Глава 6
ОПЕРАТИВНОЕ ПЛАНИРОВАНИЕ
Мы знаем – время растяжимо: Оно зависит от того, Какого рода содержимым Вы наполняете его.
С. Маршак
Каталог проблем
1. Нестабильность плановых производственных графиков.
2. Не выделены факторы, обеспечивающие устойчивость производственных графиков.
3. Неритмичность поступления ресурсов и материалов.
4. Низок уровень страховых запасов полуфабрикатов.
5. Значителен объем излишних запасов материалов.
6. Частая смена номенклатуры выпускаемой продукции.
7. Дефицит времени на участках подготовки производства.
8. Замедленная реакция системы управления на производственные изменения.
9. Поступление информации с большим опозданием.
10. Недостаточная информированность управленческого персонала первичных звеньев о перспективных задачах.
11. Отсутствие математических моделей принятия решений.
12. Отсутствие автоматизированной системы оперативного информационного обеспечения.
13. Отсутствие комплексного анализа оперативной учетной информации.
14. Многовариантная номенклатурность обеспечивающих производств.
15. Несбалансированность производственных мощностей участков.
16. Отсутствие организационных процедур саморегулирования.
17. Неразвитая исполнительская дисциплина управленческого персонала.
18. Для повышения квалификации управленческого персонала не используются деловые игры.
19. Не выделены экономические оценки для задач оперативного планирования.
20. Не выделены признаки идентификации производственных ситуаций.
21. Наличие неадекватного восприятия управленческим персоналом сущности производственных ситуаций.
22. Отсутствие научного обоснования применяемых горизонтов оперативного планирования.
2. Не выделены факторы, обеспечивающие устойчивость производственных графиков.
3. Неритмичность поступления ресурсов и материалов.
4. Низок уровень страховых запасов полуфабрикатов.
5. Значителен объем излишних запасов материалов.
6. Частая смена номенклатуры выпускаемой продукции.
7. Дефицит времени на участках подготовки производства.
8. Замедленная реакция системы управления на производственные изменения.
9. Поступление информации с большим опозданием.
10. Недостаточная информированность управленческого персонала первичных звеньев о перспективных задачах.
11. Отсутствие математических моделей принятия решений.
12. Отсутствие автоматизированной системы оперативного информационного обеспечения.
13. Отсутствие комплексного анализа оперативной учетной информации.
14. Многовариантная номенклатурность обеспечивающих производств.
15. Несбалансированность производственных мощностей участков.
16. Отсутствие организационных процедур саморегулирования.
17. Неразвитая исполнительская дисциплина управленческого персонала.
18. Для повышения квалификации управленческого персонала не используются деловые игры.
19. Не выделены экономические оценки для задач оперативного планирования.
20. Не выделены признаки идентификации производственных ситуаций.
21. Наличие неадекватного восприятия управленческим персоналом сущности производственных ситуаций.
22. Отсутствие научного обоснования применяемых горизонтов оперативного планирования.
6.1. Классификация элементов производственного процесса
Избегайте muri, muda, mura – излишков, потерь, неравномерности.
Японская пословица
Оперативное управление – комплекс организационных и технических мероприятий, обеспечивающих выбор места и времени выполнения работ. Оперативное управление включает процесс принятия решений, разработку производственных графиков, учет деятельности и ее регулирование.
Классификация производственного процесса включает следующие элементы:
• передел (производство);
• цех;
• отделение (пролет);
• участок (стадия, ступень);
• элемент;
• движение.
Александр Александрович Богданов (1873–1928) – экономист, философ, естествоиспытатель. Основатель и директор первого в мире Института переливания крови. Погиб при проведении на себе научного опыта. А. А. Богданов разработал основы всеобщей организационной науки, высказал идею о необходимости системного подхода, дал характеристику системы и ее элементов. Считая организацию сущностью живой и неживой природы, в своей теории любую деятельность он в итоге сводил к организационной. «Человек не выдумывает своих организационных методов; они имеют основу в организационных закономерностях природы и являются для человека так или иначе вынужденными. Это – основное положение». По мнению ученого, «у человечества нет иной деятельности, кроме организационной, нет иных задач, иных точек зрения на жизнь и мир, кроме организационных». А. А. Богданов осуществил попытку построения на основе сочетания различных типов и ступеней организованности единой концепции Вселенной.
