2. Сборку секций рамы конвейера выполняют на специально заготовленном кондукторе для соблюдения прямоугольности, прямолинейности, избежания скручиваний. Если секции поставляют в собранном виде, то на этом кондукторе проверяют их отклонение от формы.
Рис. 51. Ленточный транспортер: 1 – приводная станция; 2 – натяжная станция; 3 – секции рамы транспортера; 4 – роликоопоры груженой ветви; 5 – роликоопоры холостой ветви; 6 – рулон ленты; 7 – узел соединения с канатом лебедки; I, II – позиции лебедки при укладке ленты; а, б – оси приводной и натяжной станций; с – продольная ось транспортера; е – оси роликоопор.
3. Проводят разметку продольной оси транспортера.
4. Устанавливают приводную станцию. Выверяют горизонтальность оси приводного барабана, ее перпендикулярность продольной оси конвейера. Допустимое отклонение от горизонтальности – 0,2 мм на 1 м длины барабана. Электродвигатель узла привода транспортера монтируют по выверенному валу приводного барабана. Закрепляют приводную станцию к фундаменту.
5. Устанавливают последовательно секции рамы транспортера. С помощью прокладок выставляют их в проектное положение и временно закрепляют между собой болтовыми соединениями.
6. Выполняют монтаж натяжной станции. Проверяют горизонтальность оси натяжного барабана, ее параллельность оси приводного барабана.
7. Проводят выверку положения всей конструкции: допустимое отклонение продольной оси ленточного транспортера от проектного положения – не более 1 мм на 10 м длины транспортера. После этого крепят раму секций натяжной станции к фундаменту и сваривают секции между собой.
8. Устанавливают роликоопоры (рис. 52). Смещение середины роликоопоры от продольной оси транспортера – не более 1 мм, а роликоопор по высоте – не более ± 1 мм. Проверяется горизонтальность оси роликоопор и их перпендикулярность продольной оси. Для улучшения центрирования ленты каждую пятую-шестую роликоопору устанавливают наклоном на 2–3° по ходу ленты (рис. 53, а). С этой же целью могут использоваться и самоустанавливающиеся роликоопоры (рис. 53, б), которые монтируют чуть выше остальных.
Рис. 52. Схема выверки положения роликоопор при монтаже: а– по ширине; 6 – по высоте; с – продольная ось транспортера.
Рис. 53. Самоцентрирующее положение ленты опоры: а– наклоненная роликоопора; б – самоустанавливающаяся роликоопора.
9. На элеваторах, складах для сыпучего материала используют транспортеры с разгрузочными тележками. При установке тележки обеспечивают горизонтальность барабанов и проверяют шаблоном ширину колеи (отклонение не более 2 мм). Допустимая несимметричность относительно оси транспортера до 2 мм. Отклонение высоты левого и правого путей до 1 мм. Зазор в стыке до 2 мм, разность уровней в стыке рельсов до 0,3 мм.
10. Выполняют монтаж ленты. Рулон с лентой (см. рис. 51) устанавливают на козлы. При этом следят за тем, чтобы толстая (рабочая) резиновая обкладка ленты была обращена наружу. Затягивают ленту с помощью лебедки, устанавливая ее в положение I, затем II.
11. Смещают натяжной барабан в сторону приводного до упора.
12. Стягивают концы ленты до совмещения внахлестку на необходимую длину с помощью полиспаста или лебедки (рис. 54).
Рис. 54. Схема стяжки концов ленты.
13. Осуществляют стыковку ленты. Иногда сначала выполняют временную стыковку ленты (на 1–1,5 месяца). Это делается из-за того, что в этот период ленты вытягиваются наиболее интенсивно. Но обычно стыкуют концы постоянно – вулканизируют их. При выборе метода соединения конвейерных лент следует учитывать, что прочность вулканизированного, крючкового, планчатого (на болтах) соединений составляет соответственно 0,9; 0,6; 0,45 от прочности ленты.
14. Натягивают ленту с помощью натяжной станции – перемещением барабана. Прокручивают вручную, затем 2–3 раза электродвигателем. Если при этом лента смещается вбок («биг») более чем на 25 мм от середины барабана, то устраняют негоризонтальность и непараллельность осей барабанов, а также устраняют возможное осевое смещение барабанов по валу, неравномерную вытяжку ленты, перекос роликоопор, счищают грязь, пыль с барабана, проверяют легкость вращения роликоопор.
15. Выполняют монтаж загрузочного устройства (рис. 55). Загрузочный лоток монтируют симметрично относительно продольной оси, так как односторонняя загрузка ленты вызывает ее сход в сторону. Металлические части лотка не должны касаться ленты. Для исключения просыпей груза к нижней части лотка крепятся прорезиненные накладки.
