Страница:
Изготовление деталей водосточных труб
Навешивание водосточных труб
Художественное оформление водосливов
Глава 12. Сварочные работы при устройстве кровли
Организация рабочего места
Типы электродов
Основные виды сварки
Виды сварных соединений и швов при дуговой сварке
Водосточная труба состоит из:
– водоприемной воронки;
– прямых звеньев;
– колен для обхода выступов на стене;
– отмета для отвода воды от стен здания.
Основными деталями водоприемной воронки являются ободок, конус и стакан. Для ободка воронки вырезают заготовку, ширина которой равна длине верхней стороны трапециевидной заготовки для конуса, и ее края отгибают для соединения с конусом. Затем заготовку выгибают и соединяют фальцем. На готовом ободке выкатывают 2 валика жесткости и отбортовывают кромка, в которую закатывают проволоку диаметром 14 мм.
Для конуса вырезают заготовку в виде трапеции, верхняя сторона которой имеет длину, равную ширине заготовки для стакана, а нижняя равна ширине заготовки для ободка. На заготовке загибают фальцевые кромки и скатывают ее в конус на вальцовке при отклоненном сгибающем вале. Конус соединяется фальцем по своей образующей. Кромки прямоугольной заготовки стакана соединяются и обжимаются. Стакан вставляется в звено трубы.
Прямые звенья водосточных труб изготавливаются из стандартных стальных листов, которые разрезаются вдоль или поперек в зависимости от нужного количества звеньев и диаметра водосточной трубы. Чтобы готовые звенья хорошо входили друг в друга, заготовке придается небольшая конусность: одна ее сторона укорачивается на 5–6 мм.
Заготовку звена с отогнутыми кромками для фальцевого соединения свертывают вручную на брусе-оправке, стальной трубе или выкатывают на вальцовке.
На концах прямых звеньев за зигмашине выкатываются валики, выступающие над поверхностью звена на 7–8 мм. Они одновременно являются ребрами жесткости и ограничителями глубины захода одного звена в другое.
Из прямого звена трубы делаются гофрированные колена и сгибаются с помощью пресса или негофрированными из нескольких звеньев трубы.
Для изготовления отмета берется гладкое колено, нижний конец которого срезан по косой.
– водоприемной воронки;
– прямых звеньев;
– колен для обхода выступов на стене;
– отмета для отвода воды от стен здания.
Основными деталями водоприемной воронки являются ободок, конус и стакан. Для ободка воронки вырезают заготовку, ширина которой равна длине верхней стороны трапециевидной заготовки для конуса, и ее края отгибают для соединения с конусом. Затем заготовку выгибают и соединяют фальцем. На готовом ободке выкатывают 2 валика жесткости и отбортовывают кромка, в которую закатывают проволоку диаметром 14 мм.
Для конуса вырезают заготовку в виде трапеции, верхняя сторона которой имеет длину, равную ширине заготовки для стакана, а нижняя равна ширине заготовки для ободка. На заготовке загибают фальцевые кромки и скатывают ее в конус на вальцовке при отклоненном сгибающем вале. Конус соединяется фальцем по своей образующей. Кромки прямоугольной заготовки стакана соединяются и обжимаются. Стакан вставляется в звено трубы.
Прямые звенья водосточных труб изготавливаются из стандартных стальных листов, которые разрезаются вдоль или поперек в зависимости от нужного количества звеньев и диаметра водосточной трубы. Чтобы готовые звенья хорошо входили друг в друга, заготовке придается небольшая конусность: одна ее сторона укорачивается на 5–6 мм.
Заготовку звена с отогнутыми кромками для фальцевого соединения свертывают вручную на брусе-оправке, стальной трубе или выкатывают на вальцовке.
На концах прямых звеньев за зигмашине выкатываются валики, выступающие над поверхностью звена на 7–8 мм. Они одновременно являются ребрами жесткости и ограничителями глубины захода одного звена в другое.
Из прямого звена трубы делаются гофрированные колена и сгибаются с помощью пресса или негофрированными из нескольких звеньев трубы.
Для изготовления отмета берется гладкое колено, нижний конец которого срезан по косой.
Навешивание водосточных труб
Водоприемные воронки и водосточные трубы крепятся с помощью карнизных и настенных штырей со скобами. Крепежную полосу карнизного штыря, предназначенного для крепления воронки, подгибают и укорачивают так, чтобы входное отверстие конуса воронки находилось ниже капельника карнизного свеса на 7–10 мм, а валик жесткости стакана воронки опирался на хомут штыря.
Верхний настенный штырь крепится чуть ниже верхнего переходного колена, а нижний – чуть выше отмета. При необходимости между ними через равные промежутки устанавливаются дополнительные штыри, которые крепятся на березовых пробках, забитых в отверстия заподлицо со стеной (рис. 94).
Рис. 94. Навеска водосточной трубы.
Верхний настенный штырь крепится чуть ниже верхнего переходного колена, а нижний – чуть выше отмета. При необходимости между ними через равные промежутки устанавливаются дополнительные штыри, которые крепятся на березовых пробках, забитых в отверстия заподлицо со стеной (рис. 94).

Художественное оформление водосливов
В предыдущих разделах говорилось о том, как можно изготовить устройства для отвода воды с крыши и от стен дома. Чтобы они не только не портили общий вид дома, но и были его украшением, можно оформить их просечным железом. Работа с просечным железом не требует особых навыков и опыта, поэтому получить из него изделия высокого качества может даже новичок. Для этого понадобится рисунок или орнамент и минимальный набор инструментов: ножницы по металлу, угольник, рейсмус, молоток, линейка и несколько сечек.
Рейсмус для жестяных работ делают в виде пластины из закаленной стали. По обеим кромкам инструмент имеет вырезы. Используя рейсмус, прочерчивают разметочные линии, параллельные кромкам листа.
