Страница:
Так как металлические части имеются у всех ворот, то стоит позаботиться о предохранении металла от коррозии.
Самой элементарной защитной мерой является покрытие металла краской по поверхности, покрытой олифой. Перед окраской обязательно нужно снять ржавчину, иначе процесс коррозии металла будет продолжаться. Слой ржавчины можно снять старым дедовским способом, то есть напильником или наждачной шкуркой. Процесс этот долгий и трудоемкий.
Промышленность выпускает готовые химические составы для снятия ржавчины. Их можно приобрести в магазинах. Но такие составы готовят и самостоятельно, используя приведенные ниже рецепты.
1. В 1 л 15%-ного раствора соляной кислоты добавить 1 таблетку уротропина (гексаметилентетрамина). Данный раствор следует нанести на металлические детали ворот несколько раз, пока ржавчина не исчезнет и металлическая поверхность не будет чистой. Затем на металл нужно нанести 5–10%-ный раствор кальцинированной соды, который затем нужно тщательно смыть.
2. Для снятия ржавчины потребуются два раствора.
Раствор А. Концентрированный формальдегид следует смешать с 25%-ным раствором аммиака в объемном соотношении 8 : 5.
Раствор Б. В 15%-ный раствор соляной кислоты добавить уротропин из расчета 1 таблетка на 1 л раствора.
Далее эти растворы (А и Б) нужно смешать из расчета 26 мл раствора А на 1 л раствора Б. Дальнейшую обработку ворот нужно проводить, как и в первом случае.
3. Необходимы два раствора – А и Б.
А. Смешать 470 г соляной кислоты, 300 г воды, 1 таблетку уротропина и 40 г асбестовой крошки.
Б. Смешать 50 г жидкого стекла со 150 г воды.
Состав Б нужно влить в состав А, затем тщательно перемешать и выдержать в течение 18–20 ч. Обработку поверхности нужно проводить точно так же, как и в первых двух случаях.
Надежнее всего для окраски ворот использовать не краски, а асфальтовые, битумные и пековые лаки. Но они имеют черный цвет, что негативно влияет на внешний вид ворот.
Можно использовать кремнийорганическую, каучуковую, фенольную, винилхлоридную и некоторые другие виды красок. Если на их маркировке стоит цифра 1, то это означает, что они пригодны для наружных работ.
Устройство для защиты ворот от взлома
Полы
Глинобитные полы
Бетонные и цементно-песчаные полы
Мастичные полы
Полы из керамической плитки
Шлакоситалловое покрытие
Полы из крупноразмерных плит
Полы из гранита
Особенности устройства полов в зимнее время
Самой элементарной защитной мерой является покрытие металла краской по поверхности, покрытой олифой. Перед окраской обязательно нужно снять ржавчину, иначе процесс коррозии металла будет продолжаться. Слой ржавчины можно снять старым дедовским способом, то есть напильником или наждачной шкуркой. Процесс этот долгий и трудоемкий.
Промышленность выпускает готовые химические составы для снятия ржавчины. Их можно приобрести в магазинах. Но такие составы готовят и самостоятельно, используя приведенные ниже рецепты.
1. В 1 л 15%-ного раствора соляной кислоты добавить 1 таблетку уротропина (гексаметилентетрамина). Данный раствор следует нанести на металлические детали ворот несколько раз, пока ржавчина не исчезнет и металлическая поверхность не будет чистой. Затем на металл нужно нанести 5–10%-ный раствор кальцинированной соды, который затем нужно тщательно смыть.
2. Для снятия ржавчины потребуются два раствора.
Раствор А. Концентрированный формальдегид следует смешать с 25%-ным раствором аммиака в объемном соотношении 8 : 5.
Раствор Б. В 15%-ный раствор соляной кислоты добавить уротропин из расчета 1 таблетка на 1 л раствора.
Далее эти растворы (А и Б) нужно смешать из расчета 26 мл раствора А на 1 л раствора Б. Дальнейшую обработку ворот нужно проводить, как и в первом случае.
3. Необходимы два раствора – А и Б.
А. Смешать 470 г соляной кислоты, 300 г воды, 1 таблетку уротропина и 40 г асбестовой крошки.