Рис. 55. Схема загрузочного лотка: 1 – лоток; 2 – прорезиненная накладка
3.1.1. Особенности монтажа криволинейного участка транспортирования груза
3.1.2. Склеивание транспортерной ленты
3.1.3. Эксплуатация ленточного транспортера
3.2. Ковшовые конвейеры (нории)
3.2.1. Последовательность монтажа нории
3.2.2. Эксплуатация нории
3.2.3. Обслуживание нории
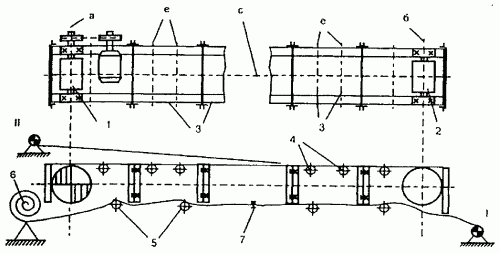
3. Проводят разметку продольной оси транспортера.
4. Устанавливают приводную станцию. Выверяют горизонтальность оси приводного барабана, ее перпендикулярность продольной оси конвейера. Допустимое отклонение от горизонтальности – 0,2 мм на 1 м длины барабана. Электродвигатель узла привода транспортера монтируют по выверенному валу приводного барабана. Закрепляют приводную станцию к фундаменту.
5. Устанавливают последовательно секции рамы транспортера. С помощью прокладок выставляют их в проектное положение и временно закрепляют между собой болтовыми соединениями.
6. Выполняют монтаж натяжной станции. Проверяют горизонтальность оси натяжного барабана, ее параллельность оси приводного барабана.
7. Проводят выверку положения всей конструкции: допустимое отклонение продольной оси ленточного транспортера от проектного положения – не более 1 мм на 10 м длины транспортера. После этого крепят раму секций натяжной станции к фундаменту и сваривают секции между собой.
8. Устанавливают роликоопоры (рис. 52). Смещение середины роликоопоры от продольной оси транспортера – не более 1 мм, а роликоопор по высоте – не более ± 1 мм. Проверяется горизонтальность оси роликоопор и их перпендикулярность продольной оси. Для улучшения центрирования ленты каждую пятую-шестую роликоопору устанавливают наклоном на 2–3° по ходу ленты (рис. 53, а). С этой же целью могут использоваться и самоустанавливающиеся роликоопоры (рис. 53, б), которые монтируют чуть выше остальных.
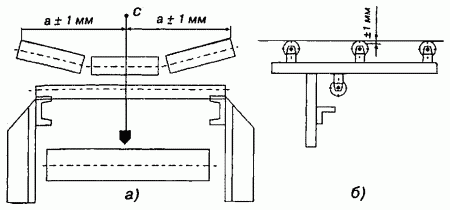
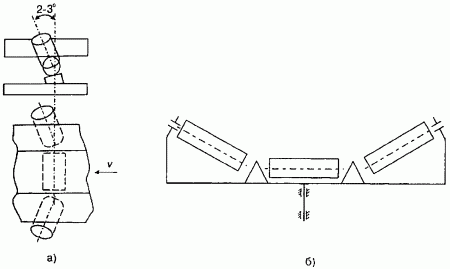
9. На элеваторах, складах для сыпучего материала используют транспортеры с разгрузочными тележками. При установке тележки обеспечивают горизонтальность барабанов и проверяют шаблоном ширину колеи (отклонение не более 2 мм). Допустимая несимметричность относительно оси транспортера до 2 мм. Отклонение высоты левого и правого путей до 1 мм. Зазор в стыке до 2 мм, разность уровней в стыке рельсов до 0,3 мм.
10. Выполняют монтаж ленты. Рулон с лентой (см. рис. 51) устанавливают на козлы. При этом следят за тем, чтобы толстая (рабочая) резиновая обкладка ленты была обращена наружу. Затягивают ленту с помощью лебедки, устанавливая ее в положение I, затем II.
11. Смещают натяжной барабан в сторону приводного до упора.
12. Стягивают концы ленты до совмещения внахлестку на необходимую длину с помощью полиспаста или лебедки (рис. 54).
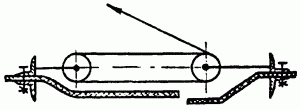
13. Осуществляют стыковку ленты. Иногда сначала выполняют временную стыковку ленты (на 1–1,5 месяца). Это делается из-за того, что в этот период ленты вытягиваются наиболее интенсивно. Но обычно стыкуют концы постоянно – вулканизируют их. При выборе метода соединения конвейерных лент следует учитывать, что прочность вулканизированного, крючкового, планчатого (на болтах) соединений составляет соответственно 0,9; 0,6; 0,45 от прочности ленты.
14. Натягивают ленту с помощью натяжной станции – перемещением барабана. Прокручивают вручную, затем 2–3 раза электродвигателем. Если при этом лента смещается вбок («биг») более чем на 25 мм от середины барабана, то устраняют негоризонтальность и непараллельность осей барабанов, а также устраняют возможное осевое смещение барабанов по валу, неравномерную вытяжку ленты, перекос роликоопор, счищают грязь, пыль с барабана, проверяют легкость вращения роликоопор.
15. Выполняют монтаж загрузочного устройства (рис. 55). Загрузочный лоток монтируют симметрично относительно продольной оси, так как односторонняя загрузка ленты вызывает ее сход в сторону. Металлические части лотка не должны касаться ленты. Для исключения просыпей груза к нижней части лотка крепятся прорезиненные накладки.
