Перед сборкой двигателя края постелей блока цилиндров очищают от нагара, а масляные канавки в постелях – от старых отложений, после чего в соответствии с нанесенными при разборке метками вставляют вкладыши коренных подшипников в постели блока цилиндров. При этом стоит помнить, что средний вкладыш в отличие от остальных не имеет проточки. Перед установкой вкладыши смазывают моторным маслом, при сборке следят за тем, чтобы стопорные усики деталей точно вошли в соответствующие пазы постелей. После установки вкладышей переходят к установке коленчатого вала в блок цилиндров.
Упорные полукольца при установке смазывают моторным маслом, не забывая при сборке, что сторона с канавками должна быть повернута к щекам коленчатого вала.
Полукольцо белого цвета из сталеалюминевого сплава устанавливается с передней стороны средней постели, там же, где находится привод распределительного вала, а желтое полукольцо из металлокерамики должно располагаться с другой стороны постели. После сборки нужно повернуть полукольца в такое положение, при котором их концы встали бы заподлицо с торцами постели.
Чтобы не перепутать крышки к цилиндру, при их установке нужно проверить соответствующие насечки на деталях, которые наносятся в соответствии с номером цилиндра. Для того чтобы различить вторую и пятую крышки, на которые наносят одинаковые метки, нужно помнить, что вторая крышка отличается наличием двух резьбовых отверстий под болты крепления маслоприемника. При сборке не забудьте смазать резьбу и торцы головок болтов крепления крышек. Заворачивают болты крышек в определенном порядке: сначала третья крышка, затем вторая, потом четвертая, следующая – первая, последней должна быть пятая.
После затяжки всех креплений проверните несколько раз коленчатый вал: если он ходит легко и не заедает, затяжка проведена правильно.
Чтобы прикрепить прокладку масляного насоса, ее смазывают специальной консистентной смазкой, в результате чего она легко прикрепляется к блоку. После присоединения излишки смазки удаляют. Затем возвращают на место масляный нанос и устанавливают держатель заднего сальника (прокладку держателя можно прикрепить к блоку той же смазкой). Установку шатуна производят в соответствии с метками, сделанными при разборке двигателя, потом вставляют поршневой палец и по обеим сторонам детали закрепляют стопорные кольца, следя за тем, чтобы они четко встали в канавки поршня. Затем надевают на поршень разжимную пружину маслосъемного кольца и при помощи специального съемника производят установку на поршень поршневых колец.
При установке колец нужно соблюдать следующий порядок: сначала надевается маслосъемное кольцо, при его установке замок кольца располагают с обратной замку разжимной пружины стороны, вторым надевают нижнее компрессионное кольцо, а затем устанавливают верхнее. В некоторых случаях на кольцах делают соответствующие надписи, указывающие, какая сторона должна идти вверх.
После сборки кольца нужно развернуть в такое положение, чтобы угол между их замками равнялся 120°.
Перед установкой шатунных шеек коленчатого вала их тщательно прочищают от грязи и смазки.
Зеркала цилиндров перед сборкой нужно очистить от накопившейся грязи и отложений и смазать моторным маслом. Вкладыш шатуна вставляют по нанесенным при разборке меткам, следя за тем, чтобы усик точно совместился с проточкой шатуна. Затем вкладыш и сам поршень смазывают маслом, на поршень надевают оправку, которая сжимает поршневые кольца, и осторожно опускают шатун в цилиндр так, чтобы стрелка на днище поршня была направлена в сторону привода распределительного вала. При проведении установки желательно перевести коленчатый вал в положение НМТ.
Для установки поршня в цилиндр необходимо очень плотно прижать оправку к блоку цилиндров, иначе можно поломать поршневые кольца, и легким давлением ручки молотка протолкнуть поршень в цилиндр. После этого нужно установить на шейку коленчатого вала нижнюю головку шатуна, совместить вкладыш шатуна с его крышкой по нанесенным при разборке меткам, при этом усик вкладыша точно совмещают с проточкой в крышке. Далее необходимо смазать вкладыш моторным маслом и закрыть цилиндр крышкой так, чтобы номера цилиндра на крышке и нижней головке шатуна были расположены с одной стороны. После затяжки крепежных элементов крышки цилиндра таким же образом собирают остальные поршни.
Для установки датчика уровня масла в блок цилиндров коленчатый вал необходимо перевести в такое положение, при котором он не будет мешать установке детали, после чего установить датчик и затянуть крепежный болт. Вслед за установкой маслоприемника приступают к креплению маховика, для чего все крепежные элементы детали обезжиривают и наносят на крепежные болты специальный герметик.