Б. Смешать 50 г жидкого стекла со 150 г воды.
Состав Б нужно влить в состав А, затем тщательно перемешать и выдержать в течение 18–20 ч. Обработку поверхности нужно проводить точно так же, как и в первых двух случаях.
Надежнее всего для окраски ворот использовать не краски, а асфальтовые, битумные и пековые лаки. Но они имеют черный цвет, что негативно влияет на внешний вид ворот.
Можно использовать кремнийорганическую, каучуковую, фенольную, винилхлоридную и некоторые другие виды красок. Если на их маркировке стоит цифра 1, то это означает, что они пригодны для наружных работ.
Устройство для защиты ворот от взлома
Считается, что автомобиль, стоящий в гараже, надежно защищен от угона. Но это не совсем так. Ворота являются самым уязвимым местом гаража. При всех гарантиях, которые дает гаражный замок, нельзя быть окончательно уверенным в абсолютной защите машины от угона.
Угонщики могут проникнуть в гараж, воспользовавшись срезкой воротных петель и последующим снятием створок. Застраховаться от непрошеных гостей можно, применив несколько простых способов. Нужно лишить взломщика возможности срезать петли.
Петли ворот следует делать более массивными: это позволит увеличить площадь предполагаемого среза. Дополнительно нужно приварить с обеих сторон от петли специальные бобышки, которые представляют собой куски металлического прута (рис. 54).
Рис. 54. Общий вид бобышек, предохраняющих петли от среза
Диаметр бобышек и их длина должны быть не меньше, чем у самой петли, так как это позволяет не только увеличить площадь среза, но и значительно уменьшить рабочий ход ножовки.
Но и бобышки не дают полной гарантии безопасности ворот, ведь их могут срезать вместе с петлями, воспользовавшись газовой сваркой.
Установка специальных уголковых кронштейнов обеспечивает более надежную защиту от взлома гаража. Необязательно устанавливать кронштейны во время строительства гаража – это можно сделать в любое время, даже после многих лет эксплуатации.
Такие кронштейны необходимо приварить у каждой створки ворот сверху и снизу. Если ворота закрывать, то свободные, неприваренные стороны уголков сразу упрутся в каркас ворот. В местах опирания нужно сделать вырезы в каркасе и затем выдолбить в кирпичной кладке под ним углубление. В него и будет свободно входить уголок. Направление движения кронштейнов при открывании ворот показано стрелками на рисунке 55.
Рис. 55. Монтаж кронштейнов, предотвращающих открывание дверей: 1 – калитка; 2 – кронштейн калитки; 3 – каркас ворот; 4 – вырез в каркасе и кирпичной кладке на месте установки кронштейна; 5 – кронштейн створки ворот; 6 – кирпичная кладка
Точно такие же кронштейны можно установить на калитке, если таковая имеется в воротах.
Кронштейны надежно защитят ворота гаража от взлома и защита от коррозии им не потребуется.
Угонщики могут проникнуть в гараж, воспользовавшись срезкой воротных петель и последующим снятием створок. Застраховаться от непрошеных гостей можно, применив несколько простых способов. Нужно лишить взломщика возможности срезать петли.
Петли ворот следует делать более массивными: это позволит увеличить площадь предполагаемого среза. Дополнительно нужно приварить с обеих сторон от петли специальные бобышки, которые представляют собой куски металлического прута (рис. 54).
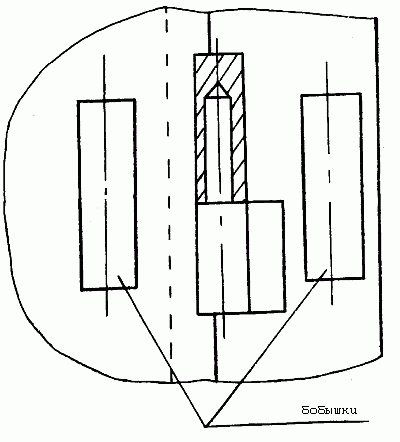
Диаметр бобышек и их длина должны быть не меньше, чем у самой петли, так как это позволяет не только увеличить площадь среза, но и значительно уменьшить рабочий ход ножовки.
