Страница:
Устройство трубчатого колодца
Устройство трубчатого колодца рассмотрим на примере сравнительно сложного колодца, типичного для северной части Московской области, где существуют многометровые по толщине валунно-галечниковые отложения. Камни этих отложений, плотно «упакованные» крепким суглинком, представляют исключительную трудность для проходки скважины самодельным инструментом и с помощью самодельного оборудования. Причем скважину приходится бурить на глубину 20–50 м. Но все эти трудности преодолимы, и в Подмосковье построен «самостроем» и действует не один трубчатый колодец.
Скважину для такого трубчатого колодца (рис. 17) стараются сначала сделать возможно большего диаметра, обычно 300–350 мм. Поскольку камни лежат сверху, под двухметровым слоем глины, через такую скважину иногда легче поднять камень на поверхность, нежели дробить его в забое. Обсадную трубу для этой первой скважины делают из какого-либо подручного материала, даже из досок или из кровельной жести. После проходки валунно-галечниковых отложений скважину начинают бурить под основную обсадную трубу.
Обсадную трубу нижним концом опускают до верхней части водоносного слоя, а ниже помещают еще одну трубу – фильтр с отстойником.
В зависимости от глубины залегания водоносного слоя, его строения и характера вышележащих пород трубчатый колодец может отличаться от приведенного на рис. 17 устройством водоприемной части, а также иметь только одну обсадную трубу.
В конструкцию некоторых трубчатых колодцев входят также детали для подключения водоподъемных насосов.
Трубчатый колодец, если он правильно построен и грамотно обслуживается, обеспечит водоснабжение приусадебного участка не хуже шахтного и не уступит ему в долговечности. К тому же он совершенно не пропускает поверхностные загрязнения при условии, что стыки обсадной трубы плотные и вода в нем не застаивается из-за малого объема водоприемной части. Этому способствует также и то, что в него не опускают обычное ведро, а воду поднимают насосом. Используя простейшее бурильное оборудование при благоприятных геологических условиях, трубчатый колодец часто можно построить быстрее (всего за 2–3 дня и даже за несколько часов) и на большую глубину, чем шахтный. Его сравнительно легко построить, скажем, глубиной 25–30 м, 50 м и более. Но все это только в том случае, когда породы, которые надо пройти скважиной, имеют, как говорят, хорошую буримость.
Рис. 17. Устройство трубчатого колодце при большом количестве валунов: 1 – вспомогательная обсадная труба; 2 – основная обсадная труба; 3 – муфта; 4 – сальник; 5 – сетка; 6 – отстойник; 7 – пробка
Горных пород, слагающих земную кору, великое множество, но для процесса бурения важна не их структура, а такие характеристики, как плотность, твердость, устойчивость. Исходя из этого все породы по буримости можно разбить условно на три группы: пластичные, способные резаться и давать стружку; твердые, которые могут только дробиться и раскалываться; сыпуче-плывучие, отличающиеся неустойчивостью, способностью оползать, осыпаться и заполнять пробуренную в них скважину. Практика бурения выработала соответственно и три типа рабочих буровых инструментов.
Поэтому, прежде чем начать строительство трубчатого колодца, надо собрать наивозможно полные сведения о характере горных пород, которые придется пройти, чтобы достичь водоносный горизонт. Значительно усложняют дело твердые каменные слои или валунно-галечниковые отложения, особенно когда они залегают па глубине 10 м и более. Эти породы представляют грозное препятствие, пройти их с помощью самодельного инструмента исключительно трудно. И для того чтобы пробиться через такие породы, понадобятся более серьезное оборудование и инструмент. Советуем сначала прочитать все, что написано здесь о трубчатых колодцах, а потом еще раз хорошенько взвесить, стоит ли «городить» такое оборудование и пробиваться скважиной через каменный пояс. Но легче ли построить шахтный колодец?
Скважину для такого трубчатого колодца (рис. 17) стараются сначала сделать возможно большего диаметра, обычно 300–350 мм. Поскольку камни лежат сверху, под двухметровым слоем глины, через такую скважину иногда легче поднять камень на поверхность, нежели дробить его в забое. Обсадную трубу для этой первой скважины делают из какого-либо подручного материала, даже из досок или из кровельной жести. После проходки валунно-галечниковых отложений скважину начинают бурить под основную обсадную трубу.
Обсадную трубу нижним концом опускают до верхней части водоносного слоя, а ниже помещают еще одну трубу – фильтр с отстойником.
В зависимости от глубины залегания водоносного слоя, его строения и характера вышележащих пород трубчатый колодец может отличаться от приведенного на рис. 17 устройством водоприемной части, а также иметь только одну обсадную трубу.
В конструкцию некоторых трубчатых колодцев входят также детали для подключения водоподъемных насосов.
Трубчатый колодец, если он правильно построен и грамотно обслуживается, обеспечит водоснабжение приусадебного участка не хуже шахтного и не уступит ему в долговечности. К тому же он совершенно не пропускает поверхностные загрязнения при условии, что стыки обсадной трубы плотные и вода в нем не застаивается из-за малого объема водоприемной части. Этому способствует также и то, что в него не опускают обычное ведро, а воду поднимают насосом. Используя простейшее бурильное оборудование при благоприятных геологических условиях, трубчатый колодец часто можно построить быстрее (всего за 2–3 дня и даже за несколько часов) и на большую глубину, чем шахтный. Его сравнительно легко построить, скажем, глубиной 25–30 м, 50 м и более. Но все это только в том случае, когда породы, которые надо пройти скважиной, имеют, как говорят, хорошую буримость.
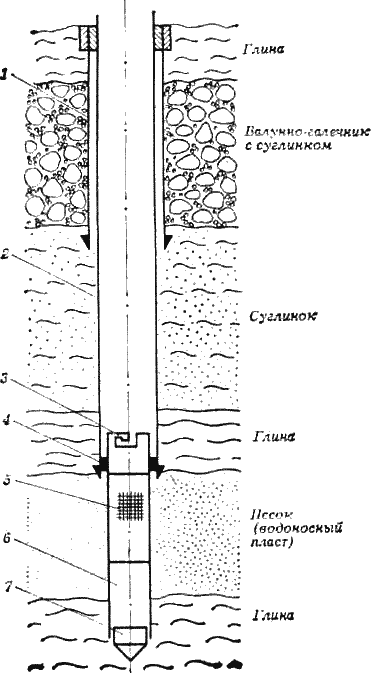
Горных пород, слагающих земную кору, великое множество, но для процесса бурения важна не их структура, а такие характеристики, как плотность, твердость, устойчивость. Исходя из этого все породы по буримости можно разбить условно на три группы: пластичные, способные резаться и давать стружку; твердые, которые могут только дробиться и раскалываться; сыпуче-плывучие, отличающиеся неустойчивостью, способностью оползать, осыпаться и заполнять пробуренную в них скважину. Практика бурения выработала соответственно и три типа рабочих буровых инструментов.
