Страница:
Монтаж магистральных и производственных трубопроводов предусматривает сварку как основной способ соединения. Ее ведут при температуре окружающего воздуха не ниже -20 °C, так как при более низких температурах происходит интенсивное насыщение расплавленного металла шва такими газами, как кислород и водород. Такое насыщение вызывает пористость и ведет к снижению механической стойкости сварного шва.
Подготовка кромок труб к сварке и качество сборки стыков оказывают влияние на качество сварного соединения. Основными типами сварных соединений труб являются v-образное или чашеобразное стыковое. В подготовку входят правка свариваемых концов, очистка кромок от грязи и масла и сборка. Для правки труб применяют механические, гидравлические и пневматические приспособления.
Кромки под сварку готовят на заводах-изготовителях труб. Угол скоса составляет 25–30°. Если скос отсутствует, следует снять фаску резцом или резаком-труборезом.
Очистка свариваемых кромок заключается в удалении масла и органических покрытий бензином или специальным растворителем. Если имеются грязь и ржавчина, то их счищают с помощью стальных щеток или абразивных кругов.
Сборка стыков под сварку состоит в том, что кромки труб совмещают таким образом, чтобы поверхность свариваемых труб совпадала и не была нарушена ось нитки трубопровода. Необходимо, чтобы зазор между кромками имел одинаковые размеры по всему контуру шва. При сборке часто используют центратор. Стыки после сборки прихватывают сварными швами длиной 60–80 мм с расстоянием между прихватами 300–400 мм при диаметре труб до 300 мм. Желательно выполнять прихватки теми же электродами, что и стык. Такой прием позволяет обеспечить однородность наплавленного металла и хорошее качество шва.
Если применяется внутренний центратор, то вместо прихватки применяют сплошную заварку корня шва в виде первого слоя.
Режимы сварки
Виды установок для ручной сварки
Автоматизированная сварка
Сварочные полуавтоматы нашли широкое применение во всех сферах строительства и промышленности. Все трудные места доступны для сварки полуавтоматом. Часть полуавтоматов снабжена программным устройством в блоке управления.
Единая система обозначения позволяет грамотно выбрать для каждого вида работ нужную марку сварочного аппарата.
В обозначении полуавтомата сначала проставляются буквы. Первая буква обозначает изделие, например: П – полуавтомат, У – установка.
Вторая буква говорит о способе сварки: Ш – шланговый, Д – для дуговой сварки.
Третья буква дает информацию о способе сварки в определенной среде, например: Ф – флюсовый, ФГ – флюсо-газовый. Наличие третьей буквы вовсе необязательно, и она может вообще отсутствовать. Обычно все полуавтоматы ведут сварку в газозащитной среде, и поэтому повторять это в обозначении не имеет смысла.
После буквенных индексов следуют цифры. Первая показывает значение силы тока в сотнях ампер. Вторая и третья цифры обозначают модификацию полуавтомата.
После третьей цифры опять следует буква, обозначающая климатические условия, например: У – район с умеренным климатом; ХЛ – район с холодным климатом; Т – тропики.
Последняя цифра указывает категорию помещения: 1 – на открытом воздухе; 2 – неотапливаемое помещение; 3 – помещение с естественной вентиляцией; 4 – помещение с принудительной вентиляцией и отоплением; 5 – помещение с повышенной влажностью. Электродная проволока в полуавтоматах подается по пустотелому шлангу (отсюда название «шланговый полуавтомат»). Все модели взаимозаменяемы и унифицированы, имеют единые разъемы и диаметры электродной проволоки; энергетические параметры у них также совпадают. Такая совместимость позволяет при необходимости использовать электродвигатели, горелки, катушки с проволокой и подающие механизмы, взятые с аппаратов разных марок. На рисунке 122 представлена схема полуавтомата для сварки в среде защитного газа.
Рис. 122. Схема сварочного полуавтомата для сварки в среде защитного газа.
Составными частями такого устройства являются сменная газовая горелка, подающий механизм, шланг подачи электродной проволоки, кассеты для хранения проволоки, газовый шланг, блок управления, источник питания, провод цепи управления, газовая аппаратура, кабели.
Устройство сварочной горелки
Управление сварочными полуавтоматами
Особенности газовой сварки черных металлов
Газовая сварка легированных сталей
Газовая сварка углеродистых сталей
Газовая резка
Классификация резаков и установок для ручной резки
Подготовка кромок труб к сварке и качество сборки стыков оказывают влияние на качество сварного соединения. Основными типами сварных соединений труб являются v-образное или чашеобразное стыковое. В подготовку входят правка свариваемых концов, очистка кромок от грязи и масла и сборка. Для правки труб применяют механические, гидравлические и пневматические приспособления.
Кромки под сварку готовят на заводах-изготовителях труб. Угол скоса составляет 25–30°. Если скос отсутствует, следует снять фаску резцом или резаком-труборезом.
Очистка свариваемых кромок заключается в удалении масла и органических покрытий бензином или специальным растворителем. Если имеются грязь и ржавчина, то их счищают с помощью стальных щеток или абразивных кругов.
Сборка стыков под сварку состоит в том, что кромки труб совмещают таким образом, чтобы поверхность свариваемых труб совпадала и не была нарушена ось нитки трубопровода. Необходимо, чтобы зазор между кромками имел одинаковые размеры по всему контуру шва. При сборке часто используют центратор. Стыки после сборки прихватывают сварными швами длиной 60–80 мм с расстоянием между прихватами 300–400 мм при диаметре труб до 300 мм. Желательно выполнять прихватки теми же электродами, что и стык. Такой прием позволяет обеспечить однородность наплавленного металла и хорошее качество шва.