Но и бобышки не дают полной гарантии безопасности ворот, ведь их могут срезать вместе с петлями, воспользовавшись газовой сваркой.
Установка специальных уголковых кронштейнов обеспечивает более надежную защиту от взлома гаража. Необязательно устанавливать кронштейны во время строительства гаража – это можно сделать в любое время, даже после многих лет эксплуатации.
Такие кронштейны необходимо приварить у каждой створки ворот сверху и снизу. Если ворота закрывать, то свободные, неприваренные стороны уголков сразу упрутся в каркас ворот. В местах опирания нужно сделать вырезы в каркасе и затем выдолбить в кирпичной кладке под ним углубление. В него и будет свободно входить уголок. Направление движения кронштейнов при открывании ворот показано стрелками на рисунке 55.
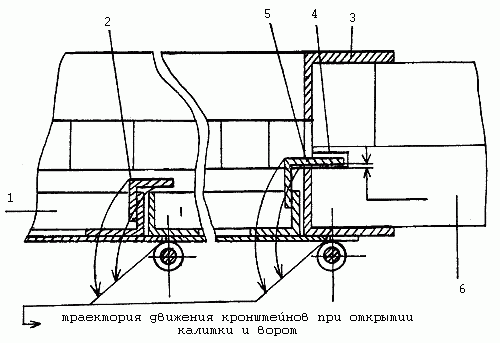
Точно такие же кронштейны можно установить на калитке, если таковая имеется в воротах.
Кронштейны надежно защитят ворота гаража от взлома и защита от коррозии им не потребуется.
Полы
Пол в гараже обязан соответствовать следующим требованиям: быть прочным, твердым и влагостойким. Поэтому в гараже лучше всего устроить глинобитный, бетонный, цементный или плиточный пол. Кроме этих, весьма распространенных, существуют и другие виды покрытий.
Глинобитные полы
Их делают из глины и щебня. Сначала площадку нужно очистить от мусора, затем засыпать всю площадь помещения слоем щебня. На щебень следует уложить слой глины и затем плотно утрамбовать, воспользовавшись небольшим катком (типа дорожно-строительного). При отсутствии катка его можно изготовить самому в домашних условиях. Для этого к металлическому цилиндру прикрепляют на подшипниках длинную ручку. Цилиндр должен быть достаточно тяжелым.
Бетонные и цементно-песчаные полы
Для них нужны бетонная смесь и цементно-песчаный раствор. Сначала грунт в гараже выравнивают, затем выкапывают в намеченном месте приямок для стока воды. Теперь можно приступить к устройству подстилающей подушки из щебня, гравия или шлака. Подушку желательно плотно утрамбовать. Бетонную смесь или цементно-песчаную стяжку рекомендуется наносить полосами шириной 1–1,5 м, двигаясь вдоль короткой стороны помещения. Такие полосы следует ограничить доской, поставленной на ребро; в дальнейшем она послужит маяком для выравнивания пола.
Для разравнивания лучше использовать деревянную рейку-правило.
Полы делаются с уклоном к трапу, который будет устроен в месте приямка. Можно одновременно забетонировать дно и стенки приямка (заранее нужно сделать опалубку из досок или горбыля). При желании полы утепляют, используя бетон, приготовленный на легких заполнителях, – керамзите, пемзе; используется и обыкновенный бетон, между слоями которого помещается засыпной утеплитель. Поверхность полов до начала схватывания раствора (которое наступает через 1–1,5 ч) нужно загладить теркой с металлическим полотном.
Для полов применяют бетон такого состава (в частях по объему): портландцемент марок 300–500 или пуццолановый цемент – 1; строительный песок – 3–3,8; щебень – 5–6,5; вода – 60–75 % от массы цемента (в зависимости от влажности песка и щебня).
При замене щебня на керамзит (или крошку пемзы) можно получить «теплый» бетон.
Для разравнивания лучше использовать деревянную рейку-правило.
Полы делаются с уклоном к трапу, который будет устроен в месте приямка. Можно одновременно забетонировать дно и стенки приямка (заранее нужно сделать опалубку из досок или горбыля). При желании полы утепляют, используя бетон, приготовленный на легких заполнителях, – керамзите, пемзе; используется и обыкновенный бетон, между слоями которого помещается засыпной утеплитель. Поверхность полов до начала схватывания раствора (которое наступает через 1–1,5 ч) нужно загладить теркой с металлическим полотном.
