Постоянно рассчитываемым параметром системы «минимум – максимум» является размер заказа. Как и в предыдущих системах управления запасами, его вычисление основывается на прогнозируемом уровне потребления до момента поступления заказа на склад организации.
Основы проектирования эффективной логистической системы управления запасами.Основные системы управления запасами – с размером заказов и фиксированным интервалом времени между заказами, а также прочие системы управления запасами – с установленной периодичностью пополнения запасов до постоянного уровня и система «минимум – максимум» разработаны для условий, когда отсутствуют отклонения от запланированных параметров поставки и потребления. Этими параметрами являются:
• размер заказа;
• интервал времени между заказами;
• время поставки;
• возможная задержка поставки;
• ожидаемое дневное потребление;
• прогнозируемое потребление до момента поставки. Непрерывное обеспечение потребности в каком-либо виде материального ресурса связано с определенными трудностями. Прежде всего это возможность появления различных отклонений в значениях перечисленных выше показателей как со стороны потребителя запаса, так и со стороны исполнителя заказа. Кроме того, вполне вероятны ошибки исполнителей, которые приводят к нарушению нормального функционирования системы управления запасами.
Практически возможны следующие отклонения запланированных и фактических показателей:
• изменение интенсивности потребления в ту или другую сторону;
• поставка незапланированного объема заказа;
• ошибки учета фактического запаса, ведущие к неправильному определению размера заказа.
Довольно часто имеют место многообразные сочетания возмущающих воздействий, отклоняющих систему управления запасами от нормального функционирования.
В рассмотренных ранее системах управления запасами, несмотря на ориентацию их на стабильные условия функционирования, предусмотрена возможность сглаживания сбоев поставки и потребления. Так, система с фиксированным размером заказа учитывает одно из восьми возмущенных воздействий, а именно задержку поставки. Это воздействие снимается введением в систему параметра гарантийного (страхового) запаса. Он позволяет обеспечивать потребность на время предполагаемой задержки поставки. Если возможная задержка поставки будет представлять собой максимально возможную задержку, то механизм системы предохранит потребителя от дефицита в случае единичного сбоя поставки. Второй расчетный параметр системы – пороговый уровень обеспечивает поддержку системы в бездефицитном состоянии. Период времени, через который происходит пополнение гарантийного запаса до расчетного объема, зависит от конкретных значений исходных и фактических параметров системы.
Система с фиксированным интервалом времени между заказами также учитывает возмущающее воздействие задержки доставки. Как и в системе с фиксированным размером заказа, это воздействие снимается параметром гарантийного (страхового) запаса. Восполнение гарантийного запаса до расчетного объема производится во время последующих поставок через пересчет размера заказа таким образом, чтобы его поставка увеличила запас до максимально желательного уровня. Если прогноз потребления до момента будущей поставки был точным, механизм системы с фиксированным интервалом времени между заказами предохранит потребителя от дефицита материальных ресурсов при сбоях поставки.
Система с установленной периодичностью пополнения запасов до постоянного уровня в отличие от основных систем управления запасами учитывает возможность как задержки поставки, так и изменения темпов потребления от запланированных. Расширение способности системы противостоять незапланированным возмущающим воздействиям связано с объединением идей использования порогового уровня и фиксированного интервала между заказами. Отслеживание порогового уровня повышает чувствительность системы к возможным колебаниям интенсивности потребления.
Система «минимум – максимум» ориентирована на ситуацию, когда затраты на учет запасов на складе и издержки на оформление заказа настолько значительны, что становятся соизмеримыми с потерями от дефицита запасов. Это единственная из рассмотренных ранее систем, допускающая дефицит запасов по экономическим соображениям. Тем не менее и система «минимум – максимум» учитывает возможность задержки поставки через параметр гарантийного запаса.
Таким образом, рассмотренные основные и прочие системы управления запасами применимы лишь к ограниченному спектру условий функционирования и взаимодействия поставщиков и потребителей. Повышение эффективности использования системы управления запасами в логистической системе организации приводит к необходимости разработки оригинальных систем управления запасами. В теории управления запасами имеется достаточное число специальных способов ведения такой работы.
Выводы
Тема 6. ЛОГИСТИКА ПРОИЗВОДСТВЕННЫХ ПРОЦЕССОВ И РАСПРЕДЕЛЕНИЯ
6.1. Организация материальных потоков в производстве
6.2. Организация производственного процесса
Основы проектирования эффективной логистической системы управления запасами.Основные системы управления запасами – с размером заказов и фиксированным интервалом времени между заказами, а также прочие системы управления запасами – с установленной периодичностью пополнения запасов до постоянного уровня и система «минимум – максимум» разработаны для условий, когда отсутствуют отклонения от запланированных параметров поставки и потребления. Этими параметрами являются:
• размер заказа;
• интервал времени между заказами;
• время поставки;
• возможная задержка поставки;
• ожидаемое дневное потребление;
• прогнозируемое потребление до момента поставки. Непрерывное обеспечение потребности в каком-либо виде материального ресурса связано с определенными трудностями. Прежде всего это возможность появления различных отклонений в значениях перечисленных выше показателей как со стороны потребителя запаса, так и со стороны исполнителя заказа. Кроме того, вполне вероятны ошибки исполнителей, которые приводят к нарушению нормального функционирования системы управления запасами.
