Страница:
Из воздуха в зону сварки поступает азот, который в зоне сварочной дуги присутствует и в атомарном, и в молекулярном, и в ионизированном состояниях. Его растворимость в железе определяется температурой. В процессе охлаждения шва азот выделяется из раствора, вступает в реакцию с металлом шва, в результате чего образуются такие химические соединения, как нитриды железа, марганца и кремния (Fe2 N, Fe4 N, MnN, SiN). Если охлаждение проходит с большой скоростью, то азот, не успевая полностью выделиться, вместе с металлом входит в перенасыщенный твердый раствор, что, с одной стороны, резко повышает прочность шва, а с другой – становится причиной постепенного старения металла шва и негативно сказывается на его механических свойствах (он утрачивает пластичность). Поэтому необходимо принимать меры по недопущению проникновения азота в зону сварочной ванны, что возможно, например, при осуществлении сварки в среде защитного газа.
При диссоциации водяных паров (они проникают в зону дуги из воздуха, флюса и др.), которая развивается в зоне сварки под воздействием высокой температуры, образуется еще один газ – водород. Он может быть и молекулярным, и атомарным, причем последний хорошо растворяется в расплавленном металле, особенно при повышении температуры. Когда она поднимается до 2400 °C, количество водорода составляет 43 см3 на 100 г металла (это максимальное значение).
По способности растворять водород металлы делятся на две группы:
– металлы, не вступающие в соединения с водородом (железо, никель, медь и др.);
– металлы, образующие при взаимодействии с водородом гидриды (ванадий, титан, редкоземельные элементы и др.).
Присутствующие в металле легирующие элементы по-разному воздействуют на растворимость водорода – могут либо повышать ее, либо понижать. К первым относятся титан и ниобий, а ко вторым – хром, алюминий, а также кремний и углерод.
При охлаждении металла атомарный кислород переходит в молекулярное состояние. Но, если кристаллизация протекает с высокой скоростью, водород не может полностью выделиться из металла, что негативно отражается на качестве шва, металл которого приобретает пористость, становится менее пластичным, усиливается трещинообразование и т. п. Чтобы минимизировать концентрацию водорода в сварочной ванне, вводят элементы, которые вступают в реакцию с ним и образуют нерастворимые соединения (например, фтористый водород), либо применяют окисление сварочной ванны.
Из всего сказанного следует вывод: физико-химические процессы, которые наблюдаются в зоне дуги, существенно влияют на качество металла сварного шва и, следовательно, всего соединения. Поэтому требуется принимать меры, защищающие расплавленный металл сварочной ванны от нежелательного воздействия на него перечисленных газов. Названный способ, предполагающий осуществление сварки в среде защитных газов, а также создание шлаковой оболочки над ванной расплавленного металла, оказывает положительное влияние, но полностью защитить металл от проникновения кислорода и образования в нем соединений с ним это не может. Более эффективным оказывается раскисление металла и извлечение из сварочной ванны оксидов.
В качестве раскислителей металла сварочной ванны используют алюминий, углерод, титан, кремний и марганец, поскольку они имеют значительное сродство к кислороду. Данные элементы вводят в расплавленный металл одним из трех способов – в виде:
– электродной проволоки или присадки;
– флюса;
– электродного покрытия.
Они взаимодействуют с окислами металла. Раскислители вводят в сварочную ванну в виде ферросплавов (ферротитана, ферромарганца и др.), входящих в состав электродного покрытия или флюса. Расплавляясь, они практически целиком переходят в шлак.
Перечисленные выше раскислители ведут себя совершенно по-разному, поэтому одним из них отдают предпочтение чаще, а другие применяют реже. К последним относится алюминий, поскольку он образует тугоплавкие соединения с кислородом, которые придают стали нежелательные качества, в частности склонность к трещинообразованию. Тем не менее при его использовании взаимодействие протекает в соответствии с реакцией:
3FeO + 2Al = 3Fe + Al2O3.
Очень активным раскислителем является титан, поэтому его применяют довольно часто. Он вводится в жидкий металл в составе электродных покрытий и взаимодействует с кислородом согласно реакции:
2FeO + Ti = 2Fe + TiO2.
Кроме того, титан уменьшает содержание азота в расплавленном металле, так как образует нитриды.
Хорошим раскислителем является кремний, который присутствует в электродных покрытиях и флюсах и взаимодействует с кислородом по следующей реакции:
2FeO + Si = 2Fe + SiO2.
Одновременно с этим в жидком металле идет реакция образования силикатов (SiO2 + FeO = FeO SiO2), которые вместе с оксидом двухвалентного железа не растворяются в железе и переходят в шлак.
Раскисление углеродом протекает по реакции:
FeO + C = Fe + CO.
Оксид углерода – это газообразное соединение, в стали оно не растворяется, выделяясь из нее в виде пузырьков. До начала кристаллизации это выглядит как кипение вещества, сопровождающееся разбрызгиванием металла, который при этом очищается от различных металлических включений. Кипение металла во время охлаждения – явление негативное, так как при высокой скорости кристаллизации часть оксида остается в металле шва, образуя поры. Чтобы предотвратить возникновение газовых пор, в сварочную ванну вводят кремний, причем его количество должно быть достаточным для подавления раскисляющего действия углерода.
Самый широко применяемый раскислитель – марганец, входящий в качестве компонента во флюсы и электродные покрытия и действующий по реакции:
FeO + Mn = Fe + MnO.
Как и оксид железа (FeO), оксид марганца вступает во взаимодействие с оксидом кремния, образуя не растворяющийся в стали силикат (MnO + SiO2 = MnO SiO2). Помимо этого, результатом реакции с сульфидом железа (FeS + Mn = MnS + Fe) является сернистый марганец, который, будучи не растворимым в стали, переходит в шлак и освобождает металл от примесей серы (она попадает в сварочную ванну из разных источников – основного металла, сварочной проволоки, флюса и др.).
