Страница:
Вторую группу составляют сопутствующие причины, которые можно предупредить или устранить. К ним относятся:
– ошибочные конструктивные решения сварных швов, например небольшое расстояние между соседними швами, слишком частое пересечение сварных швов, ошибки в выборе типа соединения и др.;
– несоблюдение техники и технологии сварки, в частности плохая подготовка кромок металла, нарушение режима сварки, использование несоответствующего электрода и др.;
– низкая квалификация исполнителя.
Величина деформаций при сварке во многом определяется теплопроводностью металла. Между ними существует прямо пропорциональная зависимость: чем выше теплопроводность, тем более равномерно распространяется поток тепла по сечению металла, тем менее значительными будут деформации. Например, при сварке нержавеющей стали как менее теплопроводной возникают большие деформации, чем при сварке низкоуглеродистых сталей.
Напряжения и деформации, которые имеют место исключительно в ходе сварки, а по ее окончании исчезают, называются временными; а если они сохраняются после охлаждения шва – остаточными. Практическое значение последних особенно велико, поскольку они могут сказываться на работе детали, изделия, всей конструкции. Если деформации носят локальный характер (например, на отдельных участках появляются выпучины, волнистость и др.), то они называются местными; если в результате деформации терпят изменения геометрические оси и размеры изделия или конструкции в целом – общими.
Кроме того, деформации могут возникать как в плоскости изделия, так и вне ее (рис. 6).
Рис. 6. Некоторые виды деформации: а – в плоскости сварного соединения; б – вне плоскости сварного соединения; 1 – форма изделия до сварки; 2 – форма изделия после сварки
Для уменьшения деформаций и напряжений при сварке придерживаются следующих конструктивных и технологических рекомендаций:
1. При подборе материала для сварных конструкций руководствуются правилом: использовать такие марки основного металла и электродов, которые либо не имеют склонности к закалке, либо подвержены ей в наименьшей степени и способны давать пластичный металл шва.
2. Избегают закладывать в конструкциях (особенно в ответственных), тем более рассчитанных на работу при ударах или вибрации, многочисленные сварные швы и их пересечения, а также использовать короткие швы замкнутого контура, поскольку в этих зонах, как правило, концентрируются собственные напряжения. Чтобы снизить тепловложения в изделие или конструкцию, оптимальная длина катетов швов должна быть не более 16 мм.
3. Стараются симметрично располагать ребра жесткости в конструкциях и сводят их количество к минимуму. Симметричность необходима и при расположении сварных швов, так как это уравновешивает возникающие деформации (рис. 7), т. е. последующий слой должен вызывать деформации, противоположные тем, которые развились в предыдущем слое.
Рис. 7. Последовательность наложения сварных швов для уравновешивания деформаций
Эффективен и способ обратных деформаций (рис. 8). Перед сваркой в конструкции (как правило, швы в ней должны располагаться с одной стороны относительно оси либо на различных расстояниях от нее) вызывают деформацию, обратную той, что возникнет в ней при сварке.
Рис. 8. Сваривание гнутых профилей как пример применения обратной деформации
4. Ограничивают применение таких способов соединения, как косынки, накладки и др.
5. По возможности отдают предпочтение стыковым швам, для которых концентрация напряжений не столь характерна.
6. Предполагают минимальные зазоры на разных участках сварки.
7. В сопряжениях деталей предусматривают возможность свободной усадки металла шва при охлаждении в отсутствие жестких заделок.
8. Практикуют изготовление конструкций по секциям, чтобы потом сваривать готовые узлы. Если последние имеют сложную конфигурацию, то заготавливают литые и штампованные детали, чтобы снизить неблагоприятное воздействие жестких связей, которые дают сварные швы.
9. Выбирают технологически обоснованную последовательность (рис. 9) выполнения сварных швов, при которой допускается свободная деформация свариваемых деталей. Если, например, требуется соединить листы, то в первую очередь выполняют поперечные швы, в результате чего получают полосы, которые потом сваривают продольными швами. Такая очередность исключает жесткую фиксацию соединяемых частей листов и позволяет им свободно деформироваться при сварке.
Рис. 9. Оптимальная последовательность выполнения сварных швов при сварке листов: а – настила; б – двутавровой балки
Направление ведения сварного шва также имеет значение. Если вести его на проход либо от центра к концам, то в середине шва разовьются поперечные напряжения сжатия; если двигаться от краев к центру, то в середине шва не избежать появления поперечных напряжений растяжения, следствием которых будут трещины в околошовной зоне или самом шве (рис. 10).
Рис. 10. Напряжение в продольном сечении шва при сварке (– – напряжение сжатия; + – напряжение растяжения): а – на проход; б – от концов к центру
10. При соединении частей из металла значительной толщины (более 20–25 мм) применяют многослойную дуговую сварку, выполняя швы горкой или каскадом (рис. 11). Шов горкой накладывается следующим образом: первый слой имеет длину примерно 200–300 мм, второй длиннее первого в 2 раза, третий длиннее второго на 200–300 мм и т. д. Достигнув «горки», сварку продолжают в обе стороны от нее короткими валиками. Такой способ способствует поддержанию участка сварки в нагретом состоянии. В результате тепло распространяется по металлу более равномерно, что снижает напряжения.
Рис. 11. Очередность наложения швов при многослойной дуговой сварке (размеры указаны в миллиметрах): а – горкой; 1 – ось «горки»; 2 – толщина металла; б – каскадом
11. Помогает снизить коробление швов соединяемых конструкций и деталей выполнение швов в обратноступенчатом порядке (рис. 12). Для этого протяженные швы делят на части длиной 150–200 мм и сваривают их, ведя каждый последующий слой в направлении, обратном предыдущему слою, причем стыки следует размещать вразбежку. Причина таких действий заключается в том, что деформации в соседних участках будут противоположно направленными по отношению друг к другу и равномерными, поскольку металл будет прогреваться равномерно.
