Страница:
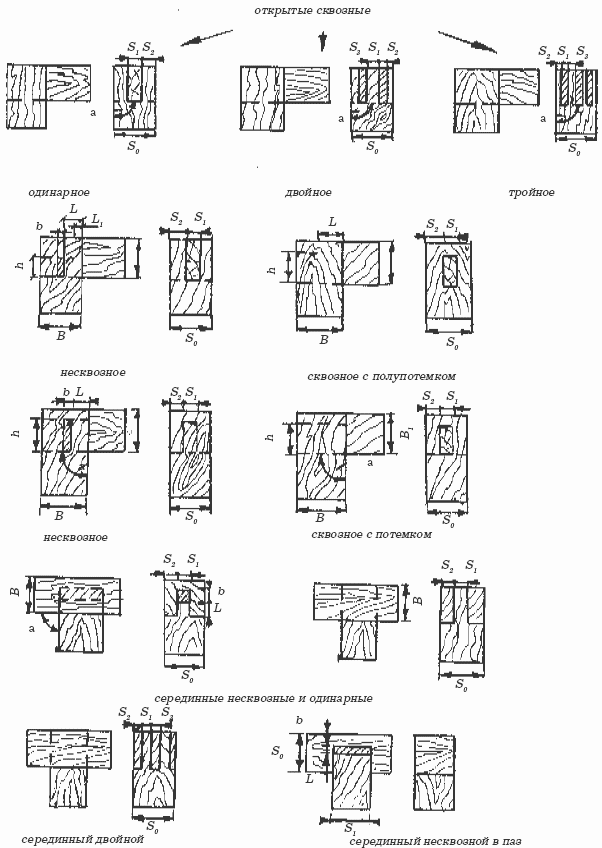
Рис. 38. Угловые шиповые соединения
Элементы деревянных конструкций соединяют с помощью нагелей, представляющих собой цилиндрические деревянные или металлические стержни, шурупов, гвоздей, болтов, расположенных в произвольном порядке.
Подготовка древесины к окрашиванию
Прежде чем приcтупить к окрашиванию древесины, следует подготовить ее поверхность, то есть произвести обессмоливание и отбеливание.
После проведенных процедур краска наносится на поверхность древесины ровным слоем.
После проведенных процедур краска наносится на поверхность древесины ровным слоем.
Обессмоливание
Обессмоливание удаляет смолянистые накопления и жировые пятна. Нередко этот процесс осуществляют одновременно с отбеливанием. Для обессмоливания используют 25 %-ный раствор технического ацетона или этиловый спирт.
При обработке этиловым спиртом поверхность получается более чистой. При этом жидкость наносят на обрабатываемый участок с помощью кисти, а затем смывают теплой водой. После этого изделие просушивают.
Для обессмоливания большой поверхности можно приготовить состав, в рецептуру которого входят следующие компоненты: 1 л воды, 40–50 г питьевой соды, 50 г поташа, 25–40 г измельченного мыла, 10 г спирта, 200 г ацетона.
Горячий раствор с помощью кисти наносят на поверхность, после чего ее промывают водой и просушивают.
При обработке этиловым спиртом поверхность получается более чистой. При этом жидкость наносят на обрабатываемый участок с помощью кисти, а затем смывают теплой водой. После этого изделие просушивают.
Для обессмоливания большой поверхности можно приготовить состав, в рецептуру которого входят следующие компоненты: 1 л воды, 40–50 г питьевой соды, 50 г поташа, 25–40 г измельченного мыла, 10 г спирта, 200 г ацетона.
Горячий раствор с помощью кисти наносят на поверхность, после чего ее промывают водой и просушивают.
Отбеливание
Отбеливание проводят непосредственно перед крашением древесины. При этом цветовой тон материала выравнивается. К отбеливающим веществам относят перекись водорода, щавелевую кислоту, хлорную известь и перекись титана. Однако наиболее эффективными в применении и доступными по цене являются перекись водорода и щавелевая кислота.
При отбеливании щавелевой кислотой готовят ее 10 %-ный раствор и 20 %-ный раствор гидросульфита натрия. Поверхность обрабатывают раствором соли, затем щавелевой кислотой. Через 5 мин растворы удаляют и промывают изделие теплой водой.
Следует учитывать, что дуб практически не поддается отбеливанию перекисью водорода.
При длительной выдержке в этом веществе его древесина приобретает зеленоватый оттенок.
Данный реактив эффективно использовать для отбеливания таких пород, как грецкий орех, береза и бук. Перед нанесением 30 %-ного раствора перекиси водорода шпон или массив смачивают теплой водой, слегка подсушивают и обрабатывают 10 %-ным раствором аммиака.
Смесь 20 %-ных растворов аммиака и перекиси водорода в соотношении 10:1 рекомендуется применять для отбеливания ясеня и березы.
Светлые породы древесины – такие, как липа, береза, клен, тополь, отбеливают раствором 1,5–6 г щавелевой кислоты в 100 г кипяченой воды. Для нейтрализации оставшейся на изделии кислоты используют следующий состав: 15 г хлорной извести, 3 г кальцинированной соды, 100 г воды.
