hЗ ≈ 0,5 м — запас высоты;
hФ — высота рампы.
Рис. 2.16. Монтаж оборудования на подготовленный фундамент
Усилие, сжимающее ногу треноги
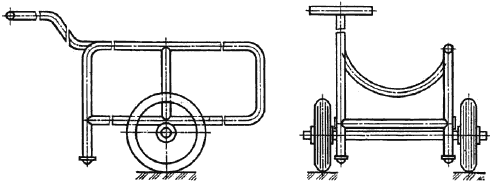
Общим требованием, предъявляемым к ручным тележкам всех типов, является их минимальная масса. Центр масс груза должен быть расположен по возможности ниже, ближе к оси колеса, что ослабляет опрокидывающее усилие, действующее на тяговые рукоятки тележки.
Наиболее распространено использование лебедок, талей, полиспастов и домкратов. Эти механизмы функционируют за счет энергии рабочего, компактны и способны развивать усилия до 100 кН. Механизмы в данных устройствах исполнены так, что при этом получается большой выигрыш в силе, а скорости исполнительных органов механизма столь же значимо уменьшаются.
Лебедки. Лебедки предназначены для подъема, опускания, оттягивания висящего оборудования и перетаскивания. По правилам Гостехнадзора лебедки должны обеспечивать надежное удерживание поднятого оборудования. Чаще используют лебедки с барабаном, конструкция которых приведена на рис. 2.2.
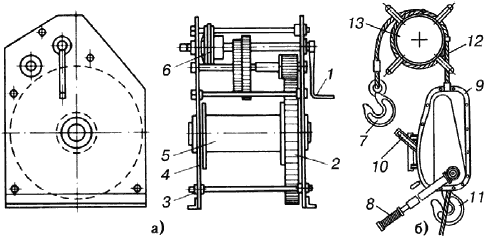
Щека 4 на лебедке с барабаном (рис. 2.2, а) скреплена болтами 3. Вращение от рукоятки 1 передается барабану 5 через зубчатые передачи. Поднятый груз удерживается храповым колесом 6. Окружная скорость барабана лебедки незначительна — v ≈ 0,01 м/с. В монтажных работах недопустимо использование лебедок с фрикционными передачами.
Ручные рычажные лебедки (рис. 2.2, б) используют на работах, связанных с подъемом и перемещением оборудования. В корпусе 9 лебедки находится тяговый механизм. Крюком 11 лебедку крепят к перемещаемому элементу, а крюком 7 — к неподвижной опоре якорю. При закреплении лебедки канат 12 сматывается с катушки 13. Канат перемещают сквозь механизм лебедки с помощью рукоятки 8 переднего хода, а возвращают с помощью рукоятки 10 заднего хода.

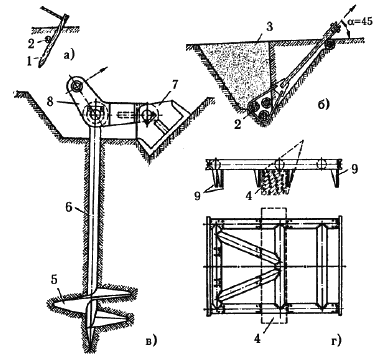
При выполнении работ лебедки должны быть закреплены от смещения. Для этого используют элементы строительных сооружений: колонны (рис. 2.3), ригели, стены или специальные анкерные устройства — якоря. Якоря заглубленные (рис. 2.4, а, б, г) выполняют вертикальными (рис. 2.4, а, в), горизонтальными (рис. 2.4, б). Деревянный якорь из бревна диаметром 180–300 мм забивают на глубину 1,5 м. Такие якоря воспринимают усилие 10–20 кН. Забивка свай — трудоемкая работа, поэтому их применяют ограниченно. Винтовой якорь (рис. 2.4, в) состоит из стержня, на котором установлен шарнирно ригель 8, один конец которого соединен с упором, а к другому крепится тяговый канат. За счет упора 7 на стержень якоря действует только вертикальное усилие. Винтовые якоря применяют при усилии 3, 5, 10 кН, а они могут быть использованы многократно.
Для восприятия усилий, направленных под разным углом, применяют горизонтальный якорь (рис. 2.4, б). Для этого 3–4 бревна скрепляют хомутом, который через косынку связывается с тягой. Для предохранения тяги от смятия устанавливают дополнительное бревно.
