Таблица 3.1
Перечень диагностических устройств, находящихся в передвижных ремонтных мастерских
4. РЕМОНТ ОБОРУДОВАНИЯ
4.1. Методы, стратегии и организационные формы ремонта
4.2. Ремонтные нормативы
4.3. Планирование ремонтных работ
Перечень диагностических устройств, находящихся в передвижных ремонтных мастерских
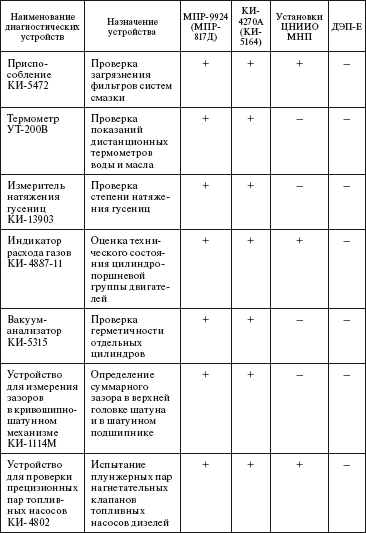
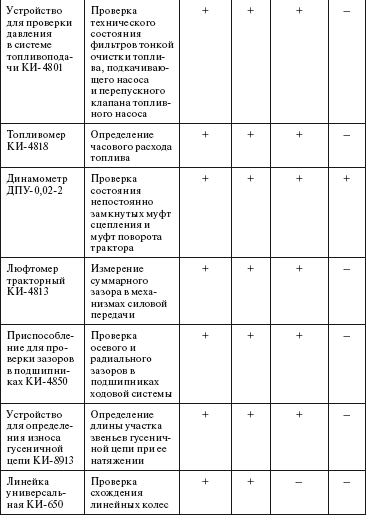
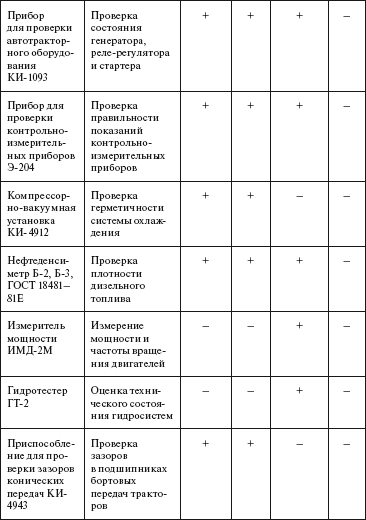
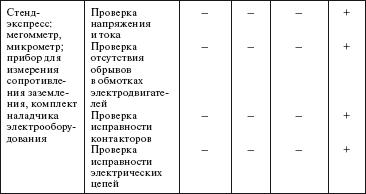
4. РЕМОНТ ОБОРУДОВАНИЯ
4.1. Методы, стратегии и организационные формы ремонта
4.1.1. Плановые ремонты являются основным видом управления техническим состоянием и восстановлением ресурса оборудования. Плановые ремонты реализуются в виде текущих и капитальных ремонтов оборудования.
4.1.2. Текущий ремонт (Т) – это ремонт, осуществляемый для восстановления работоспособности оборудования и состоящий в замене и (или) восстановлении его отдельных составных частей.
4.1.3. В зависимости от конструктивных особенностей оборудования, характера и объема проводимых работ текущие ремонты могут подразделяться на первый текущий ремонт (Т1), второй текущий ремонт (Т2) и т. д.
4.1.4. При текущем ремонте, как правило, выполняются: работы регламентированного ТО;
замена отдельных агрегатов узлов и деталей; сварочно-слесарные работы; регулировка сочленений;
ремонт футеровок и противокоррозионных покрытий; ревизия оборудования;
проверка на точность;
другие работы примерно такой же степени сложности.
4.1.5. Капитальный ремонт (К) – ремонт, выполняемый для обеспечения исправности и полного или близкого к полному восстановления ресурса оборудования с заменой или восстановлением любых его частей, включая базовые (под базовой понимают основную часть оборудования, предназначенную для компоновки и установки на нее других составных частей). Послеремонтный ресурс оборудовния должен составлять не менее 80 % ресурса нового оборудования.
4.1.6. В объем капитального ремонта входят следующие работы: объем работ текущего ремонта;
замена или восстановление всех изношенных агрегатов, узлов и деталей;
полная или частичная замена изоляции, футеровки; выверка и центровка оборудования; послеремонтные испытания.
Для выполнения капитального ремонта на предприятии должны иметься ТУ на каждое наименование ремонтируемого оборудования.
4.1.7. Перечни типовых работ при капитальном и текущем ремонтах основных наименований оборудования приведены во второй части настоящего Справочника.
4.1.8. На капитальный и на текущий ремонты оборудования составляются Ведомости дефектов (форма 3) и Сметы затрат (форма 4). Ведомость дефектов составляется с учетом технического состояния и типовой номенклатуры ремонтных работ, подписывается механиком подразделения.
4.1.9. При проведении капитального ремонта должны быть выполнены работы по техническому освидетельствованию и испытанию оборудования, подведомственного Ростехнадзору, в соответствии с требованиями действующих правил и инструкций.