Виды сварки
Деформации и напряжения при сварке
При диссоциации водяных паров (они проникают в зону дуги из воздуха, флюса и др.), которая развивается в зоне сварки под воздействием высокой температуры, образуется еще один газ – водород. Он может быть и молекулярным, и атомарным, причем последний хорошо растворяется в расплавленном металле, особенно при повышении температуры. Когда она поднимается до 2400 °C, количество водорода составляет 43 см3 на 100 г металла (это максимальное значение).
По способности растворять водород металлы делятся на две группы:
– металлы, не вступающие в соединения с водородом (железо, никель, медь и др.);
– металлы, образующие при взаимодействии с водородом гидриды (ванадий, титан, редкоземельные элементы и др.).
Присутствующие в металле легирующие элементы по-разному воздействуют на растворимость водорода – могут либо повышать ее, либо понижать. К первым относятся титан и ниобий, а ко вторым – хром, алюминий, а также кремний и углерод.
При охлаждении металла атомарный кислород переходит в молекулярное состояние. Но, если кристаллизация протекает с высокой скоростью, водород не может полностью выделиться из металла, что негативно отражается на качестве шва, металл которого приобретает пористость, становится менее пластичным, усиливается трещинообразование и т. п. Чтобы минимизировать концентрацию водорода в сварочной ванне, вводят элементы, которые вступают в реакцию с ним и образуют нерастворимые соединения (например, фтористый водород), либо применяют окисление сварочной ванны.
Из всего сказанного следует вывод: физико-химические процессы, которые наблюдаются в зоне дуги, существенно влияют на качество металла сварного шва и, следовательно, всего соединения. Поэтому требуется принимать меры, защищающие расплавленный металл сварочной ванны от нежелательного воздействия на него перечисленных газов. Названный способ, предполагающий осуществление сварки в среде защитных газов, а также создание шлаковой оболочки над ванной расплавленного металла, оказывает положительное влияние, но полностью защитить металл от проникновения кислорода и образования в нем соединений с ним это не может. Более эффективным оказывается раскисление металла и извлечение из сварочной ванны оксидов.
В качестве раскислителей металла сварочной ванны используют алюминий, углерод, титан, кремний и марганец, поскольку они имеют значительное сродство к кислороду. Данные элементы вводят в расплавленный металл одним из трех способов – в виде:
– электродной проволоки или присадки;
– флюса;
– электродного покрытия.
Они взаимодействуют с окислами металла. Раскислители вводят в сварочную ванну в виде ферросплавов (ферротитана, ферромарганца и др.), входящих в состав электродного покрытия или флюса. Расплавляясь, они практически целиком переходят в шлак.
Перечисленные выше раскислители ведут себя совершенно по-разному, поэтому одним из них отдают предпочтение чаще, а другие применяют реже. К последним относится алюминий, поскольку он образует тугоплавкие соединения с кислородом, которые придают стали нежелательные качества, в частности склонность к трещинообразованию. Тем не менее при его использовании взаимодействие протекает в соответствии с реакцией:
3FeO + 2Al = 3Fe + Al2O3.
Очень активным раскислителем является титан, поэтому его применяют довольно часто. Он вводится в жидкий металл в составе электродных покрытий и взаимодействует с кислородом согласно реакции:
2FeO + Ti = 2Fe + TiO2.
Кроме того, титан уменьшает содержание азота в расплавленном металле, так как образует нитриды.
Хорошим раскислителем является кремний, который присутствует в электродных покрытиях и флюсах и взаимодействует с кислородом по следующей реакции:
2FeO + Si = 2Fe + SiO2.
Одновременно с этим в жидком металле идет реакция образования силикатов (SiO2 + FeO = FeO SiO2), которые вместе с оксидом двухвалентного железа не растворяются в железе и переходят в шлак.
Раскисление углеродом протекает по реакции:
FeO + C = Fe + CO.
Оксид углерода – это газообразное соединение, в стали оно не растворяется, выделяясь из нее в виде пузырьков. До начала кристаллизации это выглядит как кипение вещества, сопровождающееся разбрызгиванием металла, который при этом очищается от различных металлических включений. Кипение металла во время охлаждения – явление негативное, так как при высокой скорости кристаллизации часть оксида остается в металле шва, образуя поры. Чтобы предотвратить возникновение газовых пор, в сварочную ванну вводят кремний, причем его количество должно быть достаточным для подавления раскисляющего действия углерода.
Самый широко применяемый раскислитель – марганец, входящий в качестве компонента во флюсы и электродные покрытия и действующий по реакции:
FeO + Mn = Fe + MnO.
Как и оксид железа (FeO), оксид марганца вступает во взаимодействие с оксидом кремния, образуя не растворяющийся в стали силикат (MnO + SiO2 = MnO SiO2). Помимо этого, результатом реакции с сульфидом железа (FeS + Mn = MnS + Fe) является сернистый марганец, который, будучи не растворимым в стали, переходит в шлак и освобождает металл от примесей серы (она попадает в сварочную ванну из разных источников – основного металла, сварочной проволоки, флюса и др.).
Виды сварки
Напомним, что получение неразъемного соединения твердых материалов в процессе их местного плавления или пластического деформирования называется сваркой. Металлы и сплавы, как уже было сказано, являются твердыми кристаллическими телами, состоящими из кристаллитов, между которыми существуют межатомные и межмолекулярные силы взаимодействия. При обычных условиях между силами отталкивания и притяжения наблюдается равновесие. Под воздействием энергии, направленной извне (это энергия активации), оно нарушается. В зависимости от того, как именно активируются межатомные связи для формирования неразъемного соединения, сварка подразделяется на:
– сварку плавлением. В соответствии со способом нагрева электросварка плавлением представлена таким видами, как электродуговая, электрошлаковая, электроконтактная, электронно-лучевая. При этом жидкий металл расплавленных кромок перемешивается с образованием общего объема (сварочной ванны), из которого образуется металл шва. Это происходит и в результате использования присадочного металла. Источники локального нагрева бывают различными. Например, это могут быть электрическая дуга, плазма, горелка, энергия электронного или плазменного излучения, печь и др.;
– сварку давлением, при которой сварное соединение образуется благодаря исключительно деформированию свариваемых частей (в некоторых случаях нагрузка может сочетаться с местным нагреванием). Это возможно за счет применения статической или ударной нагрузки, например при сварке взрывом, ультразвуком или в процессе холодной сварки. В ходе пластической деформации на участке свариваемых кромок (он называется зоной соединения) возникает трение, которое способствует формированию межатомных связей между частями.
