Страница:
Кроме того, чтобы избежать приклеивание поверхностей к прокладкам, понадобится подложить еще листы бумаги между прокладкой и поверхностью.
При склеивании способом сжатия обязательно следят за тем, чтобы при установке зажимов не произошло смещения поверхностей, которое потом уже невозможно будет восстановить.
Чтобы шов получился хорошим, прочным, работать лучше всего в комнате, где температура не опускается ниже 20°. Также клей нужно наносить тонким ровным слоем, при этом клей не должен быть слишком жидким. Но и толстый слой тоже недопустим – при высыхании он растрескается.
Также не рекомендуется шлифовать склеиваемые поверхности – плоскости должны быть немного шероховатыми, что позволит получить надежное соединение.
Если необходимо склеить сразу несколько деталей, нельзя наносить клей сразу на все – в нижних слоях клей начнет схватываться, но не будет равномерно распределен, от этого поверхность получится волнами. Чтобы этого не случилось, детали делят на несколько частей, склеивают планки частей между собой, а потом уже и части.
Склеивать лучше всего по уровням, например, в один прием – ножки стульев, в другой – сиденья.
Если приходится склеивать сложную конструкцию, состоящую из множества узлов, то сначала соединяют все детали без клея, подгоняют, если что-то выступает, и только потом наносят клей. Явные дефекты при склеивании устранить не удастся, а разобрать уже склеенную конструкцию без ее повреждений тоже невозможно.
После того как нанесли клей на узлы конструкции, необходимо ее положить под пресс и выдержать определенное время, чтобы клей полностью схватился и подсох. Если использовали столярный клей, то вынуть деталь из-под пресса можно только через 1 сут. Клей ПВА требует меньше времени – всего 4–5 ч. Но это еще не означает, что клей полностью высох и конструкция готова к дальнейшей работе. После того как истекло необходимое время, ослабляют зажимы, проверяют, нет ли сдвигов слоев, и кладут все еще на 1 сут, чтобы клей высох полностью.
Кроме этого, этот прием поможет и при изготовлении мозаики, которая прекрасно украсит крышку любого стола, створки шкафа, тумбочку в спальне и т. п.
Хотя здесь и используется шпон ценных пород древесины, а сама работа требует внимательности и точности глаза, эту работу может выполнить даже человек, который никогда не имел дела с деревом. Это скорее похоже на аппликацию из бумаги и картона. Но здесь есть несколько особенностей, о которых всегда надо помнить и соблюдать во время работы.
1. Приклеивать шпон нужно только на очень ровную поверхность, немного шероховатую, но без видимых зазубрин. Если можно так сказать, поверхность основы должна быть бархатной.
2. Шпон обязательно должен приклеиваться поперек направления волокон основы, но не вдоль, иначе могут появиться трещины, которые только испортят поверхность. Они возникают из-за разной усадки шпона и основания.
3. Если используется дорогой шпон и наклеивается на древесно-стружечную плиту, то обязательно наклеивают промежуточный слой из дешевого шпона или хлопчатобумажной ткани.
4. Используя шпон из капа или древесины с высокой свилеватостью, подбирают основу из тщательно высушенной древесины, чтобы потом не образовались трещины.
5. Для наклеивания шпона на небольших поверхностях используют клей ПВА, а на больших – столярный клей. Это поможет сделать наклеивание более качественным.
Так же как и склеивание, наклеивание ведется 2 способами: запрессованием и притиркой. И тот и другой способ выполняются в следующей последовательности:
– сначала наносят на основу слой клея, затем накладывают на нее шпон, проглаживают чистой суконкой, тем самым удалив из-под него все воздушные пузыри. После этого для лучшего соединения смачивают сверху шпон губкой с теплой водой. Через 1–2 ч, когда клей начнет загустевать, притиркой проглаживают шпон по направлению волокон, стараясь не задирать кромки. Для этого все движения должны быть направлены к кромкам или по диагонали к ним;
– перед тем как оставить конструкцию до полного склеивания, нужно положить листы белой бумаги на швы. Теперь все это можно оставить так, как есть, а можно положить под пресс, сверху на шпон уложив бумагу, затем прокладку и только потом зажать струбцинами;
– в качестве пресса для деталей с неровной изогнутой поверхностью может использоваться просеянный и подогретый песок. На поверхность кладут сначала лист бумаги, тем самым защитив шпон от загрязнения, а потом холщовый мешок с песком. Чем больше песка, тем больше будет оказываться давление. Но оно не должно быть чрезмерным, чтобы не произошло деформации шпона. Оптимальное давление будет оказываться слоем песка в 9–11 см. Освобождать поверхность от такого пресса можно только после окончательного остывания песка, чтобы шпон не «пошел пузырями».
При наложении шпона на основу могут появиться некоторые недростатки.
Прежде всего, это образование так называемых чижей – мест, где слой клея был недостаточным и произошло образование воздушных подушек. Обнаружить такие участки поможет самое простое простукивание – пустые места будут глухо звучать под ударами. Чиж следует надрезать ножом-косяком, затем осторожно приподнять один край и пипеткой или шприцем с иглой с большим просветом влить в пустоту несколько капель клея. После этого тряпкой, поглаживая поверхность круговыми движениями, распределяют клей внутри бывшего чижа и проглаживают шов, на который потом нужно наложить бумажную полоску.
Затем это место необходимо прогладить утюгом, нагретым до температуры в 100–110 °C (цифра «1» на регуляторе температур).
Воздушные пузыри, образовавшиеся из-за неравномерной притирки, чаще всего имеют выпуклую форму. Такой пузырь также надо разрезать, немного размочить шпон вокруг пузыря, затем влить несколько капель клея из пипетки или шприца и притереть теплым утюгом через бумагу.
Некоторые детали из шпона при наклеивании способны смещаться. Таким образом, у кромок появляются миллиметры лишнего шпона.