Для полов применяют бетон такого состава (в частях по объему): портландцемент марок 300–500 или пуццолановый цемент – 1; строительный песок – 3–3,8; щебень – 5–6,5; вода – 60–75 % от массы цемента (в зависимости от влажности песка и щебня).
При замене щебня на керамзит (или крошку пемзы) можно получить «теплый» бетон.
Мастичные полы
Такие полы представляют собой монолитную пленку из затвердевшего полимерного состава, которая и образует лицевую поверхность пола.
После подготовки основания под полы на него нужно нанести жидкую мастику. Нанесенную мастику разравнивают зубчатой рейкой до тех пор пока покрытие не приобретет необходимую толщину. Мастике следует дать затвердеть. После ее отвердения должно получиться ровное, гладкое покрытие без трещин и швов.
Нанесение мастики разделяют на два приема: нижний слой служит для выравнивания мелких неровностей основания, а верхний становится лицевой поверхностью пола.
Основанием мастичного пола будут служить стяжки из керамзито– и шлакобетона или раствора. Можно применить сборные железобетонные плиты, имеющие ровную поверхность.
Мастичные полы делятся на теплые и холодные. При укладке мастичного покрытия на стяжку из цементно-песчаного раствора или на поверхность железобетонной плиты перекрытия получается холодный пол. При стяжке из шлако-, керамзитобетона и других легких бетонов пол получается теплым.
Вид связующего материала влияет на качество полов, которые выполняются из мастик на их основе.
Мастичные полы на основе эпоксидной эмульсии отличаются большой прочностью и стойкостью к агрессивным химическим воздействиям. Эмульсия изготавливается из смеси эпоксидных и мочевиноформальдегидных смол с отвердителем, наполнителем и красителем. Такие полы будут весьма кстати в гараже.
Долговечность мастичных полов будет зависеть от того, насколько качественно подготовлено основание для них. Основание должно быть ровным, прочным и достаточно сухим: влажность не превышает 5%. В качестве основания можно использовать бетоны и растворы марки не ниже 150. Бетон следует уложить слоем толщиной 20–50 мм, который нужно уплотнить и загладить. Необходимо сделать плинтусы, которые будут ограничивать площадь пола с нанесенной мастикой.
Материалом плинтуса будет служить цементно-песчаная смесь состава 1 : 3. Смесь затворяют дисперсией ПВА, приготовленной из одной части клея и трех частей вводы.
Монолитность и целостность стяжки можно проверить простукиванием. Появление глухого стука означает наличие дефектного места. Это место нужно разрушить, убрать остатки цементной крошки и пыли и загрунтовать его цементным молоком, затем заделать раствором поверхность вровень с окружающим основанием.
Соединительный шов будет не так заметен, если в местах сопряжения уплотнить и сгладить раствор.
Раствором заделывают все раковины и западающие места глубиной более 10 мм, предварительно очистив их от пыли и прогрунтовав цементным молоком. Впадины и трещины глубиной до 10 мм заделывают полимерцементным раствором, перед этим очистив от пыли и прогрунтовав 10%-ным водным раствором ПВА. Полимерцементный раствор изготавливают из сухой цементно-песчаной смеси марки 150 и пластифицированной дисперсии ПВА, которую разбавляют водой в отношении 1 : 4.
Не всегда основание получается идеально ровным: часто оно содержит много трещин, выемок, раковин и прочих дефектов. В таком случае его необходимо выровнять слоем полимерцементного раствора толщиной 10–15 мм. Контроль горизонтальности основания проверяется специальной двухметровой рейкой. Зазоры между полом и рейкой не должны превышать 2 мм.
Основание следует предварительно очистить от мусора и обеспылить с помощью пылесоса или волосяной щетки.
Влажность основания не должна превышать 5%, так как при излишней влажности прочность сцепления мастики с поверхностью основания может снизиться и время ее окончательного отвердения значительно удлинится.
