Страница:
Однопроходная сварка с v-образной разделкой кромок выполняется с поперечными колебаниями электрода на всю ширину, с выходом дуги со скоса кромок на необработанную поверхность (рис. 108).
Рис. 108. Однопроходное сечение стыкового шва.
Если число слоев равно числу проходов дуги, то шов называют многослойным. Если слой выполняется за несколько проходов, шов называют многопроходным.
При сварке шва с v-образной разделкой за несколько проходов можно обеспечить гораздо лучший провар первого слоя в корне разделки (рис. 109).
Рис. 109. Многослойное сечение стыкового шва.
Сварку ведут без поперечных колебаний с помощью электродов диаметром 3–4 мм. В зависимости от толщины металла последующие слои выполняют электродами большего диаметра, с поперечными колебаниями. Необходимо тщательно очищать от шлака и брызг металла все предыдущие слои: это обеспечит хороший провар и высокое качество шва.
Разделку кромок можно заполнять швами с шириной на всю разделку или отдельными валиками. В многопроходных швах последний валик можно выполнить на всю ширину разделки (рис. 110).
Рис. 110. Многопроходное сечение стыкового шва.
Вышеперечисленные виды швов нашли свое применение в различных соединениях: многослойные швы в стыковых, многопроходные – в угловых и тавровых соединениях. Протяженность швов варьируется от 300 до 1000 мм. В зависимости от этого все швы подразделяются на три группы: короткие – до 300 мм, средние – 300–1000 мм, длинные – свыше 1000 мм.
На выбор того или иного способа сварки влияют протяженность шва, свойства свариваемого материала и качество сварных соединений.
Выполнение коротких швов (до 300 мм) относят к наиболее простому способу. От начала до конца шва осуществляется движение напроход (рис. 111, а). При шве средней длины сварка ведется от середины к концу (рис. 111, б) или обратноступенчатым способом.
Рис. 111. Различные схемы сварки: а – сварка напроход; б – сварка от середины к краям; в – обратноступенчатый способ; г – «каскад»; д – «горка».
Швы, имеющие большую протяженность, можно варить как обратноступенчатым способом, так и вразброс. При обратноступенчатом способе удобно разбить шов на небольшие участки длиной 150–200 мм. Направление сварки каждого участка не должно совпадать с общим направлением сварки (рис. 111, в).
Швы конструкций, несущих большую нагрузку и имеющих значительную толщину свариваемых поверхностей, обычно сваривают способом «каскад» (рис. 111, г) или «горка» (рис. 111, д).
Чтобы в зоне сварки не возникали объемные напряжения, ведущие к образованию трещин, необходимо во время работы поддерживать в ней высокую температуру. Величина сварочного тока влияет на толщину шва свариваемых деталей из низкоуглеродистой стали. Она может колебаться от 3 до 5 мм.
При силе тока, равной 100 А, происходит расплавление металла на глубину 1 мм с термической обработкой нижнего слоя на глубину 1–2 мм. Если сила тока достигает 200 А, то толщина слоя возрастает до 4 мм. При этом происходит термическая обработка нижнего слоя на глубину 2–3 мм.
Если сварка ведется на весу (рис. 112), то необходимо обеспечить максимальный провар корня шва и сформировать качественный обратный валик. В этом случае хорошо зарекомендовал себя способ сварки на съемной медной (рис. 113) или остающейся стальной подкладке (рис. 114). При этом в медной подкладке делается формирующая канавка. Чтобы расплавленный металл не вытекал из сварочной ванны, необходимо обеспечить плотное обжатие подкладок к свариваемым кромкам. Остающиеся подкладки не всегда технологичны, так как увеличивают расход металла. Если допустима выпуклость обратной стороны, то допускается подварка корня шва с последующей укладкой основного шва (рис. 115).
Рис. 112. Сварка на весу.
Рис. 113. Сварка на медной съемной подкладке.
Рис. 114. Сварка на остающейся стальной подкладке.
Рис. 115. Сварка с предварительным подварочным швом.
В зоне кратера скапливается наибольшее количество вредных примесей, образовавшихся в процессе кристаллизации металла. В этой зоне трещины образуются наиболее часто. Если сварка закончена, то при обрыве дуги не рекомендуется резко отводить электрод от изделия. Перемещения электрода следует прекратить и до обрыва медленно удлинять дугу. Такой прием способствует заполнению кратера электродным металлом. В некоторых случаях, например при сварке низкоуглеродистой стали, кратер выводят на основной металл, в сторону от шва. Если понадобилась смена электродов или произошел случайный обрыв дуги, то ее можно возбудить на еще нерасплавленном основном металле перед кратером. Металл проплавляют на кратере. Если ведется сварка стали, которая образует закалочные структуры, то вывод кратера в сторону недопустим из-за возможности образования трещин.
Сварочный ток выбирают, ориентируясь на марку и диаметр электрода, учитывая при этом положение шва в пространстве, вид соединения, а также толщину свариваемого изделия. При этом сила тока должна быть максимально возможной. Чем больше ток, тем выше производительность труда и больше наплавляется металла. Увеличение силы тока влияет также на глубину провара.
Полярность тока и его вид (постоянный или переменный) оказывают влияние на размеры шва и его форму. Если сварка ведется при постоянном токе, имеющем обратную полярность, то глубина провара на 50 % больше, чем при постоянном токе прямой полярности. Это объясняется тем, что на аноде и катоде выделяется разное количество теплоты. Глубина провара при сварке переменным током на 15 % меньше той, которая получается при сварке постоянным током прямой полярности.