Рейсмус может быть раздвижным. С его помощью можно установить необходимое расстояние, ослабив 2 винта и переместив пластину относительно основания.
Сечки изготавливают 3 видов: круглые, полукруглые и прямые. Первые делаются из закаленной легированной стальной трубки необходимого диаметра.
Рабочая часть их хорошо заточена, а верхняя имеет заглушку для удара по ней молотком. В этих сечках имеется отверстие для удаления из них осколков материала. Сечки выпускаются длиной 150–180 мм.
Сечки полукруглой формы делаются с разным поперечным сечением – крутым, отлогим, средним. Рабочая сторона затачивается на ширину 3,5–30 мм. Инструмент можно изготовить и в домашних условиях. Для этого берут обычное зубило и снимают у него рабочую часть. После этого с помощью наждачного круга придают его спинке полукруглую форму, а на краю того же круга выполняют рабочую часть инструмента, которую затем затачивают.
В качестве прямых сечек могут служить простые зубила, ширина рабочей кромки которых колеблется от 8 до 30 мм, а угол заострения – 35–40°.
Владея навыками термической обработки стали, любой необходимый инструмент, включая и сечки, можно изготовить самостоятельно.
Для этого вида работ обычно берут кровельное оцинкованное железо или черное железо. Предпочтение отдают черному железу, потому что после окрашивания, чернения на нем более четко выделяется рисунок. Недостаток этого железа в том, что оно довольно быстро ржавеет, в отличие от оцинкованного железа.
Просечной рисунок, выполненный на оцинкованном железе, начинает «играть», если кровля и стены дома окрашены в темные цвета или на фоне кирпичных стен.
Перед выполнением работ тщательно подготавливают рабочее место. Для этого выбирают дубовый или буковый чурбак и ставят его на устойчивую скамью. На верхнем торце чурбака и следует просекать железо.
Жестянщик усаживается верхом на скамью так, чтобы чурбак находился между ног. С правой стороны на одном уровне с чурбаком устанавливают небольшие козлы, а с левой – стол. Стол нужен для раскладывания инструментов, а козлы – для горизонтального расположения длинных листов просечной резьбы.
Чтобы проделать отверстия, предусмотренные заранее заготовленным рисунком, на просекаемой поверхности с помощью линейки, угольника и других инструментов делают разметку, затем лист кладут на чурбак и все отверстия пробивают сечками, ударяя по ним молотком.
Наиболее трудные участки следует пробивать полукруглыми сечками. Рисунок у кромок вырезают ножницами по металлу, а внутренний – прямыми сечками.
Кроме уже перечисленных инструментов, для пробивания мелких отверстий могут понадобиться чеканы.
Отделывают просечное железо путем чернения, то есть оксидирования.
Чернение проводят в эмалированной емкости, подогревая раствор. Но имеется некоторая сложность: чернить просечные листы больших размеров довольно трудно.
Перед чернением железо подготавливают – удаляют с него окалину и ржавчину в таких растворах (вещества, входящие в их состав, даются в массовых частях):
1. Формалин – 2.
Соляная кислота (20 %-ная) – 48.
2. Соляная кислота – 25.
Серная кислота – 15.
Уротропин – 0,06.
Вода – 200.
После удаления с железа окалины и ржавчины его тщательно промывают под струей воды и опускают в раствор для чернения, приготовленный по одному из рецептов:
1. Вода – 200.
Гипосульфит натрия – 16.
Ортофосфорная кислота – 1,4.
Хлористый аммоний – 12.
Азотная кислота – 0,6.
Раствор постепенно доводят до температуры примерно 70 °C и приблизительно на 20 мин помещают в него железо, которое покрывается черной матовой пленкой.
Раствор может действовать и при температуре 20 °C.
В этом случае изделие держат в нем не менее часа.
На изделии появляется матовая черная пленка, но менее прочная, чем при температуре 70 °C.
2. Вода – 200.
Нитрат натрия – 35.
Едкий натр – 130.
Раствор доводят до температуры 135 °C и опускают в него железо на 1,5 ч.
Железо в результате этой процедуры покрывается черной блестящей пленкой.
3. Вода – 200.
Едкий натр – 300.
Нитрат натрия – 6.
Раствор доводят до температуры 150 °C и помещают в него изделие не более чем на 10 мин. Изделие покрывается матовой черной пленкой.
После чернения изделия промывают горячей водой и сушат на открытом воздухе. Затем на них наносят тонкий слой натуральной олифы.
Рейсмус для жестяных работ делают в виде пластины из закаленной стали. По обеим кромкам инструмент имеет вырезы. Используя рейсмус, прочерчивают разметочные линии, параллельные кромкам листа.
Рейсмус может быть раздвижным. С его помощью можно установить необходимое расстояние, ослабив 2 винта и переместив пластину относительно основания.
Сечки изготавливают 3 видов: круглые, полукруглые и прямые. Первые делаются из закаленной легированной стальной трубки необходимого диаметра.
Рабочая часть их хорошо заточена, а верхняя имеет заглушку для удара по ней молотком. В этих сечках имеется отверстие для удаления из них осколков материала. Сечки выпускаются длиной 150–180 мм.
Сечки полукруглой формы делаются с разным поперечным сечением – крутым, отлогим, средним. Рабочая сторона затачивается на ширину 3,5–30 мм. Инструмент можно изготовить и в домашних условиях. Для этого берут обычное зубило и снимают у него рабочую часть. После этого с помощью наждачного круга придают его спинке полукруглую форму, а на краю того же круга выполняют рабочую часть инструмента, которую затем затачивают.
В качестве прямых сечек могут служить простые зубила, ширина рабочей кромки которых колеблется от 8 до 30 мм, а угол заострения – 35–40°.
Владея навыками термической обработки стали, любой необходимый инструмент, включая и сечки, можно изготовить самостоятельно.
