Страница:
Техническое задание согласовывается с планово-экономической службой и утверждается главным инженером предприятия.
В случае производства монтажных работ специализированными фирмами организационно-техническая подготовка подразумевает:
• получение монтажной организацией от заказчика утвержденной технической документации;
• организацию монтажной площадки;
• установление сроков строительной готовности объекта;
• организацию поставки оборудования;
• оснащение участка монтажным оборудованием;
• разработку и создание безопасных условий труда;
• организацию контроля качества работ, подготовку кадров.
Техническая документация содержит следующее:
• план строящегося объекта, с указанием дорог, коммуникаций, энергообеспечения;
• планы и разрезы цехов с указанием оборудования;
• генеральные чертежи на фундаменты и условия на монтаж оборудования;
• чертежи на трубопроводы и металлоконструкции;
• смету на производство монтажных работ;
• дополнительную документацию на монтаж отдельных узлов.
Монтажная организация разрабатывает план производства работ (ППР), который содержит основные принципиальные решения по монтажу. ППР оформляется в виде пояснительной записки, к которой прикладывается генеральный план, график производства работ, ведомость трудовых затрат и график движения рабочей силы, монтажные чертежи.
Следует отметить, что график движения рабочей силы должен иметь плавный характер (рис. 2).
Рабочие дни Рис. 2. График движения рабочей силы.
Площадка для складирования поступающего оборудования является составной частью монтажной площадки и располагается вблизи монтируемого объекта. Размеры площадки устанавливаются в зависимости от габаритных размеров поступающего оборудования, а также могут быть рассчитаны по массе оборудования:
Формула № 1.
где К – коэффициент одновременности поступления (0,5–0,9);
М – общая масса оборудования, т;
В – удельная загрузка, т/м2.
Удельная загрузка зависит от вида оборудования и материалов. Средние значения этой загрузки приведены в табл. 1.
Строительная готовность объекта. Под этим термином понимают такое состояние строительной части возводимого объекта, когда можно вести монтаж в безопасных условиях и обеспечивать сохранность оборудования и рациональные методы его монтажа. В перекрытиях и стенах должны быть предусмотрены монтажные проемы для транспортировки технологического оборудования. Опасные зоны должны быть ограждены и освещены.
При приемке строительной части объекта особое внимание уделяется фундаментам и приямкам. Размеры их должны соответствовать чертежам, а отклонения не превышать допустимых норм. Значения этих норм приведены в табл. 2.
Приемка строительной готовности объекта оформляется актом, к которому прикладывается схема фундаментов и приямков с указанием отклонений от проекта. Иногда монтажникам необходимо сделать проверочный расчет размеров фундаментов.
Фундаменты под технологическое оборудование. Фундамент – устройство, которое обеспечивает оборудованию заданную ориентацию в пространстве и поглощает вибрацию во время его эксплуатации. Фундаменты бывают групповые и индивидуальные.
Рис. 3. Расчетная схема фундамента: 1 – оборудование; 2 – фундаментный болт; 3 – фундамент.
Групповые фундаменты представляют собой бетонное или железобетонное полотно толщиной до 300 мм, на котором устанавливают аппараты массой до 2 т.
Индивидуальные фундаменты используются для установки тяжелого оборудования, а также оборудования, работающего со значительными знакопеременными динамическими нагрузками. Такие фундаменты предотвращают передачу вибрации другим аппаратам.
При проектировании фундамента необходимо составить расчетную схему, определить основные его размеры, а также выполнить проверочный расчет, рис. 3. Составление расчетной схемы заключается в определении координат точек приложения сил, действующих на фундамент, рис. 4.
Рис. 4. Построение при переносе монтажных осей: а – перпендикуляра через точку, лежащую на прямой (А) и вне прямой (В); б – параллельной прямой на расстоянии L и проходящей через точку А; в – деление угла пополам; г – деление отрезка АВ пополам; д – пример переноса осей.
В расчетной схеме величина Ga представляет собой суммарный вес аппарата и перерабатываемых на нем продуктов. Если при расчете фундамента необходимо учитывать динамические нагрузки, создаваемые центробежными и инерционными силами, то их для облегчения расчета приводят к эквивалентным статическим нагрузкам Gд:
Формула № 2.
где kд – динамический коэффициент (kд = 1,5–2);
М – вращающиеся массы, кг;
ε – эксцентриситет вращающихся масс (ε = 0,01–0,001 от диаметра вращающихся масс);
n – частота вращения масс, мин–1.
Определив величины Ga и Gд, рассчитывают суммарную статическую нагрузку, Gст = Gд + Ga вес фундамента Gф и размер подземной части h2:
Формула № 3.
где k – эмпирический коэффициент, для оборудования со статической нагрузкой k = 0,6–1,5, для оборудования с динамической нагрузкой k = 2–3.
Зная вес фундамента, площадь его основания и удельный вес материала фундамента, определяют размер его подземной части:
Формула № 4.
где a и b – ширина и длина фундамента (эти величины принимаются на 100–200 мм больше размеров опорного контура аппарата), мм;
γ – удельный вес материала фундамента, кг/мм2.
Минимальная величина h2 для фундаментов в отапливаемом помещении должна быть не менее 500 мм.
Для неотапливаемых помещений и открытых площадок величина h2 определяется по выражению:
Формула № 5.
где Нпр – глубина промерзания грунта в данном районе, мм.
Значения Нпр для некоторых районов Российской Федерации:
• I. Северные и восточные районы (Архангельск, Казань, Екатеринбург) – 2 м.
• II. Северо-западные районы (Санкт-Петербург, Тверь, Петрозаводск) – 1,6 м.
• III. Центральные районы (Москва, Тамбов, Саратов) – 1,5 м.
• IV. Южные районы (Астрахань, Волгоград, Новороссийск) – 1,1 м.
Высота надземной части фундамента h1 определяется местом расположения оборудования и требованиями технологии (обеспечение горизонтальности или уклона трубопроводного участка между соседними аппаратами и т. д.). Общая высота фундамента должна быть больше, чем длина фундаментных болтов:
Формула № 6.
где l и d – длина и диаметр фундаментного болта, мм.
Диаметр фундаментного болта определяется по выражению:
Формула № 7.