На диаметр электрода влияют толщина свариваемого металла, вид соединения и форма подготовленных кромок под сварку. Если ведется сварка стыков металла, толщина которых достигает 4 мм, то используются электроды того же диаметра, что и толщина кромок.
Если свариваемый металл имеет большую толщину, то задействуются электроды диаметром 4–8 мм. При этом должны соблюдаться условия провара основного металла. Если стыковые швы имеют несколько слоев, то желательно первый шов выполнить электродом диаметром 3–4 мм, с обязательной сваркой последующих слоев электродами большего диаметра.
Техника выполнения горизонтальных, вертикальных и потолочных швов
Особенности сварки различных материалов
Диаметр электродов, мм22,53
Сварочный ток, А40–60 50–7580–100
Диаметр электродов, мм 456
Сварочный ток, А 130–150170–200200–280
– при сварке швов применять электроды малого диаметра (1,6–2 мм);
– сила тока должна быть минимальной – 50–70 А;
– для обеспечения устойчивого горения дуги необходимо подключать осциллятор;
– для исключения образования прожогов применять отбортовки кромок свариваемых листов.
Сварку листов, имеющих разную толщину, рекомендуется делать посредством плавного перехода от более толстого металла к тонкому, применяя осциллятор.
Для малоответственных изделий применяется ручная сварка угольным электродом. Угольные электроды используются при толщине меди до 15 мм. Графитовые электроды применяются при большой толщине свариваемых поверхностей. Сварка ведется электродами, заточенными на конус на 1/3 его длины, постоянным током прямой полярности при плотности тока на электроде, равной 200–400 А/см2. Рекомендуется вести сварку длинной дугой и не погружать присадочный материал в ванну, а держать под углом 30° к изделию на расстоянии 6 мм от свариваемого изделия. Электрод лучше держать под углом 75–90° к свариваемому изделию. Выделяемый в процессе сварки углекислый газ является недостаточной защитой металла от окисления.
В качестве защиты хорошо зарекомендовал себя присадочный материал с раскислителем – фосфором, или флюс, состоящий из 94 % прокаленной буры и 4–6 % металлического магния. Поверхность прутка смачивают жидким стеклом, затем наносят флюс в виде пудры и просушивают.
Если толщина заготовок превышает 5 мм, то угол среза на кромках должен составлять 70–90°. При сварке используют графитовые или асбестовые подкладки. Зазор между кромками должен составлять 0,5 мм; электрод следует держать под углом 10–20° к вертикали. Если толщина соединения составляет около 5 мм, то его проковывают без подогрева; при большой толщине используют подогрев до 800 °C и последующее быстрое охлаждение. Во избежание снижения механических свойств сварка стыковых швов ведется в один слой и с одной стороны.
Если предпочтительна ручная сварка покрытыми электродами, то ее ведут на постоянном токе обратной полярности короткой дугой без поперечных колебаний. Для лучшего формирования шва рекомендуются возвратно-поступательные движения электродов. Если удлинить дугу, то это вызовет увеличение разбрызгивания и повлияет на формирование шва. Механические свойства соединений от этого снижаются.
При толщине медных заготовок до 4 мм сварка ведется без раздела кромок и подогрева. При толщине листа свыше 5 мм обязательны предварительный подогрев до температуры 250–300 °C и односторонняя разделка кромок с углом 60–70° с последующим притуплением их до 1,5–3 мм. X-образная разделка рекомендуется при больших толщинах. При сварке меди часто используют электроды «Комсомолец-100», получившие наибольшее распространение, в которых в качестве стержня используется медная проволока М1 и М2. Медные электроды диаметром менее 3 мм применяют редко, так как они имеют низкую механическую прочность.
Высокопроизводительные электроды марок АНЦ-1 и АНЦ-2 обеспечивают выполнение сварки без подогрева заготовок, имеющих толщину до 15 мм. Если использовать небольшой подогрев (250–400 °C), то эти электроды можно использовать для сварки медных изделий большой толщины.
Различные виды бронзы отличаются друг от друга по свариваемости, поэтому технология сварки бронзы довольно различна. Химический состав свариваемого металла должен быть сходным с составом присадочного материала. Сварку выполняют постоянным током обратной полярности, двигаясь короткими отрезками.
При сварке латуни применяют электроды марки ЗТ. Температура плавления латуни – 800–1000 °C.
Сварка ведется постоянным током обратной полярности, короткой дугой. Шов после сварки подвергается проковке и отжигу при температуре 600–660 °C: это необходимо для выравнивания химического состава и придания шву мелкозернистой структуры.
Благодаря своей высокой коррозионной стойкости, жаропрочности и жаростойкости никель и его сплавы являются важнейшими конструкционными материалами, которые используются в разных отраслях промышленности.
Никель и его сплавы можно сваривать дуговой, газовой и другими видами сварок. Если толщина заготовок не превышает 5 мм, то сварка ведется без разделки кромок. При толщине от 6 до 12 м применяется v-образная разделка кромок, а при толщине более 12 мм – х-образная, с углом раскрытия 60–70° и притуплением 2–4 мм в зависимости от толщины свариваемого металла.
Зазоры под сварку не должны превышать 1–1,5 мм. Кромки перед сваркой зачищают до металлического блеска и обезжиривают ацетоном или авиационным бензином.