Поэтому, прежде чем начать строительство трубчатого колодца, надо собрать наивозможно полные сведения о характере горных пород, которые придется пройти, чтобы достичь водоносный горизонт. Значительно усложняют дело твердые каменные слои или валунно-галечниковые отложения, особенно когда они залегают па глубине 10 м и более. Эти породы представляют грозное препятствие, пройти их с помощью самодельного инструмента исключительно трудно. И для того чтобы пробиться через такие породы, понадобятся более серьезное оборудование и инструмент. Советуем сначала прочитать все, что написано здесь о трубчатых колодцах, а потом еще раз хорошенько взвесить, стоит ли «городить» такое оборудование и пробиваться скважиной через каменный пояс. Но легче ли построить шахтный колодец?
Абиссинский трубчатый колодец
Когда твердые (каменные) породы отсутствуют или встречаются в небольшом количестве местами, локально, а водоносный пласт состоит из рыхлых зернистых пород (песок средней крупности, смесь песка с галькой) и находится на глубине не более 7 м, проще всего сделать так называемый абиссинский трубчатый забивной колодец.
Очень интересные сведения об этом колодце можно почерпнуть в старой литературе. Вот выдержка из работы К. И. Маслянникова «О земляном бураве, как средстве отыскания мест для колодцев, и об абиссинском колодце»: «Абиссинский (или нортоновский) колодец, этот отличный снаряд, почему-то, к сожалению, забыт в практике и в специальной печати. Абиссинские колодцы наделали вначале своего появления немало шуму в Европе после английской экспедиции в Абиссинии, где сослужили хорошую службу при отыскании воды. Этот шум дошел и до нас, и колодцы появились в наших складах, но вскоре были забыты. Главная часть абиссинского колодца – наконечник из трубы внутренним диаметром 1,25, 1,5 и 2 дюйма и состоит из соответственно продырявленной газовой трубки вроде фильтра и снабженного на конце копьевидным утолщением, а внутри – клапаном в виде шарика (рис. 18). Следующая принадлежность – копер (легкий железный треножник) и баба. Когда желают получить воду в данном месте, устанавливают треножник, навинчивают наконечник на газовую трубу, на которую надевают бабу, и бабой заколачивают трубу в землю. Абиссинский колодец испытывался в 1869 г. возле Царского Села в нескольких местах и с большим успехом. Места избирались каждый раз или на основании опытов местных жителей, или по общим гидротехническим соображениям.
Рис. 18. Абиссинский колодец
Несмотря на то что геологические условия Царского Села очень неблагоприятны для такого рода испытаний, так как там слои известнякового камня залегают близко от поверхности земли, при помощи абиссинского колодца удалось получить свежую и холодную воду в двух местах из пяти. В трех местах залегающий близко слой известняка заставлял прекращать работу в самом начале, причем вбитый конец абиссинского колодца легко выколачивался и затем весь прибор переносился на другое место. В других двух местах найдены были лучшие условия. Так, в одном первое колено было вколочено в 10 минут на глубину 10 футов и вода показалась в трубке с уровнем в 3 фута… На конец трубки был навинчен насос, который давал сначала грязную воду, а затем, примерно через пол часа, довольно чистую, в количестве 1 ведра в минуту. В последнем из выбранных для опыта пунктов были достигнуты наиболее интересные результаты. Хотя верхние слои почвы оказались переполненными крупными камнями и с прослойками из крепкой глины, тем не менее достоинство абиссинского колодца выказалось в значительной степени! Через 20 минут на глубине 2 сажени [1 сажень – 2,1333 м.] колодец был установлен и давал воду в количестве 1,5 ведра в минуту, которая сделалась через 0,25 часа светлою, годною для питья. Снятие абиссинского колодца в этом последнем случае потребовало еще меньше времени, чем его установка».
В этой выдержке очень образно и ярко, живым русским языком описаны простота и достоинства абиссинского колодца, в частности, отмечена быстрота установки его и снятия. Последнее определяет его ценность для временного водоснабжения в полевых условиях. Однако в первозданном виде абиссинский колодец имеет некоторые недостатки: примитивный фильтр – просто перфорированная трубка (то есть трубка с мелкими отверстиями); наибольшая глубина подъема воды всего – 7 м. Последнее объясняется конструкцией всасывающего насоса, поднимающего воду только в результате разряжения, создаваемого в трубе, а оно, как известно, не может теоретически поднять столб воды выше 10 м. Вот практически и получается – 7 м.
В настоящее время этот колодец известен, пожалуй, только специалистам.
При желании абиссинский колодец нетрудно сделать с сетчатым фильтром. Устройство и технология изготовления таких фильтров приведены ниже в разделах «Водоприемная часть трубчатых колодцев» и «Водоприемники из трубчатых колодцев».
Подъем воды с глубины более 7 м может быть осуществлен с помощью погружного насоса или эрлифта, описанных в разделе «Водоприемники из трубчатых колодцев».
В журнале «Лесное хозяйство» (1959, № 4) С. И. Дундиковым приведено описание упрощенной технологии забивки абиссинского колодца. Для этого на выбранном месте для колодца роют шахту размерами 0,8×0,8×1 м. Затем, присоединив к фильтру трубу, на нее свободно надевают бабу массой 25–30 кг. На расстоянии 1 м от фильтра на трубе укрепляют болтами стальной хомут – подбабок, состоящий из двух половин, а выше его на 1–1,5 м устанавливают второй хомут с двумя блоками (рис. 19).
