Страница:
Если шляпки гвоздей не предполагается утапливать в массив, чтобы место соединения выглядело красиво и аккуратно, делают разметку для равномерного и аккуратного размещения гвоздей. Не обязательно вбивать большое количество гвоздей близко друг к другу. Достаточно прикрепить доску или другую деревянную деталь в 2–4 местах.
Когда в неширокую доску необходимо вбить несколько гвоздей, чтобы не допустить трещины деревянного массива, их следует располагать не по одной линии, а в шахматном порядке.
Острый гвоздь может легко расколоть тонкую заготовку. Чтобы этого не произошло, его острие нужно затупить легкими ударами молотка или откусить кусачками.
Если правильно расположить места для гвоздей, то этим можно предупредить возможное коробление и изгиб детали. Очень нежелательно забивать гвозди близко к торцевым частям доски, где древесина наиболее ослаблена – так можно спровоцировать образование трещины на всю длину детали.
В случае, когда предполагается поверхность изделия полировать, шляпки гвоздей или откусывают, как сказано выше, или с помощью специального инструмента – добойника – утапливают в массив. После этого место соединения шпаклюют и зашкуривают.
Извлечение из деревянной детали ненужного гвоздя – задача несложная, но требующая определенных навыков. Проще всего, если острый конец гвоздя выходит на оборотной стороне, выбить его молотком, чтобы шляпка поднялась над поверхностью.
При креплении с помощью шурупа практически не нарушается целостность внутренних слоев древесины, не происходит их смещение, как при креплении гвоздем. Это объясняется прежде всего тем, что шуруп ввинчивается, а не забивается. Шурупы к тому же выглядят намного эстетичнее, чем гвозди. Еще одно важное удобство – это то, что их можно в случае необходимости вывернуть из гнезд и разъединить соединенные детали. Однако соединения с применением таких крепежных элементов требуют значительно большего времени, чем гвоздевые.
Так же как и при вбивании гвоздя, нужно правильно выбрать диаметр и длину шурупа. Их длина может колебаться от 0,6 до 12–15 см и выше. Соответственно, чем длиннее шуруп, тем больше его диаметр. Для разных видов крепления и материалов заготовок предназначаются отдельные виды шурупов.
Шуруп должен быть на 3–4 мм больше, чем толщина прикрепляемой планки, чтобы она могла хорошо держаться на основе.
Номер шурупа (соотношение его длины и толщины) подбирают под определенный тип планки. Для самой тонкой планки подбирают шуруп длиной 6 мм, толстую планку крепят шурупом длиной 12–15 см. В зависимости от предназначения шурупа его шляпка может быть плоской (потайной) или полукруглой (выпуклой). Первый вид шляпки предназначен для крепления деталей мебели с последующей шпаклевкой. Такие шурупы не должны быть видны на поверхности. Второй тип шурупов предназначен как для крепления деталей, так и для украшения поверхности.
В зависимости от величины шурупа его завинчивают одним из двух способов. Если шуруп небольшой, а древесина мягкая, то можно ограничиться лишь пометкой шилом на поверхности в месте ввинчивания. Но если шуруп большой или его диаметр слишком велик, то в месте крепления просверливают дрелью, буравом или коловоротом небольшое отверстие, по глубине и по диаметру немногим меньше шурупа, чтобы он мог хорошо держаться в массиве. Если таким шурупом закрепляют две достаточно толстые планки, то просверливают обе детали, чтобы при ввинчивании не растрескалась древесина.
Чтобы скрыть шляпку шурупа в массиве, делают небольшое коническое углубление, ввинчивают шуруп до предела и зашпаклевывают.
Но в любом случае, независимо от величины шурупа, его вворачивают с помощью отвертки с подходящим размером и видом полотна. Отвертку вставляют в шлиц – небольшую прорезь на шляпке шурупа, крестообразной или прямой формы.
Чтобы облегчить свой труд при ввинчивании шурупов, можно воспользоваться несколькими уже проверенными способами.
При ввинчивании шурупа в массив твердой древесины его перед началом работы смазывают хозяйственным мылом. В том случае, если на поверхность крепления будет наноситься краска или оно будет находиться внутри изделия, в качестве смазки используют солидол или лыжную мазь. При желании оставшиеся небольшие жирные следы убирают спиртом или другим обезжиривающим средством.
При работе с древесно-стружечной плитой сначала просверливают отверстие чуть меньшее, чем шуруп, затем смазывают его клеем и вставляют в него кусок трубки из пластика, и только потом в модифицированное отверстие ввинчивают приготовленный шуруп.
Нередко случается, что шуруп необходимо ввинтить в торцовую часть доски или бруска. Такое крепление никогда не считалось прочным.
Но для того, чтобы увеличить прочность крепления, можно воспользоваться двумя приемами. Первый заключается в том, что просверленное под шуруп отверстие пропитывают древесным лаком на масляной или спиртовой основе. Второй способ усиления конструкции состоит в использовании нагеля, который вбивают в торец бруска, а уже в него ввинчивают шуруп.
В ходе работы случается и такое, что уже намертво ввинченный шуруп мешает соединению тех или иных деталей. Исправить это можно несколькими приемами.
Берут разводной гаечный ключ, фиксируют между его рамками полотно отвертки, которую потом устанавливают в шлиц шурупа. Затем немного нажимают на отвертку и поворачивают гаечный ключ. Даже самый старый и непокорный шуруп должен без труда вывинтиться.
При другом способе используют молоток. Сначала вставляют жало отвертки в шлиц, захватывают рукоятку отвертки всей рукой, чтобы открытой оставалась верхушка, и, осторожно ударяя молотком по верхушке, синхронно поворачивают отвертку.
Следующий способ поможет заменить шуруп с отколовшейся наполовину декоративной шляпкой. Для этого опять понадобится гаечный ключ, отвертка и тонкая небольшая деревянная дощечка.