Только после полного закрепления клея их придется выровнять. В зависимости от размеров выступающих краев используют либо нож-косяк, либо рубанок. Рубанок пригоден только при сравнительно небольшом выступе – примерно в 1 мм. Больший выступ снимается ножом-косяком. При этом обязательно кладут рядом с деталью планку такой же толщины, чтобы при выравнивании не произошел отлом шпона.
Глава 11. Работа со сталью
Холодная клепка
Инструменты для клепки деталей
Описание процесса клепки
Паяние
Изготовление инвентаря для кровельных работ
Соединение криволинейных элементов
Заготовка элементов покрытий парапетов, брандмауэрных стен и фартуков
Выполнение воротников вокруг дымовых труб, покрытий слуховых окон, колпаков и зонтов над трубами
Закатка проволоки и выкатка валиков жесткости
Изготовление элементов настенных и подвесных желобов и покрытий разжелобков
При склеивании способом сжатия обязательно следят за тем, чтобы при установке зажимов не произошло смещения поверхностей, которое потом уже невозможно будет восстановить.
Чтобы шов получился хорошим, прочным, работать лучше всего в комнате, где температура не опускается ниже 20°. Также клей нужно наносить тонким ровным слоем, при этом клей не должен быть слишком жидким. Но и толстый слой тоже недопустим – при высыхании он растрескается.
Также не рекомендуется шлифовать склеиваемые поверхности – плоскости должны быть немного шероховатыми, что позволит получить надежное соединение.
Если необходимо склеить сразу несколько деталей, нельзя наносить клей сразу на все – в нижних слоях клей начнет схватываться, но не будет равномерно распределен, от этого поверхность получится волнами. Чтобы этого не случилось, детали делят на несколько частей, склеивают планки частей между собой, а потом уже и части.
Склеивать лучше всего по уровням, например, в один прием – ножки стульев, в другой – сиденья.
Если приходится склеивать сложную конструкцию, состоящую из множества узлов, то сначала соединяют все детали без клея, подгоняют, если что-то выступает, и только потом наносят клей. Явные дефекты при склеивании устранить не удастся, а разобрать уже склеенную конструкцию без ее повреждений тоже невозможно.
После того как нанесли клей на узлы конструкции, необходимо ее положить под пресс и выдержать определенное время, чтобы клей полностью схватился и подсох. Если использовали столярный клей, то вынуть деталь из-под пресса можно только через 1 сут. Клей ПВА требует меньше времени – всего 4–5 ч. Но это еще не означает, что клей полностью высох и конструкция готова к дальнейшей работе. После того как истекло необходимое время, ослабляют зажимы, проверяют, нет ли сдвигов слоев, и кладут все еще на 1 сут, чтобы клей высох полностью.
Наклеивание
Наклеивание отличается от склеивания тем, что здесь выполняют только облицовочные работы. Это достаточно простой способ имитировать массивы ценных пород древесины, используя только шпон и деревянную основу.Кроме этого, этот прием поможет и при изготовлении мозаики, которая прекрасно украсит крышку любого стола, створки шкафа, тумбочку в спальне и т. п.
Хотя здесь и используется шпон ценных пород древесины, а сама работа требует внимательности и точности глаза, эту работу может выполнить даже человек, который никогда не имел дела с деревом. Это скорее похоже на аппликацию из бумаги и картона. Но здесь есть несколько особенностей, о которых всегда надо помнить и соблюдать во время работы.
1. Приклеивать шпон нужно только на очень ровную поверхность, немного шероховатую, но без видимых зазубрин. Если можно так сказать, поверхность основы должна быть бархатной.
2. Шпон обязательно должен приклеиваться поперек направления волокон основы, но не вдоль, иначе могут появиться трещины, которые только испортят поверхность. Они возникают из-за разной усадки шпона и основания.
3. Если используется дорогой шпон и наклеивается на древесно-стружечную плиту, то обязательно наклеивают промежуточный слой из дешевого шпона или хлопчатобумажной ткани.
4. Используя шпон из капа или древесины с высокой свилеватостью, подбирают основу из тщательно высушенной древесины, чтобы потом не образовались трещины.
5. Для наклеивания шпона на небольших поверхностях используют клей ПВА, а на больших – столярный клей. Это поможет сделать наклеивание более качественным.
Так же как и склеивание, наклеивание ведется 2 способами: запрессованием и притиркой. И тот и другой способ выполняются в следующей последовательности:
– сначала наносят на основу слой клея, затем накладывают на нее шпон, проглаживают чистой суконкой, тем самым удалив из-под него все воздушные пузыри. После этого для лучшего соединения смачивают сверху шпон губкой с теплой водой. Через 1–2 ч, когда клей начнет загустевать, притиркой проглаживают шпон по направлению волокон, стараясь не задирать кромки. Для этого все движения должны быть направлены к кромкам или по диагонали к ним;
– перед тем как оставить конструкцию до полного склеивания, нужно положить листы белой бумаги на швы. Теперь все это можно оставить так, как есть, а можно положить под пресс, сверху на шпон уложив бумагу, затем прокладку и только потом зажать струбцинами;
– в качестве пресса для деталей с неровной изогнутой поверхностью может использоваться просеянный и подогретый песок. На поверхность кладут сначала лист бумаги, тем самым защитив шпон от загрязнения, а потом холщовый мешок с песком. Чем больше песка, тем больше будет оказываться давление. Но оно не должно быть чрезмерным, чтобы не произошло деформации шпона. Оптимальное давление будет оказываться слоем песка в 9–11 см. Освобождать поверхность от такого пресса можно только после окончательного остывания песка, чтобы шпон не «пошел пузырями».
При наложении шпона на основу могут появиться некоторые недростатки.
Прежде всего, это образование так называемых чижей – мест, где слой клея был недостаточным и произошло образование воздушных подушек. Обнаружить такие участки поможет самое простое простукивание – пустые места будут глухо звучать под ударами. Чиж следует надрезать ножом-косяком, затем осторожно приподнять один край и пипеткой или шприцем с иглой с большим просветом влить в пустоту несколько капель клея. После этого тряпкой, поглаживая поверхность круговыми движениями, распределяют клей внутри бывшего чижа и проглаживают шов, на который потом нужно наложить бумажную полоску.