Практически возможны следующие отклонения запланированных и фактических показателей:
• изменение интенсивности потребления в ту или другую сторону;
• поставка незапланированного объема заказа;
• ошибки учета фактического запаса, ведущие к неправильному определению размера заказа.
Довольно часто имеют место многообразные сочетания возмущающих воздействий, отклоняющих систему управления запасами от нормального функционирования.
В рассмотренных ранее системах управления запасами, несмотря на ориентацию их на стабильные условия функционирования, предусмотрена возможность сглаживания сбоев поставки и потребления. Так, система с фиксированным размером заказа учитывает одно из восьми возмущенных воздействий, а именно задержку поставки. Это воздействие снимается введением в систему параметра гарантийного (страхового) запаса. Он позволяет обеспечивать потребность на время предполагаемой задержки поставки. Если возможная задержка поставки будет представлять собой максимально возможную задержку, то механизм системы предохранит потребителя от дефицита в случае единичного сбоя поставки. Второй расчетный параметр системы – пороговый уровень обеспечивает поддержку системы в бездефицитном состоянии. Период времени, через который происходит пополнение гарантийного запаса до расчетного объема, зависит от конкретных значений исходных и фактических параметров системы.
Система с фиксированным интервалом времени между заказами также учитывает возмущающее воздействие задержки доставки. Как и в системе с фиксированным размером заказа, это воздействие снимается параметром гарантийного (страхового) запаса. Восполнение гарантийного запаса до расчетного объема производится во время последующих поставок через пересчет размера заказа таким образом, чтобы его поставка увеличила запас до максимально желательного уровня. Если прогноз потребления до момента будущей поставки был точным, механизм системы с фиксированным интервалом времени между заказами предохранит потребителя от дефицита материальных ресурсов при сбоях поставки.
Система с установленной периодичностью пополнения запасов до постоянного уровня в отличие от основных систем управления запасами учитывает возможность как задержки поставки, так и изменения темпов потребления от запланированных. Расширение способности системы противостоять незапланированным возмущающим воздействиям связано с объединением идей использования порогового уровня и фиксированного интервала между заказами. Отслеживание порогового уровня повышает чувствительность системы к возможным колебаниям интенсивности потребления.
Система «минимум – максимум» ориентирована на ситуацию, когда затраты на учет запасов на складе и издержки на оформление заказа настолько значительны, что становятся соизмеримыми с потерями от дефицита запасов. Это единственная из рассмотренных ранее систем, допускающая дефицит запасов по экономическим соображениям. Тем не менее и система «минимум – максимум» учитывает возможность задержки поставки через параметр гарантийного запаса.
Таким образом, рассмотренные основные и прочие системы управления запасами применимы лишь к ограниченному спектру условий функционирования и взаимодействия поставщиков и потребителей. Повышение эффективности использования системы управления запасами в логистической системе организации приводит к необходимости разработки оригинальных систем управления запасами. В теории управления запасами имеется достаточное число специальных способов ведения такой работы.
Выводы
1. Современный крупный склад – сложное техническое сооружение, которое состоит из многочисленных взаимосвязанных элементов, имеет определенную структуру и выполняет функции по преобразованию материальных потоков, накоплению, переработке и распределению грузов между потребителями.
Основное назначение склада – концентрация запасов, их хранение и обеспечение бесперебойного и ритмичного выполнения заказов потребителей. К основным функциям склада можно отнести следующие:
• складирование и хранение –позволяет выравнивать временную разницу между выпуском продукции и ее потреблением и дает возможность осуществлять непрерывное производство и снабжение на базе создаваемых товарных запасов;
• система складирования – предполагает оптимальное размещение груза на складе и рациональное управление им.
2. Запас можно определить как материальный поток, рассматриваемый в определенном временном сечении. Запасы классифицируются следующим образом: снабженческие, производственные, сбытовые (товарные), складские и транспортные.
Логистический подход к управлению товарно-материальными запасами предусматривает отказ от функционально ориентированной концепции в этой области. Логистическая система управления запасами проектируется для непрерывного обеспечения потребителя каким-либо видом материального ресурса.
Основное назначение склада – концентрация запасов, их хранение и обеспечение бесперебойного и ритмичного выполнения заказов потребителей. К основным функциям склада можно отнести следующие:
• складирование и хранение –позволяет выравнивать временную разницу между выпуском продукции и ее потреблением и дает возможность осуществлять непрерывное производство и снабжение на базе создаваемых товарных запасов;
• система складирования – предполагает оптимальное размещение груза на складе и рациональное управление им.
