Страница:
Современные буксиры, буксиры-толкачи и толкачи классифицируются в зависимости от района плавания и характера выполняемых задач. Буксиры, за исключением буксиров-плотоводов, относят к классу обслуживающих судов и разделяют на океанские, морские, рейдовые, портовые и для внутренних водных путей. Буксиры-плотоводы, буксиры-толкачи, плотоводы и толкачи эксплуатируются на внутренних водных путях. Буксиры-толкачи, которые могут буксировать суда и составы на буксирном канате или методом толкания, эксплуатируются как на внутренних водных путях, так и в морских условиях (морские барже-буксирные составы).
Буксиры отличаются малой длиной, что обеспечивает необходимые маневровые качества, высокими тяговыми показателями, большой остойчивостью. Мощность крупных океанских буксиров достигает 9200 кВт, а мощность буксиров-спасателей – 16 000 кВт, мощность портовых буксиров доходит до 2600 кВт. Скорость океанских и морских буксиров составляет 12–18 узлов (22.2—33 км/ч), портовых и рейдовых буксиров – 10–12 узлов (18.5—22.2 км/ч).
Буксирное судно для внутренних водных путей.
Буксирные суда оснащаются буксирным устройством, обеспечивающим буксировку несамоходных судов, а также судов, потерявших способность двигаться своим ходом. Основными конструктивными узлами буксирного устройства являются буксирный гак, буксирная лебёдка, на барабан которой наматывается буксирный канат, и буксирные арки, направляющие и ограничивающие движение буксирного каната. Буксирная лебёдка позволяет изменять длину буксирного каната, обеспечивая на извилистом судовом ходу при малой длине каната требуемую управляемость, а на прямом судовом ходу – уменьшать сопротивление состава за счёт увеличения длины буксирного каната. Буксирный гак используется при отказе буксирной лебёдки. Буксиры-толкачи, помимо буксирного устройства, оборудуются сцепным или автосцепным устройством, обеспечивающим жёсткую сцепку носовой части судна с кормовой частью состава. Толкачи оборудуются только сцепным (автосцепным) устройством. Конструкция сцепных и автосцепных устройств разнообразна. В речных и озёрных условиях отечественные буксиры-толкачи и толкачи оборудуются однозамковыми или двухзамковыми автосцепами, которые обеспечивают сцепку замков клешневого типа, установленных на одном судне, с вертикальными рельсами, укреплёнными на торцевой части (транце) другого судна. На морских баржебуксирных составах сцепка толкача и баржи производится с помощью мощных гидравлических сцепов, обеспечивающих возможность взаимных наклонений толкача и баржи относительно общей горизонтальной оси. На портовых буксирах применяются вакуумные сцепы. Эти буксиры оснащаются также манипуляторами для захвата буксирного каната. Для обеспечения высокой маневренности портовые буксиры оснащаются винторулевыми колонками, меняющими направление силы упора винта по желанию судоводителя. Буксиры-спасатели оснащаются разнообразным оборудованием для оказания помощи терпящим бедствие судам – буксировки судов, потерявших ход, снятия с мели, откачки воды, тушения пожаров, спасения людей. Все буксиры-толкачи и толкачи оборудуются мощным кормовым якорным устройством, обеспечивающим удержание на кормовом якоре толкаемого состава на течении. Мощность речных буксиров-толкачей и толкачей связана с размером составов, которые, в свою очередь, определяются габаритами водного пути. Т. к. эффективность перевозок возрастает при увеличении грузоподъёмности составов, на крупных реках используют мощные буксиры-толкачи. Мощность наиболее крупных отечественных толкачей достигает 2–3 тыс. кВт. На Миссисипи, где возможно применение особо крупных составов, мощность толкачей достигает 9 тыс. кВт.
БУЛЬДÓЗЕР, землеройная машина (а также съёмное землеройное оборудование на тракторе или тягаче), предназначенная для разработки и перемещения грунта, щебня, засыпки котлованов и траншей, расчистки снега на дорогах, планировки площадок и т. д. С помощью бульдозера можно перемещать грунт на небольшие расстояния (не более 80—100 м). Рабочий орган бульдозера – мощный отвал – может быть поворотным или неповоротным. Бульдозеры многоцелевого назначения наряду с выполнением традиционных работ используются для разработки и засыпки траншей, каналов, скважин, проведения земляных работ на мёрзлых грунтах, в погрузочно-разгрузочных работах. На бульдозеры приходится более 40 % всех объёмов земляных работ. Это объясняется высокой производительностью, манёвренностью, универсальностью и простотой конструкции рабочего оборудования.
Бульдозер
БУМÁГА, материал из растительных волокон, беспорядочно распределённых в тонкий лист и связанных между собой поверхностными силами сцепления. Бумагу производят гл. обр. из волокон древесины после соответствующей их обработки – размола, соединения с различными добавками (наполнителями), красителями и т. п. Впервые бумага была получена Цай Лунем во 2 в. в Китае путём осаждения водной суспензии свежих растительных волокон на сетке. В 6 в. этот способ, долго сохранявшийся в секрете, был вывезен в Японию, затем в страны Азии (6–8 вв.), где бумагу изготовляли из пенькового и льняного тряпья. Позднее таким образом бумагу стали вырабатывать в странах Северной Африки, где она вытеснила традиционный материал – папирус, в Испании и других странах Европы. В России бумага известна с 10 в. Машинное производство бумаги возникло в нач. 18 в. в Голландии, где был изготовлен первый размалывающий аппарат – ролл. В кон. 18 в. во Франции Н.-Л. Робертом был предложен способ механизированного отлива бумаги на непрерывно движущейся сетке. В дальнейшем к этому оборудованию были добавлены устройства для прессования и сушки, а также специальные прессы для уплотнения (каландры), намотки в рулоны; старые роллы заменили размалывающими аппаратами непрерывного действия. В качестве сырья начали применять появившиеся синтетические материалы, добавка которых к исходной бумажной массе улучшила прочностные качества бумаги.