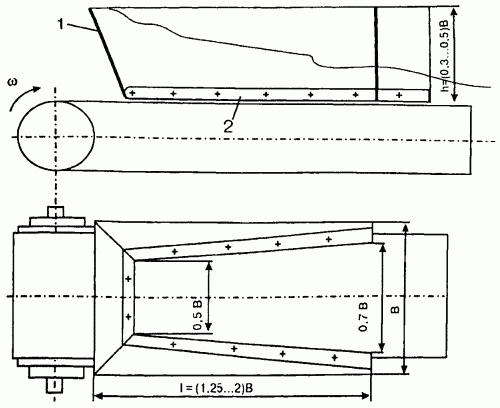
3.1.1. Особенности монтажа криволинейного участка транспортирования груза
Нередко возникает необходимость криволинейного транспортирования с применением ленточных конвейеров. Это объясняется тем, что прием груза после конвейера производится выше горизонтального участка (рис. 56).
Рис. 56. Ленточный конвейер.
Кривая линия провисания ленты, образованная действием силы тяжести ленты и груза, является параболой. Очевидно, что роликовые опоры следует ставить, строго ориентируясь на обеспечение линии провисания. В случае, если роликоопоры будут установлены выше или ниже, то желоб линии будет нарушаться, а груз рассыпаться.
В зависимости от расположения опор ленты (рис. 57) при постоянном ее натяжении возможны случаи, когда опора расположена на параболе и совпадает с низшей точкой параболы или расположена выше нее – слева или справа.
Рис. 57. Эпюра к выбору положения нижней опоры.
Расположение опоры левее низшей точки потребует некоторого снижения высоты расположения последующих роликоопор, что неприемлемо как по конструктивным соображениям, так и из-за того, что груз опять придется поднять на эту же высоту. При расположении опоры правее низшей точки часть траектории, предшествующая опоре О2 (от опоры О2 до следующей роликоопоры), будет стремиться расположиться по параболической кривой, и лента будет провисать.
С учетом этого наиболее приемлемо расположение опоры в низшей точке параболы. В этом случае стрела провисания, равная разности высот расположения опор, будет определяться как:
Формула № 43.
где g – ускорение свободного падения, м/с2;
q – линейная плотность (погонная масса) ленты и груза, Н/м;
l – расстояние (пролет) между опорами, м;
F – натяжение ленты, Н.
Натяжение ленты определяют на основе метода обход, по контуру или по несущей способности ленты:
Формула № 44.
где [Кр] – допускаемая линейная прочность одной прокладки ленты на разрыв, Н/м;
В – ширина ленты, м;
z – число прокладок ленты;
[S] = 9–11 – запас прочности ленты.
Линейную плотность находят как q = qл + qг,
где qл – погонная масса ленты, кг/м;
qг = П/V – погонная масса груза, кг/м;
П – производительность транспортера, кг/с;
V – скорость транспортера, м/с.
Расчет погонной массы ленты находят как qл = 1,12·B·δ,
где В – ширина ленты, мм;
δ = δ0·z + δ1 + δ2 – толщина ленты, мм;
δ0 = 1,2–2,0 мм – толщина прокладки, мм;
δ1 = 1-10 мм – толщина рабочей обкладки ленты, мм;
δ2 = 1–3,5 мм – толщина нерабочей обкладки ленты, мм.
Расстояние между роликоопорами при ширине ленты 400-1200 мм рекомендуется принимать в пределах lp= 1,0–1,5 м.
Учитывая, что угол наклонного (криволинейного) участка конвейера незначительный, для удобства монтажа можно принять, что проекция расстояния между роликоопорами равна расстоянию между ними.
Таким образом, определив значение lp рассчитывается необходимое h.
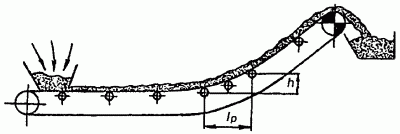
Кривая линия провисания ленты, образованная действием силы тяжести ленты и груза, является параболой. Очевидно, что роликовые опоры следует ставить, строго ориентируясь на обеспечение линии провисания. В случае, если роликоопоры будут установлены выше или ниже, то желоб линии будет нарушаться, а груз рассыпаться.
В зависимости от расположения опор ленты (рис. 57) при постоянном ее натяжении возможны случаи, когда опора расположена на параболе и совпадает с низшей точкой параболы или расположена выше нее – слева или справа.
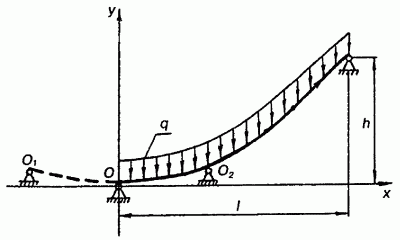
Расположение опоры левее низшей точки потребует некоторого снижения высоты расположения последующих роликоопор, что неприемлемо как по конструктивным соображениям, так и из-за того, что груз опять придется поднять на эту же высоту. При расположении опоры правее низшей точки часть траектории, предшествующая опоре О2 (от опоры О2 до следующей роликоопоры), будет стремиться расположиться по параболической кривой, и лента будет провисать.