2. Запас можно определить как материальный поток, рассматриваемый в определенном временном сечении. Запасы классифицируются следующим образом: снабженческие, производственные, сбытовые (товарные), складские и транспортные.
Логистический подход к управлению товарно-материальными запасами предусматривает отказ от функционально ориентированной концепции в этой области. Логистическая система управления запасами проектируется для непрерывного обеспечения потребителя каким-либо видом материального ресурса.
Тема 6. ЛОГИСТИКА ПРОИЗВОДСТВЕННЫХ ПРОЦЕССОВ И РАСПРЕДЕЛЕНИЯ
6.1. Организация материальных потоков в производстве
Материальный поток на своем пути от первичного источника сырья до конечного потребителя проходит ряд производственных звеньев. Управление материальным потоком на этом этапе имеет свою специфику и носит название
производственной логистики,которая рассматривает процессы, происходящие в сфере материального производства, т. е. в сфере производства материальных благ и материальных услуг.
Производственный процесспредставляет собой совокупность трудовых и естественных процессов, направленных на изготовление товаров заданного качества, ассортимента и в установленные сроки.
Все производственные процессы делятся на основные и вспомогательные.
Задачи производственной логистики касаются управления материальными потоками внутри предприятий, создающих материальные блага или оказывающих такие материальные услуги, как хранение, фасовка, развеска, укладка и др.
Главной задачей производственной логистикиявляется обеспечение производства продукции необходимого качества в установленные сроки, непрерывного движения предметов труда и непрерывной занятости рабочих мест. Объекты логистики – потоковые и материальные процессы.
Характерная черта объектов изучения в производственной логистике – их территориальная компактность. В литературе их иногда называют островными объектами логистики.
Логистические системы, рассматриваемые производственной логистикой, называются внутрипроизводственными логистическими системами.К ним можно отнести промышленные предприятия, оптовые предприятия, имеющие складские сооружения, узловую грузовую станцию, узловой морской порт и др.
Внутрипроизводственные логистические системы можно рассмотреть на макро– и микроуровнях.
На макроуровне внутрипроизводственные логистические системы выступают в качестве элементов макрологических систем. Они задают ритм работы этих систем, являются источником материальных потоков. Возможность адаптации макрологических систем к изменениям окружающей среды в большой степени определяется способностью входящих в них внутрипроизводственных логистических систем быстро менять качественный и количественный состав выходного материального потока, т. е. ассортимент и количество выпускаемой продукции.
Качественная гибкость внутрипроизводственных логистических систем может обеспечиваться за счет наличия универсального обслуживающего персонала и гибкого производства.
На микроуровневнутрипроизводственные логистические системы представляют собой подсистемы, которые находятся в отношениях и связях друг с другом, образующих определенную целостность, единство. К этим подсистемам относятся закупка, склады, запасы, обслуживающие производства, транспорт, информация, сбыт и кадры (обеспечивают вхождение материального потока в систему, прохождение внутри нее и выход из системы). В соответствии с концепцией логистики построение внутрипроизводственных логистических систем должно обеспечить возможность постоянного согласования и взаимной корректировки планов и действий снабженческих, производственных и сбытовых звеньев внутри предприятия.
Логистическая концепция организации производствавключает в себя следующие основные положения:
• отказ от избыточных запасов;
• отказ от завышенного времени на выполнение вспомогательных и транспортно-складских операций;
• отказ от изготовления серий деталей, на которые нет заказов покупателей;
• устранение простоев оборудования;
• обязательное устранение брака;
• устранение нерациональных внутризаводских перевозок;
• превращение поставщиков из противостоящей стороны в доброжелательных партнеров.
Логистическая организация позволяет снизить себестоимость в условиях конкуренции путем ориентации предприятия на рынок покупателя, т. е. приоритет получает максимальная загрузка оборудования и выпуск крупной партии изделий.
Существует два варианта управления материальными потоками.
1. Толкающая система (push system),т. е. предметы труда, поступающие на производственный участок, которые у технологического звена не заказываются (рис. 6.1).
Этот вариант предполагает, что изготовление изделий начинается на одном конце производственной линии, проходит через последовательный ряд технологических операций и заканчивается обработкой на другом конце производственной цепочки. Материальный поток выдается получателю по команде, поступающей на передающее звено из центральной системы управления производством. При этом по завершении обработки на одном участке изделие передается на следующий независимо от того, готов ли этот участок принять изделие на обработку или нет. Каждый участок имеет производственный план. Однако создать жесткий технологический процесс, все параметры которого были бы наперед точно рассчитаны, невозможно, поэтому на предприятиях всегда должен быть определенный производственный запас, который играет роль буфера и увеличивает гибкость системы. Толкающие системы известны под названием «система MRP».Названные выше системы в значительной степени характерны для традиционных методов организации производства. Возможность их применения для логистической организации производства появилась в связи с широким использованием ЭВМ, что позволило повысить гибкость этой системы.