Для этого вида работ обычно берут кровельное оцинкованное железо или черное железо. Предпочтение отдают черному железу, потому что после окрашивания, чернения на нем более четко выделяется рисунок. Недостаток этого железа в том, что оно довольно быстро ржавеет, в отличие от оцинкованного железа.
Просечной рисунок, выполненный на оцинкованном железе, начинает «играть», если кровля и стены дома окрашены в темные цвета или на фоне кирпичных стен.
Перед выполнением работ тщательно подготавливают рабочее место. Для этого выбирают дубовый или буковый чурбак и ставят его на устойчивую скамью. На верхнем торце чурбака и следует просекать железо.
Жестянщик усаживается верхом на скамью так, чтобы чурбак находился между ног. С правой стороны на одном уровне с чурбаком устанавливают небольшие козлы, а с левой – стол. Стол нужен для раскладывания инструментов, а козлы – для горизонтального расположения длинных листов просечной резьбы.
Чтобы проделать отверстия, предусмотренные заранее заготовленным рисунком, на просекаемой поверхности с помощью линейки, угольника и других инструментов делают разметку, затем лист кладут на чурбак и все отверстия пробивают сечками, ударяя по ним молотком.
Наиболее трудные участки следует пробивать полукруглыми сечками. Рисунок у кромок вырезают ножницами по металлу, а внутренний – прямыми сечками.
Кроме уже перечисленных инструментов, для пробивания мелких отверстий могут понадобиться чеканы.
Отделывают просечное железо путем чернения, то есть оксидирования.
Чернение проводят в эмалированной емкости, подогревая раствор. Но имеется некоторая сложность: чернить просечные листы больших размеров довольно трудно.
Перед чернением железо подготавливают – удаляют с него окалину и ржавчину в таких растворах (вещества, входящие в их состав, даются в массовых частях):
1. Формалин – 2.
Соляная кислота (20 %-ная) – 48.
2. Соляная кислота – 25.
Серная кислота – 15.
Уротропин – 0,06.
Вода – 200.
После удаления с железа окалины и ржавчины его тщательно промывают под струей воды и опускают в раствор для чернения, приготовленный по одному из рецептов:
1. Вода – 200.
Гипосульфит натрия – 16.
Ортофосфорная кислота – 1,4.
Хлористый аммоний – 12.
Азотная кислота – 0,6.
Раствор постепенно доводят до температуры примерно 70 °C и приблизительно на 20 мин помещают в него железо, которое покрывается черной матовой пленкой.
Раствор может действовать и при температуре 20 °C.
В этом случае изделие держат в нем не менее часа.
На изделии появляется матовая черная пленка, но менее прочная, чем при температуре 70 °C.
2. Вода – 200.
Нитрат натрия – 35.
Едкий натр – 130.
Раствор доводят до температуры 135 °C и опускают в него железо на 1,5 ч.
Железо в результате этой процедуры покрывается черной блестящей пленкой.
3. Вода – 200.
Едкий натр – 300.
Нитрат натрия – 6.
Раствор доводят до температуры 150 °C и помещают в него изделие не более чем на 10 мин. Изделие покрывается матовой черной пленкой.
После чернения изделия промывают горячей водой и сушат на открытом воздухе. Затем на них наносят тонкий слой натуральной олифы.
Глава 12. Сварочные работы при устройстве кровли
При строительстве домов свыше двух этажей обычно проводятся сварочные работы. Обычно метод сварки применяется при устройстве кровель из меди – очень декоративного материала, которые после монтажа не нуждается в дополнительном поддержании.
Также к сварочным работам можно приступать в том случае, если используемый кровельный материал достаточно тяжел.
Также к сварочным работам можно приступать в том случае, если используемый кровельный материал достаточно тяжел.
Организация рабочего места
В зависимости от характера работы сварку можно вести, находясь на одном месте или периодически передвигаясь по рабочей площадке. Поэтому рабочее место сварщика может быть как мобильным, так и постоянным. Независимо от этого существует строго определенный набор необходимых приспособлений и инструментов. Среди них выделяют: источник электропитания, сварочный трансформатор, сварочные провода, держатель электрода, защитный щиток для лица, брезентовая защитная одежда, оградительные щиты, средства пожаротушения, необходимые инструменты, асбестовый лист.
Если сварочные работы ведутся в кабине, то стены кабины лучше окрасить в светло-серый цвет. Такой тип окраски способствует лучшему поглощению ультрафиолетовых лучей. Кроме того, в кабине должно быть хорошее освещение и вентиляция.
Полы по требованиям противопожарной безопасности должны быть из кирпича, бетона или цемента. Размеры кабины – 2 х 2,5 м. Ее стенки изготавливают из тонкого металла, фанеры, брезента. И фанера, и брезент пропитываются огнестойким составом.
Рабочий стол сварщика не должен превышать высоту 0,6–0,7 м. Материал столешницы – толстая листовая сталь.
Фибровые маски и щитки защищают глаза и лицо сварщика от вредных излучений. Внутренняя сторона корпусов щитков и масок должна иметь матовую гладкую поверхность черного цвета.
Защиту от излучений обеспечивают и темно-зеленые светофильтры (тип С). Если сварочные работы выполняются покрытыми электродами, то лучше выбирать следующие светофильтры: при токе 100 А – светофильтр С5, 200 А – С6, 300 А – С7, 400 А – С8, 500–600 А – С9.
Если сварка проводится в двуокиси углерода при токе 50–100 А, то применяют светофильтр С1, 100–150 А – С2, 150–250 А – С3, 250–300 А – С4, 300–400 А – С5.
Электродержатели нужны для закрепления электрода и подвода к нему тока при ручной дуговой сварке. Различают электродержатели пассатижного, винтового, пружинного, рычажного и других типов. Электродержатели позволяют закреплять электрод в одном из трех положений: под углом 0, 60, 90° относительно продольной оси рукоятки.