С учетом этого наиболее приемлемо расположение опоры в низшей точке параболы. В этом случае стрела провисания, равная разности высот расположения опор, будет определяться как:
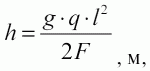
где g – ускорение свободного падения, м/с2;
q – линейная плотность (погонная масса) ленты и груза, Н/м;
l – расстояние (пролет) между опорами, м;
F – натяжение ленты, Н.
Натяжение ленты определяют на основе метода обход, по контуру или по несущей способности ленты:
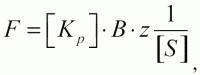
где [Кр] – допускаемая линейная прочность одной прокладки ленты на разрыв, Н/м;
В – ширина ленты, м;
z – число прокладок ленты;
[S] = 9–11 – запас прочности ленты.
Линейную плотность находят как q = qл + qг,
где qл – погонная масса ленты, кг/м;
qг = П/V – погонная масса груза, кг/м;
П – производительность транспортера, кг/с;
V – скорость транспортера, м/с.
Расчет погонной массы ленты находят как qл = 1,12·B·δ,
где В – ширина ленты, мм;
δ = δ0·z + δ1 + δ2 – толщина ленты, мм;
δ0 = 1,2–2,0 мм – толщина прокладки, мм;
δ1 = 1-10 мм – толщина рабочей обкладки ленты, мм;
δ2 = 1–3,5 мм – толщина нерабочей обкладки ленты, мм.
Расстояние между роликоопорами при ширине ленты 400-1200 мм рекомендуется принимать в пределах lp= 1,0–1,5 м.
Учитывая, что угол наклонного (криволинейного) участка конвейера незначительный, для удобства монтажа можно принять, что проекция расстояния между роликоопорами равна расстоянию между ними.
Таким образом, определив значение lp рассчитывается необходимое h.
3.1.2. Склеивание транспортерной ленты
Это наиболее трудоемкая и ответственная операция. Стык склеивают непосредственно на транспортере. На раму транспортера под ленту при снятых роликоопорах устанавливают деревянный щит, который шире рамы на 0,2–0,3 м и на 1 м длиннее стыка.
Зажимы стяжного приспособления (см. рис. 54) устанавливаются строго перпендикулярно продольной оси ленты. После чего концы ленты стягивают внахлестку на всю длину стыка. Стыкуемые концы накладывают друг на друга и проверяют параллельность кромок. Для обеспечения одинаковой прочности стыкового соединения и самой ленты, а также для того, чтобы стык плавно набегал на ролики и барабаны, концы ленты отрезают наискось (рис. 58).
Рис. 58. Схема подготовки ленты к вулканизации.
Угол скоса 18°30’ (катет в треугольнике равен 1/3 В). После этого подготавливают ступенчатый стык на обоих концах ленты. Для этого размечают размеры средних ступенек длиной 250–300 мм, крайние ступеньки делают больше остальных на 1/3. Ступеньку готовят следующим образом. Надрезают (поперек) по линии последней ступени до первой прокладки резиновую обкладку, с помощью отвертки отслаивают ее немного от каркаса. Затем эту обкладку надрезают вдоль полосами по 25–30 мм и открывают их клещами. Далее надрезают прокладку по линии границы другой ступени так, чтобы не повредить следующую прокладку. После чего подрезают эту прокладку полосами на 25–30 мм и отрывают полосы. Резиновые обкладки ленты на обеих ее сторонах срезают на скос. Стыкуемые поверхности аккуратно зачищают (шерохуют) дисковым пористым камнем или металлической щеткой, протирают бензином, сушат 15 мин. На стыкуемые поверхности кистью наносят клей, сушат 20–30 мин, затем вновь наносят и сушат 10–15 мин. На горизонтальные поверхности стыка накладывают куски каландрованной резины толщиной 0,5 мм, к вертикальным поверхностям прикатывают полоски каландрованной резины шириной 3–5 мм и толщиной 1,5 мм. Накладывают стыки один на другой, прикатывают их роликом, прокалывают шилом для выхода остатков воздуха. На оба торца накладывают брекер шириной 100 мм, а на него – резиновую заготовку толщиной на 1,5–2,0 мм больше резиновой обкладки.
Устанавливают с обеих сторон ленты пресс-вулканизатор, стягивают ленту до давления на стыке не менее 1 МПа. Продолжительность вулканизации определяют как: t = 5·z, мин, где z – число прокладок ленты.
Температура (150 ± 2)°С. Отсчет времени начинают с момента постижения рабочей температуры. Пуск ленты возможен только после ее охлаждения до 30 °C.
Зажимы стяжного приспособления (см. рис. 54) устанавливаются строго перпендикулярно продольной оси ленты. После чего концы ленты стягивают внахлестку на всю длину стыка. Стыкуемые концы накладывают друг на друга и проверяют параллельность кромок. Для обеспечения одинаковой прочности стыкового соединения и самой ленты, а также для того, чтобы стык плавно набегал на ролики и барабаны, концы ленты отрезают наискось (рис. 58).
