Страница:
Александр Игнатьевич Ящура
Система технического обслуживания и ремонта общепромышленного оборудования: Справочник
Введение
Подавляющее количество действующих в настоящее время предприятий – малые и средние, появившиеся в 1995–2005 гг. Часть из них возникла на базе прежних промышленных гигантов в результате их своеобразного «разукрупнения» в процессе развития свободного предпринимательства. Большинство же создавалось на «голом месте» с целью заполнения отдельных ниш на все более конкурентном рынке промышленных продуктов, товаров и услуг.
Новообразованные предприятия укомплектовывались, как правило, машинами, механизмами, технологическим оборудованием выпуска до 1985 г., а также импортным оборудованием.
В соответствии с главной задачей вновь создаваемых предприятий – получение максимальной прибыли в короткие сроки – не всегда находились время и силы для рационального использования техники, в том числе разработки рекомендаций по техническому обслуживанию и ремонту оборудования.
Освободившиеся от министерской опеки бывшие государственные предприятия зачастую стали игнорировать ведомственные нормативные документы, считая их требования излишними.
В стране образовалось две группы собственников фондов. Одна – бывшие промышленные государственные предприятия, по традиции, хотя и с оговорками, соблюдавшие директивные указания по эксплуатации, техническому обслуживанию и ремонту оборудования бывших министерств и ведомств. Другая – «вольница», для которой не существовало каких-либо обязательных требований к технической эксплуатации оборудования.
В последние десятилетия в добывающих отраслях промышленности страны имело место большое количество аварий, связанных с использованием устаревшего и неисправного оборудования. Это побудило Госгортехнадзор России (в настоящее время – Ростехнадзор) разработать и выпустить Правила безопасности ПБ 05-356.00, которые требуют наличия на каждом предприятии собственных Положений по планово-предупредительному ремонту принадлежащего ему оборудования, регламентирующих безопасную техническую эксплуатацию оборудования. Такие положения до настоящего времени не разработаны и не введены в действие в подавляющем большинстве предприятий вследствие необходимости значительных финансовых затрат, а также из-за недостатка квалифицированных специалистов.
После выпуска ПБ 05-356.00 в правительственные органы поступило около тысячи предложений о необходимости издания единого Положения, регламентирующего эксплуатацию, техническое обслуживание и ремонт машин и оборудования. Начатые в 2003 г. работы по созданию Справочника «Единое положение по планово-предупредительным ремонтам оборудования промышленных предприятий России» (Распоряжение № 05-900/14-108, от 29.05.2003 г.) были прекращены в связи с реорганизацией основного заказчика разработки – Минпромнауки России, несмотря на настоятельную потребность в подобном документе.
Появились новые законодательные документы, регламентирующие правила технической эксплуатации оборудования, в частности:
Федеральный Закон № 57-ФЗ от 27.07.2002 г. «Налоговый кодекс Российской Федерации»;
постановление Правительства РФ № 1 от 01.01.2002 г. «Классификация основных средств, включаемых в амортизационные группы» с новыми нормативными сроками службы оборудования;
приказ Минфина РФ № 264н от 30.03.2001 г. «Положение о бухгалтерском учете»; с новым порядком финансирования техобслуживания и ремонта,
а также ряд других документов федерального уровня, касающихся организации ремонтного производства.
Сегодня предприятия самостоятельно несут ответственность за планирование и организацию ремонтов для обеспечения постоянной работоспособности оборудования. При этом одновременно расширяются их права по многим важным направлениям, включая:
финансирование ремонта и его материального обеспечения;
регулирование численности ремонтного и оперативного персонала;
применение различных стратегий ремонта;
планирование ремонта с учетом полезного использования и ужесточенных сроков службы оборудования и другие вопросы.
В 2005 г. вышел в свет справочник «Система технического обслуживания и ремонта энергетического оборудования» (М.: Изд-во НЦ ЭНАС, 2005). Настоящий Справочник является продолжением и дополнением этого издания в части общепромышленного оборудования. И если предыдущий справочник предназначен, главным образом, для специалистов служб главного энергетика, то данный справочник ориентирован на службы главного механика промышленных предприятий. Поскольку отдельные виды энергетического оборудования по решению руководства предприятия могут находиться в ведении службы главного механика, данные по таким видам оборудования включены также и в настоящее издание.
Материалы справочника, имеющие рекомендательный характер, помогут предприятиям в разработке собственных Положений по техническому обслуживанию и ремонту оборудования, послужат необходимой методической базой для реализации новых прав и ответственности, нормативной базой для обеспечения эффективного планирования ремонтных работ, потребностей в материальных и финансовых ресурсах, а также инструментом для выработки правильных организационных решений по совершенствованию ремонтной службы.
Справочник состоит из трех частей:
Часть I. Эксплуатация, техническое обслуживание и ремонт общепромышленного оборудования.
Часть II. Типовая номенклатура ремонтных работ, ремонтные нормативы общепромышленного оборудования.
Часть III. Приложения, содержащие необходимые методические и справочные материалы, для организации эффективной эксплуатации, ТО и ремонта оборудования.
Для правильного восприятия текста и исключения разночтений в формулировках рекомендуется внимательно ознакомиться с Приложением 1 «Основные понятия, термины, определения», а также с принятыми в Справочнике сокращениями (Приложение 12).
Предложения и замечания по настоящему Справочнику следует направлять по адресу: 115201, Россия, г. Москва, Каширское ш., д. 22, корп. 3, Издательство НЦ ЭНАС.