Для соединения двух металлов в единое целое необходимо, чтобы расстояние между их атомами сократилось настолько, чтобы силы взаимного притяжения начали активизироваться. Это достижимо при условии, что промежуток между атомами составляет 4 х 10-8 см, что возможно, если:
– не нагревая детали, сжать их с приложением больших усилий, что характерно исключительно для пластичных металлов, например для алюминия;
– одновременно нагреть и сжать детали, прикладывая умеренное усилие;
– в зоне соединения нагреть детали до расплавления, не прибегая к сжатию, что и происходит при сварке металлов и сплавов.
В соответствии с этим сварка металлов классифицируется на основе различных признаков:
– физических;
– технических;
– технологических.
В основе классификации по физическим признакам лежит форма энергии, которая применяется для создания сварного соединения. Согласно ГОСТу 19521-74 выделяют 3 класса сварочных процессов:
1. Термический, при котором в зоне сварки под воздействием тепловой энергии рабочие части металла соединяются посредством плавления. Сюда входят следующие разновидности сварки:
а) дуговая. Этот вид сварки классифицируется по различным признакам (Ручная дуговая сварка. М.: Высшая школа, 1981), представленным на рис. 1.
Рис. 1. Классификация дуговой сварки
С применением электродуговой сварки осуществляется примерно 65 % сварочных работ, при которых могут использоваться как плавящиеся (металлические), так и неплавящиеся (угольные) электроды (рис. 2). Первый способ был разработан Н. Г. Славяновым, а второй – Н. Н. Бенардосом.
Рис. 2. Электродуговая сварка: а – плавящимся электродом: 1 – деталь; 2 – сварочная дуга; 3 – зажим; 4 – электрод; 5 – электродержатель; 6 – провод; 7 – кромка; б – неплавящимся электродом: 1 – деталь; 2 – присадочный материал; 3 – электрод; 4 – электродержатель; 5, 6 – провод; 7 – сварочная дуга
Участок на границе расплавленной кромки называется зоной плавления. Ее ширина измеряется микрометрами, но несмотря на такие размеры прочность сварного соединения во многом зависит от нее.
По Славянову, кромки и электрод под воздействием сварочной дуги расплавляются одновременно. Образующаяся при этом сварочная ванна заполняет зазор между соединяемыми деталями, а после кристаллизации превращается в сварной шов. Чтобы улучшить качество наплавляемого металла, на электрод наносится особое покрытие, которое, расплавившись, превращается в слой шлака, покрывающий жидкий металл. В результате этого, во-первых, в шлак переходят вредные примеси, присутствующие в расплавленном металле, а во-вторых, шлак защищает сварочную ванну от проникновения в нее кислорода и азота из атмосферного воздуха.
К электроду, зафиксированному в электродержателе, ток (при этом способе дуговой сварки он может быть как постоянным, так и переменным) поступает по электрическому проводу, а к деталям – через второй провод, закрепленный зажимом.
В методе, разработанном Бенардосом, используется неплавящийся электрод, сварочная ванная создается за счет металлического прутка, расплавляющегося под воздействием сварочной дуги. В отличие от первого способа здесь используется постоянный ток. При сварке стали он не всегда дает результат нужного качества, поэтому в основном находит применение при сварке алюминия, меди, тонколистовой стали и наплавке твердых сплавов;
б) электронно-лучевая. Для ее осуществления необходима особая камера, в которой создается вакуум. Кромки свариваемых деталей расплавляются сфокусированным пучком электронов, которые ударяются в так называемое пятно нагрева, в результате чего кинетическая энергия их торможения переходит в теплоту. При этом температура в фокусе достигает 10 000 °C;
в) электрошлаковая, при которой основной и присадочный материалы расплавляются теплом, которое выделяется при пропускании электрического тока через расплавленный шлак на протяжении всего процесса. Этот вид сварки различается по виду и количеству электродов, наличию его колебаний и т. д. Данный способ используется для сварки крупногабаритных заготовок;
г) плазменная. При сварке в столб дуги постоянно поступает неионизированный газ. Под ее воздействием он последовательно нагревается, ионизируется и трансформируется в плазменную струю, которая уплотняется вихревым потоком газа. Образуется источник тепловой энергии, концентрация которого такова, что достаточна для сваривания металла;
д) световая, при которой сваривание деталей (металлов и отдельных неметаллических материалов) обеспечивает концентрированный луч – монохроматический (при лазерной сварке), солнечный (при гелиосварке) или искусственный полихроматический;
е) индукционная, при которой металл, нагретый токами высокой частоты, сдавливается. Данный способ практикуется при сварке труб;
ж) термитная. Для ее осуществления свариваемые части кладут в огнеупорную форму, на них ставят тигель, в который помещают термит (порошок из смеси алюминия с железной окалиной). В процессе реакции восстановления выделяется большое количество тепла (реакция относится к экзотермическим), а температура металла достигает 2000 °C. В результате этого жидкий металл оплавляет кромки частей и затекает в промежуток между ними. Кристаллизовавшись, он дает сварочный шов;
з) газовая, основанная на том, что основной и присадочный металлы свариваются с помощью высокотемпературного газокислородного пламени. Для этой цели используются различные газы – ацетилен, природный газ, водород и др. Чаще всего применяется ацетиленокислородная сварка, в которой используется пламя инжекционной горелки. Роль присадочного материала играют прутки или проволока из металла, схожего по составу с основным. По качеству этот вид сварки уступает электродуговой;
и) литейная. Этим способом сваривают изделия из благородных металлов и пр. В современном производстве к такому виду сварки прибегают редко – только для исправления чугунных отливок. Суть сварки состоит в следующем: зону сварки заливают расплавленным в тигле металлом, после чего формуют шов.