При этом в горячей воде растворяют соду, а после остывания полученного раствора в него добавляют хлорную известь. Обработка этим составом способствует не только отбеливанию древесины, но и поднятию ворса.
После нанесения всех растворов деталь тщательно промывают водой и высушивают.
Для отбеливания дубового шпона используют щавелевую кислоту, 5 %-ный раствор лимонной или уксусной кислоты. Ускоренное отбеливание можно произвести с помощью водного раствора, который содержит 2 % серной, 1,5 % щавелевой кислоты и 2,5 % перекиси натрия.
При отбеливании щавелевой кислотой готовят ее 10 %-ный раствор и 20 %-ный раствор гидросульфита натрия. Поверхность обрабатывают раствором соли, затем щавелевой кислотой. Через 5 мин растворы удаляют и промывают изделие теплой водой.
Следует учитывать, что дуб практически не поддается отбеливанию перекисью водорода.
При длительной выдержке в этом веществе его древесина приобретает зеленоватый оттенок.
Данный реактив эффективно использовать для отбеливания таких пород, как грецкий орех, береза и бук. Перед нанесением 30 %-ного раствора перекиси водорода шпон или массив смачивают теплой водой, слегка подсушивают и обрабатывают 10 %-ным раствором аммиака.
Смесь 20 %-ных растворов аммиака и перекиси водорода в соотношении 10:1 рекомендуется применять для отбеливания ясеня и березы.
Светлые породы древесины – такие, как липа, береза, клен, тополь, отбеливают раствором 1,5–6 г щавелевой кислоты в 100 г кипяченой воды. Для нейтрализации оставшейся на изделии кислоты используют следующий состав: 15 г хлорной извести, 3 г кальцинированной соды, 100 г воды.
При этом в горячей воде растворяют соду, а после остывания полученного раствора в него добавляют хлорную известь. Обработка этим составом способствует не только отбеливанию древесины, но и поднятию ворса.
После нанесения всех растворов деталь тщательно промывают водой и высушивают.
Для отбеливания дубового шпона используют щавелевую кислоту, 5 %-ный раствор лимонной или уксусной кислоты. Ускоренное отбеливание можно произвести с помощью водного раствора, который содержит 2 % серной, 1,5 % щавелевой кислоты и 2,5 % перекиси натрия.
Крашение
Крашение древесины может быть поверхностным и глубоким, растворы красителей – насыщенными и слабыми. Чтобы при высыхании и шлифовании поверхность древесины не приобретала светлого оттенка, рекомендуется производить глубокое крашение.
Большинство реактивов, которые применяются при крашении древесины, ядовиты. При попадании на кожу человека они вызывают ожоги. Использовать их в работе не рекомендуется.
Но если применение данных реактивов необходимо, работу следует проводить в хорошо проветриваемом помещении, вдали от продуктов питания и использовать при этом защитные очки и перчатки.
Существуют холодный и горячий способы крашения.
При холодном способе окрашивания получают устойчивые, однотонные цвета.
Особенно эффективным является применение природных красителей, так как их пигменты не разлагаются и устойчивы к свету.
Процесс горячего окрашивания необходимо постоянно контролировать, так как при воздействии высоких температур многие красители изменяют цвет. По этой причине рекомендуется периодически вынимать изделие из кипящего раствора с помощью пинцета и, отломив кусочек, осматривать срез. На качество окрашивания влияет время выдержки заготовок и концентрация раствора. Если изделие не воспринимает цвет, следует увеличить содержание пигмента в растворе, а время на пропитку сократить.
После крашения изделие промывают, периодически переворачивая. Для сушки выбирают место, защищенное от воздействия прямых солнечных лучей. Пересушка материала недопустима. Наиболее стойкое и интенсивное окрашивание древесины происходит в случаях, когда красящие компоненты вступают в реакцию с дубильными веществами.
Чтобы проверить содержание в древесине дубильных веществ, следует нанести на образец каплю 5 %-ного раствора железного купороса.
Если она высыхает и не оставляет следа, значит, дубильные вещества отсутствуют. Серые или черные пятна свидетельствуют о наличии их в материале.
Большинство реактивов, которые применяются при крашении древесины, ядовиты. При попадании на кожу человека они вызывают ожоги. Использовать их в работе не рекомендуется.
Но если применение данных реактивов необходимо, работу следует проводить в хорошо проветриваемом помещении, вдали от продуктов питания и использовать при этом защитные очки и перчатки.
Существуют холодный и горячий способы крашения.
При холодном способе окрашивания получают устойчивые, однотонные цвета.
Особенно эффективным является применение природных красителей, так как их пигменты не разлагаются и устойчивы к свету.
Процесс горячего окрашивания необходимо постоянно контролировать, так как при воздействии высоких температур многие красители изменяют цвет. По этой причине рекомендуется периодически вынимать изделие из кипящего раствора с помощью пинцета и, отломив кусочек, осматривать срез. На качество окрашивания влияет время выдержки заготовок и концентрация раствора. Если изделие не воспринимает цвет, следует увеличить содержание пигмента в растворе, а время на пропитку сократить.
