Страница:
Однако указанные средства защиты имеют смотровое отверстие, снабженное светофильтром, который уменьшает яркость световых лучей дуги и, кроме того, задерживает инфракрасные и ультрафиолетовые лучи. Снаружи для защиты от брызг металла светофильтр защищен простым прозрачным стеклом.
Предотвращение опасности взрыва. Взрыв может возникнуть при неправильном хранении, транспортировке и использовании баллонов со сжатыми газами, а также при сварочных работах в различных емкостях без предварительной аккуратной очистки их от остатков горючих веществ. Категорически запрещается устанавливать баллоны вблизи нагревательных приборов или под солнечными лучами. Баллоны на рабочем месте должны быть хорошо укреплены в вертикальном положении, исключающем любую возможность ударов и падений. Ни в коем случае нельзя отогревать открытым пламенем редуктор баллона с углекислотой и в любых баллонах со сжатым газом. Отогревание можно производить только тряпками, смоченными горячей водой.
К эксплуатации должны допускаться только прошедшие освидетельствование и исправные баллоны. Транспортировка баллонов может осуществляться на специальных носилках или на подрессорных колясках. Для этого на баллоны навертывают предохранительные колпаки и кладут их на деревянные подкладки с гнездами, обитыми войлоком. Нужно всегда помнить о том, что совместная транспортировка кислородных и ацетиленовых баллонов запрещается.
При работе баллон фиксируют в вертикальном положении с помощью хомутика на расстоянии не менее 5 м от места сварки. Перед началом работы выходное отверстие баллона нужно продуть. Расходование газа необходимо осуществлять до остаточного давления кислорода не меньше 0,05 МПа, а ацетилена 0,05–0,1 МПа. По завершении работы следует тщательно закрыть вентиль баллона, из редуктора и шлангов выпустить газ, потом снять редуктор, зафиксировать на штуцере заглушку и навернуть колпак на вентиль.
Следует также своевременно освидетельствовать баллоны (1 раз в 5 лет) и пористую массу ацетиленовых баллонов (1 раз в год).
Категорически запрещается хранить смазочные материалы и замасленную ветошь рядом с кислородными баллонами. Емкости из-под нефтепродуктов нужно перед сваркой промыть 2–3 раза горячим 10 %-ным раствором щелочи, а затем продуть паром или воздухом для удаления запаха. Тщательную продувку нужно производить и перед сваркой газопроводов.
Защита от отравлений вредными газами, пылью и испарениями. Загрязнение воздуха указанными факторами происходит особенно сильно при работе электродами с качественным покрытием. В то же время количество пыли и газов значительно меньше при автоматической сварке, чем при ручной. Сварочная пыль является по своим физическим свойствам аэрозолью, состоящей из взвеси частиц минералов и оксидов металлов в газовой среде. Основные компоненты пыли – оксиды железа (до 70 %), хрома, марганца, кремния, а также фтористые соединения. Для организма наиболее вредны соединения фтора, марганца и хрома. Из газов, выделяемых при сварке в рабочих помещениях, наиболее токсичными являются оксиды углерода, азота, фтористый водород и другие.
Поэтому для удаления пыли и вредных газов из зоны сварки и для подачи чистого воздуха нужно организовать общую и местную вентиляцию. Общую вентиляцию нужно сделать приточно-вытяжной, тогда как местная вентиляция должна быть с верхним, нижним и боковым отсосом, обеспечивающим удаление пыли и газов непосредственно из зоны сварки.
Категорически запрещается работать в замкнутых емкостях без вентиляции, которая заключается в подаче по шлангу свежего воздуха в зону работы сварщика. Количество подаваемого воздуха должно составлять не менее 30 м3/ч.
При ручной дуговой сварке электродами с качественными покрытиями объем вентиляции должен составлять 4000–6000 м3на 1 кг расхода электродов, при сварке в углекислом газе – до 1000 куб. м на 1 кг расплавляемой проволоки, а при автоматической сварке под флюсом – приблизительно 200 м3.
Разрешается пользоваться естественной вентиляцией в том случае, если часовой расход электродов менее 0,2 кг на 1 м3помещения. Кроме этого, при эксплуатации газосварочного (резочного) оборудования нужно выполнять следующие требования.
Перед проведением сварочных работ нужно тщательно ознакомиться с инструкциями по правилам пользования и техническими характеристиками различного оборудования (горелки, емкости, редукторы, шланги). В том случае, если вы не располагаете достаточным для проведения указанных работ объемом практических знаний, то необходимо проконсультироваться у специалистов (можно у рабочего-газосварщика).
Новое оборудование нужно эксплуатировать только в течение гарантийного срока, который обеспечивает безопасность работ. Необходимо аккуратно выполнять повторные испытания, наладку и регулировку аппаратуры в те сроки, которые указаны в техническом паспорте. Причем испытания и ремонт могут проводить только специалисты.
Запрещается производить сварочные работы и устанавливать оборудование около огнеопасных материалов. В период работы нельзя оставлять генератор без надзора, а также перемещать заряженный генератор. Подвижные ацетиленовые генераторы нужно устанавливать на расстоянии не менее 10 м от очагов огня. Эти генераторы необходимо монтировать строго вертикально и заправлять водой только до рекомендуемого уровня. Загружать генератор карбидом кальция нужно только той грануляции, которая записана в паспорте машины. После загрузки указанного вещества следует осуществить продувку генератора от остатков воздуха. Для предотвращения замерзания генератора необходимо удалить после работы воду. Если генератор все-таки замерз, то отогревать его можно только паром или ветошью, смоченной горячей водой, но не открытым пламенем. Ил нужно выгружать только лишь после окончательного разложения карбида и лишь в иловые ямы с надписью о запрещении курения.