Затем основание нужно загрунтовать 10%-ным водным раствором дисперсии ПВА и нанести по просохшей грунтовке сплошной слой поливинилацетатной шпатлевки. Ее наносят с помощью шпателя с длинной ручкой слоем толщиной до 0,5 мм, заделывая каверны глубиной до 5 мм.
Консистенция шпатлевки должна напоминать густую сметану. Состав ее (в частях) следующий: 1 часть портланд-цемента марки 400, 4 части мелкого песка с размером зерен до 0,25 мм, 1/4 части – щелочестойкий пигмент.
Зашпатлеванную поверхность нужно отшлифовать и выдержать 1–2 сут, после чего начать устройство самого мастичного пола. На подсохшую зашпатлеванную поверхность следует нанести выравнивающий слой, для которого лучше применить мастику более жесткого состава, содержащую большое количество наполнителя. Стены лучше закрыть щитами или другим материалом, так как при разбрызгивании мастики они могут испачкаться.
Толщина выравнивающего слоя должна быть в пределах 2–2,5 мм. Ее контроль производится с помощью металличе-ской линейки с делениями, которую погружают в еще незастывшую мастику. При нанесении мастики желательно следить за тем, чтобы на поверхности не появлялись пузыри, так как они высыхают быстрее, чем остальная масса, и нарушают однородность мастичного состава.
Высыхание слоя продолжается 6–8 ч, после чего его нужно выровнять, срезая бугорки ножом или шпателем, а впадинки заполнить мастикой того же цвета. После этого можно нанести лицевой слой покрытия. В этом случае подойдет более эластичная мастика, содержащая меньшее количество наполнителя. Толщина слоя должна находиться в пределах 1,2–1,3 мм.
Если почаще вентилировать помещение, то пол высохнет быстрее и через 5–7 дней он уже будет готов к эксплуатации. Низкая температура замедляет процесс подсыхания: он может длиться до 10 дней.
Со временем мастичные покрытия улучшают свои качества, так как из застывшей мастики испаряется вода и она становится более устойчивой к истиранию. Эластичность и упругость покрытия при этом сохраняются.
После подготовки основания под полы на него нужно нанести жидкую мастику. Нанесенную мастику разравнивают зубчатой рейкой до тех пор пока покрытие не приобретет необходимую толщину. Мастике следует дать затвердеть. После ее отвердения должно получиться ровное, гладкое покрытие без трещин и швов.
Нанесение мастики разделяют на два приема: нижний слой служит для выравнивания мелких неровностей основания, а верхний становится лицевой поверхностью пола.
Основанием мастичного пола будут служить стяжки из керамзито– и шлакобетона или раствора. Можно применить сборные железобетонные плиты, имеющие ровную поверхность.
Мастичные полы делятся на теплые и холодные. При укладке мастичного покрытия на стяжку из цементно-песчаного раствора или на поверхность железобетонной плиты перекрытия получается холодный пол. При стяжке из шлако-, керамзитобетона и других легких бетонов пол получается теплым.
Вид связующего материала влияет на качество полов, которые выполняются из мастик на их основе.
Мастичные полы на основе эпоксидной эмульсии отличаются большой прочностью и стойкостью к агрессивным химическим воздействиям. Эмульсия изготавливается из смеси эпоксидных и мочевиноформальдегидных смол с отвердителем, наполнителем и красителем. Такие полы будут весьма кстати в гараже.
Долговечность мастичных полов будет зависеть от того, насколько качественно подготовлено основание для них. Основание должно быть ровным, прочным и достаточно сухим: влажность не превышает 5%. В качестве основания можно использовать бетоны и растворы марки не ниже 150. Бетон следует уложить слоем толщиной 20–50 мм, который нужно уплотнить и загладить. Необходимо сделать плинтусы, которые будут ограничивать площадь пола с нанесенной мастикой.
Материалом плинтуса будет служить цементно-песчаная смесь состава 1 : 3. Смесь затворяют дисперсией ПВА, приготовленной из одной части клея и трех частей вводы.
Монолитность и целостность стяжки можно проверить простукиванием. Появление глухого стука означает наличие дефектного места. Это место нужно разрушить, убрать остатки цементной крошки и пыли и загрунтовать его цементным молоком, затем заделать раствором поверхность вровень с окружающим основанием.
Соединительный шов будет не так заметен, если в местах сопряжения уплотнить и сгладить раствор.