Новообразованные предприятия укомплектовывались, как правило, машинами, механизмами, технологическим оборудованием выпуска до 1985 г., а также импортным оборудованием.
В соответствии с главной задачей вновь создаваемых предприятий – получение максимальной прибыли в короткие сроки – не всегда находились время и силы для рационального использования техники, в том числе разработки рекомендаций по техническому обслуживанию и ремонту оборудования.
Освободившиеся от министерской опеки бывшие государственные предприятия зачастую стали игнорировать ведомственные нормативные документы, считая их требования излишними.
В стране образовалось две группы собственников фондов. Одна – бывшие промышленные государственные предприятия, по традиции, хотя и с оговорками, соблюдавшие директивные указания по эксплуатации, техническому обслуживанию и ремонту оборудования бывших министерств и ведомств. Другая – «вольница», для которой не существовало каких-либо обязательных требований к технической эксплуатации оборудования.
В последние десятилетия в добывающих отраслях промышленности страны имело место большое количество аварий, связанных с использованием устаревшего и неисправного оборудования. Это побудило Госгортехнадзор России (в настоящее время – Ростехнадзор) разработать и выпустить Правила безопасности ПБ 05-356.00, которые требуют наличия на каждом предприятии собственных Положений по планово-предупредительному ремонту принадлежащего ему оборудования, регламентирующих безопасную техническую эксплуатацию оборудования. Такие положения до настоящего времени не разработаны и не введены в действие в подавляющем большинстве предприятий вследствие необходимости значительных финансовых затрат, а также из-за недостатка квалифицированных специалистов.
После выпуска ПБ 05-356.00 в правительственные органы поступило около тысячи предложений о необходимости издания единого Положения, регламентирующего эксплуатацию, техническое обслуживание и ремонт машин и оборудования. Начатые в 2003 г. работы по созданию Справочника «Единое положение по планово-предупредительным ремонтам оборудования промышленных предприятий России» (Распоряжение № 05-900/14-108, от 29.05.2003 г.) были прекращены в связи с реорганизацией основного заказчика разработки – Минпромнауки России, несмотря на настоятельную потребность в подобном документе.
Появились новые законодательные документы, регламентирующие правила технической эксплуатации оборудования, в частности:
Федеральный Закон № 57-ФЗ от 27.07.2002 г. «Налоговый кодекс Российской Федерации»;
постановление Правительства РФ № 1 от 01.01.2002 г. «Классификация основных средств, включаемых в амортизационные группы» с новыми нормативными сроками службы оборудования;
приказ Минфина РФ № 264н от 30.03.2001 г. «Положение о бухгалтерском учете»; с новым порядком финансирования техобслуживания и ремонта,
а также ряд других документов федерального уровня, касающихся организации ремонтного производства.
Сегодня предприятия самостоятельно несут ответственность за планирование и организацию ремонтов для обеспечения постоянной работоспособности оборудования. При этом одновременно расширяются их права по многим важным направлениям, включая:
финансирование ремонта и его материального обеспечения;
регулирование численности ремонтного и оперативного персонала;
применение различных стратегий ремонта;
планирование ремонта с учетом полезного использования и ужесточенных сроков службы оборудования и другие вопросы.
В 2005 г. вышел в свет справочник «Система технического обслуживания и ремонта энергетического оборудования» (М.: Изд-во НЦ ЭНАС, 2005). Настоящий Справочник является продолжением и дополнением этого издания в части общепромышленного оборудования. И если предыдущий справочник предназначен, главным образом, для специалистов служб главного энергетика, то данный справочник ориентирован на службы главного механика промышленных предприятий. Поскольку отдельные виды энергетического оборудования по решению руководства предприятия могут находиться в ведении службы главного механика, данные по таким видам оборудования включены также и в настоящее издание.
Материалы справочника, имеющие рекомендательный характер, помогут предприятиям в разработке собственных Положений по техническому обслуживанию и ремонту оборудования, послужат необходимой методической базой для реализации новых прав и ответственности, нормативной базой для обеспечения эффективного планирования ремонтных работ, потребностей в материальных и финансовых ресурсах, а также инструментом для выработки правильных организационных решений по совершенствованию ремонтной службы.
Справочник состоит из трех частей:
Часть I. Эксплуатация, техническое обслуживание и ремонт общепромышленного оборудования.
Часть II. Типовая номенклатура ремонтных работ, ремонтные нормативы общепромышленного оборудования.
Часть III. Приложения, содержащие необходимые методические и справочные материалы, для организации эффективной эксплуатации, ТО и ремонта оборудования.
Для правильного восприятия текста и исключения разночтений в формулировках рекомендуется внимательно ознакомиться с Приложением 1 «Основные понятия, термины, определения», а также с принятыми в Справочнике сокращениями (Приложение 12).
Предложения и замечания по настоящему Справочнику следует направлять по адресу: 115201, Россия, г. Москва, Каширское ш., д. 22, корп. 3, Издательство НЦ ЭНАС.
Часть I
ЭКСПЛУАТАЦИЯ, ТЕХНИЧЕСКОЕ ОБСЛУЖИВАНИЕ И РЕМОНТ ОБЩЕПРОМЫШЛЕННОГО ОБОРУДОВАНИЯ
1. СЛУЖБА ГЛАВНОГО МЕХАНИКА И СИСТЕМА ПЛАНОВО-ПРЕДУПРЕДИТЕЛЬНОГО РЕМОНТА
1.1. Общая концепция системы технического обслуживания и ремонта оборудования
1.1.1. Общей концепцией поддержания оборудования в исправном состоянии и постоянной работоспособности является внедрение системы планово-предупредительного ремонта (ППР), которая законодательно закреплена в ГОСТ для внедрения на всех предприятиях страны.