4.1.10. Устранение непредвиденных инцидентов и аварий оборудования осуществляется в ходе внеплановых ремонтов. Постановка оборудования на внеплановый ремонт производится без предварительного назначения.
При проведении внепланового ремонта заменяются (или восстанавливаются) только те элементы, которые явились причиной отказа или в которых выявлено прогрессирующее развитие дефекта. Основной задачей внепланового ремонта является восстановление работоспособности оборудования и скорейшее возобновление производства (процесса), если он был прерван.
Внеплановые ремонты проводятся на основании распоряжения руководителя структурного подразделения по представлению механика.
4.1.11. Ремонт оборудования может осуществляться с применением следующих стратегий ремонта: регламентированная (I); смешанная (II);
по техническому состоянию (III); по потребности (IV).
Сущность стратегии регламентированного ремонта заключается в том, что ремонт выполняется с периодичностью и в объеме, установленном в эксплуатационной документации независимо от технического состояния составных частей оборудования в момент начала ремонта.
Сущность смешанной стратегии ремонта заключается в том, что ремонт выполняется с периодичностью, установленной в НТД, а объем операций восстановления формируется на основе требований эксплуатационной документации с учетом технического состояния основных частей оборудования.
Сущность стратегии ремонта по техническому состоянию заключается в том, что контроль технического состояния выполняется с периодичностью и в объеме, установленном в НТД, а момент начала ремонта и объем восстановления определяется техническим состоянием составных частей оборудования.
Сущность стратегии ремонта по потребности заключается в том, что ремонт оборудования производится только в случае отказа или повреждения составных частей оборудования.
4.1.12. Стратегия I применяется для обеспечения ремонта оборудования, эксплуатация которого связана с повышенной опасностью для обслуживающего персонала, в том числе оборудования, подконтрольного органам Ростехнадзора.
4.1.13. На основании стратегии II обеспечивается ремонт всего остального основного и неосновного оборудования предприятия.
4.1.14. По решению руководства предприятия часть оборудования может быть переведена на ремонт по техническому состоянию (стратегия III). Перечень такого оборудования составляется руководителем подразделения, согласовывается главным механиком предприятия и утверждается главным инженером.
4.1.15. Стратегия IV рекомендуется к применению для оборудования первой и второй амортизационной групп. Она частично реализуется в форме внеплановых ремонтов после отказов.
4.1.16. Ремонт оборудования производится в соответствии с действующим на предприятии Положением о ППР оборудования.
4.1.17. С капитальным ремонтом может быть совмещена модернизация оборудования. При модернизации оборудования решаются следующие задачи:
увеличение мощности производственного оборудования; автоматизация производственных процессов и технологических объектов;
удешевление и упрощение эксплуатации;
повышение эксплуатационной надежности, удешевление ремонта; улучшение условий труда и повышение безопасности работы.
4.1.18. Выбор объектов, определение технической направленности и объемов модернизации оборудования осуществляются Техническим советом предприятия.
4.1.19. Модернизация оборудования производится на основании Проекта модернизации, утвержденного руководителем предприятия. Руководителем модернизации оборудования является главный механик предприятия. Затраты на модернизацию в стоимость капитального ремонта не входят, а относятся на увеличение стоимости оборудования и погашаются амортизацией.
4.1.20. Ремонт и модернизация, связанные с восстановлением или изменением несущих металлоконструкций оборудования, должны производиться по технологии, согласованной с заводом-изготовителем, и в присутствии представителей Ростехнадзора.
4.1.21. Для повышения эффективности ремонтного производства на предприятии должны применяться прогрессивные формы и методы ремонта: централизованная форма и агрегатно-узловой метод.
4.1.22. Централизация ремонтной службы достигается: подчинением всех ремонтных сил и средств предприятия одному
должностному лицу (главному инженеру – заместителю руководителя предприятия на крупных предприятиях, главному механику – на средних и малых);
организацией специализированных ремонтных участков (бригад) по ремонту однотипного оборудования;
организацией изготовления в ремонтной мастерской узкой номенклатуры деталей несложной конструкции для всех типов оборудования предприятия. Ответственные детали следует приобретать по договорам у заводов – изготовителей соответствующего оборудования.
4.1.23. При организации труда ремонтных рабочих следует ориентироваться на специализированные бригады. Предпочтение следует отдавать комплексным специализированным бригадам, работающим на единый наряд с оплатой по конечным результатам.
4.1.24. Наиболее перспективным методом ремонта оборудования является агрегатный (агрегатно-узловой), при котором неисправные агрегаты и узлы заменяются новыми или отремонтированными с использованием деталей заводского изготовления.
4.1.25. Агрегатно-узловой метод всегда предпочтителен как при текущем, так и при капитальном ремонтах.
4.1.26. Одной из разновидностей агрегатно-узлового метода является рассредоточенный капитальный ремонт, при котором восстановление ресурса оборудования осуществляется в течение нескольких этапов на протяжении всего ремонтного цикла. В этом случае остановка на выполнение капитального ремонта исключается.
4.1.27. Агрегатно-узловой метод ремонта, проводимый рассредоточенным способом, особенно успешно реализуется при внедрении на предприятиях средств технической диагностики.