Если шуруп завинчен недалеко от края, то можно просто воспользоваться гаечным ключом. Для этого крепко зажимают остатки уцелевшей половины и поворачивают ключ до тех пор, пока шуруп полностью не вывинтится.
Если же шуруп расположен посередине детали и воспользоваться одним гаечным ключом невозможно, то берут отвертку, устанавливают ее на место бывшего шлица и придвигают как можно ближе к ней приготовленную дощечку. Всю эту конструкцию фиксируют гаечным ключом, затем осторожно поворачивают ключ и следят за тем, чтобы он не сорвался.
Не следует заворачивать шурупы во влажную древесину, так как в этом случае они ржавеют и вокруг них возникают желтые пятна. Если все же потребуется осуществить такую операцию, то предварительно шурупы покрывают тонким слоем масла. То же самое делают при соединении деталей, которые будут подвергаться воздействию влажного воздуха, снега или дождя.
Можно использовать заклепки с потайной головкой, и тогда их можно будет зашпаклевать заподлицо с поверхностью и закрасить.
Длина и диаметр заклепок зависят от их назначения. Изготавливаются они как из твердых материалов, например ковких сталей, так и из мягких – сплавов меди или алюминия. При самостоятельном строительстве можно успешно использовать заклепки из цветных металлов: с ними легче работать, они обладают высокой прочностью, хотя и несколько уступают стальным.
Заклепки различают еще и по форме. Это связано с их назначением, они могут иметь головку: потайную, полупотайную, полукруглую или коническую. Первые применяют для того, чтобы поверхность клепанного шва была ровной, в остальных случаях используют заклепки любого другого типа (рис. 87).
Рис. 87. Виды заклепок: а – заклепка с потайной головкой; б – с полупотайной головкой; в – с полукруглой головкой; г – с конической головкой.
Чаще всего в домашних условиях используют заклепки от 2 до 8 мм. Длина заклепки должна быть такой, чтобы ее кончик выходил из отверстия в соединяемых деталях на 0,8–1,2 величины диаметра. Например, если диаметр заклепки 5 мм, то она должна выступать на 4–6 мм.
Определенная сложность применения заклепок определяет необходимость иметь набор специальных инструментов и приспособлений. Для работы потребуются следующие:
– поддержка– металлическая пластина с выемкой под головку заклепки;
– натяжка– стальной сердечник с неглубоким отверстием, высверленным по центральной оси;
– обжимка– тоже стальной сердечник, но с выемкой на торце.
Остальные инструменты применяют и в процессе других работ: молоток, дрель, сверла и конические зенковки для расточки верхних кромок отверстий.
Сначала на поверхности деталей, которые будут соединяться, чертят линию будущего шва и отмечают места под отверстия для заклепок. Расстояние от кромки детали до места заклепки определяют путем умножениея коэффициента 1,5 на величину диаметра самой заклепки (в миллиметрах). Чтобы определить шаг между отверстиями, величину диаметра умножают на коэффициент 3.
Пример: диаметр заклепки 5 мм, а значит, расстояние от кромки – 1,5 х 5 = 7,5 мм; 3 х 5 = 15 мм. Это шаг между отверстиями для заклепки.
После разметки линии шва и центров отверстий определяют диаметр сверла. Его подбирают на 0,1–0,2 мм больше, чем диаметр заклепки, а затем сверлят ряд отверстий. Если планируют использовать заклепки с потайными головками, то отверстия зенкуют коническими зенковками, то есть растачивают на конус. Глубина расточки составляет 0,8 диаметра заклепки.
При использовании заклепок с полупотайными, полукруглыми или коническими головками с отверстий снимают фаску на глубину 1,0–1,5 мм. Затем в него вставляют клепку и под ее головку подкладывают поддержку так, чтобы головка вошла в углубление. После этого легкими ударами молотка с помощью натяжки плотно сжимают детали между собой.
Следующий момент – это небольшое расплющивание выступающего кончика стержня заклепки, насаживание на него обжимки и формирование головки ударом молотка по ней. Точно так же обрабатывают все остальные заклепки шва (рис. 88).
Рис. 88. Последовательность установки заклепки.
При установке заклепок с потайной головкой можно вместо поддержки обойтись любой массивной металлической пластиной с плоской поверхностью. Хорошо для этих целей подходит небольшая наковальня. После установки заклепок их расплющенные выступающие концы обрабатывают напильником.
В том случае, если соединение должно быть подвижным, диаметр отверстия делают на 0,3–0,5 мм больше, чем диаметр заклепки, а под оба конца ее подкладывают металлические шайбы.
Для того чтобы разобрать соединение деталей, выступающие головки заклепок срубают зубилом, стачивают напильником или электронаждаком, потайные заклепки высверливают дрелью. Стержни, которые остаются в отверстиях, выбивают с помощью кернера.
В зависимости от толщины балок их диаметр может колебаться от 10 м до 30 мм, а по длине такие крепления могут достигать 70–90 см. При выборе размера болта обязательно должна учитываться толщина балки.
Чтобы установить болт в бревно, просверливают сквозное отверстие, чуть меньшее диаметра болта. Затем на выбранный болт надевают шайбу, которая предотвращает вдавливание шляпки болта в массив древесины. Надеваемая на болт контргайка предотвращает ослабление крепления.
Такой собранный болт вбивают в массив. Выступающий конец болта также снабжают шайбой и контргайкой. На него надевают гайку, которая до предела затягивает всю конструкцию.
Чтобы не сорвать резьбу, важно правильно определить длину ключа. Для этого величину диаметра резьбы, выраженную в миллиметрах, нужно умножить на 15. Например, диаметр резьбы равен 10 мм, при умножении получается, что гаечный ключ должен иметь длину 150 мм. Такой ключ позволит нормально затянуть гайку и позволит избежать срыва резьбы.