Если применяется внутренний центратор, то вместо прихватки применяют сплошную заварку корня шва в виде первого слоя.
Режимы сварки
Если ведется ручная дуговая сварка, то ее выполняют в 2–3 слоя, так как многослойная сварка обеспечивает глубокий провар корня и повышает плотность сварного соединения. Такой способ применяют с поворотом и без поворота свариваемых стыков.
При сварке поворотных стыков применяется следующий способ (рис. 120): первым слоем заваривают участки от точки 1 до точки 2 и от точки 4 до точки 3 на всех стыках труб.
Рис. 120. Последовательность сварки поворотных стыков.
После этого секцию поворачивают на 90° и заваривают участки от точки 4 до точки 1 и от точки 3 до точки 2. Чтобы не образовался прожог металла, рекомендуется производить сварку первого слоя электродами диаметром 4 мм при сварочном токе 120–140 А. Наварку слоев следует выполнять в одном направлении с постепенным поворотом свариваемой секции.
Если сваривается неповоротный стык, то сварку ведут при соединении секций в одну плеть и окончательном монтаже трубопровода. Порядок наложения сварных швов следующий: первый слой – швы 1, 2, 3 завариваются снизу вверх; последующие – сверху вниз.
Замки, или замыкающие участки в смежных слоях шва, должны отстоять друг от друга на расстоянии примерно 60–100 мм; в потолочной части шва удобно заканчивать сварку на расстоянии 50–70 мм от нижней точки. Если сварку неповоротных стыков выполнить невозможно, то применяют комбинированный способ (рис. 121).
Рис. 121. Комбинированный способ сварки: 1 – нижняя часть шва; 2 – вставка; 3 – верхняя часть шва.
При этом способе сваривают стык со вставкой 2, при этом нижняя часть шва 1 заваривается с внутренней стороны; верхняя часть шва 3 заваривается с наружной стороны. Тип применяемых электродов тот же, что и при сварке поворотных стыков.
При сварке поворотных стыков применяется следующий способ (рис. 120): первым слоем заваривают участки от точки 1 до точки 2 и от точки 4 до точки 3 на всех стыках труб.
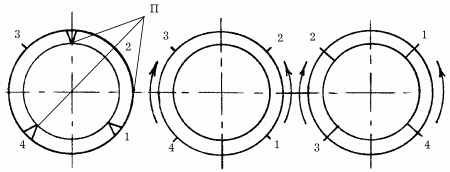
После этого секцию поворачивают на 90° и заваривают участки от точки 4 до точки 1 и от точки 3 до точки 2. Чтобы не образовался прожог металла, рекомендуется производить сварку первого слоя электродами диаметром 4 мм при сварочном токе 120–140 А. Наварку слоев следует выполнять в одном направлении с постепенным поворотом свариваемой секции.
Если сваривается неповоротный стык, то сварку ведут при соединении секций в одну плеть и окончательном монтаже трубопровода. Порядок наложения сварных швов следующий: первый слой – швы 1, 2, 3 завариваются снизу вверх; последующие – сверху вниз.
Замки, или замыкающие участки в смежных слоях шва, должны отстоять друг от друга на расстоянии примерно 60–100 мм; в потолочной части шва удобно заканчивать сварку на расстоянии 50–70 мм от нижней точки. Если сварку неповоротных стыков выполнить невозможно, то применяют комбинированный способ (рис. 121).
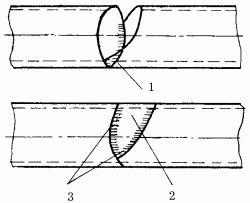
При этом способе сваривают стык со вставкой 2, при этом нижняя часть шва 1 заваривается с внутренней стороны; верхняя часть шва 3 заваривается с наружной стороны. Тип применяемых электродов тот же, что и при сварке поворотных стыков.
Виды установок для ручной сварки
Для облегчения и совершенствования процесса сварки на практике широко применяются специальные установки, работающие как при постоянном, так и при переменном токе.
Установки серии УПС предназначены для ручной дуговой сварки в непрерывном и импульсном режимах. Установка марки УПС-301У4 дает пульсирующую дугу и в состоянии обеспечить процесс точечной сварки.
В комплект входят горелка, блок поджигания с возбудителем дуги, сварочный выпрямитель с тиристорным регулированием сварочного тока, дистанционный регулятор сварочного тока. Кроме этого, УПС снабжена ротаметрами и клапанами.
Универсальная установка УДГУ-301 работает как на постоянном, так и на переменном токе.
УДГ-201УХЛ4 может работать на постоянном токе прямой полярности. Ее применяют для аргонодуговой сварки в непрерывном и импульсном режиме. При токе в 200 А установка помогает сваривать медь, никель и все сплавы на их основе, а также коррозионные стали.
При сварке переменным током хорошо зарекомендовали себя установки УДГ-301-1 и УДГ-500-1. В данных установках применяются горелки ЭЗР-4, ГР-10, ГСН-1. При монтаже на токах до 150 А хорошо зарекомендовали себя горелки с воздушным охлаждением типа ЭЗР-3 и ЭЗР-5.
Установки серии УПС предназначены для ручной дуговой сварки в непрерывном и импульсном режимах. Установка марки УПС-301У4 дает пульсирующую дугу и в состоянии обеспечить процесс точечной сварки.
В комплект входят горелка, блок поджигания с возбудителем дуги, сварочный выпрямитель с тиристорным регулированием сварочного тока, дистанционный регулятор сварочного тока. Кроме этого, УПС снабжена ротаметрами и клапанами.