После крашения изделие промывают, периодически переворачивая. Для сушки выбирают место, защищенное от воздействия прямых солнечных лучей. Пересушка материала недопустима. Наиболее стойкое и интенсивное окрашивание древесины происходит в случаях, когда красящие компоненты вступают в реакцию с дубильными веществами.
Чтобы проверить содержание в древесине дубильных веществ, следует нанести на образец каплю 5 %-ного раствора железного купороса.
Если она высыхает и не оставляет следа, значит, дубильные вещества отсутствуют. Серые или черные пятна свидетельствуют о наличии их в материале.
Работа с металлом
При проведении строительных работ и изготовлении различных изделий в большинстве случаев невозможно обойтись без применения металла. Однако предварительно необходимо научиться его обрабатывать, то есть резать, чистить, править и т. д.
Некоторые операции с металлом, описанные ниже, помогут начинающему мастеру в проведении различного вида работ.
Некоторые операции с металлом, описанные ниже, помогут начинающему мастеру в проведении различного вида работ.
Обработка металла
Обработка металла включает в себя достаточно большое количество работ различного вида, каждая из которых начинается с подготовки поверхности, которую предстоит обрабатывать.
Основными видами работ по обработке металла являются очистка, правка, окрашивание, разметка, кернение, гибка, рубка, опиливание, сверление, нарезание резьбы.
Кроме того, к обработке металла можно отнести и скрепление разнообразных металлических деталей различными способами, в том числе клепку, пайку, сварку, склеивание.
Основными видами работ по обработке металла являются очистка, правка, окрашивание, разметка, кернение, гибка, рубка, опиливание, сверление, нарезание резьбы.
Кроме того, к обработке металла можно отнести и скрепление разнообразных металлических деталей различными способами, в том числе клепку, пайку, сварку, склеивание.
Резка металла
Резка металла представляет собой операцию по обработке металла, при которой заготовку любой формы разделяют на части. Для ручной резки используют ножницы различных типов и ножовку.
Резка металла ручными ножницами
Ручные ножницы применяют при резке листовой и полосовой стали толщиной до 0,7 мм и листов латуни и дюралюминия диаметром до 1,5 мм.
Металлические листы толщиной до 0,2 мм режут вручную. Лезвия ножниц при этом разводят на 3/4 их длины, лист металла располагают перпендикулярно к плоскости режущих кромок ножниц.
При сжатии ручек ножниц не следует сводить лезвия до конца, так как это приводит к разрыву металла в конце разреза. При вырезании круглых заготовок металл режут против часовой стрелки, для чего заготовку поворачивают по часовой стрелке.
При резке на полосы листа толщиной 0,2–0,5 мм можно воспользоваться ручными ножницами, одну из рукояток которых зажимают в тисках, а на другую надавливают рукой сверху.
Металлические листы толщиной до 0,2 мм режут вручную. Лезвия ножниц при этом разводят на 3/4 их длины, лист металла располагают перпендикулярно к плоскости режущих кромок ножниц.
При сжатии ручек ножниц не следует сводить лезвия до конца, так как это приводит к разрыву металла в конце разреза. При вырезании круглых заготовок металл режут против часовой стрелки, для чего заготовку поворачивают по часовой стрелке.
При резке на полосы листа толщиной 0,2–0,5 мм можно воспользоваться ручными ножницами, одну из рукояток которых зажимают в тисках, а на другую надавливают рукой сверху.
Резка металла ручными силовыми ножницами
Сталь толщиной более 0,7 мм режут ручными силовыми ножницами. При этом рукоятку с насечкой закрепляют в тисках, рабочую рукоятку с пластмассовым наконечником удерживают в руке.
Ножи на рычажных ножницах можно менять, что предусмотрено их конструкцией.
Кроме того, на ножницах имеется приспособление для резки металлических прутков диаметром до 8 мм. Сила резания увеличивается за счет применения рычага примерно в 2 раза по сравнению с обычными ножницами.
Ножи на рычажных ножницах можно менять, что предусмотрено их конструкцией.
Кроме того, на ножницах имеется приспособление для резки металлических прутков диаметром до 8 мм. Сила резания увеличивается за счет применения рычага примерно в 2 раза по сравнению с обычными ножницами.
Резка металла настольными рычажными ножницами
Металл толщиной до 43 мм, латунь и алюминий диаметром до 6 мм режут настольными ручными рычажными ножницами.
При этом необходимо надежно прикрепить основание ножниц к столешнице верстака при помощи болтов. Один из ножей в таких ножницах закреплен на рукоятке и может опускаться вслед за рукояткой вниз.
Второй нож закреплен внутри корпуса ножниц. Нажимать на рукоятку рычажных ножниц нужно плавно, без рывков. Следует помнить также, что на рычажных ножницах можно резать металл только по прямой линии.
При этом необходимо надежно прикрепить основание ножниц к столешнице верстака при помощи болтов. Один из ножей в таких ножницах закреплен на рукоятке и может опускаться вслед за рукояткой вниз.
Второй нож закреплен внутри корпуса ножниц. Нажимать на рукоятку рычажных ножниц нужно плавно, без рывков. Следует помнить также, что на рычажных ножницах можно резать металл только по прямой линии.