Так как никель и его сплавы имеют высокое электрическое сопротивление, при сварке вылет проволоки следует уменьшать в 1,5–2 раза по сравнению с вылетом электрода при сварке сталей. Основные трудности при сварке никеля и его сплавов – высокая склонность к образованию пор и кристаллизационных трещин. Это связано с переходом металла из твердого в жидкое состояние, в результате которого образуются нерастворимые продукты, способствующие образованию пор в металле шва. Техника сварки должна предусматривать надежную защиту зоны сварки от атмосферного воздуха и хорошее раскисление варочной ванны.
Одной из эффективных мер является сварка короткой дугой (до 1,5 мм), при которой резко уменьшается подсос газов из атмосферы. Чтобы предупредить образование пор по линии сплавления, необходимо перед сваркой предварительно подогревать металл до температуры 250–300 °C с последующим охлаждением на воздухе.
При толщине листов свыше 1,5 мм применяют электроды с основным покрытием на постоянном токе обратной полярности. Для того чтобы снизить напряжение в сварном соединении и предупредить перегрев электрода, используют пониженный ток (по сравнению с током, применяемым для сварки стали).
Сварка ведется в нижнем положении, причем поперечные колебания электрода не должны превышать трех диаметров электрода. При случайных обрывах дуги ее возбуждают на зачищенном от шлака шве, отступая назад от кратера на 5–6 мм. Сварка выполняется за один проход. При большой толщине свариваемых кромок ведут многопроходную сварку после остывания соединения и тщательной очистки предыдущего слоя от брызг и шлака.
Если предпочтительна полуавтоматическая сварка, то ее ведут плавящимся электродом в среде защитных газов на постоянном токе обратной полярности. В качестве защитной среды служит аргон и гелий. Повышает качество швов введение в аргон до 20 % водорода. Сварку ведут стандартными полуавтоматами с горелкой, которую наклоняют углом вперед на 10–15° от вертикали. Чтобы в шве не образовывались поры, рекомендуется применять сварочную проволоку, легированную до 3 % титаном или добавками редкоземельных элементов.
Предупреждают прожоги и способствуют формированию обратной стороны шва флюсовые подушки или медные формующие подкладки. Сварка начинается и заканчивается на технологических планках с разделкой кромок и толщиной, равной толщине свариваемого металла.
Незначительная теплопроводность и низкая температура плавления свинца требуют применения небольшой погонной энергии сварки. Сварка свинца может проводиться в любом положении, но при наклоне изделия более 10–15° происходит вытекание металла из ванны, что влияет на формирование сварных швов. Приемлемым является нижнее положение, на которое и нужно ориентироваться при сварке свинцовых изделий.
Так как свинец имеет большую плотность и существует вероятность провалов ванны, рекомендуется применять передвижные формирующие пластины-прокладки. Кромки изделий перед сваркой протирают бензином или четыреххлористым углеродом и зачищают шабером до металлического блеска на ширину 20–25 мм.
Заготовки толщиной до 2 мм сваривают с отбортовкой кромок высотой, равной толщине свариваемого металла; при толщине свинца до 8 мм – без разделки кромок; при большей толщине делается скос кромок с общим углом раскрытия 60–70° без зазора в стыке и притупление 3–4 мм. Иногда выполняют двустороннюю подготовку кромок. Сварка свинца проводится угольным электродом, в среде инертных газов – плавящимся и неплавящимся электродами, а также ацетилено-кислородной сваркой. Сварка угольными электродами выполняется на постоянном токе прямой полярности.
Во время сварки электроды располагаются перпендикулярно или с наклоном на 10–15° от вертикали в сторону движения сварки.
Независимо от способа сварки изделия должны проходить специальную подготовку. Поверхности обезжиривают и удаляют с них пленку оксида алюминия. Точно так же подготавливают присадочную проволоку и электродные стержни перед нанесением на них покрытия.
Обезжиривание проводят с помощью растворителей, например авиационного бензина или технического ацетона. Следующий этап – механическая зачистка или химическое травление, которое удаляет оксидную пленку. Обезжиривание и травление проводят не более чем за 2–4 ч до сварки.
Для неответственных изделий применяется ручная сварка угольным электродом на постоянном токе прямой полярности. Если металл имеет толщину до 2 мм, то сварку ведут без присадки и без разделки кромок; при толщине металла свыше 2 мм сварку выполняют с зазором, равным 0,5–0,7 толщины свариваемых листов или с разделкой кромок. Ручная сварка покрытыми электродами выполняют при изготовлении конструкций из технического алюминия, сплавов АМц и АМг и силумина. При умеренных токах требуемое проплавление обеспечивается использованием постоянного тока прямой полярности с предварительным подогревом (для средних толщин – 250–300 °C, для больших толщин – до 400 °C). Скорость сварки алюминия должна быть выше, чем скорость сварки стали. Она ведется непрерывно в пределах одного электрода в связи с тем, что пленка шлака на кратере в конце электрода препятствует повторному зажиганию дуги.
Сварочный ток принимается из расчета не более 60 А на 1 мм диаметра электрода – это обеспечит устойчивость процесса и минимальные потери при разбрызгивании. Электроды предварительно просушивают при температуре 150–200 °C в течение 2 ч.
При ручной аргонодуговой сварке применяют неплавящиеся вольфрамовые электроды в осушенном от влаги аргоне высшего сорта на переменном токе. Если толщина свариваемого металла равна 5–6 мм, то применяются электроды диаметром 1,5–5 мм.
Техника сварки имеет здесь свои особенности. Между электродом и присадочной проволокой должен выдерживаться угол примерно в 85–90°. При подаче присадки используют возвратно-поступательные движения. Эффективная защита достигается оптимальным расходом газа. Металл толщиной до 10 мм сваривают справа налево: этот прием позволяет снизить перегрев свариваемого металла.