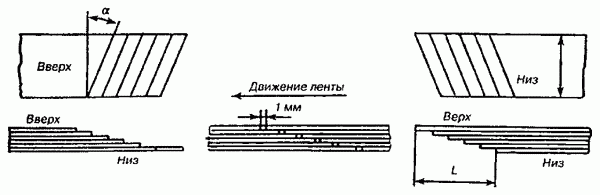
Угол скоса 18°30’ (катет в треугольнике равен 1/3 В). После этого подготавливают ступенчатый стык на обоих концах ленты. Для этого размечают размеры средних ступенек длиной 250–300 мм, крайние ступеньки делают больше остальных на 1/3. Ступеньку готовят следующим образом. Надрезают (поперек) по линии последней ступени до первой прокладки резиновую обкладку, с помощью отвертки отслаивают ее немного от каркаса. Затем эту обкладку надрезают вдоль полосами по 25–30 мм и открывают их клещами. Далее надрезают прокладку по линии границы другой ступени так, чтобы не повредить следующую прокладку. После чего подрезают эту прокладку полосами на 25–30 мм и отрывают полосы. Резиновые обкладки ленты на обеих ее сторонах срезают на скос. Стыкуемые поверхности аккуратно зачищают (шерохуют) дисковым пористым камнем или металлической щеткой, протирают бензином, сушат 15 мин. На стыкуемые поверхности кистью наносят клей, сушат 20–30 мин, затем вновь наносят и сушат 10–15 мин. На горизонтальные поверхности стыка накладывают куски каландрованной резины толщиной 0,5 мм, к вертикальным поверхностям прикатывают полоски каландрованной резины шириной 3–5 мм и толщиной 1,5 мм. Накладывают стыки один на другой, прикатывают их роликом, прокалывают шилом для выхода остатков воздуха. На оба торца накладывают брекер шириной 100 мм, а на него – резиновую заготовку толщиной на 1,5–2,0 мм больше резиновой обкладки.
Устанавливают с обеих сторон ленты пресс-вулканизатор, стягивают ленту до давления на стыке не менее 1 МПа. Продолжительность вулканизации определяют как: t = 5·z, мин, где z – число прокладок ленты.
Температура (150 ± 2)°С. Отсчет времени начинают с момента постижения рабочей температуры. Пуск ленты возможен только после ее охлаждения до 30 °C.
3.1.3. Эксплуатация ленточного транспортера
До начала работы следует проверить исправность заземления электродвигателей, пусковых устройств, всех узлов транспортера, тормозов передвижной разгрузочной тележки, наличие ограждений, натяжение ленты.
После обкатки вхолостую испытывают транспортер под нагрузкой. Груз подается только после разгона ленты до нормальной скорости, останавливают транспортер только после того, как лента освободится от груза. Необходимо следить, чтобы лента при движении опиралась на все роликовые опоры. Натяжная станция должна автоматически поддерживать натяжение в зависимости от массы груза.
При обслуживании ленточных конвейеров не разрешается:
• допускать во время работы конвейера сбегание ленты в сторону, в результате этого снижается производительность и увеличивается расход энергии;
• пользоваться палками или другими предметами в качестве дополнительной опоры для предотвращения сбегания ленты;
• допускать буксование ленты конвейера, это вызывает повышенный расход электроэнергии, преждевременный износ ленты, а при длительном буксовании лента может загореться и вызвать пожар;
• пользоваться канифолью или другими вяжущими веществами для увеличения сцепления ленты конвейера с ободом приводного барабана независимо от причины буксования;
• тянуть руками ленту, помогая ходу при пуске конвейера;
• проводить ремонтные работы при работе конвейера.
После обкатки вхолостую испытывают транспортер под нагрузкой. Груз подается только после разгона ленты до нормальной скорости, останавливают транспортер только после того, как лента освободится от груза. Необходимо следить, чтобы лента при движении опиралась на все роликовые опоры. Натяжная станция должна автоматически поддерживать натяжение в зависимости от массы груза.
При обслуживании ленточных конвейеров не разрешается:
• допускать во время работы конвейера сбегание ленты в сторону, в результате этого снижается производительность и увеличивается расход энергии;
• пользоваться палками или другими предметами в качестве дополнительной опоры для предотвращения сбегания ленты;
• допускать буксование ленты конвейера, это вызывает повышенный расход электроэнергии, преждевременный износ ленты, а при длительном буксовании лента может загореться и вызвать пожар;
• пользоваться канифолью или другими вяжущими веществами для увеличения сцепления ленты конвейера с ободом приводного барабана независимо от причины буксования;
• тянуть руками ленту, помогая ходу при пуске конвейера;
• проводить ремонтные работы при работе конвейера.
3.2. Ковшовые конвейеры (нории)
В перерабатывающих предприятиях нории используются в основном для перемещения сыпучих грузов. Основные узлы нории показаны на рис. 59.
Согласно ГОСТ 10190-70 введено разделение нории на тихоходные (тип I) и быстроходные (тип II). В нориях первого типа скорость ленты 1–1,8 м/с, и зерно из ковшей разгружается под действием сил тяжести. Такую разгрузку называют гравитационной. Эти нории используют в основном для семенного зерна, так как меньше его травмируют.
Рис. 59. Основные узлы нории (схема монтажа): 1 – головка нории; 2 – башмак; 3 – норийные трубы; 4 – лента с ковшами; 5 – отклоняющий ролик; 6 – загрузочный носок; 7 – натяжное устройство; 8 – съемная стенка; 9 – приводной барабан; 10– смотровые люки; 11 – аспирационная труба; 12– приводная станция; а, б, с, е, к – контролируемые при монтаже размеры; с = е = 100–130 мм, к = 60–80 мм.