4.1.28. Ремонт оборудования может осуществляться собственными силами предприятий, эксплуатирующих оборудование, сторонними специализированными ремонтными предприятиями; заводами – изготовителями оборудования (фирменный ремонт). Оптимальный удельный вес каждой из перечисленных организационных форм, методов и способов ремонта для каждого конкретного предприятия зависит от многих факторов: развитости собственной ремонтной базы, ее оснащенности, удаленности от предприятий – изготовителей оборудования, специализированных ремонтных организаций (фирм), финансовых возможностей предприятия.
4.1.29. На средних и малых предприятиях создаются объединенные ремонтные мастерские и участки (посты) по ТО и ремонту оборудования. Первые производят капитальный ремонт агрегатов и узлов, а также изготовление деталей. Вторые выполняют операции регламентированного ТО и производят ремонты.
4.1.30. Комплексные бригады обычно ориентированы на ремонт одного-двух типов оборудования, комплексные – многих типов. Эти бригады, как правило, включают в себя слесарей-ремонтников, слесарей-электриков, слесарей-сварщиков, ремонтников-станочников, ремонтников газового оборудования и сетей, ремонтников вентиляционной аппаратуры и т. д.
4.1.31. Реже на малых и средних предприятиях создаются специализированные бригады, выполняющие ремонтно-восстановитель-ные работы по конкретному типу оборудования. Эта форма ремонтных работ характерна для крупных предприятий с развитой ремонтной службой.
4.1.32. На предприятиях, где использование оборудования связано с отрывом от основной базы (строительные, сельскохозяйственные, дорожные и т. д.), используются передвижные мастерские по ТО и ремонту, которые монтируются на шасси колесных и гусеничных машин.
4.1.33. Передвижные мастерские оборудованы, как правило, следующими техническими средствами:
настольно-сверлильный станок; заточный станок; токарно-винторезный станок; электроточило; сварочный трансформатор;
компрессор; кран-балка; винтовой пресс; комплект инструмента; заправочный инвентарь.
4.1.34. Работы по техническому освидетельствованию, проверкам и испытаниям оборудования осуществляются по договорам с местными органами Ростехнадзора.
4.1.2. Текущий ремонт (Т) – это ремонт, осуществляемый для восстановления работоспособности оборудования и состоящий в замене и (или) восстановлении его отдельных составных частей.
4.1.3. В зависимости от конструктивных особенностей оборудования, характера и объема проводимых работ текущие ремонты могут подразделяться на первый текущий ремонт (Т1), второй текущий ремонт (Т2) и т. д.
4.1.4. При текущем ремонте, как правило, выполняются: работы регламентированного ТО;
замена отдельных агрегатов узлов и деталей; сварочно-слесарные работы; регулировка сочленений;
ремонт футеровок и противокоррозионных покрытий; ревизия оборудования;
проверка на точность;
другие работы примерно такой же степени сложности.
4.1.5. Капитальный ремонт (К) – ремонт, выполняемый для обеспечения исправности и полного или близкого к полному восстановления ресурса оборудования с заменой или восстановлением любых его частей, включая базовые (под базовой понимают основную часть оборудования, предназначенную для компоновки и установки на нее других составных частей). Послеремонтный ресурс оборудовния должен составлять не менее 80 % ресурса нового оборудования.
4.1.6. В объем капитального ремонта входят следующие работы: объем работ текущего ремонта;
замена или восстановление всех изношенных агрегатов, узлов и деталей;
полная или частичная замена изоляции, футеровки; выверка и центровка оборудования; послеремонтные испытания.
Для выполнения капитального ремонта на предприятии должны иметься ТУ на каждое наименование ремонтируемого оборудования.
4.1.7. Перечни типовых работ при капитальном и текущем ремонтах основных наименований оборудования приведены во второй части настоящего Справочника.
4.1.8. На капитальный и на текущий ремонты оборудования составляются Ведомости дефектов (форма 3) и Сметы затрат (форма 4). Ведомость дефектов составляется с учетом технического состояния и типовой номенклатуры ремонтных работ, подписывается механиком подразделения.
4.1.9. При проведении капитального ремонта должны быть выполнены работы по техническому освидетельствованию и испытанию оборудования, подведомственного Ростехнадзору, в соответствии с требованиями действующих правил и инструкций.
4.1.10. Устранение непредвиденных инцидентов и аварий оборудования осуществляется в ходе внеплановых ремонтов. Постановка оборудования на внеплановый ремонт производится без предварительного назначения.
При проведении внепланового ремонта заменяются (или восстанавливаются) только те элементы, которые явились причиной отказа или в которых выявлено прогрессирующее развитие дефекта. Основной задачей внепланового ремонта является восстановление работоспособности оборудования и скорейшее возобновление производства (процесса), если он был прерван.
Внеплановые ремонты проводятся на основании распоряжения руководителя структурного подразделения по представлению механика.
4.1.11. Ремонт оборудования может осуществляться с применением следующих стратегий ремонта: регламентированная (I); смешанная (II);
по техническому состоянию (III); по потребности (IV).
Сущность стратегии регламентированного ремонта заключается в том, что ремонт выполняется с периодичностью и в объеме, установленном в эксплуатационной документации независимо от технического состояния составных частей оборудования в момент начала ремонта.