1.1.2. Система технического обслуживания (ТО) и ремонта – это совокупность взаимосвязанных технических средств, документации, исполнителей, необходимых для поддержания и восстановления качества оборудования (ГОСТ 18322—78).
1.1.3. Система ППР представляет собой комплекс организационно-технических мероприятий, проводимых в плановом порядке для обеспечения работоспособности и исправности машин, оборудования, механизмов (далее – оборудования) в течение всего срока их службы при соблюдении заданных условий и режимов эксплуатации. Эти мероприятия разрабатываются и осуществляются при эксплуатации оборудования с обязательным выполнением указаний инструкций заводов-изготовителей, а также требований к техническому состоянию оборудования и правил безопасной эксплуатации, установленных Ростехнадзором.
1.1.4. Система ППР основана на планировании ремонтов и носит предупредительный характер. Это означает, что все мероприятия по поддержанию работоспособности оборудования выполняются в соответствии с годовыми и месячными графиками, составленными так, чтобы предупредить преждевременный и неожиданный выход оборудования из строя.
1.1.5. Планово-предупредительный характер Системы ППР реализуется:
проведением с заданной периодичностью ремонтов оборудования, сроки выполнения и материально-техническое обеспечение которых планируется заранее;
выполнением в полном объеме операций ТО, направленных на обеспечение безотказной работы оборудования;
сокращением времени нахождения оборудования в ремонте (в первую очередь капитальном);
обеспечением сроков полезного использования оборудования.
1.1.6. Рекомендации настоящего Справочника разрабатывались с учетом новых экономических и правовых условий, а в техническом плане – при максимальном использовании:
возможностей и преимуществ агрегатно-узлового метода ремонта;
всего спектра стратегий, форм и методов ТО и ремонта, в т. ч. новых средств и методов технической диагностики (ТД);
современной вычислительной техники и компьютерных технологий сбора, накопления и обработки информации о состоянии оборудования, планирования ремонтно-профилактических воздействий и их материально-технического обеспечения.
1.1.7. Действие Системы ППР распространяется на общепромышленное оборудование вне зависимости от места его нахождения и использования.
1.1.8. Все эксплуатируемое на предприятиях оборудование подразделяется на основное и неосновное.
Основным является оборудование, при непосредственном участии которого осуществляются основные производственные (технологические) процессы получения продукта (оказания услуг) и выход которого из строя приводит к прекращению или резкому сокращению выпуска продукции.
Неосновное оборудование обеспечивает полноценное протекание производственных процессов и работу основного оборудования.
В зависимости от производственной значимости и выполняемых функций в производственных процессах оборудование одного и того же вида и наименования может быть отнесено как к основному, так и к неосновному.
1.1.9. Система ППР предусматривает, что потребность оборудования в ремонтно-профилактических воздействиях удовлетворяется сочетанием различных видов ремонтно-профилактических воздействий, различающихся периодичностью и составом работ.
В зависимости от производственной значимости оборудования, влияния его отказов на безопасность персонала и стабильность производственных и технологических процессов ремонтные воздействия могут реализоваться в виде регламентированного ремонта, ремонта по наработке, ремонта по техническому состоянию, либо в виде их сочетания.
1.1.10. На практике перечень оборудования, ремонт которого может быть основан только на принципах и стратегиях регламентированного ремонта, крайне узок. Фактически ремонт большей части оборудования неизбежно основан на сочетании (в различных пропорциях) регламентированного ремонта и ремонта по техническому состоянию. В этом случае «каркас» структуры ремонтного цикла определяется совокупностью элементов оборудования, ремонт которых основан на стратегиях регламентированного ремонта или ремонта по наработке. На полученную «жесткую» основу структуры ремонтного цикла оборудования накладываются (в «нежестком» варианте) сроки проведения ремонта отдельных элементов, обслуживаемых по техническому состоянию.
1.1.11. Наиболее перспективным методом ремонта оборудования для предприятий любых форм собственности является агрегатно-узловой метод, при котором неисправные сменные элементы (агрегаты, узлы и детали) заменяются новыми или отремонтированными, взятыми из оборотного фонда.
Особенно эффективным является т. н. рассредоточенный агрегатно-узловой метод, при котором даже капитальный ремонт выполняется в течение всего ремонтного цикла; при этом замену неисправных узлов и агрегатов приурочивают к срокам проведения ТО или текущего ремонта.
В ряде зарубежных стран замена неисправных агрегатов и узлов приурочивается к плановым срокам проведения ТО, а сам ремонт называется «планово-предупредительное обслуживание».
1.1.12. Задача своевременной замены неисправных агрегатов, узлов и деталей наиболее успешно решается при внедрении ТД оборудования в процессе его ТО и ремонта.
1.1.13. Ремонт оборудования может осуществляться собственными силами предприятий, эксплуатирующих оборудование, сторонними специализированными ремонтными предприятиями, а также специализированными подразделениями заводов-изготовителей. Удельный вес каждой из перечисленных организационных форм ремонта для конкретного предприятия зависит от многих факторов: развитости собственной ремонтной базы, ее оснащенности, удаленности от предприятий – изготовителей оборудования и специализированных ремонтных организаций, а также финансовых возможностей предприятия.
1.1.14. Каждое предприятие вправе выбрать любую стратегию (форму, метод) ППР, наиболее полно отвечающую целям производства и обеспечивающую получение максимальной прибыли.