В зависимости от назначения в состав бумаги вводятся различные наполнители: каолин (глина белого цвета, состоящая из минерала каолинита), тальк и другие минеральные вещества, придающие бумаге белизну, прочность, гладкость и другие физико-химические свойства, необходимые для печати: непрозрачность, хорошее восприятие краски, смачиваемость или влагостойкость. Кроме того, в бумагу вводят проклеивающие вещества (крахмал, смолы, клеи и др.), делающие бумагу непроницаемой для чернил, упрочняющие поверхностный слой, увеличивающие её плотность и т. п. В специальные виды бумаги добавляют красители, химические волокна. В зависимости от назначения бумага имеет различные показатели: масса листа площадью 1 мІ (4 – 250 г), толщина листа (4 – 400 мкм). Выпускается более 600 видов бумаги: для печати (типографская, офсетная, иллюстрационная, для глубокой печати, картографическая, мелованная, газетная, листовая, для обоев и др.); для письма (писчая, конвертная и т. п.); чертёжно-рисовальная (в т. ч. калька и ватман); электроизоляционная; папиросная; впитывающая (фильтровальная, промокательная и др.); для производства фибры, пергамента, санитарно-гигиенических изделий и т. п.; для аппаратов (телеграфная лента, перфокарточная и др.); светочувствительная (для изготовления фотобумаги и т. п.); переводная (копировальная и др.); обёрточная (мешочная, спичечная, бутылочная, парафинированная и т. п.); промышленно-техническая (патронная, наждачная, асбестовая и другого назначения).
Изготовляют бумагу на бумагоделательных машинах из бумажной массы – смеси размолотых и особым образом обработанных волокнистых материалов в воде с добавлением наполняющих, красящих и проклеивающих веществ. Основные части бумагоделательной машины – сеточная, прессовая, сушильная, каландр, накат. Сеточная часть имеет одну или несколько движущихся бесконечных сеток, на которые непрерывным потоком поступает бумажная масса, постепенно теряющая воду и распределяющаяся по сетке для формования. Дальнейшее обезвоживание и формование бумажного полотна происходит в прессовой части, а также при сушке (до необходимой влажности 5–7 %), которая осуществляется на расположенных в два яруса вращающихся горячих цилиндрах. Затем бумага охлаждается на холодных цилиндрах и поступает на каландр, после чего сматывается на накате в рулон. Бумагоделательная машина – сложный многофункциональный технологический агрегат, имеющий длину ок. 100 м, ширину – до 20 м и высоту отдельных частей – до 15 м. Производительность современных бумагоделательных машин 250–500 т/сут.
БУ́НА (полузапруда, поперечная дамба), гидротехническое сооружение, предназначенное для регулирования режима водного потока и защиты морского или речного берега от размыва. Для устройства бун применяют грунт, камень, бетон, фашины, габионы. Габион имеет вид заполненного камнем ящика из металлической сетки. Фашиной называют туго стянутую связку ивового хвороста в форме цилиндра. Буны сооружают перпендикулярно или под некоторым углом к берегу. Донные буны служат для предохранения от размыва оснований береговых сооружений (дамб, подпорных стенок).
БУРÁВ, сверло с режущей кромкой на одном конце и круглым отверстием (ушком) для ручки на другом. Используют для ручного сверления отверстий в древесине. Бурава подразделяют на цилиндрические, улиткообразные и ложечные. Цилиндрические бурава изготовляют длиной 500–600 мм для сверления отверстий диаметром 12–38 мм; улиткообразные – длиной 285–356 мм для отверстий 16–22 мм; ложечные – длиной 150–340 мм для отверстий 5—22 мм. Цилиндрические и улиткообразные бурава имеют заборный винт, благодаря которому они легко входят в древесину. Для сверления отверстий диаметром меньше 10 мм используют буравчик – круглый стальной стержень с режущей кромкой на одном конце; другой конец стержня изогнут и образует ручку.
Бурава:
а – цилиндрический винтообразный; б – улиткообразный; в – буравчик;
1 – ушко; 2 – рабочая часть; 3 – режущая кромка; 4 – заборный винт
«БУРÁН», орбитальный космический корабль многоразового использования. Выполнен по самолётной схеме типа «бесхвостка» с низко расположенным стреловидным крылом. Стартует «Буран» с помощью ракеты-носителя; спуск вне атмосферы происходит с использованием собственных ракетных двигателей в режиме торможения, в атмосфере и при посадке – по-«самолётному». Основное назначение: доставка сменных экипажей на орбитальные станции и возвращение их на Землю; выполнение научных исследований и экспериментов в автономном полёте; ремонт космических аппаратов на орбите; доставка на Землю результатов научной и технологической деятельности экипажей орбитальных станций. Корабль оснащён оборудованием и системами для стыковки на орбите с другими космическими аппаратами и комплексами. Его максимальная стартовая масса 105 т, в т. ч. 30 т полезного груза; длина 36.37 м, размах крыльев 23.92 м, высота на стоянке 16.35 м; экипаж 2—10 человек. 15 ноября 1988 г. состоялся космический полёт «Бурана» в автоматическом режиме без экипажа. Выполнив два витка вокруг Земли и завершив программу испытательного полёта, «Буран» успешно совершил посадку на аэродроме космодрома «Байконур».
«Буран»
БУРÉНИЕ, процесс образования горной выработки (преимущественно круглого сечения) путём разрушения горных пород с последующим удалением их из забоя. Бурение осуществляется гл. обр. механическим способом (бурильным долотом, резцом), реже термическим, гидравлическим, взрывным и другими способами. Породу можно разрушать либо только по внешнему контуру с сохранением в центре колонки (керна) – т. н. колонковое бурение, – либо по всему сечению (бескерновое бурение). Выработки могут иметь разный диаметр и соответственно разные названия: шпур, шурф, скважина, шахтный ствол (иногда называется просто шахтой). Глубина выработок – от десятков сантиметров до нескольких километров в зависимости от назначения выработки, вида полезного ископаемого, способа добычи. Шурфы (диаметром 15–30 мм) для закладки взрывчатого вещества бурят на глубину до 5 м. Шурфы (25–50 мм) для систем вентиляции, отведения вод и т. п. прокладывают на глубину до 25 м. Эксплуатационные скважины для добычи газа, нефти, подземных вод (75—800 мм) могут иметь глубину от нескольких метров до 10 км и более. Бурят также вентиляционные, водоотливные, разведочные и другие скважины. Шахтные стволы прокладывают в вертикальном и наклонном направлениях, часто за несколько проходов, образуя необходимый тоннель (до нескольких метров).
Бурильное долото
БУРИ́ЛЬНО-КРÁНОВАЯ МАШИ́НА, самоходная машина для бурения скважин при сооружении опор линий электропередачи (ЛЭП) и связи, опускания и установки в котлованы бетонных блоков под опоры ЛЭП, для строительства свайных фундаментов, ограждений и т. д. Буровой инструмент и крановое оборудование могут быть установлены как на базовый трактор на гусеничном ходу, так и на специально оборудованный колёсный автомобиль. В городах применяют небольшие бурильно-крановые машины, предназначенные для бурения ям и скважин под установку столбов, посадку деревьев и т. д. Их называют ямокопатели или ямобуры.