Сварные трубы, которые применяют при прокладке технологических, магистральных и производственных трубопроводов, имеют наружный диаметр 4–1620 мм при толщине стенок 0,3–25 мм. Сварные трубы выпускают с прямым продольным или спиральным сварным швом.
Цельнокатанные трубы изготавливают из низкоуглеродистой мартеновской стали с пределом прочности 350–550 МПа. Промышленность выпускает трубы наружным диаметром 114–426 мм и толщиной стенки 4,5–20 мм.
Магистральные трубопроводы нефтяных заводов, а также трубопроводы для транспортирования жидких и агрессивных веществ монтируются из цельнокатанных труб, изготовленных из легированных жаропрочных и нержавеющих сталей.
Алюминиевые трубы предназначены для магистральных трубопроводов и трубопроводов нефтезаводов, которые находятся в средах, вызывающих коррозию. Сортаментом для этих труб предусмотрены наружные диаметры 120–280 мм и толщина стенок 10–30 мм. Для сборки магистральных и заводских производственных трубопроводов применяются специальные фасонные части. Их применяют для углов поворотов, участков ответвления и пр. Такие части представляют собой крутоизогнутые угольники, двойники, тройники, переходы, изготавливаемые из стали 20 путем протяжки или штамповки. Применяют и сварные фасонные части. Крутоизогнутые угольники выпускают с наружным диаметром 48–529 мм при толщине стенок 4,5–12 мм и среднем радиусе 80–500 мм. Сварные отводы чаще всего делают из нескольких частей (рис. 119).
Рис. 119. Типы сварных отводов.
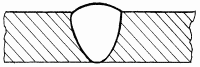
Если число слоев равно числу проходов дуги, то шов называют многослойным. Если слой выполняется за несколько проходов, шов называют многопроходным.
При сварке шва с v-образной разделкой за несколько проходов можно обеспечить гораздо лучший провар первого слоя в корне разделки (рис. 109).
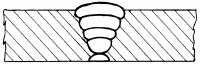
Сварку ведут без поперечных колебаний с помощью электродов диаметром 3–4 мм. В зависимости от толщины металла последующие слои выполняют электродами большего диаметра, с поперечными колебаниями. Необходимо тщательно очищать от шлака и брызг металла все предыдущие слои: это обеспечит хороший провар и высокое качество шва.
Разделку кромок можно заполнять швами с шириной на всю разделку или отдельными валиками. В многопроходных швах последний валик можно выполнить на всю ширину разделки (рис. 110).
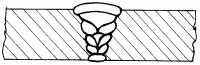
Вышеперечисленные виды швов нашли свое применение в различных соединениях: многослойные швы в стыковых, многопроходные – в угловых и тавровых соединениях. Протяженность швов варьируется от 300 до 1000 мм. В зависимости от этого все швы подразделяются на три группы: короткие – до 300 мм, средние – 300–1000 мм, длинные – свыше 1000 мм.
На выбор того или иного способа сварки влияют протяженность шва, свойства свариваемого материала и качество сварных соединений.
Выполнение коротких швов (до 300 мм) относят к наиболее простому способу. От начала до конца шва осуществляется движение напроход (рис. 111, а). При шве средней длины сварка ведется от середины к концу (рис. 111, б) или обратноступенчатым способом.
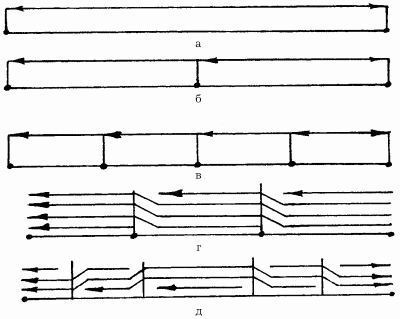
Швы, имеющие большую протяженность, можно варить как обратноступенчатым способом, так и вразброс. При обратноступенчатом способе удобно разбить шов на небольшие участки длиной 150–200 мм. Направление сварки каждого участка не должно совпадать с общим направлением сварки (рис. 111, в).
Швы конструкций, несущих большую нагрузку и имеющих значительную толщину свариваемых поверхностей, обычно сваривают способом «каскад» (рис. 111, г) или «горка» (рис. 111, д).
Чтобы в зоне сварки не возникали объемные напряжения, ведущие к образованию трещин, необходимо во время работы поддерживать в ней высокую температуру. Величина сварочного тока влияет на толщину шва свариваемых деталей из низкоуглеродистой стали. Она может колебаться от 3 до 5 мм.
При силе тока, равной 100 А, происходит расплавление металла на глубину 1 мм с термической обработкой нижнего слоя на глубину 1–2 мм. Если сила тока достигает 200 А, то толщина слоя возрастает до 4 мм. При этом происходит термическая обработка нижнего слоя на глубину 2–3 мм.
Если сварка ведется на весу (рис. 112), то необходимо обеспечить максимальный провар корня шва и сформировать качественный обратный валик. В этом случае хорошо зарекомендовал себя способ сварки на съемной медной (рис. 113) или остающейся стальной подкладке (рис. 114). При этом в медной подкладке делается формирующая канавка. Чтобы расплавленный металл не вытекал из сварочной ванны, необходимо обеспечить плотное обжатие подкладок к свариваемым кромкам. Остающиеся подкладки не всегда технологичны, так как увеличивают расход металла. Если допустима выпуклость обратной стороны, то допускается подварка корня шва с последующей укладкой основного шва (рис. 115).