Наличие, исправность и заправленность водяного затвора генератора – необходимое условие безопасности работы этой установки. Перед работой нужно обязательно установить в затворе через его смесительный кран уровень воды либо низкозамерзающей жидкости (30 %-ный раствор хлористого кальция в воде или 60 %-ный раствор этиленгликоля в воде), которая заправляется при температуре воздуха ниже 0 °C.
В водяном затворе уровень жидкости нужно устанавливать на высоте контрольного крана. После сварочных работ затвор следует промыть водой. Водяной затвор нужно еженедельно проверять на герметичность, а через каждые 3 месяца разбирать для очистки и промывания; после сборки следует выяснить надежность уплотнения обратного клапана.
Карбид кальция следует хранить только в герметически закрытых барабанах, которые должны находиться в хорошо проветриваемых и сухих помещениях. При вскрытии барабана нельзя использовать стальное зубило и молоток для предупреждения образования искр, очень опасных для ацетилено-воздушных смесей. Разрешается вскрытие только специальным ножом, причем крышку предварительно покрывают маслом в месте разреза (можно просверлить отверстие, а потом произвести вырез ножницами). Нельзя использовать и медные инструменты, потому что ацетилен в условиях влажности может образовать с медью ацетиленовую медь, которая очень взрывоопасна даже при незначительных ударах.
Фиксация редуктора на баллоне должна осуществляться с осторожностью, чтобы не сорвать резьбу; крепление должно быть плотным. Кислородная подача в редуктор проводится только при совсем ослабленной регулировочной пружине редуктора, а вентиль нужно открывать медленно. При этом следят за тем, чтобы не было утечки кислорода. При выявлении какой-либо неисправности ее надо ликвидировать после предварительного закрытия вентиля баллона.
Газоподводящие шланги нужно герметично и плотно закрепить на ниппелях стяжными хомутиками. Контроль за исправностью газопроводов и шлангов должен проводиться постоянно.
Категорически запрещается уменьшать давление кислорода на входе в резак ниже давления горючего в бачке; подсоединять более одной горелки к одному затвору; пользоваться резаком или горелкой, не снабженной обратным клапаном, который предохраняет шланг от проникновения в него пламени; перемещаться с работающей горелкой, а также оставлять без присмотра резак или горелку с зажженным пламенем.
Нельзя начинать сварочные работы при отсутствии противопожарного инвентаря (огнетушитель, бочки или ведра с водой, ящики с песком и лопата); курить в процессе работы с карбидом кальция, жидкими горючими веществами и с ацетиленовым генератором; использовать для обдувания одежды кислород, а также применять инструменты собственного изготовления.
Места проведения газопламенных работ должны быть хорошо очищены от взрывоопасных и легковоспламеняющихся веществ на расстоянии 30 м. Сами работы нужно проводить на расстоянии не менее 1,5 м от газоразборных постов и газопроводов, 5 м – от бачков с жидким горючим и баллонов, 10 м – от передвижных генераторов. Если пламя и искры направлены в сторону источников питания, то для их защиты следует воспользоваться металлическими ширмами. В сосудах и резервуарах газопламенные работы нужно выполнять в асбестовой или брезентовой одежде; работающий в сосуде должен быть снабжен страховочным канатом, предохранительным поясом, средствами индивидуальной защиты с притоком чистого воздуха.
При возникновении обратного удара пламени сварочные работы нужно немедленно остановить, вентили на горелке или резаке перекрыть, а газосварщику незамедлительно покинуть закрытую емкость (если он там работает). Затем работающий должен осмотреть затвор и установить целостность редукторов и рукавов, а также уровень жидкости в затворе, если используется жидкостный затвор.
Газопламенная пайка
Технология пайки
Дефекты сварки и способы их устранения
Глава 13. Обустройство чердачного помещения
Планировка чердачного помещения
Чердачная квартира с террасой на крыше
Предотвращение опасности взрыва. Взрыв может возникнуть при неправильном хранении, транспортировке и использовании баллонов со сжатыми газами, а также при сварочных работах в различных емкостях без предварительной аккуратной очистки их от остатков горючих веществ. Категорически запрещается устанавливать баллоны вблизи нагревательных приборов или под солнечными лучами. Баллоны на рабочем месте должны быть хорошо укреплены в вертикальном положении, исключающем любую возможность ударов и падений. Ни в коем случае нельзя отогревать открытым пламенем редуктор баллона с углекислотой и в любых баллонах со сжатым газом. Отогревание можно производить только тряпками, смоченными горячей водой.
К эксплуатации должны допускаться только прошедшие освидетельствование и исправные баллоны. Транспортировка баллонов может осуществляться на специальных носилках или на подрессорных колясках. Для этого на баллоны навертывают предохранительные колпаки и кладут их на деревянные подкладки с гнездами, обитыми войлоком. Нужно всегда помнить о том, что совместная транспортировка кислородных и ацетиленовых баллонов запрещается.
При работе баллон фиксируют в вертикальном положении с помощью хомутика на расстоянии не менее 5 м от места сварки. Перед началом работы выходное отверстие баллона нужно продуть. Расходование газа необходимо осуществлять до остаточного давления кислорода не меньше 0,05 МПа, а ацетилена 0,05–0,1 МПа. По завершении работы следует тщательно закрыть вентиль баллона, из редуктора и шлангов выпустить газ, потом снять редуктор, зафиксировать на штуцере заглушку и навернуть колпак на вентиль.