К логистическим системам с вытягиванием относят систему «Канбан». В этой системе выделяют два вида карточек:
1) карточки отбора;
2) карточки производственного заказа.
В карточке отбора указывают число деталей, которое должно быть взято на предшествующем участке обработки.
В карточке производственного заказа указано число деталей, которое должно быть изготовлено на предшествующем участке.
В месте складирования детали погружают в автопогрузчик в количестве, указанном в карточках отбора. При этом с ящиков снимают прикрепленные к ним карточки заказа, которые информируют о заказе на изготовление новых деталей в строго определенном количестве. План на участках формируют каждый день. Это обеспечивает гибкость системы. Какое-либо перемещение изделий без карточек недопустимо. Обычно система «Канбан» сочетается с системой контроля качества. Эта система не требует тотальной компьютеризации производства, однако она предполагает высокую дисциплину поставок и высокую ответственность персонала, что и ограничивает ее внедрение в различных странах.
Особое внимание производственной логистикой уделяется принципам рациональной организации производственного процесса,а именно:
1) обеспечению ритмичной согласованной работы всех звеньев производства по единому графику и равномерного выпуска продукции. Ритмичная работа предполагает организацию во времени и пространстве единичных, частичных и частных процессов в единый непрерывный производственный процесс, обеспечивающий своевременный выпуск каждой конкретной продукции в установленных объемах с минимальными затратами производственных ресурсов;
2) обеспечению максимальной непрерывности процессов производства. Непрерывность заключается в движении предметов труда и загрузки рабочих мест. Общий критерий оптимизации – минимум затрат производственных ресурсов в условиях непоточного производства может быть обеспечен за счет организации непрерывной загрузки рабочих мест, тогда как в поточном производстве – выбор варианта с минимальным временем межоперационного прослеживания деталей;
3) обеспечению максимальной надежности плановых расчетов и минимальной трудоемкости плановых работ. Нужно разрешить следующие проблемы:
• дефицит производственных мощностей;
• субоптимальность календарных планов производства;
• большие длительности производственных циклов;
• неэффективное управление запасами;
• низкий КПД оборудования;
• отклонения от технологии производства;
• достаточная гибкость и маневренность в реализации цели при возникновении различных отклонений от плана;
• непрерывность планового руководства;
• соответствие системы оперативного управления производством типу и характеру конкретного производства;
• прямоточность;
• пропорциональность, т. е. выполнение обеспечения равной пропускной способности разных рабочих мест одного процесса, а также пропорционального обеспечения рабочих мест информацией, материальными ресурсами и т. д.;
• параллельность;
• концентрация однородных предметов труда в одном месте.
Основными законами, обеспечивающими оптимизацию производственных процессов, являются: закон упорядоченности движения материальных потоков, закон календарной синхронизации технологических операций, закон резервирования ресурсов производственного процесса, закон эмерджентности основных и вспомогательных процессов и закон ритма производственного процесса.
В реализации целей логистики существенное место занимают новые методы организации производства, которые называются стройным производством.Оно рассматривает возникновение «узких» мест как шанс их полной ликвидации.
Важную роль в обеспечении рационального товародвижения играют торгово-посреднические организации, которые обеспечивают производство необходимым сырьем и материалами. Логистика здесь заключается в выборе стратегии управления приобретением, движением и хранением материалов, изделий и запасов, а также в управлении информационными потоками, сопровождающими процесс товародвижения. Логистические посредники становятся эффективным инструментом экономии финансовых и материальных ресурсов в процессе товародвижения.
Эффективность логистического подхода при управлении материальными потоками на предприятии.Известно, что 95–98 % времени, в течение которого материал находится на производственном предприятии, занимает выполнение погрузочно-разгрузочных и транспортно-складских работ. Этим обусловливается их значительная доля в себестоимости выпускаемой продукции.
Логистический подход к управлению материальными потоками на предприятии позволяет максимально оптимизировать выполнение комплекса логистических операций. По данным фирм Bosch, Siemens, Mitsubishi, General Motors,1 % сокращения расходов на выполнение логистических функций имел тот же эффект, что и увеличение на 10 % объема сбыта. Совокупный эффект от применения логистического подходак управлению материальным потоком на предприятии складывается из следующих элементов:
1) производство ориентировано на рынок, становится возможным эффективный переход на малосерийное и индивидуальное производство;
2) налаживаются партнерские отношения с поставщиками;
3) сокращаются простои оборудования (так как на рабочих местах постоянно имеются необходимые для работы материалы);
4) оптимизируются запасы – одна из центральных проблем логистики. Анализ опыта ряда фирм Западной Европы, использующих современные логистические методы организаций производства (систему «Канбан»), показывает, что применение логистики позволяет уменьшить производственные запасы на 50 %;
5) сокращается численность вспомогательных рабочих (чем меньше уровень системности, тем неопределеннее трудовой процесс и тем выше потребность во вспомогательном персонале для выполнения пиковых объемов работ);
6) улучшается качество выпускаемой продукции;
7) снижаются потери материалов (любые логистические операции – это потенциальные потери, а оптимизация логистических операций – сокращение потерь);
8) улучшается использование производственных и складских площадей (неопределенность потоковых процессов заставляет резервировать большие добавочные площади);
9) снижается травматизм (логистический подход предусматривает систему безопасности труда).