где Q3 – затягивающая сила на болтах (Q3 = 4РВ), H;
РВ – вырывающая сила, Н:
Формула № 8.
где GГ – сила горизонтального смещения, Н;
L – расстояние от точки приложения силы GГ до верхней плоскости фундамента, мм;
S – расстояние между болтами, мм;
[σ]разр – допустимое напряжение разрушения материала, МПа.
Поставка и прием оборудования. Для рациональной организации монтажных работ необходима комплектная поставка оборудования. Правила поставки оборудования следующие:
• малогабаритное оборудование (теплообменники, сосуды, трубные секции и т. д.) должно поставляться в собранном виде, на подкладках, с установленными внутренними устройствами и деталями для строповки;
• защитные покрытия свинцом, медью, лаком, эмалью выполняются на заводе-изготовителе, а футеровка кирпичом и плиткой на месте монтажа;
• крупногабаритное оборудование поставляется максимально укрупненными блоками с соответствующей маркировкой;
• поставляемое оборудование должно иметь ответные фланцы на штуцерах, а также крепежные детали и анкерные болты.
Порядок транспортировки оборудования по железной дороге и реке следующий:
• по железной дороге допускается перевозка машин и аппаратов по согласованию с Министерством путей сообщения массой до 240 т, диаметром 4 м и длиной 30 м;
• по рекам на судах: диаметром до 8 м и длиной до 55 м, а с буксировкой на плаву: диаметром до 10 м и длиной до 100 м по согласованию с Министерством речного флота.
Прием оборудования в монтаж производится на складе путем осмотра без разборки на узлы и детали. При этом проверяют:
• соответствие оборудования чертежам и проектной спецификации;
• комплектность оборудования по упаковочным ведомостям;
• наличие и полноту технической документации завода-изготовителя;
• отсутствие трещин, поломок и т. п.
При приеме оборудования допускается наличие дефектов в пределах определенных норм, которые приведены в табл. 3 для емкостных аппаратов.
Документация на поставляемое оборудование должна содержать:
• назначение машины и аппарата;
• сведения об условиях работы (давление, температура);
• способы и параметры испытания;
• данные о материале прокладок и набивок;
• таблицу штуцеров;
• указание об антикоррозийной защите;
• спецификацию деталей и узлов с указанием веса;
• комплектовочную и маркировочную ведомости для крупногабаритного оборудования и инструкцию по сборке его узлов;
• зарегистрированную книгу для аппаратов, подведомственных Госгортехнадзору;
• указания по установке и креплению оборудования;
• указания по тепловой изоляции.
Прием и сдача оборудования в монтаж оформляется специальным актом.
Общие правила производства монтажных работ включают в себя:
• монтаж оборудования проводят преимущественно днем;
• монтаж нельзя проводить на открытых площадках при ветре более шести баллов, при дожде, снегопаде, гололеде;
• подъем груза должен доводиться до проектного положения, если это не удалось сделать до конца смены, то груз должен быть опущен на нулевую отметку;
• груз при подъеме должен быть надежно застропован, т. е. стропы налагаются равномерно без узлов и перекруток и угол между ветвями строп не должен быть больше 90°;
• расстроповку груза проводят только после его установки и надежного закрепления.
Глава 2
2.1. Монтажная разметка
2.2. Выверка и закрепление оборудования ПТЛ на фундаменте
2.3. Монтажные средства
2.3.1. Канаты
В случае производства монтажных работ специализированными фирмами организационно-техническая подготовка подразумевает:
• получение монтажной организацией от заказчика утвержденной технической документации;
• организацию монтажной площадки;
• установление сроков строительной готовности объекта;
• организацию поставки оборудования;
• оснащение участка монтажным оборудованием;
• разработку и создание безопасных условий труда;
• организацию контроля качества работ, подготовку кадров.
Техническая документация содержит следующее:
• план строящегося объекта, с указанием дорог, коммуникаций, энергообеспечения;
• планы и разрезы цехов с указанием оборудования;
• генеральные чертежи на фундаменты и условия на монтаж оборудования;
• чертежи на трубопроводы и металлоконструкции;
• смету на производство монтажных работ;
• дополнительную документацию на монтаж отдельных узлов.
Монтажная организация разрабатывает план производства работ (ППР), который содержит основные принципиальные решения по монтажу. ППР оформляется в виде пояснительной записки, к которой прикладывается генеральный план, график производства работ, ведомость трудовых затрат и график движения рабочей силы, монтажные чертежи.
Следует отметить, что график движения рабочей силы должен иметь плавный характер (рис. 2).
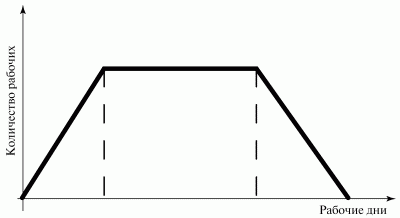
Площадка для складирования поступающего оборудования является составной частью монтажной площадки и располагается вблизи монтируемого объекта. Размеры площадки устанавливаются в зависимости от габаритных размеров поступающего оборудования, а также могут быть рассчитаны по массе оборудования:
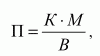
где К – коэффициент одновременности поступления (0,5–0,9);
М – общая масса оборудования, т;
В – удельная загрузка, т/м2.
Удельная загрузка зависит от вида оборудования и материалов. Средние значения этой загрузки приведены в табл. 1.
Таблица 1. Показатели удельной загрузки монтажной площадки
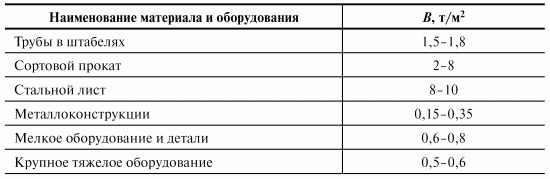
При приемке строительной части объекта особое внимание уделяется фундаментам и приямкам. Размеры их должны соответствовать чертежам, а отклонения не превышать допустимых норм. Значения этих норм приведены в табл. 2.