Универсальная установка УДГУ-301 работает как на постоянном, так и на переменном токе.
УДГ-201УХЛ4 может работать на постоянном токе прямой полярности. Ее применяют для аргонодуговой сварки в непрерывном и импульсном режиме. При токе в 200 А установка помогает сваривать медь, никель и все сплавы на их основе, а также коррозионные стали.
При сварке переменным током хорошо зарекомендовали себя установки УДГ-301-1 и УДГ-500-1. В данных установках применяются горелки ЭЗР-4, ГР-10, ГСН-1. При монтаже на токах до 150 А хорошо зарекомендовали себя горелки с воздушным охлаждением типа ЭЗР-3 и ЭЗР-5.
Автоматизированная сварка
Виды сварочных полуавтоматов
Полуавтоматы применяются при дуговой механизированной сварке. В их конструкцию, помимо других комплектующих, входят горелка, которая перемещается вручную, и автоматизированное устройство для подачи электродной проволоки.Сварочные полуавтоматы нашли широкое применение во всех сферах строительства и промышленности. Все трудные места доступны для сварки полуавтоматом. Часть полуавтоматов снабжена программным устройством в блоке управления.
Единая система обозначения позволяет грамотно выбрать для каждого вида работ нужную марку сварочного аппарата.
В обозначении полуавтомата сначала проставляются буквы. Первая буква обозначает изделие, например: П – полуавтомат, У – установка.
Вторая буква говорит о способе сварки: Ш – шланговый, Д – для дуговой сварки.
Третья буква дает информацию о способе сварки в определенной среде, например: Ф – флюсовый, ФГ – флюсо-газовый. Наличие третьей буквы вовсе необязательно, и она может вообще отсутствовать. Обычно все полуавтоматы ведут сварку в газозащитной среде, и поэтому повторять это в обозначении не имеет смысла.
После буквенных индексов следуют цифры. Первая показывает значение силы тока в сотнях ампер. Вторая и третья цифры обозначают модификацию полуавтомата.
После третьей цифры опять следует буква, обозначающая климатические условия, например: У – район с умеренным климатом; ХЛ – район с холодным климатом; Т – тропики.
Последняя цифра указывает категорию помещения: 1 – на открытом воздухе; 2 – неотапливаемое помещение; 3 – помещение с естественной вентиляцией; 4 – помещение с принудительной вентиляцией и отоплением; 5 – помещение с повышенной влажностью. Электродная проволока в полуавтоматах подается по пустотелому шлангу (отсюда название «шланговый полуавтомат»). Все модели взаимозаменяемы и унифицированы, имеют единые разъемы и диаметры электродной проволоки; энергетические параметры у них также совпадают. Такая совместимость позволяет при необходимости использовать электродвигатели, горелки, катушки с проволокой и подающие механизмы, взятые с аппаратов разных марок. На рисунке 122 представлена схема полуавтомата для сварки в среде защитного газа.
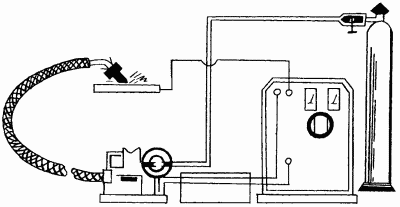
Составными частями такого устройства являются сменная газовая горелка, подающий механизм, шланг подачи электродной проволоки, кассеты для хранения проволоки, газовый шланг, блок управления, источник питания, провод цепи управления, газовая аппаратура, кабели.
Устройство сварочной горелки
Горелку используют для подачи в зону горения защитного газа или флюса и электродной проволоки. Рукоятка горелка отличается прочностью и удобством. Ее обычно выполняют из литьевого изоляционного материала. Она снабжена предохранительным щитком и пусковой кнопкой. Главными элементами горелки являются сопло и подводящий ток наконечник (рис. 123).
Рис. 123. Горелка с плавящимся электродом в среде защитного газа: 1 – трубка подачи защитного газа; 2 – вход плавящегося электрода (проволоки); 3 – подвод защитного газа к соплу; 4 – рабочее сопло; 5 – струя защитного газа вокруг электрода; 6 – электрод в месте возникновения дуги; 7 – кнопка пуска; 8 – защитный щиток; 9 – переходная втулка; 10 – сеточные (металлокерамические) вставки.
Сопло горелки постоянно подвергается налипанию расплавленного металла. Этот недостаток сопла устраняется хромированием, полированием или заменой материала на керамику. При значении сварочного тока, равном 325 А и больше, сопло горелки дополнительно охлаждается. Каждые полгода необходимо заменять горелку на новую.
Наконечники для подачи тока рассчитаны примерно на 5–10 ч непрерывной работы. Их изготавливают из самых различных материалов – меди, бронзы, сплава меди и графита, меди и вольфрама. Самый короткий срок службы – у медного наконечника.
Медно-графитовые наконечники, имея малый срок службы, лучше обеспечивают контакт при сварке и гарантируют хорошее скольжение, что особенно важно при сварке алюминиевой проволокой. Самую длительную работу обеспечивают наконечники на медно-вольфрамовой основе.
При сварке низколегированных и низкоуглеродистых сталей в среде углекислого газа применяют полуавоматы ПДГ. ПДГ состоит из источника постоянного тока, подающего механизма, газовой аппаратуры, сварочных горелок и соединительного гибкого шланга. В автоматах этого типа применяют горелки марки ГДПГ. В корпусе изделия размещен типовой блок питания. С помощью блока управления можно осуществлять в режиме наладки следующие операции: включение подачи защитного газа для настройки его расхода; подача электродной проволоки с заданной скоростью; вид рабочего цикла; настройка на определенный вид сварки (длинными, короткими, точечными швами).