Передел – это группа цехов с однотипным характером производственного процесса.
Цех – основное подразделение предприятия, выполняющее часть производственного процесса.
Участок – основное производственное подразделение цеха.
Элемент – это часть производственной операции, выполняемой при одном рабочем режиме и составе используемых агрегатов.
Совокупность цехов и обеспечивающих хозяйств предприятия называется его производственной структурой. Если они представлены в графическом виде с отображением реального расположения на местности, такой чертеж называется генеральным планом предприятия.
Типовыми способами организации производства являются:
• обработка единицами (в потоке или на конвейере);
• обработка партиями (в потоке или на конвейере);
• организация производства на универсальных рабочих местах;
• совмещение процессов обработки и движения деталей (роторные линии).
Тип производства – это комплексная характеристика технических, организационных и экономических особенностей производства, обусловленная его специализацией, объемом и постоянством номенклатуры изделий, а также формой движения изделий по рабочим местам. При описании организации производства используют понятия детали, сборочной единицы, комплекса или комплекта, партии. Деталь – это предмет, который не может быть разделен на части без его разрушения. Сборочная единица (узел) – разъемное или неразъемное соединение нескольких деталей. Комплекс или комплект – соединение нескольких сборочных единиц и деталей. Партия – количество одинаковых предметов, обрабатываемых или собираемых на операции непрерывно.
В зависимости от размера партии выделяют пять видов организации производства: индивидуальное, порционное, мелкосерийное, серийное, массовое.
При изучении производственных операций выделяют следующие их виды: простые и сложные, с перекрытием времени выполнения последовательных операций и без перекрытия, с опережением времени выполнения последовательных операций и без опережения, циклические и нециклические процессы, с параллельной и индивидуальной обработкой на операциях.
Если группа деталей обрабатывается партией на рабочих местах, то процесс называется последовательным движением. При самостоятельном перемещении отдельных деталей процесс называется параллельным движением.
Для математического описания производственных процессов используют следующие параметры:
• ритм обработки – интервал времени между последовательными изделиями;
• время обработки – общее время обработки изделия по всему производственному циклу;
• производительность процесса – количество изделий, выпускаемое за плановый интервал времени, поделенный на ритм обработки;
• пауза на операции – время между окончанием обработки предшествующего и началом обработки последующего изделия;
• машинное время на операции – время занятости оборудования при обработке изделия на операции.
При циклическом производственном процессе сумма паузы и машинного времени является постоянной величиной по операциям.
В составе времени выполнения отдельной операции выделяют: подготовительно-заключительное время (профилактика, перестройка оборудования); основное время (время выполнения производственной операции); вспомогательное время (отбор проб, контрольные замеры); время обслуживания оборудования (смазка, уборка); перерывы в работе. Перерывы дополнительно разделяют на регламентированный отдых, непроизводительные простои оборудования по организационным или технологическим причинам.
Для организации производства выработаны следующие правила:
1. Организация включает три ряда – организацию техники, людей и идей.
2. Чем меньше взаимодействие, тем оно интенсивнее.
3. Чем меньше расстояние между системами, тем сильнее их взаимодействие.
4. Организационное целое превосходит простую сумму его частей.
5. Однонаправленность и непересекаемость потоков упрощают взаимодействие систем.
6. Чем меньше элементов в системе, тем выше ее надежность.
7. Прочность цепи определяется наиболее слабым ее звеном.
8. Повторяющиеся процессы регулируют одинаково.
9. Совершенствование организации производства ориентируется на замещение квалифицированного труда на менее квалифицированный или машинную обработку. 10. Все урегулирования нацелены на сохранение и развитие факторов успеха и сильных сторон деятельности.