Таблица 2. Дополнительные нормы отклонения фундаментов
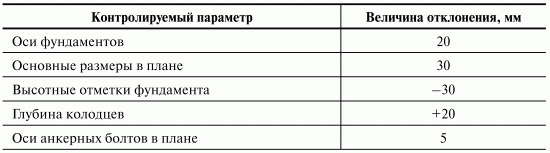
Фундаменты под технологическое оборудование. Фундамент – устройство, которое обеспечивает оборудованию заданную ориентацию в пространстве и поглощает вибрацию во время его эксплуатации. Фундаменты бывают групповые и индивидуальные.
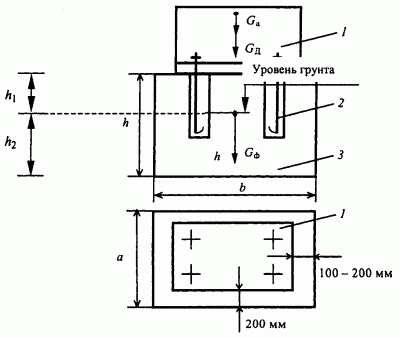
Групповые фундаменты представляют собой бетонное или железобетонное полотно толщиной до 300 мм, на котором устанавливают аппараты массой до 2 т.
Индивидуальные фундаменты используются для установки тяжелого оборудования, а также оборудования, работающего со значительными знакопеременными динамическими нагрузками. Такие фундаменты предотвращают передачу вибрации другим аппаратам.
При проектировании фундамента необходимо составить расчетную схему, определить основные его размеры, а также выполнить проверочный расчет, рис. 3. Составление расчетной схемы заключается в определении координат точек приложения сил, действующих на фундамент, рис. 4.
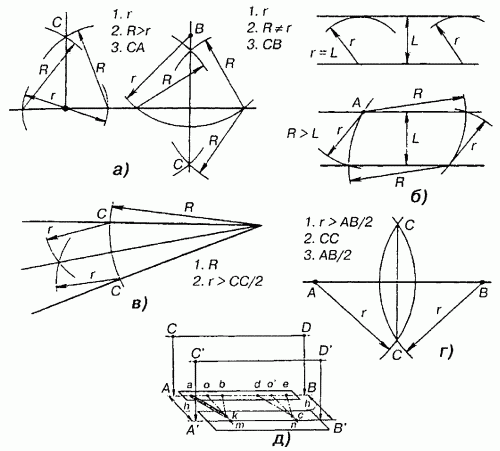
В расчетной схеме величина Ga представляет собой суммарный вес аппарата и перерабатываемых на нем продуктов. Если при расчете фундамента необходимо учитывать динамические нагрузки, создаваемые центробежными и инерционными силами, то их для облегчения расчета приводят к эквивалентным статическим нагрузкам Gд:
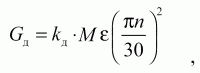
где kд – динамический коэффициент (kд = 1,5–2);
М – вращающиеся массы, кг;
ε – эксцентриситет вращающихся масс (ε = 0,01–0,001 от диаметра вращающихся масс);
n – частота вращения масс, мин–1.
Определив величины Ga и Gд, рассчитывают суммарную статическую нагрузку, Gст = Gд + Ga вес фундамента Gф и размер подземной части h2:
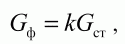
где k – эмпирический коэффициент, для оборудования со статической нагрузкой k = 0,6–1,5, для оборудования с динамической нагрузкой k = 2–3.
Зная вес фундамента, площадь его основания и удельный вес материала фундамента, определяют размер его подземной части:
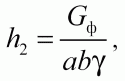
где a и b – ширина и длина фундамента (эти величины принимаются на 100–200 мм больше размеров опорного контура аппарата), мм;
γ – удельный вес материала фундамента, кг/мм2.
Минимальная величина h2 для фундаментов в отапливаемом помещении должна быть не менее 500 мм.
Для неотапливаемых помещений и открытых площадок величина h2 определяется по выражению:
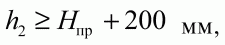
где Нпр – глубина промерзания грунта в данном районе, мм.
Значения Нпр для некоторых районов Российской Федерации:
• I. Северные и восточные районы (Архангельск, Казань, Екатеринбург) – 2 м.
• II. Северо-западные районы (Санкт-Петербург, Тверь, Петрозаводск) – 1,6 м.
• III. Центральные районы (Москва, Тамбов, Саратов) – 1,5 м.
• IV. Южные районы (Астрахань, Волгоград, Новороссийск) – 1,1 м.
Высота надземной части фундамента h1 определяется местом расположения оборудования и требованиями технологии (обеспечение горизонтальности или уклона трубопроводного участка между соседними аппаратами и т. д.). Общая высота фундамента должна быть больше, чем длина фундаментных болтов:
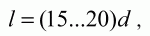
где l и d – длина и диаметр фундаментного болта, мм.
Диаметр фундаментного болта определяется по выражению:
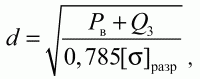
где Q3 – затягивающая сила на болтах (Q3 = 4РВ), H;
РВ – вырывающая сила, Н:
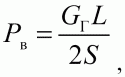
где GГ – сила горизонтального смещения, Н;
L – расстояние от точки приложения силы GГ до верхней плоскости фундамента, мм;
S – расстояние между болтами, мм;
[σ]разр – допустимое напряжение разрушения материала, МПа.
Поставка и прием оборудования. Для рациональной организации монтажных работ необходима комплектная поставка оборудования. Правила поставки оборудования следующие:
• малогабаритное оборудование (теплообменники, сосуды, трубные секции и т. д.) должно поставляться в собранном виде, на подкладках, с установленными внутренними устройствами и деталями для строповки;
• защитные покрытия свинцом, медью, лаком, эмалью выполняются на заводе-изготовителе, а футеровка кирпичом и плиткой на месте монтажа;
• крупногабаритное оборудование поставляется максимально укрупненными блоками с соответствующей маркировкой;
• поставляемое оборудование должно иметь ответные фланцы на штуцерах, а также крепежные детали и анкерные болты.
Порядок транспортировки оборудования по железной дороге и реке следующий:
• по железной дороге допускается перевозка машин и аппаратов по согласованию с Министерством путей сообщения массой до 240 т, диаметром 4 м и длиной 30 м;
• по рекам на судах: диаметром до 8 м и длиной до 55 м, а с буксировкой на плаву: диаметром до 10 м и длиной до 100 м по согласованию с Министерством речного флота.