Если полуавтомат работает в режиме сварки, то выполнение команд о начале и конце сварки обеспечивает блок управления. В начале сварки блок управления включает подачу защитного газа и источник питания и немного погодя (через 0,5 с) включает подачу электродной проволоки со стабильной скоростью.
При включении команды о прекращении сварки выключается электродвигатель подающего механизма и происходит его торможение; спустя некоторое время (до 5 с) источник питания и подача защитного газа отключаются.
Полуавтоматы ПДГ предназначены для работы в умеренном климате. Марки ПДГ-305 и ПДИ-303 предназначены для работы преимущественно в холодном климате. Если в работе будут задействованы полуавтоматы ПШ-13 или ПДГ-516, то сварка будет вестись с помощью стальной и порошковой проволоки.
Если предстоит сварка изделий из титановых сплавов, то подойдет полуавтомат ПШ-109. Он предназначен для сварки конструкций из титановых сплавов сплошной электродной проволокой в аргоносодержащих газовых смесях. С помощью этого автомата можно вести сварку во всех пространственных положениях, кроме потолочного. В качестве подающего механизма здесь используется механизм «Изаплан»; генератор ГИИДС-1 обеспечивает сварку в импульсном режиме; для принудительного обдува остывающей зоны шва в полуавтомате используется охлаждающее устройство. Скорость подачи проволоки здесь регулируется путем изменения скорости вращения вала двигателя. Усилие прижатия подающих роликов можно регулировать с помощью конусного корпуса подающей головки.
К универсальным относятся полуавтоматы А-1197 и ПШ-112. А-1197 используют для сварки в среде углекислого газа и под флюсом порошковой и сплошной проволокой. В этом автомате газовая и флюсовая аппаратура взаимозаменяема: если газовую аппаратуру заменить на флюсовую, то схема готова к сварке под флюсом.
Так же обстоит дело и с типами применяемых горелок. При работе в среде защитного газа используется горелка ГДПГ, которую в случае необходимости можно заменить другой маркой, например А-1231-5-Ф2 (в режиме сварки под флюсом).
Для сварки порошковой самозащитной проволокой применяется полуавтомат ПШ-112. Если предстоит сварка сплошной проволокой в углекислом газе, то ПШ-112 предоставляет для этого вида работ возможность переоборудования. Программное устройство, встроенное в блок управления БУСП-1, позволяет программировать линейную зависимость сварочного тока при замене электрода или режима сварки. Благодаря такому устройству облегчается наладка автомата и гарантируется качество швов.
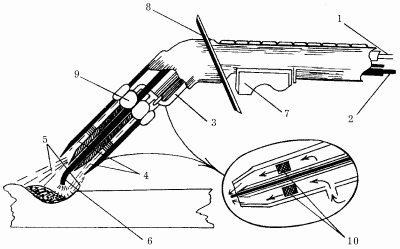
Сопло горелки постоянно подвергается налипанию расплавленного металла. Этот недостаток сопла устраняется хромированием, полированием или заменой материала на керамику. При значении сварочного тока, равном 325 А и больше, сопло горелки дополнительно охлаждается. Каждые полгода необходимо заменять горелку на новую.
Наконечники для подачи тока рассчитаны примерно на 5–10 ч непрерывной работы. Их изготавливают из самых различных материалов – меди, бронзы, сплава меди и графита, меди и вольфрама. Самый короткий срок службы – у медного наконечника.
Медно-графитовые наконечники, имея малый срок службы, лучше обеспечивают контакт при сварке и гарантируют хорошее скольжение, что особенно важно при сварке алюминиевой проволокой. Самую длительную работу обеспечивают наконечники на медно-вольфрамовой основе.
При сварке низколегированных и низкоуглеродистых сталей в среде углекислого газа применяют полуавоматы ПДГ. ПДГ состоит из источника постоянного тока, подающего механизма, газовой аппаратуры, сварочных горелок и соединительного гибкого шланга. В автоматах этого типа применяют горелки марки ГДПГ. В корпусе изделия размещен типовой блок питания. С помощью блока управления можно осуществлять в режиме наладки следующие операции: включение подачи защитного газа для настройки его расхода; подача электродной проволоки с заданной скоростью; вид рабочего цикла; настройка на определенный вид сварки (длинными, короткими, точечными швами).
Если полуавтомат работает в режиме сварки, то выполнение команд о начале и конце сварки обеспечивает блок управления. В начале сварки блок управления включает подачу защитного газа и источник питания и немного погодя (через 0,5 с) включает подачу электродной проволоки со стабильной скоростью.
При включении команды о прекращении сварки выключается электродвигатель подающего механизма и происходит его торможение; спустя некоторое время (до 5 с) источник питания и подача защитного газа отключаются.
Полуавтоматы ПДГ предназначены для работы в умеренном климате. Марки ПДГ-305 и ПДИ-303 предназначены для работы преимущественно в холодном климате. Если в работе будут задействованы полуавтоматы ПШ-13 или ПДГ-516, то сварка будет вестись с помощью стальной и порошковой проволоки.
Если предстоит сварка изделий из титановых сплавов, то подойдет полуавтомат ПШ-109. Он предназначен для сварки конструкций из титановых сплавов сплошной электродной проволокой в аргоносодержащих газовых смесях. С помощью этого автомата можно вести сварку во всех пространственных положениях, кроме потолочного. В качестве подающего механизма здесь используется механизм «Изаплан»; генератор ГИИДС-1 обеспечивает сварку в импульсном режиме; для принудительного обдува остывающей зоны шва в полуавтомате используется охлаждающее устройство. Скорость подачи проволоки здесь регулируется путем изменения скорости вращения вала двигателя. Усилие прижатия подающих роликов можно регулировать с помощью конусного корпуса подающей головки.