Бурильно-крановая машина
БУРОВÁЯ УСТАНÓВКА, комплекс машин и механизмов, предназначенных для бурения, крепления и по-следующего обслуживания буровых скважин и шахтных стволов. Буровые установки сооружают для разведки месторождений полезных ископаемых, на месте их добычи и эксплуатации, а также для проведения глубинных геологических исследований. Для работы установки либо доставляют в разобранном виде (отдельно механизмы, конструкции и т. п.) и собирают на месте, либо транспортируют уже в собранном виде по рельсовому пути на катках, на барже (т. н. самоходные установки). В состав буровой установки входит буровая вышка (от 10 до 60 м), монтируемая обычно из металлических конструкций, которая служит для размещения оборудования, спуска и подъёма бурового инструмента. На установке работают лебёдка и другие подъёмные механизмы, насосы, компрессор и пр. Для питания машин и механизмов энергией предусматривается автономное энергоснабжение от двигателей внутреннего сгорания или дизель-генераторных агрегатов либо имеются распределительные устройства для подключения к централизованным системам электроснабжения. На буровой установке осуществляются сложные технологические процессы, управление которыми и согласованная работа всех её частей обеспечивается автоматизированной системой управления.
БЫ́СТРЫЙ РЕÁКТОР, см. в ст. Ядерный реактор.
БЬЕФ, часть водоёма, реки, канала, расположенная по течению выше водонапорного сооружения (плотины, шлюза), т. н. верхний бьеф, или ниже него – нижний бьеф. Бьеф, образованный двумя или несколькими последовательно расположенными водоподпорными сооружениями и находящийся на водораздельном участке водной системы или водотока, называется раздельным.
В
Буксиры отличаются малой длиной, что обеспечивает необходимые маневровые качества, высокими тяговыми показателями, большой остойчивостью. Мощность крупных океанских буксиров достигает 9200 кВт, а мощность буксиров-спасателей – 16 000 кВт, мощность портовых буксиров доходит до 2600 кВт. Скорость океанских и морских буксиров составляет 12–18 узлов (22.2—33 км/ч), портовых и рейдовых буксиров – 10–12 узлов (18.5—22.2 км/ч).
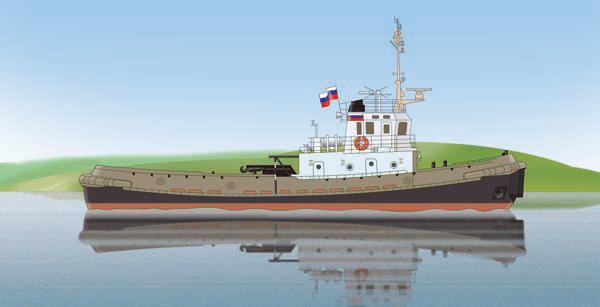
Буксирные суда оснащаются буксирным устройством, обеспечивающим буксировку несамоходных судов, а также судов, потерявших способность двигаться своим ходом. Основными конструктивными узлами буксирного устройства являются буксирный гак, буксирная лебёдка, на барабан которой наматывается буксирный канат, и буксирные арки, направляющие и ограничивающие движение буксирного каната. Буксирная лебёдка позволяет изменять длину буксирного каната, обеспечивая на извилистом судовом ходу при малой длине каната требуемую управляемость, а на прямом судовом ходу – уменьшать сопротивление состава за счёт увеличения длины буксирного каната. Буксирный гак используется при отказе буксирной лебёдки. Буксиры-толкачи, помимо буксирного устройства, оборудуются сцепным или автосцепным устройством, обеспечивающим жёсткую сцепку носовой части судна с кормовой частью состава. Толкачи оборудуются только сцепным (автосцепным) устройством. Конструкция сцепных и автосцепных устройств разнообразна. В речных и озёрных условиях отечественные буксиры-толкачи и толкачи оборудуются однозамковыми или двухзамковыми автосцепами, которые обеспечивают сцепку замков клешневого типа, установленных на одном судне, с вертикальными рельсами, укреплёнными на торцевой части (транце) другого судна. На морских баржебуксирных составах сцепка толкача и баржи производится с помощью мощных гидравлических сцепов, обеспечивающих возможность взаимных наклонений толкача и баржи относительно общей горизонтальной оси. На портовых буксирах применяются вакуумные сцепы. Эти буксиры оснащаются также манипуляторами для захвата буксирного каната. Для обеспечения высокой маневренности портовые буксиры оснащаются винторулевыми колонками, меняющими направление силы упора винта по желанию судоводителя. Буксиры-спасатели оснащаются разнообразным оборудованием для оказания помощи терпящим бедствие судам – буксировки судов, потерявших ход, снятия с мели, откачки воды, тушения пожаров, спасения людей. Все буксиры-толкачи и толкачи оборудуются мощным кормовым якорным устройством, обеспечивающим удержание на кормовом якоре толкаемого состава на течении. Мощность речных буксиров-толкачей и толкачей связана с размером составов, которые, в свою очередь, определяются габаритами водного пути. Т. к. эффективность перевозок возрастает при увеличении грузоподъёмности составов, на крупных реках используют мощные буксиры-толкачи. Мощность наиболее крупных отечественных толкачей достигает 2–3 тыс. кВт. На Миссисипи, где возможно применение особо крупных составов, мощность толкачей достигает 9 тыс. кВт.
БУЛЬДÓЗЕР, землеройная машина (а также съёмное землеройное оборудование на тракторе или тягаче), предназначенная для разработки и перемещения грунта, щебня, засыпки котлованов и траншей, расчистки снега на дорогах, планировки площадок и т. д. С помощью бульдозера можно перемещать грунт на небольшие расстояния (не более 80—100 м). Рабочий орган бульдозера – мощный отвал – может быть поворотным или неповоротным. Бульдозеры многоцелевого назначения наряду с выполнением традиционных работ используются для разработки и засыпки траншей, каналов, скважин, проведения земляных работ на мёрзлых грунтах, в погрузочно-разгрузочных работах. На бульдозеры приходится более 40 % всех объёмов земляных работ. Это объясняется высокой производительностью, манёвренностью, универсальностью и простотой конструкции рабочего оборудования.