Рис. 12. Последовательность наложения обратнопоступательного шва
12. Рассчитывают адекватный тепловой режим сварки. Если при работе есть возможность перемещать изделие (деталь) или если основной металл предрасположен к закалке, тогда используют более сильный тепловой режим, благодаря чему объем разогреваемого материала возрастает, а сам он остывает медленнее. В определенных ситуациях (если сварка проводится при пониженной температуре воздуха, металл имеет большую толщину или является сталью, склонной к закалке, и др.) помогают предварительный или сопровождающий подогрев либо околошовной зоны, либо всего изделия. Температура, до которой следует довести металл, зависит от его свойств и составляет 300–400 °C для бронзы, 250-270 °C для алюминия, 500–600 °C для стали, 700–800 °C для чугуна и т. д.
Если сваривают жестко зафиксированные детали или конструкции, тогда применяют менее интенсивный тепловой режим и варят электродами, способными давать пластичный металл шва.
13. Осуществляют отжиг и нормализацию изделия или конструкции после окончания сварки (последнее полностью ликвидирует напряжения). При отжиге температуру стального изделия доводят до 820–930 °C, выдерживают (общее время составляет примерно 30 минут, длительная выдержка нежелательна, поскольку приводит к росту зерен) и постепенно охлаждают (на 50–75 °C в час), доводя температуру до 300 °C. Это дает ряд преимуществ: во-первых, шов приобретает мелкозернистую структуру с улучшенным сцеплением зерен, благодаря которой металл шва и околошовной зоны становится более пластичным, во-вторых, металл шва получается менее твердым, что имеет большое значение для последующей обработки резанием или давлением; в-третьих, это полностью снимает внутренние напряжения в изделии.
Основные отличия нормализации от полного отжига – более высокая скорость охлаждения, для чего температура, до которой нагревают изделие, на 20–30 °C превышает критическую, и то, что выдержка и охлаждение проводятся на воздухе.
14. Избегают планировать в изделиях и конструкциях сварные швы, неудобные для выполнения, например вертикальные, потолочные.
15. Обеспечивают минимальную погонную энергию, достижимую при высокой скорости сварки в сочетании с наименьшими поперечными сечениями швов.
16. Уменьшают число прихваток и их сечения.
17. Проковывают швы в холодном или горячем состоянии, что уменьшает внутренние напряжения и увеличивает прочность конструкции.
Сварочные материалы и оборудование для дуговой сварки
Сварочная проволока
Электроды
– ошибочные конструктивные решения сварных швов, например небольшое расстояние между соседними швами, слишком частое пересечение сварных швов, ошибки в выборе типа соединения и др.;
– несоблюдение техники и технологии сварки, в частности плохая подготовка кромок металла, нарушение режима сварки, использование несоответствующего электрода и др.;
– низкая квалификация исполнителя.
Величина деформаций при сварке во многом определяется теплопроводностью металла. Между ними существует прямо пропорциональная зависимость: чем выше теплопроводность, тем более равномерно распространяется поток тепла по сечению металла, тем менее значительными будут деформации. Например, при сварке нержавеющей стали как менее теплопроводной возникают большие деформации, чем при сварке низкоуглеродистых сталей.
Напряжения и деформации, которые имеют место исключительно в ходе сварки, а по ее окончании исчезают, называются временными; а если они сохраняются после охлаждения шва – остаточными. Практическое значение последних особенно велико, поскольку они могут сказываться на работе детали, изделия, всей конструкции. Если деформации носят локальный характер (например, на отдельных участках появляются выпучины, волнистость и др.), то они называются местными; если в результате деформации терпят изменения геометрические оси и размеры изделия или конструкции в целом – общими.
Кроме того, деформации могут возникать как в плоскости изделия, так и вне ее (рис. 6).
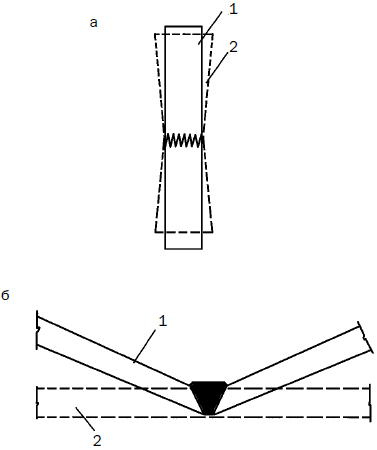
Для уменьшения деформаций и напряжений при сварке придерживаются следующих конструктивных и технологических рекомендаций:
1. При подборе материала для сварных конструкций руководствуются правилом: использовать такие марки основного металла и электродов, которые либо не имеют склонности к закалке, либо подвержены ей в наименьшей степени и способны давать пластичный металл шва.
2. Избегают закладывать в конструкциях (особенно в ответственных), тем более рассчитанных на работу при ударах или вибрации, многочисленные сварные швы и их пересечения, а также использовать короткие швы замкнутого контура, поскольку в этих зонах, как правило, концентрируются собственные напряжения. Чтобы снизить тепловложения в изделие или конструкцию, оптимальная длина катетов швов должна быть не более 16 мм.
3. Стараются симметрично располагать ребра жесткости в конструкциях и сводят их количество к минимуму. Симметричность необходима и при расположении сварных швов, так как это уравновешивает возникающие деформации (рис. 7), т. е. последующий слой должен вызывать деформации, противоположные тем, которые развились в предыдущем слое.