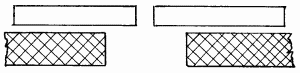



Окончание сварки
Правильная заварка кратера при обрыве дуги – окончание сварки – играет важную роль в сварочном процессе.В зоне кратера скапливается наибольшее количество вредных примесей, образовавшихся в процессе кристаллизации металла. В этой зоне трещины образуются наиболее часто. Если сварка закончена, то при обрыве дуги не рекомендуется резко отводить электрод от изделия. Перемещения электрода следует прекратить и до обрыва медленно удлинять дугу. Такой прием способствует заполнению кратера электродным металлом. В некоторых случаях, например при сварке низкоуглеродистой стали, кратер выводят на основной металл, в сторону от шва. Если понадобилась смена электродов или произошел случайный обрыв дуги, то ее можно возбудить на еще нерасплавленном основном металле перед кратером. Металл проплавляют на кратере. Если ведется сварка стали, которая образует закалочные структуры, то вывод кратера в сторону недопустим из-за возможности образования трещин.
Определение режима сварки
Основными параметрами нормального режима сварки являются величина и полярность тока, диаметр электрода, скорость сварки и напряжение на дуге. Существуют и дополнительные параметры – толщина покрытия электрода и его состав, положение электрода и положение изделия.Сварочный ток выбирают, ориентируясь на марку и диаметр электрода, учитывая при этом положение шва в пространстве, вид соединения, а также толщину свариваемого изделия. При этом сила тока должна быть максимально возможной. Чем больше ток, тем выше производительность труда и больше наплавляется металла. Увеличение силы тока влияет также на глубину провара.
Полярность тока и его вид (постоянный или переменный) оказывают влияние на размеры шва и его форму. Если сварка ведется при постоянном токе, имеющем обратную полярность, то глубина провара на 50 % больше, чем при постоянном токе прямой полярности. Это объясняется тем, что на аноде и катоде выделяется разное количество теплоты. Глубина провара при сварке переменным током на 15 % меньше той, которая получается при сварке постоянным током прямой полярности.
На диаметр электрода влияют толщина свариваемого металла, вид соединения и форма подготовленных кромок под сварку. Если ведется сварка стыков металла, толщина которых достигает 4 мм, то используются электроды того же диаметра, что и толщина кромок.
Если свариваемый металл имеет большую толщину, то задействуются электроды диаметром 4–8 мм. При этом должны соблюдаться условия провара основного металла. Если стыковые швы имеют несколько слоев, то желательно первый шов выполнить электродом диаметром 3–4 мм, с обязательной сваркой последующих слоев электродами большего диаметра.
Техника выполнения горизонтальных, вертикальных и потолочных швов
Если сварка швов ведется в положениях, отличающихся от нижнего, то возникает вероятность вытекания расплавленного металла из сварочной ванны. В таких положениях металл может капать мимо нее. Для предотвращения этого сварку следует вести наиболее короткой дугой, ведя поперечные колебания электродов.
Слой расплавленного металла удерживается от вытекания из сварочной ванны силой поверхностного натяжения. Чем тоньше пленка расплавленного металла, тем больше вероятность ее удержания этой силой. Достигается это за счет периодического отведения в сторону от ванны конца электрода. Такое отведение создает возможность быстрой кристаллизации металла. Удерживать металл от вытекания помогают и такие приемы, как понижение на 10–20 % силы тока и применение электродов уменьшенного диаметра: для вертикальных и горизонтальных швов – не более 5 мм, для потолочных – 10 мм.
Рис. 116. Вертикальный шов.
При сварке на подъем нижележащий металл шва, который почти закристаллизовался, удерживает расплавленный металл, находящийся в сварочной ванне. Сварка на подъем дает возможность более тщательно проваривать корень шва и кромки, так как расплавленный металл стекает с электрода прямо в сварочную ванну. Недостатком данного способа является грубый внешний вид шва: его поверхность как будто покрыта чешуей.
При сварке на спуск трудно получить качественный провар места соединения деталей, так как шлак и расплавленный металл подтекают под дугу. При малом значении силы поверхностного натяжения происходит вытекание металла из сварочной ванны.
Рис. 117. Потолочный шов.
Металл сварочной ванны начинает кристаллизоваться, тем самым уменьшая объем сварочной ванны. Параллельно этому в сварочную ванну вносится расплавленный электродный металл. Подрезы образуются при удлинении дуги. Сварка таких швов создает неблагоприятные условия для выделения шлаков и газов из сварочной ванны.
Рис. 118. Горизонтальный шов.
Объясняется это тем, что расплавленный металл стекает из сварочной ванны на нижнюю кромку, что влечет за собой образование подреза по верхней кромке. По этой причине сварку металла повышенной толщины производят со скосом только одной верхней кромки. Нижняя помогает удерживать расплавленный металл в сварочной ванне. В нахлесточных соединениях сварка угловых швов не представляет особых трудностей и выполняется по тому же способу, что и сварка в нижнем положении.
Слой расплавленного металла удерживается от вытекания из сварочной ванны силой поверхностного натяжения. Чем тоньше пленка расплавленного металла, тем больше вероятность ее удержания этой силой. Достигается это за счет периодического отведения в сторону от ванны конца электрода. Такое отведение создает возможность быстрой кристаллизации металла. Удерживать металл от вытекания помогают и такие приемы, как понижение на 10–20 % силы тока и применение электродов уменьшенного диаметра: для вертикальных и горизонтальных швов – не более 5 мм, для потолочных – 10 мм.