Затем это место необходимо прогладить утюгом, нагретым до температуры в 100–110 °C (цифра «1» на регуляторе температур).
Воздушные пузыри, образовавшиеся из-за неравномерной притирки, чаще всего имеют выпуклую форму. Такой пузырь также надо разрезать, немного размочить шпон вокруг пузыря, затем влить несколько капель клея из пипетки или шприца и притереть теплым утюгом через бумагу.
Некоторые детали из шпона при наклеивании способны смещаться. Таким образом, у кромок появляются миллиметры лишнего шпона.
Только после полного закрепления клея их придется выровнять. В зависимости от размеров выступающих краев используют либо нож-косяк, либо рубанок. Рубанок пригоден только при сравнительно небольшом выступе – примерно в 1 мм. Больший выступ снимается ножом-косяком. При этом обязательно кладут рядом с деталью планку такой же толщины, чтобы при выравнивании не произошел отлом шпона.
Глава 11. Работа со сталью
При устройстве кровли часто приходится выполнять жестяные работы, к которым относятся паяние, холодная клепка и изготовление инвентаря из жести. Об этих видах работ и пойдет речь далее.
Холодная клепка
Клепка необходима для более прочного сращивания деталей. Клепку применяют при изготовлении желобов и инвентаря, прикреплении зонтов над отверстиями вентиляционных и дымовых труб и т. д.
Клепку проводят с помощью заклепок, изготовленных из мягкого металла (медь, алюминий) и представляющих собой стержень цилиндрической формы с закладной головкой на конце. При расклепке стержня заклепки получают замыкающую головку. Для кровельных работ берут заклепки, диаметр которых в 2 раза больше толщины одной из сращиваемых деталей, а длина равна толщине обеих деталей плюс 3–5 мм для образования головки.
Длину выступающего конца заклепки выбирают в зависимости от формы замыкающей головки. При полукруглой форме головки длина выступающего конца должна составлять 1,5 диаметра стержня. Если головка плоская, длина выступающего конца стержня должна составлять примерно 1,1 стержневого диаметра. Клепка может быть обычной или потайной. При обычной клепке головки заклепок находятся над поверхностью деталей, а при потайной расплющиваются заподлицо с поверхностью сращиваемых деталей.
Если соединяют детали из кровельной стали с деталями из сортовой стали, то обычно используют заклепки диаметром 2,5–3 мм, располагая закладные головки на стороне тонкой детали.
Обычно детали сращивают одним заклепочным швом, а иногда и 2. Заклепки располагают на расстоянии 3 см друг от друга и на расстоянии 1,5 длины стержня от кромки деталей. Для заклепок в деталях делают отверстия больше диаметра стержня заклепки на 1/4. При сращивании деталей влетай, т. е. клепку делают заподлицо с поверхностью деталей, отверстия для клепки зенкуют (придают отверстию форму усеченного конуса) на глубину, равную высоте головки, под углом 60–80°.
Клепку проводят с помощью заклепок, изготовленных из мягкого металла (медь, алюминий) и представляющих собой стержень цилиндрической формы с закладной головкой на конце. При расклепке стержня заклепки получают замыкающую головку. Для кровельных работ берут заклепки, диаметр которых в 2 раза больше толщины одной из сращиваемых деталей, а длина равна толщине обеих деталей плюс 3–5 мм для образования головки.
Длину выступающего конца заклепки выбирают в зависимости от формы замыкающей головки. При полукруглой форме головки длина выступающего конца должна составлять 1,5 диаметра стержня. Если головка плоская, длина выступающего конца стержня должна составлять примерно 1,1 стержневого диаметра. Клепка может быть обычной или потайной. При обычной клепке головки заклепок находятся над поверхностью деталей, а при потайной расплющиваются заподлицо с поверхностью сращиваемых деталей.
Если соединяют детали из кровельной стали с деталями из сортовой стали, то обычно используют заклепки диаметром 2,5–3 мм, располагая закладные головки на стороне тонкой детали.
Обычно детали сращивают одним заклепочным швом, а иногда и 2. Заклепки располагают на расстоянии 3 см друг от друга и на расстоянии 1,5 длины стержня от кромки деталей. Для заклепок в деталях делают отверстия больше диаметра стержня заклепки на 1/4. При сращивании деталей влетай, т. е. клепку делают заподлицо с поверхностью деталей, отверстия для клепки зенкуют (придают отверстию форму усеченного конуса) на глубину, равную высоте головки, под углом 60–80°.
Инструменты для клепки деталей
Поддержка
Применяется для установки закладной головки. Для этого поверхность инструмента, которая при работе соприкасается с головкой, имеет углубление в форме головки.Молоток
Берется молоток массой 3 кг. Используется при вбивании заклепок в отверстие.Осадка
Необходима для уплотнения сращиваемых деталей.Обжимка
Используется для доводки (окончательного формирования) замыкающей головки.
Описание процесса клепки
Сращивание деталей начинают с установки ориентировочных клепок на концах заклепочного ряда и через определенные промежутки между ними.
Клепка выполняется в таком порядке: подгон сращиваемых деталей; разметка отверстий для заклепок; просверливание отверстий; укладка заклепки; осадка сращиваемых деталей для плотного их прилегания друг к другу и замыкающей головке; доводка замыкающей головки с помощью обжимки.
Клепка выполняется в таком порядке: подгон сращиваемых деталей; разметка отверстий для заклепок; просверливание отверстий; укладка заклепки; осадка сращиваемых деталей для плотного их прилегания друг к другу и замыкающей головке; доводка замыкающей головки с помощью обжимки.
Паяние
Для получения плотного и водонепроницаемого шва применяют паяние – скрепление металлических деталей расплавленным припоем. Припоем называются оловянно-свинцовые сплавы, которые легко поддаются плавке. При паянии расплавленный припой помещают в промежуток между предварительно разогретыми паяльником деталями. Припой заполняет поры основного металла и образует плотный шов. Для кровельных работ берут мягкие припои, температура плавления которых не более 300 °C.