Затем возвращают на место масляный картер и дальнейшую сборку двигателя производят в последовательности, обратной его разборке.
Упорные полукольца при установке смазывают моторным маслом, не забывая при сборке, что сторона с канавками должна быть повернута к щекам коленчатого вала.
Полукольцо белого цвета из сталеалюминевого сплава устанавливается с передней стороны средней постели, там же, где находится привод распределительного вала, а желтое полукольцо из металлокерамики должно располагаться с другой стороны постели. После сборки нужно повернуть полукольца в такое положение, при котором их концы встали бы заподлицо с торцами постели.
Вкладыши крышек коренных подшипников устанавливают по меткам или номерам, которые наносились при их разборке; при сборке нужно внимательно следить за тем, чтобы стопорные усики деталей точно вошли в соответствующие пазы крышек.При установке вкладыши необходимо смазать моторным маслом.
Чтобы не перепутать крышки к цилиндру, при их установке нужно проверить соответствующие насечки на деталях, которые наносятся в соответствии с номером цилиндра. Для того чтобы различить вторую и пятую крышки, на которые наносят одинаковые метки, нужно помнить, что вторая крышка отличается наличием двух резьбовых отверстий под болты крепления маслоприемника. При сборке не забудьте смазать резьбу и торцы головок болтов крепления крышек. Заворачивают болты крышек в определенном порядке: сначала третья крышка, затем вторая, потом четвертая, следующая – первая, последней должна быть пятая.
После затяжки всех креплений проверните несколько раз коленчатый вал: если он ходит легко и не заедает, затяжка проведена правильно.
Чтобы прикрепить прокладку масляного насоса, ее смазывают специальной консистентной смазкой, в результате чего она легко прикрепляется к блоку. После присоединения излишки смазки удаляют. Затем возвращают на место масляный нанос и устанавливают держатель заднего сальника (прокладку держателя можно прикрепить к блоку той же смазкой). Установку шатуна производят в соответствии с метками, сделанными при разборке двигателя, потом вставляют поршневой палец и по обеим сторонам детали закрепляют стопорные кольца, следя за тем, чтобы они четко встали в канавки поршня. Затем надевают на поршень разжимную пружину маслосъемного кольца и при помощи специального съемника производят установку на поршень поршневых колец.
При установке колец нужно соблюдать следующий порядок: сначала надевается маслосъемное кольцо, при его установке замок кольца располагают с обратной замку разжимной пружины стороны, вторым надевают нижнее компрессионное кольцо, а затем устанавливают верхнее. В некоторых случаях на кольцах делают соответствующие надписи, указывающие, какая сторона должна идти вверх.
В том случае, если специального съемника нет, нужно постараться очень осторожно развести замки колец руками и установить детали на поршень.Нижнее компрессионное кольцо от верхнего отличается как по толщине, так и по направлению проточки, которая в этом случае идет вниз. После установки кольца вращают, чтобы проверить легкость хода. Если кольца деформированы и заедают при вращении, их заменяют новыми.
После сборки кольца нужно развернуть в такое положение, чтобы угол между их замками равнялся 120°.
Перед установкой шатунных шеек коленчатого вала их тщательно прочищают от грязи и смазки.
Зеркала цилиндров перед сборкой нужно очистить от накопившейся грязи и отложений и смазать моторным маслом. Вкладыш шатуна вставляют по нанесенным при разборке меткам, следя за тем, чтобы усик точно совместился с проточкой шатуна. Затем вкладыш и сам поршень смазывают маслом, на поршень надевают оправку, которая сжимает поршневые кольца, и осторожно опускают шатун в цилиндр так, чтобы стрелка на днище поршня была направлена в сторону привода распределительного вала. При проведении установки желательно перевести коленчатый вал в положение НМТ.
Для установки поршня в цилиндр необходимо очень плотно прижать оправку к блоку цилиндров, иначе можно поломать поршневые кольца, и легким давлением ручки молотка протолкнуть поршень в цилиндр. После этого нужно установить на шейку коленчатого вала нижнюю головку шатуна, совместить вкладыш шатуна с его крышкой по нанесенным при разборке меткам, при этом усик вкладыша точно совмещают с проточкой в крышке. Далее необходимо смазать вкладыш моторным маслом и закрыть цилиндр крышкой так, чтобы номера цилиндра на крышке и нижней головке шатуна были расположены с одной стороны. После затяжки крепежных элементов крышки цилиндра таким же образом собирают остальные поршни.