Рационализация рабочих движений играет важную роль при анализе действий рабочих на конвейере, на операциях с большой долей ручного труда.
Необходимо дать следующие основные рекомендации для совершения эффективных трудовых движений (данные принципы сформулированы Ф. Гильбертом):
• движения должны реализовываться в пределах нормативной рабочей зоны;
• траектория движений должна быть плавной;
• перемещать предметы необходимо без излишнего подъема;
• загружать требуется обе руки;
• одинаковые движения целесообразно совмещать;
• холостые движения следует исключить;
• размещать используемые предметы (инструмент) следует с учетом частоты их использования;
• руки следует освобождать от длительных операций поддерживания.
Движения должны быть естественными, ритмичными, симметричными и одновременными.
6.2. Методы представления календарных графиков
У человечества нет иной деятельности, кроме организационной, нет иных задач, иных точек зрения на жизнь и мир, кроме организационных.
А. А. Богданов
Первый автоконвейер изобрел Ранс Олдс, владелец Olds Motors Company. Генри Форд развил его идею «движущейся сборки» автомобилей, сконструировав ленточный конвейер.
Совокупность методов представления календарных графиков можно разделить на две группы: графические и табличные.
К графическим методам относятся планировочный и диспетчерский графики, ленточный график-хронограмма, график Ганта (Гант-карта), сетевой график.
Планировочный график представляет собой схематическое изображение производственного процесса. Для каждой работы в графике отводится отдельная строка, в которой пишется наименование работы и с помощью определенного расположения линии работы по отношению к оси времени указывается время ее выполнения.
Ленточный график-хронограмма представляет собой последовательность отрезков ленточки, каждый из которых соответствует определенному виду работ. Расположение графика синхронизируется с осью времени. На отрезках ленточки с помощью цвета, штриховки или надписей указываются виды выполняемых операции или работ.
Диспетчерский график является разновидностью планировочного или ленточного, но строится он в процессе фактического выполнения работ. Конечные точки графика в каждый момент времени сигнализируют о состоянии оборудования и выполняемых работах.
График Ганта строится в координатах «операции-время». По вертикальной оси откладывают номер операций, по горизонтальной – количество времени, требующееся для ее осуществления. График обработки конкретного изделия имеет вид нисходящей или восходящей лестницы. Размер ступеньки соответствует объему времени обработки на соответствующей операции, наклонный переход от одной операции к другой – времени движения изделия между операциями.
Сетевой график состоит из узлов, соединенных стрелками. Стрелки символизируют отдельные работы рассматриваемого комплекса, узлы – моменты начала или окончания работ.
Табличный график выполнения работ менее нагляден, но содержит больше информации. По видам работ в строках таблицы указывают: номер работы, ее наименование, время начала и окончания, привлекаемые ресурсы, исполнителей и т. д.
Критериями оптимизации при выборе очередности могут быть: минимизация общей продолжительности (интервала времени между моментом начала первой операции в последовательности и моментом окончания последней); минимизация общего запаздывания (разницы между плановым и директивным сроком завершения операций); минимизация потерь, обусловленных запаздыванием; • минимизация стоимости межоперационных заделов.
Для более сложного критерия может быть использована сумма нескольких слагаемых (потери от запаздывания, производственные затраты, стоимость межоперационных заделов).
6.3. Выбор очередности (одно рабочее место)
Элементарные задачи упорядочения решались с помощью графиков, подобных графикам Ганта. Аналитические методы решения подобных задач разработаны главным образом для несложных типовых случаев.
Для большинства задач упорядочения решение приходится искать с помощью метода моделирования или через эвристические алгоритмы построения решения.
Ситуация 1. Рассмотрим элементарную практическую ситуацию. В водохранилище перед шлюзом стоят три судна. Их подготовка и проводка через шлюз требуют 8, 10 и 27 часов соответственно. Требуется выбрать очередность проводки судов, обеспечивающую минимальную сумму времени ожидания. Если, например, первым пойдет второе судно, то два оставшихся будут ожидать 10 часов.