С кромок сращиваемых деталей перед паянием удаляют ржавчину, грязь, шлифуют их, чтобы не было заусенцев и неровностей. После этого лудят (покрывают тонким слоем олова) участки спаивания, шлифуют и лудят жало паяльника. Детали кладут на ровную деревянную поверхность (брусок). После подгонки кромок деталей в промежуток между ними с помощью кисточки или тонкой палочки вводят хлористый цинк (соляную кислоту). В том случае, если шов большой, его в нескольких местах припаивают. Жало паяльника с припоем ставят в начале шва и по мере попадания припоя в промежуток между деталями шов в этом месте прижимают деревянным бруском, а паяльник перемещают на новое место и т. д. Количество припоя на жале время от времени пополняют.
Сращиваемые детали во время пайки слегка наклоняют в сторону перемещения паяльника. Прижим с кромок деталей снимают только после того, как припой затвердеет, а спаянный шов станет матово-серым. Шов затем промывают под струей воды или протирают тампоном, смоченным в содовом растворе, и сушат ветошью.
Паяние параллельно с клепкой применяют при изготовлении инвентаря, воротников для труб и т. д.
С кромок сращиваемых деталей перед паянием удаляют ржавчину, грязь, шлифуют их, чтобы не было заусенцев и неровностей. После этого лудят (покрывают тонким слоем олова) участки спаивания, шлифуют и лудят жало паяльника. Детали кладут на ровную деревянную поверхность (брусок). После подгонки кромок деталей в промежуток между ними с помощью кисточки или тонкой палочки вводят хлористый цинк (соляную кислоту). В том случае, если шов большой, его в нескольких местах припаивают. Жало паяльника с припоем ставят в начале шва и по мере попадания припоя в промежуток между деталями шов в этом месте прижимают деревянным бруском, а паяльник перемещают на новое место и т. д. Количество припоя на жале время от времени пополняют.
Сращиваемые детали во время пайки слегка наклоняют в сторону перемещения паяльника. Прижим с кромок деталей снимают только после того, как припой затвердеет, а спаянный шов станет матово-серым. Шов затем промывают под струей воды или протирают тампоном, смоченным в содовом растворе, и сушат ветошью.
Паяние параллельно с клепкой применяют при изготовлении инвентаря, воротников для труб и т. д.
Изготовление инвентаря для кровельных работ
При выполнении кровельных работ используют ведро цилиндрической формы, ведро конической формы и бидон, правила изготовления которых приведены ниже.
Рис. 77. Цилиндрическое ведро: 1 – общий вид ведра; 2 – заготовка днища ведра; 3 – проволочный ободок в развернутом виде; 4 – половина обечайки; 5 – дужка ведра.
Для изготовления обечайки берут листовую сталь толщиной 1 мм и отмечают на ней размеры обечайки (высоту и длину, равную длине окружности днища плюс припуск 12 мм на швы, соединяющие кромки обечайки и обечайку с днищем, и на закатку ободка). Проволоку для ободка берут диаметром 4 мм. Ушки прикрепляют к обечайке с помощью заклепок сечением 6 х 4 мм.
Для дужки используют проволоку диаметром 6 мм и вставляют ее в ушки. При скреплении деталей все фальцы для более прочного соединения смазывают суриковой замазкой.
Рис. 78. Изготовление конического ведра.
Чтобы сделать коническое ведро, берут листовую сталь толщиной 0,65–0,7 мм и размечают на ней выкройку ведра. Чертят круг диаметром 30–40 см, затем чертят второй круг диаметром 20 см внутри первого. Круги должны иметь один центр. Затем их делят пополам и откладывают припуски для спайки бокового шва и для проволочного ободка. После этого вырезают половинку большого круга, а также входящую в нее половину маленького круга. Спаивают боковые кромки. Измерив диаметр маленького отверстия, чертят на листовой стали круг диаметром, равном диаметру этого отверстия, и вырезают его. Таким образом получают днище конического ведра. Днище припаивают к нижним кромкам обечайки. Затем закатывают проволочный ободок, придав ему сначала форму кольца, и забортовывают его с помощью молотка; вырезают из более толстой стали (1–1,2 мм) ушки и заклепками приклепывают их к верхней части обечайки. Проволочную дужку вставляют в ушки.
Рис. 79. Бидон: 1 – крышка бидона; 2 – вид сбоку; 3 – половина выкройки днища видона; 4 – выкройка конуса.
Рис. 79. Бидон: (продолжение) 5 – выкройка обечайки бидона; 6 – ободок из проволоки; 7 – выкройка горловины; 8 – выкройка ручки; 9 – выкройка обечайки карышки; 10 – половина выкройки верха крышки.
На выкройке даны припуски для фальцевых сращений. Детали круглой и конической формы делают вручную или на вальцовке.
Днище бидона делают с упором. Крышка должна плотно сидеть в горловине, поэтому соединительные фальцы делают один внутрь, а другой выводят наружу. Чтобы ручка была более крепкой, ее снабжают проволочными ободками и приклепывают к верхней части крышки.
Изготовление цилиндрического ведра
Ведро цилиндрической формы состоит из таких элементов: днище, обечайка, ободок, ушки, дужка, заклепки (рис. 77).
Для изготовления обечайки берут листовую сталь толщиной 1 мм и отмечают на ней размеры обечайки (высоту и длину, равную длине окружности днища плюс припуск 12 мм на швы, соединяющие кромки обечайки и обечайку с днищем, и на закатку ободка). Проволоку для ободка берут диаметром 4 мм. Ушки прикрепляют к обечайке с помощью заклепок сечением 6 х 4 мм.
Для дужки используют проволоку диаметром 6 мм и вставляют ее в ушки. При скреплении деталей все фальцы для более прочного соединения смазывают суриковой замазкой.