Для установки датчика уровня масла в блок цилиндров коленчатый вал необходимо перевести в такое положение, при котором он не будет мешать установке детали, после чего установить датчик и затянуть крепежный болт. Вслед за установкой маслоприемника приступают к креплению маховика, для чего все крепежные элементы детали обезжиривают и наносят на крепежные болты специальный герметик.
Затем возвращают на место масляный картер и дальнейшую сборку двигателя производят в последовательности, обратной его разборке.
Рекомендации по работе с двигателем
В том случае, если по некоторым причинам проворачивание коленчатого вала за болт крепления к нему шкива затруднительно или неудобно производить, можно использовать иные способы. Например, можно включить четвертую передачу и на медленной скорости прокатить автомобиль, пока метки на шкиве распределительного вала полностью не совпадут с меткой на задней крышке ремня привода распределительного вала. В том случае, если у вас есть возможность вывесить автомобиль на переднее колесо, можно использовать другой способ: включить любую передачу и начать поворачивать вывешенное колесо, пока метки на шкиве распределительного вала не совпадут с меткой на задней крышке ремня привода распределительного вала.
При проведении ремонтных работ по замене ремня привода распределительного вала, а также при необходимости его снятия поршень первого цилиндра всегда нужно переводить в верхнюю мертвую точку такта сжатия: в этом случае установка фаз газораспределения не будет нарушаться и после сборки двигателя система будет работать исправно.
Диагностика двигателя
Средний ресурс агрегатов и деталей двигателя
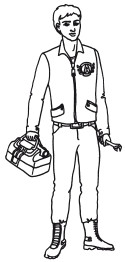
Такие цифры уместны только в том случае, когда в ходе эксплуатации автомобиля его владелец соблюдал все необходимые правила и проводил мероприятия по уходу за авто.
Износ некоторых двигателей может происходить уже при пробеге в 40—60 тыс. км, если машина эксплуатировалась при несоблюдении нужных мер текущего профилактического осмотра и ремонта.
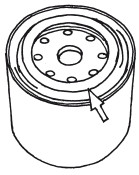
Рисунок 17. Масляный фильтр
После капитального ремонта двигателя при использовании некачественных комплектующих пробег может не выйти и за рамки его обкатки – до 3 тыс. км. На более долгую службу двигателя влияет и использование качественного масла, и его своевременная замена (рис. 17), а также использование дополнительных присадок.
Для того чтобы двигатель служил долго, необходимо соблюдать следующие правила:
✓ применять только качественное машинное масло;
✓ своевременно заменять масло и масляный фильтр – это значительно увеличивает пробег двигателя;
✓ при использовании недорогого моторного масла следует приобретать качественные противоизносные присадки, которые действительно увеличивают срок службы двигателя;
✓ лучше всего приобретать качественные комплектующие цилиндро-поршневой группы.
Причины быстрого износа основных деталей двигателя
Иногда, приобретая подержанный автомобиль, его владелец не знает, какие детали были заменены, а каким требуется текущий ремонт. Зная средний ресурс основных деталей двигателя, можно вовремя произвести ремонт, тем самым оградив себя от нежелательных поломок в пути и существенных материальных затрат на капитальный ремонт.
Знание ресурса основных деталей двигателя значительно облегчит жизнь владельцу и новенького авто, так как можно будет своевременно проводить замену или ремонт комплектующих двигателя.
Поршневые кольца
Поршневые кольца (рис. 18) определяют пробег двигателя между капитальными ремонтами. Больше всего износ наблюдается у маслосъемных колец, несмотря на то что они мало подвержены воздействиям температуры и имеют достаточную смазку. Износ маслосъемных колец происходит из-за малой площади соприкосновения с цилиндром, а пружинно-радиальные расширители дополнительно усиливают давление маслосъемных колец на цилиндр по сравнению с компрессионными.
Поэтому по причине повышенного расхода масла двигатель попадает в ремонт чаще, чем при плохих тяговых характеристиках. Внешне износ маслосъемных колец проявляется как увеличенный зазор в их замках (рис. 19).
Рисунок 18. Поршневые кольца
Если изначально в среднем зазор составляет от 0,2 мм до 0,45 мм, то ко времени капитального ремонта он уже достигает 3—3,5 мм и даже больше. Из-за неравномерного давления колец на стенки цилиндров происходит истирание металла по его радиальной толщине и ее противоположной части.
Рисунок 19. Проверка зазора
Износ маслосъемного кольца по высоте происходит незначительно.
Из-за некачественного моторного масла, его несвоевременной замены или неисправностей в системе очистки воздуха происходит повышенный износ колец. Ресурс поршневых колец в среднем находится в пределах пробега отечественного автомобиля от 80 до 150 тыс. км.