Правильно выполненное соединение – это когда концы болтов выступают над поверхностью гаек примерно на 2–3 витка резьбы.
Если конструкция, соединенная болтами, будет подвергаться атмосферным воздействиям, чтобы не допустить ржавчины, резьбу болтов и гаек перед завинчиванием покрывают тонким слоем машинного масла.
При отвинчивании туго затянутой гайки применяют ключ более длинный, чем при завинчивании. Если это не помогает, то можно попробовать осторожно постучать молотком по рукоятке надетого на гайку ключа так, чтобы сдвинуть ее с мертвой точки.
Задача существенно осложняется, если у гайки сорваны или скруглены углы ее граней. В этом случае их восстанавливают напильником.
Заржавевшее соединение перед отвинчиванием смачивают керосином, а наросты ржавчины сбивают легкими ударами молотка по головке винта и по бокам гайки. Поврежденную резьбу на выступающем конце болта исправляют с помощью тонкой ножовки по металлу или напильника.
Чаще всего для крепления несущих конструкций используют хомуты из нержавеющей стали, которые представляют собой полоски толщиной 8–16 мм и шириной от 28 до 105 мм. Хомуты могут быть прямоугольными, квадратными и круглыми и использоваться в зависимости от формы соединяемых деталей. На место крепления двух или более досок или балок устанавливают одну половину хомута, с другой стороны на этом же уровне устанавливают вторую часть и затягивают их болтами.
Вдоль пластины располагается несколько отверстий для закрепления накладок на древесине. Обычно соединяют их с помощью шурупов или болтов.
Лучшего соединения балок между собой достигают, взяв развернутую скобу, или s-образную. Концы такой скобы располагают параллельно друг другу. Если необходимо максимально закрепить деревянное соединение, то лучше всего использовать повернутую скобу, один конец которой загибают под углом 45°.
Глютеиновые клеибывают костными и мездровыми. Они относятся к клеям животного происхождения.
Мездровый делают из подкожного слоя шкур животных – мездры и обрезков шкур, отходов и т. д. Костный клей изготавливают из обезжиренных и очищенных костей, рогов и копыт. Обычная упаковка глютеиновых клеев – сухие плитки длиной 150–200 мм, шириной – 80–100 мм и толщиной – 10–15 мм. Встречается клей и в виде гранул, крупинок, опилок или чешуек. Эти виды более удобны, так как быстро набухают в процессе приготовления.
Костный клей может быть не только в сухом виде, но и в студнеобразном (галерта). Галерта позволяет быстро приготовить раствор для склеивания, но при использовании этого клея в него необходимо добавлять антисептики. Плиточный клей бывает разного цвета, от светло-желтого до темно-коричневого, это зависит от состава сырья.
Глютеиновые клеи бывают четырех сортов: высшего, первого, второго и третьего. Клей высшего качества должен быть стекловидным, светлым и при изломе оставлять острые края.
Рекомендуется хранить эти марки клея при температуре не более 15 °C в сухом проветриваемом помещении. Можно хранить клей в холодильнике, а галерту вообще не рекомендуется хранить долго.
Недостатком костных клеев является то, что они плохо реагируют на влажность, из-за чего их невозможно использовать для склеивания деревянных конструкций во влажных помещениях, например в подвалах, банях или на открытом воздухе.
Казеиновые клеиимеют в основе обезжиренный творог (молочный белок, или казеин). Кроме этого, в состав клея первого и второго сорта входят: гашеная известь, фтористый натрий, медный купорос и керосин. Марки казеиновых клеев отличаются составом. В марке «Экстра» (В-107), присутствуют перечисленные выше ингредиенты, а если это «Об» (обыкновенный), то в нем нет медного купороса, а казеин для него берется второго сорта.
Казеиновый клей представляет собой однородную массу беловато-желтого цвета. Его надо хранить в сухом проветриваемом помещении с температурой не выше 30 °C. При повышении температуры казеиновый клей теряет свои свойства.
Следует помнить, что уже через 5 мес хранения, начиная со дня выпуска, требуется проверить клей на прочность склеивания. При работе с древесиной казеиновый клей окрашивает ее поверхность, так как в качестве растворителя в нем используется щелочь.
Синтетические клеиполучили сейчас широкое распространение. Это карбамидные, меламино-мочевиноформальдегидные и др. Они водостойки, обладают противогрибковым эффектом, очень прочны. Промышленность выпускает их в различной форме: твердые, жидкие, пастообразные и порошкообразные.
Перед использованием таких клеев необходимо внимательно ознакомиться с инструкцией по их приготовлению, способам склеивания и руководствоваться принципами техники безопасности, так как клеи представляют определенную опасность для человека. Эпоксидный клейдает прочное соединение без высокого давления при запрессовке и является универсальным. Однако он требует очень тщательной подготовки поверхности для склеивания.
Время отвердевания эпоксидного клея при температуре воздуха 20 °C составляет 24 ч, при 60 °C – 4 ч, а при 120 °C – 2 ч.
Клей ПВА,или поливинилацетатная дисперсия, дает пластичное соединение. Клей довольно быстро схватывается и требует быстрого выполнения операции склеивания. ПВА представляет собой белую жидкость, которая при высыхании становится прозрачной. Клей может применяться для склеивания любых деревянных деталей.
Склеивание используют при соединениях на шип и на ус. Наклеивание применяют при изготовлении фанеры, при отделке поверхности шпоном и т. п.
Склеить детали можно двумя способами: сжав поверхности зажимами или притерев поверхности друг к другу после нанесения на них клея. Притиркой соединяют преимущественно тонкие детали, которые после небольшого схватывания подгоняют друг к другу и оставляют до полного высыхания клея.