1.1.15. При наличии на предприятии крупного технологического и энергетического оборудования, подвижного состава, сложных технологических (производственных) процессов с целью повышения ответственности за постоянную работоспособность оборудования на предприятиях вводится должность заместителя руководителя по основным фондам. В переходный период обязанности заместителя руководителя по основным фондам возлагаются на главного инженера; в этом случае его должность называется главный инженер – заместитель руководителя предприятия. В обоих случаях заместитель руководителя по основным фондам единолично несет ответственность за содержание, ТО и ремонт всех фондов предприятия.
1.1.16. Планирование ТО, текущего и капитального ремонта осуществляется на основе разрабатываемых и утверждаемых нормативов ППР (периодичности, продолжительности и трудоемкости). В настоящем Справочнике приведены опытно-статистические данные, которые могут быть использованы при разработке соответствующих нормативов на конкретных предприятиях.
1.1.2. Система технического обслуживания (ТО) и ремонта – это совокупность взаимосвязанных технических средств, документации, исполнителей, необходимых для поддержания и восстановления качества оборудования (ГОСТ 18322—78).
1.1.3. Система ППР представляет собой комплекс организационно-технических мероприятий, проводимых в плановом порядке для обеспечения работоспособности и исправности машин, оборудования, механизмов (далее – оборудования) в течение всего срока их службы при соблюдении заданных условий и режимов эксплуатации. Эти мероприятия разрабатываются и осуществляются при эксплуатации оборудования с обязательным выполнением указаний инструкций заводов-изготовителей, а также требований к техническому состоянию оборудования и правил безопасной эксплуатации, установленных Ростехнадзором.
1.1.4. Система ППР основана на планировании ремонтов и носит предупредительный характер. Это означает, что все мероприятия по поддержанию работоспособности оборудования выполняются в соответствии с годовыми и месячными графиками, составленными так, чтобы предупредить преждевременный и неожиданный выход оборудования из строя.
1.1.5. Планово-предупредительный характер Системы ППР реализуется:
проведением с заданной периодичностью ремонтов оборудования, сроки выполнения и материально-техническое обеспечение которых планируется заранее;
выполнением в полном объеме операций ТО, направленных на обеспечение безотказной работы оборудования;
сокращением времени нахождения оборудования в ремонте (в первую очередь капитальном);
обеспечением сроков полезного использования оборудования.
1.1.6. Рекомендации настоящего Справочника разрабатывались с учетом новых экономических и правовых условий, а в техническом плане – при максимальном использовании:
возможностей и преимуществ агрегатно-узлового метода ремонта;
всего спектра стратегий, форм и методов ТО и ремонта, в т. ч. новых средств и методов технической диагностики (ТД);
современной вычислительной техники и компьютерных технологий сбора, накопления и обработки информации о состоянии оборудования, планирования ремонтно-профилактических воздействий и их материально-технического обеспечения.
1.1.7. Действие Системы ППР распространяется на общепромышленное оборудование вне зависимости от места его нахождения и использования.
1.1.8. Все эксплуатируемое на предприятиях оборудование подразделяется на основное и неосновное.
Основным является оборудование, при непосредственном участии которого осуществляются основные производственные (технологические) процессы получения продукта (оказания услуг) и выход которого из строя приводит к прекращению или резкому сокращению выпуска продукции.
Неосновное оборудование обеспечивает полноценное протекание производственных процессов и работу основного оборудования.
В зависимости от производственной значимости и выполняемых функций в производственных процессах оборудование одного и того же вида и наименования может быть отнесено как к основному, так и к неосновному.
1.1.9. Система ППР предусматривает, что потребность оборудования в ремонтно-профилактических воздействиях удовлетворяется сочетанием различных видов ремонтно-профилактических воздействий, различающихся периодичностью и составом работ.
В зависимости от производственной значимости оборудования, влияния его отказов на безопасность персонала и стабильность производственных и технологических процессов ремонтные воздействия могут реализоваться в виде регламентированного ремонта, ремонта по наработке, ремонта по техническому состоянию, либо в виде их сочетания.
1.1.10. На практике перечень оборудования, ремонт которого может быть основан только на принципах и стратегиях регламентированного ремонта, крайне узок. Фактически ремонт большей части оборудования неизбежно основан на сочетании (в различных пропорциях) регламентированного ремонта и ремонта по техническому состоянию. В этом случае «каркас» структуры ремонтного цикла определяется совокупностью элементов оборудования, ремонт которых основан на стратегиях регламентированного ремонта или ремонта по наработке. На полученную «жесткую» основу структуры ремонтного цикла оборудования накладываются (в «нежестком» варианте) сроки проведения ремонта отдельных элементов, обслуживаемых по техническому состоянию.
1.1.11. Наиболее перспективным методом ремонта оборудования для предприятий любых форм собственности является агрегатно-узловой метод, при котором неисправные сменные элементы (агрегаты, узлы и детали) заменяются новыми или отремонтированными, взятыми из оборотного фонда.
Особенно эффективным является т. н. рассредоточенный агрегатно-узловой метод, при котором даже капитальный ремонт выполняется в течение всего ремонтного цикла; при этом замену неисправных узлов и агрегатов приурочивают к срокам проведения ТО или текущего ремонта.
В ряде зарубежных стран замена неисправных агрегатов и узлов приурочивается к плановым срокам проведения ТО, а сам ремонт называется «планово-предупредительное обслуживание».
1.1.12. Задача своевременной замены неисправных агрегатов, узлов и деталей наиболее успешно решается при внедрении ТД оборудования в процессе его ТО и ремонта.