В наземном якоре (рис. 2.4, г) к раме приварено несколько шипов, часть из которых может охватывать бетонные блоки, врытые в грунт, а другие могут быть просто заглублены в землю. В случае если грунт неплотный, то засыпают слой крупного песка или щебня. На наземные якоря укладывают железобетонные блоки, в зависимости от количества последних изменяется усилие, которое воспринимается таким якорем. Крепление оттяжки, полиспаста к наземному якорю осуществляют в середине рамы.
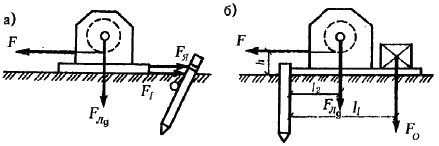
Для подбора анкера и силы тяжести контргруза (железобетонных блоков) выполняют расчет. При определении усилия (F), которое должен обеспечить якорь, препятствующий только горизонтальному смещению лебедки (рис. 2.5, а), используют зависимость:
где F1 — сила трения лебедки об опорную поверхность;FЯ = F — F1 = F — FЛg × f
f — коэффициент трения, равный 0,3–0,5;
FЛg — сила тяжести лебедки;
F — необходимое тяговое усилие.
В случае если необходимо определить массу контргруза, препятствующего опрокидыванию (рис. 2.5, б), пользуются зависимостью:
где h, l1, l2 — плечи усилий (рис. 2.5, б);m0 = F0 / g = ((Fh — FЛgl2)k) / gl1
F0 — сила тяжести контргруза;
k=1,2–2,0 — коэффициент запаса устойчивости.
Тали — это подвесные лебедки, используемые для подъема, удержания, опускания оборудования. В случае если таль устанавливают на тележке, передвигающейся по монорельсу, то это устройство называется тельфер.
В качестве тягового органа у талей используют не канат, а цепь, что позволяет обходиться без барабана и делает подъемный механизм более компактным и легким. По конструкции наиболее распространены червячные и шестеренчатые тали (рис. 2.6). Применение тормоза обязательно как в шестеренчатых, так и червячных талях. Скорость подъема груза у талей незначительна v ≈ 0,01 м/с.
Шпили используют только для горизонтального перемещения (рис. 2.7). Основным элементом этого механизма является небольшой барабан — шпиль.
В качестве тягового органа используется канат, который на шпиле не закрепляется, укладывается рядом в бухту. Канат сцепляется с барабаном возникающей силой трения между поверхностью барабана и несколькими витками.
Необходимый для создания тягового усилия F крутящий момент на валу шпиля определится из выражения:
где D, dk — диаметр шпиля, каната (рис. 2.7);T = F((D+0,5dk)/2) — Fp((D+0,5dk)/2) = (F-F0)(D+0,5dk)/2
Fp — усилие рабочего, удерживающего канат от проскальзывания.
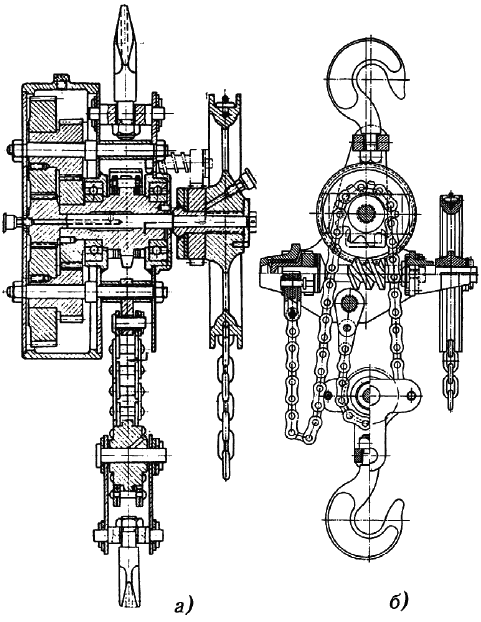
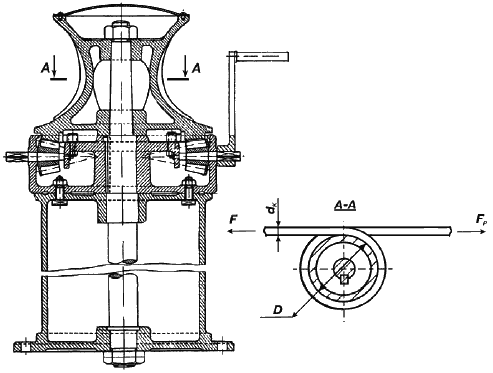
Имеем F = 2T/(D+0,5dk)+Fp, т. е. для увеличения тягового усилия F выгодно использовать шпили малого диаметра.