Несложно придти к выводу, что предпочтительная очередность соответствует проводке судов в порядке повышения индивидуальных затрат времени. «Меньшее время обработки ставится на первое место».
Ситуация 2. Рассмотрим подобную ситуацию с тремя судами при условии, что подготовка и проводка требуют одинакового времени, но плата за простой для судов составляет 1, 5 и 9 руб. в час соответственно. Требуется выбрать очередность проводки судов, обеспечивающую минимум суммы выплат за простой судов.
Предпочтительная очередность соответствует проводке судов в порядке уменьшения цены за простой. «Большая цена за ожидание ставится на первое место».
Ситуация 3. Рассмотрим практическую ситуацию, объединяющую первые две. В водохранилище перед шлюзом стоят три судна. Их подготовка и проводка через шлюз требуют 8, 10 и 27 часов соответственно. Плата за их простой равняется 1, 5 и 9 руб. в час соответственно. Требуется выбрать очередность проводки судов, обеспечивающую минимум суммы оплаты за их простой.
На выбор очередности проводки судов влияют два параметра, причем действующие в противоположных направлениях. Правило приоритета очередности в этом случае базируется на отношении время/цена. Деление на цену простоя фактически приводит к одинаковой ценности времени и сводит третью ситуацию по «времени проводки» к первой, откуда следует правило очередности. «Меньшее время проводки ставится на первое место».
Математическая постановка задачи Совокупность деталей (работ) (/) характеризуется t (i) – временем обработки (выполнения), с() – платой за единицу времени простоя (ожидания).
Для первой ситуации, в которой предполагается равенство цены простоя, оценка имеет следующий вид:
J = T(1) + T(2) +… + T(i) → min,
где T (i) – время ожидания детали, поставленной на i – е место.
Правило выбора очередности обработки деталей (выполнения работ) должно приводить к условию
t(1) < t(2) < t(3)…
«Деталь с меньшим временем обработки проходит в первую очередь». Для второй ситуации оценка имеет вид
J = T(1) c(1) + T(2) c(2) + … → min.
Правило выбора очередности обработки деталей должно приводить к условию
с(1) > c(2) > c(3) …
«Деталь с большей ценой пролеживания обрабатывается в первую очередь». Для третьей ситуации оценка имеет вид
J = T(1) c(1) + T(2) c(2) + … → min.
Правило выбора очередности обработки деталей должно приводить к условию?
«Деталь с меньшим приведенным временем пролеживания обрабатывается в первую очередь».
Для большинства задач упорядочения решение приходится искать с помощью метода моделирования или через эвристические алгоритмы построения решения.
Ситуация 1. Рассмотрим элементарную практическую ситуацию. В водохранилище перед шлюзом стоят три судна. Их подготовка и проводка через шлюз требуют 8, 10 и 27 часов соответственно. Требуется выбрать очередность проводки судов, обеспечивающую минимальную сумму времени ожидания. Если, например, первым пойдет второе судно, то два оставшихся будут ожидать 10 часов.
Несложно придти к выводу, что предпочтительная очередность соответствует проводке судов в порядке повышения индивидуальных затрат времени. «Меньшее время обработки ставится на первое место».
Ситуация 2. Рассмотрим подобную ситуацию с тремя судами при условии, что подготовка и проводка требуют одинакового времени, но плата за простой для судов составляет 1, 5 и 9 руб. в час соответственно. Требуется выбрать очередность проводки судов, обеспечивающую минимум суммы выплат за простой судов.
Предпочтительная очередность соответствует проводке судов в порядке уменьшения цены за простой. «Большая цена за ожидание ставится на первое место».
Ситуация 3. Рассмотрим практическую ситуацию, объединяющую первые две. В водохранилище перед шлюзом стоят три судна. Их подготовка и проводка через шлюз требуют 8, 10 и 27 часов соответственно. Плата за их простой равняется 1, 5 и 9 руб. в час соответственно. Требуется выбрать очередность проводки судов, обеспечивающую минимум суммы оплаты за их простой.