1.1.13. Ремонт оборудования может осуществляться собственными силами предприятий, эксплуатирующих оборудование, сторонними специализированными ремонтными предприятиями, а также специализированными подразделениями заводов-изготовителей. Удельный вес каждой из перечисленных организационных форм ремонта для конкретного предприятия зависит от многих факторов: развитости собственной ремонтной базы, ее оснащенности, удаленности от предприятий – изготовителей оборудования и специализированных ремонтных организаций, а также финансовых возможностей предприятия.
1.1.14. Каждое предприятие вправе выбрать любую стратегию (форму, метод) ППР, наиболее полно отвечающую целям производства и обеспечивающую получение максимальной прибыли.
1.1.15. При наличии на предприятии крупного технологического и энергетического оборудования, подвижного состава, сложных технологических (производственных) процессов с целью повышения ответственности за постоянную работоспособность оборудования на предприятиях вводится должность заместителя руководителя по основным фондам. В переходный период обязанности заместителя руководителя по основным фондам возлагаются на главного инженера; в этом случае его должность называется главный инженер – заместитель руководителя предприятия. В обоих случаях заместитель руководителя по основным фондам единолично несет ответственность за содержание, ТО и ремонт всех фондов предприятия.
1.1.16. Планирование ТО, текущего и капитального ремонта осуществляется на основе разрабатываемых и утверждаемых нормативов ППР (периодичности, продолжительности и трудоемкости). В настоящем Справочнике приведены опытно-статистические данные, которые могут быть использованы при разработке соответствующих нормативов на конкретных предприятиях.
1.2. Организация технического обслуживания и ремонта в передовых зарубежных странах
1.2.1. Утверждение некоторых отечественных специалистов, что за рубежом система ТО и ремонта отсутствует, не соответствует действительности.
1.2.2. В передовых промышленно развитых странах система организации ремонтно-профилактических работ называется несколько иначе, а именно:
система обслуживания – в Европе, США, Канаде и др.; система сохранения – в Японии, Южной Корее и других азиатских странах.
1.2.3. Как правило, на предприятиях нет специальных подразделений по ремонту (ремонтно-строительного управления, отделов главного механика, главного энергетика и др.). Такие службы возглавляет на основе принципа единоначалия технический руководитель фирмы по оборудованию, а работами руководят непосредственно мастера (механики).
1.2.4. Порядок выполнения работ по ТО, текущему и капитальному ремонтам разрабатывается заводами – изготовителями оборудования. Этот порядок определяется в инструкциях по эксплуатации соответствующих машин и неукоснительно выполняется на производственных предприятиях.
1.2.5. Еще одна существенная особенность ремонтного производства заключается в том, что ремонт с полной разборкой оборудования практически не применяется. Как текущий, так и капитальный ремонты выполняются путем замены пришедших в негодность агрегатов, узлов и деталей на годные заводского изготовления. Ремонтно-механические цеха по изготовлению и восстановлению деталей отсутствуют.
1.2.6. В США существует система планово-предупредительного обслуживания основных фондов, которая предусматривает содержание основных фондов в работоспособном состоянии путем замены любого сменного элемента, если есть опасность выхода оборудования из строя.
1.2.7. Для обеспечения возможности восстановления оборудования путем замены отдельных агрегатов, узлов и деталей предприятия-изготовители резервируют до 25 % своих производственных мощностей для выпуска такой продукции.
В США изготовление запасных частей поощряется тем, что их разрешается продавать на 20–25 % дороже, чем в виде собранного оборудования.
1.2.8. В США доля выполнения ремонтных работ так называемым «фирменным ремонтом» (силами специализированных ремонтных фирм) не превышает 10 % всего объема ремонтов в стране. Преимущественно это наладка, испытания, модернизация, сложные регулировочные работы, реже – замена сложных агрегатов.
1.2.9. Специалисты Японии и Южной Кореи считают, что для значительного увеличения прибыли от эксплуатации оборудования необходимо, чтобы ремонтно-восстановительное производство носило ритмичный (плановый) характер, как и в основном производстве. В японской системе обеспечения сохранности оборудования заложен следующий принцип: все работы по замене агрегатов, узлов и деталей самой сложной машины по возможности следует производить на месте ее установки силами собственного специально подготовленного персонала.
1.2.10. Во всех зарубежных странах большое внимание уделяется нормированию затрат труда, времени остановки на восстановление работоспособности машин и времени плановой замены сменных элементов.
1.2.11. Снижение издержек на восстановление неисправных основных фондов – это необходимое условие эффективной работы на конкурентном рынке.
1.2.2. В передовых промышленно развитых странах система организации ремонтно-профилактических работ называется несколько иначе, а именно:
система обслуживания – в Европе, США, Канаде и др.; система сохранения – в Японии, Южной Корее и других азиатских странах.
1.2.3. Как правило, на предприятиях нет специальных подразделений по ремонту (ремонтно-строительного управления, отделов главного механика, главного энергетика и др.). Такие службы возглавляет на основе принципа единоначалия технический руководитель фирмы по оборудованию, а работами руководят непосредственно мастера (механики).
1.2.4. Порядок выполнения работ по ТО, текущему и капитальному ремонтам разрабатывается заводами – изготовителями оборудования. Этот порядок определяется в инструкциях по эксплуатации соответствующих машин и неукоснительно выполняется на производственных предприятиях.