2. Термомеханический, который включает сварку и с использованием тепловой энергии, и с применением давления. Это такие виды сварки, как:
а) контактная, осуществляемая тремя способами, например встык, что практикуется для соединения частей с малыми сечениями. Сначала гидравлический пресс сжимает кромки, потом с помощью электрического тока металл на кромках нагревается до пластического состояния и сваривается;
б) индукционно-прессовая, при которой под воздействием токов высокой частоты соединяемые части или детали, расположенные под определенным углом друг к другу и контактирующие на участке сварки, нагреваются, расплавляются, стягиваются обжимными роликами и осаживаются. Результат – прочное соединение;
в) диффузионная, основанная на способности атомов контактирующий деталей к диффузии. Их устанавливают встык, нагревают с помощью индуктора и сжимают. Процесс проходит либо в вакууме, либо в газовой среде (для этого используются инертные газы). При этом способе достаточно довести температуру до 750–800 °C;
г) газопрессовая, при которой кромки свариваемых частей нагревают с помощью ацетиленокислородной горелки и сжимают, применяя специальный осадочный механизм;
д) термокомпрессионная, для осуществления которой необходимость расплавления материалов отсутствует. Компонент, например проволочные выводы, и подложку покрывают ковким материалом (золотом), нагревают до 300 °C и сжимают примерно на полсекунды. В результате образуется соединение по типу диффузной сварки;
е) дугопрессовая, которая находит применение при необходимости присоединить к пластине детали вроде болтов или шпилек. Когда шпилька или болт отводится от пластины, между ними возникает дуговой разряд, из-за которого температура их торцов и металла пластины повышается, они нагреваются и расплавляются. В тот момент, когда при отключенном токе шпилька или болт ударяются о пластину, они свариваются;
ж) печная, практикующаяся, например, для приваривания фланцев к трубам. Для этого стыки покрывают специальным составом (вставка между ними латунного или бронзового кольца – еще один вариант). В таком виде все помещают в электропечь, в которой при температуре 1100–1500 °C происходит сваривание;
и) термитно-прессовая, при которой соединяемые части или детали нагревают газовым пламенем и сжимают.
3. Механический, в него входят виды сварки, для осуществления которых используется комбинация механической энергии и давления. Эту группу составляют следующие виды сварки:
а) холодная, в основе которой лежит способность кристаллитов металла срастаться под воздействием высокого давления. Таким способом соединяют исключительно пластичные материалы, такие как алюминий, свинец и др.;
б) ультразвуковая, при которой свариваемые части сближают и стягивают вибрирующим зажимом, через который поступают высокочастотные колебания от магнитострикционного генератора. Благодаря колебаниям состыкованные части нагреваются, после чего свариваются в процессе диффузии атомов контактирующих материалов;
в) магнитно-импульсная, для проведения которой под воздействием импульсного тока индуктора и наведенных им вихревыми токами в соединяемых частях, деталях и ином свариваемые поверхности соударяются;
г) сварка взрывом, которая используется для соединения тонких листов с более массивными (процесс называется «плакирование»), например стали с латунью. Детали укладывают друг на друга, на поверхность помещают взрывчатое вещество, которое при детонировании взрывается и соединяет их в результате соударения;
д) сварка трением, практикуемая для соединения мелких деталей, одна из которых неподвижна, а другая вращается вокруг нее (или они вращаются в разные стороны). При трении выделяется тепло, которое нагревает и сваривает детали.
Техническими признаками, на которые опирается классификация сварки металлов, являются:
– способы защиты металла на участке сварки. Среди используемых представлена сварка в вакууме, защитных газах (в углекислом газе, водяных парах, инертных газах и др.), воздухе, пене, по флюсу и под ним. Кроме того, возможно комбинирование способов;
– степень непрерывности сварочных работ. По этому признаку различаются как прерывистые, так и непрерывные способы сварки;
– наличие механизации процесса сварки. Сюда входят ручные, автоматизированные, механизированные и автоматические способы сварки.
О технологических признаках следует сказать, что для каждого вида сварки они разрабатываются отдельно.
– сварку плавлением. В соответствии со способом нагрева электросварка плавлением представлена таким видами, как электродуговая, электрошлаковая, электроконтактная, электронно-лучевая. При этом жидкий металл расплавленных кромок перемешивается с образованием общего объема (сварочной ванны), из которого образуется металл шва. Это происходит и в результате использования присадочного металла. Источники локального нагрева бывают различными. Например, это могут быть электрическая дуга, плазма, горелка, энергия электронного или плазменного излучения, печь и др.;
– сварку давлением, при которой сварное соединение образуется благодаря исключительно деформированию свариваемых частей (в некоторых случаях нагрузка может сочетаться с местным нагреванием). Это возможно за счет применения статической или ударной нагрузки, например при сварке взрывом, ультразвуком или в процессе холодной сварки. В ходе пластической деформации на участке свариваемых кромок (он называется зоной соединения) возникает трение, которое способствует формированию межатомных связей между частями.
Для соединения двух металлов в единое целое необходимо, чтобы расстояние между их атомами сократилось настолько, чтобы силы взаимного притяжения начали активизироваться. Это достижимо при условии, что промежуток между атомами составляет 4 х 10-8 см, что возможно, если:
– не нагревая детали, сжать их с приложением больших усилий, что характерно исключительно для пластичных металлов, например для алюминия;
– одновременно нагреть и сжать детали, прикладывая умеренное усилие;
– в зоне соединения нагреть детали до расплавления, не прибегая к сжатию, что и происходит при сварке металлов и сплавов.
В соответствии с этим сварка металлов классифицируется на основе различных признаков:
– физических;
– технических;
– технологических.