Прием оборудования в монтаж производится на складе путем осмотра без разборки на узлы и детали. При этом проверяют:
• соответствие оборудования чертежам и проектной спецификации;
• комплектность оборудования по упаковочным ведомостям;
• наличие и полноту технической документации завода-изготовителя;
• отсутствие трещин, поломок и т. п.
При приеме оборудования допускается наличие дефектов в пределах определенных норм, которые приведены в табл. 3 для емкостных аппаратов.
Таблица 3. Нормы дефектов на поставку оборудования
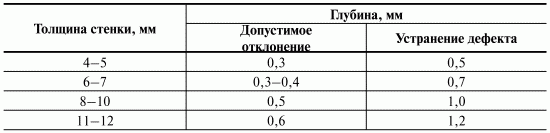
• назначение машины и аппарата;
• сведения об условиях работы (давление, температура);
• способы и параметры испытания;
• данные о материале прокладок и набивок;
• таблицу штуцеров;
• указание об антикоррозийной защите;
• спецификацию деталей и узлов с указанием веса;
• комплектовочную и маркировочную ведомости для крупногабаритного оборудования и инструкцию по сборке его узлов;
• зарегистрированную книгу для аппаратов, подведомственных Госгортехнадзору;
• указания по установке и креплению оборудования;
• указания по тепловой изоляции.
Прием и сдача оборудования в монтаж оформляется специальным актом.
Общие правила производства монтажных работ включают в себя:
• монтаж оборудования проводят преимущественно днем;
• монтаж нельзя проводить на открытых площадках при ветре более шести баллов, при дожде, снегопаде, гололеде;
• подъем груза должен доводиться до проектного положения, если это не удалось сделать до конца смены, то груз должен быть опущен на нулевую отметку;
• груз при подъеме должен быть надежно застропован, т. е. стропы налагаются равномерно без узлов и перекруток и угол между ветвями строп не должен быть больше 90°;
• расстроповку груза проводят только после его установки и надежного закрепления.
Глава 2
Общие методы и средства монтажа
2.1. Монтажная разметка
Монтажная разметка включает в себя соответственно разметку расположения монтажных осей во всех помещениях и устройство физических аналогов монтажных осей.
Координаты монтажных осей находят путем плоскопараллельного переноса строительных осей в горизонтальном и вертикальном напра влениях, поворотом или наклоном их на заданный угол к горизонтальной плоскости, рис. 4. Обеспечение горизонтальности основных и вспомогательных монтажных осей и содержащих их плоскостей обеспечиваются нивелировкой. Устройство физических аналогов монтажных осей (обычно на высоте 2–2,2 м) заключается в натяжении струны, закрепленной жестко одним концом к строительным конструкциям и переброшенной через ролик другим концом с натяжным грузом и строго совпадающей в натянутом состоянии с положением монтажной оси. Для этой цели используют капроновую, шелковую, нейлоновую нити либо стальную проволоку диаметром 0,3–0,5 мм с массой натяжных грузов соответственно 7–20 к г, обеспечивающей усилие натяжения струны, соответствующее до 2/3 разрывной нагрузки последней. Стрела прогиба струны диаметром 0,5 мм при расстоянии между точками ее крепления 5; 10 или 15 м не должна превышать 24; 86 или 160 мкм, что согласовывается с допустимыми отклонениями в расположении монтируемого оборудования.
Соответствие положения струны монтажной оси обеспечивается путем вертикального и горизонтального перемещения одной из точек ее закрепления, выполняемой в виде кронштейна с двумя взаимно перпендикулярными микрометрическими винтами, рис. 5.
Используя натертый мелом (углем) шнур, производят отбивку проекций монтажной оси на перекрытии. Для этого шнур натягивают и прижимают в отмеченных точках – проекциях струны и, оттянув его, резко отпускают, вследствие чего при ударе на размечаемой поверхности остается мелованный след.
Перенос монтажных осей в соседние помещения возможен при использовании имеющихся в стене проектных (дверной проем, вентиляционное отверстие и т. д.) либо специально выполненных отверстий, через которые пропускают параллельную строительной оси струну, служащую базой для разметки монтажных осей в соседних помещениях. Аналогично этому с помощью отвесов осуществляют перенос монтажных осей на выше– или нижележащие этажи.
Отмеченные на перекрытии проекции являются рабочими монтажными осями, по которым размечают опорную поверхность для установки машины, геометрию и координаты отверстий для ее крепления и расположения материалопроводов, передач и других элементов. В случае группового монтажа однотипных машин для разметки опорной поверхности целесообразно применять шаблон из листового материала или рамы, что существенно сокращает затраты времени на разметку и значительно повышает ее точность.
Рис. 5 – Варианты устройства монтажных осей: а – микрометрическое координатное устройство; б – кронштейн для крепления струны; в – подвешивание струны на колоннах; 1 – вертикальная направляющая; 2 – горизонтальная направляющая; 3 – подвижный корпус; 4 – ролик для струны; 5 – регулировочная гайка; 6 – стопорная гайка.
При разметке помещений под монтаж оборудования важным является нанесение на стены линий, отмечающих уровень чистых полов.
Проверку размеров по высоте проводят с помощью нивелира от постоянной точки, высота которой заранее известна. Такая точка называется репером, а численное значение высоты – отметкой. Высотным репером может служить заклепка диаметром 25–30 мм, приваренная к арматуре фундамента или к пластине и залитая цементным раствором соответственно рис. 6.
Рис. 6. Схемы установки контрольных осевых плашек и высотных реперов.
Верхняя скругленная поверхность репера служит началом отсчета всех высотных отметок.
Высотные отметки наносят по гидростатическим уровням, точность которых ±1–2 мм. Гидростатический уровень состоит из прозрачных разградуированных трубок, соединенных резиновым шлангом и заполненных закрашенной водой, рис. 7.