Следует также своевременно освидетельствовать баллоны (1 раз в 5 лет) и пористую массу ацетиленовых баллонов (1 раз в год).
Категорически запрещается хранить смазочные материалы и замасленную ветошь рядом с кислородными баллонами. Емкости из-под нефтепродуктов нужно перед сваркой промыть 2–3 раза горячим 10 %-ным раствором щелочи, а затем продуть паром или воздухом для удаления запаха. Тщательную продувку нужно производить и перед сваркой газопроводов.
Защита от отравлений вредными газами, пылью и испарениями. Загрязнение воздуха указанными факторами происходит особенно сильно при работе электродами с качественным покрытием. В то же время количество пыли и газов значительно меньше при автоматической сварке, чем при ручной. Сварочная пыль является по своим физическим свойствам аэрозолью, состоящей из взвеси частиц минералов и оксидов металлов в газовой среде. Основные компоненты пыли – оксиды железа (до 70 %), хрома, марганца, кремния, а также фтористые соединения. Для организма наиболее вредны соединения фтора, марганца и хрома. Из газов, выделяемых при сварке в рабочих помещениях, наиболее токсичными являются оксиды углерода, азота, фтористый водород и другие.
Поэтому для удаления пыли и вредных газов из зоны сварки и для подачи чистого воздуха нужно организовать общую и местную вентиляцию. Общую вентиляцию нужно сделать приточно-вытяжной, тогда как местная вентиляция должна быть с верхним, нижним и боковым отсосом, обеспечивающим удаление пыли и газов непосредственно из зоны сварки.
Категорически запрещается работать в замкнутых емкостях без вентиляции, которая заключается в подаче по шлангу свежего воздуха в зону работы сварщика. Количество подаваемого воздуха должно составлять не менее 30 м3/ч.
При ручной дуговой сварке электродами с качественными покрытиями объем вентиляции должен составлять 4000–6000 м3на 1 кг расхода электродов, при сварке в углекислом газе – до 1000 куб. м на 1 кг расплавляемой проволоки, а при автоматической сварке под флюсом – приблизительно 200 м3.
Разрешается пользоваться естественной вентиляцией в том случае, если часовой расход электродов менее 0,2 кг на 1 м3помещения. Кроме этого, при эксплуатации газосварочного (резочного) оборудования нужно выполнять следующие требования.
Перед проведением сварочных работ нужно тщательно ознакомиться с инструкциями по правилам пользования и техническими характеристиками различного оборудования (горелки, емкости, редукторы, шланги). В том случае, если вы не располагаете достаточным для проведения указанных работ объемом практических знаний, то необходимо проконсультироваться у специалистов (можно у рабочего-газосварщика).
Новое оборудование нужно эксплуатировать только в течение гарантийного срока, который обеспечивает безопасность работ. Необходимо аккуратно выполнять повторные испытания, наладку и регулировку аппаратуры в те сроки, которые указаны в техническом паспорте. Причем испытания и ремонт могут проводить только специалисты.
Запрещается производить сварочные работы и устанавливать оборудование около огнеопасных материалов. В период работы нельзя оставлять генератор без надзора, а также перемещать заряженный генератор. Подвижные ацетиленовые генераторы нужно устанавливать на расстоянии не менее 10 м от очагов огня. Эти генераторы необходимо монтировать строго вертикально и заправлять водой только до рекомендуемого уровня. Загружать генератор карбидом кальция нужно только той грануляции, которая записана в паспорте машины. После загрузки указанного вещества следует осуществить продувку генератора от остатков воздуха. Для предотвращения замерзания генератора необходимо удалить после работы воду. Если генератор все-таки замерз, то отогревать его можно только паром или ветошью, смоченной горячей водой, но не открытым пламенем. Ил нужно выгружать только лишь после окончательного разложения карбида и лишь в иловые ямы с надписью о запрещении курения.
Наличие, исправность и заправленность водяного затвора генератора – необходимое условие безопасности работы этой установки. Перед работой нужно обязательно установить в затворе через его смесительный кран уровень воды либо низкозамерзающей жидкости (30 %-ный раствор хлористого кальция в воде или 60 %-ный раствор этиленгликоля в воде), которая заправляется при температуре воздуха ниже 0 °C.
В водяном затворе уровень жидкости нужно устанавливать на высоте контрольного крана. После сварочных работ затвор следует промыть водой. Водяной затвор нужно еженедельно проверять на герметичность, а через каждые 3 месяца разбирать для очистки и промывания; после сборки следует выяснить надежность уплотнения обратного клапана.
Карбид кальция следует хранить только в герметически закрытых барабанах, которые должны находиться в хорошо проветриваемых и сухих помещениях. При вскрытии барабана нельзя использовать стальное зубило и молоток для предупреждения образования искр, очень опасных для ацетилено-воздушных смесей. Разрешается вскрытие только специальным ножом, причем крышку предварительно покрывают маслом в месте разреза (можно просверлить отверстие, а потом произвести вырез ножницами). Нельзя использовать и медные инструменты, потому что ацетилен в условиях влажности может образовать с медью ацетиленовую медь, которая очень взрывоопасна даже при незначительных ударах.
Фиксация редуктора на баллоне должна осуществляться с осторожностью, чтобы не сорвать резьбу; крепление должно быть плотным. Кислородная подача в редуктор проводится только при совсем ослабленной регулировочной пружине редуктора, а вентиль нужно открывать медленно. При этом следят за тем, чтобы не было утечки кислорода. При выявлении какой-либо неисправности ее надо ликвидировать после предварительного закрытия вентиля баллона.