В основе классификации по физическим признакам лежит форма энергии, которая применяется для создания сварного соединения. Согласно ГОСТу 19521-74 выделяют 3 класса сварочных процессов:
1. Термический, при котором в зоне сварки под воздействием тепловой энергии рабочие части металла соединяются посредством плавления. Сюда входят следующие разновидности сварки:
а) дуговая. Этот вид сварки классифицируется по различным признакам (Ручная дуговая сварка. М.: Высшая школа, 1981), представленным на рис. 1.
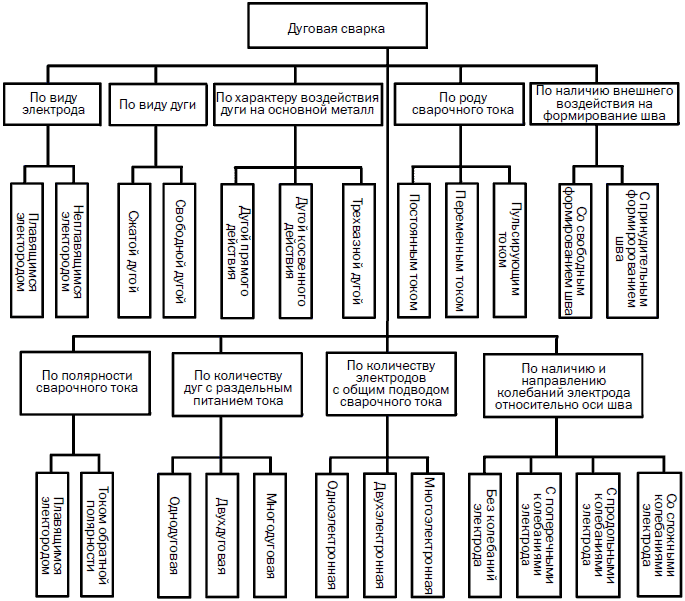
С применением электродуговой сварки осуществляется примерно 65 % сварочных работ, при которых могут использоваться как плавящиеся (металлические), так и неплавящиеся (угольные) электроды (рис. 2). Первый способ был разработан Н. Г. Славяновым, а второй – Н. Н. Бенардосом.
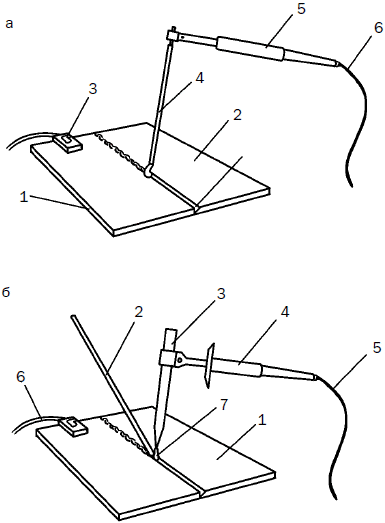
Участок на границе расплавленной кромки называется зоной плавления. Ее ширина измеряется микрометрами, но несмотря на такие размеры прочность сварного соединения во многом зависит от нее.
По Славянову, кромки и электрод под воздействием сварочной дуги расплавляются одновременно. Образующаяся при этом сварочная ванна заполняет зазор между соединяемыми деталями, а после кристаллизации превращается в сварной шов. Чтобы улучшить качество наплавляемого металла, на электрод наносится особое покрытие, которое, расплавившись, превращается в слой шлака, покрывающий жидкий металл. В результате этого, во-первых, в шлак переходят вредные примеси, присутствующие в расплавленном металле, а во-вторых, шлак защищает сварочную ванну от проникновения в нее кислорода и азота из атмосферного воздуха.
К электроду, зафиксированному в электродержателе, ток (при этом способе дуговой сварки он может быть как постоянным, так и переменным) поступает по электрическому проводу, а к деталям – через второй провод, закрепленный зажимом.
В методе, разработанном Бенардосом, используется неплавящийся электрод, сварочная ванная создается за счет металлического прутка, расплавляющегося под воздействием сварочной дуги. В отличие от первого способа здесь используется постоянный ток. При сварке стали он не всегда дает результат нужного качества, поэтому в основном находит применение при сварке алюминия, меди, тонколистовой стали и наплавке твердых сплавов;
б) электронно-лучевая. Для ее осуществления необходима особая камера, в которой создается вакуум. Кромки свариваемых деталей расплавляются сфокусированным пучком электронов, которые ударяются в так называемое пятно нагрева, в результате чего кинетическая энергия их торможения переходит в теплоту. При этом температура в фокусе достигает 10 000 °C;
в) электрошлаковая, при которой основной и присадочный материалы расплавляются теплом, которое выделяется при пропускании электрического тока через расплавленный шлак на протяжении всего процесса. Этот вид сварки различается по виду и количеству электродов, наличию его колебаний и т. д. Данный способ используется для сварки крупногабаритных заготовок;
г) плазменная. При сварке в столб дуги постоянно поступает неионизированный газ. Под ее воздействием он последовательно нагревается, ионизируется и трансформируется в плазменную струю, которая уплотняется вихревым потоком газа. Образуется источник тепловой энергии, концентрация которого такова, что достаточна для сваривания металла;
д) световая, при которой сваривание деталей (металлов и отдельных неметаллических материалов) обеспечивает концентрированный луч – монохроматический (при лазерной сварке), солнечный (при гелиосварке) или искусственный полихроматический;
е) индукционная, при которой металл, нагретый токами высокой частоты, сдавливается. Данный способ практикуется при сварке труб;
ж) термитная. Для ее осуществления свариваемые части кладут в огнеупорную форму, на них ставят тигель, в который помещают термит (порошок из смеси алюминия с железной окалиной). В процессе реакции восстановления выделяется большое количество тепла (реакция относится к экзотермическим), а температура металла достигает 2000 °C. В результате этого жидкий металл оплавляет кромки частей и затекает в промежуток между ними. Кристаллизовавшись, он дает сварочный шов;
з) газовая, основанная на том, что основной и присадочный металлы свариваются с помощью высокотемпературного газокислородного пламени. Для этой цели используются различные газы – ацетилен, природный газ, водород и др. Чаще всего применяется ацетиленокислородная сварка, в которой используется пламя инжекционной горелки. Роль присадочного материала играют прутки или проволока из металла, схожего по составу с основным. По качеству этот вид сварки уступает электродуговой;
и) литейная. Этим способом сваривают изделия из благородных металлов и пр. В современном производстве к такому виду сварки прибегают редко – только для исправления чугунных отливок. Суть сварки состоит в следующем: зону сварки заливают расплавленным в тигле металлом, после чего формуют шов.