Сущность смешанной стратегии ремонта заключается в том, что ремонт выполняется с периодичностью, установленной в НТД, а объем операций восстановления формируется на основе требований эксплуатационной документации с учетом технического состояния основных частей оборудования.
Сущность стратегии ремонта по техническому состоянию заключается в том, что контроль технического состояния выполняется с периодичностью и в объеме, установленном в НТД, а момент начала ремонта и объем восстановления определяется техническим состоянием составных частей оборудования.
Сущность стратегии ремонта по потребности заключается в том, что ремонт оборудования производится только в случае отказа или повреждения составных частей оборудования.
4.1.12. Стратегия I применяется для обеспечения ремонта оборудования, эксплуатация которого связана с повышенной опасностью для обслуживающего персонала, в том числе оборудования, подконтрольного органам Ростехнадзора.
4.1.13. На основании стратегии II обеспечивается ремонт всего остального основного и неосновного оборудования предприятия.
4.1.14. По решению руководства предприятия часть оборудования может быть переведена на ремонт по техническому состоянию (стратегия III). Перечень такого оборудования составляется руководителем подразделения, согласовывается главным механиком предприятия и утверждается главным инженером.
4.1.15. Стратегия IV рекомендуется к применению для оборудования первой и второй амортизационной групп. Она частично реализуется в форме внеплановых ремонтов после отказов.
4.1.16. Ремонт оборудования производится в соответствии с действующим на предприятии Положением о ППР оборудования.
4.1.17. С капитальным ремонтом может быть совмещена модернизация оборудования. При модернизации оборудования решаются следующие задачи:
увеличение мощности производственного оборудования; автоматизация производственных процессов и технологических объектов;
удешевление и упрощение эксплуатации;
повышение эксплуатационной надежности, удешевление ремонта; улучшение условий труда и повышение безопасности работы.
4.1.18. Выбор объектов, определение технической направленности и объемов модернизации оборудования осуществляются Техническим советом предприятия.
4.1.19. Модернизация оборудования производится на основании Проекта модернизации, утвержденного руководителем предприятия. Руководителем модернизации оборудования является главный механик предприятия. Затраты на модернизацию в стоимость капитального ремонта не входят, а относятся на увеличение стоимости оборудования и погашаются амортизацией.
4.1.20. Ремонт и модернизация, связанные с восстановлением или изменением несущих металлоконструкций оборудования, должны производиться по технологии, согласованной с заводом-изготовителем, и в присутствии представителей Ростехнадзора.
4.1.21. Для повышения эффективности ремонтного производства на предприятии должны применяться прогрессивные формы и методы ремонта: централизованная форма и агрегатно-узловой метод.
4.1.22. Централизация ремонтной службы достигается: подчинением всех ремонтных сил и средств предприятия одному
должностному лицу (главному инженеру – заместителю руководителя предприятия на крупных предприятиях, главному механику – на средних и малых);
организацией специализированных ремонтных участков (бригад) по ремонту однотипного оборудования;
организацией изготовления в ремонтной мастерской узкой номенклатуры деталей несложной конструкции для всех типов оборудования предприятия. Ответственные детали следует приобретать по договорам у заводов – изготовителей соответствующего оборудования.
4.1.23. При организации труда ремонтных рабочих следует ориентироваться на специализированные бригады. Предпочтение следует отдавать комплексным специализированным бригадам, работающим на единый наряд с оплатой по конечным результатам.
4.1.24. Наиболее перспективным методом ремонта оборудования является агрегатный (агрегатно-узловой), при котором неисправные агрегаты и узлы заменяются новыми или отремонтированными с использованием деталей заводского изготовления.
4.1.25. Агрегатно-узловой метод всегда предпочтителен как при текущем, так и при капитальном ремонтах.
4.1.26. Одной из разновидностей агрегатно-узлового метода является рассредоточенный капитальный ремонт, при котором восстановление ресурса оборудования осуществляется в течение нескольких этапов на протяжении всего ремонтного цикла. В этом случае остановка на выполнение капитального ремонта исключается.
4.1.27. Агрегатно-узловой метод ремонта, проводимый рассредоточенным способом, особенно успешно реализуется при внедрении на предприятиях средств технической диагностики.
4.1.28. Ремонт оборудования может осуществляться собственными силами предприятий, эксплуатирующих оборудование, сторонними специализированными ремонтными предприятиями; заводами – изготовителями оборудования (фирменный ремонт). Оптимальный удельный вес каждой из перечисленных организационных форм, методов и способов ремонта для каждого конкретного предприятия зависит от многих факторов: развитости собственной ремонтной базы, ее оснащенности, удаленности от предприятий – изготовителей оборудования, специализированных ремонтных организаций (фирм), финансовых возможностей предприятия.
4.1.29. На средних и малых предприятиях создаются объединенные ремонтные мастерские и участки (посты) по ТО и ремонту оборудования. Первые производят капитальный ремонт агрегатов и узлов, а также изготовление деталей. Вторые выполняют операции регламентированного ТО и производят ремонты.
4.1.30. Комплексные бригады обычно ориентированы на ремонт одного-двух типов оборудования, комплексные – многих типов. Эти бригады, как правило, включают в себя слесарей-ремонтников, слесарей-электриков, слесарей-сварщиков, ремонтников-станочников, ремонтников газового оборудования и сетей, ремонтников вентиляционной аппаратуры и т. д.