Газоподводящие шланги нужно герметично и плотно закрепить на ниппелях стяжными хомутиками. Контроль за исправностью газопроводов и шлангов должен проводиться постоянно.
Категорически запрещается уменьшать давление кислорода на входе в резак ниже давления горючего в бачке; подсоединять более одной горелки к одному затвору; пользоваться резаком или горелкой, не снабженной обратным клапаном, который предохраняет шланг от проникновения в него пламени; перемещаться с работающей горелкой, а также оставлять без присмотра резак или горелку с зажженным пламенем.
Нельзя начинать сварочные работы при отсутствии противопожарного инвентаря (огнетушитель, бочки или ведра с водой, ящики с песком и лопата); курить в процессе работы с карбидом кальция, жидкими горючими веществами и с ацетиленовым генератором; использовать для обдувания одежды кислород, а также применять инструменты собственного изготовления.
Места проведения газопламенных работ должны быть хорошо очищены от взрывоопасных и легковоспламеняющихся веществ на расстоянии 30 м. Сами работы нужно проводить на расстоянии не менее 1,5 м от газоразборных постов и газопроводов, 5 м – от бачков с жидким горючим и баллонов, 10 м – от передвижных генераторов. Если пламя и искры направлены в сторону источников питания, то для их защиты следует воспользоваться металлическими ширмами. В сосудах и резервуарах газопламенные работы нужно выполнять в асбестовой или брезентовой одежде; работающий в сосуде должен быть снабжен страховочным канатом, предохранительным поясом, средствами индивидуальной защиты с притоком чистого воздуха.
При возникновении обратного удара пламени сварочные работы нужно немедленно остановить, вентили на горелке или резаке перекрыть, а газосварщику незамедлительно покинуть закрытую емкость (если он там работает). Затем работающий должен осмотреть затвор и установить целостность редукторов и рукавов, а также уровень жидкости в затворе, если используется жидкостный затвор.
Газопламенная пайка
Газопламенная пайка отличается от сварки тем, что при пайке расплавляется только припой, тогда как при сварке плавятся соединяемые кромки металла. При этом температура плавления припоя значительно меньше, чем у соединяемого металла.
Нужно заметить, что при пайке происходит довольно большой расход металла, а отдельные виды припоев очень дороги. Кроме этого, часто пайка предполагает применение швов внахлестку. Ввиду этих причин пайка не так широко распространена, как сварка. Однако при некоторых видах работ она незаменима (пайка электро– и радиоаппаратуры, печатных схем точных приборов, внутренних швов пищевой и медицинской аппаратуры и др.).
В паяльных работах используются низкотемпературные и высокотемпературные пайки.
Низкотемпературная пайка осуществляется с использованием припоев с температурой плавления ниже 550 °C, а высокотемпературная предусматривает применение припоев с температурой плавления свыше 550 °C. Низкотемпературную пайку можно осуществлять электрическими паяльниками или газоводушными горелками, а высокотемпературную – горелками, которые работают на кислородно-пропановой или ацетилен-бутановой смеси. При пайке крупногабаритных изделий можно применять многопламенные горелки.
Выбор того или иного вида припоя будет зависеть от вида паяемого металла и, конечно, от вида пайки. Для низкотемпературной пайки используются оловянисто-цинковые и оловянисто-свинцовые припои, причем последние получили довольно широкое распространение. Для высокотемпературной пайки применяются серебряные, медно-цинковые и медно-фосфористые припои. Самую широкую область применения имеют серебряные припои, которые дают высокое качество пайки почти всех черных и цветных металлов (за исключением цинка и алюминия). Медно-цинковые припои находят применение для пайки никеля, стали и чугуна, хотя их можно использовать и для паяния металлов медной группы. Медно-фосфористые припои применяются только при пайке меди и ее сплавов (латунь, бронза). Эти припои характеризуются тем, что при пайке меди вообще не требуют флюса, но они довольно хрупкие и поэтому их нельзя применять в конструкциях, которые подвергаются механическим нагрузкам.
Применение флюсов при пайке необходимо практически всегда, так как они растворяют образующиеся при пайке оксиды, улучшают смачивание припоем металла, а также препятствуют окислению металла и припоя.
При низкотемпературной пайке наиболее часто используется такой флюс, как канифоль. Хлористый цинк, хлористый аммоний, фтористый натрий применяются реже.
Высокотемпературная пайка цветных и черных металлов предполагает использование флюсов чаще всего на основе буры. В случае повышения рабочей температуры пайки (когда применяются более тугоплавкие припои) иногда добавляется борная кислота. Комплекс солей, состоящий из хлоридов щелочных и щелочно-земельных металлов, используется при пайке магниевых и алюминиевых сплавов. Во флюс вводится хлористый цинк, фтористый калий и другие соединения щелочных металлов тогда, когда необходимо выполнить работу легкоплавким припоем.
Следует заметить, что при газопламенной пайке лучше всего применять флюсы в виде порошка или паст.
Особенности паяных швов. При пайке, как уже указывалось выше, используются в основном нахлесточные швы, прочность соединения которых тесно связана с величиной нахлеста. Однако при паяльных работах применяются еще стыковые, втулочные, специальные швы, а также швы с отбортовкой (рис. 136).
Рис. 136. Типы паяных швов: 1 – стыковые; 2 – нахлесточные; 3 – с отбортовкой; 4 – втулочные; 5 – специальные.