Резка металла ножовкой
Зубья на полотне ручных ножовок бывают крупными и мелкими. При работе их вершины направлены в одну сторону, что позволяет достаточно легко резать металл. Кроме того, на ножовочных полотнах производится развод зубьев, которые по одному или группами поочередно отгибаются в разные стороны, что значительно снижает трение инструмента.
Очистка и мойка металла
Приступая к обработке металлической поверхности, ее предварительно очищают. Чистая поверхность заготовки ржавеет значительно реже, чем неочищенная. Кроме того, работая с чистой поверхностью, гораздо легче выдерживать необходимые размеры детали. При очистке металла удаляют слои краски, антикоррозионной смазки, окалины, ржавчины. Проводить очистку можно с применением различных скребков и щеток.
После очистки металла осуществляют его мойку, которая заключается в удалении небольших загрязнений и жировых пленок с помощью моющих средств.
В качестве моющих жидкостей применяются органические растворители: бензин, керосин, спирт, смесь бензина со спиртом. Если заготовка загрязнена смолой или нитроэмалью, в процессе мойки можно применить ацетон или смесь спирта с ацетоном.
Используют также водные растворы щелочей и синтетических поверхностно-активных веществ. Следует помнить, что температура органических растворителей при мойке не должна превышать 30 °C, а их водных растворов – 45–60 °C.
Если требуется удалить ржавчину с металлической поверхности, а специальных моющих средств под рукой нет, можно смочить мягкие стальные опилки машинным маслом и при помощи тампона из ветоши протереть ржавую поверхность до металлического блеска. После этого останется лишь удалить остатки машинного масла.
Зачастую коррозия металла приводит к образованию ржавчины на стальных и чугунных поверхностях.
Происходит это под воздействием кислорода, входящего в состав воды и воздуха. Возникает коррозия и от соприкосновения металлов с электролитами.
Значительно усиливается коррозия в районах с повышенной влажностью, а также с пониженной температурой воздуха. Ржавчину можно удалять с металлической поверхности шкуркой. Однако нужно сразу сказать, что зачистку поверхности шкуркой не проводят при большом объеме работы.
Избавиться от ржавчины можно, если воспользоваться химическим способом ее удаления. Для этого поверхность обезжиривают бензином и просушивают. Затем готовят раствор с содержанием 20 % фосфорной кислоты плотностью 1,7 г/м3 и 80 % воды.
В раствор добавляют 8 % хромового ангидрида и нагревают его до температуры 60–65 °C. В зависимости от степени коррозии поврежденную заготовку покрывают полученным раствором на 10–15 мин.
По истечении положенного срока заготовку промывают 5 %-ным раствором кальцинированной соды при температуре 80 °C, после чего ополаскивают горячей или холодной водой. С целью предотвращения коррозии обработанные поверхности покрывают техническим вазелином.
После очистки металла осуществляют его мойку, которая заключается в удалении небольших загрязнений и жировых пленок с помощью моющих средств.
В качестве моющих жидкостей применяются органические растворители: бензин, керосин, спирт, смесь бензина со спиртом. Если заготовка загрязнена смолой или нитроэмалью, в процессе мойки можно применить ацетон или смесь спирта с ацетоном.
Используют также водные растворы щелочей и синтетических поверхностно-активных веществ. Следует помнить, что температура органических растворителей при мойке не должна превышать 30 °C, а их водных растворов – 45–60 °C.
Если требуется удалить ржавчину с металлической поверхности, а специальных моющих средств под рукой нет, можно смочить мягкие стальные опилки машинным маслом и при помощи тампона из ветоши протереть ржавую поверхность до металлического блеска. После этого останется лишь удалить остатки машинного масла.
Зачастую коррозия металла приводит к образованию ржавчины на стальных и чугунных поверхностях.
Происходит это под воздействием кислорода, входящего в состав воды и воздуха. Возникает коррозия и от соприкосновения металлов с электролитами.
Значительно усиливается коррозия в районах с повышенной влажностью, а также с пониженной температурой воздуха. Ржавчину можно удалять с металлической поверхности шкуркой. Однако нужно сразу сказать, что зачистку поверхности шкуркой не проводят при большом объеме работы.
Избавиться от ржавчины можно, если воспользоваться химическим способом ее удаления. Для этого поверхность обезжиривают бензином и просушивают. Затем готовят раствор с содержанием 20 % фосфорной кислоты плотностью 1,7 г/м3 и 80 % воды.
В раствор добавляют 8 % хромового ангидрида и нагревают его до температуры 60–65 °C. В зависимости от степени коррозии поврежденную заготовку покрывают полученным раствором на 10–15 мин.
По истечении положенного срока заготовку промывают 5 %-ным раствором кальцинированной соды при температуре 80 °C, после чего ополаскивают горячей или холодной водой. С целью предотвращения коррозии обработанные поверхности покрывают техническим вазелином.
Правка металла
Правку металла применяют в тех случаях, когда нужно устранить искажение формы заготовки – волнистость, коробление, вмятины, искривления. Существует несколько вариантов правки металла. Однако независимо от степени сложности работы правку материала производят в рабочих рукавицах.
Металл можно править в холодном виде, однако чаще всего его нагревают, так как нагретый материал правится гораздо легче.