Клеевое соединение деталей должно происходить быстро и четко, поэтому перед тем, как приступить к склеиванию, готовят все необходимое для работы: зажимы, прокладки, ленты, опоры, ремни, а также поверхности склеиваемых деталей, которые при необходимости очищают. Места загрязнения протирают ацетоном или спиртом.
Прокладки при склеивании используют для максимально равномерного распределения усилия при сжатии. Также они предохраняют поверхности от образования вмятин при зажиме струбцинами. Прокладку всегда делают чуть больше размера склеиваемых деталей. Чаще всего прокладки изготавливают из листов фанеры.
А чтобы избежать приклеивания поверхностей к прокладкам, подкладывают еще листы бумаги между прокладкой и поверхностью.
При склеивании способом сжатия обязательно следят за тем, чтобы при установке зажимов не произошло смещения поверхностей, которое потом уже невозможно будет восстановить.
Чтобы шов получился хорошим, прочным, работать лучше всего в комнате, где температура не опускается ниже 20 °C. Клей необходимо наносить тонким ровным слоем, при этом он не должен быть слишком жидким. Толстый слой клея недопустим, так как при высыхании он растрескивается.
Не надо стараться шлифовать склеиваемые поверхности – плоскости должны быть немного шероховатыми, это позволит получить более надежное соединение.
Если склеивают сразу несколько деталей, не наносят клей сразу на все – в нижних слоях клей начнет схватываться, но не будет равномерно распределен, поверхность получится волнами. Чтобы этого не случилось, детали разделяют на несколько частей, склеивают планки частей между собой, а потом уже части.
Склеивать лучше всего по уровням, например в один прием – ножки стульев, в другой – сиденья.
Если склеивают сложную конструкцию, состоящую из множества узлов, то сначала соединяют все детали без клея, подгоняют, если что-то выступает, и только потом наносят клей, так как явные дефекты при склеивании устранить не удастся и разобрать уже склеенную конструкцию без повреждений невозможно.
После нанесения клея на узлы конструкции ее кладут под пресс и выдерживают определенное время, чтобы клей полностью схватился и подсох. Если используют столярный клей, то вынуть деталь из-под пресса можно только через 1 сут. Клей ПВА требует меньше времени – всего 4–5 ч. Но это еще не означает, что клей полностью высох и конструкция готова к дальнейшей работе. После того как истекло необходимое время, ослабляют зажимы, проверяют, нет ли сдвигов слоев, и кладут еще на 1 сут, чтобы клей высох полностью.
Этот прием используют и при изготовлении мозаики, которая прекрасно украсит крышку любого стола, створки шкафа, тумбочку в спальне и т. п.
Хотя здесь и используют шпон ценных пород древесины, а сама работа требует внимательности и точности глаза, ее сможет выполнить даже человек, который никогда не имел дела с деревом. Это похоже на аппликацию из бумаги и картона. Но есть несколько особенностей, о которых необходимо помнить.
1. Приклеивать шпон нужно только на очень ровную поверхность, немного шероховатую, без видимых зазубрин (поверхность основы должна быть «бархатной»).
2. Шпон обязательно приклеивают поперек направления волокон основы, но не вдоль, иначе могут появиться трещины, портящие поверхность и возникающие из-за разной усадки шпона и основания.
3. Если используют дорогой шпон и наклеивают его на древесно-стружечную плиту, то обязательно наклеивают промежуточный слой из дешевого шпона или хлопчатобумажной ткани.
4. Используя шпон из капа или древесины с высокой свилеватостью, подбирают основу из тщательно высушенной древесины, чтобы потом не образовались трещины.
5. При наклеивании шпона на небольшие поверхности используют клей ПВА, а на большие – столярный клей, это делает наклеивание более качественным.
Так же как и склеивание, наклеивание ведется двумя способами: запрессованием и притиркой. И тот и другой способ выполняют в такой последовательности:
– сначала наносят на основу слой клея, затем накладывают на нее шпон, проглаживают чистой суконкой, тем самым удаляя из-под него все воздушные пузыри. После этого для лучшего соединения протирают сверху шпон губкой, пропитанной теплой водой.
Через 1–2 ч, когда клей начнет загустевать, притиркой проглаживают шпон по направлению волокон, стараясь не задирать кромки. Для этого все движения направляют к кромкам или по диагонали к ним;
– конструкцию оставляют до полного склеивания, положив предварительно листы белой бумаги на швы, кладут под пресс, уложив бумагу сверху на шпон, затем прокладку, и только потом зажимают струбцинами;
Когда в неширокую доску необходимо вбить несколько гвоздей, чтобы не допустить трещины деревянного массива, их следует располагать не по одной линии, а в шахматном порядке.
Острый гвоздь может легко расколоть тонкую заготовку. Чтобы этого не произошло, его острие нужно затупить легкими ударами молотка или откусить кусачками.
Если правильно расположить места для гвоздей, то этим можно предупредить возможное коробление и изгиб детали. Очень нежелательно забивать гвозди близко к торцевым частям доски, где древесина наиболее ослаблена – так можно спровоцировать образование трещины на всю длину детали.
В случае, когда предполагается поверхность изделия полировать, шляпки гвоздей или откусывают, как сказано выше, или с помощью специального инструмента – добойника – утапливают в массив. После этого место соединения шпаклюют и зашкуривают.
Извлечение из деревянной детали ненужного гвоздя – задача несложная, но требующая определенных навыков. Проще всего, если острый конец гвоздя выходит на оборотной стороне, выбить его молотком, чтобы шляпка поднялась над поверхностью.