Нужно запомнить, что для улучшения надежности стыкового соединения его площадь можно увеличить путем выполнения косого или зубчатого стыка. Конечно, такая конструкция паяного шва потребует специальной и точной механической обработки, но она хорошо оправдывает себя, например, при пайке полотен циркулярных и ленточных пил.
Пайка различных трубчатых конструкций применяется весьма широко. Особенности трубчатых соединений показаны на рис. 137.
Рис. 137. Варианты трубчатых соединений.
Трубчатые соединения типов 1 и 2 возможны в том случае, когда допускается увеличение наружного диаметра трубы, а соединения типов 3 и 4 – когда нужно сохранить точный диаметр трубы. При пайке величину зазора между деталями необходимо сделать наименьшей. Это нужно для улучшения заполнения зазора припоем под воздействием капиллярных сил.
Тавровый тип соединения используется при пайке относительно редко.
Нужно заметить, что при пайке происходит довольно большой расход металла, а отдельные виды припоев очень дороги. Кроме этого, часто пайка предполагает применение швов внахлестку. Ввиду этих причин пайка не так широко распространена, как сварка. Однако при некоторых видах работ она незаменима (пайка электро– и радиоаппаратуры, печатных схем точных приборов, внутренних швов пищевой и медицинской аппаратуры и др.).
В паяльных работах используются низкотемпературные и высокотемпературные пайки.
Низкотемпературная пайка осуществляется с использованием припоев с температурой плавления ниже 550 °C, а высокотемпературная предусматривает применение припоев с температурой плавления свыше 550 °C. Низкотемпературную пайку можно осуществлять электрическими паяльниками или газоводушными горелками, а высокотемпературную – горелками, которые работают на кислородно-пропановой или ацетилен-бутановой смеси. При пайке крупногабаритных изделий можно применять многопламенные горелки.
Выбор того или иного вида припоя будет зависеть от вида паяемого металла и, конечно, от вида пайки. Для низкотемпературной пайки используются оловянисто-цинковые и оловянисто-свинцовые припои, причем последние получили довольно широкое распространение. Для высокотемпературной пайки применяются серебряные, медно-цинковые и медно-фосфористые припои. Самую широкую область применения имеют серебряные припои, которые дают высокое качество пайки почти всех черных и цветных металлов (за исключением цинка и алюминия). Медно-цинковые припои находят применение для пайки никеля, стали и чугуна, хотя их можно использовать и для паяния металлов медной группы. Медно-фосфористые припои применяются только при пайке меди и ее сплавов (латунь, бронза). Эти припои характеризуются тем, что при пайке меди вообще не требуют флюса, но они довольно хрупкие и поэтому их нельзя применять в конструкциях, которые подвергаются механическим нагрузкам.
Применение флюсов при пайке необходимо практически всегда, так как они растворяют образующиеся при пайке оксиды, улучшают смачивание припоем металла, а также препятствуют окислению металла и припоя.
При низкотемпературной пайке наиболее часто используется такой флюс, как канифоль. Хлористый цинк, хлористый аммоний, фтористый натрий применяются реже.
Высокотемпературная пайка цветных и черных металлов предполагает использование флюсов чаще всего на основе буры. В случае повышения рабочей температуры пайки (когда применяются более тугоплавкие припои) иногда добавляется борная кислота. Комплекс солей, состоящий из хлоридов щелочных и щелочно-земельных металлов, используется при пайке магниевых и алюминиевых сплавов. Во флюс вводится хлористый цинк, фтористый калий и другие соединения щелочных металлов тогда, когда необходимо выполнить работу легкоплавким припоем.
Следует заметить, что при газопламенной пайке лучше всего применять флюсы в виде порошка или паст.
Особенности паяных швов. При пайке, как уже указывалось выше, используются в основном нахлесточные швы, прочность соединения которых тесно связана с величиной нахлеста. Однако при паяльных работах применяются еще стыковые, втулочные, специальные швы, а также швы с отбортовкой (рис. 136).
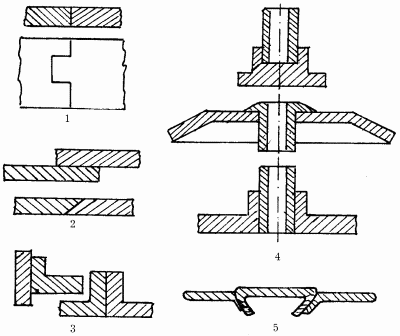
Нужно запомнить, что для улучшения надежности стыкового соединения его площадь можно увеличить путем выполнения косого или зубчатого стыка. Конечно, такая конструкция паяного шва потребует специальной и точной механической обработки, но она хорошо оправдывает себя, например, при пайке полотен циркулярных и ленточных пил.
Пайка различных трубчатых конструкций применяется весьма широко. Особенности трубчатых соединений показаны на рис. 137.
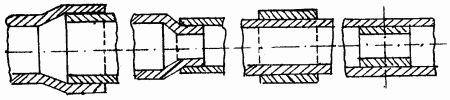
Трубчатые соединения типов 1 и 2 возможны в том случае, когда допускается увеличение наружного диаметра трубы, а соединения типов 3 и 4 – когда нужно сохранить точный диаметр трубы. При пайке величину зазора между деталями необходимо сделать наименьшей. Это нужно для улучшения заполнения зазора припоем под воздействием капиллярных сил.
Тавровый тип соединения используется при пайке относительно редко.
Технология пайки
Ход работы при низкотемпературной пайке будет таким. Перед началом работы соединяемые детали следует тщательно очистить, а затем провести их лужение, то есть нанести путем натирания, погружения в расплав или электролитическим методом тонкий слой олова на поверхность этих деталей. Затем нужно соединить детали так, чтобы между ними остался зазор в 1–2 мм. Потом на поверхность участка соединения необходимо нанести флюс. На заключительном этапе расплавленный с помощью горелки припой заливают в зазор, а потом наносят еще на поверхность металла вокруг зазора.