Поставив в центре шахты подготовленную для забивки трубу, шахту заполняют грунтом и утрамбовывают его. После этого забивают абиссинский колодец, поднимая бабу за веревки. Падая, баба ударяет по нижнему хомуту и заглубляет трубу. По мере заглубления колодца подбабок и хомут с блоками передвигают вверх по трубе. Заглубив первую трубу, навинчивают следующую и т. д. В процессе забивки проверяют, не появилась ли вода в трубе. Для этого в трубу опускают на шнуре небольшой длины отрезок тонкой трубки, который при соприкосновении с водой издает характерный хлопок. Таким образом, технология С. И. Дундикова позволяет обойтись без копра.
Забивку труб производят до тех пор, пока фильтр не погрузится в водоносный слой и уровень воды в трубе не будет стоять на 0,5–1 м выше верхнего края фильтра. После этого забивку труб прекращают и откачивают воду до полного ее осветления.
Для подъема воды из абиссинского колодца на высоту до 7 м годятся ручные поршневые насосы, например БКФ-4, НР-3,КР-3, КР-4, «Дон», НК-10, «Урал», «Ноток». Ручной насос плотно закрепляют на резьбе или на фланцах непосредственно на обсадной трубе колодца.
Рис. 19. Установка абиссинского колодца без треноги: 1 – хомут; 2 – блок; 3 – веревка; 4 – баба; 5 – подбабок; 6 – труба; 7 – сетчатый фильтр
Очень интересные сведения об этом колодце можно почерпнуть в старой литературе. Вот выдержка из работы К. И. Маслянникова «О земляном бураве, как средстве отыскания мест для колодцев, и об абиссинском колодце»: «Абиссинский (или нортоновский) колодец, этот отличный снаряд, почему-то, к сожалению, забыт в практике и в специальной печати. Абиссинские колодцы наделали вначале своего появления немало шуму в Европе после английской экспедиции в Абиссинии, где сослужили хорошую службу при отыскании воды. Этот шум дошел и до нас, и колодцы появились в наших складах, но вскоре были забыты. Главная часть абиссинского колодца – наконечник из трубы внутренним диаметром 1,25, 1,5 и 2 дюйма и состоит из соответственно продырявленной газовой трубки вроде фильтра и снабженного на конце копьевидным утолщением, а внутри – клапаном в виде шарика (рис. 18). Следующая принадлежность – копер (легкий железный треножник) и баба. Когда желают получить воду в данном месте, устанавливают треножник, навинчивают наконечник на газовую трубу, на которую надевают бабу, и бабой заколачивают трубу в землю. Абиссинский колодец испытывался в 1869 г. возле Царского Села в нескольких местах и с большим успехом. Места избирались каждый раз или на основании опытов местных жителей, или по общим гидротехническим соображениям.
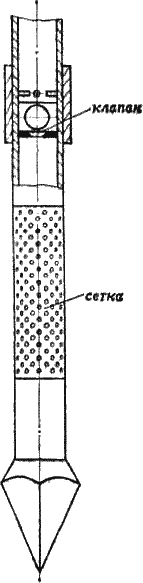
Несмотря на то что геологические условия Царского Села очень неблагоприятны для такого рода испытаний, так как там слои известнякового камня залегают близко от поверхности земли, при помощи абиссинского колодца удалось получить свежую и холодную воду в двух местах из пяти. В трех местах залегающий близко слой известняка заставлял прекращать работу в самом начале, причем вбитый конец абиссинского колодца легко выколачивался и затем весь прибор переносился на другое место. В других двух местах найдены были лучшие условия. Так, в одном первое колено было вколочено в 10 минут на глубину 10 футов и вода показалась в трубке с уровнем в 3 фута… На конец трубки был навинчен насос, который давал сначала грязную воду, а затем, примерно через пол часа, довольно чистую, в количестве 1 ведра в минуту. В последнем из выбранных для опыта пунктов были достигнуты наиболее интересные результаты. Хотя верхние слои почвы оказались переполненными крупными камнями и с прослойками из крепкой глины, тем не менее достоинство абиссинского колодца выказалось в значительной степени! Через 20 минут на глубине 2 сажени [1 сажень – 2,1333 м.] колодец был установлен и давал воду в количестве 1,5 ведра в минуту, которая сделалась через 0,25 часа светлою, годною для питья. Снятие абиссинского колодца в этом последнем случае потребовало еще меньше времени, чем его установка».
В этой выдержке очень образно и ярко, живым русским языком описаны простота и достоинства абиссинского колодца, в частности, отмечена быстрота установки его и снятия. Последнее определяет его ценность для временного водоснабжения в полевых условиях. Однако в первозданном виде абиссинский колодец имеет некоторые недостатки: примитивный фильтр – просто перфорированная трубка (то есть трубка с мелкими отверстиями); наибольшая глубина подъема воды всего – 7 м. Последнее объясняется конструкцией всасывающего насоса, поднимающего воду только в результате разряжения, создаваемого в трубе, а оно, как известно, не может теоретически поднять столб воды выше 10 м. Вот практически и получается – 7 м.
В настоящее время этот колодец известен, пожалуй, только специалистам.
При желании абиссинский колодец нетрудно сделать с сетчатым фильтром. Устройство и технология изготовления таких фильтров приведены ниже в разделах «Водоприемная часть трубчатых колодцев» и «Водоприемники из трубчатых колодцев».
Подъем воды с глубины более 7 м может быть осуществлен с помощью погружного насоса или эрлифта, описанных в разделе «Водоприемники из трубчатых колодцев».
В журнале «Лесное хозяйство» (1959, № 4) С. И. Дундиковым приведено описание упрощенной технологии забивки абиссинского колодца. Для этого на выбранном месте для колодца роют шахту размерами 0,8×0,8×1 м. Затем, присоединив к фильтру трубу, на нее свободно надевают бабу массой 25–30 кг. На расстоянии 1 м от фильтра на трубе укрепляют болтами стальной хомут – подбабок, состоящий из двух половин, а выше его на 1–1,5 м устанавливают второй хомут с двумя блоками (рис. 19).
Поставив в центре шахты подготовленную для забивки трубу, шахту заполняют грунтом и утрамбовывают его. После этого забивают абиссинский колодец, поднимая бабу за веревки. Падая, баба ударяет по нижнему хомуту и заглубляет трубу. По мере заглубления колодца подбабок и хомут с блоками передвигают вверх по трубе. Заглубив первую трубу, навинчивают следующую и т. д. В процессе забивки проверяют, не появилась ли вода в трубе. Для этого в трубу опускают на шнуре небольшой длины отрезок тонкой трубки, который при соприкосновении с водой издает характерный хлопок. Таким образом, технология С. И. Дундикова позволяет обойтись без копра.