Изготовление конического ведра
Как и цилиндрическое, коническое ведро состоит из обечайки, ободка, днища, ушек и заклепок (рис. 78).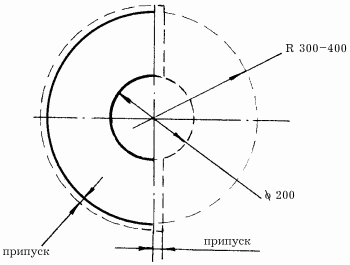
Чтобы сделать коническое ведро, берут листовую сталь толщиной 0,65–0,7 мм и размечают на ней выкройку ведра. Чертят круг диаметром 30–40 см, затем чертят второй круг диаметром 20 см внутри первого. Круги должны иметь один центр. Затем их делят пополам и откладывают припуски для спайки бокового шва и для проволочного ободка. После этого вырезают половинку большого круга, а также входящую в нее половину маленького круга. Спаивают боковые кромки. Измерив диаметр маленького отверстия, чертят на листовой стали круг диаметром, равном диаметру этого отверстия, и вырезают его. Таким образом получают днище конического ведра. Днище припаивают к нижним кромкам обечайки. Затем закатывают проволочный ободок, придав ему сначала форму кольца, и забортовывают его с помощью молотка; вырезают из более толстой стали (1–1,2 мм) ушки и заклепками приклепывают их к верхней части обечайки. Проволочную дужку вставляют в ушки.
Изготовление бидона
Бидон состоит из обечайки, конуса, днища, горловины, ободка, верхней части крышки, обечайки крышки и ручки. Для изготовления бидона берут сталь толщиной 0,8–0,9 мм. Делают его делают выкройке, изображенной на рисунке 79.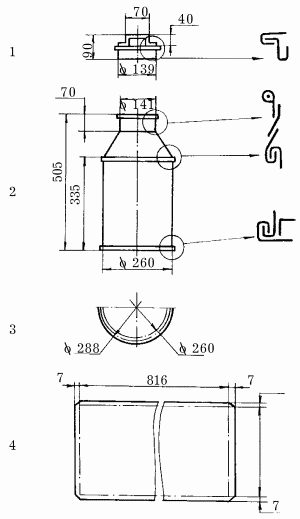
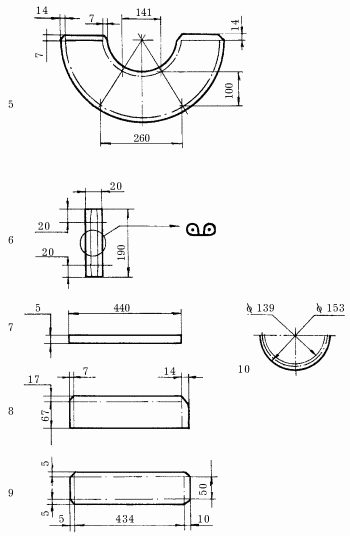
На выкройке даны припуски для фальцевых сращений. Детали круглой и конической формы делают вручную или на вальцовке.
Днище бидона делают с упором. Крышка должна плотно сидеть в горловине, поэтому соединительные фальцы делают один внутрь, а другой выводят наружу. Чтобы ручка была более крепкой, ее снабжают проволочными ободками и приклепывают к верхней части крышки.
Соединение криволинейных элементов
Рассмотреть соединение криволинейных элементов можно на примере переходного колена между воронкой и водосточной трубой, которое состоит из 3 звеньев.
Перед тем как приступить к заготовке звеньев, на стальном листе делается шаблон переходной кривой по размерам косого среза звена.
Затем на одном листе по шаблону с учетом припусков на фальцевое соединение размечаются все 3 заготовки (рис. 80). Вырезанные заготовки выкатывают и соединяют одинарными лежачими фальцами. Готовые звенья соединяют фальцовкой (рис. 81).
Рис. 80. Раскрой звеньев с использованием шаблона переходной кривой.
Рис. 81. Соединие звеньев переходного колена: а – общий вид; б – сечение фальцев.
Остановимся поподробнее на операциях, проводимых при изготовлении переходного колена. На внутренней поверхности звена в местах, предназначенных для соединения, наносятся риски. Звено кладут на наковальню, совмещая риску с его ребром, и короткими ударами носика молотка по кругу отгибают кромку на 10–15°.
Операцию повторяют до тех пор, пока отгиб не составит сначала 60° (рис. 82), а затем 120°. Потом сваливают бортик и осуществляют его усадку (рис. 83). Для соединения звеньев между собой на нижнем и верхнем звеньях отбортовывают кромку шириной 5 мм и вставляют ее в углубленние, образованное бортиком на среднем звене и фальцуют шов (рис. 84).
Рис. 82. Отбортовка кромки звена на 60°.
Рис. 83. Сваливание бортика.
Рис. 84. Соединение звеньев в колене.
Перед тем как приступить к заготовке звеньев, на стальном листе делается шаблон переходной кривой по размерам косого среза звена.
Затем на одном листе по шаблону с учетом припусков на фальцевое соединение размечаются все 3 заготовки (рис. 80). Вырезанные заготовки выкатывают и соединяют одинарными лежачими фальцами. Готовые звенья соединяют фальцовкой (рис. 81).
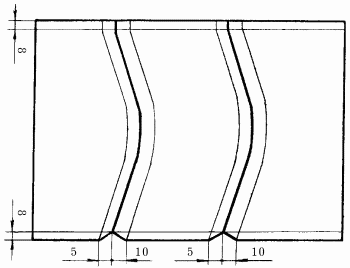
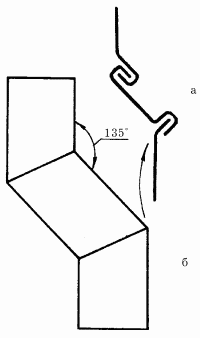
Остановимся поподробнее на операциях, проводимых при изготовлении переходного колена. На внутренней поверхности звена в местах, предназначенных для соединения, наносятся риски. Звено кладут на наковальню, совмещая риску с его ребром, и короткими ударами носика молотка по кругу отгибают кромку на 10–15°.