При высокотемпературной пайке технология будет несколько иной. Вначале нужно провести очистку деталей и их лужение таким же образом, как и при низкотемпературной пайке. Потом необходимо аккуратно соединить детали, тщательно соблюдая рекомендуемую величину зазора. Затем следует прогреть детали в месте соединения факелом горелки до температуры расплавления и растекания припоя (это составит зону шириной около 30 мм в обе стороны от центра пайки) и нанести флюс. Далее нужно расплавить сам припой и погрузить его во флюс, а затем через некоторое время вынуть. Как только флюс на припое расплавится, надо залить припой в зазор и для хорошего растекания его в полости зазора несколько раз чуть сместить разогретые ранее детали. При этом нельзя плавить припой в пламени горелки.
Высокотемпературную пайку следует производить газовым пламенем нормального состава (небольшой избыток горючего допускается). Удельная мощность пламени должна составить (по ацетилену) для нержавеющей стали 60–70, для углеродистой стали – 100–200, меди – 150–200, латуни – 100–120 л/чмм. Здесь следует упомянуть о том, что под удельной мощностью пламени понимается часовой расход ацетилена в литрах, приходящийся на 1 мм толщины свариваемого или подвергаемого пайке металла.
После окончания процесса пайки следует отвести пламя горелки в сторону, а соединенные детали оставить для естественного остывания. При этом ни в коем случае нельзя пытаться ускорить процесс охлаждения. В конце работы нужно очистить шов от флюса смоченной в теплой воде ветошью.
При высокотемпературной пайке технология будет несколько иной. Вначале нужно провести очистку деталей и их лужение таким же образом, как и при низкотемпературной пайке. Потом необходимо аккуратно соединить детали, тщательно соблюдая рекомендуемую величину зазора. Затем следует прогреть детали в месте соединения факелом горелки до температуры расплавления и растекания припоя (это составит зону шириной около 30 мм в обе стороны от центра пайки) и нанести флюс. Далее нужно расплавить сам припой и погрузить его во флюс, а затем через некоторое время вынуть. Как только флюс на припое расплавится, надо залить припой в зазор и для хорошего растекания его в полости зазора несколько раз чуть сместить разогретые ранее детали. При этом нельзя плавить припой в пламени горелки.
Высокотемпературную пайку следует производить газовым пламенем нормального состава (небольшой избыток горючего допускается). Удельная мощность пламени должна составить (по ацетилену) для нержавеющей стали 60–70, для углеродистой стали – 100–200, меди – 150–200, латуни – 100–120 л/чмм. Здесь следует упомянуть о том, что под удельной мощностью пламени понимается часовой расход ацетилена в литрах, приходящийся на 1 мм толщины свариваемого или подвергаемого пайке металла.
После окончания процесса пайки следует отвести пламя горелки в сторону, а соединенные детали оставить для естественного остывания. При этом ни в коем случае нельзя пытаться ускорить процесс охлаждения. В конце работы нужно очистить шов от флюса смоченной в теплой воде ветошью.
Дефекты сварки и способы их устранения
Дефекты сварных швов появляются в результате либо неправильного выбора, либо нарушения технологии изготовления сварной конструкции, а также в результате использования некачественных сварочных материалов и невысокой квалификации сварщика.
Дефекты подразделяются на внешние и внутренние. Причем внешние дефекты можно выявить путем осмотра невооруженным глазом или с помощью лупы с десятикратным увеличением, в то время как для установления внутренних дефектов требуется использование специальных методов: металлографические исследования, химический анализ, механические испытания, просвечивание рентгеновскими или гамма-лучами, магнитные и ультразвуковые методы контроля. Для выявления дефектов сварное соединение нужно предварительно очистить от шлака, окалины и металлических брызг.
К внешним дефектам относятся: нарушение размеров и формы шва, подрез зоны сплавления, прожог, наплыв, непровар, поверхностное окисление, незаваренные кратеры, поверхностные поры, продольные и поперечные трещины.
К внутренним дефектам относятся следующие: внутренние поры, непровар, неметаллические включения и микротрещины.
Нарушение размеров и форм шва проявляется в чрезмерном усилении и резких переходах от основного металла к наплавленному, а также в неполномерности высоты и ширины шва. При ручной сварке данные дефекты возникают в результате неаккуратной подготовки свариваемых кромок, неправильного выбора сварочного тока, невысокого качества сборки под сварку и низкой квалификации сварщика. Дефекты формы шва могут возникнуть и в результате колебания напряжения в сети при выполнении работы. При автоматизированной сварке нарушения размеров и формы швов могут быть из-за несоблюдения режима сварочного процесса (скорости сварки, скорости подачи электродов, сварочного тока) и неправильной разделки шва.
Подрез зоны сплавления выглядит в виде узкого углубления в основном металле вдоль края сварного шва. Этот дефект возникает при усиленной мощности горелки, при сварке удлиненной дугой, неправильном положении электрода или горелки и присадочного прутка, а также при сварке большим током.
Прожог представляет собой сквозное отверстие в сварном шве. Основные причины его возникновения следующие: малая толщина свариваемого металла, завышенная мощность пламени горелки, большой сварочный ток, незначительное притупление свариваемых кромок и неравномерный зазор между ними по расстоянию.