В большинстве случаев используют нории второго типа, в них скорость ленты 2,2–3,6 м/с, и продукт из ковша выбрасывается центробежными силами (центробежная разгрузка).
Нории со скоростью ленты более 5 м/с используют очень редко из-за плохой загрузки, травмирования зерна.
Характеристика норий, используемых на современных элеваторах, приведена в табл. 13 (отдельные параметры ковша нории указаны на рис. 60).
Рис. 60. Параметры ковша нории: a – расстояние между центрами болтов; b – ширина; I – вылет; h – высота; в – ширина ленты.
В качестве несущего элемента в нориях используют ленты 5-820 (055), БКНЛ-65 (65), ТА-150 (150), ТК-300 (300). В скобках указана прочность на разрыв (Н/мм). Благодаря высокой прочности современных лент с синтетической основой, уже не являются исключением высота транспортирования 80 м и производительность до 1000 т/ч.
Согласно ГОСТ 10190-70 введено разделение нории на тихоходные (тип I) и быстроходные (тип II). В нориях первого типа скорость ленты 1–1,8 м/с, и зерно из ковшей разгружается под действием сил тяжести. Такую разгрузку называют гравитационной. Эти нории используют в основном для семенного зерна, так как меньше его травмируют.
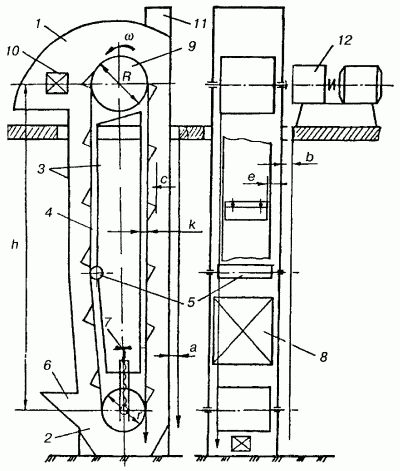
В большинстве случаев используют нории второго типа, в них скорость ленты 2,2–3,6 м/с, и продукт из ковша выбрасывается центробежными силами (центробежная разгрузка).
Нории со скоростью ленты более 5 м/с используют очень редко из-за плохой загрузки, травмирования зерна.
Характеристика норий, используемых на современных элеваторах, приведена в табл. 13 (отдельные параметры ковша нории указаны на рис. 60).
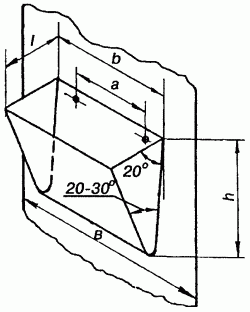
Таблица 13. Характеристика элеваторной нории
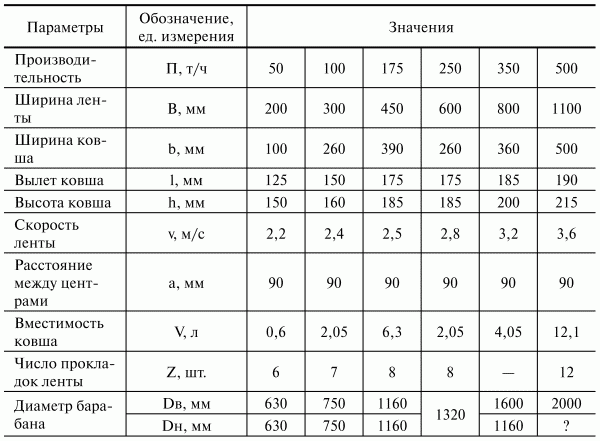
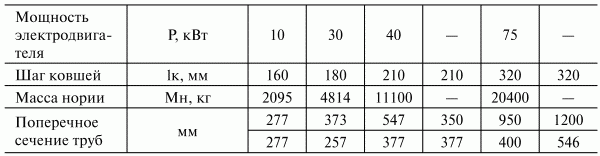
3.2.1. Последовательность монтажа нории
1. Проверка прямоугольности, прямолинейности и отсутствия скручивания норийных труб (на специальном кондукторе).
2. Вытяжка ленты в течение двух-трех суток. Ее перекидывают через барабан и натяжением создают напряжение в ленте, равное 3,0–3,5 Н/мм2. В процессе вытяжки проверяют параллельность кромок. Возможный перекос устраняют перевешиванием груза с вытянутой ленты на середину.
3. Разметка и пробивка (сверление) отверстия под ковши на ленте производятся по шаблону на столе. Шаблон – стальной лист толщиной 2 мм, длиной 1,2 м и шириной, равной ширине ленты.
4. Установка верхнего шаблона (горизонтально) или верхней головки нории (горизонтально).
5. Разметка монтажных осей, начиная с верхнего этажа, для этого опускают отвесы до места установки башмака.
6. Установка башмака в сборе. Выверка горизонтальности плоскости верхних фланцев.
