Страница:
Второй метод – косвенный, основанный на измерении электропроводности древесины с помощью электровлагомера. При таком измерении шкала прибора показывает величину влажности. Этот способ дает возможность быстро определить влажность. Но его недостаток заключается в погрешности измерения, которая составляет 2–3 %, а при влажности древесины более 30 % – еще выше.
Вода в древесине находится в связанном и свободном состоянии. Связанная вода находится в клеточных стенках и удерживается прочно. Удаление такой воды затруднено и оказывает существенное влияние на изменение большинства свойств древесины. Максимальное количество связанной воды соответствует пределу насыщения клеточных стенок, который в расчетах принимается: Wп.н. = 30 %.
Свободная вода находится в полостях клеток и межклеточных пространствах, поэтому удаляется из древесины легче.
Свежесрубленная древесина имеет влажность в пределах 50—100 %, а при длительном нахождении в воде – более 100 %.
После сушки на открытом воздухе влажность снижается до 15–20 %. Влажность величиной 20–22 % называется транспортной, а влажность, которую древесина имеет в период эксплуатации, – эксплуатационной.
Сушка древесины бывает двух видов – атмосферной, при температуре окружающей среды, и искусственной, или камерной, когда температура может быть до 100 °C и выше. При камерной сушке происходит усушка древесины, т. е. уменьшение линейных размеров в радиальном направлении на 3–7 %, а в тангенциальном – на 8—10 %, вдоль волокон – 0,1–0,3 %. Полная объемная усушка составляет 11–17 %.
При сушке древесины с уменьшением влажности меняются ее механические свойства – уменьшается упругость, но увеличивается прочность при сжатии, а также уменьшается электропроводность.
3. Плотность древесины. Тепловые свойства древесины
4. Электрические и акустические свойства древесины
5. Прочность древесины
6. Технологические свойства древесины
ЛЕКЦИЯ № 5. Сплавы
1. Строение металлов
Вода в древесине находится в связанном и свободном состоянии. Связанная вода находится в клеточных стенках и удерживается прочно. Удаление такой воды затруднено и оказывает существенное влияние на изменение большинства свойств древесины. Максимальное количество связанной воды соответствует пределу насыщения клеточных стенок, который в расчетах принимается: Wп.н. = 30 %.
Свободная вода находится в полостях клеток и межклеточных пространствах, поэтому удаляется из древесины легче.
Свежесрубленная древесина имеет влажность в пределах 50—100 %, а при длительном нахождении в воде – более 100 %.
После сушки на открытом воздухе влажность снижается до 15–20 %. Влажность величиной 20–22 % называется транспортной, а влажность, которую древесина имеет в период эксплуатации, – эксплуатационной.
Сушка древесины бывает двух видов – атмосферной, при температуре окружающей среды, и искусственной, или камерной, когда температура может быть до 100 °C и выше. При камерной сушке происходит усушка древесины, т. е. уменьшение линейных размеров в радиальном направлении на 3–7 %, а в тангенциальном – на 8—10 %, вдоль волокон – 0,1–0,3 %. Полная объемная усушка составляет 11–17 %.
При сушке древесины с уменьшением влажности меняются ее механические свойства – уменьшается упругость, но увеличивается прочность при сжатии, а также уменьшается электропроводность.
3. Плотность древесины. Тепловые свойства древесины
Плотность древесины – это масса единицы объема материала, выражающаяся в г/см 3 или кг/м 3. Существует несколько показателей плотности древесины, которые зависят от влажности. Плотность древесного вещества – это масса единицы объема материала, образующего клеточные стенки. Она для всех пород примерно одинакова и равна 1,53 г/см 3, т. е. в 1,5 раза выше плотности воды.
Плотность абсолютно сухой древесины – это масса единицы объема древесины при отсутствии в ней воды. Она определяется по формуле:
ρ0 = m0 / V0,
где р0 – плотность абсолютно сухой древесины, г/см 3 или кг/м 3;
m0 – масса образца древесины при влажности 0 %, г или кг; V0 – объем образца древесины при влажности 0 %, см 3 или м 3.