1.2.5. Еще одна существенная особенность ремонтного производства заключается в том, что ремонт с полной разборкой оборудования практически не применяется. Как текущий, так и капитальный ремонты выполняются путем замены пришедших в негодность агрегатов, узлов и деталей на годные заводского изготовления. Ремонтно-механические цеха по изготовлению и восстановлению деталей отсутствуют.
1.2.6. В США существует система планово-предупредительного обслуживания основных фондов, которая предусматривает содержание основных фондов в работоспособном состоянии путем замены любого сменного элемента, если есть опасность выхода оборудования из строя.
1.2.7. Для обеспечения возможности восстановления оборудования путем замены отдельных агрегатов, узлов и деталей предприятия-изготовители резервируют до 25 % своих производственных мощностей для выпуска такой продукции.
В США изготовление запасных частей поощряется тем, что их разрешается продавать на 20–25 % дороже, чем в виде собранного оборудования.
1.2.8. В США доля выполнения ремонтных работ так называемым «фирменным ремонтом» (силами специализированных ремонтных фирм) не превышает 10 % всего объема ремонтов в стране. Преимущественно это наладка, испытания, модернизация, сложные регулировочные работы, реже – замена сложных агрегатов.
1.2.9. Специалисты Японии и Южной Кореи считают, что для значительного увеличения прибыли от эксплуатации оборудования необходимо, чтобы ремонтно-восстановительное производство носило ритмичный (плановый) характер, как и в основном производстве. В японской системе обеспечения сохранности оборудования заложен следующий принцип: все работы по замене агрегатов, узлов и деталей самой сложной машины по возможности следует производить на месте ее установки силами собственного специально подготовленного персонала.
1.2.10. Во всех зарубежных странах большое внимание уделяется нормированию затрат труда, времени остановки на восстановление работоспособности машин и времени плановой замены сменных элементов.
1.2.11. Снижение издержек на восстановление неисправных основных фондов – это необходимое условие эффективной работы на конкурентном рынке.
1.3. Реализация концепции Системы ППР в отечественной практике
1.3.1. Система ППР оборудования, сложившаяся в соответствии с требованиями ГОСТ 18322—78, представлена на рис. 1.
Она отличается от ремонтных технологий, принятых в зарубежных странах, направленностью на поддержание работоспособности оборудования путем проведения текущих и капитальных ремонтов. Последнее объясняется тем, что в бывшем СССР нормативный коэффициент обновления основных фондов, в том числе их активной части, постоянно не выполнялся. В промышленности накапливалось большое количество амортизированного оборудования, которое восстанавливалось путем проведения сложных ремонтов.
1.3.2. К началу экономических реформ в промышленности скопилось до 25 % активной части основных фондов, требующих замены. При ежегодной амортизации машин 3,7–5,1 % и почти полном приостановлении в 90-х годах прошлого столетия замены негодного оборудования к 2000 г. в эксплуатации находилось более 60 % полностью амортизированных машин и оборудования.
Рис. 1. Дифференциация работ по системе планово-предупредительного ремонта
1.3.3. По данным зарубежных экономистов, если в любом производстве находится более 50 % полностью амортизированных машин и оборудования, такое производство без экономического анализа признается деградировавшим и объявляется банкротом.
1.3.4. Именно в таком состоянии находится значительная часть промышленных производств в России. Поэтому необходимо незамедлительно переходить, если это еще не сделано, на систему ППР, используя имеющийся мировой опыт, особенно в части организации ремонтов.
1.3.5. Организация ТО и ремонта оборудования на основе Системы ППР осуществляется отделом главного механика (ОГМ). Основная задача этого отдела – поддержание оборудования предприятия в постоянно работоспособном состоянии на основе ППР.
1.3.6. Главный механик, возглавляющий отдел, несет полную ответственность перед руководством предприятия за технически исправное и работоспособное состояние всего оборудования предприятия. Ему подчинены ремонтно-механический и ремонтно-строительные цеха, а на небольших предприятиях – и энергетическое хозяйство.
Положение об ОГМ и обязанности его руководителя приведены в Приложении 10.
1.3.7. В своей работе ОГМ руководствуется действующим законодательством, постановлениями Правительства РФ, приказами руководителя предприятия, действующими правилами безопасности, ГОСТ, ОСТ и инструкциями по эксплуатации оборудования заводов-изготовителей.
Основными задачами и функциями ОГМ являются организация технически правильного и рационального перспективного развития ремонтно-механической службы предприятия, внедрение Системы ППР общепромышленного оборудования.
В задачи ОГМ входит также контроль соблюдения установленных норм простоя в ремонте и непрерывной работы оборудования между ремонтами, качества ремонта и состояния промышленной безопасности при производстве ремонта, выполнения эксплуатационными и ремонтными подразделениями функций по организации и осуществлению технического надзора за эксплуатацией оборудования.
1.3.8. ОГМ разрабатывает мероприятия по улучшению организации ремонта и эксплуатации оборудования, внедрению прогрессивных методов ремонта, сокращению трудоемкости ремонта, норм простоя оборудования в ремонте, экономии материалов и средств на проведение ТО и ремонта основных фондов предприятия.
1.3.9. Отдел участвует в работе по планированию технического развития производства, капитального ремонта и модернизации основных фондов, баланса производственных мощностей и их использования. Разрабатывает нормативные материалы по ТО и ремонту оборудования (нормы расхода материалов, деталей, агрегатов и узлов основного оборудования), привлекая в необходимых случаях сторонние организации, участвует в расследовании причин инцидентов и аварий оборудования, производственного травматизма, принимает меры по их предупреждению.