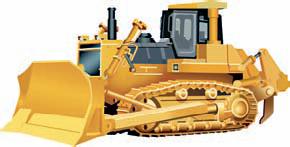
БУМÁГА, материал из растительных волокон, беспорядочно распределённых в тонкий лист и связанных между собой поверхностными силами сцепления. Бумагу производят гл. обр. из волокон древесины после соответствующей их обработки – размола, соединения с различными добавками (наполнителями), красителями и т. п. Впервые бумага была получена Цай Лунем во 2 в. в Китае путём осаждения водной суспензии свежих растительных волокон на сетке. В 6 в. этот способ, долго сохранявшийся в секрете, был вывезен в Японию, затем в страны Азии (6–8 вв.), где бумагу изготовляли из пенькового и льняного тряпья. Позднее таким образом бумагу стали вырабатывать в странах Северной Африки, где она вытеснила традиционный материал – папирус, в Испании и других странах Европы. В России бумага известна с 10 в. Машинное производство бумаги возникло в нач. 18 в. в Голландии, где был изготовлен первый размалывающий аппарат – ролл. В кон. 18 в. во Франции Н.-Л. Робертом был предложен способ механизированного отлива бумаги на непрерывно движущейся сетке. В дальнейшем к этому оборудованию были добавлены устройства для прессования и сушки, а также специальные прессы для уплотнения (каландры), намотки в рулоны; старые роллы заменили размалывающими аппаратами непрерывного действия. В качестве сырья начали применять появившиеся синтетические материалы, добавка которых к исходной бумажной массе улучшила прочностные качества бумаги.
В зависимости от назначения в состав бумаги вводятся различные наполнители: каолин (глина белого цвета, состоящая из минерала каолинита), тальк и другие минеральные вещества, придающие бумаге белизну, прочность, гладкость и другие физико-химические свойства, необходимые для печати: непрозрачность, хорошее восприятие краски, смачиваемость или влагостойкость. Кроме того, в бумагу вводят проклеивающие вещества (крахмал, смолы, клеи и др.), делающие бумагу непроницаемой для чернил, упрочняющие поверхностный слой, увеличивающие её плотность и т. п. В специальные виды бумаги добавляют красители, химические волокна. В зависимости от назначения бумага имеет различные показатели: масса листа площадью 1 мІ (4 – 250 г), толщина листа (4 – 400 мкм). Выпускается более 600 видов бумаги: для печати (типографская, офсетная, иллюстрационная, для глубокой печати, картографическая, мелованная, газетная, листовая, для обоев и др.); для письма (писчая, конвертная и т. п.); чертёжно-рисовальная (в т. ч. калька и ватман); электроизоляционная; папиросная; впитывающая (фильтровальная, промокательная и др.); для производства фибры, пергамента, санитарно-гигиенических изделий и т. п.; для аппаратов (телеграфная лента, перфокарточная и др.); светочувствительная (для изготовления фотобумаги и т. п.); переводная (копировальная и др.); обёрточная (мешочная, спичечная, бутылочная, парафинированная и т. п.); промышленно-техническая (патронная, наждачная, асбестовая и другого назначения).
Изготовляют бумагу на бумагоделательных машинах из бумажной массы – смеси размолотых и особым образом обработанных волокнистых материалов в воде с добавлением наполняющих, красящих и проклеивающих веществ. Основные части бумагоделательной машины – сеточная, прессовая, сушильная, каландр, накат. Сеточная часть имеет одну или несколько движущихся бесконечных сеток, на которые непрерывным потоком поступает бумажная масса, постепенно теряющая воду и распределяющаяся по сетке для формования. Дальнейшее обезвоживание и формование бумажного полотна происходит в прессовой части, а также при сушке (до необходимой влажности 5–7 %), которая осуществляется на расположенных в два яруса вращающихся горячих цилиндрах. Затем бумага охлаждается на холодных цилиндрах и поступает на каландр, после чего сматывается на накате в рулон. Бумагоделательная машина – сложный многофункциональный технологический агрегат, имеющий длину ок. 100 м, ширину – до 20 м и высоту отдельных частей – до 15 м. Производительность современных бумагоделательных машин 250–500 т/сут.
БУ́НА (полузапруда, поперечная дамба), гидротехническое сооружение, предназначенное для регулирования режима водного потока и защиты морского или речного берега от размыва. Для устройства бун применяют грунт, камень, бетон, фашины, габионы. Габион имеет вид заполненного камнем ящика из металлической сетки. Фашиной называют туго стянутую связку ивового хвороста в форме цилиндра. Буны сооружают перпендикулярно или под некоторым углом к берегу. Донные буны служат для предохранения от размыва оснований береговых сооружений (дамб, подпорных стенок).
БУРÁВ, сверло с режущей кромкой на одном конце и круглым отверстием (ушком) для ручки на другом. Используют для ручного сверления отверстий в древесине. Бурава подразделяют на цилиндрические, улиткообразные и ложечные. Цилиндрические бурава изготовляют длиной 500–600 мм для сверления отверстий диаметром 12–38 мм; улиткообразные – длиной 285–356 мм для отверстий 16–22 мм; ложечные – длиной 150–340 мм для отверстий 5—22 мм. Цилиндрические и улиткообразные бурава имеют заборный винт, благодаря которому они легко входят в древесину. Для сверления отверстий диаметром меньше 10 мм используют буравчик – круглый стальной стержень с режущей кромкой на одном конце; другой конец стержня изогнут и образует ручку.
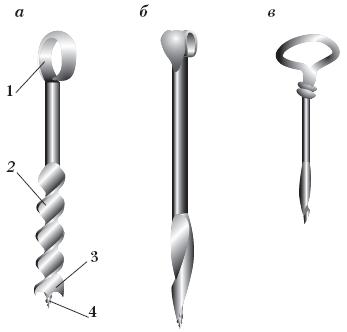
а – цилиндрический винтообразный; б – улиткообразный; в – буравчик;
1 – ушко; 2 – рабочая часть; 3 – режущая кромка; 4 – заборный винт
«БУРÁН», орбитальный космический корабль многоразового использования. Выполнен по самолётной схеме типа «бесхвостка» с низко расположенным стреловидным крылом. Стартует «Буран» с помощью ракеты-носителя; спуск вне атмосферы происходит с использованием собственных ракетных двигателей в режиме торможения, в атмосфере и при посадке – по-«самолётному». Основное назначение: доставка сменных экипажей на орбитальные станции и возвращение их на Землю; выполнение научных исследований и экспериментов в автономном полёте; ремонт космических аппаратов на орбите; доставка на Землю результатов научной и технологической деятельности экипажей орбитальных станций. Корабль оснащён оборудованием и системами для стыковки на орбите с другими космическими аппаратами и комплексами. Его максимальная стартовая масса 105 т, в т. ч. 30 т полезного груза; длина 36.37 м, размах крыльев 23.92 м, высота на стоянке 16.35 м; экипаж 2—10 человек. 15 ноября 1988 г. состоялся космический полёт «Бурана» в автоматическом режиме без экипажа. Выполнив два витка вокруг Земли и завершив программу испытательного полёта, «Буран» успешно совершил посадку на аэродроме космодрома «Байконур».