Забивку труб производят до тех пор, пока фильтр не погрузится в водоносный слой и уровень воды в трубе не будет стоять на 0,5–1 м выше верхнего края фильтра. После этого забивку труб прекращают и откачивают воду до полного ее осветления.
Для подъема воды из абиссинского колодца на высоту до 7 м годятся ручные поршневые насосы, например БКФ-4, НР-3,КР-3, КР-4, «Дон», НК-10, «Урал», «Ноток». Ручной насос плотно закрепляют на резьбе или на фланцах непосредственно на обсадной трубе колодца.
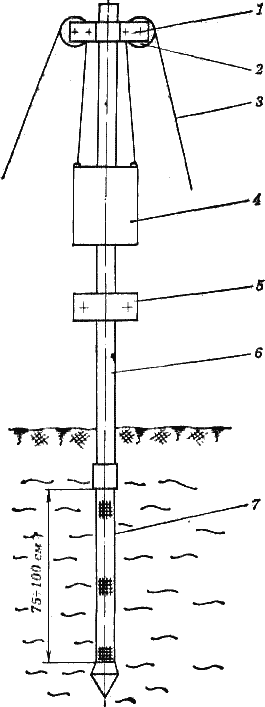
Ручное ударно-вращательное бурение скважин
Ручное бурение скважин на воду как промышленный способ применялось еще сравнительно недавно. Да и теперь оно возможно в тех местах, куда трудно доставить буровую технику. Ручным ударно-вращательным бурением, используя только мускульную силу человека, проходят скважины наибольшим диаметром 200–250 мм и глубиной до 70 м, а в отдельных случаях – и до 100 м. Проходку скважины ударно-вращательным бурением ведут вращением различных буров, а в твердых и сыпуче-плывучих породах – долблением специальными долотами и стаканами. Эти буровые инструменты подсоединяют к стержням – буровым штангам, которые соответственно вращают руками или попеременно поднимают и сбрасывают в забой. Отсюда и название способа проходки «ручное ударно-вращательное бурение».
Для проходки пластичных пород (глины и смеси глин с песками) наиболее приспособленным инструментом являются ложковые буры (ложки). Ложка – это полуцилиндр, свернутый из листовой стали, например Ст. 3, с левой отогнутой режущей кромкой (если смотреть сверху). Порода в полости полуцилиндра удерживается сжатием и прилипанием, поэтому продольная щель между кромками для более сыпучих пород должна быть более узкой. Ложка забирает породу вертикальной и нижней режущими кромками. Нижнюю часть ложки устраивают по-разному. Для самодельного исполнения наиболее доступны следующие варианты (рис. 20): низ ложки выполнен ковшеобразным резцом; низ ложки с левой стороны сделан в виде резца, а с правой – в виде поперечного выступа, причем между этими отгибами можно пропустить сверло по металлу и приварить его к телу ложки. И то и другое несложно выполнить, если есть возможность нагреть металл до пластичного состояния. Ложку можно также сделать из трубы подходящего диаметра и использовать ее даже без термического упрочнения режущих кромок. Существенной особенностью ложковых буров является то, что их корытообразный корпус обычно смещают на некоторое расстояние от оси вращения. Так, у бура со сверлом ось нижнего сверла и ось вращения штанги должны совпадать, а ось тела ложки следует сместить на расстояние е (эксцентриситет), равное 10–15 мм. Такой ложковый бур, вращаясь в скважине, своей продольной режущей кромкой будет вырабатывать в породе скважину большего диаметра по сравнению с диаметром ложки. Подобное уширение скважины необходимо для прохода обсадных труб, внутренний диаметр которых в большинстве случаев приходится брать больше наружного диаметра ложки. Объясняется это тем, что при опасности обвалов стенок скважины бурение и закрепление скважины обсадной трубой ведут одновременно, и ложка должна при этом проходить в обсадную трубу.
Рис. 20. Ложковые буры: а – с ковшеобразным резцом; б – с отгибами и сверлом
Порода, которую ложка забирает в забое скважины, извлекается на поверхность вместе с инструментом. За одну забурку ложкой обычно углубляют скважину на 30–40 см.
Иногда самодельный буровой инструмент делают в виде простого бурава – стального диска с вырезанным узким сектором и отогнутыми кромками. Конечно, можно что-то сделать и таким буром в пластичных, необваливающихся породах. Однако он очень легко уходит в сторону, вызывая часто недопустимое искривление ствола скважины. Если еще с этим как-то можно бороться установкой выше бура центрирующего пояска, то об уширении скважины для обсадной трубы в данном случае не может быть и речи.
Рис. 21. Змеевиковый бур
Для бурения плотных глин и суглинков применяют змеевиковый бур (змеевик), напоминающий бурав по дереву (рис. 21). Нижнее режущее лезвие змеевика имеет форму ласточкина хвоста и должно закаливаться. Змеевик действует подобно штопору: вращаясь, он ввинчивается в породу. При подъеме бура порода удерживается на его винтовых лопастях. Змеевик во время работы приподнимают на несколько сантиметров через каждые 1,5–2 оборота буровых штанг для отрыва от основного массива породы. В противном случае усилие подъема будет очень велико и штанги можно порвать.
Изготовить самому такой змеевик трудно, поэтому в самодеятельном бурении вместо него с успехом используют отрезки винтовых шнеков от сельхозмашин. Для этого берут часть шнека с 3–4 витками, снизу приваривают сверло по металлу (или просто конический штырь) для центрирования бура в забое, а сверху – отрезок трубы для соединения со штангами. Хорошие результаты получают, приспосабливая для бурения плотных глин и суглинков рыболовные ледовые буры.
Для проходки твердых пород и валунно-галечниковых отложений служат буровые долота. При необходимости их также делают эксцентричными по отношению к оси шейки, чтобы вырабатывать уширенную скважину, доступную для прохода обсадной трубы. Долота изготавливают из закаливающихся сталей У10, 45, 65Г, 40ХН п др.) и закаливают до твердости зубила на высоту не более 25 мм. В зависимости от крепости проходимых пород лезвие долот должно иметь различный угол заострения. Для проходки относительно мягких пород угол заострения (двугранный угол) – 70–80°, для твердых пород и валунно-галечниковых отложений – 110–130°.