Шурупы
Используя при креплении детали шурупы, получают более качественное и надежное крепление. Чаще всего шурупы используют для крепления дверных и оконных петель, ручек, штапиков, обкладок и т. п.При креплении с помощью шурупа практически не нарушается целостность внутренних слоев древесины, не происходит их смещение, как при креплении гвоздем. Это объясняется прежде всего тем, что шуруп ввинчивается, а не забивается. Шурупы к тому же выглядят намного эстетичнее, чем гвозди. Еще одно важное удобство – это то, что их можно в случае необходимости вывернуть из гнезд и разъединить соединенные детали. Однако соединения с применением таких крепежных элементов требуют значительно большего времени, чем гвоздевые.
Так же как и при вбивании гвоздя, нужно правильно выбрать диаметр и длину шурупа. Их длина может колебаться от 0,6 до 12–15 см и выше. Соответственно, чем длиннее шуруп, тем больше его диаметр. Для разных видов крепления и материалов заготовок предназначаются отдельные виды шурупов.
Шуруп должен быть на 3–4 мм больше, чем толщина прикрепляемой планки, чтобы она могла хорошо держаться на основе.
Номер шурупа (соотношение его длины и толщины) подбирают под определенный тип планки. Для самой тонкой планки подбирают шуруп длиной 6 мм, толстую планку крепят шурупом длиной 12–15 см. В зависимости от предназначения шурупа его шляпка может быть плоской (потайной) или полукруглой (выпуклой). Первый вид шляпки предназначен для крепления деталей мебели с последующей шпаклевкой. Такие шурупы не должны быть видны на поверхности. Второй тип шурупов предназначен как для крепления деталей, так и для украшения поверхности.
В зависимости от величины шурупа его завинчивают одним из двух способов. Если шуруп небольшой, а древесина мягкая, то можно ограничиться лишь пометкой шилом на поверхности в месте ввинчивания. Но если шуруп большой или его диаметр слишком велик, то в месте крепления просверливают дрелью, буравом или коловоротом небольшое отверстие, по глубине и по диаметру немногим меньше шурупа, чтобы он мог хорошо держаться в массиве. Если таким шурупом закрепляют две достаточно толстые планки, то просверливают обе детали, чтобы при ввинчивании не растрескалась древесина.
Чтобы скрыть шляпку шурупа в массиве, делают небольшое коническое углубление, ввинчивают шуруп до предела и зашпаклевывают.
Но в любом случае, независимо от величины шурупа, его вворачивают с помощью отвертки с подходящим размером и видом полотна. Отвертку вставляют в шлиц – небольшую прорезь на шляпке шурупа, крестообразной или прямой формы.
Чтобы облегчить свой труд при ввинчивании шурупов, можно воспользоваться несколькими уже проверенными способами.
При ввинчивании шурупа в массив твердой древесины его перед началом работы смазывают хозяйственным мылом. В том случае, если на поверхность крепления будет наноситься краска или оно будет находиться внутри изделия, в качестве смазки используют солидол или лыжную мазь. При желании оставшиеся небольшие жирные следы убирают спиртом или другим обезжиривающим средством.
При работе с древесно-стружечной плитой сначала просверливают отверстие чуть меньшее, чем шуруп, затем смазывают его клеем и вставляют в него кусок трубки из пластика, и только потом в модифицированное отверстие ввинчивают приготовленный шуруп.
Нередко случается, что шуруп необходимо ввинтить в торцовую часть доски или бруска. Такое крепление никогда не считалось прочным.
Но для того, чтобы увеличить прочность крепления, можно воспользоваться двумя приемами. Первый заключается в том, что просверленное под шуруп отверстие пропитывают древесным лаком на масляной или спиртовой основе. Второй способ усиления конструкции состоит в использовании нагеля, который вбивают в торец бруска, а уже в него ввинчивают шуруп.
В ходе работы случается и такое, что уже намертво ввинченный шуруп мешает соединению тех или иных деталей. Исправить это можно несколькими приемами.
Берут разводной гаечный ключ, фиксируют между его рамками полотно отвертки, которую потом устанавливают в шлиц шурупа. Затем немного нажимают на отвертку и поворачивают гаечный ключ. Даже самый старый и непокорный шуруп должен без труда вывинтиться.
При другом способе используют молоток. Сначала вставляют жало отвертки в шлиц, захватывают рукоятку отвертки всей рукой, чтобы открытой оставалась верхушка, и, осторожно ударяя молотком по верхушке, синхронно поворачивают отвертку.
Следующий способ поможет заменить шуруп с отколовшейся наполовину декоративной шляпкой. Для этого опять понадобится гаечный ключ, отвертка и тонкая небольшая деревянная дощечка.
Если шуруп завинчен недалеко от края, то можно просто воспользоваться гаечным ключом. Для этого крепко зажимают остатки уцелевшей половины и поворачивают ключ до тех пор, пока шуруп полностью не вывинтится.
Если же шуруп расположен посередине детали и воспользоваться одним гаечным ключом невозможно, то берут отвертку, устанавливают ее на место бывшего шлица и придвигают как можно ближе к ней приготовленную дощечку. Всю эту конструкцию фиксируют гаечным ключом, затем осторожно поворачивают ключ и следят за тем, чтобы он не сорвался.
Не следует заворачивать шурупы во влажную древесину, так как в этом случае они ржавеют и вокруг них возникают желтые пятна. Если все же потребуется осуществить такую операцию, то предварительно шурупы покрывают тонким слоем масла. То же самое делают при соединении деталей, которые будут подвергаться воздействию влажного воздуха, снега или дождя.
Заклепки
Заклепки пригодны для соединения заготовок из дерева, металла, пластмассы и других материалов. Это более сложное соединение, чем на гвоздях, шурупах или болтах. Зато заклепки имеют много преимуществ и применяются в очень ответственных конструкциях, например при строительстве кораблей, самолетов, подводных лодок. Прочность, герметичность и надежность – основные достоинства заклепок.Можно использовать заклепки с потайной головкой, и тогда их можно будет зашпаклевать заподлицо с поверхностью и закрасить.