Операцию повторяют до тех пор, пока отгиб не составит сначала 60° (рис. 82), а затем 120°. Потом сваливают бортик и осуществляют его усадку (рис. 83). Для соединения звеньев между собой на нижнем и верхнем звеньях отбортовывают кромку шириной 5 мм и вставляют ее в углубленние, образованное бортиком на среднем звене и фальцуют шов (рис. 84).
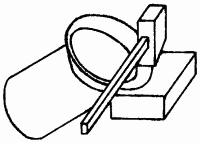
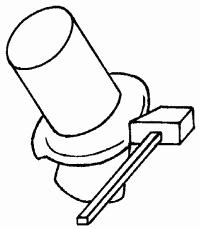
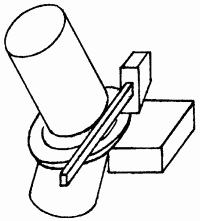
Заготовка элементов покрытий парапетов, брандмауэрных стен и фартуков
Чтобы уберечь парапет от воздействия атмосферных осадков, используется стальное покрытие, имеющее по краям капельники, а при высоте парапета до 50 мм устраивают еще и фартук (рис. 85).
Рис. 85. Покрытие парапета: 1 – парапет; 2 – стальное покрытие; 3 – фартук; 4 – капельник.
Стальное покрытие крепится т-образными костылями, которые прибиваются к брускам через каждые 600–700 мм. Для усиления жесткости покрытия к брускам прибивают дополнительно крючья из полосовой стали длиной 420 мм и шириной 30–40 мм.
Соединение брандмауэра со стальным кровельным покрытием осуществляется с помощью выдры, для чего отогнутый на 60–80 мм край кровельного листа вводится в борозду, оставленную во время кирпичной кладки, на полную ее глубину (60 мм). В зависимости от климатических условий брандмауэр покрывается кровельной сталью либо только сверху, либо сверху и с боков (рис. 86).
Рис. 86. Покрытие брандмауэра: 1 – брандмауэр; 2 – стальное покрытие; 3 – фартук; 4 – капельник.
Кровельные листы для покрытия парапетов и брандмауэров размечают в строгом соответствии с заданными размерами, разрезают в продольном направлении и соединяют в двойные картины одинарными лежачими фальцами с подсечкой.
Фартуки делают из стальных листов, разрезанных в продольном направлении.
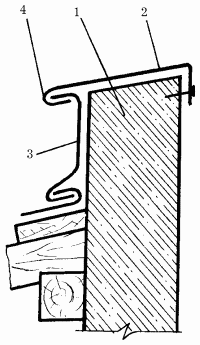
Стальное покрытие крепится т-образными костылями, которые прибиваются к брускам через каждые 600–700 мм. Для усиления жесткости покрытия к брускам прибивают дополнительно крючья из полосовой стали длиной 420 мм и шириной 30–40 мм.
Соединение брандмауэра со стальным кровельным покрытием осуществляется с помощью выдры, для чего отогнутый на 60–80 мм край кровельного листа вводится в борозду, оставленную во время кирпичной кладки, на полную ее глубину (60 мм). В зависимости от климатических условий брандмауэр покрывается кровельной сталью либо только сверху, либо сверху и с боков (рис. 86).
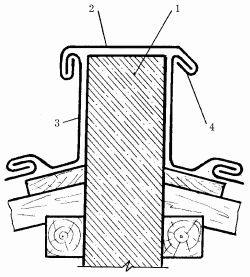
Кровельные листы для покрытия парапетов и брандмауэров размечают в строгом соответствии с заданными размерами, разрезают в продольном направлении и соединяют в двойные картины одинарными лежачими фальцами с подсечкой.
Фартуки делают из стальных листов, разрезанных в продольном направлении.
Выполнение воротников вокруг дымовых труб, покрытий слуховых окон, колпаков и зонтов над трубами
Изготовление воротника начинают с тщательной разметки кровельного листа по заданным размерам. Разрезанные заготовки гнут так, чтобы в результате детали верхней и нижней частей боковых фартуков получились парными: 2 левые и 2 правые (рис. 87).
Рис. 87. Заготовление воротника дымовой трубы: а – общий вид дымовой трубы; б – детали воротника, подготовленные к укладке; Ду – длина дымовой трубы по уклону; Ш – ширина дымовой трубы; У – угол между стенкой трубы и скатом крыши.
Половины воротника соединяют одинарными фальцами и пропаиваются третником.
Вместо фальцевых соединений можно сделать отгибы, направленные по стоку воды, которые сначала заклепывают (2–3 заклепки диаметром 2–3 мм), а затем запаивают.
Слуховое окно, в зависимости от его размера, покрывают 1 или 2 картинами. Перед изготовлением картин необходимо провести замеры обрешетки, чтобы установить:
– диаметр основания окна;
– длину полуконуса по уклону;
– длину полуконуса по коньку.
По полученным размерам составляют чертеж окна (вид спереди и сбоку), по которому с учетом припусков на свес и фальцы раскраивают кровельный лист и заготавливают 2 картины.
Воротник слухового окна состоит из 3 фартуков: 2 боковых и 1 переднего (рис. 88).
Рис. 88. Воротник слухового окна: а – общий вид окна; б – передний фартук; в – боковой фартук; А – ширина фартука; Б – ширина нижней оконной обвязки; Д – длина боковой стенки окна по скату; Ш – ширина окна; У – угол между передней стенкой окна.
Заготавливают их по заданным размерам на верстаке с использованием бруса-оправки и киянки.
На переднем фартуке сначала отгибают короткие боковые отвороты, а затем длинный, расположенный между ними. На боковом фартуке сначала отгибают долевую кромку, а затем край, укладываемый на обрешетку. Короткую узкую кромку сваливают на плоскость, а длинную отгибают под прямым углом.
Колпак, защищающий оголовок дымовой или вентиляционной трубы, состоит из 4 боковин и крышки (рис. 89).
Рис. 89. Колпак для дымовой или вентиляционной трубы.
Заготовки по шаблонам вырезают из листовой стали.