Поэтому по причине повышенного расхода масла двигатель попадает в ремонт чаще, чем при плохих тяговых характеристиках. Внешне износ маслосъемных колец проявляется как увеличенный зазор в их замках (рис. 19).
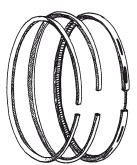
Рисунок 18. Поршневые кольца
Если изначально в среднем зазор составляет от 0,2 мм до 0,45 мм, то ко времени капитального ремонта он уже достигает 3—3,5 мм и даже больше. Из-за неравномерного давления колец на стенки цилиндров происходит истирание металла по его радиальной толщине и ее противоположной части.
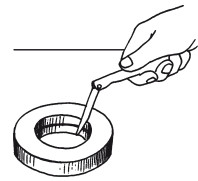
Рисунок 19. Проверка зазора
Износ маслосъемного кольца по высоте происходит незначительно.
Из-за некачественного моторного масла, его несвоевременной замены или неисправностей в системе очистки воздуха происходит повышенный износ колец. Ресурс поршневых колец в среднем находится в пределах пробега отечественного автомобиля от 80 до 150 тыс. км.
Шатуны
На автомобилях «Жигули» (ВАЗ) шатуны не имеют подшипников в верхней части, поэтому их хватает на все время эксплуатации.
Шатуны при ремонте обновляются полной их заменой, если в верхней головке есть втулка (рис. 20).
Рисунок 20. Шатун
Втулка обычно меняется в том случае, если происходит замена поршневого пальца при капитальном ремонте двигателя, а в штатной ситуации служит достаточно долго.
Шатуны при ремонте обновляются полной их заменой, если в верхней головке есть втулка (рис. 20).
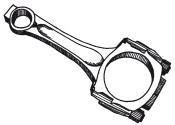
Рисунок 20. Шатун
Втулка обычно меняется в том случае, если происходит замена поршневого пальца при капитальном ремонте двигателя, а в штатной ситуации служит достаточно долго.
Поршни
Ресурс поршней в отечественных автомобилях составляет в среднем от 200 до 250 тыс. км пробега двигателя.
Износ поршня можно проверить в трех местах:
✓ отверстие под поршневой палец. Предельный зазор во время эксплуатации в среднем составляет около 0,05 мм;
✓ проточки под поршневые кольца. В основном износ затрагивает проточку под верхнее компрессионное кольцо из-за наибольшей нагрузки на него. Износ определяется по зазору, достигающему допустимых размеров в 0,15 мм при среднем пробеге двигателя от 220 до 250 тыс. км;
✓ юбка поршня. Износ определяется в сопряжении цилиндр – юбка. В этом случае наиболее допустимый зазор составляет 0,15 мм, который возникает при среднем пробеге двигателя от 200 до 220 тыс. км.
Износ поршня можно проверить в трех местах:
✓ отверстие под поршневой палец. Предельный зазор во время эксплуатации в среднем составляет около 0,05 мм;
✓ проточки под поршневые кольца. В основном износ затрагивает проточку под верхнее компрессионное кольцо из-за наибольшей нагрузки на него. Износ определяется по зазору, достигающему допустимых размеров в 0,15 мм при среднем пробеге двигателя от 220 до 250 тыс. км;
✓ юбка поршня. Износ определяется в сопряжении цилиндр – юбка. В этом случае наиболее допустимый зазор составляет 0,15 мм, который возникает при среднем пробеге двигателя от 200 до 220 тыс. км.
Блок цилиндров
Износ блока цилиндров происходит в основном в верхней части цилиндров. Размер износа определяется по величине эллипса в области верхней мертвой точки верхнего поршневого кольца и по зазору между поршнем и юбкой. При диаметре поршней от 76 до 79 мм эллипсность должна составлять не более 0,14 мм. Ресурс поверхности цилиндров определяется возможностью работы в нем поршневых колец и вырабатывается при пробеге в среднем от 200 до 230 тыс. км.
Коленчатый вал
Износ коленчатого вала в первую очередь наблюдается в области шатунных шеек, так как именно здесь он испытывает наибольшую нагрузку под воздействием возвратно-поступательных движений механизмов цилиндро-поршневой группы.
В процессе длительной работы шейки коленчатого вала (рис. 21) в сечении обретают форму эллипса, допустимый износ которого по своей величине в среднем составляет 0,03 мм.