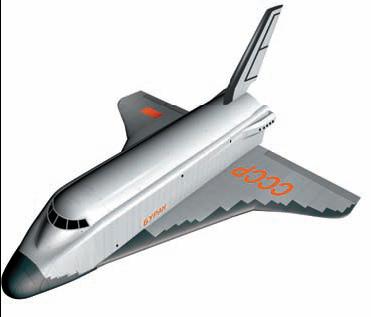
БУРÉНИЕ, процесс образования горной выработки (преимущественно круглого сечения) путём разрушения горных пород с последующим удалением их из забоя. Бурение осуществляется гл. обр. механическим способом (бурильным долотом, резцом), реже термическим, гидравлическим, взрывным и другими способами. Породу можно разрушать либо только по внешнему контуру с сохранением в центре колонки (керна) – т. н. колонковое бурение, – либо по всему сечению (бескерновое бурение). Выработки могут иметь разный диаметр и соответственно разные названия: шпур, шурф, скважина, шахтный ствол (иногда называется просто шахтой). Глубина выработок – от десятков сантиметров до нескольких километров в зависимости от назначения выработки, вида полезного ископаемого, способа добычи. Шурфы (диаметром 15–30 мм) для закладки взрывчатого вещества бурят на глубину до 5 м. Шурфы (25–50 мм) для систем вентиляции, отведения вод и т. п. прокладывают на глубину до 25 м. Эксплуатационные скважины для добычи газа, нефти, подземных вод (75—800 мм) могут иметь глубину от нескольких метров до 10 км и более. Бурят также вентиляционные, водоотливные, разведочные и другие скважины. Шахтные стволы прокладывают в вертикальном и наклонном направлениях, часто за несколько проходов, образуя необходимый тоннель (до нескольких метров).
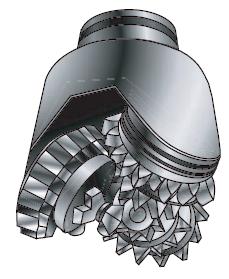
БУРИ́ЛЬНО-КРÁНОВАЯ МАШИ́НА, самоходная машина для бурения скважин при сооружении опор линий электропередачи (ЛЭП) и связи, опускания и установки в котлованы бетонных блоков под опоры ЛЭП, для строительства свайных фундаментов, ограждений и т. д. Буровой инструмент и крановое оборудование могут быть установлены как на базовый трактор на гусеничном ходу, так и на специально оборудованный колёсный автомобиль. В городах применяют небольшие бурильно-крановые машины, предназначенные для бурения ям и скважин под установку столбов, посадку деревьев и т. д. Их называют ямокопатели или ямобуры.
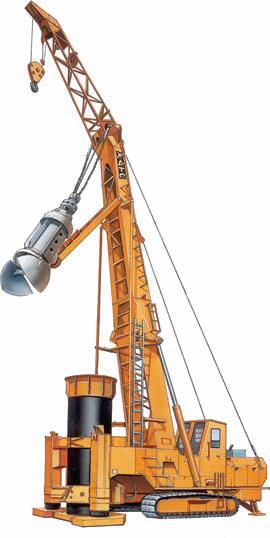
БУРОВÁЯ УСТАНÓВКА, комплекс машин и механизмов, предназначенных для бурения, крепления и по-следующего обслуживания буровых скважин и шахтных стволов. Буровые установки сооружают для разведки месторождений полезных ископаемых, на месте их добычи и эксплуатации, а также для проведения глубинных геологических исследований. Для работы установки либо доставляют в разобранном виде (отдельно механизмы, конструкции и т. п.) и собирают на месте, либо транспортируют уже в собранном виде по рельсовому пути на катках, на барже (т. н. самоходные установки). В состав буровой установки входит буровая вышка (от 10 до 60 м), монтируемая обычно из металлических конструкций, которая служит для размещения оборудования, спуска и подъёма бурового инструмента. На установке работают лебёдка и другие подъёмные механизмы, насосы, компрессор и пр. Для питания машин и механизмов энергией предусматривается автономное энергоснабжение от двигателей внутреннего сгорания или дизель-генераторных агрегатов либо имеются распределительные устройства для подключения к централизованным системам электроснабжения. На буровой установке осуществляются сложные технологические процессы, управление которыми и согласованная работа всех её частей обеспечивается автоматизированной системой управления.
БЫ́СТРЫЙ РЕÁКТОР, см. в ст. Ядерный реактор.
БЬЕФ, часть водоёма, реки, канала, расположенная по течению выше водонапорного сооружения (плотины, шлюза), т. н. верхний бьеф, или ниже него – нижний бьеф. Бьеф, образованный двумя или несколькими последовательно расположенными водоподпорными сооружениями и находящийся на водораздельном участке водной системы или водотока, называется раздельным.
В
ВАГÓН, происходит от английского waggon; так называлась небольшая повозка в виде ящика на колёсах, которая передвигалась по деревянным желобам-рельсам на шахтах и рудниках в Средние века.
Вагоны для пассажиров впервые появились в кон. 1780-х гг. в Англии с открытием первой конно-чугунной дороги близ Лондона. В России вагонетки с канатной, а позднее с конной тягой использовались на рудничных и внутризаводских рельсовых дорогах на Алтае (с 1764 г.), на Александровском заводе в Петрозаводске (с 1788 г.), на Змеиногорском руднике (с 1810 г.). Первые пассажирские вагоны были изготовлены для Царскосельской железной дороги, открытой в 1837 г. В зависимости от конструкции и удобств для пассажиров они именовались каретами, шарабанами, дилижансами. Первоначально эти экипажи не входили в состав поезда, а устанавливались на специальных платформах, из которых составлялись поезда. В те же поезда входили платформы и открытые вагоны для грузов. В 1846 г. на Александровском заводе начали выпускать вагоны для железной дороги между Санкт-Петербургом и Москвой. Основные узлы этих вагонов (кузов, рама, колёсные пары, ходовые тележки, буксы, рессоры, тормоза), а также их внутренняя планировка сохранились до наших дней, совершенствуясь со временем в соответствии с развитием производства и появлением новых материалов и технологий.