Сварочные кабели служат для подвода тока к электродержателю и, соответственно, к изделию от источника питания. Наиболее распространены кабели марок РГД, РГДО, РГДВ. Рекомендуемая длина кабеля – 2–3 м, остальную часть можно заменить кабелями марок КРПНТ и КРПСН. Если длина кабеля превышает 30–40 м, то происходит значительное падение напряжения в сварочной цепи, что, естественно, плохо влияет на качество сварки. При силе тока дуги 200 А площадь сечения кабеля должна быть 40 мм2, 300 А – 70 мм2, 400 А – 120 мм2.
Комплекты для сварочных работ включают в себя три разновидности: КИ-50, КИ-315, КИ-125. Кроме того, существуют наборы ЭНИ-300 и ЭНИ-300/1. Они включают в себя следующие инструменты: электродержатель с запасными частями, соединительная муфта, клемма заземления, щетка-зубило, отвертка с диэлектрической ручкой, две диэлектрические ручки, плоскогубцы комбинированные, ключ гаечный разводной, клеймо сварщика, молоток, два защитных светофильтра, стекло покровное для щитка сварщика, отрезок кабеля марки РГД длиной 3 м.
Если сварочные работы ведутся в кабине, то стены кабины лучше окрасить в светло-серый цвет. Такой тип окраски способствует лучшему поглощению ультрафиолетовых лучей. Кроме того, в кабине должно быть хорошее освещение и вентиляция.
Полы по требованиям противопожарной безопасности должны быть из кирпича, бетона или цемента. Размеры кабины – 2 х 2,5 м. Ее стенки изготавливают из тонкого металла, фанеры, брезента. И фанера, и брезент пропитываются огнестойким составом.
Рабочий стол сварщика не должен превышать высоту 0,6–0,7 м. Материал столешницы – толстая листовая сталь.
Фибровые маски и щитки защищают глаза и лицо сварщика от вредных излучений. Внутренняя сторона корпусов щитков и масок должна иметь матовую гладкую поверхность черного цвета.
Защиту от излучений обеспечивают и темно-зеленые светофильтры (тип С). Если сварочные работы выполняются покрытыми электродами, то лучше выбирать следующие светофильтры: при токе 100 А – светофильтр С5, 200 А – С6, 300 А – С7, 400 А – С8, 500–600 А – С9.
Если сварка проводится в двуокиси углерода при токе 50–100 А, то применяют светофильтр С1, 100–150 А – С2, 150–250 А – С3, 250–300 А – С4, 300–400 А – С5.
Электродержатели нужны для закрепления электрода и подвода к нему тока при ручной дуговой сварке. Различают электродержатели пассатижного, винтового, пружинного, рычажного и других типов. Электродержатели позволяют закреплять электрод в одном из трех положений: под углом 0, 60, 90° относительно продольной оси рукоятки.
Сварочные кабели служат для подвода тока к электродержателю и, соответственно, к изделию от источника питания. Наиболее распространены кабели марок РГД, РГДО, РГДВ. Рекомендуемая длина кабеля – 2–3 м, остальную часть можно заменить кабелями марок КРПНТ и КРПСН. Если длина кабеля превышает 30–40 м, то происходит значительное падение напряжения в сварочной цепи, что, естественно, плохо влияет на качество сварки. При силе тока дуги 200 А площадь сечения кабеля должна быть 40 мм2, 300 А – 70 мм2, 400 А – 120 мм2.
Комплекты для сварочных работ включают в себя три разновидности: КИ-50, КИ-315, КИ-125. Кроме того, существуют наборы ЭНИ-300 и ЭНИ-300/1. Они включают в себя следующие инструменты: электродержатель с запасными частями, соединительная муфта, клемма заземления, щетка-зубило, отвертка с диэлектрической ручкой, две диэлектрические ручки, плоскогубцы комбинированные, ключ гаечный разводной, клеймо сварщика, молоток, два защитных светофильтра, стекло покровное для щитка сварщика, отрезок кабеля марки РГД длиной 3 м.
Типы электродов
При дуговой сварке плавлением применяют плавящиеся электроды, выполненные из холоднотянутой калиброванной или горячекатаной проволоки диаметром 0,3–12 мм, или порошковой проволоки. В качестве электродов используют также электродные ленты и пластины.
Электроды классифицируют по материалу, назначению для сварки определенных сталей, по толщине покрытия, нанесенного на стержень, видам покрытия, характеру шлака, образующегося при расплавлении, техническим свойствам металла шва и пр.
На все электроды наносится определенный состав – покрытие. Общее назначение электродных покрытий – обеспечение стабильности горения сварочной дуги и получение металла шва с заранее заданными свойствами. Наиболее важными свойствами являются пластичность, прочность, ударная вязкость, стойкость против коррозии.
Покрытие выполняет множество важных функций.
Во-первых, это газовая защита зоны сварки и раплавленного металла, которая образуется при сгорании газообразующих веществ. Она предохраняет раплавленный металл от воздействия кислорода и азота. Такие вещества вводятся в покрытие в виде древесной муки, целлюлозы, хлопчатобумажной ткани.
Во-вторых, раскисление металла сварочной ванны элементами, обладающими большим родством с кислородом, чем железо. К таким элементам относятся марганец, титан, молибден, хром, кремний, алюминий, графит. Раскислители входят в покрытие не в чистом виде, а в виде ферросплавов.
В-третьих, шлаковая защита. Шлаковое покрытие уменьшает скорость охлаждения и затвердения металла шва, способствуя тем самым выходу газовых и неметаллических включений.
Шлакообразующие компоненты покрытий представляют собой титановые и марганцевые руды, каолин, мрамор, кварцевый песок, доломит, полевой шпат и др.