Долота имеют разную форму применительно к различным по буримости породам (рис. 22). Бурение не очень твердых пород ведут зубильным (плоским долотом), более твердых – двутавровым и с Z-образным лезвием. Для бурения твердых трещиноватых пород служит крестовое долото, у которого два лезвия пересекаются под прямым углом, – это препятствует его заклиниванию в трещине. Скругляющее долото применяют также для проходки твердых пород, оно обеспечивает более правильную округлость скважины и дает хорошие результаты при проходке трещиноватых пород и валунно-галечниковых отложений. Эксцентричное долото разрабатывает скважины большего диаметра, чем размер лезвия. Для раздробления небольших валунов или отодвигания их в сторону в забое применяют долото в форме клина – пирамидальное долото.
Рис. 22. Буровые долота: 1 – зубильное (плоское); 2 – двутавровое; 3 – крестовое; 4 – скругляющее; 5 – эксцентричное; 6 – пирамидальное
Сделать самому в домашних условиях долота классической формы, представленные на рис. 22, чрезвычайно сложно. Изготовляют их ковкой в штампах из цельной заготовки, сварка категорически запрещается, так как при сварке закаливающихся сталей шов в обычных условиях получается хрупким. Для изготовления таких долот необходимы: кузнечно-прессовое тяжелое оборудование, закрытые печи с восстановительной атмосферой, специальная технологическая оснастка и т. п. Кузнецы, работающие в настоящее время вручную еще в некоторых ремонтных мастерских, неспособны сделать такие долота из-за невозможности прогреть массивную заготовку в открытом горне и невозможности удержать ее раскаленную в клещах из-за большой массы. Например, наименьшее плоское долото с длиной лезвия 148 мм имеет массу 42 кг. Поэтому форму долот надо воспринимать как «информацию к размышлению» при конструировании самодельных аналогов.
Итак, возникает проблема. Решить ее можно следующим образом: либо фрезеровать долото из цельной заготовки (такую возможность имеет далеко не каждый); либо все же попытаться сварить долото из мягкой стали (имея в виду его непродолжительную работу) с твердосплавной наплавкой режущих кромок, либо сделать долото составным, то есть корпус сварить из мягкой стали, а режущую часть набрать из таких стальных зубильных лезвий, которые кузнец смог бы прогреть, вручную отковать и закалить.
На рис. 23 показаны составные долота, способные разрабатывать скважину диаметром 250 мм. Все долота сделаны в основном своими руками, опробованы на практике (поработали они основательно), показав хорошие результаты.
Рис. 23. Составные долота: 1 – клин; 2 – вставное лезвие; 3 – заклепка
Корпус долота (а) вырезали кислородным резаком из стальной пластины толщиной 40 мм. Механической обработке его не подвергали, кроме незначительной зачистки на наждаке. К корпусу сверху приварена электросваркой шейка для соединения со штангами. Снизу просверлены 4 глухих отверстия диаметром 20 мм для вставных зубильных лезвий и 4 сквозных боковых отверстия диаметром 12 мм для цилиндрических клиньев, закрепляющих зубильные лезвия (аналогичными цилиндрическими клиньями закрепляются, например, шатуны у велосипеда). Зубильные лезвия были откованы кузнецом из заготовок (инструментальная сталь У10), предварительно выточенных на токарном станке. После ковки и закалки зубильные лезвия были заточены, на хвостовиках напильником сделаны лыски. Затем лезвия закрепили в отверстиях цилиндрическими клиньями, нарезанными из стального прутка диаметром 12 мм. Клиновые лыски на этих деталях также сделали напильником. Вставные зубильные лезвия можно отковать не из точеных заготовок, а, к примеру, из изношенных пальцев тракторных гусениц. Смонтировать зубильные лезвия в корпусе также можно по-разному – в линию, крестообразно, змейкой и др., приблизив форму долот к вышеописанным классическим образцам. Все это, понятно, легко сделать в одном корпусе, меняя только зубильные лезвия.
Лезвия долота (б) изготовили из куска листовой рессоры, которую обрезали кислородным резаком в размер, отпустили, просверлили отверстия и установили на заклепках в корпус, подготовленный сваркой из нарубленных стальных пластин. Клепка горячая.
Для долота (в) в качестве лезвий использовали обрезки отличной стали от гильотинных ножниц для рубки листового металла. Толщина обрезков 36 мм, поэтому вставные долота получились очень «мощными» и показали хорошие результаты при проходке валунно-галечниковых отложений. Форма этого долота в какой-то мере воспроизводит классическое скругляющее долото.
Как видим, во всех случаях соединение лезвий, сделанных из закаливающихся сталей, с корпусом из стали, не способной к закалке, выполнено клиньями, заклепками, болтами, но только не сваркой, которая бы дала хрупкий шов.
Конечно, у самодельных составных долот, да еще изготовленных с применением сварки, ресурс работы и производительность будут меньше, но уж тут, как говорится, не до жиру… Тем более что задача самодеятельного бурильщика сделать только одну свою скважину, а для этого составного долота должно хватить. Во всяком случае, в практике автора вставные лезвия тупились, по поломок но было. Кстати, по старым инструкциям при каждом поднятии долота из забоя на поверхность его нужно тщательно осматривать, своевременно производить заточку и т. д.
Заметим, что если в породе много валунов, может оказаться легче поднять их на поверхность, чем дробить в забое. На этот счет самодеятельными бурильщиками придумано немало хитроумных устройств: различные «пауки», вилки с тремя-четырьмя стальными зубьями и др. Автор при глубине до 10 м применял сачок – овальный стальной пруток с мешком (пруток приварен к штанге) и «гарпун» – заостренный стальной стержень с приваренной на конце под углом острой пластинкой. Вылавливали валуны так: «гарпуном» валун выворачивали из окружающего плотного суглинка, предварительно размоченного водой, и закатывали в сачок.