Рисунок 21. Коленчатый вал
Коренные и шатунные шейки перешлифовывают на ремонтные размеры, при этом происходит уменьшение начального размера на 0,25, 0,5, 0,7 и 1 мм. До ремонтного шлифования средний ресурс коленчатого вала вырабатывается при пробеге от 200 до 250 тыс. км. Ресурс снижается в результате шлифовки шеек, а после шлифовки на 1 мм коленчатый вал будет годен к эксплуатации в среднем еще на 100 тыс. км пробега. Также есть возможность полностью восстановить изношенные шейки при помощи наплавки, а затем шлифовки под начальный размер. Этот метод довольно сложен и требует предельной осторожности, а также специальных технологических условий. Коленчатый вал подвергается износу при контакте с упорными полукольцами, которые ограничивают его осевой люфт. Увеличенный зазор в этом случае можно легко устранить с помощью ремонтных полуколец. При пробеге двигателя менее 200—250 тыс. км достаточно заменить полукольца новыми номинального размера.
В процессе длительной работы шейки коленчатого вала (рис. 21) в сечении обретают форму эллипса, допустимый износ которого по своей величине в среднем составляет 0,03 мм.
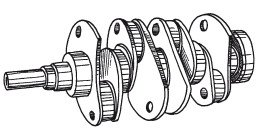
Рисунок 21. Коленчатый вал
Коренные и шатунные шейки перешлифовывают на ремонтные размеры, при этом происходит уменьшение начального размера на 0,25, 0,5, 0,7 и 1 мм. До ремонтного шлифования средний ресурс коленчатого вала вырабатывается при пробеге от 200 до 250 тыс. км. Ресурс снижается в результате шлифовки шеек, а после шлифовки на 1 мм коленчатый вал будет годен к эксплуатации в среднем еще на 100 тыс. км пробега. Также есть возможность полностью восстановить изношенные шейки при помощи наплавки, а затем шлифовки под начальный размер. Этот метод довольно сложен и требует предельной осторожности, а также специальных технологических условий. Коленчатый вал подвергается износу при контакте с упорными полукольцами, которые ограничивают его осевой люфт. Увеличенный зазор в этом случае можно легко устранить с помощью ремонтных полуколец. При пробеге двигателя менее 200—250 тыс. км достаточно заменить полукольца новыми номинального размера.
Вкладыши коленчатого вала
Ресурс вкладышей коленчатого вала значительно больше ресурса шеек коленчатого вала, хотя они имеют меньшую твердость.
Причиной износа вкладышей становится то, что их мягкий рабочий слой накапливает твердые частицы (они образуются в процессе износа механизмов самого двигателя), которые и заносятся в зазор загрязненным маслом, вследствие чего царапают поверхность шеек.Меняют вкладыши, определяя состояние зазора в сопряжении вкладыш – шейка. Сначала следует определить размер деталей, так как наибольший зазор для шатунных подшипников должен составлять 0,1 мм, а для коренных – 0,15 мм. Но предпочтительнее менять вкладыши коленчатого вала при каждом капитальном ремонте цилиндро-поршневой группы.
Маховик двигателя
Износ маховика двигателя (рис. 22) изначально проявляется на его зубчатом венце, ресурс которого, как правило, заканчивается после пробега в 220 тыс. км.
Зубчатый венец является съемной деталью и на износ самого маховика не влияет. Контактную с диском сцепления поверхность протачивают на токарном станке, устраняя при этом ее износ. Практически маховик служит столько же, сколько и сам двигатель.
Рисунок 22. Маховик
Зубчатый венец является съемной деталью и на износ самого маховика не влияет. Контактную с диском сцепления поверхность протачивают на токарном станке, устраняя при этом ее износ. Практически маховик служит столько же, сколько и сам двигатель.
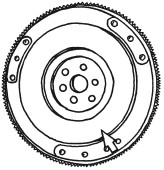
Рисунок 22. Маховик
Распределительный вал
В первую очередь износу подвергаются кулачки распределительного вала, после чего – шейки, а в последнюю очередь изнашиваются корпуса подшипников, в которых вращается распределительный вал. Его пробег в среднем составляет от 80 до 90 тыс. км. Так как замена корпуса вала и рычагов привода клапанов проводится в комплекте, то срок их замены можно определить по ресурсу распределительного вала.
Поскольку его довольно непросто подобрать по размерам, то заодно производят и замену корпусов подшипников.
Детали привода распределительного вала меняются в комплекте и в среднем вырабатываются при пробеге от 80 до 120 тыс. км. Не учитывая остаточный ресурс колец, осуществляют замену успокоителя цепи и башмака натяжителя. Если привод вала осуществляет зубчатый ремень, то его замену производят профилактически вместе с натяжным роликом в среднем после пробега в 60 тыс. км или по рекомендации завода-изготовителя.