Первые грузовые (товарные) вагоны – крытые и открытые (полувагоны, платформы) – в России были построены в 1855 г., с 1862 г. стали выпускать вагоны-ледники, с 1868 г. – вагоны с опрокидывающимся кузовом (вагон-самосвал, или думпкар), а с 1872 г. – вагоны-цистерны (для перевозки гл. обр. нефти, а также молока, живой рыбы, сыпучих продуктов и т. п.). Вагоны нового поколения, созданные в сер. 20 в., могли перевозить 50–60 т груза, вместимость кузова универсальных крытых вагонов достигала 120 мі. Выпускаются цельнометаллические полувагоны – основной тип грузового вагона, в котором можно перевозить грузы широкого ассортимента; платформы с металлическими бортами для сыпучих грузов; рефрижераторные вагоны; саморазгружающиеся бункерные вагоны-хопперы и хоппер-дозаторы, специализированные вагоны для грузов, требующих особых условий перевозки (для горячего агломерата, шлаков, чугуновозы миксерного типа, цистерны для кислот, сжиженных газов и пр.).
Грузовые вагоны
Первые пассажирские вагоны в России строились по образцу заграничных, поступавших из Германии, Бельгии и других стран. В 1850-е гг. были созданы отечественные пассажирские вагоны, отличающиеся внутренним оборудованием и отделкой; в 1866 г. в скорых поездах Санкт-Петербург – Москва введены впервые спальные вагоны (в США такие вагоны называют пульманами). Особое внимание уделялось отоплению вагонов с учётом климатических условий страны. В 1-й пол. 20 в. отечественное вагоностроение освоило выпуск купейных, жёстких, мягких, багажных, почтовых, а также вагонов для пригородного сообщения. К кон. 20 в. на железных дорогах страны использовались пассажирские вагоны практически всех типов: несамоходные с локомотивной тягой и самоходные (моторвагонные секции) для электропоездов и метрополитена; спальные, купейные, плацкартные и только с местами для сидения (креслами самолётного типа); специализированные вагоны для монорельсовых дорог, фуникулёра, трамвая и высокоскоростного железнодорожного транспорта.
Пассажирские вагоны
ВАГОНООПРОКИ́ДЫВАТЕЛЬ, установка для поворота (опрокидывания) вагона (иногда двух) и самопроизвольной разгрузки сыпучих грузов (зерно, руда, уголь, песок и т. п.). Вагоноопрокидыватели оборудуются системами автоматизации, виброустройствами для разрыхления слежавшихся и смёрзшихся грузов или удаления их остатков из вагона. Выгрузка может осуществляться через торцовые стенки вагона или через боковые (вагоноопрокидыватели роторного типа). Вагоноопрокидыватели устанавливают на грузовых площадках крупных металлургических, химических комбинатов, на электростанциях, предприятиях машиностроения и строительной индустрии, в морских и речных портах и т. п. В России первое такое сооружение с выгрузкой из торцовых дверей вагона построено в кон. 19 в. в Мариупольском порту (с 1991 г. на Украине).
Вагоноопрокидыватель
ВАГРÁНКА, печь, применяемая в литейном производстве для плавки чугуна. Прототипом вагранки послужили доменные печи, в которых переплавляли литейный чугун и лом до сер. 18 в. Появление вагранки способствовало выделению чугунолитейных цехов в особое производство. Вагранка имеет вертикальную шахту, в нижней части которой расположен горн, служащий для накопления жидкого чугуна. Средняя часть шахты полностью загружается шихтовыми материалами – смесью металла, топлива (кокса) и флюсов (специальных добавок), обеспечивающих жидкотекучесть и другие свойства расплава. Из горна чугун перетекает в копильник, откуда выпускается в разливочный ковш через нижнюю лётку (специальное отверстие, заделываемое после окончания плавки и выпуска металла). Металлическая шихта состоит из получаемого в домне литейного чугуна (в чушках), чугунного лома, возврата металла литейного цеха (брак отливок, лом литников, прибылей и т. п.), стальных отходов металлургического производства (т. н. скрапа), ферросплавов для улучшения свойств (легирования) получаемого чугуна. Для ускорения розжига печи и интенсификации плавки металла в печь подают обогащённый кислородом воздух. Производительность вагранки зависит от её размеров, состава шихты, вида и расхода топлива.
Схема вагранки:
1 – жёлоб для выпуска чугуна из копильника; 2 – лётка; 3 – копильник; 4 – фурмы для дутья; 5 – воздушный коллектор; 6 – шахта; 7 – загрузочное окно; 8 – искроуловитель; 9 – труба; 10 – загрузочная бадья; 11 – разливочный ковш
ВАКУУММÉТР (вакуумный манометр), прибор для измерения давления разреженного газа. Давление (разрежение) в вакуумметре определяется с помощью какой-либо физической величины, связанной с давлением (напр., деформации чувствительного элемента, вязкости, теплопроводности газа). Основные части вакуумметра: измерительный преобразователь давления в физическую величину (напр., в перемещение или электрический сигнал) и измерительный блок, непосредственно измеряющий этот сигнал. Результат измерения определяют по отсчётному устройству в виде шкалы, проградуированной в единицах давления (разрежения). В зависимости от устройства и принципа действия вакуумметры разделяются на жидкостные, механические, тепловые и др. В жидкостных вакуумметрах преобразователем давления служит столб жидкости (ртути или масла). Газ давит на жидкость, находящуюся в U-образной трубке. В одном из колен находится газ при измеряемом давлении Рх, а в другом – при известном (опорном) давлении Роп. Жидкостные вакуумметры бывают с закрытым и открытым коленом и др. Их недостатком является небольшой диапазон измерения давлений с нижним пределом до 10–3 мм рт. ст. В механических вакуумметрах давление газа воспринимает упругий чувствительный элемент – сильфон или мембрана, деформация которых передаётся стрелочному указателю. В мембранном вакуумметре мембрана герметически отделяет вакуумную систему от объёма, в котором поддерживается постоянное опорное давление. Деформация мембраны передаётся стрелке, передвигающейся по шкале. При измерении малых давлений для повышения чувствительности мембрану соединяют с электрическим датчиком. Принцип действия тепловых вакуумметров основан на зависимости теплопроводности разреженных газов от давления. Датчиком прибора служит герметичный баллон с проволокой, нагреваемой электрическим током. При изменении давления в системе изменяются отвод тепла от нити датчика и, следовательно, её температура (при постоянной мощности). Различают термопарные вакуумметры, температура нити которых измеряется присоединённой к ней термопарой, и теплоэлектрические вакуумметры сопротивления, температуру нити которых определяют по её электрическому сопротивлению.