Длина и диаметр заклепок зависят от их назначения. Изготавливаются они как из твердых материалов, например ковких сталей, так и из мягких – сплавов меди или алюминия. При самостоятельном строительстве можно успешно использовать заклепки из цветных металлов: с ними легче работать, они обладают высокой прочностью, хотя и несколько уступают стальным.
Заклепки различают еще и по форме. Это связано с их назначением, они могут иметь головку: потайную, полупотайную, полукруглую или коническую. Первые применяют для того, чтобы поверхность клепанного шва была ровной, в остальных случаях используют заклепки любого другого типа (рис. 87).
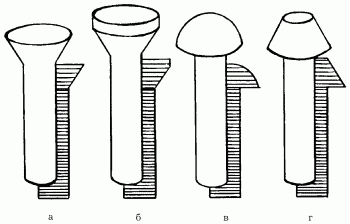
Чаще всего в домашних условиях используют заклепки от 2 до 8 мм. Длина заклепки должна быть такой, чтобы ее кончик выходил из отверстия в соединяемых деталях на 0,8–1,2 величины диаметра. Например, если диаметр заклепки 5 мм, то она должна выступать на 4–6 мм.
Определенная сложность применения заклепок определяет необходимость иметь набор специальных инструментов и приспособлений. Для работы потребуются следующие:
– поддержка– металлическая пластина с выемкой под головку заклепки;
– натяжка– стальной сердечник с неглубоким отверстием, высверленным по центральной оси;
– обжимка– тоже стальной сердечник, но с выемкой на торце.
Остальные инструменты применяют и в процессе других работ: молоток, дрель, сверла и конические зенковки для расточки верхних кромок отверстий.
Сначала на поверхности деталей, которые будут соединяться, чертят линию будущего шва и отмечают места под отверстия для заклепок. Расстояние от кромки детали до места заклепки определяют путем умножениея коэффициента 1,5 на величину диаметра самой заклепки (в миллиметрах). Чтобы определить шаг между отверстиями, величину диаметра умножают на коэффициент 3.
Пример: диаметр заклепки 5 мм, а значит, расстояние от кромки – 1,5 х 5 = 7,5 мм; 3 х 5 = 15 мм. Это шаг между отверстиями для заклепки.
После разметки линии шва и центров отверстий определяют диаметр сверла. Его подбирают на 0,1–0,2 мм больше, чем диаметр заклепки, а затем сверлят ряд отверстий. Если планируют использовать заклепки с потайными головками, то отверстия зенкуют коническими зенковками, то есть растачивают на конус. Глубина расточки составляет 0,8 диаметра заклепки.
При использовании заклепок с полупотайными, полукруглыми или коническими головками с отверстий снимают фаску на глубину 1,0–1,5 мм. Затем в него вставляют клепку и под ее головку подкладывают поддержку так, чтобы головка вошла в углубление. После этого легкими ударами молотка с помощью натяжки плотно сжимают детали между собой.
Следующий момент – это небольшое расплющивание выступающего кончика стержня заклепки, насаживание на него обжимки и формирование головки ударом молотка по ней. Точно так же обрабатывают все остальные заклепки шва (рис. 88).
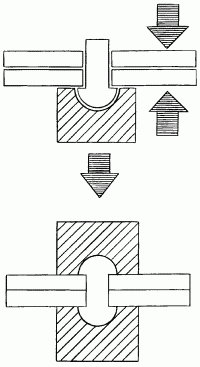
При установке заклепок с потайной головкой можно вместо поддержки обойтись любой массивной металлической пластиной с плоской поверхностью. Хорошо для этих целей подходит небольшая наковальня. После установки заклепок их расплющенные выступающие концы обрабатывают напильником.
В том случае, если соединение должно быть подвижным, диаметр отверстия делают на 0,3–0,5 мм больше, чем диаметр заклепки, а под оба конца ее подкладывают металлические шайбы.
Для того чтобы разобрать соединение деталей, выступающие головки заклепок срубают зубилом, стачивают напильником или электронаждаком, потайные заклепки высверливают дрелью. Стержни, которые остаются в отверстиях, выбивают с помощью кернера.
Болты
Основное предназначение болтов – соединять между собой бревна, брусья или толстые доски в несущих конструкциях.В зависимости от толщины балок их диаметр может колебаться от 10 м до 30 мм, а по длине такие крепления могут достигать 70–90 см. При выборе размера болта обязательно должна учитываться толщина балки.
Чтобы установить болт в бревно, просверливают сквозное отверстие, чуть меньшее диаметра болта. Затем на выбранный болт надевают шайбу, которая предотвращает вдавливание шляпки болта в массив древесины. Надеваемая на болт контргайка предотвращает ослабление крепления.
Такой собранный болт вбивают в массив. Выступающий конец болта также снабжают шайбой и контргайкой. На него надевают гайку, которая до предела затягивает всю конструкцию.
Чтобы не сорвать резьбу, важно правильно определить длину ключа. Для этого величину диаметра резьбы, выраженную в миллиметрах, нужно умножить на 15. Например, диаметр резьбы равен 10 мм, при умножении получается, что гаечный ключ должен иметь длину 150 мм. Такой ключ позволит нормально затянуть гайку и позволит избежать срыва резьбы.
Правильно выполненное соединение – это когда концы болтов выступают над поверхностью гаек примерно на 2–3 витка резьбы.
Если конструкция, соединенная болтами, будет подвергаться атмосферным воздействиям, чтобы не допустить ржавчины, резьбу болтов и гаек перед завинчиванием покрывают тонким слоем машинного масла.
При отвинчивании туго затянутой гайки применяют ключ более длинный, чем при завинчивании. Если это не помогает, то можно попробовать осторожно постучать молотком по рукоятке надетого на гайку ключа так, чтобы сдвинуть ее с мертвой точки.