4.1.31. Реже на малых и средних предприятиях создаются специализированные бригады, выполняющие ремонтно-восстановитель-ные работы по конкретному типу оборудования. Эта форма ремонтных работ характерна для крупных предприятий с развитой ремонтной службой.
4.1.32. На предприятиях, где использование оборудования связано с отрывом от основной базы (строительные, сельскохозяйственные, дорожные и т. д.), используются передвижные мастерские по ТО и ремонту, которые монтируются на шасси колесных и гусеничных машин.
4.1.33. Передвижные мастерские оборудованы, как правило, следующими техническими средствами:
настольно-сверлильный станок; заточный станок; токарно-винторезный станок; электроточило; сварочный трансформатор;
компрессор; кран-балка; винтовой пресс; комплект инструмента; заправочный инвентарь.
4.1.34. Работы по техническому освидетельствованию, проверкам и испытаниям оборудования осуществляются по договорам с местными органами Ростехнадзора.
4.2. Ремонтные нормативы
4.2.1. К числу основных ремонтных нормативов, необходимых для планирования и выполнения ремонта оборудования, относятся периодичность проведения, продолжительность простоя и трудоемкость выполнения ремонта. Численные значения ремонтных нормативов приведены во второй и третьей частях Сравочника.
Периодичность ремонта
4.2.2. Периодичность ремонта – это интервал наработки оборудования в часах между окончанием данного вида обслуживания (ремонта) и началом последующего такого же ремонта или другого профилактического воздействия большей (меньшей) сложности.
4.2.3. Наработка оборудования измеряется количеством отработанных часов (машино-часов). Учет работы в часах на предприятии ведется только по основному оборудованию. Наработка неосновного оборудования учитывается по наработке основного оборудования, работу которого оно обеспечивает.
4.2.4. Периодичность остановок оборудования на ТО, текущий и капитальный ремонты принята на основе показателей надежности оборудования и определяется сроками службы и техническим состоянием агрегатов, узлов и деталей соответствующего оборудования.
4.2.5. Периодичность капитального ремонта определяет длительность ремонтного цикла оборудования, в течение которого в соответствии с требованиями НТД выполняются в определенной последовательности все установленные виды ремонта. В частном случае началом отсчета ремонтного цикла может быть начало эксплуатации оборудования.
4.2.6. Периодичность остановок оборудования на текущий и капитальный ремонты принята в машино-часах работы и увязана с календарным планированием (месяц, год). При непрерывной трехсменной работе максимальная наработка оборудования в месяц составляет 720 ч, в год – 8640 ч. В условиях односменной работы к нормам периодичности применяется коэффициент 0,6, а для двухсменной работы – 0,8.
4.2.7. В зависимости от условий работы и с учетом технического состояния оборудования допускаются отклонения от нормативной периодичности ремонта:
± 20 % – для текущего ремонта; ± 15 % – для капитального ремонта.
Отклонения более указанных и ли замена одного вида ремонта другим допускаются только по решению руководителя механо-службы предприятия.
Продолжительность ремонта
4.2.8. Продолжительность ремонта – это регламентированный интервал времени (в часах) от момента вывода оборудования из эксплуатации для проведения планового ремонта до момента его ввода в эксплуатацию в нормальном режиме.
4.2.9. Продолжительность простоя оборудования в ремонте включает в себя время на подготовку оборудования к ремонту, проведение ремонта, пуск и опробование оборудования.
4.2.10. Продолжительность ремонта рассчитывается исходя из максимально возможного количества ремонтников, одновременно задействованных на ремонте единицы оборудования.
4.2.11. Началом ремонта оборудования считается время прекращения производственного процесса или вывода оборудования в ремонт из резерва по разрешению руководства механической службы предприятия.
4.2.12. Окончанием ремонта считается включение оборудования под нагрузку для нормальной эксплуатации (или вывода его в резерв).
Испытания под нагрузкой в продолжительность ремонта не входят, если в процессе испытаний отремонтированное оборудование работало нормально.
4.2.13. При модернизации оборудования продолжительность выполнения капитального ремонта увеличивается на время, необходимое для выполнения объема работ по модернизации.
4.2.14. На предприятиях, где фактическая продолжительность ремонта меньше, чем предусмотрено нормативами, ремонтные работы должны планироваться по достигнутым показателям. При этом не должно допускаться снижение качества ремонта или выполнение ремонтных работ в неполном объеме.
4.2.15. При ремонте технологического комплекса продолжительность ремонта устанавливается по наиболее сложному оборудованию, имеющему максимальную продолжительность ремонта. Если ремонт технологического комплекса не вызывает ограничения по времени и не снижает надежности оборудования, то продолжительность его ремонта может быть установлена исходя из условия наиболее рациональной загрузки ремонтного персонала.
Трудоемкость ремонта
4.2.16. Трудоемкость ремонта – это трудозатраты на проведение одного вида ремонта, выраженная в человеко-часах.
Нормативы трудоемкости даны на полный перечень ремонтных работ, включая подготовительно-заключительные работы, непосредственно связанные с проведением ремонта, приведенные к четвертому разряду работ по шестиразрядной сетке. Они установлены как максимальные величины и предназначены для ориентировочного расчета объема ремонтных работ и необходимого количества ремонтников, но не могут служить основанием для оплаты труда ремонтного персонала.