ВÁКУУМНАЯ МЕТАЛЛУ́РГИ́Я, металлургические процессы, при проведении которых используется вакуумное оборудование. Идея помещения расплавленного металла в вакуум для удаления из него газов высказывалась неоднократно ещё в 19 в., однако тогда невозможно было построить необходимое оборудование. Быстрое развитие вакуумной металлургии началось во 2-й пол. 20 в. В вакуумной металлургии различают операцию вакуумной обработки выплавленного металла и собственно процесс плавки в вакууме. Выплавленный обычным способом металл подвергают вакуумной обработке во время выпуска из печи или в разливочном ковше и таким образом очищают его от газов – дегазируют. Во втором случае и плавку, и разливку металла проводят в условиях вакуума. В вакуумной металлургии применяются индукционные печи, дуговые и электронно-лучевые печи. Электронно-лучевой способ вакуумной плавки обладает рядом преимуществ по сравнению с другими: плавка проводится в медном тигле, охлаждаемом водой, что позволяет избежать реакций расплава со стенками тигля. В электронно-лучевой печи можно переплавлять все без исключения металлы и сплавы, в т. ч. тугоплавкие и быстро окисляющиеся.
ВÁКУУМНЫЙ МАНÓМЕТР, то же, что вакуумметр.
ВÁКУУМНЫЙ НАСÓС, устройство, предназначенное для удаления (откачки) газов или паров из замкнутого объёма (системы) с целью получения в нём вакуума. Основные характеристики вакуумных насосов: предельное давление (остаточное давление или предельный вакуум); быстрота откачки – объём газа, откачиваемый при данном давлении в единицу времени. Различают следующие вакуумные насосы: механические, пароструйные, сорбционные, криогенные. В свою очередь, механические вакуумные насосы делятся на вращательные, двухроторные и турбомолекулярные. Среди вращательных вакуумных насосов наибольшее распространение получил пластинчато-роторный насос с масляным уплотнением. Всасывание и выталкивание газа в таком насосе осуществляется при изменении объёма ячеек, образованных эксцентрично расположенным ротором, в прорезях которого помещены подвижные пластины. Уплотнение зазоров между деталями насоса обеспечивается маслом. Двухроторный вакуумный насос состоит из двух фигурных роторов, которые при вращении создают в камере насоса направленное движение газа. Работа турбомолекулярного вакуумного насоса основана на использовании движения молекул газа в направлении его откачки при вращении ротора, состоящего из дисков. Принцип действия пароструйных насосов основан на захвате откачиваемого газа струёй пара.
Вагоны для пассажиров впервые появились в кон. 1780-х гг. в Англии с открытием первой конно-чугунной дороги близ Лондона. В России вагонетки с канатной, а позднее с конной тягой использовались на рудничных и внутризаводских рельсовых дорогах на Алтае (с 1764 г.), на Александровском заводе в Петрозаводске (с 1788 г.), на Змеиногорском руднике (с 1810 г.). Первые пассажирские вагоны были изготовлены для Царскосельской железной дороги, открытой в 1837 г. В зависимости от конструкции и удобств для пассажиров они именовались каретами, шарабанами, дилижансами. Первоначально эти экипажи не входили в состав поезда, а устанавливались на специальных платформах, из которых составлялись поезда. В те же поезда входили платформы и открытые вагоны для грузов. В 1846 г. на Александровском заводе начали выпускать вагоны для железной дороги между Санкт-Петербургом и Москвой. Основные узлы этих вагонов (кузов, рама, колёсные пары, ходовые тележки, буксы, рессоры, тормоза), а также их внутренняя планировка сохранились до наших дней, совершенствуясь со временем в соответствии с развитием производства и появлением новых материалов и технологий.
Первые грузовые (товарные) вагоны – крытые и открытые (полувагоны, платформы) – в России были построены в 1855 г., с 1862 г. стали выпускать вагоны-ледники, с 1868 г. – вагоны с опрокидывающимся кузовом (вагон-самосвал, или думпкар), а с 1872 г. – вагоны-цистерны (для перевозки гл. обр. нефти, а также молока, живой рыбы, сыпучих продуктов и т. п.). Вагоны нового поколения, созданные в сер. 20 в., могли перевозить 50–60 т груза, вместимость кузова универсальных крытых вагонов достигала 120 мі. Выпускаются цельнометаллические полувагоны – основной тип грузового вагона, в котором можно перевозить грузы широкого ассортимента; платформы с металлическими бортами для сыпучих грузов; рефрижераторные вагоны; саморазгружающиеся бункерные вагоны-хопперы и хоппер-дозаторы, специализированные вагоны для грузов, требующих особых условий перевозки (для горячего агломерата, шлаков, чугуновозы миксерного типа, цистерны для кислот, сжиженных газов и пр.).

Первые пассажирские вагоны в России строились по образцу заграничных, поступавших из Германии, Бельгии и других стран. В 1850-е гг. были созданы отечественные пассажирские вагоны, отличающиеся внутренним оборудованием и отделкой; в 1866 г. в скорых поездах Санкт-Петербург – Москва введены впервые спальные вагоны (в США такие вагоны называют пульманами). Особое внимание уделялось отоплению вагонов с учётом климатических условий страны. В 1-й пол. 20 в. отечественное вагоностроение освоило выпуск купейных, жёстких, мягких, багажных, почтовых, а также вагонов для пригородного сообщения. К кон. 20 в. на железных дорогах страны использовались пассажирские вагоны практически всех типов: несамоходные с локомотивной тягой и самоходные (моторвагонные секции) для электропоездов и метрополитена; спальные, купейные, плацкартные и только с местами для сидения (креслами самолётного типа); специализированные вагоны для монорельсовых дорог, фуникулёра, трамвая и высокоскоростного железнодорожного транспорта.

ВАГОНООПРОКИ́ДЫВАТЕЛЬ, установка для поворота (опрокидывания) вагона (иногда двух) и самопроизвольной разгрузки сыпучих грузов (зерно, руда, уголь, песок и т. п.). Вагоноопрокидыватели оборудуются системами автоматизации, виброустройствами для разрыхления слежавшихся и смёрзшихся грузов или удаления их остатков из вагона. Выгрузка может осуществляться через торцовые стенки вагона или через боковые (вагоноопрокидыватели роторного типа). Вагоноопрокидыватели устанавливают на грузовых площадках крупных металлургических, химических комбинатов, на электростанциях, предприятиях машиностроения и строительной индустрии, в морских и речных портах и т. п. В России первое такое сооружение с выгрузкой из торцовых дверей вагона построено в кон. 19 в. в Мариупольском порту (с 1991 г. на Украине).