На выбор очередности проводки судов влияют два параметра, причем действующие в противоположных направлениях. Правило приоритета очередности в этом случае базируется на отношении время/цена. Деление на цену простоя фактически приводит к одинаковой ценности времени и сводит третью ситуацию по «времени проводки» к первой, откуда следует правило очередности. «Меньшее время проводки ставится на первое место».
Математическая постановка задачи Совокупность деталей (работ) (/) характеризуется t (i) – временем обработки (выполнения), с() – платой за единицу времени простоя (ожидания).
Для первой ситуации, в которой предполагается равенство цены простоя, оценка имеет следующий вид:
J = T(1) + T(2) +… + T(i) → min,
где T (i) – время ожидания детали, поставленной на i – е место.
Правило выбора очередности обработки деталей (выполнения работ) должно приводить к условию
t(1) < t(2) < t(3)…
«Деталь с меньшим временем обработки проходит в первую очередь». Для второй ситуации оценка имеет вид
J = T(1) c(1) + T(2) c(2) + … → min.
Правило выбора очередности обработки деталей должно приводить к условию
с(1) > c(2) > c(3) …
«Деталь с большей ценой пролеживания обрабатывается в первую очередь». Для третьей ситуации оценка имеет вид
J = T(1) c(1) + T(2) c(2) + … → min.
Правило выбора очередности обработки деталей должно приводить к условию?
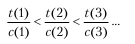
«Деталь с меньшим приведенным временем пролеживания обрабатывается в первую очередь».
6.4. Выбор очередности обработки при двух агрегатах (алгоритм Джонсона)
Общий случай задачи выбора последовательности обработки деталей на двух станках, если детали должны пройти обработку на одном станке, а затем на втором и на станке не может обрабатываться больше одной детали, рассмотрел в 1954 г. С. Джонсон. Метод решения такой задачи называют алгоритмом Джонсона.
Рассмотрим участок с двумя агрегатами. Совокупность деталей должна последовательно пройти обработку на первом агрегате, а потом на втором. Между агрегатами отсутствует склад, поэтому занятость второго агрегата задерживает освобождение первого. Требуется выбрать очередность обработки деталей, обеспечивающую меньшее суммарное время занятости участка. Это время рассчитывается от момента начала обработки первой детали на первом агрегате до окончания обработки последней детали на втором агрегате.
Очевидным является вывод, что выигрыша во времени можно достигнуть только за счет параллельной работы агрегатов. Длительная занятость первого агрегата, пока второй стоит, так же как и занятость второго, когда первый агрегат уже закончил работу, нерациональны. Отсюда ясно, что на первое место в очередности следует поставить деталь с меньшим временем обработки на первом агрегате. Аналогично на последнее место следует поставить деталь, у которой самое короткое время обработки на втором агрегате. Если это правило распространить на всю совокупность деталей, то получим алгоритм Джонсона.
Сначала выбираются детали, у которых время выполнения первой операции короче времени выполнения второй операции. Эти детали обрабатываются в порядке возрастания времени выполнения первой операции. Остальные детали обрабатываются в порядке убывания времени выполнения второй операции.
Условие оптимальной очередности пар деталей выглядит следующим образом:
min [a(i), b(i + 1)] < min [a(i + 1), b(i)].
Простой алгоритм решения задачи для двух станков вызвал многочисленные попытки обобщения полученного результата применительно к ситуации наличия нескольких станков. Однако все предпринятые попытки оказались успешными только в немногочисленных частных случаях. Общего алгоритма найти не удалось.
Большое распространение получили эвристические методы выбора последовательности обработки деталей, базирующиеся на правилах предпочтения. Выделим следующие используемые на практике правила предпочтения:
• раньше срок готовности на заключительной стадии технологического процесса;
• больше потери от пролеживания в незавершенном производстве;
• меньше запас времени по отношению к сроку готовности;
• деталь поступила на обработку первой;
• больший процент брака на последующих участках;
• меньше время обработки на первой стадии технологического процесса;
• больше время обработки на завершающей стадии технологического процесса.