В боковинах отгибают капельники, верхние прямоугольные ободки и кромки для фальцевого соединения, а в крышке прорезают отверстие по размеру дымохода и отгибают внутренние бортики.
После этого крышку соединяют с боковинами угловыми фальцами.
Зонты защищают дымовые каналы от попадания в них атмосферной влаги. В зависимости от формы зонты бывают коническими или пирамидальными.
Для изготовления конических зонтов используют кровельная сталь толщиной 1–1,5 мм, а для пирамидальных – в 2 раза тоньше.
Для выполнения развертки конического зонта (рис. 90) необходимо начертить окружность нужного диаметра, провести из ее центра 2 радиуса так, чтобы угол между ними составил 35°, сделать припуск на нахлестку и вырезать заготовку. Затем края заготовки соединяют и закрепляют 3–4 заклепками, с наружной стороны к зонту также заклепками прикрепляют 3 стойки.
Рис. 90. Заготовка для конического зонта: 1 – стойка; 2 – заклепка.
Для выполнения развертки пирамидального зонта (рис. 91) чертят квадрат заданного размера, противоположные углы соединяют диагоналями, образуя 4 треугольника, одну из сторон треугольника разрезают, по линии разреза заготовка раздвигают на угол 25°, делают припуски на подгиб и на фальцевое соединение.
Рис. 91. Заготовка для пирамидального конуса.
Готовую заготовку слегка прогибают по сторонам треугольников и соединяют замыкающим фальцем.
К внешней стороне зонта крепятся 4 стойки.
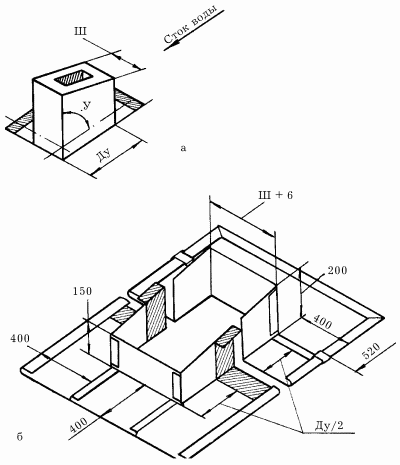
Половины воротника соединяют одинарными фальцами и пропаиваются третником.
Вместо фальцевых соединений можно сделать отгибы, направленные по стоку воды, которые сначала заклепывают (2–3 заклепки диаметром 2–3 мм), а затем запаивают.
Слуховое окно, в зависимости от его размера, покрывают 1 или 2 картинами. Перед изготовлением картин необходимо провести замеры обрешетки, чтобы установить:
– диаметр основания окна;
– длину полуконуса по уклону;
– длину полуконуса по коньку.
По полученным размерам составляют чертеж окна (вид спереди и сбоку), по которому с учетом припусков на свес и фальцы раскраивают кровельный лист и заготавливают 2 картины.
Воротник слухового окна состоит из 3 фартуков: 2 боковых и 1 переднего (рис. 88).
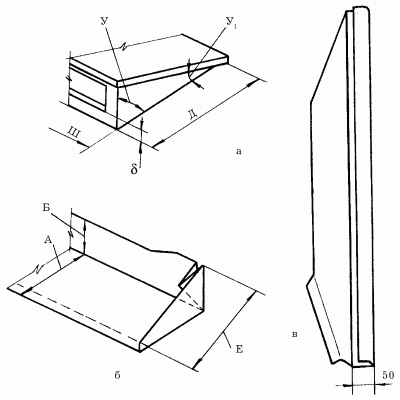
Заготавливают их по заданным размерам на верстаке с использованием бруса-оправки и киянки.
На переднем фартуке сначала отгибают короткие боковые отвороты, а затем длинный, расположенный между ними. На боковом фартуке сначала отгибают долевую кромку, а затем край, укладываемый на обрешетку. Короткую узкую кромку сваливают на плоскость, а длинную отгибают под прямым углом.
Колпак, защищающий оголовок дымовой или вентиляционной трубы, состоит из 4 боковин и крышки (рис. 89).
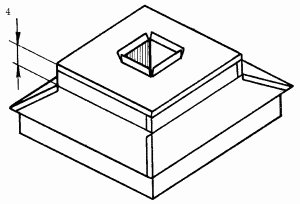
Заготовки по шаблонам вырезают из листовой стали.
В боковинах отгибают капельники, верхние прямоугольные ободки и кромки для фальцевого соединения, а в крышке прорезают отверстие по размеру дымохода и отгибают внутренние бортики.
После этого крышку соединяют с боковинами угловыми фальцами.
Зонты защищают дымовые каналы от попадания в них атмосферной влаги. В зависимости от формы зонты бывают коническими или пирамидальными.
Для изготовления конических зонтов используют кровельная сталь толщиной 1–1,5 мм, а для пирамидальных – в 2 раза тоньше.
Для выполнения развертки конического зонта (рис. 90) необходимо начертить окружность нужного диаметра, провести из ее центра 2 радиуса так, чтобы угол между ними составил 35°, сделать припуск на нахлестку и вырезать заготовку. Затем края заготовки соединяют и закрепляют 3–4 заклепками, с наружной стороны к зонту также заклепками прикрепляют 3 стойки.
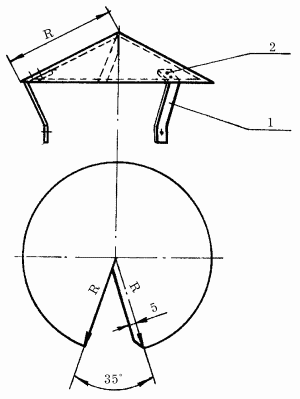
Для выполнения развертки пирамидального зонта (рис. 91) чертят квадрат заданного размера, противоположные углы соединяют диагоналями, образуя 4 треугольника, одну из сторон треугольника разрезают, по линии разреза заготовка раздвигают на угол 25°, делают припуски на подгиб и на фальцевое соединение.