Плотность древесины меньше плотности древесного вещества, так как она имеет пустоты, заполненные воздухом, т. е. пористость, которая выражается в процентах и характеризует отношение пустот в абсолютно сухой древесине. Чем больше плотность древесины, тем меньше ее пористость.
Плотность древесины существенно зависит от влажности С увеличением влажности плотность древесины возрастает По плотности все породы делятся на три группы (при влажности древесины 12 %):
1) породы с малой плотностью – 540 кг/м 3 и менее – это ель, сосна, липа и др.;
2) породы средней плотности – от 550 до 740 кг/м 3– это дуб, береза, вяз и др.;
3) породы высокой плотности – 750 кг/м 3 и более – это кизил, граб, фисташка и др.
Тепловые свойства древесины – это теплоемкость, теплопроводность, температуропроводность и тепловое расширение. Теплоемкость – способность древесины аккумулировать тепло. За показатель теплоемкости принята удельная теплоемкость С – количество теплоты, необходимое для нагревания 1 кг массы древесины на 1 °C. Она измеряется в кДж/кг × t °С.
Сухая древесина представляет собой древесное вещество и воздух, причем массовая доля воздуха в ней незначительна Поэтому теплоемкость сухой древесины практически равна теплоемкости древесного вещества. Удельная теплоемкость древесины практически не зависит от породы и при температуре 0 °C для абсолютно сухой древесины равна 1,55 кДж. С повышением температуры удельная теплоемкость несколько возрастает и при температуре 100 °C увеличивается примерно на 25 %. При увлажнении древесины ее теплоемкость увеличивается.
Процесс переноса тепла в древесине характеризуется двумя показателями – коэффициентом теплопроводности и коэффициентом температуропроводности. Коэффициент теплопроводности? численно равен количеству теплоты, которое проходит в единицу времени через стенку из древесины площадью 1 м 2 и толщиной 1 м при разности температур на противоположных сторонах стенки в 1 °C. Он измеряется в Вт / (м × °С).
Коэффициент температуропроводности характеризует скорость изменения температуры древесины при ее нагревании или охлаждении. Он определяет тепловую инерционность древесины, т. е. ее способность выравнивать температуру. Коэффициент температуропроводности рассчитывают по формуле:
α = λ/с × ρ,
где ρ – плотность материала, кг/м3;
λ – коэффициент теплопроводности, Вт / (м × °С);
с – удельная теплоемкость древесины, кДж / (кг × °С).
Плотность абсолютно сухой древесины – это масса единицы объема древесины при отсутствии в ней воды. Она определяется по формуле:
ρ0 = m0 / V0,
где р0 – плотность абсолютно сухой древесины, г/см 3 или кг/м 3;
m0 – масса образца древесины при влажности 0 %, г или кг; V0 – объем образца древесины при влажности 0 %, см 3 или м 3.
Плотность древесины меньше плотности древесного вещества, так как она имеет пустоты, заполненные воздухом, т. е. пористость, которая выражается в процентах и характеризует отношение пустот в абсолютно сухой древесине. Чем больше плотность древесины, тем меньше ее пористость.
Плотность древесины существенно зависит от влажности С увеличением влажности плотность древесины возрастает По плотности все породы делятся на три группы (при влажности древесины 12 %):
1) породы с малой плотностью – 540 кг/м 3 и менее – это ель, сосна, липа и др.;
2) породы средней плотности – от 550 до 740 кг/м 3– это дуб, береза, вяз и др.;
3) породы высокой плотности – 750 кг/м 3 и более – это кизил, граб, фисташка и др.
Тепловые свойства древесины – это теплоемкость, теплопроводность, температуропроводность и тепловое расширение. Теплоемкость – способность древесины аккумулировать тепло. За показатель теплоемкости принята удельная теплоемкость С – количество теплоты, необходимое для нагревания 1 кг массы древесины на 1 °C. Она измеряется в кДж/кг × t °С.
Сухая древесина представляет собой древесное вещество и воздух, причем массовая доля воздуха в ней незначительна Поэтому теплоемкость сухой древесины практически равна теплоемкости древесного вещества. Удельная теплоемкость древесины практически не зависит от породы и при температуре 0 °C для абсолютно сухой древесины равна 1,55 кДж. С повышением температуры удельная теплоемкость несколько возрастает и при температуре 100 °C увеличивается примерно на 25 %. При увлажнении древесины ее теплоемкость увеличивается.