Рассмотрим участок с двумя агрегатами. Совокупность деталей должна последовательно пройти обработку на первом агрегате, а потом на втором. Между агрегатами отсутствует склад, поэтому занятость второго агрегата задерживает освобождение первого. Требуется выбрать очередность обработки деталей, обеспечивающую меньшее суммарное время занятости участка. Это время рассчитывается от момента начала обработки первой детали на первом агрегате до окончания обработки последней детали на втором агрегате.
Очевидным является вывод, что выигрыша во времени можно достигнуть только за счет параллельной работы агрегатов. Длительная занятость первого агрегата, пока второй стоит, так же как и занятость второго, когда первый агрегат уже закончил работу, нерациональны. Отсюда ясно, что на первое место в очередности следует поставить деталь с меньшим временем обработки на первом агрегате. Аналогично на последнее место следует поставить деталь, у которой самое короткое время обработки на втором агрегате. Если это правило распространить на всю совокупность деталей, то получим алгоритм Джонсона.
Сначала выбираются детали, у которых время выполнения первой операции короче времени выполнения второй операции. Эти детали обрабатываются в порядке возрастания времени выполнения первой операции. Остальные детали обрабатываются в порядке убывания времени выполнения второй операции.
Условие оптимальной очередности пар деталей выглядит следующим образом:
min [a(i), b(i + 1)] < min [a(i + 1), b(i)].
Простой алгоритм решения задачи для двух станков вызвал многочисленные попытки обобщения полученного результата применительно к ситуации наличия нескольких станков. Однако все предпринятые попытки оказались успешными только в немногочисленных частных случаях. Общего алгоритма найти не удалось.
Большое распространение получили эвристические методы выбора последовательности обработки деталей, базирующиеся на правилах предпочтения. Выделим следующие используемые на практике правила предпочтения:
• раньше срок готовности на заключительной стадии технологического процесса;
• больше потери от пролеживания в незавершенном производстве;
• меньше запас времени по отношению к сроку готовности;
• деталь поступила на обработку первой;
• больший процент брака на последующих участках;
• меньше время обработки на первой стадии технологического процесса;
• больше время обработки на завершающей стадии технологического процесса.
6.5. Управление запасами
Почему математика, будучи в конечном счете продуктом человеческого мышления, столь превосходно приспособлена к объектам реальности?
Альберт Эйнштейн
Виды запасов
Ключевые вопросы для управления запасами таковы:
• Когда заказать?
• Сколько заказать?
• Сколько иметь на складе?
• Сколько отгрузить?
Основные понятия для управления запасами: склад, партия, время заказа поставок, затраты хранения.
Склад – сооружение, здание, устройство, предназначенное для приемки, размещения и хранения поступающих на него товаров, подготовки их к потреблению и отпуску потребителям. Склад обеспечивает сохранность материальных ценностей, позволяет накапливать необходимые запасы. Запас материалов необходим практически для каждого вида деятельности, связанного с привлечением поставок от партнеров или смежников.
Причины появления запасов:
• необходимость накопления партии потребления при поставке малых партий от партнеров;
• необходимость накопления партии транспортировки при изготовлении малыми партиями;
• рассогласование режимов работы поставщика и потребителя;
• компенсация сбоев в системе поставок материалов.
Запас состоит из годных к употреблению, но неиспользуемых ресурсов: материалов, готовой продукции, машин, инструмента.
Общий запас на складе предприятия состоит из нескольких слагаемых. Совокупный запас предприятия включает запасы средств и предметов труда, предназначенных для обеспечения непрерывности производства и снабжения потребителей. Совокупный запас складывается из запасов готовой продукции, производственных запасов сырья и материалов, запасных частей, инструмента и хозяйственного инвентаря. Товарный запас образуется из готовой продукции на складах у поставщика и в каналах сферы обращения.
В структуре производственного запаса выделяют текущий, подготовительный, страховой, сезонный, излишний запасы.