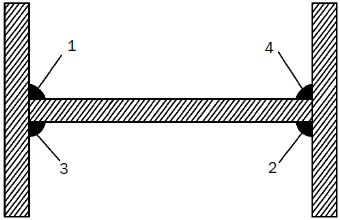
Эффективен и способ обратных деформаций (рис. 8). Перед сваркой в конструкции (как правило, швы в ней должны располагаться с одной стороны относительно оси либо на различных расстояниях от нее) вызывают деформацию, обратную той, что возникнет в ней при сварке.
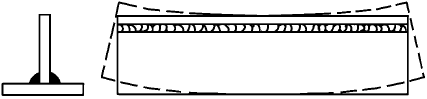
4. Ограничивают применение таких способов соединения, как косынки, накладки и др.
5. По возможности отдают предпочтение стыковым швам, для которых концентрация напряжений не столь характерна.
6. Предполагают минимальные зазоры на разных участках сварки.
7. В сопряжениях деталей предусматривают возможность свободной усадки металла шва при охлаждении в отсутствие жестких заделок.
8. Практикуют изготовление конструкций по секциям, чтобы потом сваривать готовые узлы. Если последние имеют сложную конфигурацию, то заготавливают литые и штампованные детали, чтобы снизить неблагоприятное воздействие жестких связей, которые дают сварные швы.
9. Выбирают технологически обоснованную последовательность (рис. 9) выполнения сварных швов, при которой допускается свободная деформация свариваемых деталей. Если, например, требуется соединить листы, то в первую очередь выполняют поперечные швы, в результате чего получают полосы, которые потом сваривают продольными швами. Такая очередность исключает жесткую фиксацию соединяемых частей листов и позволяет им свободно деформироваться при сварке.
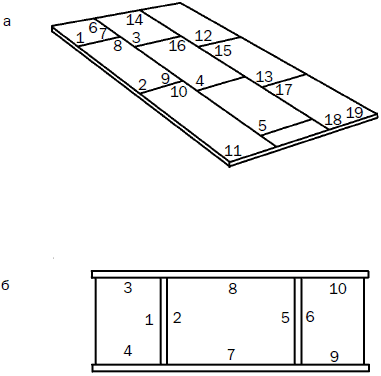
Направление ведения сварного шва также имеет значение. Если вести его на проход либо от центра к концам, то в середине шва разовьются поперечные напряжения сжатия; если двигаться от краев к центру, то в середине шва не избежать появления поперечных напряжений растяжения, следствием которых будут трещины в околошовной зоне или самом шве (рис. 10).
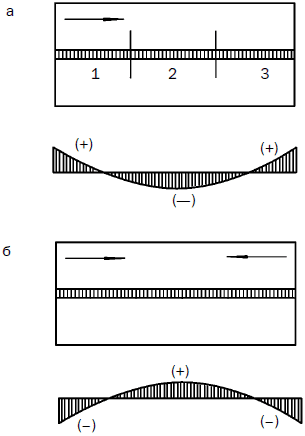
10. При соединении частей из металла значительной толщины (более 20–25 мм) применяют многослойную дуговую сварку, выполняя швы горкой или каскадом (рис. 11). Шов горкой накладывается следующим образом: первый слой имеет длину примерно 200–300 мм, второй длиннее первого в 2 раза, третий длиннее второго на 200–300 мм и т. д. Достигнув «горки», сварку продолжают в обе стороны от нее короткими валиками. Такой способ способствует поддержанию участка сварки в нагретом состоянии. В результате тепло распространяется по металлу более равномерно, что снижает напряжения.
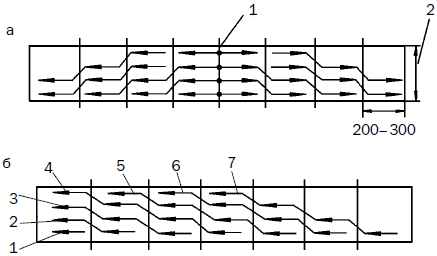
11. Помогает снизить коробление швов соединяемых конструкций и деталей выполнение швов в обратноступенчатом порядке (рис. 12). Для этого протяженные швы делят на части длиной 150–200 мм и сваривают их, ведя каждый последующий слой в направлении, обратном предыдущему слою, причем стыки следует размещать вразбежку. Причина таких действий заключается в том, что деформации в соседних участках будут противоположно направленными по отношению друг к другу и равномерными, поскольку металл будет прогреваться равномерно.
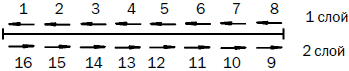
12. Рассчитывают адекватный тепловой режим сварки. Если при работе есть возможность перемещать изделие (деталь) или если основной металл предрасположен к закалке, тогда используют более сильный тепловой режим, благодаря чему объем разогреваемого материала возрастает, а сам он остывает медленнее. В определенных ситуациях (если сварка проводится при пониженной температуре воздуха, металл имеет большую толщину или является сталью, склонной к закалке, и др.) помогают предварительный или сопровождающий подогрев либо околошовной зоны, либо всего изделия. Температура, до которой следует довести металл, зависит от его свойств и составляет 300–400 °C для бронзы, 250-270 °C для алюминия, 500–600 °C для стали, 700–800 °C для чугуна и т. д.
Если сваривают жестко зафиксированные детали или конструкции, тогда применяют менее интенсивный тепловой режим и варят электродами, способными давать пластичный металл шва.
13. Осуществляют отжиг и нормализацию изделия или конструкции после окончания сварки (последнее полностью ликвидирует напряжения). При отжиге температуру стального изделия доводят до 820–930 °C, выдерживают (общее время составляет примерно 30 минут, длительная выдержка нежелательна, поскольку приводит к росту зерен) и постепенно охлаждают (на 50–75 °C в час), доводя температуру до 300 °C. Это дает ряд преимуществ: во-первых, шов приобретает мелкозернистую структуру с улучшенным сцеплением зерен, благодаря которой металл шва и околошовной зоны становится более пластичным, во-вторых, металл шва получается менее твердым, что имеет большое значение для последующей обработки резанием или давлением; в-третьих, это полностью снимает внутренние напряжения в изделии.