При расположении трубок на требуемом расстоянии одна от другой по закону сообщающихся сосудов уровень воды в них будет одинаковым, а линия, соединяющая мениски жидкости в трубках, – горизонтальной (см. пунктирную линию АБ). Установив одну из трубок возле репера, а вторую – рядом с местом, куда необходимо перенести отметку, производят отсчет. Зная длину горизонтальной линии между менисками L и проектный уклон, можно определить величину требуемого снижения по шкале второй трубки. Если переносимая отметка Н выше репера, то отсчет высоты производят вверх.
Рис. 7. Схема применения гидростатических уровней: а – обычного; б – с дополнительным бачком; 1 – трубки; 2 – шланги; 3 – бачок; 4 – репер.
Установку оборудования с более высокой точностью (до 0,5 мм) проверяют геодезическим инструментом – нивелиром. Геодезическую проверку при монтаже целесообразно осуществлять в том случае, если оборудование имеет значительную длину (ленточные транспортеры, скребковые конвейеры).
Координаты монтажных осей находят путем плоскопараллельного переноса строительных осей в горизонтальном и вертикальном напра влениях, поворотом или наклоном их на заданный угол к горизонтальной плоскости, рис. 4. Обеспечение горизонтальности основных и вспомогательных монтажных осей и содержащих их плоскостей обеспечиваются нивелировкой. Устройство физических аналогов монтажных осей (обычно на высоте 2–2,2 м) заключается в натяжении струны, закрепленной жестко одним концом к строительным конструкциям и переброшенной через ролик другим концом с натяжным грузом и строго совпадающей в натянутом состоянии с положением монтажной оси. Для этой цели используют капроновую, шелковую, нейлоновую нити либо стальную проволоку диаметром 0,3–0,5 мм с массой натяжных грузов соответственно 7–20 к г, обеспечивающей усилие натяжения струны, соответствующее до 2/3 разрывной нагрузки последней. Стрела прогиба струны диаметром 0,5 мм при расстоянии между точками ее крепления 5; 10 или 15 м не должна превышать 24; 86 или 160 мкм, что согласовывается с допустимыми отклонениями в расположении монтируемого оборудования.
Соответствие положения струны монтажной оси обеспечивается путем вертикального и горизонтального перемещения одной из точек ее закрепления, выполняемой в виде кронштейна с двумя взаимно перпендикулярными микрометрическими винтами, рис. 5.
Используя натертый мелом (углем) шнур, производят отбивку проекций монтажной оси на перекрытии. Для этого шнур натягивают и прижимают в отмеченных точках – проекциях струны и, оттянув его, резко отпускают, вследствие чего при ударе на размечаемой поверхности остается мелованный след.
Перенос монтажных осей в соседние помещения возможен при использовании имеющихся в стене проектных (дверной проем, вентиляционное отверстие и т. д.) либо специально выполненных отверстий, через которые пропускают параллельную строительной оси струну, служащую базой для разметки монтажных осей в соседних помещениях. Аналогично этому с помощью отвесов осуществляют перенос монтажных осей на выше– или нижележащие этажи.
Отмеченные на перекрытии проекции являются рабочими монтажными осями, по которым размечают опорную поверхность для установки машины, геометрию и координаты отверстий для ее крепления и расположения материалопроводов, передач и других элементов. В случае группового монтажа однотипных машин для разметки опорной поверхности целесообразно применять шаблон из листового материала или рамы, что существенно сокращает затраты времени на разметку и значительно повышает ее точность.
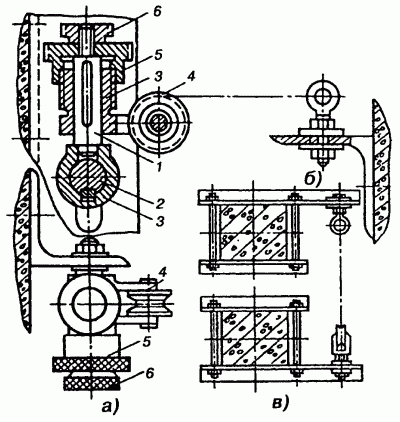
При разметке помещений под монтаж оборудования важным является нанесение на стены линий, отмечающих уровень чистых полов.
Проверку размеров по высоте проводят с помощью нивелира от постоянной точки, высота которой заранее известна. Такая точка называется репером, а численное значение высоты – отметкой. Высотным репером может служить заклепка диаметром 25–30 мм, приваренная к арматуре фундамента или к пластине и залитая цементным раствором соответственно рис. 6.
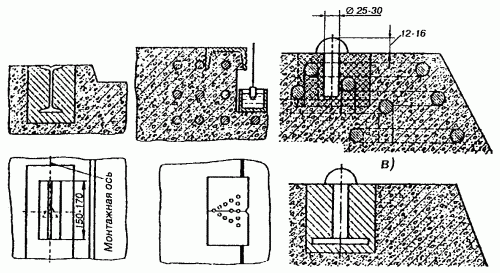
Верхняя скругленная поверхность репера служит началом отсчета всех высотных отметок.
Высотные отметки наносят по гидростатическим уровням, точность которых ±1–2 мм. Гидростатический уровень состоит из прозрачных разградуированных трубок, соединенных резиновым шлангом и заполненных закрашенной водой, рис. 7.
При расположении трубок на требуемом расстоянии одна от другой по закону сообщающихся сосудов уровень воды в них будет одинаковым, а линия, соединяющая мениски жидкости в трубках, – горизонтальной (см. пунктирную линию АБ). Установив одну из трубок возле репера, а вторую – рядом с местом, куда необходимо перенести отметку, производят отсчет. Зная длину горизонтальной линии между менисками L и проектный уклон, можно определить величину требуемого снижения по шкале второй трубки. Если переносимая отметка Н выше репера, то отсчет высоты производят вверх.
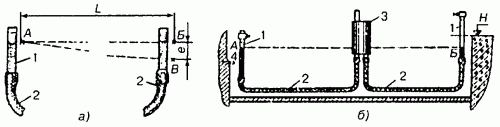
Установку оборудования с более высокой точностью (до 0,5 мм) проверяют геодезическим инструментом – нивелиром. Геодезическую проверку при монтаже целесообразно осуществлять в том случае, если оборудование имеет значительную длину (ленточные транспортеры, скребковые конвейеры).
2.2. Выверка и закрепление оборудования ПТЛ на фундаменте
Опирание оборудования на фундамент может быть сплошным, местным и комбинированным. Варианты подобных опираний приведены на рис. 8.