Процесс переноса тепла в древесине характеризуется двумя показателями – коэффициентом теплопроводности и коэффициентом температуропроводности. Коэффициент теплопроводности? численно равен количеству теплоты, которое проходит в единицу времени через стенку из древесины площадью 1 м 2 и толщиной 1 м при разности температур на противоположных сторонах стенки в 1 °C. Он измеряется в Вт / (м × °С).
Коэффициент температуропроводности характеризует скорость изменения температуры древесины при ее нагревании или охлаждении. Он определяет тепловую инерционность древесины, т. е. ее способность выравнивать температуру. Коэффициент температуропроводности рассчитывают по формуле:
α = λ/с × ρ,
где ρ – плотность материала, кг/м3;
λ – коэффициент теплопроводности, Вт / (м × °С);
с – удельная теплоемкость древесины, кДж / (кг × °С).
4. Электрические и акустические свойства древесины
Как показали многочисленные исследования электрических свойств древесины, ее электропроводность, т. е. способность проводить электрический ток, находится в обратной зависимости от ее электрического сопротивления. Существуют поверхностное и объемное сопротивления, которые в сумме дают полное сопротивление образца древесины, размещенного между двумя электродами. Объемное сопротивление характеризует препятствие прохождению тока сквозь толщу образца, а поверхностное – по поверхности. Показателями электрического сопротивления служат удельное объемное и удельное поверхностное сопротивления.
Исследования показали, что сухая древесина плохо проводит ток, но с повышением влажности ее сопротивление уменьшается. Это видно из данных, полученных при исследованиях (табл. 1).
Таблица 1
Снижение поверхностного сопротивления происходит при увеличении влажности. Например, при увеличении влажности бука от 4,5 до 17 % поверхностное электрическое сопротивление уменьшается с 1,2 × 1013 до 1 × 107 Ом.
Кроме того, в результате исследований установлено, что снижение электрического сопротивления древесины происходит при ее нагревании, особенно при ее низкой влажности Так, увеличение температуры от 20 до 94 °C снижает сопротивление абсолютно сухой древесины в 10 6 раз.
Акустические свойства. При исследованиях акустических свойств древесины установлено, что скорость распространения звука в древесине тем больше, чем меньше ее плотность и выше модуль упругости. Средние значения скорости звука вдоль волокон для комнатно—сухой древесины равны: дуб – 4720 м/с, ясень – 4730 м/с, сосна – 5360 м/с, лиственница – 4930 м/с. Далее исследования показали, что скорость звука поперек волокон в 3–4 раза меньше, чем вдоль волокон. Скорость распространения звука зависит от свойств материалов и в первую очередь от плотности, например в стали звук распространяется со скоростью 5050 м/с, в воздухе – 330 м/с, а в каучуке – 30 м/с. На данных, полученных при исследованиях акустических свойств древесины, построен ультразвуковой метод определения ее прочности и внутренних скрытых дефектов По существующим строительным нормам звукоизоляция стен и перегородок должна быть не ниже 40, а междуэтажных – 48 дБ. Согласно данным исследований звукопоглощающая способность древесины низка, например звукоизоляция сосновой древесины при толщине 3 см составляет 12 дБ, а дубовой при толщине 4,5 см – 27 дБ. Как установлено исследованиями, наилучшие акустические свойства в части наибольшего излучения звука имеет древесина ели, пихты и кедра, которая используется для изготовления многих музыкальных инструментов: щипковых, смычковых, клавишных и др. Как показала практика, наилучшими акустическими свойствами обладает древесина длительной выдержки – в течение 50 лет и более.
Исследования показали, что сухая древесина плохо проводит ток, но с повышением влажности ее сопротивление уменьшается. Это видно из данных, полученных при исследованиях (табл. 1).
Таблица 1
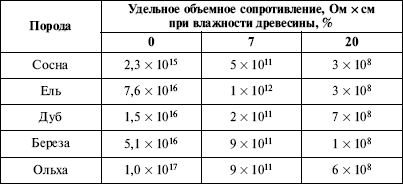
Снижение поверхностного сопротивления происходит при увеличении влажности. Например, при увеличении влажности бука от 4,5 до 17 % поверхностное электрическое сопротивление уменьшается с 1,2 × 1013 до 1 × 107 Ом.