Запасы подготовительные – это часть товарных запасов, наличие которых вызвано необходимостью подготовки ресурсов к использованию в производстве. Подготовка может состоять в сортировке, контроле, раскрое, сушке. Размер подготовительных запасов определяется временем подготовки и объемом их среднесуточного потребления.
Запасы производственные – часть запасов, распределенная по стадиям производства. Они образуются из материалов, хранящихся перед агрегатами и участками с целью обеспечения бесперебойности процессов.
Текущий запас – основная часть производственного запаса. За его счет обеспечивается непрерывность снабжения производственного процесса между последующими поставками.
Страховой запас предназначен для непрерывного снабжения производства в случае непредвиденных обстоятельств: отклонения в периодичности и величине фактических поставок от плановых или договорных, задержке материала в пути при доставке от поставщика, непредвиденной порче материала.
Сезонный запас образуется при сезонном характере условий поставки материала. Его назначение – обеспечить нормальную работу предприятия на время сезонного перерыва в поставке материала или перерывов в работе у поставщика. Нормативная величина сезонного запаса определяется на основе величины его среднесуточного потребления и длительности временного перерыва в поставке.
Запасы неликвидные – не используемые в течение длительного срока производственные и товарные запасы. Образуются вследствие ухудшения качества материала в процессе хранения, ошибок при заказе материала, морального износа. Излишние запасы, потребность в которых отсутствует, также считаются неликвидными.
Запасы переходящие – это остатки ресурсов материала или топлива на конец отчетного периода.
Переработка материальных ценностей на складах предусматривает учет, контроль, сортировку поступающих грузов, внутрискладскую транспортировку груза к местам временного хранения, установку грузов на складских стеллажах или площадках, формирование партий грузов для отправки заказчику. Время выполнения отдельных операций называют оперативным временем, а общую сумму временных затрат – циклом грузопереработки. Задачей системы управления является минимизация затрат на грузопереработку. «Перемещать груз наилучшим образом – это не перемещать его вовсе». Принимая решение о размещении груза, следует учесть, когда и в какой ситуации он потребуется. На складе необходимо снижать затраты, увеличивать оперативное складское пространство, улучшать условия труда. Предпочтительнее получать грузы с учетом последовательности их использования, уменьшать количество промежуточных складских операций, перемещать грузы только на короткие расстояния, размещать грузы в положении, удобном для их последующего изъятия со склада.
Транспортировку нельзя безоговорочно принимать за плодотворную деятельность. Перемещение материалов на складе, движение транспортных средств порожняком – это прямая неоправданная потеря средств предприятия. Руководитель складского хозяйства должен стремиться, чтобы всякое перемещение являлось эффективной работой. В складской системе запасы могут храниться в одном или нескольких местах. Когда имеется более одного пункта хранения, то возникает необходимость взаимодействия.
Выделяют следующие типы складских систем:
• локальный склад (специализированный или универсальный) – одиночный склад;
• совокупность складов – несколько совместно управляемых складов;
• иерархическая система складов – несколько складов, имеющих линейную структуру подчиненности, при которой склад более высокого уровня обеспечивает поставки материалов на зависимые склады, находящиеся уровнем ниже;
• специализированная совокупность складов – несколько складов, функционирующих параллельно и ориентированных на различные виды материалов;
• автоматизированный склад – соединение складского оборудования и системы автоматического управления складированием и доставкой материалов.
Складские системы имеют существенные отличия друг от друга. Они различаются размерами, сложностью, составом хранимых материалов, размером издержек, частотой попадания случайных материалов в общий поток.
По условиям хранения различают закрытые, полузакрытые, открытые склады. По характеру труда – немеханизированные, механизированные, автоматизированные, полностью автоматические склады.
Склад характеризуется тремя группами параметров: параметры поступающего потока материалов (размер партии, общая поставка за интервал времени, интервал поставок, тип транспорта, время поставок); параметры склада (потенциальный размер запасов, тип материалов, издержки, выполняемые дополнительные работы, потери, степень автоматизации, режим контроля); параметры уходящего потока (размер партии, общая потребность, интервал отправки, тип транспорта, время доставки).