Выполнение вертикальных швов
Сварку таких швов можно осуществлять как на подъем, так и на спуск (рис. 116).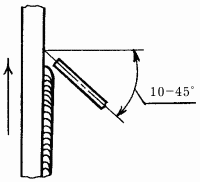
При сварке на подъем нижележащий металл шва, который почти закристаллизовался, удерживает расплавленный металл, находящийся в сварочной ванне. Сварка на подъем дает возможность более тщательно проваривать корень шва и кромки, так как расплавленный металл стекает с электрода прямо в сварочную ванну. Недостатком данного способа является грубый внешний вид шва: его поверхность как будто покрыта чешуей.
При сварке на спуск трудно получить качественный провар места соединения деталей, так как шлак и расплавленный металл подтекают под дугу. При малом значении силы поверхностного натяжения происходит вытекание металла из сварочной ванны.
Выполнение потолочного шва
Выполнение потолочного шва (рис. 117) представляет определенные трудности. По возможности следует заменять этот трудоемкий вид каким-либо другим. При таком способе сварку производят, периодически замыкая конец электрода на сварочную ванну.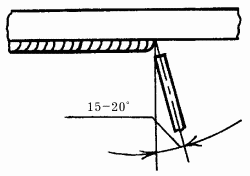
Металл сварочной ванны начинает кристаллизоваться, тем самым уменьшая объем сварочной ванны. Параллельно этому в сварочную ванну вносится расплавленный электродный металл. Подрезы образуются при удлинении дуги. Сварка таких швов создает неблагоприятные условия для выделения шлаков и газов из сварочной ванны.
Выполнение горизонтального шва
Горизонтальные стыковые швы (рис. 118), в отличие от вертикальных, более сложны в выполнении.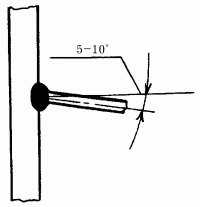
Объясняется это тем, что расплавленный металл стекает из сварочной ванны на нижнюю кромку, что влечет за собой образование подреза по верхней кромке. По этой причине сварку металла повышенной толщины производят со скосом только одной верхней кромки. Нижняя помогает удерживать расплавленный металл в сварочной ванне. В нахлесточных соединениях сварка угловых швов не представляет особых трудностей и выполняется по тому же способу, что и сварка в нижнем положении.
Особенности сварки различных материалов
Сварка низкоуглеродистых сталей
Хорошо свариваются низкоуглеродистые стали, содержащие до 0,25 % углерода. Такие соединения легко обрабатываются режущими инструментами. Чтобы исключить перегрев и образование закалочных структур, используют многослойную сварку с большим интервалом времени между наложением слоев. Дуговую сварку металла толщиной 2 мм обычно ведут на постоянном токе обратной полярности. Изделия толщиной более 15 мм подвергают после сварки термообработке. Сварка толстого металла «каскадом» или «горкой» с замедлением скорости охлаждения металла и околошовной зоны предупреждает образование закалочных структур. Дефектные участки обычно подваривают швами нормального сечения длиной не менее 100 мм или предварительно подогревают до температуры 150–200 °C.Сварка углеродистых сталей
Сварка таких марок сталей часто чревата образованием трещин как в основном, так и в наплавленном металле. Чтобы получить качественное соединение, необходимо соблюдать следующие соотношения между диаметром электрода и значением сварочного тока:Диаметр электродов, мм22,53
Сварочный ток, А40–60 50–7580–100
Диаметр электродов, мм 456
Сварочный ток, А 130–150170–200200–280
Сварка тонколистовой стали
При толщине свариваемого металла менее 2 мм применение ручной дуговой сварки часто вызывает образование прожогов. Чтобы избежать этого, следует выполнить следующие рекомендации:– при сварке швов применять электроды малого диаметра (1,6–2 мм);
– сила тока должна быть минимальной – 50–70 А;
– для обеспечения устойчивого горения дуги необходимо подключать осциллятор;
– для исключения образования прожогов применять отбортовки кромок свариваемых листов.
Сварку листов, имеющих разную толщину, рекомендуется делать посредством плавного перехода от более толстого металла к тонкому, применяя осциллятор.
Сварка цветных металлов
Сварка меди осложняется наличием примесей, имеющихся в ее составе, большой теплопроводностью и способностью сильно окисляться в расплавленном состоянии. Кроме того, медь сильно поглощает водород в расплавленном состоянии. Внутри свариваемого участка образуются пузырьки воды, которые являются причиной возникновения большого количества микротрещин. Такое явление называется водородной болезнью меди. Предупреждает образование болезни снижение количества водорода в зоне сварки путем прокалки электродов и флюсов и применения защитных газов.Для малоответственных изделий применяется ручная сварка угольным электродом. Угольные электроды используются при толщине меди до 15 мм. Графитовые электроды применяются при большой толщине свариваемых поверхностей. Сварка ведется электродами, заточенными на конус на 1/3 его длины, постоянным током прямой полярности при плотности тока на электроде, равной 200–400 А/см2. Рекомендуется вести сварку длинной дугой и не погружать присадочный материал в ванну, а держать под углом 30° к изделию на расстоянии 6 мм от свариваемого изделия. Электрод лучше держать под углом 75–90° к свариваемому изделию. Выделяемый в процессе сварки углекислый газ является недостаточной защитой металла от окисления.
В качестве защиты хорошо зарекомендовал себя присадочный материал с раскислителем – фосфором, или флюс, состоящий из 94 % прокаленной буры и 4–6 % металлического магния. Поверхность прутка смачивают жидким стеклом, затем наносят флюс в виде пудры и просушивают.