В-четвертых, легирование металла шва для придания ему специальных свойств (повышение механических свойств, износостойкости, жаростойкости, сопротивления коррозии).
В качестве легирующих компонентов используются хром, никель, молибден, вольфрам, марганец, титан.
Кроме того, для повышения производительности сварки в электродные покрытия вводят железный порошок. Такой порошок облегчает повторное зажигание дуги, уменьшает скорость охлаждения наплавленного металла, что благоприятно сказывается на сварке в условиях низких температур. Содержание порошка может достигать до 60 % массы покрытия.
Для закрепления покрытия на стержне электрода обычно используют связующие компоненты – такие, как жидкое стекло.
Для придания покрытию лучших пластических свойств в него вводят формующие добавки – такие, как бетонит, каолин, декстрин, слюда и пр.
В зависимости от свариваемых материалов все электроды делятся на следующие группы:
Л – для сварки легированных конструкционных сталей с временным сопротивлением разрыву свыше 600 МПа (пять типов: Э70, Э85, Э100, Э125, Э150);
У – для сварки углеродистых и низкоуглеродистых конструкционных сталей;
В – для сварки высоколегированных сталей с особыми свойствами;
Т – для сварки легированных теплоустойчивых сталей – 9 типов;
Н – для наплавки поверхностных слоев с особыми свойствами – 44 типа.
Гарантируемый предел прочности металла шва обозначается в марке электродов цифрами. Например, название электрода, обозначенное Э42, говорит о том, что он предназначен для дуговой сварки; минимальный предел прочности металла шва – 420 МПа.
Электроды классифицируют по материалу, назначению для сварки определенных сталей, по толщине покрытия, нанесенного на стержень, видам покрытия, характеру шлака, образующегося при расплавлении, техническим свойствам металла шва и пр.
На все электроды наносится определенный состав – покрытие. Общее назначение электродных покрытий – обеспечение стабильности горения сварочной дуги и получение металла шва с заранее заданными свойствами. Наиболее важными свойствами являются пластичность, прочность, ударная вязкость, стойкость против коррозии.
Покрытие выполняет множество важных функций.
Во-первых, это газовая защита зоны сварки и раплавленного металла, которая образуется при сгорании газообразующих веществ. Она предохраняет раплавленный металл от воздействия кислорода и азота. Такие вещества вводятся в покрытие в виде древесной муки, целлюлозы, хлопчатобумажной ткани.
Во-вторых, раскисление металла сварочной ванны элементами, обладающими большим родством с кислородом, чем железо. К таким элементам относятся марганец, титан, молибден, хром, кремний, алюминий, графит. Раскислители входят в покрытие не в чистом виде, а в виде ферросплавов.
В-третьих, шлаковая защита. Шлаковое покрытие уменьшает скорость охлаждения и затвердения металла шва, способствуя тем самым выходу газовых и неметаллических включений.
Шлакообразующие компоненты покрытий представляют собой титановые и марганцевые руды, каолин, мрамор, кварцевый песок, доломит, полевой шпат и др.
В-четвертых, легирование металла шва для придания ему специальных свойств (повышение механических свойств, износостойкости, жаростойкости, сопротивления коррозии).
В качестве легирующих компонентов используются хром, никель, молибден, вольфрам, марганец, титан.
Кроме того, для повышения производительности сварки в электродные покрытия вводят железный порошок. Такой порошок облегчает повторное зажигание дуги, уменьшает скорость охлаждения наплавленного металла, что благоприятно сказывается на сварке в условиях низких температур. Содержание порошка может достигать до 60 % массы покрытия.
Для закрепления покрытия на стержне электрода обычно используют связующие компоненты – такие, как жидкое стекло.
Для придания покрытию лучших пластических свойств в него вводят формующие добавки – такие, как бетонит, каолин, декстрин, слюда и пр.
В зависимости от свариваемых материалов все электроды делятся на следующие группы:
Л – для сварки легированных конструкционных сталей с временным сопротивлением разрыву свыше 600 МПа (пять типов: Э70, Э85, Э100, Э125, Э150);
У – для сварки углеродистых и низкоуглеродистых конструкционных сталей;
В – для сварки высоколегированных сталей с особыми свойствами;
Т – для сварки легированных теплоустойчивых сталей – 9 типов;
Н – для наплавки поверхностных слоев с особыми свойствами – 44 типа.
Гарантируемый предел прочности металла шва обозначается в марке электродов цифрами. Например, название электрода, обозначенное Э42, говорит о том, что он предназначен для дуговой сварки; минимальный предел прочности металла шва – 420 МПа.
Основные виды сварки
Дуговая сварка представляет собой соединение расплавленных металлов между собой с помощью электрической дуги (рис. 95).
Рис. 95. Дуговая сварка: 1 – соединяемые детали; 2 – электрод; 3 – дуга; 4 – сварочная ванна.
Этот тип сварки включает в себя такие виды, как плазменная, электрошлаковая, электронно-лучевая и термитная.
Плазменная сварка основана на пропускании электрического тока большой плотности через газовую среду, находящуюся под некоторым давлением. Ионизированный газ называют плазмой. Температура плазменной струи достигает 50 000 °C.
В электрошлаковой сварке плавление металла происходит за счет теплоты, выделяемой электрическим током, проходящим через расплавленный шлак (рис. 96).
Рис. 96. Электрошлаковая сварка: 1 – электрод; 2 – электропроводный шлак; 3 – образуемый шов; 4 – сварочная ванна; 5 – перегородки, формирующие шов; 6 – металл.
Энергия электронного луча нашла свое применение в электронно-лучевой сварке. Теплота выделяется в результате бомбардировки поверхности металла электронами, имеющими большие скорости; анодом служит свариваемая деталь, катодом – вольфрамовая спираль (рис. 97).
Рис. 97. Электронно-лучевая сварка: 1 – катод; 2 – пучок; 3 – соединяемые заготовки; 4 – магнитная линза; 5 – катушка.