4.2.17. Нормативные значения трудоемкости приняты исходя из следующих организационно-технических условий проведения ремонта:
в период, предшествующий остановке оборудования на ремонт, производится максимально возможный объем подготовительных работ;
при текущем и капитальном ремонтах широко практикуется замена неисправных агрегатов, узлов и изношенных деталей на исправные вместо их восстановления непосредственно на оборудовании;
максимально используются грузоподъемные и транспортирующие средства, специализированный инструмент и другие средства механизации тяжелых и трудоемких работ.
4.2.18. Нормативная трудоемкость учитывает труд слесарей, станочников, монтажников, электрогазосварщиков, газорезчиков и ремонтников других специальностей, а также другого ремонтного персонала, привлекаемого для проведения ремонтных работ.
Нормативная трудоемкость охватывает следующие работы и операции:
подготовительные операции, непосредственно связанные с проведением ремонта оборудования, в том числе выполнение мероприятий, предусмотренных правилами промышленной и пожарной безопасности;
виды ремонтных работ со строповкой, перемещением агрегатов, узлов и деталей в пределах помещения, где выполняется ремонт;
разборку (и сборку) оборудования на агрегаты, узлы и детали с последующей дефектовкой;
замену неисправных агрегатов, узлов и изношенных деталей;
разборку (и сборку) отдельных агрегатов и узлов с заменой деталей и выполнением необходимых ремонтных операций;
станочные работы;
разборочно-сборочные, обмуровочные, теплоизоляционные, пропиточные, сварочные, слесарно-пригоночные и другие слесарные работы;
заключительные операции.
Нормативами трудоемкости учтено также время на регламентированный отдых и личные надобности ремонтного персонала в период выполнения ремонта.
4.2.19. Ориентировочная трудоемкость станочных работ по изготовлению быстроизнашиваемых деталей определяется исходя из структуры трудозатрат, приведенных в Приложении 7.
4.2.20. Нормативы трудоемкости установлены применительно к ремонту оборудования, не исчерпавшего нормативный срок службы, при выполнении ремонтных работ в оборудованных помещениях и в нормальных температурных условиях.
При выполнении ремонтных работ в условиях, отличных от указанных, нормативы трудоемкости уточняются в соответствии с приведенными ниже коэффициентами (к):
4.2.21. Приведенные нормативы трудоемкости являются максимально допустимыми (с учетом поправочных коэффициентов). На предприятиях, достигших более прогрессивных значений трудоемкости при соблюдении технологии ремонта, трудоемкость ремонта планируется по достигнутым показателям.
4.2.22. Отделы труда и заработной платы предприятий должны периодически проверять соответствие фактических трудозатрат нормативным и вносить предложения о необходимости их уточнения.
4.2.23. При отсутствии в нормативных разделах Справочника (части II и III) оборудования с технической характеристикой, полностью соответствующей данному оборудованию, допускается пользоваться ремонтными нормативами на оборудование того же наименования и типа с наиболее близкой к искомому технической характеристикой.
Периодичность ремонта
4.2.2. Периодичность ремонта – это интервал наработки оборудования в часах между окончанием данного вида обслуживания (ремонта) и началом последующего такого же ремонта или другого профилактического воздействия большей (меньшей) сложности.
4.2.3. Наработка оборудования измеряется количеством отработанных часов (машино-часов). Учет работы в часах на предприятии ведется только по основному оборудованию. Наработка неосновного оборудования учитывается по наработке основного оборудования, работу которого оно обеспечивает.
4.2.4. Периодичность остановок оборудования на ТО, текущий и капитальный ремонты принята на основе показателей надежности оборудования и определяется сроками службы и техническим состоянием агрегатов, узлов и деталей соответствующего оборудования.
4.2.5. Периодичность капитального ремонта определяет длительность ремонтного цикла оборудования, в течение которого в соответствии с требованиями НТД выполняются в определенной последовательности все установленные виды ремонта. В частном случае началом отсчета ремонтного цикла может быть начало эксплуатации оборудования.
4.2.6. Периодичность остановок оборудования на текущий и капитальный ремонты принята в машино-часах работы и увязана с календарным планированием (месяц, год). При непрерывной трехсменной работе максимальная наработка оборудования в месяц составляет 720 ч, в год – 8640 ч. В условиях односменной работы к нормам периодичности применяется коэффициент 0,6, а для двухсменной работы – 0,8.
4.2.7. В зависимости от условий работы и с учетом технического состояния оборудования допускаются отклонения от нормативной периодичности ремонта:
± 20 % – для текущего ремонта; ± 15 % – для капитального ремонта.
Отклонения более указанных и ли замена одного вида ремонта другим допускаются только по решению руководителя механо-службы предприятия.
Продолжительность ремонта
4.2.8. Продолжительность ремонта – это регламентированный интервал времени (в часах) от момента вывода оборудования из эксплуатации для проведения планового ремонта до момента его ввода в эксплуатацию в нормальном режиме.
4.2.9. Продолжительность простоя оборудования в ремонте включает в себя время на подготовку оборудования к ремонту, проведение ремонта, пуск и опробование оборудования.