Кроме того, в результате исследований установлено, что снижение электрического сопротивления древесины происходит при ее нагревании, особенно при ее низкой влажности Так, увеличение температуры от 20 до 94 °C снижает сопротивление абсолютно сухой древесины в 10 6 раз.
Акустические свойства. При исследованиях акустических свойств древесины установлено, что скорость распространения звука в древесине тем больше, чем меньше ее плотность и выше модуль упругости. Средние значения скорости звука вдоль волокон для комнатно—сухой древесины равны: дуб – 4720 м/с, ясень – 4730 м/с, сосна – 5360 м/с, лиственница – 4930 м/с. Далее исследования показали, что скорость звука поперек волокон в 3–4 раза меньше, чем вдоль волокон. Скорость распространения звука зависит от свойств материалов и в первую очередь от плотности, например в стали звук распространяется со скоростью 5050 м/с, в воздухе – 330 м/с, а в каучуке – 30 м/с. На данных, полученных при исследованиях акустических свойств древесины, построен ультразвуковой метод определения ее прочности и внутренних скрытых дефектов По существующим строительным нормам звукоизоляция стен и перегородок должна быть не ниже 40, а междуэтажных – 48 дБ. Согласно данным исследований звукопоглощающая способность древесины низка, например звукоизоляция сосновой древесины при толщине 3 см составляет 12 дБ, а дубовой при толщине 4,5 см – 27 дБ. Как установлено исследованиями, наилучшие акустические свойства в части наибольшего излучения звука имеет древесина ели, пихты и кедра, которая используется для изготовления многих музыкальных инструментов: щипковых, смычковых, клавишных и др. Как показала практика, наилучшими акустическими свойствами обладает древесина длительной выдержки – в течение 50 лет и более.
5. Прочность древесины
К механическим свойствам относятся прочность и дефор—мативность древесины, а также некоторые технологические свойства. Прочность древесины – это способность ее сопротивляться разрушениям под воздействием внешних нагрузок. Предел прочности древесины определяется путем испытания образцов на сжатие, растяжение, изгиб, сдвиг.
При испытании древесины на сжатие нагрузку производят вдоль волокон, затем поперек и в одном месте. Предел прочности определяют в МПа по формуле:
бсж = Рmax / a × b,
где Pmax – максимальная разрушающая нагрузка, Н;
а и b – размеры образца древесины, мм.
По данным испытаний установлено, что при растяжении древесины поперек волокон прочность составляет примерно 1/20 прочности при растяжении вдоль волокон. Поэтому при конструировании изделий и устройстве различных строительных конструкций не допускают случаев, чтобы растягивающие нагрузки были направлены поперек волокон.
На практике в большинстве случаев изделия из древесины работают с нагрузками на изгиб. Поэтому образцы древесины обязательно испытывают на изгиб, при этом определяют предел прочности в МПа по формуле:
биз = 3Рmax × l/2 × b × h2,
где l – расстояние между опорами, мм;
b – ширина образца в радиальном направлении, мм;
h – высота образца в тангенциальном направлении, мм.
При изгибании образца с выпуклой стороны возникают напряжения растяжения, а с вогнутой – сжатия. При нагрузках выше предельной величины разрушение древесины происходит в виде разрыва растянутых волокон на выпуклой стороне излома образца.
Большое значение имеет показатель прочности при сдвиге. Этот показатель определяют при испытаниях трех видов сдвига: на скалывание вдоль и поперек волокон; на перерезание древесины поперек волокон. При этом предел прочности древесины на скалывание – бск, МПа определяют по формуле:
бск = Рmax / b × l,
где P max – максимальная нагрузка, Н;
b, l – толщина и длина образца в плоскости скалывания, мм. Испытания на перерезание древесины поперек волокон проводят на образцах с применением подвижного ножа. При этом предел прочности в МПа определяют по формуле:
τ = Рmax / 2 × a × b,
где Pmax – максимальная нагрузка, Н;
а и b – размеры сечения образца, мм (поперечные). Как показывают результаты испытаний, прочность древесины при перерезании поперек волокон в 4 раза больше, чем при скалывании вдоль волокон.