Раствором заделывают все раковины и западающие места глубиной более 10 мм, предварительно очистив их от пыли и прогрунтовав цементным молоком. Впадины и трещины глубиной до 10 мм заделывают полимерцементным раствором, перед этим очистив от пыли и прогрунтовав 10%-ным водным раствором ПВА. Полимерцементный раствор изготавливают из сухой цементно-песчаной смеси марки 150 и пластифицированной дисперсии ПВА, которую разбавляют водой в отношении 1 : 4.
Не всегда основание получается идеально ровным: часто оно содержит много трещин, выемок, раковин и прочих дефектов. В таком случае его необходимо выровнять слоем полимерцементного раствора толщиной 10–15 мм. Контроль горизонтальности основания проверяется специальной двухметровой рейкой. Зазоры между полом и рейкой не должны превышать 2 мм.
Основание следует предварительно очистить от мусора и обеспылить с помощью пылесоса или волосяной щетки.
Влажность основания не должна превышать 5%, так как при излишней влажности прочность сцепления мастики с поверхностью основания может снизиться и время ее окончательного отвердения значительно удлинится.
Затем основание нужно загрунтовать 10%-ным водным раствором дисперсии ПВА и нанести по просохшей грунтовке сплошной слой поливинилацетатной шпатлевки. Ее наносят с помощью шпателя с длинной ручкой слоем толщиной до 0,5 мм, заделывая каверны глубиной до 5 мм.
Консистенция шпатлевки должна напоминать густую сметану. Состав ее (в частях) следующий: 1 часть портланд-цемента марки 400, 4 части мелкого песка с размером зерен до 0,25 мм, 1/4 части – щелочестойкий пигмент.
Зашпатлеванную поверхность нужно отшлифовать и выдержать 1–2 сут, после чего начать устройство самого мастичного пола. На подсохшую зашпатлеванную поверхность следует нанести выравнивающий слой, для которого лучше применить мастику более жесткого состава, содержащую большое количество наполнителя. Стены лучше закрыть щитами или другим материалом, так как при разбрызгивании мастики они могут испачкаться.
Толщина выравнивающего слоя должна быть в пределах 2–2,5 мм. Ее контроль производится с помощью металличе-ской линейки с делениями, которую погружают в еще незастывшую мастику. При нанесении мастики желательно следить за тем, чтобы на поверхности не появлялись пузыри, так как они высыхают быстрее, чем остальная масса, и нарушают однородность мастичного состава.
Высыхание слоя продолжается 6–8 ч, после чего его нужно выровнять, срезая бугорки ножом или шпателем, а впадинки заполнить мастикой того же цвета. После этого можно нанести лицевой слой покрытия. В этом случае подойдет более эластичная мастика, содержащая меньшее количество наполнителя. Толщина слоя должна находиться в пределах 1,2–1,3 мм.
Если почаще вентилировать помещение, то пол высохнет быстрее и через 5–7 дней он уже будет готов к эксплуатации. Низкая температура замедляет процесс подсыхания: он может длиться до 10 дней.
Со временем мастичные покрытия улучшают свои качества, так как из застывшей мастики испаряется вода и она становится более устойчивой к истиранию. Эластичность и упругость покрытия при этом сохраняются.
Полы из керамической плитки
Они удобны тем, что обладают влагостойкостью и легко моются. Можно покрыть плиткой не всю поверхность пола, а только ту его часть, которая наиболее подвержена увлажнению.
Перед облицовкой пола плиткой следует провести ряд подготовительных работ. Сначала нужно очистить и обеспылить поверхность влажным способом. Горизонтальность пола проверяется с помощью строительного уровня и двухметровой рейки; при имеющихся отклонениях по горизонтали на поверхности следует уложить слой цементно-песчаного раствора, который исправит неровности.
По периметру стен нужно закрепить отметки уровня пола: для этого строительный уровень нужно установить на рейку поочередно вдоль каждой из стен. Положение воздушного пузырька на уровне должно находиться строго на нулевой отметке. После фиксации отметок на стене следует провести черту.