1.3.10. ОГМ осуществляет контроль соблюдения установленных сроков составления подразделениями ведомостей дефектов и смет затрат на ремонт оборудования, заявок на запасные части, материалы, инструмент; контролирует правильность их расходования. Готовит материалы для заключения договоров с предприятиями-изготовителями на поставку запасных частей и оборудования и со специализированными подрядными ремонтными организациями – на капитальный ремонт и модернизацию оборудования; осуществляет контроль расходования средств на эти цели.
1.3.11. ОГМ принимает участие в разработке и внедрении технических условий на капитальный ремонт оборудования. Дает заключения по рационализаторским предложениям и изобретениям, связанным с совершенствованием технологии и организации ремонтных работ, оказывает рационализаторам и изобретателям практическую помощь и организует внедрение принятых предложений.
1.3.12. ОГМ разрабатывает, согласовывает с подразделениями и службами предприятия и утверждает у руководителя предприятия форму организации ТО и ремонта оборудования.
1.3.13. Существуют три основные формы организации ремонтного хозяйства: централизованная, децентрализованная и смешанная.
1.3.14. Централизованная организация ремонтного хозяйства предусматривает выполнение всех ремонтных работ на предприятии силами ОГМ и его ремонтно-механического цеха (ремонтной мастерской). Такая организация типична для предприятий с небольшим количеством оборудования.
1.3.15. Децентрализованная организация ремонтного хозяйства состоит в том, что все виды ремонтных работ – ТО, текущий и капитальный ремонты – проводятся под руководством механиков цехов (подразделений) комплексными бригадами. Ремонтно-механический цех (мастерская) осуществляет капитальный ремонт агрегатов и сложных узлов, изготавливает детали для цеховых ремонтных комплексных бригад.
1.3.16. При смешанной организации ремонтного хозяйства ТО и текущий ремонт выполняют комплексные бригады подразделений (цехов), а капитальный ремонт – ремонтно-механический цех (мастерская) ОГМ.
Она отличается от ремонтных технологий, принятых в зарубежных странах, направленностью на поддержание работоспособности оборудования путем проведения текущих и капитальных ремонтов. Последнее объясняется тем, что в бывшем СССР нормативный коэффициент обновления основных фондов, в том числе их активной части, постоянно не выполнялся. В промышленности накапливалось большое количество амортизированного оборудования, которое восстанавливалось путем проведения сложных ремонтов.
1.3.2. К началу экономических реформ в промышленности скопилось до 25 % активной части основных фондов, требующих замены. При ежегодной амортизации машин 3,7–5,1 % и почти полном приостановлении в 90-х годах прошлого столетия замены негодного оборудования к 2000 г. в эксплуатации находилось более 60 % полностью амортизированных машин и оборудования.
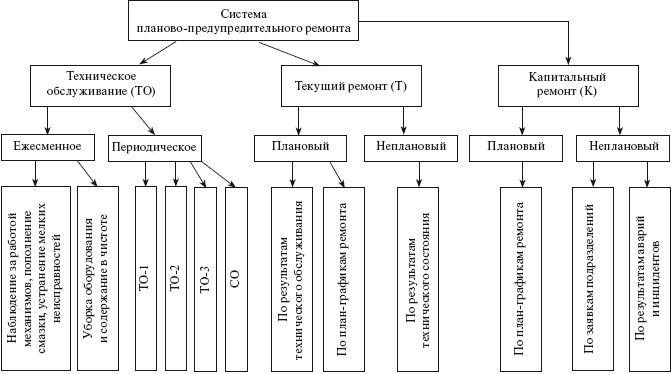
Рис. 1. Дифференциация работ по системе планово-предупредительного ремонта
1.3.3. По данным зарубежных экономистов, если в любом производстве находится более 50 % полностью амортизированных машин и оборудования, такое производство без экономического анализа признается деградировавшим и объявляется банкротом.
1.3.4. Именно в таком состоянии находится значительная часть промышленных производств в России. Поэтому необходимо незамедлительно переходить, если это еще не сделано, на систему ППР, используя имеющийся мировой опыт, особенно в части организации ремонтов.
1.3.5. Организация ТО и ремонта оборудования на основе Системы ППР осуществляется отделом главного механика (ОГМ). Основная задача этого отдела – поддержание оборудования предприятия в постоянно работоспособном состоянии на основе ППР.
1.3.6. Главный механик, возглавляющий отдел, несет полную ответственность перед руководством предприятия за технически исправное и работоспособное состояние всего оборудования предприятия. Ему подчинены ремонтно-механический и ремонтно-строительные цеха, а на небольших предприятиях – и энергетическое хозяйство.
Положение об ОГМ и обязанности его руководителя приведены в Приложении 10.
1.3.7. В своей работе ОГМ руководствуется действующим законодательством, постановлениями Правительства РФ, приказами руководителя предприятия, действующими правилами безопасности, ГОСТ, ОСТ и инструкциями по эксплуатации оборудования заводов-изготовителей.
Основными задачами и функциями ОГМ являются организация технически правильного и рационального перспективного развития ремонтно-механической службы предприятия, внедрение Системы ППР общепромышленного оборудования.
В задачи ОГМ входит также контроль соблюдения установленных норм простоя в ремонте и непрерывной работы оборудования между ремонтами, качества ремонта и состояния промышленной безопасности при производстве ремонта, выполнения эксплуатационными и ремонтными подразделениями функций по организации и осуществлению технического надзора за эксплуатацией оборудования.