Как показали испытания, модули упругости при сжатии и растяжении древесины примерно одинаковы и составляют для сосны – 12,3 ГПа, для дуба – 14,6 ГПа и для березы – 16,4 ГПа при влажности 12 %. Модуль упругости поперек волокон примерно в 20–25 раз меньше, чем вдоль, а в радиальном направлении выше, чем в тангенциальном, примерно на 20–50 %.
При испытаниях древесины также определяют модуль упругости:
Е = 3 × Р × l / (64b × h3 × f),
где Р – нагрузка, равная разности между верхними и нижними пределами измерения, Н;
l – расстояние между опорами (на которых располагается образец древесины), мм;
b и h – ширина и высота образца, мм;
f — прогиб, равный разности среднеарифметических значений прогиба при верхнем и нижнем пределах нагружения, мм.
При испытании древесины на сжатие нагрузку производят вдоль волокон, затем поперек и в одном месте. Предел прочности определяют в МПа по формуле:
бсж = Рmax / a × b,
где Pmax – максимальная разрушающая нагрузка, Н;
а и b – размеры образца древесины, мм.
По данным испытаний установлено, что при растяжении древесины поперек волокон прочность составляет примерно 1/20 прочности при растяжении вдоль волокон. Поэтому при конструировании изделий и устройстве различных строительных конструкций не допускают случаев, чтобы растягивающие нагрузки были направлены поперек волокон.
На практике в большинстве случаев изделия из древесины работают с нагрузками на изгиб. Поэтому образцы древесины обязательно испытывают на изгиб, при этом определяют предел прочности в МПа по формуле:
биз = 3Рmax × l/2 × b × h2,
где l – расстояние между опорами, мм;
b – ширина образца в радиальном направлении, мм;
h – высота образца в тангенциальном направлении, мм.
При изгибании образца с выпуклой стороны возникают напряжения растяжения, а с вогнутой – сжатия. При нагрузках выше предельной величины разрушение древесины происходит в виде разрыва растянутых волокон на выпуклой стороне излома образца.
Большое значение имеет показатель прочности при сдвиге. Этот показатель определяют при испытаниях трех видов сдвига: на скалывание вдоль и поперек волокон; на перерезание древесины поперек волокон. При этом предел прочности древесины на скалывание – бск, МПа определяют по формуле:
бск = Рmax / b × l,
где P max – максимальная нагрузка, Н;
b, l – толщина и длина образца в плоскости скалывания, мм. Испытания на перерезание древесины поперек волокон проводят на образцах с применением подвижного ножа. При этом предел прочности в МПа определяют по формуле:
τ = Рmax / 2 × a × b,
где Pmax – максимальная нагрузка, Н;
а и b – размеры сечения образца, мм (поперечные). Как показывают результаты испытаний, прочность древесины при перерезании поперек волокон в 4 раза больше, чем при скалывании вдоль волокон.
Как показали испытания, модули упругости при сжатии и растяжении древесины примерно одинаковы и составляют для сосны – 12,3 ГПа, для дуба – 14,6 ГПа и для березы – 16,4 ГПа при влажности 12 %. Модуль упругости поперек волокон примерно в 20–25 раз меньше, чем вдоль, а в радиальном направлении выше, чем в тангенциальном, примерно на 20–50 %.
При испытаниях древесины также определяют модуль упругости:
Е = 3 × Р × l / (64b × h3 × f),
где Р – нагрузка, равная разности между верхними и нижними пределами измерения, Н;
l – расстояние между опорами (на которых располагается образец древесины), мм;
b и h – ширина и высота образца, мм;
f — прогиб, равный разности среднеарифметических значений прогиба при верхнем и нижнем пределах нагружения, мм.
6. Технологические свойства древесины
Технологические свойства: ударная вязкость, твердость, износоустойчивость, способность удерживать шурупы, гвозди и другие крепления, а также обрабатываемость режущими инструментами.