2. Термомеханический, который включает сварку и с использованием тепловой энергии, и с применением давления. Это такие виды сварки, как:
а) контактная, осуществляемая тремя способами, например встык, что практикуется для соединения частей с малыми сечениями. Сначала гидравлический пресс сжимает кромки, потом с помощью электрического тока металл на кромках нагревается до пластического состояния и сваривается;
б) индукционно-прессовая, при которой под воздействием токов высокой частоты соединяемые части или детали, расположенные под определенным углом друг к другу и контактирующие на участке сварки, нагреваются, расплавляются, стягиваются обжимными роликами и осаживаются. Результат – прочное соединение;
в) диффузионная, основанная на способности атомов контактирующий деталей к диффузии. Их устанавливают встык, нагревают с помощью индуктора и сжимают. Процесс проходит либо в вакууме, либо в газовой среде (для этого используются инертные газы). При этом способе достаточно довести температуру до 750–800 °C;
г) газопрессовая, при которой кромки свариваемых частей нагревают с помощью ацетиленокислородной горелки и сжимают, применяя специальный осадочный механизм;
д) термокомпрессионная, для осуществления которой необходимость расплавления материалов отсутствует. Компонент, например проволочные выводы, и подложку покрывают ковким материалом (золотом), нагревают до 300 °C и сжимают примерно на полсекунды. В результате образуется соединение по типу диффузной сварки;
е) дугопрессовая, которая находит применение при необходимости присоединить к пластине детали вроде болтов или шпилек. Когда шпилька или болт отводится от пластины, между ними возникает дуговой разряд, из-за которого температура их торцов и металла пластины повышается, они нагреваются и расплавляются. В тот момент, когда при отключенном токе шпилька или болт ударяются о пластину, они свариваются;
ж) печная, практикующаяся, например, для приваривания фланцев к трубам. Для этого стыки покрывают специальным составом (вставка между ними латунного или бронзового кольца – еще один вариант). В таком виде все помещают в электропечь, в которой при температуре 1100–1500 °C происходит сваривание;
и) термитно-прессовая, при которой соединяемые части или детали нагревают газовым пламенем и сжимают.
3. Механический, в него входят виды сварки, для осуществления которых используется комбинация механической энергии и давления. Эту группу составляют следующие виды сварки:
а) холодная, в основе которой лежит способность кристаллитов металла срастаться под воздействием высокого давления. Таким способом соединяют исключительно пластичные материалы, такие как алюминий, свинец и др.;
б) ультразвуковая, при которой свариваемые части сближают и стягивают вибрирующим зажимом, через который поступают высокочастотные колебания от магнитострикционного генератора. Благодаря колебаниям состыкованные части нагреваются, после чего свариваются в процессе диффузии атомов контактирующих материалов;
в) магнитно-импульсная, для проведения которой под воздействием импульсного тока индуктора и наведенных им вихревыми токами в соединяемых частях, деталях и ином свариваемые поверхности соударяются;
г) сварка взрывом, которая используется для соединения тонких листов с более массивными (процесс называется «плакирование»), например стали с латунью. Детали укладывают друг на друга, на поверхность помещают взрывчатое вещество, которое при детонировании взрывается и соединяет их в результате соударения;
д) сварка трением, практикуемая для соединения мелких деталей, одна из которых неподвижна, а другая вращается вокруг нее (или они вращаются в разные стороны). При трении выделяется тепло, которое нагревает и сваривает детали.
Техническими признаками, на которые опирается классификация сварки металлов, являются:
– способы защиты металла на участке сварки. Среди используемых представлена сварка в вакууме, защитных газах (в углекислом газе, водяных парах, инертных газах и др.), воздухе, пене, по флюсу и под ним. Кроме того, возможно комбинирование способов;
– степень непрерывности сварочных работ. По этому признаку различаются как прерывистые, так и непрерывные способы сварки;
– наличие механизации процесса сварки. Сюда входят ручные, автоматизированные, механизированные и автоматические способы сварки.
О технологических признаках следует сказать, что для каждого вида сварки они разрабатываются отдельно.
Деформации и напряжения при сварке
Процесс, при котором в результате воздействия силы форма и размер твердого тела изменяют свою форму, называется деформацией. Различаются следующие ее виды:
– упругая, при которой тело восстанавливает исходную форму, как только действие силы прекращается. Такая деформация, как правило, бывает незначительной, например для низкоуглеродистых сталей она составляет не более 0,2 %.
– остаточная (пластическая), возникающая в том случае, если тело после устранения воздействия не возвращается в первоначальное состояние. Этот вид деформации характерен для пластичных тел, а также отмечается при приложении к телу очень значительной силы. Для пластической деформации нагретого металла, в отличие от холодного, требуется меньше нагрузки.
Степень деформации зависит от величины приложенной силы, т. е. между ними прослеживается прямо пропорциональная зависимость: чем больше сила, тем сильнее деформация.
Силы, которые действуют на изделие, делятся на:
– внешние, к которым относятся собственно вес изделия, давление газа на стенки сосуда и пр. Такие нагрузки могут быть статическими (не изменяющимися по величине и направлению), динамическими (переменными) или ударными;
– внутренние, возникающие в результате изменения структуры металла, которое возможно под воздействием внешней нагрузки или, например, сварки и др. Рассчитывая прочность изделия, внутреннюю силу обычно называют усилием.