1.3.8. ОГМ разрабатывает мероприятия по улучшению организации ремонта и эксплуатации оборудования, внедрению прогрессивных методов ремонта, сокращению трудоемкости ремонта, норм простоя оборудования в ремонте, экономии материалов и средств на проведение ТО и ремонта основных фондов предприятия.
1.3.9. Отдел участвует в работе по планированию технического развития производства, капитального ремонта и модернизации основных фондов, баланса производственных мощностей и их использования. Разрабатывает нормативные материалы по ТО и ремонту оборудования (нормы расхода материалов, деталей, агрегатов и узлов основного оборудования), привлекая в необходимых случаях сторонние организации, участвует в расследовании причин инцидентов и аварий оборудования, производственного травматизма, принимает меры по их предупреждению.
1.3.10. ОГМ осуществляет контроль соблюдения установленных сроков составления подразделениями ведомостей дефектов и смет затрат на ремонт оборудования, заявок на запасные части, материалы, инструмент; контролирует правильность их расходования. Готовит материалы для заключения договоров с предприятиями-изготовителями на поставку запасных частей и оборудования и со специализированными подрядными ремонтными организациями – на капитальный ремонт и модернизацию оборудования; осуществляет контроль расходования средств на эти цели.
1.3.11. ОГМ принимает участие в разработке и внедрении технических условий на капитальный ремонт оборудования. Дает заключения по рационализаторским предложениям и изобретениям, связанным с совершенствованием технологии и организации ремонтных работ, оказывает рационализаторам и изобретателям практическую помощь и организует внедрение принятых предложений.
1.3.12. ОГМ разрабатывает, согласовывает с подразделениями и службами предприятия и утверждает у руководителя предприятия форму организации ТО и ремонта оборудования.
1.3.13. Существуют три основные формы организации ремонтного хозяйства: централизованная, децентрализованная и смешанная.
1.3.14. Централизованная организация ремонтного хозяйства предусматривает выполнение всех ремонтных работ на предприятии силами ОГМ и его ремонтно-механического цеха (ремонтной мастерской). Такая организация типична для предприятий с небольшим количеством оборудования.
1.3.15. Децентрализованная организация ремонтного хозяйства состоит в том, что все виды ремонтных работ – ТО, текущий и капитальный ремонты – проводятся под руководством механиков цехов (подразделений) комплексными бригадами. Ремонтно-механический цех (мастерская) осуществляет капитальный ремонт агрегатов и сложных узлов, изготавливает детали для цеховых ремонтных комплексных бригад.
1.3.16. При смешанной организации ремонтного хозяйства ТО и текущий ремонт выполняют комплексные бригады подразделений (цехов), а капитальный ремонт – ремонтно-механический цех (мастерская) ОГМ.
2. ПРОИЗВОДСТВЕННАЯ ЭКСПЛУАТАЦИЯ ОБОРУДОВАНИЯ
Под производственной эксплуатацией понимают стадию жизненного цикла оборудования, заключающуюся в его использовании по назначению. В стадию жизненного цикла оборудования входят следующие этапы: прием, монтаж, ввод в эксплуатацию, организация эксплуатации, служба в течение определенного срока, амортизация, хранение, выбытие оборудования.
2.1. Прием оборудования
2.1.1. Прием оборудования, поступившего от заводов-изготовителей на предприятие, производится комиссиями. Для основного оборудования председателем комиссии является главный инженер – заместитель руководителя предприятия, членами – главный механик, главный бухгалтер (бухгалтер) и руководитель подразделения по принадлежности оборудования, а также представители Ростехнадзора – для приема оборудования опасных производств. Остальное (неосновное) оборудование принимается комиссией, члены которой хорошо знакомы с устройством и эксплуатацией принимаемого оборудования.
2.1.2. Комиссии несут ответственность за строгое и точное соблюдение правил приемки оборудования, в том числе:
выявление внешних дефектов;
проверка фактической комплектности оборудования и технической документации;
сохранение оборудования в целостности;
проверка качества изготовленного оборудования и материалов (Приложения 2–6).
2.1.3. В соответствии с ГОСТ 16504—70 предприятия обязаны соблюдать правила приема, в том числе проводить входной контроль. В случае нарушения перечисленных выше требований по приему оборудования предприятия-потребители лишаются права на устранение заводом-изготовителем дефектов и возмещение понесенных потребителем убытков.
2.1.4. Прием оборудования, состоящий из проверки наличия технической документации и комплектности поставки, а также выявление внешних дефектов, не требующих разборки оборудования, выполняются в соответствии с требованиями ГОСТ 2.601—68 «Эксплуатационная и ремонтная документация» и ГОСТ 13168—69 «Консервация металлических изделий».
2.1.2. Комиссии несут ответственность за строгое и точное соблюдение правил приемки оборудования, в том числе:
выявление внешних дефектов;
проверка фактической комплектности оборудования и технической документации;
сохранение оборудования в целостности;
проверка качества изготовленного оборудования и материалов (Приложения 2–6).
2.1.3. В соответствии с ГОСТ 16504—70 предприятия обязаны соблюдать правила приема, в том числе проводить входной контроль. В случае нарушения перечисленных выше требований по приему оборудования предприятия-потребители лишаются права на устранение заводом-изготовителем дефектов и возмещение понесенных потребителем убытков.
2.1.4. Прием оборудования, состоящий из проверки наличия технической документации и комплектности поставки, а также выявление внешних дефектов, не требующих разборки оборудования, выполняются в соответствии с требованиями ГОСТ 2.601—68 «Эксплуатационная и ремонтная документация» и ГОСТ 13168—69 «Консервация металлических изделий».