Поверхность катода испускает электроны, формируемые в пучок, который фокусируется на соединяемые заготовки магнитной линзой. Перемещает луч специальная катушка.
Использование теплоты, выделяемой нагретой смесью оксида железа и алюминия, лежит в основе термитной сварки. Свариваемые детали находятся в огнеупорной форме, а в тигле, находящемся сверху, находится смесь металлов. При горении температура этой смеси (по-другому, термита) достигает более 2000 °C. В результате образуется жидкий металл, который при заполнении формы оплавляет кромки свариваемых изделий, заполняет зазор, образуя тем самым шов.
В ультразвуковой сварке ультразвуковые колебания передаются по волноводу от преобразователя к рабочему наконечнику.
Соединяемые изделия помещают между наконечником и специальной опорой.
Под действием вертикального сжимающего усилия и ультразвуковых колебаний в заготовках возникают силы трения, достаточные для получения сварного соединения (рис. 98).
Рис. 98. Ультразвуковая сварка: 1 – магнитострикционный преобразователь; 2 – волновод; 3 – рабочий наконечник; 4 – соединяемые изделия; 5 – опора.
При контактной сварке, которая, в свою очередь, делится на точечную и стыковую, происходит сварка давлением. Здесь соединяемые заготовки зажимаются электродами. В зоне контакта под действием сварочного тока происходит сильный разогрев, затем сжатие заготовок и, как результат, образование сварного соединения (рис. 99).
Рис. 99. Контактная сварка: 1 – соединяемые заготовки; 2 – электроды; 3 – зона контакта.
Если при соединении изделия используют радиочастотную сварку, то свариваемые заготовки нагреваются с помощью высокочастотного индуктора. В результате этого происходит оплавление кромок заготовок. Сварное соединение получается в результате сжимающего действия роликов (рис. 100). Сердечник из феррита повышает эффективность процесса.
Рис. 100. Радиочастотная сварка: 1 – высокочастотный индуктор; 2 – свариваемые части; 3 – ролики; 4 – ферритовый сердечник.
Лазерная сварка осуществляется световым лучом, получаемым от специальных твердых и газовых излучателей. Вакуум при сварке лазером не нужен, и ее можно выполнять на воздухе даже на значительном расстоянии от генератора (рис. 101).
Рис. 101. Лазерная сварка: 1 – излучение лазера; 2 – линза; 3 – свариваемые заготовки; 4 – лампа накачки; 5 – рубиновый стержень.
Сварка трением осуществляется с помощью вращения одного из стержней и соприкосновения его торца с торцом закрепленного стержня; концы стержней разогреваются и с приложением осевого усилия свариваются.
Холодная сварка базируется на свойстве металла схватываться при значительном давлении.
В зависимости от механизации процесса сварку можно разделить на ручную, механизированную и автоматическую.
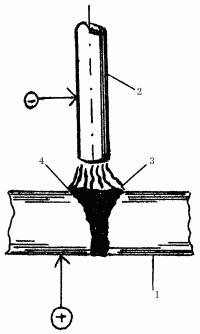
Этот тип сварки включает в себя такие виды, как плазменная, электрошлаковая, электронно-лучевая и термитная.
Плазменная сварка основана на пропускании электрического тока большой плотности через газовую среду, находящуюся под некоторым давлением. Ионизированный газ называют плазмой. Температура плазменной струи достигает 50 000 °C.
В электрошлаковой сварке плавление металла происходит за счет теплоты, выделяемой электрическим током, проходящим через расплавленный шлак (рис. 96).
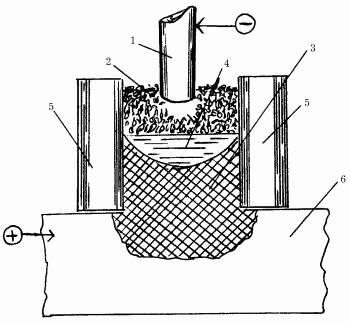
Энергия электронного луча нашла свое применение в электронно-лучевой сварке. Теплота выделяется в результате бомбардировки поверхности металла электронами, имеющими большие скорости; анодом служит свариваемая деталь, катодом – вольфрамовая спираль (рис. 97).
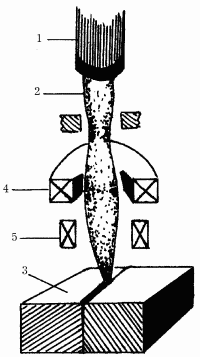
Поверхность катода испускает электроны, формируемые в пучок, который фокусируется на соединяемые заготовки магнитной линзой. Перемещает луч специальная катушка.
Использование теплоты, выделяемой нагретой смесью оксида железа и алюминия, лежит в основе термитной сварки. Свариваемые детали находятся в огнеупорной форме, а в тигле, находящемся сверху, находится смесь металлов. При горении температура этой смеси (по-другому, термита) достигает более 2000 °C. В результате образуется жидкий металл, который при заполнении формы оплавляет кромки свариваемых изделий, заполняет зазор, образуя тем самым шов.
В ультразвуковой сварке ультразвуковые колебания передаются по волноводу от преобразователя к рабочему наконечнику.
Соединяемые изделия помещают между наконечником и специальной опорой.
Под действием вертикального сжимающего усилия и ультразвуковых колебаний в заготовках возникают силы трения, достаточные для получения сварного соединения (рис. 98).
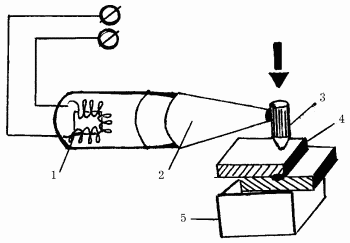
При контактной сварке, которая, в свою очередь, делится на точечную и стыковую, происходит сварка давлением. Здесь соединяемые заготовки зажимаются электродами. В зоне контакта под действием сварочного тока происходит сильный разогрев, затем сжатие заготовок и, как результат, образование сварного соединения (рис. 99).