Если толщина заготовок превышает 5 мм, то угол среза на кромках должен составлять 70–90°. При сварке используют графитовые или асбестовые подкладки. Зазор между кромками должен составлять 0,5 мм; электрод следует держать под углом 10–20° к вертикали. Если толщина соединения составляет около 5 мм, то его проковывают без подогрева; при большой толщине используют подогрев до 800 °C и последующее быстрое охлаждение. Во избежание снижения механических свойств сварка стыковых швов ведется в один слой и с одной стороны.
Если предпочтительна ручная сварка покрытыми электродами, то ее ведут на постоянном токе обратной полярности короткой дугой без поперечных колебаний. Для лучшего формирования шва рекомендуются возвратно-поступательные движения электродов. Если удлинить дугу, то это вызовет увеличение разбрызгивания и повлияет на формирование шва. Механические свойства соединений от этого снижаются.
При толщине медных заготовок до 4 мм сварка ведется без раздела кромок и подогрева. При толщине листа свыше 5 мм обязательны предварительный подогрев до температуры 250–300 °C и односторонняя разделка кромок с углом 60–70° с последующим притуплением их до 1,5–3 мм. X-образная разделка рекомендуется при больших толщинах. При сварке меди часто используют электроды «Комсомолец-100», получившие наибольшее распространение, в которых в качестве стержня используется медная проволока М1 и М2. Медные электроды диаметром менее 3 мм применяют редко, так как они имеют низкую механическую прочность.
Высокопроизводительные электроды марок АНЦ-1 и АНЦ-2 обеспечивают выполнение сварки без подогрева заготовок, имеющих толщину до 15 мм. Если использовать небольшой подогрев (250–400 °C), то эти электроды можно использовать для сварки медных изделий большой толщины.
Различные виды бронзы отличаются друг от друга по свариваемости, поэтому технология сварки бронзы довольно различна. Химический состав свариваемого металла должен быть сходным с составом присадочного материала. Сварку выполняют постоянным током обратной полярности, двигаясь короткими отрезками.
При сварке латуни применяют электроды марки ЗТ. Температура плавления латуни – 800–1000 °C.
Сварка ведется постоянным током обратной полярности, короткой дугой. Шов после сварки подвергается проковке и отжигу при температуре 600–660 °C: это необходимо для выравнивания химического состава и придания шву мелкозернистой структуры.
Благодаря своей высокой коррозионной стойкости, жаропрочности и жаростойкости никель и его сплавы являются важнейшими конструкционными материалами, которые используются в разных отраслях промышленности.
Никель и его сплавы можно сваривать дуговой, газовой и другими видами сварок. Если толщина заготовок не превышает 5 мм, то сварка ведется без разделки кромок. При толщине от 6 до 12 м применяется v-образная разделка кромок, а при толщине более 12 мм – х-образная, с углом раскрытия 60–70° и притуплением 2–4 мм в зависимости от толщины свариваемого металла.
Зазоры под сварку не должны превышать 1–1,5 мм. Кромки перед сваркой зачищают до металлического блеска и обезжиривают ацетоном или авиационным бензином.
Так как никель и его сплавы имеют высокое электрическое сопротивление, при сварке вылет проволоки следует уменьшать в 1,5–2 раза по сравнению с вылетом электрода при сварке сталей. Основные трудности при сварке никеля и его сплавов – высокая склонность к образованию пор и кристаллизационных трещин. Это связано с переходом металла из твердого в жидкое состояние, в результате которого образуются нерастворимые продукты, способствующие образованию пор в металле шва. Техника сварки должна предусматривать надежную защиту зоны сварки от атмосферного воздуха и хорошее раскисление варочной ванны.
Одной из эффективных мер является сварка короткой дугой (до 1,5 мм), при которой резко уменьшается подсос газов из атмосферы. Чтобы предупредить образование пор по линии сплавления, необходимо перед сваркой предварительно подогревать металл до температуры 250–300 °C с последующим охлаждением на воздухе.
При толщине листов свыше 1,5 мм применяют электроды с основным покрытием на постоянном токе обратной полярности. Для того чтобы снизить напряжение в сварном соединении и предупредить перегрев электрода, используют пониженный ток (по сравнению с током, применяемым для сварки стали).
Сварка ведется в нижнем положении, причем поперечные колебания электрода не должны превышать трех диаметров электрода. При случайных обрывах дуги ее возбуждают на зачищенном от шлака шве, отступая назад от кратера на 5–6 мм. Сварка выполняется за один проход. При большой толщине свариваемых кромок ведут многопроходную сварку после остывания соединения и тщательной очистки предыдущего слоя от брызг и шлака.
Если предпочтительна полуавтоматическая сварка, то ее ведут плавящимся электродом в среде защитных газов на постоянном токе обратной полярности. В качестве защитной среды служит аргон и гелий. Повышает качество швов введение в аргон до 20 % водорода. Сварку ведут стандартными полуавтоматами с горелкой, которую наклоняют углом вперед на 10–15° от вертикали. Чтобы в шве не образовывались поры, рекомендуется применять сварочную проволоку, легированную до 3 % титаном или добавками редкоземельных элементов.
Предупреждают прожоги и способствуют формированию обратной стороны шва флюсовые подушки или медные формующие подкладки. Сварка начинается и заканчивается на технологических планках с разделкой кромок и толщиной, равной толщине свариваемого металла.
Незначительная теплопроводность и низкая температура плавления свинца требуют применения небольшой погонной энергии сварки. Сварка свинца может проводиться в любом положении, но при наклоне изделия более 10–15° происходит вытекание металла из ванны, что влияет на формирование сварных швов. Приемлемым является нижнее положение, на которое и нужно ориентироваться при сварке свинцовых изделий.