К универсальным относятся полуавтоматы А-1197 и ПШ-112. А-1197 используют для сварки в среде углекислого газа и под флюсом порошковой и сплошной проволокой. В этом автомате газовая и флюсовая аппаратура взаимозаменяема: если газовую аппаратуру заменить на флюсовую, то схема готова к сварке под флюсом.
Так же обстоит дело и с типами применяемых горелок. При работе в среде защитного газа используется горелка ГДПГ, которую в случае необходимости можно заменить другой маркой, например А-1231-5-Ф2 (в режиме сварки под флюсом).
Для сварки порошковой самозащитной проволокой применяется полуавтомат ПШ-112. Если предстоит сварка сплошной проволокой в углекислом газе, то ПШ-112 предоставляет для этого вида работ возможность переоборудования. Программное устройство, встроенное в блок управления БУСП-1, позволяет программировать линейную зависимость сварочного тока при замене электрода или режима сварки. Благодаря такому устройству облегчается наладка автомата и гарантируется качество швов.
Управление сварочными полуавтоматами
В зависимости от того, какой тип двигателя подающего механизма встроен в конкретный автомат, все системы управления ими делятся на три группы.
В первую группу входят полуавтоматы, работающие от электродвигателя постоянного тока, который подсоединен к источнику питания сварочной дуги.
Во вторую группу входят полуавтоматы, работающие от асинхронных двигателей.
Третья группа включает в себя полуавтоматы, работающие от электродвигателей постоянного тока, которые регулируют плавную подачу проволоки в определенном диапазоне. Система управления автоматами представлена в виде отдельных узлов.
Для работы первой группы системы управления необходимо убрать блоки 3, 5, 7. Здесь скорость подачи проволоки регулируется в узком диапазоне напряжения сварочной дуги, что существенно влияет на применение данной схемы.
Вторая группа системы управления начинает работать при выключении из работы блоков 3 и 5. В этой схеме производительность работы полуавтомата уменьшается за счет постоянного регулирования скорости подачи электродной проволоки.
Самой совершенной является третья группа системы управления. В ней нет недостатков, присущих двум первым системам. Тиристоры и транзисторы позволяют регулировать скорость подачи электродной проволоки в широком диапазоне. Это влияет на надежность системы в целом и позволяет уменьшить размеры аппаратуры.
В первую группу входят полуавтоматы, работающие от электродвигателя постоянного тока, который подсоединен к источнику питания сварочной дуги.
Во вторую группу входят полуавтоматы, работающие от асинхронных двигателей.
Третья группа включает в себя полуавтоматы, работающие от электродвигателей постоянного тока, которые регулируют плавную подачу проволоки в определенном диапазоне. Система управления автоматами представлена в виде отдельных узлов.
Для работы первой группы системы управления необходимо убрать блоки 3, 5, 7. Здесь скорость подачи проволоки регулируется в узком диапазоне напряжения сварочной дуги, что существенно влияет на применение данной схемы.
Вторая группа системы управления начинает работать при выключении из работы блоков 3 и 5. В этой схеме производительность работы полуавтомата уменьшается за счет постоянного регулирования скорости подачи электродной проволоки.
Самой совершенной является третья группа системы управления. В ней нет недостатков, присущих двум первым системам. Тиристоры и транзисторы позволяют регулировать скорость подачи электродной проволоки в широком диапазоне. Это влияет на надежность системы в целом и позволяет уменьшить размеры аппаратуры.
Особенности газовой сварки черных металлов
Процесс газовой сварки черных металлов имеет ряд особенностей. О них будет рассказно ниже.
Газовая сварка легированных сталей
Возможность осуществления газовой сварки для соединения легированных сталей, которые имеют в своем составе хром, никель, молибден, титан и другие элементы, зависит от особенностей химического состава того или иного вида стали.
Таким образом, газовая сварка в принципе применима для соединения хромистых сталей, но лишь при тщательном соблюдении термического режима.
Хромоникелевая стальможет быть подвергнута сварке ацетиленом, но при этом обязательно нужно использовать специальные флюсы. Кроме того, толщина свариваемого металла не должна быть более 1–2 мм, а последующая термическая обработка его крайне необходима.
Следует заметить, что при неукоснительном соблюдении указанных условий механические характеристики шовного соединения будут значительно хуже, чем у основного металла. Чтобы добиться высокого качества шва, сварку необходимо производить только электродами со специальными покрытиями.
Нужно запомнить, что применение газов-заменителей ацетилена при газовой сварке данной стали совершенно исключено.
Для высококачественного соединения хромоникелевых сталей нужно применять аргонодуговую сварку, так как в результате получаются прочные и надежные швы.
Молибденовая сталь, подобно хромистым сталям, имеет склонность к закалке на воздухе при температуре ниже 0 °C. Поэтому по завершении газовой сварки необходимо провести термообработку с целью замедления процесса остывания шва. Помимо этого, сварку упомянутой стали нужно проводить лишь после того, как металл будет прогрет до температуры 250–300 °C.
Указанное условие приобретает особенно важное значение при сварке металла толщиной свыше 10 мм и при сварке в условиях отрицательных температур.