В домашних условиях правку следует проводить на наковальне или массивной плите, изготовленной из стали или чугуна. Рабочая поверхность плиты должна быть ровной и чистой. Для того чтобы шум от ударов был менее громким, плиту следует устанавливать на деревянном столе.
Для правки необходим специальный слесарный инструмент. В противном случае металл может приобрести еще более заметные дефекты. Молоток, предназначенный для правки металла, должен быть изготовлен из мягкого материала – такого, как свинец, медь, дерево, резина.
Следует учитывать, что править металл молотком с квадратным бойком не рекомендуется, так как инструмент оставит на поверхности материала следы в виде забоин. Боек молотка должен быть круглым и отполированным.
Для правки тонкого листового и полосового металла нередко применяют деревянные и металлические гладилки и поддержки.
Для правки закаленных деталей с фасонными поверхностями существуют правильные бабки.
Чтобы проверить кривизну заготовки, деталь укладывают на гладкую плиту, поворачивают вверх той стороной, которая после правки должна быть плоской. Зазор между плитой и заготовкой указывает на степень искривленности, которую необходимо устранить. Изогнутые участки отмечают мелом, после чего наносят по ним удары молотком.
Существуют различные способы правки металла. Примеры основных приемов по проведению данного вида работы приведены ниже.
Металл можно править в холодном виде, однако чаще всего его нагревают, так как нагретый материал правится гораздо легче.
В домашних условиях правку следует проводить на наковальне или массивной плите, изготовленной из стали или чугуна. Рабочая поверхность плиты должна быть ровной и чистой. Для того чтобы шум от ударов был менее громким, плиту следует устанавливать на деревянном столе.
Для правки необходим специальный слесарный инструмент. В противном случае металл может приобрести еще более заметные дефекты. Молоток, предназначенный для правки металла, должен быть изготовлен из мягкого материала – такого, как свинец, медь, дерево, резина.
Следует учитывать, что править металл молотком с квадратным бойком не рекомендуется, так как инструмент оставит на поверхности материала следы в виде забоин. Боек молотка должен быть круглым и отполированным.
Для правки тонкого листового и полосового металла нередко применяют деревянные и металлические гладилки и поддержки.
Для правки закаленных деталей с фасонными поверхностями существуют правильные бабки.
Чтобы проверить кривизну заготовки, деталь укладывают на гладкую плиту, поворачивают вверх той стороной, которая после правки должна быть плоской. Зазор между плитой и заготовкой указывает на степень искривленности, которую необходимо устранить. Изогнутые участки отмечают мелом, после чего наносят по ним удары молотком.
Существуют различные способы правки металла. Примеры основных приемов по проведению данного вида работы приведены ниже.
Правка полосового металла, изогнутого в плоскости
Правка полосового металла, изогнутого в плоскости, является наиболее простой операцией по обработке железа. Изогнутую заготовку располагают таким образом, чтобы она имела две точки соприкосновения с наковальней.
Удары молотком или кувалдой наносят по наиболее выпуклым местам. Силу ударов уменьшают по мере сокращения количества неровных участков.
При этом следует учитывать, что при нанесении ударов с одной стороны заготовки металл выгибается в обратную сторону. Поэтому заготовку нужно периодически переворачивать. Кроме того, не рекомендуется наносить несколько ударов подряд по одному участку поверхности материала.
В том случае, если на поверхности металла имеется несколько неровных участков, следует предварительно выправить края заготовки, а затем середину.
Удары молотком или кувалдой наносят по наиболее выпуклым местам. Силу ударов уменьшают по мере сокращения количества неровных участков.
При этом следует учитывать, что при нанесении ударов с одной стороны заготовки металл выгибается в обратную сторону. Поэтому заготовку нужно периодически переворачивать. Кроме того, не рекомендуется наносить несколько ударов подряд по одному участку поверхности материала.
В том случае, если на поверхности металла имеется несколько неровных участков, следует предварительно выправить края заготовки, а затем середину.
Правка круглого металла
Процесс правки круглого металла во многом схож с правкой полосового металла. При этом на поверхности материала отмечают мелом неровные места, располагают заготовку выпуклой частью вверх, после чего наносят удары от краев изгиба к середине.
Выправив основное искривление, силу ударов уменьшают, металлический прут периодически поворачивают вокруг его оси так, чтобы не допустить искривления металла в обратную сторону.
Металлические пруты квадратного сечения правят аналогичным способом.
Правка металла, изогнутого по ребру, является более сложной задачей. В этом случае часть заготовки предварительно подвергают растяжению.
Выправив основное искривление, силу ударов уменьшают, металлический прут периодически поворачивают вокруг его оси так, чтобы не допустить искривления металла в обратную сторону.
Металлические пруты квадратного сечения правят аналогичным способом.
Правка металла, изогнутого по ребру, является более сложной задачей. В этом случае часть заготовки предварительно подвергают растяжению.
Правка скрученного по спирали металла
Этот вид правки производится методом раскручивания. Для того чтобы выпрямить кривизну, 1 конец скрученного металла зажимают в большие тиски на слесарном столе, а другой – в ручные тиски.