Ударная вязкость древесины – это ее способность поглощать усилия (работу) при ударе без разрушения. Чем больше величина работы, необходимой для излома образца, тем выше его вязкость. Ударную вязкость определяют по формуле:
A = Q/b х h, Дж/см 2,
где Q – работа, затрачиваемая на излом образца, Дж;
b и h – ширина и высота образца.
Твердость древесины – это ее способность сопротивляться вдавливанию тела из более твердого материала – стального пуансона с полусферическим наконечником радиусом r = = 5,64 мм на глубину 5,64 мм. При этом в конце нагружения по шкале силоизмерителя машины отсчитывают нагрузку Р. После испытания в древесине остается отпечаток площадью 100 мм 2. Статическую твердость образца определяют в Н/мм по формуле:
Н = Р / π × r2,
где π × r2 – площадь отпечатка в древесине при вдавливании в нее полусферы радиусом r, мм.
Если имеет место раскалывание образцов в процессе испытаний, то пуансон вдавливают на меньшую глубину – 2,82 мм, а твердость определяют по формуле:
Н = 4Р / (3π × r2).
Все породы по твердости торцовой поверхности делят на три группы: мягкие – твердостью 40 Н/мм 2 и меньше, твердые – 41–80 Н/мм 2 и очень твердые – более 80 Н/мм 2.
Износостойкость древесины характеризует ее способность сопротивляться износу при трении о поверхность абразивных элементов или микронеровностей более твердого тела. При испытании на истирание создают условия, которые имитируют реальный процесс истирания древесины, используемой для полов, лестниц, настилов. Истирания производят на специальной машине. При этом показатель истирания t вычисляют в мм по формуле:
t = h × (m1 – m2) / m1,
где h – высота образца до истирания, мм;
m 1 и m 2 – масса образца соответственно до и после испытания, г.
Удельное сопротивление выдергиванию гвоздя или шурупа определяется по формуле:
Руд. = Рmax / l (Н/мм),
где Pmax – максимальная нагрузка при выдергивании гвоздей или шурупов;
l – длина забивки гвоздя или ввинчивания шурупа. Способность древесины удерживать крепежные элементы зависит от ее породы, плотности и влажности. Сопротивление выдергиванию гвоздей, забитых в радиальном и тангенциальном направлениях, примерно одинаковое, но оно выше, чем при забивании гвоздей в торец образца.
Способность древесины к гнутью – наилучшая у бука, дуба, ясеня, хуже – у хвойных пород. Для улучшения податливости древесины перед гнутьем ее пропаривают, затем после гнутья охлаждают и сушат в зафиксированном состоянии, в результате чего она приобретает стабильную изогнутую форму.
Способность древесины раскалываться – это процесс разделения ее вдоль волокон под действием нагрузки, передаваемой на клин. Это является отрицательным свойством древесины при забивании гвоздей близко от кромки, а также костылей, шурупов при ввинчивании, но положительным – при колке дров или заготовке колотых сортиментов.
Ударная вязкость древесины – это ее способность поглощать усилия (работу) при ударе без разрушения. Чем больше величина работы, необходимой для излома образца, тем выше его вязкость. Ударную вязкость определяют по формуле:
A = Q/b х h, Дж/см 2,
где Q – работа, затрачиваемая на излом образца, Дж;
b и h – ширина и высота образца.
Твердость древесины – это ее способность сопротивляться вдавливанию тела из более твердого материала – стального пуансона с полусферическим наконечником радиусом r = = 5,64 мм на глубину 5,64 мм. При этом в конце нагружения по шкале силоизмерителя машины отсчитывают нагрузку Р. После испытания в древесине остается отпечаток площадью 100 мм 2. Статическую твердость образца определяют в Н/мм по формуле:
Н = Р / π × r2,
где π × r2 – площадь отпечатка в древесине при вдавливании в нее полусферы радиусом r, мм.
Если имеет место раскалывание образцов в процессе испытаний, то пуансон вдавливают на меньшую глубину – 2,82 мм, а твердость определяют по формуле:
Н = 4Р / (3π × r2).
Все породы по твердости торцовой поверхности делят на три группы: мягкие – твердостью 40 Н/мм 2 и меньше, твердые – 41–80 Н/мм 2 и очень твердые – более 80 Н/мм 2.