Сроки замены ремня ГРМ следует сократить, если его приводные шестерни уже изношены, в противном случае при обрыве ремня во время движения автомобиля (что порой происходит на некоторых автомобилях) клапаны и поршни обязательно ударятся друг о друга, вследствие чего заклинит двигатель.
Поскольку его довольно непросто подобрать по размерам, то заодно производят и замену корпусов подшипников.
Детали привода распределительного вала меняются в комплекте и в среднем вырабатываются при пробеге от 80 до 120 тыс. км. Не учитывая остаточный ресурс колец, осуществляют замену успокоителя цепи и башмака натяжителя. Если привод вала осуществляет зубчатый ремень, то его замену производят профилактически вместе с натяжным роликом в среднем после пробега в 60 тыс. км или по рекомендации завода-изготовителя.
Сроки замены ремня ГРМ следует сократить, если его приводные шестерни уже изношены, в противном случае при обрыве ремня во время движения автомобиля (что порой происходит на некоторых автомобилях) клапаны и поршни обязательно ударятся друг о друга, вследствие чего заклинит двигатель.
Головка блока цилиндров
Ресурс головки блока цилиндров совпадает с ресурсом блока всего двигателя, но при условии, что в процессе эксплуатации он не перегревался. К заменяемым деталям относятся направляющие втулки стержней клапанов и их седла. Ресурс направляющих втулок практически совпадает с ресурсом стержней клапанов и в среднем составляет около 250 тыс. км пробега.
Седло клапана практически сохраняется при пробеге до 150 тыс. км, поэтому во время замены комплекта поршневых колец следует произвести профилактическую притирку этих сопряжений. Ресурс седел клапанов обычно рассчитан на весь срок службы двигателя при условии, что при каждой замене клапанов и втулок будет проводиться обработка контактных поверхностей специальными шарошками. Не рекомендуется обрабатывать контактные поверхности абразивной пастой, так как в результате происходит значительная потеря металла на седлах и клапанах. Замена пружин клапанов не производится, так как их ресурс рассчитан на весь срок эксплуатации двигателя.
Седло клапана практически сохраняется при пробеге до 150 тыс. км, поэтому во время замены комплекта поршневых колец следует произвести профилактическую притирку этих сопряжений. Ресурс седел клапанов обычно рассчитан на весь срок службы двигателя при условии, что при каждой замене клапанов и втулок будет проводиться обработка контактных поверхностей специальными шарошками. Не рекомендуется обрабатывать контактные поверхности абразивной пастой, так как в результате происходит значительная потеря металла на седлах и клапанах. Замена пружин клапанов не производится, так как их ресурс рассчитан на весь срок эксплуатации двигателя.
Масляный насос
Ресурс масляного насоса зависит от качества его фильтрующего элемента и моторного масла. Масляный насос подлежит ремонту, его восстановление производится заменой приводной оси и рабочих шестерен. Ресурс шестерни привода масляного насоса обычно рассчитан на 100 тыс. км пробега.
Износ внутренних зубцов шестерни является причиной отказа привода масляного насоса, вследствие чего происходит сбой в работе системы смазки и распределителя системы зажигания.
Износ внутренних зубцов шестерни является причиной отказа привода масляного насоса, вследствие чего происходит сбой в работе системы смазки и распределителя системы зажигания.
Промежуточный валик
Ресурс промежуточного валика составляет в среднем от 200 до 250 тыс. км пробега, после чего его опорные шейки следует перешлифовать с уменьшением в диаметре на 0,3 мм. Лучше всего ремонтировать «родной» валик, так как он проверен в работе двигателя, а не заменять его новым.
Масляный насос лучше всего менять в комплекте, так как поставляемые для него запасные части не всегда имеют хорошее качество.
Помпа системы охлаждения
Долговечность помпы системы охлаждения зависит от ресурса ее подшипникового узла, она рассчитана обычно на пробег около 200 тыс. км. Возможный ремонт значительно облегчается тем, что подшипниковая передняя часть помпы и крыльчатка поставляются в сборе запасных частей.
Для обеспечения более длительного срока службы помпы системы охлаждения нужно точно и правильно выставить зазор между корпусом и крыльчаткой путем подбора толщины прокладки.
Прокладка двигателя
Прокладка двигателя заменяется при первой же его разборке.
В дорожных условиях ее можно дополнительно покрыть слоем герметика и обезжирить. При демонтаже головки блока цилиндров прокладка меняется обязательно вне зависимости от пробега.
В дорожных условиях ее можно дополнительно покрыть слоем герметика и обезжирить. При демонтаже головки блока цилиндров прокладка меняется обязательно вне зависимости от пробега.