Рис. 24. Желонки: а – с плоским клапаном: б – с шариковым клапаном; 1 – труба; 2 – отбивной штифт; 3 – клапан; 4 – ось; 5 – башмак; 6 – ограничитель
Для бурения пород рыхлых, сыпучих, обломочных (пески, гравий, галечник, ил), пород, наполненных водой, а также для чистки скважины после работы долотом применяют инструмент, называемый желонкой. Последняя представляет собой: отрезок трубы длиной 2–3 м, иногда до 4 м, снабженной внизу башмаком с клапаном, а вверху – устройством для соединения со штангами (рис. 24). Клапан обычно делается плоским из стальной пластины с уплотнением резиной, кожей или без него. В желонках небольшого диаметра применяют шариковый клапан. При сбрасывании в забой башмак желонки врезается в породу, которая приподнимает клапан и входит в трубу. Когда желонку поднимают, клапан закрывается и удерживает набранную породу. После заполнения породой желонку извлекают на поверхность и очищают, поворачивая ее для этого вверх клапаном с помощью специального устройства, позволяющего не отсоединять желонку от штанги. Бурильщику, который впервые «изобретает» желонку из случайных материалов, порекомендуем не гнаться за производительностью и сделать общую высоту желонки поменьше, скажем, около 1 м, и с боковым окном (рис. 25), чтобы можно было рукой дотянуться до клапана. Через это окно можно ее и чистить не переворачивая. Косынки и конус в верхней части желонки предназначены для того, чтобы при подъеме не зацепить желонку за обсадную трубу.
Рис. 25. Самодельная желонка: 1 – ударная штанга; 2 – окно; 3 – клапан; 4 – башмак
В качестве буровых штанг для неглубокого бурения (до 25 м) вполне достаточными по прочности являются газовые трубы внутренним диаметром 33 мм (применяют также трубы диаметром 42 и 48 мм). Длина труб отдельных звеньев штанги – 5 м. Отбирая трубы для штанг, надо внимательно осмотреть сварные швы. Если швы плохо проварены, то во время бурения при скручивающих нагрузках они легко расходятся.
Обычные водопроводные или газовые муфты для соединения штанг нежелательны из-за недостаточных прочности и длины. Для соединения буровых штанг лучше изготовить специальные муфты большей длины, бочкообразной формы и с гладкими концевыми внутренними проточками, в которые концы свинчиваемых штанг должны плотно заходить своими ненарезанными частями (рис. 26). Последнее делается для того, чтобы уменьшить опасные изгибающие нагрузки в концевых сечениях штанг, ослабленных резьбой. Конечно, намного ускоряет процесс соединения-разъединения штанг коническая резьба. Однако сделать такую резьбу очень трудно, и если, что скорее всего, придется ограничиться цилиндрической резьбой, то нарезать ее на штангах надо на токарном станке или клуппом с направляющей втулкой, чтобы избежать перекоса резьбы. Штанги с перекошенной резьбой при свинчивании будут располагаться не соосно, что чревато большими неприятностями, поскольку приводит к вихлянию всей буровой колонны, особенно заметному при ее длине более 10 м.
Рис. 26. Муфта
Для проходки пластичных пород (глины и смеси глин с песками) наиболее приспособленным инструментом являются ложковые буры (ложки). Ложка – это полуцилиндр, свернутый из листовой стали, например Ст. 3, с левой отогнутой режущей кромкой (если смотреть сверху). Порода в полости полуцилиндра удерживается сжатием и прилипанием, поэтому продольная щель между кромками для более сыпучих пород должна быть более узкой. Ложка забирает породу вертикальной и нижней режущими кромками. Нижнюю часть ложки устраивают по-разному. Для самодельного исполнения наиболее доступны следующие варианты (рис. 20): низ ложки выполнен ковшеобразным резцом; низ ложки с левой стороны сделан в виде резца, а с правой – в виде поперечного выступа, причем между этими отгибами можно пропустить сверло по металлу и приварить его к телу ложки. И то и другое несложно выполнить, если есть возможность нагреть металл до пластичного состояния. Ложку можно также сделать из трубы подходящего диаметра и использовать ее даже без термического упрочнения режущих кромок. Существенной особенностью ложковых буров является то, что их корытообразный корпус обычно смещают на некоторое расстояние от оси вращения. Так, у бура со сверлом ось нижнего сверла и ось вращения штанги должны совпадать, а ось тела ложки следует сместить на расстояние е (эксцентриситет), равное 10–15 мм. Такой ложковый бур, вращаясь в скважине, своей продольной режущей кромкой будет вырабатывать в породе скважину большего диаметра по сравнению с диаметром ложки. Подобное уширение скважины необходимо для прохода обсадных труб, внутренний диаметр которых в большинстве случаев приходится брать больше наружного диаметра ложки. Объясняется это тем, что при опасности обвалов стенок скважины бурение и закрепление скважины обсадной трубой ведут одновременно, и ложка должна при этом проходить в обсадную трубу.
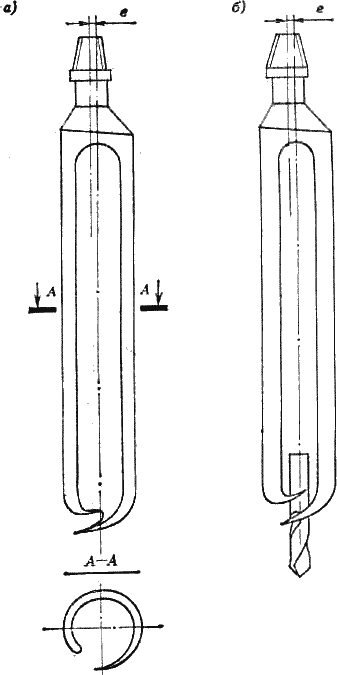
Порода, которую ложка забирает в забое скважины, извлекается на поверхность вместе с инструментом. За одну забурку ложкой обычно углубляют скважину на 30–40 см.
Иногда самодельный буровой инструмент делают в виде простого бурава – стального диска с вырезанным узким сектором и отогнутыми кромками. Конечно, можно что-то сделать и таким буром в пластичных, необваливающихся породах. Однако он очень легко уходит в сторону, вызывая часто недопустимое искривление ствола скважины. Если еще с этим как-то можно бороться установкой выше бура центрирующего пояска, то об уширении скважины для обсадной трубы в данном случае не может быть и речи.