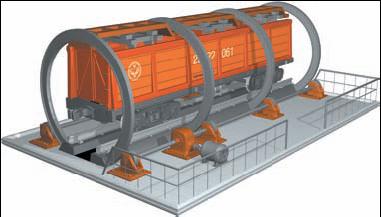
ВАГРÁНКА, печь, применяемая в литейном производстве для плавки чугуна. Прототипом вагранки послужили доменные печи, в которых переплавляли литейный чугун и лом до сер. 18 в. Появление вагранки способствовало выделению чугунолитейных цехов в особое производство. Вагранка имеет вертикальную шахту, в нижней части которой расположен горн, служащий для накопления жидкого чугуна. Средняя часть шахты полностью загружается шихтовыми материалами – смесью металла, топлива (кокса) и флюсов (специальных добавок), обеспечивающих жидкотекучесть и другие свойства расплава. Из горна чугун перетекает в копильник, откуда выпускается в разливочный ковш через нижнюю лётку (специальное отверстие, заделываемое после окончания плавки и выпуска металла). Металлическая шихта состоит из получаемого в домне литейного чугуна (в чушках), чугунного лома, возврата металла литейного цеха (брак отливок, лом литников, прибылей и т. п.), стальных отходов металлургического производства (т. н. скрапа), ферросплавов для улучшения свойств (легирования) получаемого чугуна. Для ускорения розжига печи и интенсификации плавки металла в печь подают обогащённый кислородом воздух. Производительность вагранки зависит от её размеров, состава шихты, вида и расхода топлива.
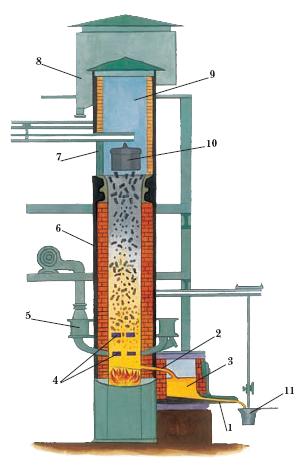
1 – жёлоб для выпуска чугуна из копильника; 2 – лётка; 3 – копильник; 4 – фурмы для дутья; 5 – воздушный коллектор; 6 – шахта; 7 – загрузочное окно; 8 – искроуловитель; 9 – труба; 10 – загрузочная бадья; 11 – разливочный ковш
ВАКУУММÉТР (вакуумный манометр), прибор для измерения давления разреженного газа. Давление (разрежение) в вакуумметре определяется с помощью какой-либо физической величины, связанной с давлением (напр., деформации чувствительного элемента, вязкости, теплопроводности газа). Основные части вакуумметра: измерительный преобразователь давления в физическую величину (напр., в перемещение или электрический сигнал) и измерительный блок, непосредственно измеряющий этот сигнал. Результат измерения определяют по отсчётному устройству в виде шкалы, проградуированной в единицах давления (разрежения). В зависимости от устройства и принципа действия вакуумметры разделяются на жидкостные, механические, тепловые и др. В жидкостных вакуумметрах преобразователем давления служит столб жидкости (ртути или масла). Газ давит на жидкость, находящуюся в U-образной трубке. В одном из колен находится газ при измеряемом давлении Рх, а в другом – при известном (опорном) давлении Роп. Жидкостные вакуумметры бывают с закрытым и открытым коленом и др. Их недостатком является небольшой диапазон измерения давлений с нижним пределом до 10–3 мм рт. ст. В механических вакуумметрах давление газа воспринимает упругий чувствительный элемент – сильфон или мембрана, деформация которых передаётся стрелочному указателю. В мембранном вакуумметре мембрана герметически отделяет вакуумную систему от объёма, в котором поддерживается постоянное опорное давление. Деформация мембраны передаётся стрелке, передвигающейся по шкале. При измерении малых давлений для повышения чувствительности мембрану соединяют с электрическим датчиком. Принцип действия тепловых вакуумметров основан на зависимости теплопроводности разреженных газов от давления. Датчиком прибора служит герметичный баллон с проволокой, нагреваемой электрическим током. При изменении давления в системе изменяются отвод тепла от нити датчика и, следовательно, её температура (при постоянной мощности). Различают термопарные вакуумметры, температура нити которых измеряется присоединённой к ней термопарой, и теплоэлектрические вакуумметры сопротивления, температуру нити которых определяют по её электрическому сопротивлению.
ВÁКУУМНАЯ МЕТАЛЛУ́РГИ́Я, металлургические процессы, при проведении которых используется вакуумное оборудование. Идея помещения расплавленного металла в вакуум для удаления из него газов высказывалась неоднократно ещё в 19 в., однако тогда невозможно было построить необходимое оборудование. Быстрое развитие вакуумной металлургии началось во 2-й пол. 20 в. В вакуумной металлургии различают операцию вакуумной обработки выплавленного металла и собственно процесс плавки в вакууме. Выплавленный обычным способом металл подвергают вакуумной обработке во время выпуска из печи или в разливочном ковше и таким образом очищают его от газов – дегазируют. Во втором случае и плавку, и разливку металла проводят в условиях вакуума. В вакуумной металлургии применяются индукционные печи, дуговые и электронно-лучевые печи. Электронно-лучевой способ вакуумной плавки обладает рядом преимуществ по сравнению с другими: плавка проводится в медном тигле, охлаждаемом водой, что позволяет избежать реакций расплава со стенками тигля. В электронно-лучевой печи можно переплавлять все без исключения металлы и сплавы, в т. ч. тугоплавкие и быстро окисляющиеся.
ВÁКУУМНЫЙ МАНÓМЕТР, то же, что вакуумметр.
ВÁКУУМНЫЙ НАСÓС, устройство, предназначенное для удаления (откачки) газов или паров из замкнутого объёма (системы) с целью получения в нём вакуума. Основные характеристики вакуумных насосов: предельное давление (остаточное давление или предельный вакуум); быстрота откачки – объём газа, откачиваемый при данном давлении в единицу времени. Различают следующие вакуумные насосы: механические, пароструйные, сорбционные, криогенные. В свою очередь, механические вакуумные насосы делятся на вращательные, двухроторные и турбомолекулярные. Среди вращательных вакуумных насосов наибольшее распространение получил пластинчато-роторный насос с масляным уплотнением. Всасывание и выталкивание газа в таком насосе осуществляется при изменении объёма ячеек, образованных эксцентрично расположенным ротором, в прорезях которого помещены подвижные пластины. Уплотнение зазоров между деталями насоса обеспечивается маслом. Двухроторный вакуумный насос состоит из двух фигурных роторов, которые при вращении создают в камере насоса направленное движение газа. Работа турбомолекулярного вакуумного насоса основана на использовании движения молекул газа в направлении его откачки при вращении ротора, состоящего из дисков. Принцип действия пароструйных насосов основан на захвате откачиваемого газа струёй пара.