Сальники клапанов
Еще до капитального ремонта двигателя приходят в негодность сальники клапанов, так как они подвергаются сильному истиранию и температурному воздействию.
Ресурс сальников клапанов зависит от фирмы-изготовителя и качества материала и рассчитан на пробег от 20 до 100 тыс. км. Некачественные сальники прослужат не более 10 тыс. км пробега.
Любые, даже самые качественные сальники клапанов может вывести из строя возникший хотя бы раз перегрев головки блока цилиндров.
Ресурс сальников клапанов зависит от фирмы-изготовителя и качества материала и рассчитан на пробег от 20 до 100 тыс. км. Некачественные сальники прослужат не более 10 тыс. км пробега.
Любые, даже самые качественные сальники клапанов может вывести из строя возникший хотя бы раз перегрев головки блока цилиндров.
Сальники двигателя
Даже несмотря на хороший внешний вид, при капитальном ремонте всегда необходимо менять и сальники двигателя. Существенных затрат сил и средств потребует замена заднего сальника коленчатого вала. Ресурс сальников рассчитан на пробег примерно от 100 до 150 тыс. км, а при выходе из строя одного из них следует заменять и все остальные.
Генератор
Ресурс генератора в среднем составляет 120– 300 тыс. км пробега и зависит от качества его подшипников. Перед заменой подшипников в процессе эксплуатации производят замену щеток, ресурс которых не влияет на ресурс самого генератора. Если было несколько смен комплектов подшипников, то тогда нужно протачивать или заменять контактные кольца ротора.
Стартер
Ресурс стартера (рис. 23) напрямую зависит от состояния аккумулятора и двигателя автомобиля, поэтому может быть разным на машинах с одинаковым пробегом.
Из строя первой выходит обычно обгонная муфта, или бендикс, срок службы которой составляет в среднем 80 тыс. км пробега. Срок службы втулки ротора
также составляет около 80 тыс. км, но первой обычно выходит из строя наиболее перегруженная втулка передней части. Но замену всей втулки производят в комплекте.
На весь срок службы двигателя хватает ресурса контактных ламелей ротора, но при своевременном обслуживании, а именно: очистке и выравнивании поверхности.
Рисунок 23. Стартер
Из строя первой выходит обычно обгонная муфта, или бендикс, срок службы которой составляет в среднем 80 тыс. км пробега. Срок службы втулки ротора
также составляет около 80 тыс. км, но первой обычно выходит из строя наиболее перегруженная втулка передней части. Но замену всей втулки производят в комплекте.
На весь срок службы двигателя хватает ресурса контактных ламелей ротора, но при своевременном обслуживании, а именно: очистке и выравнивании поверхности.
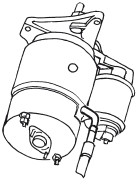
Рисунок 23. Стартер
Топливный насос
Срок службы механического насоса зависит от состояния его мембран и рассчитан в среднем на 150 тыс. км пробега. Работоспособность клапанного механизма в среднем составляет 250 тыс. км пробега.
Рисунок 24. Топливный насос
Срок службы топливного насоса (рис. 24) впрыскового двигателя зависит от качества топлива и от степени его загрязненности.
Топливный насос может быть выведен из строя безвозвратно в процессе эксплуатации впрыскового двигателя автомобиля при пустом бензобаке.
В этом случае при попытке завести двигатель «на пустой бак» происходит перегрев топливного насоса. К выходу его из строя также приводит сетка топливо-заборника, если она забита грязью.
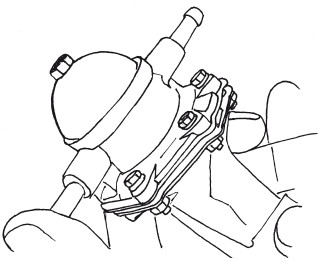
Рисунок 24. Топливный насос
Срок службы топливного насоса (рис. 24) впрыскового двигателя зависит от качества топлива и от степени его загрязненности.
Топливный насос может быть выведен из строя безвозвратно в процессе эксплуатации впрыскового двигателя автомобиля при пустом бензобаке.
В этом случае при попытке завести двигатель «на пустой бак» происходит перегрев топливного насоса. К выходу его из строя также приводит сетка топливо-заборника, если она забита грязью.
Трамблер, или распределитель зажигания
В трамблере (рис. 25) в негодность в первую очередь приходит контактная группа, затем – подшипник опорной пластины, после чего, как правило, проявляются неисправности изоляции высоковольтных частей – бегунка и крышки.
Рисунок 25. Распределитель зажигания
Затем появляется лишний зазор во втулках и заканчивается все приведением в негодность механизмов опережения зажигания.