Высокохромистая сталь
Подвергать эту сталь газовой сварке не рекомендуется вообще, так как при длительном термическом воздействии в процессе сварки будет происходить возникновение многочисленных зерен из-за большого содержания хрома – свыше 15 %.Хромистая сталь
Совершенно очевидно, что при проведении газовой сварки роста зерен не будет, так как указанная сталь содержит в своем составе гораздо меньше хрома, чем высокохромистая. Однако хромистая сталь непосредственно после сварки быстро закаливается на воздухе, а это всегда приводит к возникновению трещин. Предупредить этот негативный процесс можно лишь таким образом: осуществить замедление остывания шовного соединения. Для этого по окончании сварки следует продолжить нагревание металла пламенем горелки вблизи шва, в зоне 30–40 мм от него.Таким образом, газовая сварка в принципе применима для соединения хромистых сталей, но лишь при тщательном соблюдении термического режима.
Хромоникелевая стальможет быть подвергнута сварке ацетиленом, но при этом обязательно нужно использовать специальные флюсы. Кроме того, толщина свариваемого металла не должна быть более 1–2 мм, а последующая термическая обработка его крайне необходима.
Следует заметить, что при неукоснительном соблюдении указанных условий механические характеристики шовного соединения будут значительно хуже, чем у основного металла. Чтобы добиться высокого качества шва, сварку необходимо производить только электродами со специальными покрытиями.
Нужно запомнить, что применение газов-заменителей ацетилена при газовой сварке данной стали совершенно исключено.
Для высококачественного соединения хромоникелевых сталей нужно применять аргонодуговую сварку, так как в результате получаются прочные и надежные швы.
Молибденовая сталь, подобно хромистым сталям, имеет склонность к закалке на воздухе при температуре ниже 0 °C. Поэтому по завершении газовой сварки необходимо провести термообработку с целью замедления процесса остывания шва. Помимо этого, сварку упомянутой стали нужно проводить лишь после того, как металл будет прогрет до температуры 250–300 °C.
Указанное условие приобретает особенно важное значение при сварке металла толщиной свыше 10 мм и при сварке в условиях отрицательных температур.
Хромомолибденовая сталь
Ее можно подвергать газовой сварке при соблюдении определенных условий.
Газовая сварка углеродистых сталей
Нужно сразу заметить, что при работе с высокоуглеродистой сталью следует применять только наплавку или пайку; газовую сварку использовать нельзя.
В отношении низко– и среднеуглеродистых сталей возможно применение газовой сварки, эффективность которой в смысле прочности шва будет тем выше, чем меньше содержание углерода в стали. Таким образом, очень хорошая свариваемость будет у низкоуглеродистой стали, особенности сварки которой изложены ниже.
Низкоуглеродистая сталь подвергается газовой сварке без использования флюсов; в результате получаются швы с хорошими механическими параметрами. В качестве рабочего газа следует использовать смесь ацетилена и кислорода. Сразу после сварки нужно произвести проковку шва при температуре вишнево-красного накала.
Потом необходимо медленно охладить сваренную конструкцию. При сварке изделий из низкоуглеродистой стали можно использовать присадки с меньшим содержанием углерода, чем в основном металле. Это нужно для того, чтобы предупредить появление пористости. Указанные технологические особенности относятся к работе с листами или деталями толщиной до 5 мм.
При работе с металлом толщиной более 5 мм лучше всего использовать дуговую сварку с применением плавящихся электродов, которые могут функционировать в среде углекислого газа.
Необходимо отметить, что механические качества шва будут хуже в том случае, если вместо ацетилен-кислородной смеси придется применять в качестве горючего газа пропан, бутан или природный газ.
Среднеуглеродистая сталь характеризуется тем, что после сварки может появиться большая вероятность возникновения трещин, так как указанная сталь так же, как и хромистая и молибденовая, имеет тенденцию закаливаться на воздухе.
Поэтому после сварки обязательно нужно провести медленное охлаждение шва.
Получение качественного шва возможно только при применении в качестве горючего газа ацетиленокислорода; использование газов-заменителей абсолютно исключено.
Однако и применение ацетиленокислорода не позволит выполнить высококачественный шов при сварке сталей с содержанием углерода свыше 0,4 %. Для повышения качества шовного соединения следует применить дуговую сварку.
В отношении низко– и среднеуглеродистых сталей возможно применение газовой сварки, эффективность которой в смысле прочности шва будет тем выше, чем меньше содержание углерода в стали. Таким образом, очень хорошая свариваемость будет у низкоуглеродистой стали, особенности сварки которой изложены ниже.
Низкоуглеродистая сталь подвергается газовой сварке без использования флюсов; в результате получаются швы с хорошими механическими параметрами. В качестве рабочего газа следует использовать смесь ацетилена и кислорода. Сразу после сварки нужно произвести проковку шва при температуре вишнево-красного накала.
Потом необходимо медленно охладить сваренную конструкцию. При сварке изделий из низкоуглеродистой стали можно использовать присадки с меньшим содержанием углерода, чем в основном металле. Это нужно для того, чтобы предупредить появление пористости. Указанные технологические особенности относятся к работе с листами или деталями толщиной до 5 мм.
При работе с металлом толщиной более 5 мм лучше всего использовать дуговую сварку с применением плавящихся электродов, которые могут функционировать в среде углекислого газа.
Необходимо отметить, что механические качества шва будут хуже в том случае, если вместо ацетилен-кислородной смеси придется применять в качестве горючего газа пропан, бутан или природный газ.
Среднеуглеродистая сталь характеризуется тем, что после сварки может появиться большая вероятность возникновения трещин, так как указанная сталь так же, как и хромистая и молибденовая, имеет тенденцию закаливаться на воздухе.
Поэтому после сварки обязательно нужно провести медленное охлаждение шва.