4.2.10. Продолжительность ремонта рассчитывается исходя из максимально возможного количества ремонтников, одновременно задействованных на ремонте единицы оборудования.
4.2.11. Началом ремонта оборудования считается время прекращения производственного процесса или вывода оборудования в ремонт из резерва по разрешению руководства механической службы предприятия.
4.2.12. Окончанием ремонта считается включение оборудования под нагрузку для нормальной эксплуатации (или вывода его в резерв).
Испытания под нагрузкой в продолжительность ремонта не входят, если в процессе испытаний отремонтированное оборудование работало нормально.
4.2.13. При модернизации оборудования продолжительность выполнения капитального ремонта увеличивается на время, необходимое для выполнения объема работ по модернизации.
4.2.14. На предприятиях, где фактическая продолжительность ремонта меньше, чем предусмотрено нормативами, ремонтные работы должны планироваться по достигнутым показателям. При этом не должно допускаться снижение качества ремонта или выполнение ремонтных работ в неполном объеме.
4.2.15. При ремонте технологического комплекса продолжительность ремонта устанавливается по наиболее сложному оборудованию, имеющему максимальную продолжительность ремонта. Если ремонт технологического комплекса не вызывает ограничения по времени и не снижает надежности оборудования, то продолжительность его ремонта может быть установлена исходя из условия наиболее рациональной загрузки ремонтного персонала.
Трудоемкость ремонта
4.2.16. Трудоемкость ремонта – это трудозатраты на проведение одного вида ремонта, выраженная в человеко-часах.
Нормативы трудоемкости даны на полный перечень ремонтных работ, включая подготовительно-заключительные работы, непосредственно связанные с проведением ремонта, приведенные к четвертому разряду работ по шестиразрядной сетке. Они установлены как максимальные величины и предназначены для ориентировочного расчета объема ремонтных работ и необходимого количества ремонтников, но не могут служить основанием для оплаты труда ремонтного персонала.
4.2.17. Нормативные значения трудоемкости приняты исходя из следующих организационно-технических условий проведения ремонта:
в период, предшествующий остановке оборудования на ремонт, производится максимально возможный объем подготовительных работ;
при текущем и капитальном ремонтах широко практикуется замена неисправных агрегатов, узлов и изношенных деталей на исправные вместо их восстановления непосредственно на оборудовании;
максимально используются грузоподъемные и транспортирующие средства, специализированный инструмент и другие средства механизации тяжелых и трудоемких работ.
4.2.18. Нормативная трудоемкость учитывает труд слесарей, станочников, монтажников, электрогазосварщиков, газорезчиков и ремонтников других специальностей, а также другого ремонтного персонала, привлекаемого для проведения ремонтных работ.
Нормативная трудоемкость охватывает следующие работы и операции:
подготовительные операции, непосредственно связанные с проведением ремонта оборудования, в том числе выполнение мероприятий, предусмотренных правилами промышленной и пожарной безопасности;
виды ремонтных работ со строповкой, перемещением агрегатов, узлов и деталей в пределах помещения, где выполняется ремонт;
разборку (и сборку) оборудования на агрегаты, узлы и детали с последующей дефектовкой;
замену неисправных агрегатов, узлов и изношенных деталей;
разборку (и сборку) отдельных агрегатов и узлов с заменой деталей и выполнением необходимых ремонтных операций;
станочные работы;
разборочно-сборочные, обмуровочные, теплоизоляционные, пропиточные, сварочные, слесарно-пригоночные и другие слесарные работы;
заключительные операции.
Нормативами трудоемкости учтено также время на регламентированный отдых и личные надобности ремонтного персонала в период выполнения ремонта.
4.2.19. Ориентировочная трудоемкость станочных работ по изготовлению быстроизнашиваемых деталей определяется исходя из структуры трудозатрат, приведенных в Приложении 7.
4.2.20. Нормативы трудоемкости установлены применительно к ремонту оборудования, не исчерпавшего нормативный срок службы, при выполнении ремонтных работ в оборудованных помещениях и в нормальных температурных условиях.
При выполнении ремонтных работ в условиях, отличных от указанных, нормативы трудоемкости уточняются в соответствии с приведенными ниже коэффициентами (к):
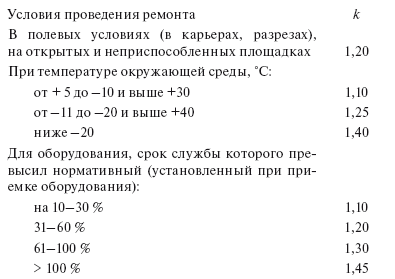
4.2.21. Приведенные нормативы трудоемкости являются максимально допустимыми (с учетом поправочных коэффициентов). На предприятиях, достигших более прогрессивных значений трудоемкости при соблюдении технологии ремонта, трудоемкость ремонта планируется по достигнутым показателям.
4.2.22. Отделы труда и заработной платы предприятий должны периодически проверять соответствие фактических трудозатрат нормативным и вносить предложения о необходимости их уточнения.
4.2.23. При отсутствии в нормативных разделах Справочника (части II и III) оборудования с технической характеристикой, полностью соответствующей данному оборудованию, допускается пользоваться ремонтными нормативами на оборудование того же наименования и типа с наиболее близкой к искомому технической характеристикой.