Горизонтальность настилаемого пола можно проверять по маячным плиткам. Их размещают в углах помещения на гипсовом растворе, выверив перпендикулярность двух смежных рядов по угольнику. По окончании настилки всего пола плитки должны быть удалены и заменены плитками на растворе.
Поверхность пола нужно обильно смочить водой, выдержать 5–6 ч и затем уже начинать работы по укладке плитки. Плитку кладут на цементно-песчаный раствор. Начинать кладку лучше с рядов, проходящих вдоль стен, в дальнейшем от них протянутся ряды плитки по направлению к выходу. Увлажненное основание пола нужно покрыть раствором, слой которого должен иметь толщину не более 1–1,5 см.
После этого тыльную сторону плитки следует смочить водой с помощью малярной кисти. Плитку нужно прижать к прослойке раствора и осадить до нужного уровня легкими постукиваниями ручкой лопатки или молотком через деревянный брусок. Избыток раствора, выступивший на стыках, нужно удалять и фиксировать величину шва гвоздиками одинакового диаметра или просто спичками, которые после укладки 10–15 плиток можно убрать.
Для того чтобы твердение раствора происходило быстро, стыки между плитками заполняются на 1/2 их глубины. Плитку, которая не умещается по размерам в конце ряда, нужно подрезать, применяя обычный стеклорез.
Горизонтальность плиточного пола можно проконтролировать строительным уровнем, установленным на двухметровую рейку.
Обнаруженные зазоры можно исправить, удалив осевшую плитку. Затем на это место нужно добавить раствор и установить ее на место. Прямолинейность стыков проверяется с помощью мастерка. При качественной работе при проведении ребром мастерка по шву он не должен цепляться за углы плиток.
После того как цементно-песчаный раствор наберет до-статочную прочность (а это происходит на 3–4-й день), стыки между плитками можно затереть.
Керамический пол имеет некоторые недостатки. К наиболее существенному из них относится низкое сопротивление удару. Так что ронять на него инструменты крайне нежелательно.
Перед облицовкой пола плиткой следует провести ряд подготовительных работ. Сначала нужно очистить и обеспылить поверхность влажным способом. Горизонтальность пола проверяется с помощью строительного уровня и двухметровой рейки; при имеющихся отклонениях по горизонтали на поверхности следует уложить слой цементно-песчаного раствора, который исправит неровности.
По периметру стен нужно закрепить отметки уровня пола: для этого строительный уровень нужно установить на рейку поочередно вдоль каждой из стен. Положение воздушного пузырька на уровне должно находиться строго на нулевой отметке. После фиксации отметок на стене следует провести черту.
Горизонтальность настилаемого пола можно проверять по маячным плиткам. Их размещают в углах помещения на гипсовом растворе, выверив перпендикулярность двух смежных рядов по угольнику. По окончании настилки всего пола плитки должны быть удалены и заменены плитками на растворе.
Поверхность пола нужно обильно смочить водой, выдержать 5–6 ч и затем уже начинать работы по укладке плитки. Плитку кладут на цементно-песчаный раствор. Начинать кладку лучше с рядов, проходящих вдоль стен, в дальнейшем от них протянутся ряды плитки по направлению к выходу. Увлажненное основание пола нужно покрыть раствором, слой которого должен иметь толщину не более 1–1,5 см.
После этого тыльную сторону плитки следует смочить водой с помощью малярной кисти. Плитку нужно прижать к прослойке раствора и осадить до нужного уровня легкими постукиваниями ручкой лопатки или молотком через деревянный брусок. Избыток раствора, выступивший на стыках, нужно удалять и фиксировать величину шва гвоздиками одинакового диаметра или просто спичками, которые после укладки 10–15 плиток можно убрать.
Для того чтобы твердение раствора происходило быстро, стыки между плитками заполняются на 1/2 их глубины. Плитку, которая не умещается по размерам в конце ряда, нужно подрезать, применяя обычный стеклорез.
Горизонтальность плиточного пола можно проконтролировать строительным уровнем, установленным на двухметровую рейку.
Обнаруженные зазоры можно исправить, удалив осевшую плитку. Затем на это место нужно добавить раствор и установить ее на место. Прямолинейность стыков проверяется с помощью мастерка. При качественной работе при проведении ребром мастерка по шву он не должен цепляться за углы плиток.