Величину усилия характеризует и напряжение, которое возникает в теле в результате этого усилия. Таким образом, между напряжением и деформацией имеется тесная связь.
Относительно сечения металла действующие на него силы могут иметь разное направление. В соответствии с этим возникает напряжение растяжения, сжатия, кручения, среза или изгиба (рис. 3).
Рис. 3. Виды напряжения, изменяющие форму металла и сплава (стрелки указывают направление уравновешивающих сил): а – растяжение; б – сжатие; в – кручение; г – срез; д – изгиб
Появление деформации в сварных конструкциях объясняется возникновением внутренних напряжений, причины которых могут быть разными и подразделяются на две группы.
К первой относятся неизбежные причины, которые обязательно возникают в ходе обработки изделия. При сварке это:
1. Кристаллизационная усадка наплавленного металла. Когда он переходит из жидкого состояния в твердое, его плотность возрастает, поэтому изменяется и его объем (это и называется усадкой), например уменьшение объема олова в таком случае может достигать 26 %. Данный процесс сопровождается растягивающими напряжениями, которые развиваются в соседних участках и влекут за собой соответствующие им напряжения и деформации. Усадка измеряется в процентах от первоначального линейного размера, а каждый металл или сплав имеет собственные показатели (табл. 1).
Напряжения, причиной которых является усадка, увеличиваются до тех пор, пока не наступает момент перехода упругих деформаций в пластические. При низкой пластичности металла на наиболее слабом участке может образоваться трещина. Чаще всего таким местом бывает околошовная зона.
При сварке наблюдаются два вида усадки, которые вызывают соответствующие деформации:
а) продольная (рис. 4), которая приводит к уменьшению длины листов при выполнении продольных швов. При несовпадении центров тяжести поперечного сечения шва и сечения свариваемой детали усадка вызывает ее коробление;
Рис. 4. Продольная усадка и деформации при различном расположении шва по отношению к центру тяжести сечения элемента: а – при симметричном; б, в – при несимметричном; 1 – график напряжений; 2 – шов; ΔL – деформация; b – ширина зоны нагрева; напряжение сжатия; + – напряжение растяжения; г – при несимметричном; 2 – шов
б) поперечная (рис. 5), следствием которой всегда является коробление листов в сторону более значительного объема наплавленного металла, т. е. листы коробятся вверх, в направлении утолщения шва. Фиксация детали воспрепятствует деформации от усадки, но станет причиной возникновения напряжений в закрепленных участках.
Рис. 5. Поперечная усадка и деформации: а – деформации до и после сварки; б – график распределения напряжения (О – центр тяжести поперечного сечения шва; напряжение сжатия; + – напряжение растяжения)
Величина деформаций при сварке зависит, во-первых, от размера зоны нагрева: чем больший объем металла подвергается нагреванию, тем значительнее деформации. Следует отметить, что для различных видов сварки характерны разные по размеру зоны нагрева и деформации, в частности при газовой сварке кислородно-ацетиленовым пламенем она больше, чем при дуговой сварке.
Во-вторых, имеют значение размер и положение сварного шва. Величина деформации тем существеннее, чем длиннее шов и больше его сечение, определенную роль играют также несимметричность шва и главной оси сечения свариваемого изделия.
В-третьих, если деталь сложна по своей форме, то швов на ней бывает больше, поэтому можно предположить, что напряжения и деформация обязательно проявятся.
2. Неравномерный нагрев свариваемых частей или деталей. Как известно, при нагревании тела расширяются, а при охлаждении – сужаются. При сварке используется сосредоточенный источник тепла, например сварочная дуга или сварочное пламя, который с определенной скоростью перемещается вдоль шва и поэтому неравномерно нагревает его. Если свободному расширению или сокращению мешают какие-либо препятствия, то в изделии развиваются внутренние напряжения. Более холодные соседние участки и становятся такой помехой, поскольку их расширение выражено в меньшей степени, чем у нагретых участков. Поскольку термические напряжения, ставшие следствием неравномерного нагревания, развиваются без внешнего воздействия, то они называются внутренними, или собственными. Наиболее важными являются те из них, которые возникают при охлаждении изделия, причем напряжения, действующие вдоль шва, менее опасны, поскольку не меняют прочности сварного соединения, в отличие от напряжений, перпендикулярных шву, которые приводят к образованию трещин в околошовной зоне;
3. Структурные трансформации, которые развиваются в околошовной зоне или металле шва. В процессе нагревания и охлаждения металла размер и расположение зерен относительно друг друга изменяются, что отражается на объеме металла и становится причиной возникновения внутренних напряжений со всеми вытекающими последствиями, представленными в первом пункте. В наибольшей степени этому подвержены легированные и высокоуглеродистые стали, предрасположенные к закалке; низкоуглеродистые – в меньшей. В последнем случае при изготовлении сварных конструкций это явление может не приниматься в расчет.
– упругая, при которой тело восстанавливает исходную форму, как только действие силы прекращается. Такая деформация, как правило, бывает незначительной, например для низкоуглеродистых сталей она составляет не более 0,2 %.
– остаточная (пластическая), возникающая в том случае, если тело после устранения воздействия не возвращается в первоначальное состояние. Этот вид деформации характерен для пластичных тел, а также отмечается при приложении к телу очень значительной силы. Для пластической деформации нагретого металла, в отличие от холодного, требуется меньше нагрузки.
Степень деформации зависит от величины приложенной силы, т. е. между ними прослеживается прямо пропорциональная зависимость: чем больше сила, тем сильнее деформация.
Силы, которые действуют на изделие, делятся на:
– внешние, к которым относятся собственно вес изделия, давление газа на стенки сосуда и пр. Такие нагрузки могут быть статическими (не изменяющимися по величине и направлению), динамическими (переменными) или ударными;
– внутренние, возникающие в результате изменения структуры металла, которое возможно под воздействием внешней нагрузки или, например, сварки и др. Рассчитывая прочность изделия, внутреннюю силу обычно называют усилием.