Основные отличия нормализации от полного отжига – более высокая скорость охлаждения, для чего температура, до которой нагревают изделие, на 20–30 °C превышает критическую, и то, что выдержка и охлаждение проводятся на воздухе.
14. Избегают планировать в изделиях и конструкциях сварные швы, неудобные для выполнения, например вертикальные, потолочные.
15. Обеспечивают минимальную погонную энергию, достижимую при высокой скорости сварки в сочетании с наименьшими поперечными сечениями швов.
16. Уменьшают число прихваток и их сечения.
17. Проковывают швы в холодном или горячем состоянии, что уменьшает внутренние напряжения и увеличивает прочность конструкции.
Сварочные материалы и оборудование для дуговой сварки
Сварочная проволока
Чтобы заполнить зазор между свариваемыми частями, применяют присадочный материал, который имеет вид прутка или проволоки и вводится в зону сварочной дуги.
Если осуществляется ручная дуговая сварка, то используют плавящиеся электроды, которые представляют собой прутки или стержни с нанесенным на них специальным покрытием (обмазкой). При механизированном процессе электрод имеет вид проволоки, которая намотана на кассету (катушку). Для плавящихся электродов и наплавочных работ применяются различные марки проволоки (табл. 2).
Для маркировки сварочной проволоки существует специальное обозначение – индекс «Св», после которого идут цифры и буквы. За каждой из них стоит определенное значение:
– индекс «Св» обозначает «сварочная»;
– две цифры после индекса – среднее содержание в материале углерода, составляющее сотые доли процента;
– буквы – легирующие химические элементы: азот (А), который встречается исключительно в высоколегированной проволоке, марганец (Г), кремний (С), хром (Х), никель (Н), титан (Т), алюминий (Ю), молибден (М), ниобий (Б), цирконий (Ц), бор (Р), вольфрам (В), ванадий (Ф), медь (Д), кобальт (К);
– цифры после букв – содержание указанного элемента, составляющее проценты; отсутствие цифры после букв показывает, что содержание данного элемента составляет менее 1 %;
– буква А, завершающая маркировку низкоуглеродистой и легированной проволоки, свидетельствует о повышенной чистоте материала по содержанию серы и фосфора; удвоенная буква А в проволоке марки Св-08 АА – о пониженном содержании серы и фосфора относительно проволоки марки Св-08 А.
Например, проволока, имеющая маркировку Св-08 ХГ2 С, расшифровывается так: в состав сварочной проволоки входят углерод (0,08 %), хром (менее 1 %), марганец (до 2 %), кремний (менее 1 %); Св-02 Х19 Н9 – углерод (не более 0,02 %), хром (19 %), никель (9 %).
При всех видах сварки плавлением и для электродов используется стальная сварочная проволока различного диаметра – 0,3, 0,5, 0,8, 1, 1,2, 1,6 2, 2,5, 3, 4, 5, 6, 8, 10 или 12 мм, причем для изготовления электродов для ручной дуговой сварки применяется проволока диаметром 2–6 мм; для автоматизированной и механизированной сварки в среде защитных газов и под флюсом – 0,8–5 мм; для наплавочных работ – от 5 мм.
Стальная наплавочная проволока диаметром 0,3–8 мм изготавливается из стали различных марок – углеродистой (Нп-25, Нп-40 и т. д.); легированной (Нп-40 Г, Нп-30 ХГСА и др.); высоколегированной (Нп-30 Х13 и др.).
Стальная и алюминиевая сварочная проволока отличается от обычной товарной тем, что должна отвечать специальным требованиям, которые изложены в ГОСТах и касаются следующего:
1. Химический состав. По этому признаку марки стальной проволоки подразделяются на три основные группы:
– углеродистые. Они используются для сварки низко-, среднеуглеродистых и некоторых низколегированных сталей, например Св-08; Св-08 А; Св-08 АА и др.;
– легированные такими элементами, как хром, никель, марганец, титан и др. Допускается 2,5-10 %-ное данных компонентов. Они предназначаются для сварки низколегированных сталей. В эту группу входит проволока марок Св-08 ГС; Св-08 Г2 С и др.;
– высоколегированные (содержание легирующих элементов составляет более 10 %), например Св-06 Х14; Св-02 Х19 Н9 и др.
Всего ГОСТ 2246-70 предусматривает применение 77 марок стальной сварочной проволоки, химический состав некоторых из них представлен в табл. 3.
2. Способ и точность изготовления.
3. Упаковка.
4. Транспортировка.
5. Хранение.
Проволока реализуется в виде мотков, внутренний диаметр которых составляет 150–750 мм, а масса – 1,5-40 кг, и бухт, имеющих бирку с указанием выходных данных, в частности завода-изготовителя, маркировки, номера партии, клейма техконтроля. Кроме того, прилагается так называемый сертификат соответствия.
В последние годы для сварки и наплавки стали шире применять порошковую проволоку, имеющую вид свернутой из стальной ленты (20 х 0,2 мм) трубки (для этого используется лента из низкоуглеродистой стали марки 08 КП холодного проката мягкая или особо мягкая), в которую засыпана шихта (порошок) из газо– и шлакообразующих компонентов, благодаря которым значительно улучшаются сварочный процесс и его результат. Сварной шов отличается высокими механическим свойствами, визуально выглядит более аккуратно. Кроме того, снижаются деформации, возрастает глубина проплавления и устраняется разбрызгивание металла при сварке.
Для придания проволоке необходимой жесткости и защиты от смятия подающими роликами при наплавке ее сечение специально делают сложным (рис. 13).