Получение качественного шва возможно только при применении в качестве горючего газа ацетиленокислорода; использование газов-заменителей абсолютно исключено.
Однако и применение ацетиленокислорода не позволит выполнить высококачественный шов при сварке сталей с содержанием углерода свыше 0,4 %. Для повышения качества шовного соединения следует применить дуговую сварку.
Газовая резка
Кислородная резка – роцесс сгорания металлов и их сплавов в струе технически чистого кислорода. Для этого металл вдоль линии предполагаемого разреза предварительно нагревают до температуры его воспламенения в кислороде. Таким образом, весь процесс можно подразделить на стадию подогрева ацетиленовым пламенем (или пламенем других газов) и стадию резки металла струей кислорода, во время которой происходит сгорание металла, а образовавшиеся оксиды выдуваются из участка разреза. Такая резка носит еще одно название – разделительная (рис. 124). Она предназначена для раскроя листов металла, разделки кромок под сварку, вырезки заготовок различной формы и других работ, связанных с разрезанием металла на части.
Рис. 124. Разделительная резка.
Однако вышеописанную резку можно применять и для разделки канавок, удаления поверхностного слоя металла и устранения поверхностных дефектов. В этом случае резка будет называться поверхностной (рис. 125).
Рис. 125. Поверхностная резка.
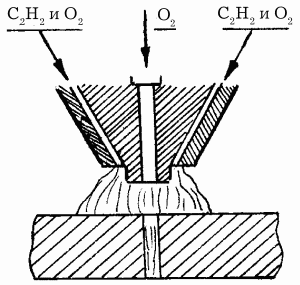
Однако вышеописанную резку можно применять и для разделки канавок, удаления поверхностного слоя металла и устранения поверхностных дефектов. В этом случае резка будет называться поверхностной (рис. 125).
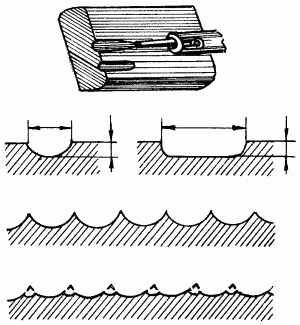
Классификация резаков и установок для ручной резки
Такой инструмент, как кислородный резак, удобно совмещает все стадии резки и предназначен для правильного смешивания горючих газов или паров жидкости с кислородом, образования подогревающего пламени и подачи струи чистого кислорода в зону резки.
Резаки классифицируют по принципу смешения газов (инжекторные и безынжекторные), по назначению (универсальные, вставные и специальные), по применению (для ручной и машинной резки) и по виду резки (для разделительной и поверхностной резки).
В настоящее время широко используются универсальные инжекторные ручные резаки для разделительной резки, схема строения которых представлена на рисунке 126.
Рис. 126. Схема строения ручного резака: 1, 2 – ниппели, 3, 4 – кислородные трубки, 5 – наружный мундштук, 6 – инжектор, 7 – смесительная камера, 8 – внутренний мундштук.
За образец взят резак средней мощности Р2А-01, применяемый для ручной резки низкоуглеродистой и низколегированной стали толщиной до 200 мм. Принцип действия горелки заключается в следующем. Ацетилен подается по шлангу к ниппелю 1, а кислород – к ниппелю 2. От ниппеля 2 кислород идет по двум направлениям. Одна часть кислорода, как и в обычных сварочных горелках, попадает в инжектор 6, а потом в смесительную камеру 7. В последней образуется горючая смесь кислорода с ацетиленом, который поступает через ниппель 1. Далее смесь идет по трубке, проходит через кольцевой зазор между наружным 5 и внутренним 8 мундштуками и образует подогревательное пламя. Остальная часть кислорода через трубки 3 и 4 продвигается к центральному отверстию внутреннего мундштука 8 и создает струю режущего кислорода.
В небольших мастерских сейчас используются специальные, универсальные и вставные резаки малой, средней и большой мощности.
Специальные резаки марок РПА-2-72, РПК-2-72, РЗР-2, РК-02 могут разрезать металл толщиной от 200 до 800 мм.
Резак РЗР-2 массой 5,5 кг в качестве горючего газа использует пропан-бутановую смесь, максимальный расход которой 7,5 м3/ч. Наибольший расход кислорода 114,5 м3/ч. Инструмент имеет сопло для смешивания кислорода и горючего газа. Давление горючего газа на входе в резак составляет не ниже 0,05 МПа (0,5 кгс/см2), а для контроля давления кислорода имеется манометр. Поступление горючего газа происходит от распределительных рамп или от цеховых магистралей. Если используется магистраль, то нужно иметь пропан-бутановую рампу на 3 баллона и кислородную рампу на 10 баллонов. РЗР-2 применяется для резки прибылей, поковок и отливок из низкоуглеродистых и низколегированных сталей; он способен резать металл толщиной до 800 мм.
Резак РК-02, или керосинорез, имеет обогреваемый подогревающим пламенем испаритель. В качестве горючего используется бензин или керосин (или их смесь). Это горючее поступает из шаровидного бачка БГ-02 объемом 8 л под давлением 0,3 МПа (3 кгс/см3). Бачок имеет предохранительный клапан и ручной насос. Российской промышленностью резак РК-02 производится в виде комплекта КЖГ-1 вместе с бачком БГ-02 для резки с использованием только жидкого горючего. Инструмент предназначен для разделительной ручной резки металлургического лома, листового металла, рельсов и скрапа толщиной до 200 мм.