Наплыв – натекание металла шва на непрогретую поверхность свариваемого металла или прежде выполненного валика без сплавления с ним. Дефект возникает при некачественных электродах и несоответствии скорости сварки и сварочного тока разделке шва, а также при низкой квалификации сварщика.
Непровар проявляется в виде местного несплавления свариваемых кромок основного и наплавленного металлов и может быть результатом плохой подготовки свариваемых кромок (отсутствие зазора, большое притупление, незначительный угол скоса), смещения электрода к одной из кромок, быстрого перемещения электрода по шву.
Поверхностное окисление – окисление металла шва и примыкающего к нему основного металла главным образом из-за сильно окисляющей среды, очень высокой мощности пламени сварочной горелки, большой длины дуги, слишком сильного сварочного тока, медленного перемещения электрода или горелки вдоль шва.
Поверхностные и внутренние поры являются результатом попадания в металлический шов различных газов, образующихся при сварке (азот, водород, углекислый газ и др.). Азот попадает в шов из атмосферного воздуха при недостаточно тщательной защите расплавленного металла в зоне сварки. Из компонентов покрытия электродов, воды и масла образуется водород. Оксид углерода возникает в процессе сварки стали при сгорании содержащегося в ней углерода. Дело в том, что при повышенном содержании углерода в электродах и свариваемой стали, а также при дефиците в сварочной ванне раскислителей и высокой скорости сварки оксид углерода не успевает улетучиться и остается в металле. Итак, пористость – итог неаккуратной подготовки свариваемых кромок (ржавчина, замасленность, загрязненность), недостатка раскислителей, использования влажного флюса, электродов с сырым покрытием и больших скоростей сварки.
Наружные и внутренние трещины (микротрещины) возникают главным образом в результате появляющихся в металле напряжений из-за его неравномерного нагревания, охлаждения и усадки. Легированные и высокоуглеродистые стали при охлаждении после сварки закаливаются; в результате этого могут появиться трещины. Высокое содержание в стали вредных примесей (серы и фосфора) также может вызвать образование трещин. Следует заметить, что наружные и внутренние трещины являются наиболее опасными и недопустимыми дефектами швов.
Дефекты подразделяются на внешние и внутренние. Причем внешние дефекты можно выявить путем осмотра невооруженным глазом или с помощью лупы с десятикратным увеличением, в то время как для установления внутренних дефектов требуется использование специальных методов: металлографические исследования, химический анализ, механические испытания, просвечивание рентгеновскими или гамма-лучами, магнитные и ультразвуковые методы контроля. Для выявления дефектов сварное соединение нужно предварительно очистить от шлака, окалины и металлических брызг.
К внешним дефектам относятся: нарушение размеров и формы шва, подрез зоны сплавления, прожог, наплыв, непровар, поверхностное окисление, незаваренные кратеры, поверхностные поры, продольные и поперечные трещины.
К внутренним дефектам относятся следующие: внутренние поры, непровар, неметаллические включения и микротрещины.
Нарушение размеров и форм шва проявляется в чрезмерном усилении и резких переходах от основного металла к наплавленному, а также в неполномерности высоты и ширины шва. При ручной сварке данные дефекты возникают в результате неаккуратной подготовки свариваемых кромок, неправильного выбора сварочного тока, невысокого качества сборки под сварку и низкой квалификации сварщика. Дефекты формы шва могут возникнуть и в результате колебания напряжения в сети при выполнении работы. При автоматизированной сварке нарушения размеров и формы швов могут быть из-за несоблюдения режима сварочного процесса (скорости сварки, скорости подачи электродов, сварочного тока) и неправильной разделки шва.
Подрез зоны сплавления выглядит в виде узкого углубления в основном металле вдоль края сварного шва. Этот дефект возникает при усиленной мощности горелки, при сварке удлиненной дугой, неправильном положении электрода или горелки и присадочного прутка, а также при сварке большим током.
Прожог представляет собой сквозное отверстие в сварном шве. Основные причины его возникновения следующие: малая толщина свариваемого металла, завышенная мощность пламени горелки, большой сварочный ток, незначительное притупление свариваемых кромок и неравномерный зазор между ними по расстоянию.
Наплыв – натекание металла шва на непрогретую поверхность свариваемого металла или прежде выполненного валика без сплавления с ним. Дефект возникает при некачественных электродах и несоответствии скорости сварки и сварочного тока разделке шва, а также при низкой квалификации сварщика.
Непровар проявляется в виде местного несплавления свариваемых кромок основного и наплавленного металлов и может быть результатом плохой подготовки свариваемых кромок (отсутствие зазора, большое притупление, незначительный угол скоса), смещения электрода к одной из кромок, быстрого перемещения электрода по шву.
Поверхностное окисление – окисление металла шва и примыкающего к нему основного металла главным образом из-за сильно окисляющей среды, очень высокой мощности пламени сварочной горелки, большой длины дуги, слишком сильного сварочного тока, медленного перемещения электрода или горелки вдоль шва.
Поверхностные и внутренние поры являются результатом попадания в металлический шов различных газов, образующихся при сварке (азот, водород, углекислый газ и др.). Азот попадает в шов из атмосферного воздуха при недостаточно тщательной защите расплавленного металла в зоне сварки. Из компонентов покрытия электродов, воды и масла образуется водород. Оксид углерода возникает в процессе сварки стали при сгорании содержащегося в ней углерода. Дело в том, что при повышенном содержании углерода в электродах и свариваемой стали, а также при дефиците в сварочной ванне раскислителей и высокой скорости сварки оксид углерода не успевает улетучиться и остается в металле. Итак, пористость – итог неаккуратной подготовки свариваемых кромок (ржавчина, замасленность, загрязненность), недостатка раскислителей, использования влажного флюса, электродов с сырым покрытием и больших скоростей сварки.