Затем продолжают правку на гладкой выверенной плите обычным способом, следя за кривизной на просвет.
Затем продолжают правку на гладкой выверенной плите обычным способом, следя за кривизной на просвет.
Правка листового металла
Сложность правки листового металла зависит от характера повреждения материала: волнистость кромки, выпуклость или вмятина в середине листа или несколько типов дефектов одновременно.
Во время правки выпуклости удары наносят, начиная от края листа по направлению к поврежденному участку поверхности материала.
Наиболее распространенная ошибка начинающих мастеров заключается в том, что сильные удары наносят непосредственно по поврежденному участку листового металла, в результате чего поверхность материала еще более деформируется.
Кроме того, металл при подобной обработке испытывает довольно сильную деформацию на разрыв. По этой причине удары следует наносить слабые, но частые. Лист металла нужно периодически поворачивать в горизонтальной плоскости так, чтобы удары равномерно распределялись по всей его поверхности.
Если лист имеет несколько выпуклых участков, нужно свести их в один. Для этого удары молотком следует наносить в промежутках между повреждениями. При этом металл растягивается, все выпуклые участки объединяются в один. Затем продолжают правку обычным способом.
Если середина листа ровная, а края искажены волнами, то последовательность ударов при правке должна быть противоположной. В таком случае наносить их следует от середины к изогнутым краям листового металла. При этом металл в средней части листа растянется, волны на его краях исчезнут.
Тонкие листы правят с помощью бруска-гладилки, изготовленного из металла или дерева. При этом лист выглаживают с двух сторон, периодически поворачивая его. Качество такой правки контролируют с помощью металлической линейки.
Правка стального листа – достаточно трудная работа. Для этого стальной лист помещают на плиту-подкладку со множеством мелких затупленных бугорков, равномерно расположенных на ее поверхности.
Удары наносят резиновым молотком. При этом на листе образуются едва заметные волны, которые при шпатлевании и покраске станут совершенно незаметными. Единственная сложность заключается в изготовлении плиты-подкладки, которую в домашних условиях сделать довольно трудно. Плиту-подкладку обрабатывают на строгальном или фрезерном станке.
Во время правки выпуклости удары наносят, начиная от края листа по направлению к поврежденному участку поверхности материала.
Наиболее распространенная ошибка начинающих мастеров заключается в том, что сильные удары наносят непосредственно по поврежденному участку листового металла, в результате чего поверхность материала еще более деформируется.
Кроме того, металл при подобной обработке испытывает довольно сильную деформацию на разрыв. По этой причине удары следует наносить слабые, но частые. Лист металла нужно периодически поворачивать в горизонтальной плоскости так, чтобы удары равномерно распределялись по всей его поверхности.
Если лист имеет несколько выпуклых участков, нужно свести их в один. Для этого удары молотком следует наносить в промежутках между повреждениями. При этом металл растягивается, все выпуклые участки объединяются в один. Затем продолжают правку обычным способом.
Если середина листа ровная, а края искажены волнами, то последовательность ударов при правке должна быть противоположной. В таком случае наносить их следует от середины к изогнутым краям листового металла. При этом металл в средней части листа растянется, волны на его краях исчезнут.
Тонкие листы правят с помощью бруска-гладилки, изготовленного из металла или дерева. При этом лист выглаживают с двух сторон, периодически поворачивая его. Качество такой правки контролируют с помощью металлической линейки.
Правка стального листа – достаточно трудная работа. Для этого стальной лист помещают на плиту-подкладку со множеством мелких затупленных бугорков, равномерно расположенных на ее поверхности.
Удары наносят резиновым молотком. При этом на листе образуются едва заметные волны, которые при шпатлевании и покраске станут совершенно незаметными. Единственная сложность заключается в изготовлении плиты-подкладки, которую в домашних условиях сделать довольно трудно. Плиту-подкладку обрабатывают на строгальном или фрезерном станке.
Правка закаленного металла (рихтовка)
Для правки закаленного металла (рихтовки) необходим специальный молоток с бойком, изготовленным из закаленного металла. Нередко применяют молоток с закругленной узкой стороной бойка.
Рихтовочный молоток можно изготовить самостоятельно. Для этого в узком бойке молотка проделывают прорезь и плотно прессуют в нее заточенную под радиусом 0,1–0,2 мм пластинку из твердого сплава ВК 6 или ВК 8.
При правке закаленного металла удары наносят по вогнутому участку заготовки, которая начинает выпрямляться вследствие растяжения материала.
Рихтовку удобно производить на специальной рихтовочной бабке, которая имеет выпуклую поверхность. При этом заготовку следует периодически перемещать вверх и вниз.
Довольно сложной задачей для неопытного мастера является правка плоского угольника, угол которого стал больше или меньше 90°. При этом, если прямой угол уменьшился и составляет менее 90°, удары молотком нужно наносить по плоскости угольника у вершины внутреннего угла.
Если прямой угол увеличился и составляет более 90°, удары наносят у вершины внешнего угла.
Рихтовочный молоток можно изготовить самостоятельно. Для этого в узком бойке молотка проделывают прорезь и плотно прессуют в нее заточенную под радиусом 0,1–0,2 мм пластинку из твердого сплава ВК 6 или ВК 8.