Задача существенно осложняется, если у гайки сорваны или скруглены углы ее граней. В этом случае их восстанавливают напильником.
Заржавевшее соединение перед отвинчиванием смачивают керосином, а наросты ржавчины сбивают легкими ударами молотка по головке винта и по бокам гайки. Поврежденную резьбу на выступающем конце болта исправляют с помощью тонкой ножовки по металлу или напильника.
Хомуты
Для крепления двух балок или толстых досок используют такое крепление, как хомут. Многим оно известно из слесарного дела, когда необходимо заделать на время дыру в водопроводной трубе.Чаще всего для крепления несущих конструкций используют хомуты из нержавеющей стали, которые представляют собой полоски толщиной 8–16 мм и шириной от 28 до 105 мм. Хомуты могут быть прямоугольными, квадратными и круглыми и использоваться в зависимости от формы соединяемых деталей. На место крепления двух или более досок или балок устанавливают одну половину хомута, с другой стороны на этом же уровне устанавливают вторую часть и затягивают их болтами.
Уголки
Уголки представляют собой металлические полоски из нержавеющей стали с несколькими отверстиями для крепления. Уголки могут быть прямыми или комбинированными. У комбинированных имеется еще одна планка, расположенная под углом 45°. Различные толщина и ширина уголков позволяют их использовать и при креплении оконных рам, дверных полотен, ворот и т. п.Накладки
Накладки применяют при соединениях в торец или при наращивании. Они представляют собой стальные пластины различной толщины, длины и ширины в зависимости от наращиваемых деталей.Вдоль пластины располагается несколько отверстий для закрепления накладок на древесине. Обычно соединяют их с помощью шурупов или болтов.
Строительные скобы
Строительные скобы используют для крепления всевозможных деревянных конструкций. Внешне они представляют п-образные или s-образные прутья из толстой квадратной или цилиндрической стали, достигающие в длину 45–55 см. Различные типы скоб используют при различных типах соединений. Наиболее часто встречаются прямые скобы, концы которых направлены в одну сторону.Лучшего соединения балок между собой достигают, взяв развернутую скобу, или s-образную. Концы такой скобы располагают параллельно друг другу. Если необходимо максимально закрепить деревянное соединение, то лучше всего использовать повернутую скобу, один конец которой загибают под углом 45°.
Глухари
Этот тип крепления чем-то напоминает концы скобы. Именно их используют при закреплении оконных блоков и дверных коробок в проемах. Длина глухарей может колебаться от 10 до 12 см.Соединение деревянных деталей с помощью клея
Без клея практически невозможно обойтись при соединении деталей. При склеивании древесины используют клей, который должен быть прозрачным, светлым, не изменять цвет древесины, не слишком быстро схватываться, чтобы можно было легко удалить его излишки, а внутри шва он должен способствовать предохранению древесины от гниения и проникновения внутрь микроорганизмов.Клеи
Существует два основных типа клеев: природные, из компонентов животного, минерального или растительного происхождения, и синтетические, изготовляемые только из искусственных ингредиентов.Глютеиновые клеибывают костными и мездровыми. Они относятся к клеям животного происхождения.
Мездровый делают из подкожного слоя шкур животных – мездры и обрезков шкур, отходов и т. д. Костный клей изготавливают из обезжиренных и очищенных костей, рогов и копыт. Обычная упаковка глютеиновых клеев – сухие плитки длиной 150–200 мм, шириной – 80–100 мм и толщиной – 10–15 мм. Встречается клей и в виде гранул, крупинок, опилок или чешуек. Эти виды более удобны, так как быстро набухают в процессе приготовления.
Костный клей может быть не только в сухом виде, но и в студнеобразном (галерта). Галерта позволяет быстро приготовить раствор для склеивания, но при использовании этого клея в него необходимо добавлять антисептики. Плиточный клей бывает разного цвета, от светло-желтого до темно-коричневого, это зависит от состава сырья.
Глютеиновые клеи бывают четырех сортов: высшего, первого, второго и третьего. Клей высшего качества должен быть стекловидным, светлым и при изломе оставлять острые края.
Рекомендуется хранить эти марки клея при температуре не более 15 °C в сухом проветриваемом помещении. Можно хранить клей в холодильнике, а галерту вообще не рекомендуется хранить долго.
Недостатком костных клеев является то, что они плохо реагируют на влажность, из-за чего их невозможно использовать для склеивания деревянных конструкций во влажных помещениях, например в подвалах, банях или на открытом воздухе.
Казеиновые клеиимеют в основе обезжиренный творог (молочный белок, или казеин). Кроме этого, в состав клея первого и второго сорта входят: гашеная известь, фтористый натрий, медный купорос и керосин. Марки казеиновых клеев отличаются составом. В марке «Экстра» (В-107), присутствуют перечисленные выше ингредиенты, а если это «Об» (обыкновенный), то в нем нет медного купороса, а казеин для него берется второго сорта.
Казеиновый клей представляет собой однородную массу беловато-желтого цвета. Его надо хранить в сухом проветриваемом помещении с температурой не выше 30 °C. При повышении температуры казеиновый клей теряет свои свойства.
Следует помнить, что уже через 5 мес хранения, начиная со дня выпуска, требуется проверить клей на прочность склеивания. При работе с древесиной казеиновый клей окрашивает ее поверхность, так как в качестве растворителя в нем используется щелочь.
Синтетические клеиполучили сейчас широкое распространение. Это карбамидные, меламино-мочевиноформальдегидные и др. Они водостойки, обладают противогрибковым эффектом, очень прочны. Промышленность выпускает их в различной форме: твердые, жидкие, пастообразные и порошкообразные.
Перед использованием таких клеев необходимо внимательно ознакомиться с инструкцией по их приготовлению, способам склеивания и руководствоваться принципами техники безопасности, так как клеи представляют определенную опасность для человека. Эпоксидный клейдает прочное соединение без высокого давления при запрессовке и является универсальным. Однако он требует очень тщательной подготовки поверхности для склеивания.