Рис. 13. Сечение оболочек порошковой проволоки: а – трубчатое; б – трубчатое с нахлестом; в, г – с загибом в оболочке; д – двухслойное
Шихта может иметь различный состав, в частности:
– рутиловый;
– рутилово-целлюлозный;
– рутилово-флюоритный;
– карбонатно-флюоритный;
– флюоритный (флюорит – это плавиковый шпат CaF2, о котором упоминалось выше).
Но при этом она должна быть такой, чтобы сплав, который получится после расплавления оболочки проволоки и порошка и их затвердения, имел бы химический состав и характеристики, требуемые от металла шва.
Порошковая проволока находит применение в следующих случаях:
– для сварки открытой дугой;
– для сварки под флюсом;
– для сварки в защитных газах (в углекислом, инертных);
– для наплавки с целью образования твердосплавного слоя.
В строительно-монтажных работах используется порошковая проволока марок ПП-АН1, ПП-АН2 и др.
Порошковая проволока различается диаметром, который может составлять 2,3, 2,5 или 3,2 мм. Как и сварочная проволока, она имеет специальную маркировку, которая расшифровывается следующим образом:
– тип проволоки обозначается буквами ПГ (нуждающаяся в дополнительной защите) или ПС (самозащитная);
– цифры, следующие за буквами, указывают характеристику прочности металла шва или сварного соединения по гарантируемому пределу прочности;
– буквы Н, В, Вх, Ву, Т обозначают допускаемое пространственное положение при выполнении сварки (нижнее и горизонтальное на вертикальной поверхности; вертикальное, нижнее и горизонтальное; горизонтальные швы; вертикальные швы; любые положения, в том числе и кольцевые швы без вращения);
– последние цифры указывают на критическую температуру перехода к хрупкому состоянию металла шва, характеризующемуся значениями ударной вязкости менее 35 Дж/см2:
0 – +20 °C; 1–0 °C; 2 – -20 °C; 3 – -30 °C; 4 – -40 °C; <5 – -50 °C;
– буква Д, присутствующая в обозначении, говорит о том, что требования по температуре не регламентированы, т. е. применение проволоки ограничено исключительно сваркой наиболее неответственных изделий и конструкций, которые предполагается эксплуатировать при положительной температуре окружающего воздуха.
Например, маркировку порошковой проволоки ПС-50-Н2 следует понимать так:
– ПС – «проволока самозащитная»;
– 50 – минимально гарантируемый предел прочности металла шва или сварного соединения составляет 50 кгс/мм2;
– Н – проволока используется для сварки в нижнем положении;
– критическая температура – -20 °C.
Порошковая проволока должна соответствовать определенным требованиям:
– обеспечивать легкое возбуждение сварочной дуги и ее стабильное горение;
– плавиться равномерно, с минимальным разбрызгиванием;
– образовывать шлак, равномерно покрывающий сварочную ванну и не создающий проблем при отделении его после охлаждения сварного шва;
– формировать качественный и прочный сварной шов, т. е. такой, который не имеет пор, трещин и других повреждений и дефектов.
Порошковую проволоку используют при сварке конструкций из углеродистых и низколегированных сталей, которые рассчитаны на средние и тяжелые режимы эксплуатации.
Если осуществляется ручная дуговая сварка, то используют плавящиеся электроды, которые представляют собой прутки или стержни с нанесенным на них специальным покрытием (обмазкой). При механизированном процессе электрод имеет вид проволоки, которая намотана на кассету (катушку). Для плавящихся электродов и наплавочных работ применяются различные марки проволоки (табл. 2).
Таблица 2. МАРКИ ПРОВОЛОКИ, ПРЕДНАЗНАЧЕННОЙ ДЛЯ СВАРКИ ПЛАВЯЩИМИСЯ ЭЛЕКТРОДАМИ И НАПЛАВОЧНЫХ РАБОТ
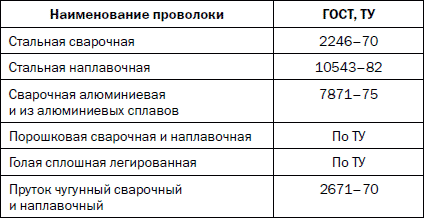
– индекс «Св» обозначает «сварочная»;
– две цифры после индекса – среднее содержание в материале углерода, составляющее сотые доли процента;
– буквы – легирующие химические элементы: азот (А), который встречается исключительно в высоколегированной проволоке, марганец (Г), кремний (С), хром (Х), никель (Н), титан (Т), алюминий (Ю), молибден (М), ниобий (Б), цирконий (Ц), бор (Р), вольфрам (В), ванадий (Ф), медь (Д), кобальт (К);
– цифры после букв – содержание указанного элемента, составляющее проценты; отсутствие цифры после букв показывает, что содержание данного элемента составляет менее 1 %;
– буква А, завершающая маркировку низкоуглеродистой и легированной проволоки, свидетельствует о повышенной чистоте материала по содержанию серы и фосфора; удвоенная буква А в проволоке марки Св-08 АА – о пониженном содержании серы и фосфора относительно проволоки марки Св-08 А.
Например, проволока, имеющая маркировку Св-08 ХГ2 С, расшифровывается так: в состав сварочной проволоки входят углерод (0,08 %), хром (менее 1 %), марганец (до 2 %), кремний (менее 1 %); Св-02 Х19 Н9 – углерод (не более 0,02 %), хром (19 %), никель (9 %).
При всех видах сварки плавлением и для электродов используется стальная сварочная проволока различного диаметра – 0,3, 0,5, 0,8, 1, 1,2, 1,6 2, 2,5, 3, 4, 5, 6, 8, 10 или 12 мм, причем для изготовления электродов для ручной дуговой сварки применяется проволока диаметром 2–6 мм; для автоматизированной и механизированной сварки в среде защитных газов и под флюсом – 0,8–5 мм; для наплавочных работ – от 5 мм.