Производственный процесспредставляет собой совокупность трудовых и естественных процессов, направленных на изготовление товаров заданного качества, ассортимента и в установленные сроки.
Все производственные процессы делятся на основные и вспомогательные.
Задачи производственной логистики касаются управления материальными потоками внутри предприятий, создающих материальные блага или оказывающих такие материальные услуги, как хранение, фасовка, развеска, укладка и др.
Главной задачей производственной логистикиявляется обеспечение производства продукции необходимого качества в установленные сроки, непрерывного движения предметов труда и непрерывной занятости рабочих мест. Объекты логистики – потоковые и материальные процессы.
Характерная черта объектов изучения в производственной логистике – их территориальная компактность. В литературе их иногда называют островными объектами логистики.
Логистические системы, рассматриваемые производственной логистикой, называются внутрипроизводственными логистическими системами.К ним можно отнести промышленные предприятия, оптовые предприятия, имеющие складские сооружения, узловую грузовую станцию, узловой морской порт и др.
Внутрипроизводственные логистические системы можно рассмотреть на макро– и микроуровнях.
На макроуровне внутрипроизводственные логистические системы выступают в качестве элементов макрологических систем. Они задают ритм работы этих систем, являются источником материальных потоков. Возможность адаптации макрологических систем к изменениям окружающей среды в большой степени определяется способностью входящих в них внутрипроизводственных логистических систем быстро менять качественный и количественный состав выходного материального потока, т. е. ассортимент и количество выпускаемой продукции.
Качественная гибкость внутрипроизводственных логистических систем может обеспечиваться за счет наличия универсального обслуживающего персонала и гибкого производства.
На микроуровневнутрипроизводственные логистические системы представляют собой подсистемы, которые находятся в отношениях и связях друг с другом, образующих определенную целостность, единство. К этим подсистемам относятся закупка, склады, запасы, обслуживающие производства, транспорт, информация, сбыт и кадры (обеспечивают вхождение материального потока в систему, прохождение внутри нее и выход из системы). В соответствии с концепцией логистики построение внутрипроизводственных логистических систем должно обеспечить возможность постоянного согласования и взаимной корректировки планов и действий снабженческих, производственных и сбытовых звеньев внутри предприятия.
Логистическая концепция организации производствавключает в себя следующие основные положения:
• отказ от избыточных запасов;
• отказ от завышенного времени на выполнение вспомогательных и транспортно-складских операций;
• отказ от изготовления серий деталей, на которые нет заказов покупателей;
• устранение простоев оборудования;
• обязательное устранение брака;
• устранение нерациональных внутризаводских перевозок;
• превращение поставщиков из противостоящей стороны в доброжелательных партнеров.
Логистическая организация позволяет снизить себестоимость в условиях конкуренции путем ориентации предприятия на рынок покупателя, т. е. приоритет получает максимальная загрузка оборудования и выпуск крупной партии изделий.
Существует два варианта управления материальными потоками.
1. Толкающая система (push system),т. е. предметы труда, поступающие на производственный участок, которые у технологического звена не заказываются (рис. 6.1).
Этот вариант предполагает, что изготовление изделий начинается на одном конце производственной линии, проходит через последовательный ряд технологических операций и заканчивается обработкой на другом конце производственной цепочки. Материальный поток выдается получателю по команде, поступающей на передающее звено из центральной системы управления производством. При этом по завершении обработки на одном участке изделие передается на следующий независимо от того, готов ли этот участок принять изделие на обработку или нет. Каждый участок имеет производственный план. Однако создать жесткий технологический процесс, все параметры которого были бы наперед точно рассчитаны, невозможно, поэтому на предприятиях всегда должен быть определенный производственный запас, который играет роль буфера и увеличивает гибкость системы. Толкающие системы известны под названием «система MRP».Названные выше системы в значительной степени характерны для традиционных методов организации производства. Возможность их применения для логистической организации производства появилась в связи с широким использованием ЭВМ, что позволило повысить гибкость этой системы.
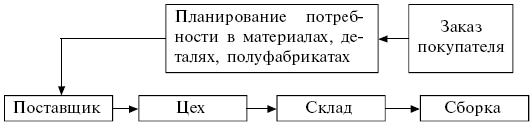
Рис. 6.1. Система с выталкиванием изделия, запущенного в производство
2. Тянущая система (pull system),при которой предметы труда на технологический участок поступают по мере необходимости. Она способствует сокращению производственных запасов при одновременном увеличении гибкости производства (рис. 6.2).