Так как свинец имеет большую плотность и существует вероятность провалов ванны, рекомендуется применять передвижные формирующие пластины-прокладки. Кромки изделий перед сваркой протирают бензином или четыреххлористым углеродом и зачищают шабером до металлического блеска на ширину 20–25 мм.
Заготовки толщиной до 2 мм сваривают с отбортовкой кромок высотой, равной толщине свариваемого металла; при толщине свинца до 8 мм – без разделки кромок; при большей толщине делается скос кромок с общим углом раскрытия 60–70° без зазора в стыке и притупление 3–4 мм. Иногда выполняют двустороннюю подготовку кромок. Сварка свинца проводится угольным электродом, в среде инертных газов – плавящимся и неплавящимся электродами, а также ацетилено-кислородной сваркой. Сварка угольными электродами выполняется на постоянном токе прямой полярности.
Во время сварки электроды располагаются перпендикулярно или с наклоном на 10–15° от вертикали в сторону движения сварки.
Сварка алюминия и его сплавов
Чистый алюминий имеет ограниченное применение из-за своей низкой прочности и высокой пластичности. В повседневной жизни находят применение сплавы алюминия – дюралюмины и силумины. При сварке алюминия на поверхности расплавленного металла образуется тугоплавкая пленка оксида алюминия, которая препятствует процессу сплавления между собой частиц металла. Разность между температурой плавления оксида алюминия (2050 °C) и температурой плавления алюминия (658 °C) создает технологические трудности в ходе сварочных работ.Независимо от способа сварки изделия должны проходить специальную подготовку. Поверхности обезжиривают и удаляют с них пленку оксида алюминия. Точно так же подготавливают присадочную проволоку и электродные стержни перед нанесением на них покрытия.
Обезжиривание проводят с помощью растворителей, например авиационного бензина или технического ацетона. Следующий этап – механическая зачистка или химическое травление, которое удаляет оксидную пленку. Обезжиривание и травление проводят не более чем за 2–4 ч до сварки.
Для неответственных изделий применяется ручная сварка угольным электродом на постоянном токе прямой полярности. Если металл имеет толщину до 2 мм, то сварку ведут без присадки и без разделки кромок; при толщине металла свыше 2 мм сварку выполняют с зазором, равным 0,5–0,7 толщины свариваемых листов или с разделкой кромок. Ручная сварка покрытыми электродами выполняют при изготовлении конструкций из технического алюминия, сплавов АМц и АМг и силумина. При умеренных токах требуемое проплавление обеспечивается использованием постоянного тока прямой полярности с предварительным подогревом (для средних толщин – 250–300 °C, для больших толщин – до 400 °C). Скорость сварки алюминия должна быть выше, чем скорость сварки стали. Она ведется непрерывно в пределах одного электрода в связи с тем, что пленка шлака на кратере в конце электрода препятствует повторному зажиганию дуги.
Сварочный ток принимается из расчета не более 60 А на 1 мм диаметра электрода – это обеспечит устойчивость процесса и минимальные потери при разбрызгивании. Электроды предварительно просушивают при температуре 150–200 °C в течение 2 ч.
При ручной аргонодуговой сварке применяют неплавящиеся вольфрамовые электроды в осушенном от влаги аргоне высшего сорта на переменном токе. Если толщина свариваемого металла равна 5–6 мм, то применяются электроды диаметром 1,5–5 мм.
Техника сварки имеет здесь свои особенности. Между электродом и присадочной проволокой должен выдерживаться угол примерно в 85–90°. При подаче присадки используют возвратно-поступательные движения. Эффективная защита достигается оптимальным расходом газа. Металл толщиной до 10 мм сваривают справа налево: этот прием позволяет снизить перегрев свариваемого металла.
Сварка трубопроводов
Основным способом сварки неповоротных стыков магистральных трубопроводов или отдельных труб в непрерывную является ручная сварка электродами. Преимуществами такой сварки являются простота работы и возможность применения его в разных климатических условиях.Сварные трубы, которые применяют при прокладке технологических, магистральных и производственных трубопроводов, имеют наружный диаметр 4–1620 мм при толщине стенок 0,3–25 мм. Сварные трубы выпускают с прямым продольным или спиральным сварным швом.
Цельнокатанные трубы изготавливают из низкоуглеродистой мартеновской стали с пределом прочности 350–550 МПа. Промышленность выпускает трубы наружным диаметром 114–426 мм и толщиной стенки 4,5–20 мм.
Магистральные трубопроводы нефтяных заводов, а также трубопроводы для транспортирования жидких и агрессивных веществ монтируются из цельнокатанных труб, изготовленных из легированных жаропрочных и нержавеющих сталей.
Алюминиевые трубы предназначены для магистральных трубопроводов и трубопроводов нефтезаводов, которые находятся в средах, вызывающих коррозию. Сортаментом для этих труб предусмотрены наружные диаметры 120–280 мм и толщина стенок 10–30 мм. Для сборки магистральных и заводских производственных трубопроводов применяются специальные фасонные части. Их применяют для углов поворотов, участков ответвления и пр. Такие части представляют собой крутоизогнутые угольники, двойники, тройники, переходы, изготавливаемые из стали 20 путем протяжки или штамповки. Применяют и сварные фасонные части. Крутоизогнутые угольники выпускают с наружным диаметром 48–529 мм при толщине стенок 4,5–12 мм и среднем радиусе 80–500 мм. Сварные отводы чаще всего делают из нескольких частей (рис. 119).