4.3. Планирование ремонтных работ
4.3.1. Основными документами по планированию ремонта оборудования являются:
ведомость годовых затрат на ремонты (форма 9); годовой план-график ППР оборудования (форма 7); месячный план-график-отчет ППР (форма 8) или месячный отчет о ремонтах (форма 8А).
4.3.2. Ведомость годовых затрат на ремонт оборудования разрабатывается ОГМ на основе проектов ведомостей годовых затрат на ремонт оборудования подразделений, ремонтной и сметной документации на текущий и капитальный ремонты.
В проекты ведомостей годовых затрат включаются также затраты, связанные с проведением ТО.
4.3.3. На основании проектов ведомостей годовых затрат на ремонты подразделений ОГМ составляет ведомость годовых затрат на ремонт по предприятию, которую начальник ОГМ подписывает и направляет в планово-экономический отдел предприятия к 15 января года, предшествующего планируемому. Допускается представление проектов годовых затрат подразделений непосредственно в планово-экономический отдел.
Общая сумма годовых затрат на ремонты не может превышать годовых затрат, расчет которых рассматривается в п. 4.6.
4.3.4. Годовые планы-графики ППР оборудования составляются механиками подразделений, которые предварительно согласовывают их с другими службами предприятия и представляют в трех экземплярах в ОГМ к 10 ноября года, предшествующего планируемому.
4.3.5. Представленные годовые планы-графики подписываются главным механиком, согласовываются с главным энергетиком (при наличии такового), с производственным отделом и утверждаются главным инженером предприятия. Один экземпляр утвержденных графиков ОГМ направляет в подразделения, другой экземпляр остается в ОГМ для контроля.
4.3.6. В годовые планы-графики ППР включается все оборудование, подлежащее ремонту в планируемом году, а также регламентированному ТО.
4.3.7. Месячные планы-графики-отчеты ремонта[1] составляют механики подразделений на основе годовых планов-графиков ремонта оборудования, согласовывают их со службами производства, подписывают у руководителя подразделения и представляют на утверждение главному механику за десять дней до конца месяца, предшествующего планируемому. В месячные графики включается регламентированное ТО.
4.3.8. Календарные сроки ремонта неосновного оборудования по месячному плану-графику-отчету, как правило, приурочиваются к срокам ремонта основного оборудования, работу которого оно обеспечивает.
4.3.9. Утвержденные месячные графики ремонта не позднее чем за неделю до начала планируемого месяца направляются в подразделения по принадлежности и являются для них планом-заданием на предстоящий месяц. Они же являются и отчетным документом о производственной деятельности ремонтного персонала.
ведомость годовых затрат на ремонты (форма 9); годовой план-график ППР оборудования (форма 7); месячный план-график-отчет ППР (форма 8) или месячный отчет о ремонтах (форма 8А).
4.3.2. Ведомость годовых затрат на ремонт оборудования разрабатывается ОГМ на основе проектов ведомостей годовых затрат на ремонт оборудования подразделений, ремонтной и сметной документации на текущий и капитальный ремонты.
В проекты ведомостей годовых затрат включаются также затраты, связанные с проведением ТО.
4.3.3. На основании проектов ведомостей годовых затрат на ремонты подразделений ОГМ составляет ведомость годовых затрат на ремонт по предприятию, которую начальник ОГМ подписывает и направляет в планово-экономический отдел предприятия к 15 января года, предшествующего планируемому. Допускается представление проектов годовых затрат подразделений непосредственно в планово-экономический отдел.
Общая сумма годовых затрат на ремонты не может превышать годовых затрат, расчет которых рассматривается в п. 4.6.
4.3.4. Годовые планы-графики ППР оборудования составляются механиками подразделений, которые предварительно согласовывают их с другими службами предприятия и представляют в трех экземплярах в ОГМ к 10 ноября года, предшествующего планируемому.
4.3.5. Представленные годовые планы-графики подписываются главным механиком, согласовываются с главным энергетиком (при наличии такового), с производственным отделом и утверждаются главным инженером предприятия. Один экземпляр утвержденных графиков ОГМ направляет в подразделения, другой экземпляр остается в ОГМ для контроля.
4.3.6. В годовые планы-графики ППР включается все оборудование, подлежащее ремонту в планируемом году, а также регламентированному ТО.
4.3.7. Месячные планы-графики-отчеты ремонта[1] составляют механики подразделений на основе годовых планов-графиков ремонта оборудования, согласовывают их со службами производства, подписывают у руководителя подразделения и представляют на утверждение главному механику за десять дней до конца месяца, предшествующего планируемому. В месячные графики включается регламентированное ТО.
4.3.8. Календарные сроки ремонта неосновного оборудования по месячному плану-графику-отчету, как правило, приурочиваются к срокам ремонта основного оборудования, работу которого оно обеспечивает.
4.3.9. Утвержденные месячные графики ремонта не позднее чем за неделю до начала планируемого месяца направляются в подразделения по принадлежности и являются для них планом-заданием на предстоящий месяц. Они же являются и отчетным документом о производственной деятельности ремонтного персонала.
Конец бесплатного ознакомительного фрагмента