Шпили делают вогнутыми для того, чтобы канат под действием сдвигающей силы (F × sin φ) преодолевал силу трения (f × F × cos φ) каната о барабан и устанавливался на минимальном диаметре (φ — угол между касательной к вогнутой кривой и вертикальной осью).
Полиспасты. Полиспасты — наиболее простейшие механизмы подъема. Могут использоваться самостоятельно или как средство, увеличивающее тяговое усилие лебедки, тали (рис. 2.8). Полиспаст — система подвижных и неподвижных блоков, соединенных гибкой связью. Полиспасты запасовывают канатами при расположении блоков в рабочем положении или плашмя на полу.
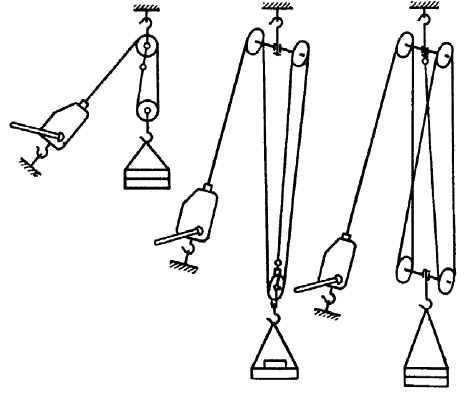
Основной характеристикой полиспастов является кратность (Uп), определяемая как отношение числа ветвей, на которых висит груз (Z), к числу ветвей, наматываемых на барабан (ZH) лебедки. Полиспаст, приведенный на рис. 2.9, в, имеет кратность:
Усилие, действующее на крепление всего верхнего неподвижного блока (рис. 2.9, б), определяется как FБ =Fg +FЛ, где FЛ — усилие на лебедку.Uп = Z / ZН = 6/1 = 6
При эксплуатации полиспастов допустимо отклонение сбегающей ветви от оси ручья на угол не более 6°. В противном случае канат может выйти из ручья блока.
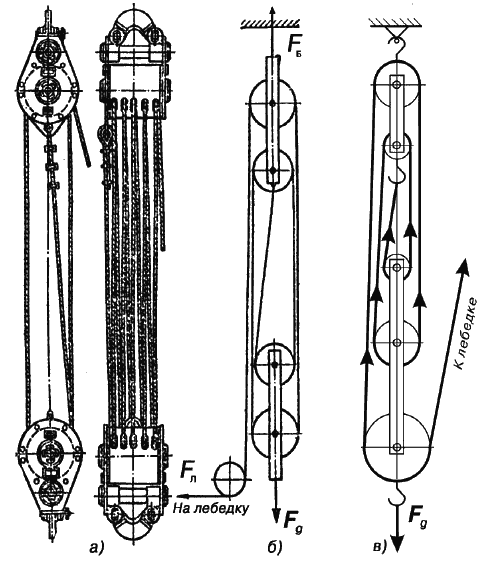
Домкраты — переносимые, передвижные устройства для подъема, удержания, опускания оборудования. Домкраты некоторых типов обеспечивают и горизонтальное перемещение.
Домкраты по конструктивному исполнению разделяются на винтовые, реечные, гидравлические (рис. 2.10).
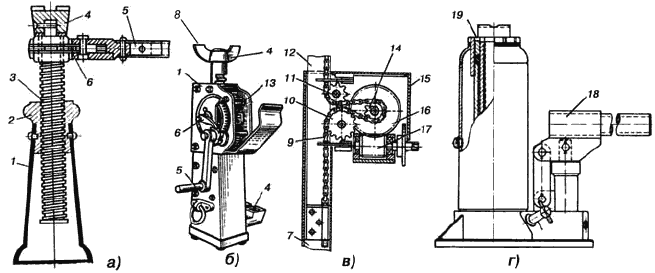
Область применения различных домкратов характеризуется примерно следующей схемой (рис. 2.11).
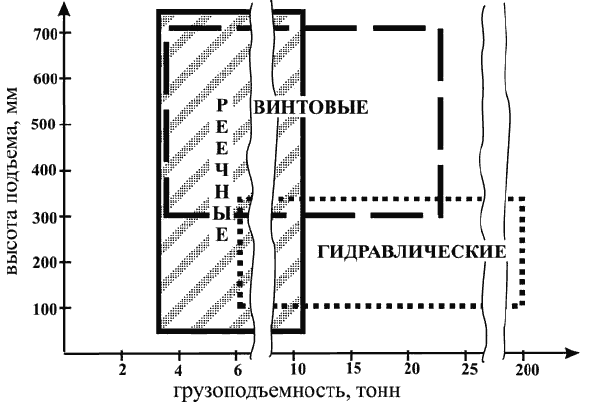
Домкраты испытывают раз в год, для чего при максимально выдвинутом подъемном устройстве их загружают на 110 % в течение 10 мин. Новые гидравлические домкраты испытывают под нагрузкой в 125 %, при этом через 10 минут падение давления не должно быть более 5 %.