Закрепляют оборудование фундаментными болтами трех типов: анкерными, т. е. болтами, имеющими анкерующее устройство (рис. 8, а), прямыми (рис. 8, в) и распорного типа (рис. 8, б). Анкерные болты применяются до монтажа оборудования и до бетонирования фундамента. Прямые и распорного типа болты устанавливают в пробуриваемые в фундаменте скважины (отверстия) после установки оборудования. Глубина скважин (отверстий) должна быть не менее пяти диаметров болта. Болты распорного типа размещать ближе, чем десять диаметров болта, к краю фундамента недопустимо. Оборудование может крепиться и обычными болтами (винтами) к закладным деталям.
Рис. 8. Варианты опирания оборудования с помощью фундаментных болтов: а – сплошное; б – местное; в – комбинированное.
При монтаже оборудования не допускается придерживать машину (узел) за барабан, шкивы, открывающиеся крышки и другие подвижные (съемные) элементы. Кроме того, при предварительной установке оборудования (перед окончательным опусканием) допускается прикладывать усилие, отталкивая узел (машину) от себя соответственно рис. 9.
Рис. 9. Приложение усилия при наведении монтажного оборудования в проектное положение: <– допустимое приложение усилия; <-||– допустимое приложение усилия; 1 – монтажные оси; 2 – ось оборудования; 3 – монтажник; 4 – оборудование.
Широко распространен способ регулирования положения оборудования, устанавливаемого со сплошным опиранием на подливку. В этом случае опорные элементы (установленные предварительно) служат только для совмещения положения осей оборудования и монтажных осей.
Применяют различные, регулируемые по высоте опорные элементы: отжимные винты, винтовые опоры, пакеты подкладок, рис. 10.
Суммарная грузоподъемность опорных элементов, размещать которые следует как можно ближе к фундаментным болтам, должна в 2 раза превышать силу тяжести монтируемого узла. При этом минимально допускаемая площадь опирания всех элементов должна быть:
Формула № 9.
где М – масса оборудования, т;
n – число фундаментных болтов;
а – площадь поперечного сечения фундаментного болта, см2, выбираемого по графику рисунка 11.
Рис. 10. Регулируемые по размеру опорные элементы: а – винт отжимной; б – винтовая опора; в – пакет прокладок; 1 – регулировочный винт; 2 – стопорная гайка; 3 – опорная пластина; 4 – опорная часть оборудования; 5 – фундаментный болт; 6 – болт; 7 – гайка.
Рис. 11. Площадь поперечного сечения (а) и момент затяжки болтов (Т) в зависимости от их диаметра.
Положение оборудования при выверке:
• в плане контролируют струнным, струнно-оптическим методом, боковым нивелированием теодолитами, способом прямого контроля линейных размеров;
• по высоте контролируют относительно рабочих реперов геометрическим или тригонометрическим нивелированием, гидростатическим методом или измерением размеров от промежуточной базы до репера;
• по горизонтали контролируют с применением уровней, нивелиров, отвесов и теодолитов.
После выверки выполняется предварительное закрепление оборудования, при этом затягивают гайки только тех фундаментных болтов, которые расположены вблизи опорных элементов. После этого вновь контролируют положение осей оборудования, затем выполняется подливка бетона (наращивание фундамента), которая и воспринимает эксплуатационную нагрузку от оборудования. При этом условии фундамент получается более жестким, прочным и виброустойчивым. По достижении бетоном 70 % проектной прочности окончательно затягивают болты (момент затяжки принимается согласно рис. 11) равномерно в два-три обхода. Общее правило при затяжке болтов: вначале затягивают болты, расположенные по осям симметрии опорной части, затем более удаленные от оси симметрии. Для некоторых случаев последовательность затяжки приведена на рис. 12. Для качественного сцепления подливаемого бетона с поверхностью фундамента и монтируемого оборудования эти поверхности очищают от посторонних предметов, пыли, обезжиривают и промывают чистой водой, не допуская скопления воды в углублениях и приямках.
Рис. 12. Последовательность затяжки болтов: а – опирание на линии; б, в – опирание на плоскость.
Марку бетона для подливки используют не ниже марки бетона фундамента, а размер элементов фракции заполнителя (щебень, гравий) составляет 5–20 мм. Толщина слоя подливки должна быть не менее 50 мм. При ширине опорной части базовой детали оборудования более 2 м толщину слоя подливки следует принимать равной 80–100 мм.
Бетонную смесь с применением вибраторов подают через отверстия в опорной части или с одной стороны подливаемой детали до тех пор, пока с противоположной стороны смесь не достигнет уровня, на 20–30 мм превышающего высоту основной части подливки. Расстояние от опорной части оборудования до края слоя подливки должно составлять 100–200 мм. Поверхность подливки, примыкающей к основной части оборудования, должна иметь уклон в сторону от оборудования, равный 1: 50.
Последовательность сплошного опирания на подливку при выверке оборудования отжимным винтом и закрепления анкерным болтом, устанавливаемым в специальном колодце, показана на рисунках 12, 13.
Рис. 13. Схема установки, выверки и подливки бетона: а – установка анкерного болта в колодце оборудования; б – заливка установленных болтов; в – подливка бетона; 1 – монтируемое оборудование; 2 – анкерный болт; 3 – трубка, изолирующая участок болта от сцепления с бетоном; 4 – брусок; 5 – отжимной винт; 6 – опорная подкладка отжимного винта.
Закрепляют оборудование фундаментными болтами трех типов: анкерными, т. е. болтами, имеющими анкерующее устройство (рис. 8, а), прямыми (рис. 8, в) и распорного типа (рис. 8, б). Анкерные болты применяются до монтажа оборудования и до бетонирования фундамента. Прямые и распорного типа болты устанавливают в пробуриваемые в фундаменте скважины (отверстия) после установки оборудования. Глубина скважин (отверстий) должна быть не менее пяти диаметров болта. Болты распорного типа размещать ближе, чем десять диаметров болта, к краю фундамента недопустимо. Оборудование может крепиться и обычными болтами (винтами) к закладным деталям.