7. Монтаж секций норийных труб (снизу вверх). Отклонение норийной трубы не более 1,5 мм. Для выполнения этого условия между фланцами устанавливают прокладки. Вертикальность обеспечивается расклиниванием норийных труб в проемах деревянными клиньями.
8. Монтаж верхней головки. При этом проверяют, находятся ли торцевые плоскости верхнего и нижнего барабанов в одной плоскости.
9. Поднятие натяжным устройством нижнего барабана в крайнее верхнее положение.
10. Монтаж ленты. Необходимую ее длину L определяют как:
Формула № 45.
где h, R, r – размеры нории (см. рис. 58), мм;
l – длина места сшивки внахлест, l = 1000 мм.
Ленту затягивают канатом на барабан через монтажное отверстие (рис. 61, а) либо опускают сверху (рис. 61, б). При опускании сверху ленту предварительно наматывают на монтажный барабан в два слоя.
Рис. 61. Монтаж ленты: а– через монтажный люк; б – через отверстия сверху; в – устранение скручивания ленты.
Для устранения перекручивания ленты в трубе к концу ленты крепят пластину длиной, равной диагонали трубы (рис. 61, в).
После того, как лента опустится до нижнего барабана, ее с помощью каната (лебедки) вытаскивают вверх. Концы ленты стягивают так же, как и концы ленточных транспортеров, двумя полиспастами. Скрепляют концы ленты у норий малой производительности встык с отбортовкой зажимными уголками (рис. 62, а), внахлест (рис. 62, б) или накладкой (рис. 62, в).
11. Установка ковшей (см. рис. 62). На ленте ковши устанавливают в монтажном люке или у верхнего барабана. Для того, чтобы лента самопроизвольно не опускалась, ковши монтируют партиями: устанавливают 50–60 шт. и опускают ленту вниз, затем еще 50–60 шт. и т. д.
12. Натяжение ленты. Ее прокручивают вручную, затем 2–3 раза электродвигателем. Если при этом лента смещается вбок («биг») более чем на 25 мм от середины барабана, то устраняют негоризонтальность положения осей барабанов, возможное осевое смещение барабана по валу, наклон нории, перекос в стыковке, неравномерную вытяжку ленты, обратное высыпание зерна, счищают грязь и пыль с барабана.
Рис. 62. Соединение ленты нории и крепления ковша: а– встык с отбортовкой; б – внахлест; в – с накладками.
2. Вытяжка ленты в течение двух-трех суток. Ее перекидывают через барабан и натяжением создают напряжение в ленте, равное 3,0–3,5 Н/мм2. В процессе вытяжки проверяют параллельность кромок. Возможный перекос устраняют перевешиванием груза с вытянутой ленты на середину.
3. Разметка и пробивка (сверление) отверстия под ковши на ленте производятся по шаблону на столе. Шаблон – стальной лист толщиной 2 мм, длиной 1,2 м и шириной, равной ширине ленты.
4. Установка верхнего шаблона (горизонтально) или верхней головки нории (горизонтально).
5. Разметка монтажных осей, начиная с верхнего этажа, для этого опускают отвесы до места установки башмака.
6. Установка башмака в сборе. Выверка горизонтальности плоскости верхних фланцев.
7. Монтаж секций норийных труб (снизу вверх). Отклонение норийной трубы не более 1,5 мм. Для выполнения этого условия между фланцами устанавливают прокладки. Вертикальность обеспечивается расклиниванием норийных труб в проемах деревянными клиньями.
8. Монтаж верхней головки. При этом проверяют, находятся ли торцевые плоскости верхнего и нижнего барабанов в одной плоскости.
9. Поднятие натяжным устройством нижнего барабана в крайнее верхнее положение.
10. Монтаж ленты. Необходимую ее длину L определяют как:

где h, R, r – размеры нории (см. рис. 58), мм;
l – длина места сшивки внахлест, l = 1000 мм.
Ленту затягивают канатом на барабан через монтажное отверстие (рис. 61, а) либо опускают сверху (рис. 61, б). При опускании сверху ленту предварительно наматывают на монтажный барабан в два слоя.
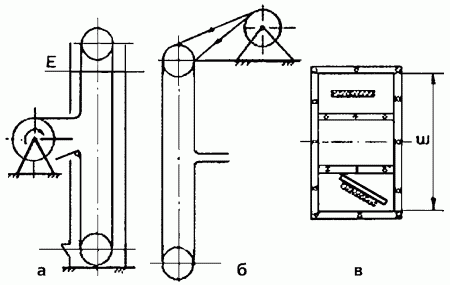
Для устранения перекручивания ленты в трубе к концу ленты крепят пластину длиной, равной диагонали трубы (рис. 61, в).
После того, как лента опустится до нижнего барабана, ее с помощью каната (лебедки) вытаскивают вверх. Концы ленты стягивают так же, как и концы ленточных транспортеров, двумя полиспастами. Скрепляют концы ленты у норий малой производительности встык с отбортовкой зажимными уголками (рис. 62, а), внахлест (рис. 62, б) или накладкой (рис. 62, в).
11. Установка ковшей (см. рис. 62). На ленте ковши устанавливают в монтажном люке или у верхнего барабана. Для того, чтобы лента самопроизвольно не опускалась, ковши монтируют партиями: устанавливают 50–60 шт. и опускают ленту вниз, затем еще 50–60 шт. и т. д.