При правке закаленного металла удары наносят по вогнутому участку заготовки, которая начинает выпрямляться вследствие растяжения материала.
Рихтовку удобно производить на специальной рихтовочной бабке, которая имеет выпуклую поверхность. При этом заготовку следует периодически перемещать вверх и вниз.
Довольно сложной задачей для неопытного мастера является правка плоского угольника, угол которого стал больше или меньше 90°. При этом, если прямой угол уменьшился и составляет менее 90°, удары молотком нужно наносить по плоскости угольника у вершины внутреннего угла.
Если прямой угол увеличился и составляет более 90°, удары наносят у вершины внешнего угла.
Окрашивание металла под разметку
Для окрашивания металлической поверхности под разметку рекомендуется использовать медный купорос, который хорошо держится на зачищенном металле.
Для этой цели нередко применяют краску или лак, которые достаточно быстро сохнут. В некоторых случаях используют разведенный до густоты молока мел с добавлением сиккатива или столярного клея, что способствует быстрому высыханию нанесенной на поверхность смеси.
При окрашивании красящее вещество растирают для того, чтобы оно ложилось по всей поверхности ровным слоем без пятен.
Если заготовка большая, кисточкой наносят окрашивающий слой на те ее поверхности, на которых предполагается нанесение разметочных рисок.
Для этой цели нередко применяют краску или лак, которые достаточно быстро сохнут. В некоторых случаях используют разведенный до густоты молока мел с добавлением сиккатива или столярного клея, что способствует быстрому высыханию нанесенной на поверхность смеси.
При окрашивании красящее вещество растирают для того, чтобы оно ложилось по всей поверхности ровным слоем без пятен.
Если заготовка большая, кисточкой наносят окрашивающий слой на те ее поверхности, на которых предполагается нанесение разметочных рисок.
Разметка металла
Работа с металлом требует максимальной точности. В противном случае усилия, затраченные на изготовление заготовки, окажутся напрасными.
Разметка металла означает нанесение разметочной линии, или риски, указывающей границы, до которых необходимо обработать материал. Различают разметку на плоскости и разметку пространственных заготовок.
Разметка металла означает нанесение разметочной линии, или риски, указывающей границы, до которых необходимо обработать материал. Различают разметку на плоскости и разметку пространственных заготовок.
Разметка на плоскости
Разметка на плоскости выполняется в следующей последовательности: наносят горизонтальные линии, затем вертикальные и наклонные. Последними размечают окружности, дуги и сопряжения, что дает возможность проконтролировать точность разметки прямых линий. При этом следует учитывать, что сопряжения должны быть плавными, а дуги – точно замкнуть прямые линии.
Линии рекомендуется проводить с помощью чертилки, которую прижимают к линейке или угольнику и не меняют угол наклона. В противном случае линия окажется не параллельной линейке.
Следует учитывать, что проводить одну линию 2 раза не рекомендуется, так как в результате она получится двойной.
Для проведения перпендикулярных линий используют стальной угольник, называемый двутавровым, к короткой стороне которого приварена небольшая металлическая пластина под углом 90°.
Угольник прикладывают к боковой поверхности верстака и с большой точностью проводят на металле перпендикулярные линии.
Для нахождения центра при выполнении отверстий на заготовке используют раздвижной центроискатель, кернер-центроискатель, угольник-центроискатель.
Линии рекомендуется проводить с помощью чертилки, которую прижимают к линейке или угольнику и не меняют угол наклона. В противном случае линия окажется не параллельной линейке.
Следует учитывать, что проводить одну линию 2 раза не рекомендуется, так как в результате она получится двойной.
Для проведения перпендикулярных линий используют стальной угольник, называемый двутавровым, к короткой стороне которого приварена небольшая металлическая пластина под углом 90°.
Угольник прикладывают к боковой поверхности верстака и с большой точностью проводят на металле перпендикулярные линии.
Для нахождения центра при выполнении отверстий на заготовке используют раздвижной центроискатель, кернер-центроискатель, угольник-центроискатель.
Разметка пространственных заготовок
Разметить деталь целиком, то есть сделать пространственную разметку, довольно сложно. Здесь необходимы знания приемов и методов пространственного черчения.
Прежде всего необходимо выбрать базовую поверхность. При этом следует руководствоваться следующими правилами:
– если у заготовки уже обработаны несколько плоских поверхностей, базовой считают ту из них, площадь которой больше;
– если заготовка имеет необработанные наружную и внутреннюю поверхности, за базовую принимают наружную поверхность;
– если не требуется обрабатывать всю поверхность заготовки, базовой должна стать та, которая не подвергнется обработке;
– если заготовка имеет цилиндрическую форму, базовой нужно считать поверхность, параллельную оси цилиндра;
– если заготовка имеет отверстия, за базовую принимается поверхность, параллельная оси отверстия.
Чтобы упростить процесс разметки, заготовку на разметочную плиту устанавливают таким образом, чтобы все ее поверхности были перпендикулярны к поверхности плиты или параллельны ей. Для этого используют различные металлические предметы – прокладки, призмы, бруски, кубики, клинья.