Время отвердевания эпоксидного клея при температуре воздуха 20 °C составляет 24 ч, при 60 °C – 4 ч, а при 120 °C – 2 ч.
Клей ПВА,или поливинилацетатная дисперсия, дает пластичное соединение. Клей довольно быстро схватывается и требует быстрого выполнения операции склеивания. ПВА представляет собой белую жидкость, которая при высыхании становится прозрачной. Клей может применяться для склеивания любых деревянных деталей.
Склеивание
Соединять детали с помощью клея можно двумя способами: склеиванием или наклеиванием.Склеивание используют при соединениях на шип и на ус. Наклеивание применяют при изготовлении фанеры, при отделке поверхности шпоном и т. п.
Склеить детали можно двумя способами: сжав поверхности зажимами или притерев поверхности друг к другу после нанесения на них клея. Притиркой соединяют преимущественно тонкие детали, которые после небольшого схватывания подгоняют друг к другу и оставляют до полного высыхания клея.
Клеевое соединение деталей должно происходить быстро и четко, поэтому перед тем, как приступить к склеиванию, готовят все необходимое для работы: зажимы, прокладки, ленты, опоры, ремни, а также поверхности склеиваемых деталей, которые при необходимости очищают. Места загрязнения протирают ацетоном или спиртом.
Прокладки при склеивании используют для максимально равномерного распределения усилия при сжатии. Также они предохраняют поверхности от образования вмятин при зажиме струбцинами. Прокладку всегда делают чуть больше размера склеиваемых деталей. Чаще всего прокладки изготавливают из листов фанеры.
А чтобы избежать приклеивания поверхностей к прокладкам, подкладывают еще листы бумаги между прокладкой и поверхностью.
При склеивании способом сжатия обязательно следят за тем, чтобы при установке зажимов не произошло смещения поверхностей, которое потом уже невозможно будет восстановить.
Чтобы шов получился хорошим, прочным, работать лучше всего в комнате, где температура не опускается ниже 20 °C. Клей необходимо наносить тонким ровным слоем, при этом он не должен быть слишком жидким. Толстый слой клея недопустим, так как при высыхании он растрескивается.
Не надо стараться шлифовать склеиваемые поверхности – плоскости должны быть немного шероховатыми, это позволит получить более надежное соединение.
Если склеивают сразу несколько деталей, не наносят клей сразу на все – в нижних слоях клей начнет схватываться, но не будет равномерно распределен, поверхность получится волнами. Чтобы этого не случилось, детали разделяют на несколько частей, склеивают планки частей между собой, а потом уже части.
Склеивать лучше всего по уровням, например в один прием – ножки стульев, в другой – сиденья.
Если склеивают сложную конструкцию, состоящую из множества узлов, то сначала соединяют все детали без клея, подгоняют, если что-то выступает, и только потом наносят клей, так как явные дефекты при склеивании устранить не удастся и разобрать уже склеенную конструкцию без повреждений невозможно.
После нанесения клея на узлы конструкции ее кладут под пресс и выдерживают определенное время, чтобы клей полностью схватился и подсох. Если используют столярный клей, то вынуть деталь из-под пресса можно только через 1 сут. Клей ПВА требует меньше времени – всего 4–5 ч. Но это еще не означает, что клей полностью высох и конструкция готова к дальнейшей работе. После того как истекло необходимое время, ослабляют зажимы, проверяют, нет ли сдвигов слоев, и кладут еще на 1 сут, чтобы клей высох полностью.
Наклеивание
Наклеивание отличается от склеивания тем, что применяется только при облицовочных работах. Это достаточно простой способ имитировать массивы ценных пород древесины, используя только шпон и деревянную основу.Этот прием используют и при изготовлении мозаики, которая прекрасно украсит крышку любого стола, створки шкафа, тумбочку в спальне и т. п.
Хотя здесь и используют шпон ценных пород древесины, а сама работа требует внимательности и точности глаза, ее сможет выполнить даже человек, который никогда не имел дела с деревом. Это похоже на аппликацию из бумаги и картона. Но есть несколько особенностей, о которых необходимо помнить.
1. Приклеивать шпон нужно только на очень ровную поверхность, немного шероховатую, без видимых зазубрин (поверхность основы должна быть «бархатной»).
2. Шпон обязательно приклеивают поперек направления волокон основы, но не вдоль, иначе могут появиться трещины, портящие поверхность и возникающие из-за разной усадки шпона и основания.
3. Если используют дорогой шпон и наклеивают его на древесно-стружечную плиту, то обязательно наклеивают промежуточный слой из дешевого шпона или хлопчатобумажной ткани.
4. Используя шпон из капа или древесины с высокой свилеватостью, подбирают основу из тщательно высушенной древесины, чтобы потом не образовались трещины.
5. При наклеивании шпона на небольшие поверхности используют клей ПВА, а на большие – столярный клей, это делает наклеивание более качественным.
Так же как и склеивание, наклеивание ведется двумя способами: запрессованием и притиркой. И тот и другой способ выполняют в такой последовательности:
– сначала наносят на основу слой клея, затем накладывают на нее шпон, проглаживают чистой суконкой, тем самым удаляя из-под него все воздушные пузыри. После этого для лучшего соединения протирают сверху шпон губкой, пропитанной теплой водой.
Через 1–2 ч, когда клей начнет загустевать, притиркой проглаживают шпон по направлению волокон, стараясь не задирать кромки. Для этого все движения направляют к кромкам или по диагонали к ним;
– конструкцию оставляют до полного склеивания, положив предварительно листы белой бумаги на швы, кладут под пресс, уложив бумагу сверху на шпон, затем прокладку, и только потом зажимают струбцинами;