Стальная наплавочная проволока диаметром 0,3–8 мм изготавливается из стали различных марок – углеродистой (Нп-25, Нп-40 и т. д.); легированной (Нп-40 Г, Нп-30 ХГСА и др.); высоколегированной (Нп-30 Х13 и др.).
Стальная и алюминиевая сварочная проволока отличается от обычной товарной тем, что должна отвечать специальным требованиям, которые изложены в ГОСТах и касаются следующего:
1. Химический состав. По этому признаку марки стальной проволоки подразделяются на три основные группы:
– углеродистые. Они используются для сварки низко-, среднеуглеродистых и некоторых низколегированных сталей, например Св-08; Св-08 А; Св-08 АА и др.;
– легированные такими элементами, как хром, никель, марганец, титан и др. Допускается 2,5-10 %-ное данных компонентов. Они предназначаются для сварки низколегированных сталей. В эту группу входит проволока марок Св-08 ГС; Св-08 Г2 С и др.;
– высоколегированные (содержание легирующих элементов составляет более 10 %), например Св-06 Х14; Св-02 Х19 Н9 и др.
Всего ГОСТ 2246-70 предусматривает применение 77 марок стальной сварочной проволоки, химический состав некоторых из них представлен в табл. 3.
Таблица 3. ХИМИЧЕСКИЙ СОСТАВ СВАРОЧНОЙ ПРОВОЛОКИ НЕКОТОРЫХ МАРОК ПО ГОСТУ 2246-70
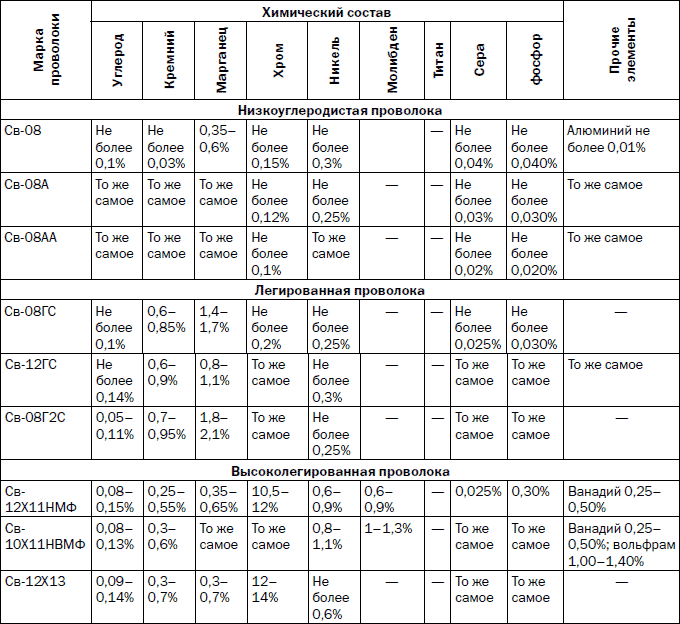
3. Упаковка.
4. Транспортировка.
5. Хранение.
Проволока реализуется в виде мотков, внутренний диаметр которых составляет 150–750 мм, а масса – 1,5-40 кг, и бухт, имеющих бирку с указанием выходных данных, в частности завода-изготовителя, маркировки, номера партии, клейма техконтроля. Кроме того, прилагается так называемый сертификат соответствия.
В последние годы для сварки и наплавки стали шире применять порошковую проволоку, имеющую вид свернутой из стальной ленты (20 х 0,2 мм) трубки (для этого используется лента из низкоуглеродистой стали марки 08 КП холодного проката мягкая или особо мягкая), в которую засыпана шихта (порошок) из газо– и шлакообразующих компонентов, благодаря которым значительно улучшаются сварочный процесс и его результат. Сварной шов отличается высокими механическим свойствами, визуально выглядит более аккуратно. Кроме того, снижаются деформации, возрастает глубина проплавления и устраняется разбрызгивание металла при сварке.
Для придания проволоке необходимой жесткости и защиты от смятия подающими роликами при наплавке ее сечение специально делают сложным (рис. 13).
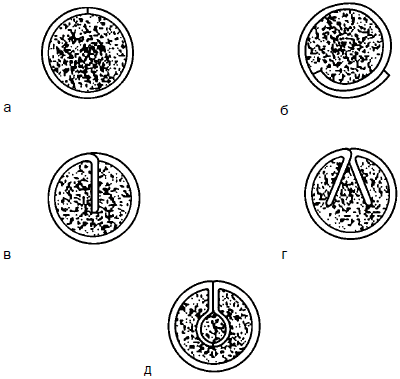
Шихта может иметь различный состав, в частности:
– рутиловый;
– рутилово-целлюлозный;
– рутилово-флюоритный;
– карбонатно-флюоритный;
– флюоритный (флюорит – это плавиковый шпат CaF2, о котором упоминалось выше).
Но при этом она должна быть такой, чтобы сплав, который получится после расплавления оболочки проволоки и порошка и их затвердения, имел бы химический состав и характеристики, требуемые от металла шва.
Порошковая проволока находит применение в следующих случаях:
– для сварки открытой дугой;
– для сварки под флюсом;
– для сварки в защитных газах (в углекислом, инертных);
– для наплавки с целью образования твердосплавного слоя.
В строительно-монтажных работах используется порошковая проволока марок ПП-АН1, ПП-АН2 и др.