Горизонтальные риски наносят с 4 сторон заготовки (в некоторых случаях достаточно наметить риски с двух противоположных сторон детали).
После этого выполняют вертикальные риски, затем дуги, окружности, сопряжения и наклонные линии.
Прежде всего необходимо выбрать базовую поверхность. При этом следует руководствоваться следующими правилами:
– если у заготовки уже обработаны несколько плоских поверхностей, базовой считают ту из них, площадь которой больше;
– если заготовка имеет необработанные наружную и внутреннюю поверхности, за базовую принимают наружную поверхность;
– если не требуется обрабатывать всю поверхность заготовки, базовой должна стать та, которая не подвергнется обработке;
– если заготовка имеет цилиндрическую форму, базовой нужно считать поверхность, параллельную оси цилиндра;
– если заготовка имеет отверстия, за базовую принимается поверхность, параллельная оси отверстия.
Чтобы упростить процесс разметки, заготовку на разметочную плиту устанавливают таким образом, чтобы все ее поверхности были перпендикулярны к поверхности плиты или параллельны ей. Для этого используют различные металлические предметы – прокладки, призмы, бруски, кубики, клинья.
Горизонтальные риски наносят с 4 сторон заготовки (в некоторых случаях достаточно наметить риски с двух противоположных сторон детали).
После этого выполняют вертикальные риски, затем дуги, окружности, сопряжения и наклонные линии.
Кернение
После нанесения рисок приступают к их кернению, которое необходимо для того, чтобы при сверлении сверло можно было точно установить по направлению оси отверстия.
Керн представляет собой неглубокое конусное углубление в поверхности металла, которое выполняется с помощью кернера. При выполнении кернения важно точно установить кернер в центре отметки и при ударе по нему молотком не сместить его.
Кернер устанавливают следующим образом: наклоняют от себя так, чтобы острие попало в центр отметки, затем переводят в перпендикулярное положение к обрабатываемой поверхности и наносят по кернеру удар молотком.
Керны следует наносить на длинные разметочные риски на расстоянии 25–30 мм и 10–15 мм – на короткие. На криволинейных участках разметки – таких, как сопряжения, закругления, – керны наносят чаще – на расстоянии 5-10 мм друг от друга.
Маленькие окружности накернивают в четырех взаимно перпендикулярных точках. Большие окружности подвергают кернению в 6–8 местах. Кроме того, необходимо накернивать все точки пересечений и сопряжений.
Керн представляет собой неглубокое конусное углубление в поверхности металла, которое выполняется с помощью кернера. При выполнении кернения важно точно установить кернер в центре отметки и при ударе по нему молотком не сместить его.
Кернер устанавливают следующим образом: наклоняют от себя так, чтобы острие попало в центр отметки, затем переводят в перпендикулярное положение к обрабатываемой поверхности и наносят по кернеру удар молотком.
Керны следует наносить на длинные разметочные риски на расстоянии 25–30 мм и 10–15 мм – на короткие. На криволинейных участках разметки – таких, как сопряжения, закругления, – керны наносят чаще – на расстоянии 5-10 мм друг от друга.
Маленькие окружности накернивают в четырех взаимно перпендикулярных точках. Большие окружности подвергают кернению в 6–8 местах. Кроме того, необходимо накернивать все точки пересечений и сопряжений.
Гибка металла
При работе с металлом очень часто приходится выполнять операцию, связанную с его пластическим деформированием, – гибку. При сгибании металла его волокна сжимаются и растягиваются. Поэтому для того, чтобы пластическая деформация не перешла в деформацию разрыва, нужно внимательно выбирать усилия и радиусы загибов.
Диаметр загиба не должен быть меньше, чем толщина заготовки. В противном случае на металле могут образоваться трещины. Не рекомендуется гнуть заготовки из стального прутка диаметром более 10 мм.
Толщина полосовой стали должна составлять примерно 7 мм, диаметр стальных листов – 5 мм.
Гнуть металл будет значительно легче, если его предварительно подогреть. Но можно выполнять данный вид работы и без подогрева материала. Для этого на внешнюю поверхность в зоне сгиба наносят поперечные риски.
Существует несколько способов гибки металла. Наиболее распространенные из них описаны ниже.
Диаметр загиба не должен быть меньше, чем толщина заготовки. В противном случае на металле могут образоваться трещины. Не рекомендуется гнуть заготовки из стального прутка диаметром более 10 мм.
Толщина полосовой стали должна составлять примерно 7 мм, диаметр стальных листов – 5 мм.
Гнуть металл будет значительно легче, если его предварительно подогреть. Но можно выполнять данный вид работы и без подогрева материала. Для этого на внешнюю поверхность в зоне сгиба наносят поперечные риски.
Существует несколько способов гибки металла. Наиболее распространенные из них описаны ниже.
Гибка металла в тисках
Полосовую сталь удобно гнуть в слесарных тисках. Для этого заготовку устанавливают таким образом, чтобы сторона с нанесенной на нее риской была обращена к неподвижной губке тисков. При этом риска должна выступать над губкой примерно на 0,5 мм. Удары наносят в направлении неподвижной губки тисков.