Винтовые домкраты — наиболее простые по конструкции (рис. 2.10). Домкрат состоит из корпуса 1 с закрепленной в нем гайкой 2. Винт 3 с опорной головкой 4 имеет трапецеидальную или прямоугольную резьбу и вращается рукоятью 5 с храповым механизмом 6.
Для перемещения груза с помощью винтового домкрата необходимо приложить усилие на рукоятке, равное:
где Fg — сила тяжести груза;Fp = (Fg[f × dc + d2 × tg(α-φ)]) / l
f — коэффициент трения на торце винта;
dc — средний диаметр опорного торца винта;
d2 — средний диаметр резьбы;
l — длина рукоятки;
α — угол подъема винтовой линии;
φ — угол трения.
Очевидно, что самопроизвольно груз не опустится, в случае если угол подъема винтовой линии будет меньше угла трения. Поэтому для обеспечения самоторможения в винтовых домкратах угол подъема — около 4°, что меньше угла трения: около 6° при f ≈ 0,1.
Однако данное преимущество обуславливает и недостаток винтовых домкратов — низкий КПД (0,3…0,4), который определяется как:
где АП, АЗ — полезная, затраченная работа при подъеме груза;η=АП-АЗ=(Fg×p)/Fp×2π×l
р — шаг винта (путь силы тяжести груза за один оборот винта);
2π×l — длина окружности, описываемая концом рукоятки (путь силы рабочего за один оборот винта).
При работе с винтовыми домкратами следует соблюдать следующие правила:
1) устанавливать домкрат строго под центром груза, так как винт домкрата рассчитан только на центральное сжатие и при неправильной установке может легко согнуться;
2) не увеличивать длину рукоятки домкрата путем надевания на нее отрезков труб или каким-либо другим способом, так как тогда домкрат будет развивать силу большую, чем может выдержать поперечное сечение винта;
3) под домкраты рекомендуется устанавливать прокладки, увеличивающие их опорную поверхность, что обеспечивает надежность работы.
Реечные домкраты выполняются с несколько меньшей грузоподъемностью, чем винтовые. Но минимальная высота, начиная с которой возможен подъем, у таких домкратов — 60–70 мм. Принципиальная схема реечного домкрата и существующие конструктивные решения приведены на рис. 2.10, б, в. Разновидностью реечно-зубчатых домкратов являются цепные домкраты.
Домкрат, показанный на рис. 2.10, в, имеет пустотелую опорную стойку 7 квадратного сечения и выдвижную секцию 12 такого же сечения с грузовой площадкой. Внутри секции к ее верхнему и нижнему концам прикреплена втулочно-роликовая цепь 9, которая огибает холостые 10 и 11 и приводную 14 звездочки привода, смонтированного в корпусе 15. Вращение звездочек 14 сообщается через червячное колесо 16 и червяк 17. В зависимости от направления вращения вала червяка звездочка 14 перемещает цепь, а вместе с ней и выдвижную секцию 12 вверх или вниз. На конце вала червяка имеется хвостовик для установки рукоятки ручного привода. В корпусе реечного домкрата расположена выдвижная зубчатая рейка, на верхнем конце которой установлена головка-подхват, а нижний конец загнут и образует лапу для подъема низко расположенных грузов. Грузоподъемность домкрата при подъеме груза лапой меньше на 40–50 %, чем при подъеме верхним концом. Рейка поднимается и опускается вращением рукоятки 5, которая может быть связана с рейкой одной или несколькими передачами.
Коэффициент полезного действия для реечного домкрата составляет 0,6–0,8 и определяется как:

Подъемное усилие реечного домкрата равно:
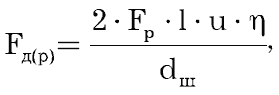
Все реечные домкраты по правилам Гостехнадзора должны иметь безопасные рукоятки, т. е. должны иметь устройства, предотвращающие опасное для обслуживающего персонала произвольное вращение рукоятки под действием силы тяжести груза.