Для бурения плотных глин и суглинков применяют змеевиковый бур (змеевик), напоминающий бурав по дереву (рис. 21). Нижнее режущее лезвие змеевика имеет форму ласточкина хвоста и должно закаливаться. Змеевик действует подобно штопору: вращаясь, он ввинчивается в породу. При подъеме бура порода удерживается на его винтовых лопастях. Змеевик во время работы приподнимают на несколько сантиметров через каждые 1,5–2 оборота буровых штанг для отрыва от основного массива породы. В противном случае усилие подъема будет очень велико и штанги можно порвать.
Изготовить самому такой змеевик трудно, поэтому в самодеятельном бурении вместо него с успехом используют отрезки винтовых шнеков от сельхозмашин. Для этого берут часть шнека с 3–4 витками, снизу приваривают сверло по металлу (или просто конический штырь) для центрирования бура в забое, а сверху – отрезок трубы для соединения со штангами. Хорошие результаты получают, приспосабливая для бурения плотных глин и суглинков рыболовные ледовые буры.
Для проходки твердых пород и валунно-галечниковых отложений служат буровые долота. При необходимости их также делают эксцентричными по отношению к оси шейки, чтобы вырабатывать уширенную скважину, доступную для прохода обсадной трубы. Долота изготавливают из закаливающихся сталей У10, 45, 65Г, 40ХН п др.) и закаливают до твердости зубила на высоту не более 25 мм. В зависимости от крепости проходимых пород лезвие долот должно иметь различный угол заострения. Для проходки относительно мягких пород угол заострения (двугранный угол) – 70–80°, для твердых пород и валунно-галечниковых отложений – 110–130°.
Долота имеют разную форму применительно к различным по буримости породам (рис. 22). Бурение не очень твердых пород ведут зубильным (плоским долотом), более твердых – двутавровым и с Z-образным лезвием. Для бурения твердых трещиноватых пород служит крестовое долото, у которого два лезвия пересекаются под прямым углом, – это препятствует его заклиниванию в трещине. Скругляющее долото применяют также для проходки твердых пород, оно обеспечивает более правильную округлость скважины и дает хорошие результаты при проходке трещиноватых пород и валунно-галечниковых отложений. Эксцентричное долото разрабатывает скважины большего диаметра, чем размер лезвия. Для раздробления небольших валунов или отодвигания их в сторону в забое применяют долото в форме клина – пирамидальное долото.
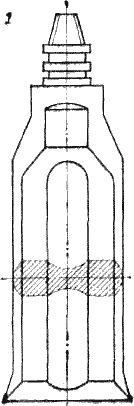
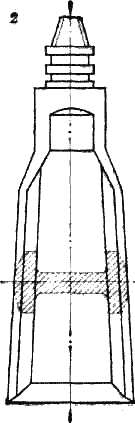
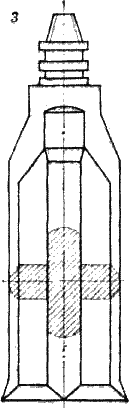
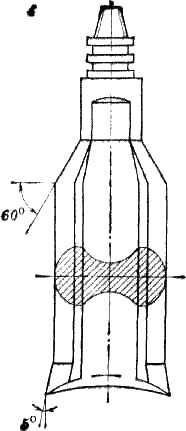
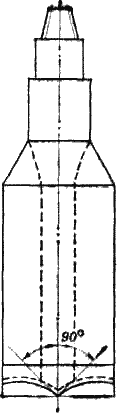
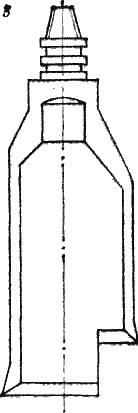
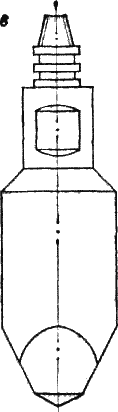
Сделать самому в домашних условиях долота классической формы, представленные на рис. 22, чрезвычайно сложно. Изготовляют их ковкой в штампах из цельной заготовки, сварка категорически запрещается, так как при сварке закаливающихся сталей шов в обычных условиях получается хрупким. Для изготовления таких долот необходимы: кузнечно-прессовое тяжелое оборудование, закрытые печи с восстановительной атмосферой, специальная технологическая оснастка и т. п. Кузнецы, работающие в настоящее время вручную еще в некоторых ремонтных мастерских, неспособны сделать такие долота из-за невозможности прогреть массивную заготовку в открытом горне и невозможности удержать ее раскаленную в клещах из-за большой массы. Например, наименьшее плоское долото с длиной лезвия 148 мм имеет массу 42 кг. Поэтому форму долот надо воспринимать как «информацию к размышлению» при конструировании самодельных аналогов.
Итак, возникает проблема. Решить ее можно следующим образом: либо фрезеровать долото из цельной заготовки (такую возможность имеет далеко не каждый); либо все же попытаться сварить долото из мягкой стали (имея в виду его непродолжительную работу) с твердосплавной наплавкой режущих кромок, либо сделать долото составным, то есть корпус сварить из мягкой стали, а режущую часть набрать из таких стальных зубильных лезвий, которые кузнец смог бы прогреть, вручную отковать и закалить.
На рис. 23 показаны составные долота, способные разрабатывать скважину диаметром 250 мм. Все долота сделаны в основном своими руками, опробованы на практике (поработали они основательно), показав хорошие результаты.
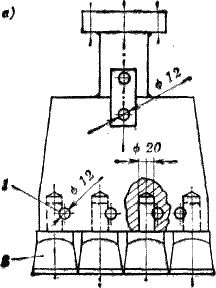
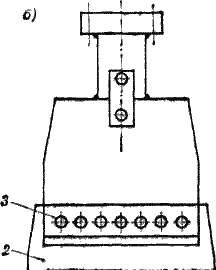
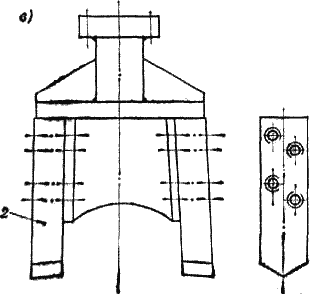
Корпус долота (а) вырезали кислородным резаком из стальной пластины толщиной 40 мм. Механической обработке его не подвергали, кроме незначительной зачистки на наждаке. К корпусу сверху приварена электросваркой шейка для соединения со штангами. Снизу просверлены 4 глухих отверстия диаметром 20 мм для вставных зубильных лезвий и 4 сквозных боковых отверстия диаметром 12 мм для цилиндрических клиньев, закрепляющих зубильные лезвия (аналогичными цилиндрическими клиньями закрепляются, например, шатуны у велосипеда). Зубильные лезвия были откованы кузнецом из заготовок (инструментальная сталь У10), предварительно выточенных на токарном станке. После ковки и закалки зубильные лезвия были заточены, на хвостовиках напильником сделаны лыски. Затем лезвия закрепили в отверстиях цилиндрическими клиньями, нарезанными из стального прутка диаметром 12 мм. Клиновые лыски на этих деталях также сделали напильником. Вставные зубильные лезвия можно отковать не из точеных заготовок, а, к примеру, из изношенных пальцев тракторных гусениц. Смонтировать зубильные лезвия в корпусе также можно по-разному – в линию, крестообразно, змейкой и др., приблизив форму долот к вышеописанным классическим образцам. Все это, понятно, легко сделать в одном корпусе, меняя только зубильные лезвия.