Рис. 6.2. Система с вытягиванием изделия, запущенного в производство
Эта система предполагает получение изделий с предыдущего участка по мере необходимости. Центральная система управления не вмешивается в обмен материальными потоками между различными участками предприятия, не устанавливает для них текущих производственных заданий. На промышленных предприятиях план имеет только линия окончательной сборки, и отсюда информация о необходимости производить нужные детали поступает на предыдущие участки посредством специальных карточек. План на участках формируется каждый день, что и обеспечивает гибкость системы.К логистическим системам с вытягиванием относят систему «Канбан». В этой системе выделяют два вида карточек:
1) карточки отбора;
2) карточки производственного заказа.
В карточке отбора указывают число деталей, которое должно быть взято на предшествующем участке обработки.
В карточке производственного заказа указано число деталей, которое должно быть изготовлено на предшествующем участке.
В месте складирования детали погружают в автопогрузчик в количестве, указанном в карточках отбора. При этом с ящиков снимают прикрепленные к ним карточки заказа, которые информируют о заказе на изготовление новых деталей в строго определенном количестве. План на участках формируют каждый день. Это обеспечивает гибкость системы. Какое-либо перемещение изделий без карточек недопустимо. Обычно система «Канбан» сочетается с системой контроля качества. Эта система не требует тотальной компьютеризации производства, однако она предполагает высокую дисциплину поставок и высокую ответственность персонала, что и ограничивает ее внедрение в различных странах.
Особое внимание производственной логистикой уделяется принципам рациональной организации производственного процесса,а именно:
1) обеспечению ритмичной согласованной работы всех звеньев производства по единому графику и равномерного выпуска продукции. Ритмичная работа предполагает организацию во времени и пространстве единичных, частичных и частных процессов в единый непрерывный производственный процесс, обеспечивающий своевременный выпуск каждой конкретной продукции в установленных объемах с минимальными затратами производственных ресурсов;
2) обеспечению максимальной непрерывности процессов производства. Непрерывность заключается в движении предметов труда и загрузки рабочих мест. Общий критерий оптимизации – минимум затрат производственных ресурсов в условиях непоточного производства может быть обеспечен за счет организации непрерывной загрузки рабочих мест, тогда как в поточном производстве – выбор варианта с минимальным временем межоперационного прослеживания деталей;
3) обеспечению максимальной надежности плановых расчетов и минимальной трудоемкости плановых работ. Нужно разрешить следующие проблемы:
• дефицит производственных мощностей;
• субоптимальность календарных планов производства;
• большие длительности производственных циклов;
• неэффективное управление запасами;
• низкий КПД оборудования;
• отклонения от технологии производства;
• достаточная гибкость и маневренность в реализации цели при возникновении различных отклонений от плана;
• непрерывность планового руководства;
• соответствие системы оперативного управления производством типу и характеру конкретного производства;
• прямоточность;
• пропорциональность, т. е. выполнение обеспечения равной пропускной способности разных рабочих мест одного процесса, а также пропорционального обеспечения рабочих мест информацией, материальными ресурсами и т. д.;
• параллельность;
• концентрация однородных предметов труда в одном месте.
Основными законами, обеспечивающими оптимизацию производственных процессов, являются: закон упорядоченности движения материальных потоков, закон календарной синхронизации технологических операций, закон резервирования ресурсов производственного процесса, закон эмерджентности основных и вспомогательных процессов и закон ритма производственного процесса.
В реализации целей логистики существенное место занимают новые методы организации производства, которые называются стройным производством.Оно рассматривает возникновение «узких» мест как шанс их полной ликвидации.
Важную роль в обеспечении рационального товародвижения играют торгово-посреднические организации, которые обеспечивают производство необходимым сырьем и материалами. Логистика здесь заключается в выборе стратегии управления приобретением, движением и хранением материалов, изделий и запасов, а также в управлении информационными потоками, сопровождающими процесс товародвижения. Логистические посредники становятся эффективным инструментом экономии финансовых и материальных ресурсов в процессе товародвижения.
Эффективность логистического подхода при управлении материальными потоками на предприятии.Известно, что 95–98 % времени, в течение которого материал находится на производственном предприятии, занимает выполнение погрузочно-разгрузочных и транспортно-складских работ. Этим обусловливается их значительная доля в себестоимости выпускаемой продукции.
Логистический подход к управлению материальными потоками на предприятии позволяет максимально оптимизировать выполнение комплекса логистических операций. По данным фирм Bosch, Siemens, Mitsubishi, General Motors,1 % сокращения расходов на выполнение логистических функций имел тот же эффект, что и увеличение на 10 % объема сбыта. Совокупный эффект от применения логистического подходак управлению материальным потоком на предприятии складывается из следующих элементов:
1) производство ориентировано на рынок, становится возможным эффективный переход на малосерийное и индивидуальное производство;
2) налаживаются партнерские отношения с поставщиками;
3) сокращаются простои оборудования (так как на рабочих местах постоянно имеются необходимые для работы материалы);
4) оптимизируются запасы – одна из центральных проблем логистики. Анализ опыта ряда фирм Западной Европы, использующих современные логистические методы организаций производства (систему «Канбан»), показывает, что применение логистики позволяет уменьшить производственные запасы на 50 %;
5) сокращается численность вспомогательных рабочих (чем меньше уровень системности, тем неопределеннее трудовой процесс и тем выше потребность во вспомогательном персонале для выполнения пиковых объемов работ);
6) улучшается качество выпускаемой продукции;
7) снижаются потери материалов (любые логистические операции – это потенциальные потери, а оптимизация логистических операций – сокращение потерь);
8) улучшается использование производственных и складских площадей (неопределенность потоковых процессов заставляет резервировать большие добавочные площади);
9) снижается травматизм (логистический подход предусматривает систему безопасности труда).