Срок службы трамблера составляет в среднем от 100 до 120 тыс. км пробега, и его неисправности, как правило, автолюбителей не тревожат. Но отремонтированный трамблер служит недолго, а при обращении в спецсервис ремонт будет стоить как совершенно новый узел, поэтому лучше всего заменить его новым трамблером в полном сборе.
Трамблер обычно подвержен износу по ряду причин:
✓ износ центробежного регулятора;
✓ прогорание изоляции высоковольтных частей;
✓ нарушение сопряжения втулка – валик привода;
✓ подгорание контактной группы (при ее наличии);
✓ износ подшипника подвижной пластины.
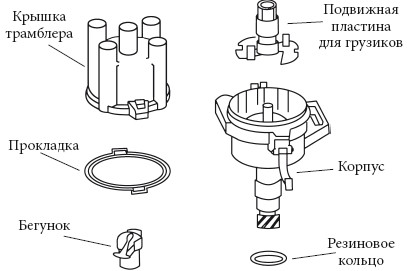
Рисунок 25. Распределитель зажигания
Затем появляется лишний зазор во втулках и заканчивается все приведением в негодность механизмов опережения зажигания.
Срок службы трамблера составляет в среднем от 100 до 120 тыс. км пробега, и его неисправности, как правило, автолюбителей не тревожат. Но отремонтированный трамблер служит недолго, а при обращении в спецсервис ремонт будет стоить как совершенно новый узел, поэтому лучше всего заменить его новым трамблером в полном сборе.
Трамблер обычно подвержен износу по ряду причин:
✓ износ центробежного регулятора;
✓ прогорание изоляции высоковольтных частей;
✓ нарушение сопряжения втулка – валик привода;
✓ подгорание контактной группы (при ее наличии);
✓ износ подшипника подвижной пластины.
Карбюратор
Срок службы карбюратора в основном значительный. Первыми выходят из строя как в отечественных, так и в импортных автомобилях мембраны пускового устройства. Их ресурс составляет в основном от 100 до 150 тыс. км пробега.
Ресурс диафрагмы ускорительного насоса в два раза больше. На весь срок службы карбюратора хватает ресурса диафрагмы привода вторичной камеры (там, где она присутствует).
Ресурс диафрагмы ускорительного насоса в два раза больше. На весь срок службы карбюратора хватает ресурса диафрагмы привода вторичной камеры (там, где она присутствует).
Датчики двигателя
Особых хлопот во время эксплуатации не доставляют датчики двигателя, так как они достаточно долговечны. Единственное исключение составляет датчик системы охлаждения на отечественных автомобилях. Срок его службы трудно предположить из-за нестабильности качества изготовления.
Диагностика без разборки двигателя
Для серьезного ремонта двигателя автомобиля необходимо правильно провести его диагностику, желательно без радикальной разборки.
Диагностику механизмов двигателя без его разборки можно провести следующими способами:
✓ с помощью приборов;
✓ методом анализа акустических шумов;
✓ по состоянию выхлопа;
✓ по состоянию свечей зажигания.
Более точный результат можно получить при применении одновременно всех перечисленных методов с сопоставлением полученных результатов.
Диагностику механизмов двигателя без его разборки можно провести следующими способами:
✓ с помощью приборов;
✓ методом анализа акустических шумов;
✓ по состоянию выхлопа;
✓ по состоянию свечей зажигания.
Более точный результат можно получить при применении одновременно всех перечисленных методов с сопоставлением полученных результатов.
Диагностика двигателя с помощью приборов
При приборном методе диагностики применяются измерительные приборы: компрессор для измерения компрессии и манометр для измерения давления в масляной магистрали. Масляной манометр поможет оценить общее состояние шатунных коренных шеек коленчатого вала, масляного насоса и всех сопряжений, в которые при работе двигателя поступает под давлением масло. Путем прямого введения наконечника манометра, который имеет резьбу, в масляную магистраль проводится замер. Нужный прибор можно сделать самостоятельно. Он состоит из масляного манометра, имеющего шкалу с делениями 1,0—1,5 МПа или 10– 15 кгс/см2, шланга из резины высокого давления и штуцера с резьбой, подходящей к штатному датчику давления в автомобиле. Перед тем как собрать прибор, необходимо проверить точность показаний масляного манометра, для чего следует снять показания в масляной магистрали сначала проверенным или контрольным масляным манометром, а затем сравнить с показаниями самодельного прибора. При этом жидкость следует подавать под разным давлением и сравнивать показания приборов в различных точках шкалы, для того чтобы проверить отсутствие или наличие нелинейности шкалы.
Конец бесплатного ознакомительного фрагмента