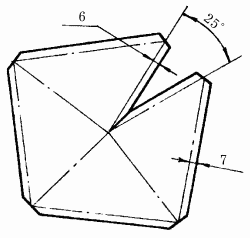
Готовую заготовку слегка прогибают по сторонам треугольников и соединяют замыкающим фальцем.
К внешней стороне зонта крепятся 4 стойки.
Закатка проволоки и выкатка валиков жесткости
Для придания жесткости кровельным изделиям в них закатывают проволоку. Вдоль кромки стального листа с помощью линейки проводят 2 риски: первую на расстоянии, равном 1/2 диаметра закатываемой проволоки, а вторую на расстоянии, равном 1/3 расстояния до первой риски.
Затем совмещают вторую риску с краем верстака и под прямым углом отгибают кромку (рис. 92, а), лист переворачивают и отогнутую кромку загибают внутрь листа еще на 15° (рис. 92, б), переворачивают лист и делают отгиб по первой риске (рис. 92, в), опять переворачивают лист и отгиб кромки доводят до 90° (рис. 92, г), в отгиб закладывают отрезок проволоки (рис. 92, д) и деревянным молотком сваливают кромку (рис. 92, е).
Рис. 92. Закатка проволоки: а – совмещение второй риски с краем верстака; б – загиб кромки на 15°; в – отгиб по первой риске; г – отгиб кромки до 90°; д – заладывание проволоки; е – сваливание кромки; ж – обжимание.
В заключение лист устанавливается вертикально и проволока окончательно обжимается со всех сторон (рис. 92, ж).
В круглых изделиях сначала отбортовывают кромку заданной ширины на 90°, закладывают в нее проволочное кольцо соответствующего диаметра, на брусе-оправке или наковальне делают прихватку в нескольких местах, сваливают отгиб и укладывают его на кольцо.
Затем совмещают вторую риску с краем верстака и под прямым углом отгибают кромку (рис. 92, а), лист переворачивают и отогнутую кромку загибают внутрь листа еще на 15° (рис. 92, б), переворачивают лист и делают отгиб по первой риске (рис. 92, в), опять переворачивают лист и отгиб кромки доводят до 90° (рис. 92, г), в отгиб закладывают отрезок проволоки (рис. 92, д) и деревянным молотком сваливают кромку (рис. 92, е).
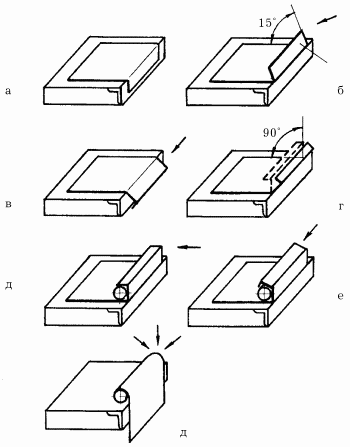
В заключение лист устанавливается вертикально и проволока окончательно обжимается со всех сторон (рис. 92, ж).
В круглых изделиях сначала отбортовывают кромку заданной ширины на 90°, закладывают в нее проволочное кольцо соответствующего диаметра, на брусе-оправке или наковальне делают прихватку в нескольких местах, сваливают отгиб и укладывают его на кольцо.
Изготовление элементов настенных и подвесных желобов и покрытий разжелобков
Картины настенных желобов выполняют на верстаке.
В двойной картине (рис. 93) короткие стороны листов соединяются между собой двойными лежачими фальцами, расположенными по направлению стока воды.
Рис. 93. Двойная картина настенного желоба.
На одной длинной стороне картины отгибается кромка для соединения с рядовым покрытием, а на коротких сторонах, отступив от другой длинной стороны 200–250 мм, делают по 1 надрезу глубиной 30 мм и вдоль длинной кромки под углом 60° к плоскости картины отгибают отворотную ленту. Углы кромок под двойные лежачие фальцы обрезают на 45°. Борт желоба отгибается на высоту 120–150 мм в зависимости от годового количества осадков, выпадающих в данной местности.
Затем на коротких сторонах картины отгибаются кромки под лежачие фальцы: у картин желобов, расположенных справа от водоприемной воронки, правые отгибы делают вверх, а левые вниз, а у левых картин – наоборот.
Подвесные желоба, как правило, бывают полукруглыми, но встречаются и прямоугольные. Изготавливаются они звеньями длиной по 3–4 м. Листы в картине соединяются двойными лежачими фальцами и осаживаются так, чтобы они оказались с наружной стороны желоба. Выгибается готовая картина на специальном приспособлении с помощью киянки. В конце желобов, не соединяющихся с воронками, ставятся заглушки.
В двойной картине (рис. 93) короткие стороны листов соединяются между собой двойными лежачими фальцами, расположенными по направлению стока воды.
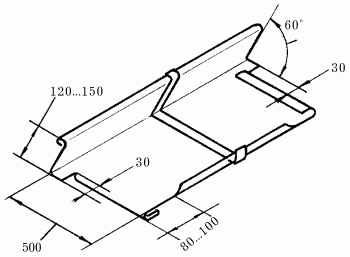
На одной длинной стороне картины отгибается кромка для соединения с рядовым покрытием, а на коротких сторонах, отступив от другой длинной стороны 200–250 мм, делают по 1 надрезу глубиной 30 мм и вдоль длинной кромки под углом 60° к плоскости картины отгибают отворотную ленту. Углы кромок под двойные лежачие фальцы обрезают на 45°. Борт желоба отгибается на высоту 120–150 мм в зависимости от годового количества осадков, выпадающих в данной местности.
Затем на коротких сторонах картины отгибаются кромки под лежачие фальцы: у картин желобов, расположенных справа от водоприемной воронки, правые отгибы делают вверх, а левые вниз, а у левых картин – наоборот.
Подвесные желоба, как правило, бывают полукруглыми, но встречаются и прямоугольные. Изготавливаются они звеньями длиной по 3–4 м. Листы в картине соединяются двойными лежачими фальцами и осаживаются так, чтобы они оказались с наружной стороны желоба. Выгибается готовая картина на специальном приспособлении с помощью киянки. В конце желобов, не соединяющихся с воронками, ставятся заглушки.