6.2. Организация производственного процесса
Процесс производства –это соединение ресурсов и факторов производства в определенной комбинации в целях создания продукции и ее последующего сбыта.
Существует две концепции организации производства:логистическая и традиционная.
Логистическая концепциявключает в себя следующие основные положения:
1) отказ от избыточных запасов;
2) отказ от завышенного времени на выполнение основных и транспортно-складских операций;
3) отказ от изготовления серий деталей, на которые нет заказа покупателей;
4) устранение простоев оборудования;
5) обязательное устранение брака;
6) устранение нерациональных внутризаводских перевозок;
7) превращение поставщиков из противостоящей стороны в доброжелательных партнеров.
В отличие от логистической традиционная концепцияпредполагает:
1) никогда не останавливать основное оборудование и поддерживать во что бы то ни стало высокий коэффициент его использования;
2) изготавливать продукцию как можно более крупными партиями;
3) иметь максимально большой запас материальных ресурсов «на всякий случай».
Содержание концептуальных положений свидетельствует о том, что традиционная концепция производства наиболее приемлема для условий «рынка продавца», в то время как логистическая концепция – для условий «рынка покупателей».
Когда спрос превышает предложение, можно с уверенностью сказать, что изготовленная с учетом конъюнктуры рынка партия изделий будет реализована, поэтому приоритет получает цель максимальной загрузки оборудования. Причем чем крупнее будет изготовленная партия, тем ниже окажется себестоимость единицы изделия.
Ситуация меняется с приходом на рынок «диктата» покупателя. Задача реализации произведенного продукта в условиях конкуренции выходит на первое место. Непостоянство и непредсказуемость рыночного спроса делают нецелесообразным создание и содержание больших запасов. В то же время производственник уже не имеет права упустить ни одного заказа. Отсюда возникает необходимость в гибких производственных мощностях, способных быстро отреагировать производством на спрос.
Производство в условиях рыночной экономики может выжить лишь в том случае, если оно способно быстро менять ассортимент и количество выпускаемой продукции. До 1970-х гг. весь мир решал эту задачу за счет наличия на складах готовой продукции. Сегодня логистика предлагает адаптироваться к изменениям спроса за счет запаса производственной мощности.
Запас производственной мощности появляется при наличии качественной и количественной гибкости производственных систем. Качественная гибкость обеспечивается за счет наличия универсального обслуживающего персонала и гибкого производства. Количественная гибкость может обеспечиваться разными способами. Например, на некоторых предприятиях Японии основной персонал составляет не более 20 % максимальной численности работающих, остальные 80 % – временные работники. Таким образом, при численности персонала в 200 человек предприятие в любой момент может поставить на выполнение заказа до 1000 человек. Резерв рабочей силы дополняется соответствующим резервом средств труда.
Процесс организации производства должен быть тщательно спланирован. При планировании производства определяются следующие показатели:
1) число комплектующих изделий, необходимых для производства;
2) промежуток времени, в течение которого производится продукция;
3) количество сырья и оборудования, необходимого для производства требуемого объема продукции в рамках запланированного периода времени.
Планирование подразделяют на следующие виды:
1) по срокам:
а) календарное – включает в себя распределение годовых плановых заданий по производственным подразделениям и срокам выполнения, а также доведение установленных показателей до конкретных исполнителей работ;
б) текущее – представляет собой постоянный оперативный контроль и непрерывное текущее регулирование хода производственных процессов;
2) по сфере применения:
а) межцеховое – разработка, регулирование и контроль над выполнением планов производства всеми функциональными подразделениями предприятия;
б) внутрицеховое – это процедура разработки оперативных планов и текущих графиков работы для отдельного производственного участка.
Используют также системы оперативного планирования:
1) подетальная –применяется в условиях высокоорганизованного и стабильного производства. С помощью данной системы планируют и регулируют ход выполнения работ, технологических операций и производственных процессов по каждой детали на определенный плановый период (час, смену, день, неделю);
2) позаказная –используется в единичном и мелкосерийном производстве с большой номенклатурой и небольшим объемом выпускаемой продукции. Объектом планирования является отдельный заказ на производство однотипных работ. Данная система планирования основана на расчетах длительности производственных циклов и нормативов опережения, с помощью которых устанавливаются требуемые заказчиком сроки выполнения как отдельных процессов или работ, так и всего заказа в целом;
3) некомплектная –применяется в серийном машиностроительном производстве. В качестве основной планово-учетной единицы используются различные детали, входящие в общий комплект продукции. При покомплектной системе планирования календарные задания производственным подразделениям разрабатываются не по деталям отдельного наименования, а по укрупненным группам или комплектам деталей на узел, машину, заказ или определенный объем продукции.