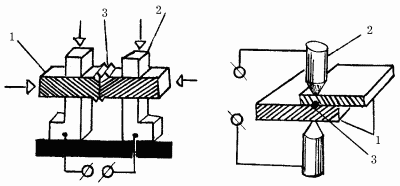
Если при соединении изделия используют радиочастотную сварку, то свариваемые заготовки нагреваются с помощью высокочастотного индуктора. В результате этого происходит оплавление кромок заготовок. Сварное соединение получается в результате сжимающего действия роликов (рис. 100). Сердечник из феррита повышает эффективность процесса.
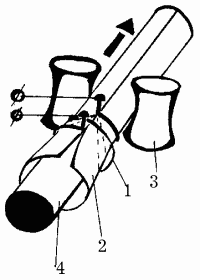
Лазерная сварка осуществляется световым лучом, получаемым от специальных твердых и газовых излучателей. Вакуум при сварке лазером не нужен, и ее можно выполнять на воздухе даже на значительном расстоянии от генератора (рис. 101).
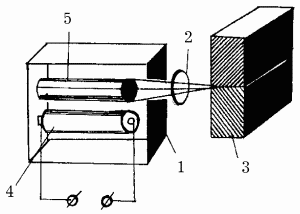
Сварка трением осуществляется с помощью вращения одного из стержней и соприкосновения его торца с торцом закрепленного стержня; концы стержней разогреваются и с приложением осевого усилия свариваются.
Холодная сварка базируется на свойстве металла схватываться при значительном давлении.
В зависимости от механизации процесса сварку можно разделить на ручную, механизированную и автоматическую.
Виды сварных соединений и швов при дуговой сварке
Сварные швы можно разделить на 4 вида: стыковые, тавровые, угловые и нахлесточные.
Сам по себе шов представляет закристаллизовавшийся металл, который в процессе сварки находился в расплавленном состоянии.
Стыковой шов предназначен для соединения торцевых поверхностей деталей, причем толщина их может быть различной (рис. 102).
Рис. 102. Стыковой шов.
Стыковые швы широко применяют в машиностроении, а также при сварке больших емкостей и труб.
В тавровом шве торец одной заготовки приваривается к боковой поверхности другой (рис. 103).
Рис. 103. Тавровый шов.
Обычно такие соединения имеют вид буквы «Т» (отсюда и название).
Элементы в тавровом соединении можно соединять как под прямым, так и под любым другим углом.
Угловой шов соединяет два элемента, которые находятся под любым углом друг к другу (рис. 104).
Рис. 104. Угловой шов.
Такие швы получили распространение в строительстве.
При соединении 2 листов металла, в котором один лист накладывается на другой с нахлестом, образуется нахлесточный шов (рис. 105).
Рис. 105. Нахлесточный шов.
Нахлесточные швы применяются в конструкциях металлических форм, резервуаров и пр.
Правку выполняют на станках или вручную. При правке устраняются деформации металла. Металл небольшой толщины правится в холодном состоянии, а толстый предварительно подогревается до 250–300 °C.
Целью разметки является нанесение размеров детали на металл. Обычно ее наносят по шаблонам из алюминиевого листа. При разметке используют линейку, угольник, рулетку, чертилку.
Резка может быть как механической, так и термической. Наиболее производительной является механическая. Термическая же, уступая ей, является более универсальной, так как позволяет с большей точностью выкроить заготовки различной геометрической формы.
Подготовка кромок, как и резка, ведется 2 способами: механическим и термическим. В основном используется механический способ. Используя 2 или 3 резака, расположенных под разными углами, можно получить кромки с односторонним или двусторонним скосом.
Кроме классической гибки, осуществляемой на листогибочных вальцах, существует множество других способов.
В подготовительные работы, кроме вышеперечисленных, входит также очистка металла от масла, ржавчины, окалины, влаги и различных неметаллических загрязнений. Присутствие этих загрязнений часто является причиной образования в сварных швах пор, трещин, шлаковых включений, что ведет к снижению прочности сварного соединения.
Зажигать дугу можно разными способами. При первом способе электрод приближают перпендикулярно к поверхности изделия и, коснувшись металла, быстро отводят вверх на необходимую длину дуги. При втором способе электродом вскользь чиркают по поверхности металла.
Существует такое понятие, как длина дуги. Она напрямую зависит от марки и диаметра электрода, разделки свариваемых кромок.
Нормальная длина дуги составляет 0,5–1,1 диаметра электрода. Если длину увеличить, то качество наплавленного металла шва снижается ввиду его интенсивного окисления и азотирования; глубина проплавления основного металла уменьшается, ухудшая внешний вид шва. Сварку можно вести в разных направлениях: от себя, к себе, слева направо, справа налево (рис. 106).
Рис. 106. Направление движения электродов: а – движение электрода вправо; б – движение электрода влево; в – движение электрода вверх; г – движение электрода вниз.
Независимо от этого электрод всегда должен быть наклонен к оси шва таким образом, чтобы основной металл проплавлялся на наибольшую глубину. Для получения гладкого и плотного шва необходимо, чтобы угол наклона электрода в сторону ведения шва составлял 15°.
Существует 3 основных направления движения электрода. Первое из них – поступательное вдоль оси. Движение вдоль оси позволяет обеспечить постоянство длины дуги и связать это со скоростью плавления электродов.
Второе движение электрода – перемещение вдоль оси образуемого валика в направлении наплавки для образования шва. Образуется узкий валик, ширина которого зависит от скорости перемещения дуги по поверхности и сварочного тока. Узкий валик накладывают, проваривая корень шва или сваривая тонкие листы.
Третье движение включает в себя поперечные колебательные движения электрода (рис. 107).