Величину усилия характеризует и напряжение, которое возникает в теле в результате этого усилия. Таким образом, между напряжением и деформацией имеется тесная связь.
Относительно сечения металла действующие на него силы могут иметь разное направление. В соответствии с этим возникает напряжение растяжения, сжатия, кручения, среза или изгиба (рис. 3).
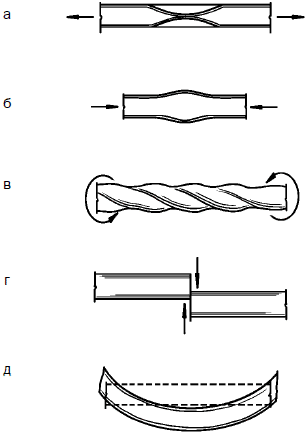
Появление деформации в сварных конструкциях объясняется возникновением внутренних напряжений, причины которых могут быть разными и подразделяются на две группы.
К первой относятся неизбежные причины, которые обязательно возникают в ходе обработки изделия. При сварке это:
1. Кристаллизационная усадка наплавленного металла. Когда он переходит из жидкого состояния в твердое, его плотность возрастает, поэтому изменяется и его объем (это и называется усадкой), например уменьшение объема олова в таком случае может достигать 26 %. Данный процесс сопровождается растягивающими напряжениями, которые развиваются в соседних участках и влекут за собой соответствующие им напряжения и деформации. Усадка измеряется в процентах от первоначального линейного размера, а каждый металл или сплав имеет собственные показатели (табл. 1).
Таблица 1. ЛИНЕЙНАЯ УСАДКА НЕКОТОРЫХ МЕТАЛЛОВ И СПЛАВОВ
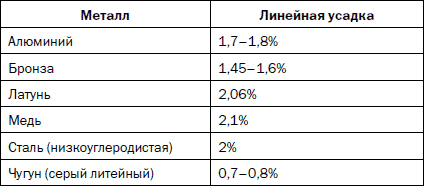
При сварке наблюдаются два вида усадки, которые вызывают соответствующие деформации:
а) продольная (рис. 4), которая приводит к уменьшению длины листов при выполнении продольных швов. При несовпадении центров тяжести поперечного сечения шва и сечения свариваемой детали усадка вызывает ее коробление;
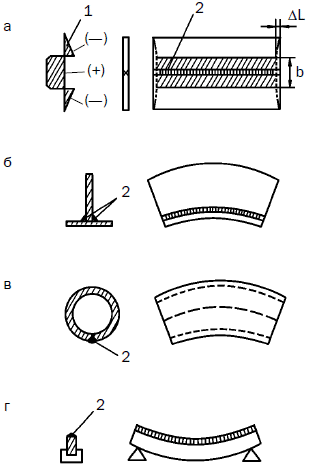
б) поперечная (рис. 5), следствием которой всегда является коробление листов в сторону более значительного объема наплавленного металла, т. е. листы коробятся вверх, в направлении утолщения шва. Фиксация детали воспрепятствует деформации от усадки, но станет причиной возникновения напряжений в закрепленных участках.
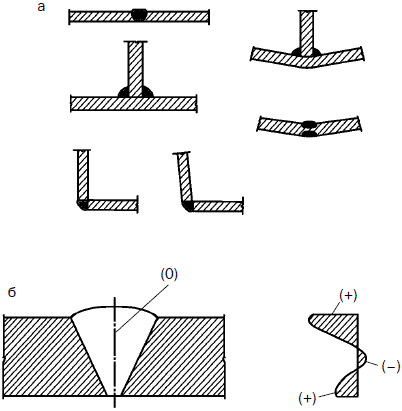
Величина деформаций при сварке зависит, во-первых, от размера зоны нагрева: чем больший объем металла подвергается нагреванию, тем значительнее деформации. Следует отметить, что для различных видов сварки характерны разные по размеру зоны нагрева и деформации, в частности при газовой сварке кислородно-ацетиленовым пламенем она больше, чем при дуговой сварке.
Во-вторых, имеют значение размер и положение сварного шва. Величина деформации тем существеннее, чем длиннее шов и больше его сечение, определенную роль играют также несимметричность шва и главной оси сечения свариваемого изделия.
В-третьих, если деталь сложна по своей форме, то швов на ней бывает больше, поэтому можно предположить, что напряжения и деформация обязательно проявятся.
2. Неравномерный нагрев свариваемых частей или деталей. Как известно, при нагревании тела расширяются, а при охлаждении – сужаются. При сварке используется сосредоточенный источник тепла, например сварочная дуга или сварочное пламя, который с определенной скоростью перемещается вдоль шва и поэтому неравномерно нагревает его. Если свободному расширению или сокращению мешают какие-либо препятствия, то в изделии развиваются внутренние напряжения. Более холодные соседние участки и становятся такой помехой, поскольку их расширение выражено в меньшей степени, чем у нагретых участков. Поскольку термические напряжения, ставшие следствием неравномерного нагревания, развиваются без внешнего воздействия, то они называются внутренними, или собственными. Наиболее важными являются те из них, которые возникают при охлаждении изделия, причем напряжения, действующие вдоль шва, менее опасны, поскольку не меняют прочности сварного соединения, в отличие от напряжений, перпендикулярных шву, которые приводят к образованию трещин в околошовной зоне;
3. Структурные трансформации, которые развиваются в околошовной зоне или металле шва. В процессе нагревания и охлаждения металла размер и расположение зерен относительно друг друга изменяются, что отражается на объеме металла и становится причиной возникновения внутренних напряжений со всеми вытекающими последствиями, представленными в первом пункте. В наибольшей степени этому подвержены легированные и высокоуглеродистые стали, предрасположенные к закалке; низкоуглеродистые – в меньшей. В последнем случае при изготовлении сварных конструкций это явление может не приниматься в расчет.