Порошковая проволока различается диаметром, который может составлять 2,3, 2,5 или 3,2 мм. Как и сварочная проволока, она имеет специальную маркировку, которая расшифровывается следующим образом:
– тип проволоки обозначается буквами ПГ (нуждающаяся в дополнительной защите) или ПС (самозащитная);
– цифры, следующие за буквами, указывают характеристику прочности металла шва или сварного соединения по гарантируемому пределу прочности;
– буквы Н, В, Вх, Ву, Т обозначают допускаемое пространственное положение при выполнении сварки (нижнее и горизонтальное на вертикальной поверхности; вертикальное, нижнее и горизонтальное; горизонтальные швы; вертикальные швы; любые положения, в том числе и кольцевые швы без вращения);
– последние цифры указывают на критическую температуру перехода к хрупкому состоянию металла шва, характеризующемуся значениями ударной вязкости менее 35 Дж/см2:
0 – +20 °C; 1–0 °C; 2 – -20 °C; 3 – -30 °C; 4 – -40 °C; <5 – -50 °C;
– буква Д, присутствующая в обозначении, говорит о том, что требования по температуре не регламентированы, т. е. применение проволоки ограничено исключительно сваркой наиболее неответственных изделий и конструкций, которые предполагается эксплуатировать при положительной температуре окружающего воздуха.
Например, маркировку порошковой проволоки ПС-50-Н2 следует понимать так:
– ПС – «проволока самозащитная»;
– 50 – минимально гарантируемый предел прочности металла шва или сварного соединения составляет 50 кгс/мм2;
– Н – проволока используется для сварки в нижнем положении;
– критическая температура – -20 °C.
Порошковая проволока должна соответствовать определенным требованиям:
– обеспечивать легкое возбуждение сварочной дуги и ее стабильное горение;
– плавиться равномерно, с минимальным разбрызгиванием;
– образовывать шлак, равномерно покрывающий сварочную ванну и не создающий проблем при отделении его после охлаждения сварного шва;
– формировать качественный и прочный сварной шов, т. е. такой, который не имеет пор, трещин и других повреждений и дефектов.
Порошковую проволоку используют при сварке конструкций из углеродистых и низколегированных сталей, которые рассчитаны на средние и тяжелые режимы эксплуатации.
Электроды
Сварочный электрод представляет собой металлический либо неметаллический электропроводный стержень длиной 250–450 мм со специальным покрытием или без него, через который к свариваемым изделиям или конструкциям подводится электрический ток. Современная промышленность производит более 200 марок электродов, и большая часть из них – это плавящиеся сварочные электроды, предназначенные для ручной дуговой сварки. Все типы сварочных электродов должны соответствовать определенным требованиям:
1) обеспечивать:
– устойчивое горение сварочной дуги;
– качественное формирование сварного шва и его прочность;
– равномерное расплавление стержня и покрытия с минимальным разбрызгиванием металла электрода;
– беспрепятственное удаление шлаков;
– высокопроизводительную сварку;
2) давать металл сварного шва необходимого химического состава;
3) сохранять свои физико-химические и технологические свойства на протяжении заданного количества времени;
4) обладать минимальной токсичностью.
Кроме того, имеются специальные технические требования, например:
– получение металла шва с особыми свойствами, к которым относятся окалино– и износостойкость, коррозионная устойчивость, повышенная прочность;
– формирование шва заранее определенной формы (с глубоким проваром, вогнутой поверхностью);
– осуществление сварки конкретным способом (с опиранием вертикальных швов сверху вниз, в любых пространственных положениях).
Разнообразие сварочных электродов и различные принципы, которые могут быть положены в основу их классификации, делают разработку единой системы достаточно затруднительной. Кроме того, марки электродов не стандартизированы, их деление осуществляется по техническим условиям и паспортам, причем каждый тип электродов может соотноситься как с одной, так и с несколькими марками. Однако электроды можно разделить по наличию тех или иных признаков на группы и подгруппы, что позволит в значительной степени облегчить их применение:
1. По материалу, из которого они изготовлены:
1) металлические, которые подразделяются на:
а) плавящиеся, которые по наличию или отсутствию покрытия бывают:
– покрытыми (стальными, медными, чугунными, бронзовыми, алюминиевыми и др.) (рис. 14);
Рис. 14. Покрытый сварочный электрод: 1 – стержень; 2 – покрытие; 3 – контактный торец, свободный от покрытия
– непокрытыми, которые в настоящее время используются в виде проволоки для проведения сварочных работ в среде защитных газов (по этой причине дальнейший разговор будет вестись исключительно о покрытых электродах);
б) неплавящиеся. К ним относятся вольфрамовые электроды, для облегчения возбуждения сварочной дуги, повышения устойчивости дугового разряда и электропроводности дугового промежутка которых вводятся добавки из оксидов тория (марка ЭВТ), иттрия (ЭВИ-10, ЭВИ-2) или лантана (ЭВЛ-10, ЭВЛ-20). Используются электроды и из чистого вольфрама (ЭВ4). Диаметр вольфрамовых электродов подбирается в зависимости от величины тока и может составлять 0,2-12 мм, а длина – 75, 140, 170 мм.
Вольфрамовые электроды находят применение при дуговой сварке в среде инертных газов, при атомно-водородной или плазменной сварке. Кроме того, они используются для резки и наплавки. Сварку вольфрамовыми электродами ведут от источника переменного тока, электродами с присадками – от источника постоянного и переменного тока прямой и обратной полярности.