К безопасным относится рукоятка, сконструированная по типу дискового грузоупорного тормоза с размыкающимися поверхностями трения, которые замыкаются грузом (рис. 2.12).
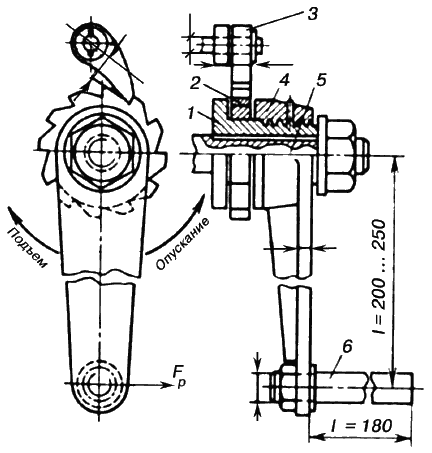
На валу 5 закреплена на шпонке резьбовая втулка с диском 1. Второй диск 4 представляет собой гайку с рукояткой 6. Между этими дисками находится храповое колесо с собачкой 3. Храповое колесо свободно сидит на втулке диска 1. Резьба на втулке диска 1 направлена так, что при вращении рукоятки по часовой стрелке (при подъеме груза) гайка перемещается влево и зажимает храповое колесо 2 между дисками 1 и 4. Благодаря соответствующему направлению зубьев храпового колеса диски и храповое колесо могут свободно вращаться при подъеме груза. По окончании подъема груз останавливается, так как храповое колесо удерживается от обратного вращения собачкой 3, а диски 1 и 4 сцеплены с храповым колесом силами трения (грузовой момент как при подъеме, так и при спуске направлен в одну и ту же сторону).
Для спуска груза необходимо вращать рукоятку против часовой стрелки. Так как вал 5 и диск 1 закреплены от осевого смещения, то диск 4 будет перемещаться по резьбе вправо до тех пор, пока момент трения между дисками и храповым колесом станет недостаточным для удержания диска от вращения под действием силы тяжести груза. При этом груз начнет опускаться. Свободное опускание груза продолжается до тех пор, пока угловая скорость диска 1 не превысит угловой скорости вращения рукоятки. Тогда втулка диска 1 опять начнет передвигаться по резьбе и перемещать диск 4 влево, увеличивая момент трения между дисками и храповым колесом и прекращая их относительное перемещение. Это относительное перемещение переходит в непрерывное скольжение дисков 1 и 4 по храповому колесу 2, при котором груз опускается со скоростью, не превышающей соответствующей окружной скорости рукоятки.
Гидравлический домкрат — устройства (рис. 2.10, г), в которых жидкость подается под давлением насосом с ручным приводом и из цилиндра выдвигается поршень, осуществляющий подъем груза. Гидравлические домкраты компактны, плавно поднимают груз, имеют высокий КПД (0,7–0,8). В качестве рабочей жидкости в домкратах используется индустриальное масло 12.
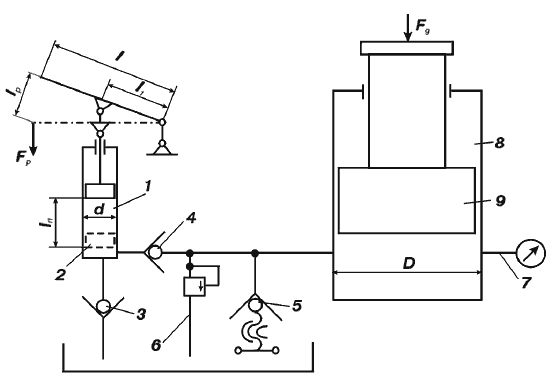
Схема гидравлического домкрата приведена на рис. 2.13. Все домкраты имеют всасывающий, нагнетательный и спускной клапаны. Отдельные домкраты могут быть оснащены предохранительным клапаном, манометром для контроля за давлением (или развиваемым усилием). В свое время получили распространение домкраты «Перпетуум» (рис. 2.14), у которых под действием давления жидкости поднимается цилиндр, и домкраты завода «Ленинская кузница», у которых поднимается поршень. Для подъема груза на большую высоту домкратами типа «Перпетуум» необходимо использование брусьев (шпал). Схема работы домкрата показана на рис. 2.15.