12. Натяжение ленты. Ее прокручивают вручную, затем 2–3 раза электродвигателем. Если при этом лента смещается вбок («биг») более чем на 25 мм от середины барабана, то устраняют негоризонтальность положения осей барабанов, возможное осевое смещение барабана по валу, наклон нории, перекос в стыковке, неравномерную вытяжку ленты, обратное высыпание зерна, счищают грязь и пыль с барабана.
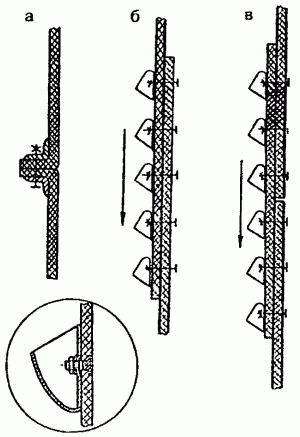
3.2.2. Эксплуатация нории
Нория требует тщательного технического обслуживания, осмотра, контроля за работой.
Нория – мощный пылеисточник. Возникновение в ней известного «треугольника взрыва» наиболее вероятно.
Вследствие вытяжки ленты возможно буксование ее на барабане. При самопроизвольном опускании груженой ветви образуется завал в нижней части нории (нория «завалилась»). Запускать такую норию, не вычистив завал от груза, нельзя, так как двигатель при этом перегружается в 3 раза и более, лента буксует или разрывается.
Нория – мощный пылеисточник. Возникновение в ней известного «треугольника взрыва» наиболее вероятно.
Вследствие вытяжки ленты возможно буксование ее на барабане. При самопроизвольном опускании груженой ветви образуется завал в нижней части нории (нория «завалилась»). Запускать такую норию, не вычистив завал от груза, нельзя, так как двигатель при этом перегружается в 3 раза и более, лента буксует или разрывается.
3.2.3. Обслуживание нории
При обслуживании норий необходимо выполнять следующие требования:
• норийные трубы, башмаки, колпаки головок и смотровые люки в своих соединениях должны быть герметичными и не пропускать пыль и зерно, в случае обнаружения неисправности необходимо устранить;
• при необходимости расчистки башмака нории от завала рабочий должен убедиться в том, что привод нории выключен, поставлен на тормоз и возможность обратного хода исключена;
• чистить башмак нории от продукта нужно только специальным скребком с гладкой ручкой. При этом следует быть особенно осторожным, чтобы в случае непроизвольного обратного хода норийной ленты ковшами не захватило руки;
• после ликвидации завала нории надо выявить причины завала и принять меры к их устранению (слабо закрепленные и оторванные ковши, слабое натяжение ленты или нарушение ее центровки и т. п.);
• не разрешается спускаться и работать в норийных приемниках, если они не освещены;
• запрещается ремонтировать нории на ходу. Перед началом ремонта необходимо выключить электродвигатель, а на пусковую аппаратуру повесить специальную табличку с надписью «Не включать, ремонт, работают люди»;
• необходимо следить за исправностью заземления токоприемников и изоляции электроприводов. При возникновении неисправностей следует вызвать электромонтера.
Для автоматического контроля за работой нории используют датчик скорости ДМ-12 (помещают на приводном барабане) и датчик уровня МДУ-2с (устанавливают в нижнем башмаке).
Буксование можно оценить по разности скоростей барабанов.
С целью исключения буксования барабанов делают футеровку (шевронную, колосовидную) барабана резиной или устанавливают приводной барабан большего диаметра.
• норийные трубы, башмаки, колпаки головок и смотровые люки в своих соединениях должны быть герметичными и не пропускать пыль и зерно, в случае обнаружения неисправности необходимо устранить;
• при необходимости расчистки башмака нории от завала рабочий должен убедиться в том, что привод нории выключен, поставлен на тормоз и возможность обратного хода исключена;
• чистить башмак нории от продукта нужно только специальным скребком с гладкой ручкой. При этом следует быть особенно осторожным, чтобы в случае непроизвольного обратного хода норийной ленты ковшами не захватило руки;
• после ликвидации завала нории надо выявить причины завала и принять меры к их устранению (слабо закрепленные и оторванные ковши, слабое натяжение ленты или нарушение ее центровки и т. п.);
• не разрешается спускаться и работать в норийных приемниках, если они не освещены;
• запрещается ремонтировать нории на ходу. Перед началом ремонта необходимо выключить электродвигатель, а на пусковую аппаратуру повесить специальную табличку с надписью «Не включать, ремонт, работают люди»;
• необходимо следить за исправностью заземления токоприемников и изоляции электроприводов. При возникновении неисправностей следует вызвать электромонтера.
Для автоматического контроля за работой нории используют датчик скорости ДМ-12 (помещают на приводном барабане) и датчик уровня МДУ-2с (устанавливают в нижнем башмаке).
Буксование можно оценить по разности скоростей барабанов.
С целью исключения буксования барабанов делают футеровку (шевронную, колосовидную) барабана резиной или устанавливают приводной барабан большего диаметра.
Конец бесплатного ознакомительного фрагмента