Наилучшими сварочными свойствами обладают итерированные электроды, которые позволяют повышать плотность тока и уменьшать расход вольфрама;
2) неметаллические. Они не плавятся в процессе сварки и представлены следующими электродами:
а) угольные, произведенные из электротехнического угля в соответствии с ГОСТом 4425-72. Их диаметр – 5-25 мм, длина – 200–300 мм. В зависимости от того, какой материал предполагается сваривать, конец электрода затачивается под углом 60–70° (для стали) или 20–40° (для цветных металлов);
б) графитовые, изготовленные из синтетического прессованного графита по ГОСТу 4426-71. Их эффективность выше, чем угольных, они отличаются мягкостью, поэтому легко режутся. Поскольку такие электроды имеют высокую электропроводность и повышенную стойкость к окислению на воздухе, возможно увеличение плотности тока примерно в 2,5–3 раза, что дополнительно снижает расход материала.
Угольные и графитовые электроды характеризуются высокой температурой плавления и кипения и низкой теплопроводностью. Качественными считаются те электроды, которые имеют правильную форму, ровную поверхность, не оставляют следов на бумаге и издают металлический звук при ударе. Для повышения стойкости данных видов электродов на них наносят слой меди толщиной 0,06-0,07 мм. Для подведения тока к угольным и графитовым электродам используют электродержатели.
2. По качеству (точности) изготовления, состоянию поверхности покрытия и количеству вредных примесей (серы и фосфора) сварочные электроды делят на три группы, которые обозначаются 1, 2 или 3 (чем больше число, тем выше качество изделия).
3. По назначению сварочные электроды (обозначение указано в скобках) согласно ГОСТу делятся на:
1) предназначенные для сварки:
– легированных теплоустойчивых сталей (Т);
1) обеспечивать:
– устойчивое горение сварочной дуги;
– качественное формирование сварного шва и его прочность;
– равномерное расплавление стержня и покрытия с минимальным разбрызгиванием металла электрода;
– беспрепятственное удаление шлаков;
– высокопроизводительную сварку;
2) давать металл сварного шва необходимого химического состава;
3) сохранять свои физико-химические и технологические свойства на протяжении заданного количества времени;
4) обладать минимальной токсичностью.
Кроме того, имеются специальные технические требования, например:
– получение металла шва с особыми свойствами, к которым относятся окалино– и износостойкость, коррозионная устойчивость, повышенная прочность;
– формирование шва заранее определенной формы (с глубоким проваром, вогнутой поверхностью);
– осуществление сварки конкретным способом (с опиранием вертикальных швов сверху вниз, в любых пространственных положениях).
Разнообразие сварочных электродов и различные принципы, которые могут быть положены в основу их классификации, делают разработку единой системы достаточно затруднительной. Кроме того, марки электродов не стандартизированы, их деление осуществляется по техническим условиям и паспортам, причем каждый тип электродов может соотноситься как с одной, так и с несколькими марками. Однако электроды можно разделить по наличию тех или иных признаков на группы и подгруппы, что позволит в значительной степени облегчить их применение:
1. По материалу, из которого они изготовлены:
1) металлические, которые подразделяются на:
а) плавящиеся, которые по наличию или отсутствию покрытия бывают:
– покрытыми (стальными, медными, чугунными, бронзовыми, алюминиевыми и др.) (рис. 14);

– непокрытыми, которые в настоящее время используются в виде проволоки для проведения сварочных работ в среде защитных газов (по этой причине дальнейший разговор будет вестись исключительно о покрытых электродах);
б) неплавящиеся. К ним относятся вольфрамовые электроды, для облегчения возбуждения сварочной дуги, повышения устойчивости дугового разряда и электропроводности дугового промежутка которых вводятся добавки из оксидов тория (марка ЭВТ), иттрия (ЭВИ-10, ЭВИ-2) или лантана (ЭВЛ-10, ЭВЛ-20). Используются электроды и из чистого вольфрама (ЭВ4). Диаметр вольфрамовых электродов подбирается в зависимости от величины тока и может составлять 0,2-12 мм, а длина – 75, 140, 170 мм.
Вольфрамовые электроды находят применение при дуговой сварке в среде инертных газов, при атомно-водородной или плазменной сварке. Кроме того, они используются для резки и наплавки. Сварку вольфрамовыми электродами ведут от источника переменного тока, электродами с присадками – от источника постоянного и переменного тока прямой и обратной полярности.
Наилучшими сварочными свойствами обладают итерированные электроды, которые позволяют повышать плотность тока и уменьшать расход вольфрама;
2) неметаллические. Они не плавятся в процессе сварки и представлены следующими электродами:
а) угольные, произведенные из электротехнического угля в соответствии с ГОСТом 4425-72. Их диаметр – 5-25 мм, длина – 200–300 мм. В зависимости от того, какой материал предполагается сваривать, конец электрода затачивается под углом 60–70° (для стали) или 20–40° (для цветных металлов);
б) графитовые, изготовленные из синтетического прессованного графита по ГОСТу 4426-71. Их эффективность выше, чем угольных, они отличаются мягкостью, поэтому легко режутся. Поскольку такие электроды имеют высокую электропроводность и повышенную стойкость к окислению на воздухе, возможно увеличение плотности тока примерно в 2,5–3 раза, что дополнительно снижает расход материала.
Угольные и графитовые электроды характеризуются высокой температурой плавления и кипения и низкой теплопроводностью. Качественными считаются те электроды, которые имеют правильную форму, ровную поверхность, не оставляют следов на бумаге и издают металлический звук при ударе. Для повышения стойкости данных видов электродов на них наносят слой меди толщиной 0,06-0,07 мм. Для подведения тока к угольным и графитовым электродам используют электродержатели.
2. По качеству (точности) изготовления, состоянию поверхности покрытия и количеству вредных примесей (серы и фосфора) сварочные электроды делят на три группы, которые обозначаются 1, 2 или 3 (чем больше число, тем выше качество изделия).
3. По назначению сварочные электроды (обозначение указано в скобках) согласно ГОСТу делятся на:
1) предназначенные для сварки:
– легированных теплоустойчивых сталей (Т);
Конец бесплатного ознакомительного фрагмента