Износостойкость древесины характеризует ее способность сопротивляться износу при трении о поверхность абразивных элементов или микронеровностей более твердого тела. При испытании на истирание создают условия, которые имитируют реальный процесс истирания древесины, используемой для полов, лестниц, настилов. Истирания производят на специальной машине. При этом показатель истирания t вычисляют в мм по формуле:
t = h × (m1 – m2) / m1,
где h – высота образца до истирания, мм;
m 1 и m 2 – масса образца соответственно до и после испытания, г.
Удельное сопротивление выдергиванию гвоздя или шурупа определяется по формуле:
Руд. = Рmax / l (Н/мм),
где Pmax – максимальная нагрузка при выдергивании гвоздей или шурупов;
l – длина забивки гвоздя или ввинчивания шурупа. Способность древесины удерживать крепежные элементы зависит от ее породы, плотности и влажности. Сопротивление выдергиванию гвоздей, забитых в радиальном и тангенциальном направлениях, примерно одинаковое, но оно выше, чем при забивании гвоздей в торец образца.
Способность древесины к гнутью – наилучшая у бука, дуба, ясеня, хуже – у хвойных пород. Для улучшения податливости древесины перед гнутьем ее пропаривают, затем после гнутья охлаждают и сушат в зафиксированном состоянии, в результате чего она приобретает стабильную изогнутую форму.
Способность древесины раскалываться – это процесс разделения ее вдоль волокон под действием нагрузки, передаваемой на клин. Это является отрицательным свойством древесины при забивании гвоздей близко от кромки, а также костылей, шурупов при ввинчивании, но положительным – при колке дров или заготовке колотых сортиментов.
ЛЕКЦИЯ № 5. Сплавы
1. Строение металлов
Металлы и их сплавы – основной материал в машиностроении. Они обладают многими ценными свойствами, обусловленными в основном их внутренним строением. Мягкий и пластичный металл или сплав можно сделать твердым, хрупким, и наоборот. Для того чтобы сознательно изменять свойства металлов, необходимо знать основы их кристаллического строения. Как известно, все тела состоят из большого количества атомов, которые удерживаются силами сцепления, совершая колебания большой частоты возле точек равновесия. Поскольку атомы разных металлов различны, каждый металл имеет свои определенные свойства. Эти свойства зависят от расположения атомов между собой, характера их связей, от расстояния между ними. Если изменить расстояние между атомами или порядок их расположения, изменятся и свойства металла. В аморфных телах – смоле, стекле, канифоли и т. п. – атомы расположены беспорядочно. В металлах они находятся в определенном геометрическом порядке, образуя кристаллы, поэтому металлы являются кристаллическими телами. Металлы различаются не только порядком расположения атомов, но и кристаллической решеткой, которая представляет собой воображаемую пространственную сетку, состоящую из элементарных ячеек, в узлах которой находятся атомы.
Различают следующие кристаллические решетки металлов с плотной упаковкой атомов: кубическую объемно—центрированную, кубическую гранецентрированную и гексагональную. В ячейке кубической объемно—центрированной решетки атомы расположены в вершинах и центре куба. Такая ячейка содержит девять атомов (хром, вольфрам, ванадий, молибден, литий, а при определенных температурах – железо и другие металлы).
В ячейке кубической гранецентрированной решетки атомы находятся в вершинах куба и на пересечении диагоналей каждой плоскости. Такая ячейка имеет 14 атомов (свинец, никель, медь, золото, серебро, пластина, железо при определенных температурах и другие металлы).
Различают следующие кристаллические решетки металлов с плотной упаковкой атомов: кубическую объемно—центрированную, кубическую гранецентрированную и гексагональную. В ячейке кубической объемно—центрированной решетки атомы расположены в вершинах и центре куба. Такая ячейка содержит девять атомов (хром, вольфрам, ванадий, молибден, литий, а при определенных температурах – железо и другие металлы).
В ячейке кубической гранецентрированной решетки атомы находятся в вершинах куба и на пересечении диагоналей каждой плоскости. Такая ячейка имеет 14 атомов (свинец, никель, медь, золото, серебро, пластина, железо при определенных температурах и другие металлы).
Конец бесплатного ознакомительного фрагмента