Наружные и внутренние трещины (микротрещины) возникают главным образом в результате появляющихся в металле напряжений из-за его неравномерного нагревания, охлаждения и усадки. Легированные и высокоуглеродистые стали при охлаждении после сварки закаливаются; в результате этого могут появиться трещины. Высокое содержание в стали вредных примесей (серы и фосфора) также может вызвать образование трещин. Следует заметить, что наружные и внутренние трещины являются наиболее опасными и недопустимыми дефектами швов.
Глава 13. Обустройство чердачного помещения
Чердак – это помещение, которое находится между крышей и верхним (чердачным) перекрытием здания. Как правило, в нем устанавливают водяные баки, прокладки разводных труб отопления и размещают сборные каналы и камеры вентиляции.
В индивидуальном доме проветривание чердака осуществляется через слуховые окна, а также через приточные отверстия под карнизом и вытяжные в коньке крыши. Данные приспособления призваны бороться с конденсатом, который образуется в результате проникновения влажного воздуха из кухни, санузлов и лестничных клеток.
Слуховые окна изобрел русский мастер Слухов, который, возглавляя артель, осуществлял строительство московского Манежа в 1824 г. При монтаже крыши мастер не предусмотрел устройства для проветривания чердака. После того как крыша накалилась на солнце, в чердачном помещении произошло расширение воздуха, что привело к деформации крыши. Об этом происшествии стало известно Александру I. Надо было срочно спасать положение. Слухов вернул крыше первоначальный вид, устроив на чердаке специальные окна для проветривания. Впоследствии они были названы слуховыми.
Чердачное пространство можно использовать для хозяйственных целей, например разместить в нем мастерскую. Для этого необходимо укрепить чердачное перекрытие, чтобы избежать его провисания. Кроме этого, надо позаботиться об освещении, которое может быть естественным и искусственным. Для обеспечения первого требуется устройство чердачных окон, для второго – электрическая проводка.
Чердак можно также оборудовать под помещение для сушки белья. Для этого следует предусмотреть наличие дополнительных вентиляционных устройств.
Чердачное помещение может служить в качестве кладовки для хранения различных материалов и инструментов.
Однако в последнее время развитие строительства, разработка рациональных планировочных решений, появление новых высококачественных материалов сделало возможным использование чердака в качестве жилого помещения.
В индивидуальном доме проветривание чердака осуществляется через слуховые окна, а также через приточные отверстия под карнизом и вытяжные в коньке крыши. Данные приспособления призваны бороться с конденсатом, который образуется в результате проникновения влажного воздуха из кухни, санузлов и лестничных клеток.
Слуховые окна изобрел русский мастер Слухов, который, возглавляя артель, осуществлял строительство московского Манежа в 1824 г. При монтаже крыши мастер не предусмотрел устройства для проветривания чердака. После того как крыша накалилась на солнце, в чердачном помещении произошло расширение воздуха, что привело к деформации крыши. Об этом происшествии стало известно Александру I. Надо было срочно спасать положение. Слухов вернул крыше первоначальный вид, устроив на чердаке специальные окна для проветривания. Впоследствии они были названы слуховыми.
Чердачное пространство можно использовать для хозяйственных целей, например разместить в нем мастерскую. Для этого необходимо укрепить чердачное перекрытие, чтобы избежать его провисания. Кроме этого, надо позаботиться об освещении, которое может быть естественным и искусственным. Для обеспечения первого требуется устройство чердачных окон, для второго – электрическая проводка.
Чердак можно также оборудовать под помещение для сушки белья. Для этого следует предусмотреть наличие дополнительных вентиляционных устройств.
Чердачное помещение может служить в качестве кладовки для хранения различных материалов и инструментов.
Однако в последнее время развитие строительства, разработка рациональных планировочных решений, появление новых высококачественных материалов сделало возможным использование чердака в качестве жилого помещения.
Планировка чердачного помещения
Прежде чем приступить к составлению плана обустройства чердачного помещения, необходимо решить, станет ли оно автономной квартирой или будет использоваться в качестве дополнительной жилой площади. В первом случае требуется определить степень пригодности чердака, которая зависит как от его размеров, так и от возможности размещения на нем приспособлений, необходимых для устройства кухни, ванной комнаты и туалета. Во втором случае конструирование пространства будет обусловлено архитектурными особенностями крыши (тип крыши, угол наклона скатов). Площадь чердака может быть неделимой, то есть полностью использоваться под гостиную, кабинет, детскую комнату.
Составление чертежной документации лучше поручить специалисту, который сумеет включить необходимые вспомогательные помещения (прихожие, коридоры и др.) в общее пространство. Самостоятельное планирование чердачного пространства может вызвать определенные трудности, обусловленные его ограниченной площадью.
Ниже приводится несколько вариантов обустройства чердачного помещения.
Составление чертежной документации лучше поручить специалисту, который сумеет включить необходимые вспомогательные помещения (прихожие, коридоры и др.) в общее пространство. Самостоятельное планирование чердачного пространства может вызвать определенные трудности, обусловленные его ограниченной площадью.
Ниже приводится несколько вариантов обустройства чердачного помещения.
Чердачная квартира с террасой на крыше
Оригинальность данного проекта (рис. 138) заключается в том, что площадь прихожей оказывается включенной в жилую зону. Спальная комната и прихожая имеют выход на террасу. Балконная дверь обеспечивает прекрасное естественное освещение прихожей.