Существует две концепции организации производства:логистическая и традиционная.
Логистическая концепциявключает в себя следующие основные положения:
1) отказ от избыточных запасов;
2) отказ от завышенного времени на выполнение основных и транспортно-складских операций;
3) отказ от изготовления серий деталей, на которые нет заказа покупателей;
4) устранение простоев оборудования;
5) обязательное устранение брака;
6) устранение нерациональных внутризаводских перевозок;
7) превращение поставщиков из противостоящей стороны в доброжелательных партнеров.
В отличие от логистической традиционная концепцияпредполагает:
1) никогда не останавливать основное оборудование и поддерживать во что бы то ни стало высокий коэффициент его использования;
2) изготавливать продукцию как можно более крупными партиями;
3) иметь максимально большой запас материальных ресурсов «на всякий случай».
Содержание концептуальных положений свидетельствует о том, что традиционная концепция производства наиболее приемлема для условий «рынка продавца», в то время как логистическая концепция – для условий «рынка покупателей».
Когда спрос превышает предложение, можно с уверенностью сказать, что изготовленная с учетом конъюнктуры рынка партия изделий будет реализована, поэтому приоритет получает цель максимальной загрузки оборудования. Причем чем крупнее будет изготовленная партия, тем ниже окажется себестоимость единицы изделия.
Ситуация меняется с приходом на рынок «диктата» покупателя. Задача реализации произведенного продукта в условиях конкуренции выходит на первое место. Непостоянство и непредсказуемость рыночного спроса делают нецелесообразным создание и содержание больших запасов. В то же время производственник уже не имеет права упустить ни одного заказа. Отсюда возникает необходимость в гибких производственных мощностях, способных быстро отреагировать производством на спрос.
Производство в условиях рыночной экономики может выжить лишь в том случае, если оно способно быстро менять ассортимент и количество выпускаемой продукции. До 1970-х гг. весь мир решал эту задачу за счет наличия на складах готовой продукции. Сегодня логистика предлагает адаптироваться к изменениям спроса за счет запаса производственной мощности.
Запас производственной мощности появляется при наличии качественной и количественной гибкости производственных систем. Качественная гибкость обеспечивается за счет наличия универсального обслуживающего персонала и гибкого производства. Количественная гибкость может обеспечиваться разными способами. Например, на некоторых предприятиях Японии основной персонал составляет не более 20 % максимальной численности работающих, остальные 80 % – временные работники. Таким образом, при численности персонала в 200 человек предприятие в любой момент может поставить на выполнение заказа до 1000 человек. Резерв рабочей силы дополняется соответствующим резервом средств труда.
Процесс организации производства должен быть тщательно спланирован. При планировании производства определяются следующие показатели:
1) число комплектующих изделий, необходимых для производства;
2) промежуток времени, в течение которого производится продукция;
3) количество сырья и оборудования, необходимого для производства требуемого объема продукции в рамках запланированного периода времени.
Планирование подразделяют на следующие виды:
1) по срокам:
а) календарное – включает в себя распределение годовых плановых заданий по производственным подразделениям и срокам выполнения, а также доведение установленных показателей до конкретных исполнителей работ;
б) текущее – представляет собой постоянный оперативный контроль и непрерывное текущее регулирование хода производственных процессов;
2) по сфере применения:
а) межцеховое – разработка, регулирование и контроль над выполнением планов производства всеми функциональными подразделениями предприятия;
б) внутрицеховое – это процедура разработки оперативных планов и текущих графиков работы для отдельного производственного участка.
Используют также системы оперативного планирования:
1) подетальная –применяется в условиях высокоорганизованного и стабильного производства. С помощью данной системы планируют и регулируют ход выполнения работ, технологических операций и производственных процессов по каждой детали на определенный плановый период (час, смену, день, неделю);
2) позаказная –используется в единичном и мелкосерийном производстве с большой номенклатурой и небольшим объемом выпускаемой продукции. Объектом планирования является отдельный заказ на производство однотипных работ. Данная система планирования основана на расчетах длительности производственных циклов и нормативов опережения, с помощью которых устанавливаются требуемые заказчиком сроки выполнения как отдельных процессов или работ, так и всего заказа в целом;
3) некомплектная –применяется в серийном машиностроительном производстве. В качестве основной планово-учетной единицы используются различные детали, входящие в общий комплект продукции. При покомплектной системе планирования календарные задания производственным подразделениям разрабатываются не по деталям отдельного наименования, а по укрупненным группам или комплектам деталей на узел, машину, заказ или определенный объем продукции.