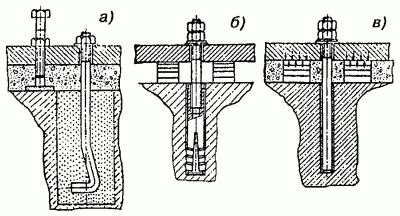
При монтаже оборудования не допускается придерживать машину (узел) за барабан, шкивы, открывающиеся крышки и другие подвижные (съемные) элементы. Кроме того, при предварительной установке оборудования (перед окончательным опусканием) допускается прикладывать усилие, отталкивая узел (машину) от себя соответственно рис. 9.
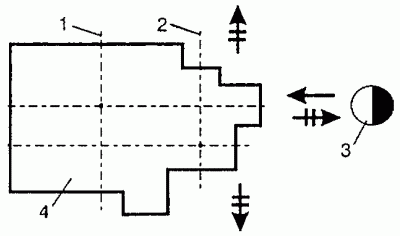
Широко распространен способ регулирования положения оборудования, устанавливаемого со сплошным опиранием на подливку. В этом случае опорные элементы (установленные предварительно) служат только для совмещения положения осей оборудования и монтажных осей.
Применяют различные, регулируемые по высоте опорные элементы: отжимные винты, винтовые опоры, пакеты подкладок, рис. 10.
Суммарная грузоподъемность опорных элементов, размещать которые следует как можно ближе к фундаментным болтам, должна в 2 раза превышать силу тяжести монтируемого узла. При этом минимально допускаемая площадь опирания всех элементов должна быть:

где М – масса оборудования, т;
n – число фундаментных болтов;
а – площадь поперечного сечения фундаментного болта, см2, выбираемого по графику рисунка 11.
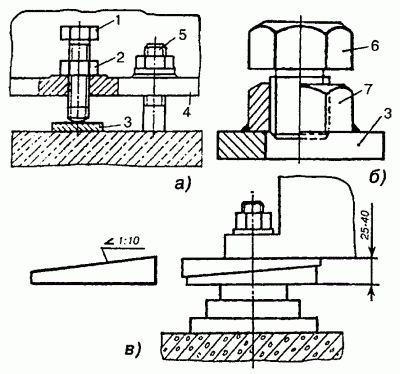
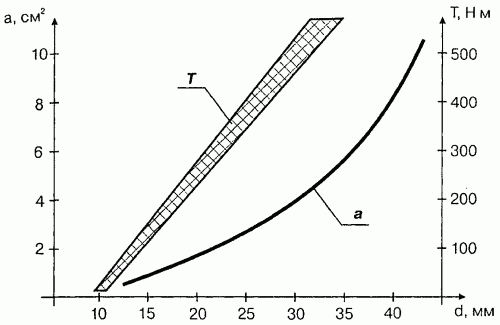
Положение оборудования при выверке:
• в плане контролируют струнным, струнно-оптическим методом, боковым нивелированием теодолитами, способом прямого контроля линейных размеров;
• по высоте контролируют относительно рабочих реперов геометрическим или тригонометрическим нивелированием, гидростатическим методом или измерением размеров от промежуточной базы до репера;
• по горизонтали контролируют с применением уровней, нивелиров, отвесов и теодолитов.
После выверки выполняется предварительное закрепление оборудования, при этом затягивают гайки только тех фундаментных болтов, которые расположены вблизи опорных элементов. После этого вновь контролируют положение осей оборудования, затем выполняется подливка бетона (наращивание фундамента), которая и воспринимает эксплуатационную нагрузку от оборудования. При этом условии фундамент получается более жестким, прочным и виброустойчивым. По достижении бетоном 70 % проектной прочности окончательно затягивают болты (момент затяжки принимается согласно рис. 11) равномерно в два-три обхода. Общее правило при затяжке болтов: вначале затягивают болты, расположенные по осям симметрии опорной части, затем более удаленные от оси симметрии. Для некоторых случаев последовательность затяжки приведена на рис. 12. Для качественного сцепления подливаемого бетона с поверхностью фундамента и монтируемого оборудования эти поверхности очищают от посторонних предметов, пыли, обезжиривают и промывают чистой водой, не допуская скопления воды в углублениях и приямках.
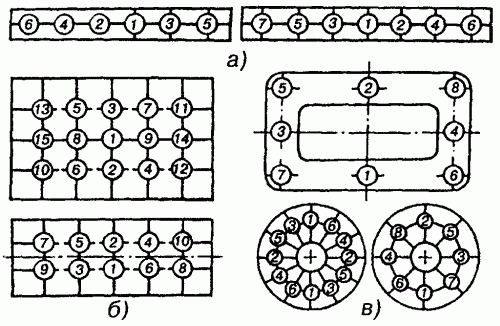
Марку бетона для подливки используют не ниже марки бетона фундамента, а размер элементов фракции заполнителя (щебень, гравий) составляет 5–20 мм. Толщина слоя подливки должна быть не менее 50 мм. При ширине опорной части базовой детали оборудования более 2 м толщину слоя подливки следует принимать равной 80–100 мм.
Бетонную смесь с применением вибраторов подают через отверстия в опорной части или с одной стороны подливаемой детали до тех пор, пока с противоположной стороны смесь не достигнет уровня, на 20–30 мм превышающего высоту основной части подливки. Расстояние от опорной части оборудования до края слоя подливки должно составлять 100–200 мм. Поверхность подливки, примыкающей к основной части оборудования, должна иметь уклон в сторону от оборудования, равный 1: 50.
Последовательность сплошного опирания на подливку при выверке оборудования отжимным винтом и закрепления анкерным болтом, устанавливаемым в специальном колодце, показана на рисунках 12, 13.
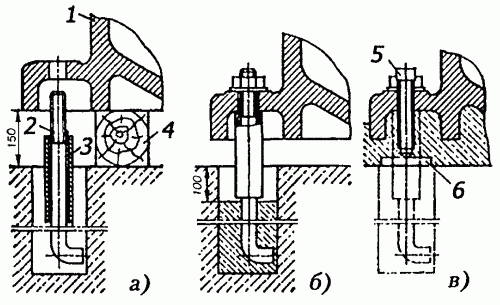
2.3. Монтажные средства
2.3.1. Канаты
При производстве монтажных работ используются стальные канаты, из органических и синтетических волокон в качестве оттяжек и строп грузовых канатов для лебедок (полиспастов).