Лезвия долота (б) изготовили из куска листовой рессоры, которую обрезали кислородным резаком в размер, отпустили, просверлили отверстия и установили на заклепках в корпус, подготовленный сваркой из нарубленных стальных пластин. Клепка горячая.
Для долота (в) в качестве лезвий использовали обрезки отличной стали от гильотинных ножниц для рубки листового металла. Толщина обрезков 36 мм, поэтому вставные долота получились очень «мощными» и показали хорошие результаты при проходке валунно-галечниковых отложений. Форма этого долота в какой-то мере воспроизводит классическое скругляющее долото.
Как видим, во всех случаях соединение лезвий, сделанных из закаливающихся сталей, с корпусом из стали, не способной к закалке, выполнено клиньями, заклепками, болтами, но только не сваркой, которая бы дала хрупкий шов.
Конечно, у самодельных составных долот, да еще изготовленных с применением сварки, ресурс работы и производительность будут меньше, но уж тут, как говорится, не до жиру… Тем более что задача самодеятельного бурильщика сделать только одну свою скважину, а для этого составного долота должно хватить. Во всяком случае, в практике автора вставные лезвия тупились, по поломок но было. Кстати, по старым инструкциям при каждом поднятии долота из забоя на поверхность его нужно тщательно осматривать, своевременно производить заточку и т. д.
Заметим, что если в породе много валунов, может оказаться легче поднять их на поверхность, чем дробить в забое. На этот счет самодеятельными бурильщиками придумано немало хитроумных устройств: различные «пауки», вилки с тремя-четырьмя стальными зубьями и др. Автор при глубине до 10 м применял сачок – овальный стальной пруток с мешком (пруток приварен к штанге) и «гарпун» – заостренный стальной стержень с приваренной на конце под углом острой пластинкой. Вылавливали валуны так: «гарпуном» валун выворачивали из окружающего плотного суглинка, предварительно размоченного водой, и закатывали в сачок.

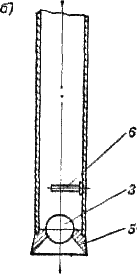
Для бурения пород рыхлых, сыпучих, обломочных (пески, гравий, галечник, ил), пород, наполненных водой, а также для чистки скважины после работы долотом применяют инструмент, называемый желонкой. Последняя представляет собой: отрезок трубы длиной 2–3 м, иногда до 4 м, снабженной внизу башмаком с клапаном, а вверху – устройством для соединения со штангами (рис. 24). Клапан обычно делается плоским из стальной пластины с уплотнением резиной, кожей или без него. В желонках небольшого диаметра применяют шариковый клапан. При сбрасывании в забой башмак желонки врезается в породу, которая приподнимает клапан и входит в трубу. Когда желонку поднимают, клапан закрывается и удерживает набранную породу. После заполнения породой желонку извлекают на поверхность и очищают, поворачивая ее для этого вверх клапаном с помощью специального устройства, позволяющего не отсоединять желонку от штанги. Бурильщику, который впервые «изобретает» желонку из случайных материалов, порекомендуем не гнаться за производительностью и сделать общую высоту желонки поменьше, скажем, около 1 м, и с боковым окном (рис. 25), чтобы можно было рукой дотянуться до клапана. Через это окно можно ее и чистить не переворачивая. Косынки и конус в верхней части желонки предназначены для того, чтобы при подъеме не зацепить желонку за обсадную трубу.
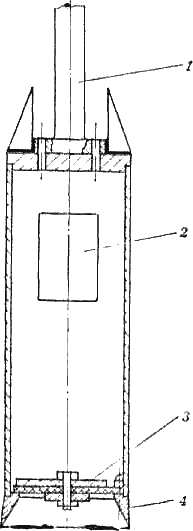
В качестве буровых штанг для неглубокого бурения (до 25 м) вполне достаточными по прочности являются газовые трубы внутренним диаметром 33 мм (применяют также трубы диаметром 42 и 48 мм). Длина труб отдельных звеньев штанги – 5 м. Отбирая трубы для штанг, надо внимательно осмотреть сварные швы. Если швы плохо проварены, то во время бурения при скручивающих нагрузках они легко расходятся.
Обычные водопроводные или газовые муфты для соединения штанг нежелательны из-за недостаточных прочности и длины. Для соединения буровых штанг лучше изготовить специальные муфты большей длины, бочкообразной формы и с гладкими концевыми внутренними проточками, в которые концы свинчиваемых штанг должны плотно заходить своими ненарезанными частями (рис. 26). Последнее делается для того, чтобы уменьшить опасные изгибающие нагрузки в концевых сечениях штанг, ослабленных резьбой. Конечно, намного ускоряет процесс соединения-разъединения штанг коническая резьба. Однако сделать такую резьбу очень трудно, и если, что скорее всего, придется ограничиться цилиндрической резьбой, то нарезать ее на штангах надо на токарном станке или клуппом с направляющей втулкой, чтобы избежать перекоса резьбы. Штанги с перекошенной резьбой при свинчивании будут располагаться не соосно, что чревато большими неприятностями, поскольку приводит к вихлянию всей буровой колонны, особенно заметному при ее длине более 10 м.
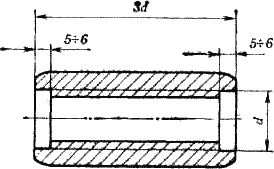