Резаки РПК-2-72 и РПА-2-72 массой по 2,5 кг и длиной 13,5 см снабжены корпусом с внутренним и наружным мундштуками, рычагом пуска режущего кислорода и несколькими вентилями. С целью получения широкой и мягкой струи режущего кислорода диаметры выходных каналов в мундштуках и проходные сечения немного больше, чем в универсальных резаках.
Универсальные резаки Р2А-01 и Р3П-01, соответственно средней и большой мощности, имеют достаточно большие диаметры каналов мундштуков, смесительной камеры и инжектора. Резак Р2А-01 предполагает использование ацетилена, а резак Р3П-01 – бутана, пропана и природного газа.
Шарнирные установки АСШ («Огонек») и АСШ-В для кислородной резки имеют пантограф, позволяющий производить фигурную вырезку одновременно трех деталей небольших размеров при толщине материала от 5 до 100 мм при скорости резания до 1600 мм/мин. Масса этих установок около 350 кг, и они обеспечивают при использовании только одного резака первый класс точности.
Резаки классифицируют по принципу смешения газов (инжекторные и безынжекторные), по назначению (универсальные, вставные и специальные), по применению (для ручной и машинной резки) и по виду резки (для разделительной и поверхностной резки).
В настоящее время широко используются универсальные инжекторные ручные резаки для разделительной резки, схема строения которых представлена на рисунке 126.
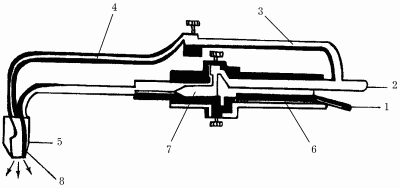
За образец взят резак средней мощности Р2А-01, применяемый для ручной резки низкоуглеродистой и низколегированной стали толщиной до 200 мм. Принцип действия горелки заключается в следующем. Ацетилен подается по шлангу к ниппелю 1, а кислород – к ниппелю 2. От ниппеля 2 кислород идет по двум направлениям. Одна часть кислорода, как и в обычных сварочных горелках, попадает в инжектор 6, а потом в смесительную камеру 7. В последней образуется горючая смесь кислорода с ацетиленом, который поступает через ниппель 1. Далее смесь идет по трубке, проходит через кольцевой зазор между наружным 5 и внутренним 8 мундштуками и образует подогревательное пламя. Остальная часть кислорода через трубки 3 и 4 продвигается к центральному отверстию внутреннего мундштука 8 и создает струю режущего кислорода.
В небольших мастерских сейчас используются специальные, универсальные и вставные резаки малой, средней и большой мощности.
Специальные резаки марок РПА-2-72, РПК-2-72, РЗР-2, РК-02 могут разрезать металл толщиной от 200 до 800 мм.
Резак РЗР-2 массой 5,5 кг в качестве горючего газа использует пропан-бутановую смесь, максимальный расход которой 7,5 м3/ч. Наибольший расход кислорода 114,5 м3/ч. Инструмент имеет сопло для смешивания кислорода и горючего газа. Давление горючего газа на входе в резак составляет не ниже 0,05 МПа (0,5 кгс/см2), а для контроля давления кислорода имеется манометр. Поступление горючего газа происходит от распределительных рамп или от цеховых магистралей. Если используется магистраль, то нужно иметь пропан-бутановую рампу на 3 баллона и кислородную рампу на 10 баллонов. РЗР-2 применяется для резки прибылей, поковок и отливок из низкоуглеродистых и низколегированных сталей; он способен резать металл толщиной до 800 мм.
Резак РК-02, или керосинорез, имеет обогреваемый подогревающим пламенем испаритель. В качестве горючего используется бензин или керосин (или их смесь). Это горючее поступает из шаровидного бачка БГ-02 объемом 8 л под давлением 0,3 МПа (3 кгс/см3). Бачок имеет предохранительный клапан и ручной насос. Российской промышленностью резак РК-02 производится в виде комплекта КЖГ-1 вместе с бачком БГ-02 для резки с использованием только жидкого горючего. Инструмент предназначен для разделительной ручной резки металлургического лома, листового металла, рельсов и скрапа толщиной до 200 мм.
Резаки РПК-2-72 и РПА-2-72 массой по 2,5 кг и длиной 13,5 см снабжены корпусом с внутренним и наружным мундштуками, рычагом пуска режущего кислорода и несколькими вентилями. С целью получения широкой и мягкой струи режущего кислорода диаметры выходных каналов в мундштуках и проходные сечения немного больше, чем в универсальных резаках.
Универсальные резаки Р2А-01 и Р3П-01, соответственно средней и большой мощности, имеют достаточно большие диаметры каналов мундштуков, смесительной камеры и инжектора. Резак Р2А-01 предполагает использование ацетилена, а резак Р3П-01 – бутана, пропана и природного газа.
Установки для ручной резки
Установка УФР-5 предназначена для порошково-кислородной резки железобетона толщиной до 300 мм и работает на пропане или бутане в смеси с кислородом. В состав аппарата входит флюсоноситель на тележке, резак, крепление для баллонов и копьедержатель, предназначенный для фиксирования трубы, по которой поступает кислород. Флюс представляет собой смесь двух порошков: железного (75–85 %) и алюминиевого (15–25 %); причем воздух используется в качестве флюсонесущего газа. Глубина отверстия, прожигаемого в железобетоне УФР-5, может составить 1,5 м.Шарнирные установки АСШ («Огонек») и АСШ-В для кислородной резки имеют пантограф, позволяющий производить фигурную вырезку одновременно трех деталей небольших размеров при толщине материала от 5 до 100 мм при скорости резания до 1600 мм/мин. Масса этих установок около 350 кг, и они обеспечивают при использовании только одного резака первый класс точности.