Канаты из органических волокон (пеньковые, сизалевые) применяют при подъеме небольших грузов, для оттяжек и строп, для наведения поднятых грузов на нужное место. Такие канаты бывают пропитанные смолой, составом Е-1 и не пропитанные – бельные. Канаты из синтетических волокон могут быть использованы и в полиспастах при небольшой нагрузке. При нагрузке, близкой к разрывной, удлинение канатов из органических волокон составляет до 20 %, из синтетических – до 50 %. Канаты из искусственных волокон не гниют, почти не поглощают воду (не замерзают), имеют хорошие диэлектрические свойства, но подвержены плавлению при высоких температурах (вблизи сварочных работ применять не допускается).
Используются и комбинированные канаты – «пенька-сталь», изготовленные из стальной оцинкованной проволоки и пеньковой (сизальской) пряди.
Рис. 14. Сравнительные характеристики не стальных канатов (q – линейная плотность, Fр – разрывное усилие).
В маркировке не стальных канатов первые две буквы означают наименование каната (ПБ – пеньковый белый; ПС – пеньковый, пропитанный смолой; КК – канат капроновый), последующие две цифры – линейная плотность каната, указывается в контекстах (контекст – масса (в кг) 1 км длины), две последующие буквы – группа по исполнению (Пв – повышенной прочности, Об – обыкновенные, Сп – специальные).
Основные параметры, характеризующие данные типы канатов, приведены на рис. 14.
Для строповки оборудования в качестве тягового органа в талях используют и цепи. Преимущество цепей в том, что они не разрушаются при высоких температурах, более гибки, чем канаты.
Стальные канаты при той же разрушающей нагрузке, что и цепи, имеют значительно меньшую (примерно в 10 раз) массу, лучше воспринимают рывки, бесшумны в работе, разрываются постепенно.
Выбор каната производится по величине разрушающей нагрузки
Формула № 10.
где Fmax – максимальная нагрузка на канат, Н;
S – запас прочности, Н.
Значение запаса прочности принимают согласно таблице 4.
Маркировка стальных канатов. Первые две (три) буквы означают характер контакта проволок между собой в пряди (ЛК – линейный контакт, ТК – точечный контакт), следующие (через дефис) буквы показывают, какие проволоки в прядях (Р – разных диаметров, О – одинаковых). Цифры, допустим, 6x19+1 ОС показывают, что в канате 6 прядей, в каждой из которых 19 проволочек, один органический сердечник (ОС) или металлический (МС).
Пример: ЛК-РО (6x36+7x7) (канат двойной свивки). Здесь ЛК – линейный контакт, Р – проволоки в верхних прядях разного диаметра, О – проволоки во внутренних прядях одного диаметра, 6x36 – 6 прядей (вторая свивка) по 36 проволочек в каждой, 7x7 – 7 прядей (первая свивка) по 7 проволочек в каждой.
Эксплуатация канатов включает: хранение, разматывание, резание, испытание, выполнение концевых креплений (оконцевание), смазывание, освидетельствование.
Канаты из органических волокон (пеньковые, сизалевые) применяют при подъеме небольших грузов, для оттяжек и строп, для наведения поднятых грузов на нужное место. Такие канаты бывают пропитанные смолой, составом Е-1 и не пропитанные – бельные. Канаты из синтетических волокон могут быть использованы и в полиспастах при небольшой нагрузке. При нагрузке, близкой к разрывной, удлинение канатов из органических волокон составляет до 20 %, из синтетических – до 50 %. Канаты из искусственных волокон не гниют, почти не поглощают воду (не замерзают), имеют хорошие диэлектрические свойства, но подвержены плавлению при высоких температурах (вблизи сварочных работ применять не допускается).
Используются и комбинированные канаты – «пенька-сталь», изготовленные из стальной оцинкованной проволоки и пеньковой (сизальской) пряди.
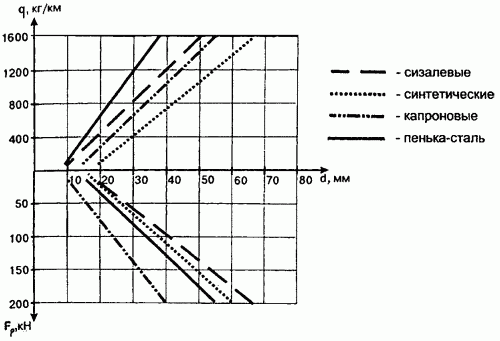
В маркировке не стальных канатов первые две буквы означают наименование каната (ПБ – пеньковый белый; ПС – пеньковый, пропитанный смолой; КК – канат капроновый), последующие две цифры – линейная плотность каната, указывается в контекстах (контекст – масса (в кг) 1 км длины), две последующие буквы – группа по исполнению (Пв – повышенной прочности, Об – обыкновенные, Сп – специальные).
Основные параметры, характеризующие данные типы канатов, приведены на рис. 14.
Для строповки оборудования в качестве тягового органа в талях используют и цепи. Преимущество цепей в том, что они не разрушаются при высоких температурах, более гибки, чем канаты.
Стальные канаты при той же разрушающей нагрузке, что и цепи, имеют значительно меньшую (примерно в 10 раз) массу, лучше воспринимают рывки, бесшумны в работе, разрываются постепенно.
Выбор каната производится по величине разрушающей нагрузки
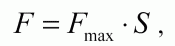
где Fmax – максимальная нагрузка на канат, Н;
S – запас прочности, Н.
Значение запаса прочности принимают согласно таблице 4.
Таблица 4. Запас прочности канатов

Пример: ЛК-РО (6x36+7x7) (канат двойной свивки). Здесь ЛК – линейный контакт, Р – проволоки в верхних прядях разного диаметра, О – проволоки во внутренних прядях одного диаметра, 6x36 – 6 прядей (вторая свивка) по 36 проволочек в каждой, 7x7 – 7 прядей (первая свивка) по 7 проволочек в каждой.
Эксплуатация канатов включает: хранение, разматывание, резание, испытание, выполнение концевых креплений (оконцевание), смазывание, освидетельствование.