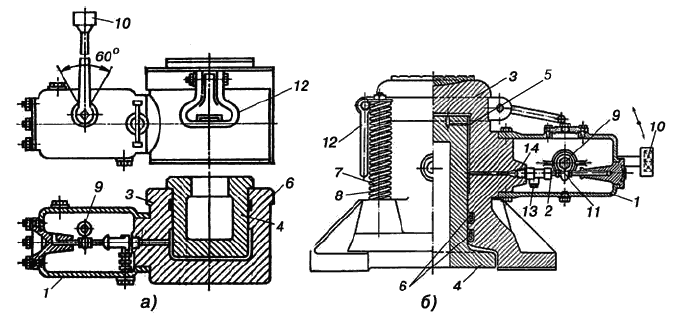
В общем случае для подъема груза домкратами на высоту, превышающую их ход, используют способ ступенчатого подъема. Вначале грузовые площадки домкратов взаимодействуют с упорами на грузе. Подъем производится за несколько повторяющихся циклов: первый цикл — под домкраты устанавливают прокладки и аппарат поднимают на ход домкрата; второй цикл — под аппарат подкладывают прокладки из шпал, а поршни домкратов опускают; третий цикл — под домкраты устанавливают новый ряд прокладок и снова поднимают аппарат; четвертый цикл и так далее — последовательно выполняют описанные операции, пока аппарат не окажется на необходимой высоте.
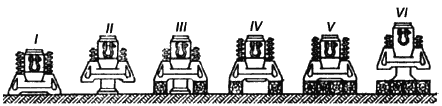
Коэффициент полезного действия гидравлического домкрата определяется как:
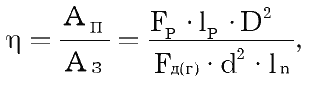
где (d/D)²×ln — ход поршня за одно качание рукоятки ручного насоса.
Скорость подъема груза:
где n — количество качаний рукоятки (n ≈ 20–30 раз в минуту);v=k×n×(d/D)²×ln
k = 0,9–0,95 — коэффициент, учитывающий утечки рабочей жидкости через уплотнения.
Давление жидкости в домкратах обычно в пределах 30–40 МПа, это обусловлено следующим. За счет рукоятки сила, которую прикладывает рабочий, увеличивается на плунжере насоса в l/l1 раз и становится равной Fp×l/l1, при диаметре плунжера d давление жидкости будет:
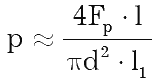
Если принимать рекомендуемые практикой значения параметров: Fp = 150…200 Н; l = 200…400 мм; d = 10…200 мм;
l1=l/(15…20), то получим p = 10…40 МПа.
Правила эксплуатации гидравлических домкратов:
1) домкраты следует устанавливать на плотное основание с тем, чтобы при подъеме не могло возникнуть перекосов, которые приводят к заеданию поршня;
2) для предотвращения аварий в случае внезапного оседания домкрата или прорыва манжеты между неподвижной частью домкрата и поднимаемым грузом следует укладывать специальные прокладки (полукольца);
3) не разрешается работать домкратом с неисправным манометром.
Специальные средства. Производство работ зачастую невозможно при использовании только штатных инвентарных средств и приспособлений. Из-за стесненных условий, отсутствия более совершенных грузоподъемных механизмов используют средства, изготовленные обычно на монтажной площадке.
Монтажные треноги (рис. 2.16) могут быть использованы при одноразовой погрузке или разгрузке упакованного груза или оборудования. Необходимые расчеты проводятся в следующей последовательности. Определяют:
Высоту ноги треноги H = (hФ + hЗ + ho + hC + hП + hОГ)/cos δ,
где hОГ ≈ 0,5–1,0 м — высота оголовка треноги;
hП — высота полиспаста в стянутом состоянии;
hС — высота строп;
hО — высота оборудования;
hЗ ≈ 0,5 м — запас высоты;
hФ — высота рампы.
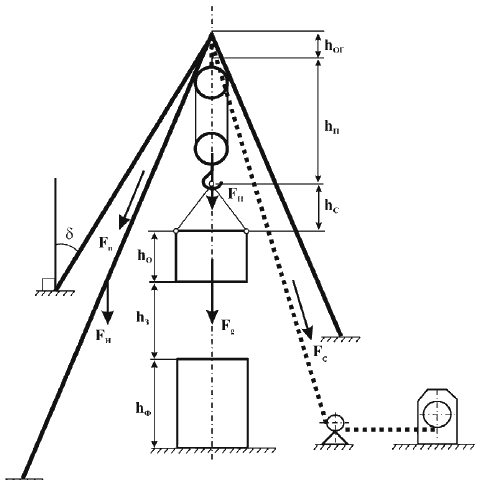
Усилие, сжимающее ногу треноги