Рис. 107. Виды поперечных движений электрода при различных режимах прогрева: а – при слабом прогреве кромок; б – при усиленном прогреве кромок; в – при усиленном прогреве одной кромки; г – при хорошем прогреве корня шва.
Сам по себе шов представляет закристаллизовавшийся металл, который в процессе сварки находился в расплавленном состоянии.
Стыковой шов предназначен для соединения торцевых поверхностей деталей, причем толщина их может быть различной (рис. 102).
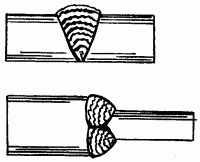
Стыковые швы широко применяют в машиностроении, а также при сварке больших емкостей и труб.
В тавровом шве торец одной заготовки приваривается к боковой поверхности другой (рис. 103).
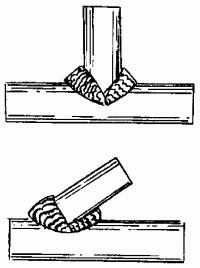
Обычно такие соединения имеют вид буквы «Т» (отсюда и название).
Элементы в тавровом соединении можно соединять как под прямым, так и под любым другим углом.
Угловой шов соединяет два элемента, которые находятся под любым углом друг к другу (рис. 104).
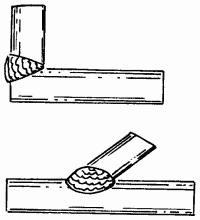
Такие швы получили распространение в строительстве.
При соединении 2 листов металла, в котором один лист накладывается на другой с нахлестом, образуется нахлесточный шов (рис. 105).
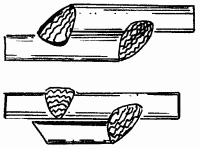
Нахлесточные швы применяются в конструкциях металлических форм, резервуаров и пр.
Подготовительные работы
Подготовительные работы включают в себя правку, разметку, резку, подготовку кромок под сварку и холодную или горячую гибку.Правку выполняют на станках или вручную. При правке устраняются деформации металла. Металл небольшой толщины правится в холодном состоянии, а толстый предварительно подогревается до 250–300 °C.
Целью разметки является нанесение размеров детали на металл. Обычно ее наносят по шаблонам из алюминиевого листа. При разметке используют линейку, угольник, рулетку, чертилку.
Резка может быть как механической, так и термической. Наиболее производительной является механическая. Термическая же, уступая ей, является более универсальной, так как позволяет с большей точностью выкроить заготовки различной геометрической формы.
Подготовка кромок, как и резка, ведется 2 способами: механическим и термическим. В основном используется механический способ. Используя 2 или 3 резака, расположенных под разными углами, можно получить кромки с односторонним или двусторонним скосом.
Кроме классической гибки, осуществляемой на листогибочных вальцах, существует множество других способов.
В подготовительные работы, кроме вышеперечисленных, входит также очистка металла от масла, ржавчины, окалины, влаги и различных неметаллических загрязнений. Присутствие этих загрязнений часто является причиной образования в сварных швах пор, трещин, шлаковых включений, что ведет к снижению прочности сварного соединения.
Техника выполнения ручной дуговой сварки
Дуговая сварка металлическими электродами с покрытием остается самым распространенным методом, применяемым при изготовлении и монтаже конструкций. В начале работы следует зажечь (возбудить) дугу, установив нужное значение сварочного тока. Оно зависит от марки электрода и типа сварного соединения.Зажигать дугу можно разными способами. При первом способе электрод приближают перпендикулярно к поверхности изделия и, коснувшись металла, быстро отводят вверх на необходимую длину дуги. При втором способе электродом вскользь чиркают по поверхности металла.
Существует такое понятие, как длина дуги. Она напрямую зависит от марки и диаметра электрода, разделки свариваемых кромок.
Нормальная длина дуги составляет 0,5–1,1 диаметра электрода. Если длину увеличить, то качество наплавленного металла шва снижается ввиду его интенсивного окисления и азотирования; глубина проплавления основного металла уменьшается, ухудшая внешний вид шва. Сварку можно вести в разных направлениях: от себя, к себе, слева направо, справа налево (рис. 106).
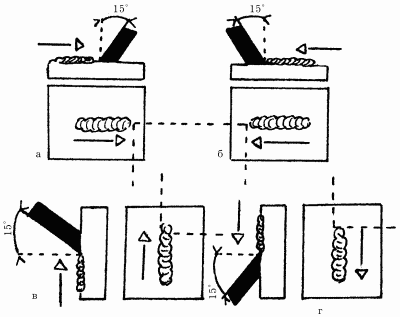
Независимо от этого электрод всегда должен быть наклонен к оси шва таким образом, чтобы основной металл проплавлялся на наибольшую глубину. Для получения гладкого и плотного шва необходимо, чтобы угол наклона электрода в сторону ведения шва составлял 15°.
Существует 3 основных направления движения электрода. Первое из них – поступательное вдоль оси. Движение вдоль оси позволяет обеспечить постоянство длины дуги и связать это со скоростью плавления электродов.
Второе движение электрода – перемещение вдоль оси образуемого валика в направлении наплавки для образования шва. Образуется узкий валик, ширина которого зависит от скорости перемещения дуги по поверхности и сварочного тока. Узкий валик накладывают, проваривая корень шва или сваривая тонкие листы.
Третье движение включает в себя поперечные колебательные движения электрода (рис. 107).
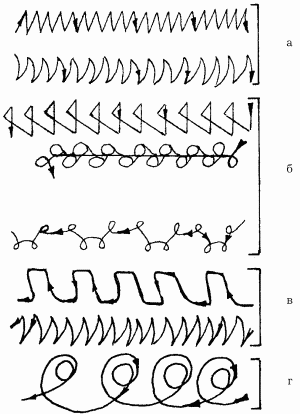