После того как цементно-песчаный раствор наберет до-статочную прочность (а это происходит на 3–4-й день), стыки между плитками можно затереть.
Керамический пол имеет некоторые недостатки. К наиболее существенному из них относится низкое сопротивление удару. Так что ронять на него инструменты крайне нежелательно.
Шлакоситалловое покрытие
Существуют типы покрытий, обладающие стойким сопротивлением удару. Одним из них является
шлакоситалловое.
Стеклокристаллический материал шлакоситалловых плиток обладает массой достоинств: он в 4 раза прочнее стекла, химически стоек, жаропрочен, не поглощает воду, к тому же плотность его весьма мала.
Плиты из шлакоситалла выпускают следующих размеров: листами длиной 600–2800 мм, шириной 300–900 мм, толщиной 8–10 мм и плитами двух типоразмеров – 300 х 300 х 10 и 600 х 600 х 15 мм. Цвет плит белый или серый.
Перед началом облицовки полов кислотоупорными плитками следует устроить грунтовку из жидкого стекла. Пол в помещении лучше не увлажнять, так как жидкое стекло растворимо в воде.
Сухую поверхность плиток нужно покрыть с тыльной стороны и по краям раствором жидкого стекла и затем приступить к укладке с минимальной толщиной шва.
Плиты укладываются на слой цементно-песчаного раствора следующего состава: цемент марки 200 или 300 – 1 часть, песок – 1,5–3 части.
Если используется прослойка из цемента, то перед укладкой поступают как обычно, то есть смачивают пол; если же его хотят сделать кислотоупорным, то основу грунтуют жидким стеклом. Здесь можно использовать силикатную мастику, приготовленную из жидкого стекла и наполнителя. В качестве наполнителя используется порошкообразный андезит или диабаз кремнефтористого натрия.
Укладку плит ведут ровными рядами, параллельными стенам помещения. Правильность укладки можно проверить, используя причальной шнур. Кладку плит пола начинают вести от стены, противоположной въезду в гараж.
Сначала на основание следует нанести раствор. Делается это в виде полосы, длина которой должна быть достаточной для укладки 6–8 плит одного ряда. Ширина полосы обычно больше ряда плит на 3–4 см. После укладки плит на раствор их нужно осаживать до полного заполнения швов раствором.
Горизонтальность пола проверяется с помощью постоянного перемещения двухметровой рейки. Смежные плиты не должны отличаться по высоте более чем на 1 мм, а просветы под рейкой – на 4 мм.
Стеклокристаллический материал шлакоситалловых плиток обладает массой достоинств: он в 4 раза прочнее стекла, химически стоек, жаропрочен, не поглощает воду, к тому же плотность его весьма мала.
Плиты из шлакоситалла выпускают следующих размеров: листами длиной 600–2800 мм, шириной 300–900 мм, толщиной 8–10 мм и плитами двух типоразмеров – 300 х 300 х 10 и 600 х 600 х 15 мм. Цвет плит белый или серый.
Перед началом облицовки полов кислотоупорными плитками следует устроить грунтовку из жидкого стекла. Пол в помещении лучше не увлажнять, так как жидкое стекло растворимо в воде.
Сухую поверхность плиток нужно покрыть с тыльной стороны и по краям раствором жидкого стекла и затем приступить к укладке с минимальной толщиной шва.
Плиты укладываются на слой цементно-песчаного раствора следующего состава: цемент марки 200 или 300 – 1 часть, песок – 1,5–3 части.
Если используется прослойка из цемента, то перед укладкой поступают как обычно, то есть смачивают пол; если же его хотят сделать кислотоупорным, то основу грунтуют жидким стеклом. Здесь можно использовать силикатную мастику, приготовленную из жидкого стекла и наполнителя. В качестве наполнителя используется порошкообразный андезит или диабаз кремнефтористого натрия.
Укладку плит ведут ровными рядами, параллельными стенам помещения. Правильность укладки можно проверить, используя причальной шнур. Кладку плит пола начинают вести от стены, противоположной въезду в гараж.
Сначала на основание следует нанести раствор. Делается это в виде полосы, длина которой должна быть достаточной для укладки 6–8 плит одного ряда. Ширина полосы обычно больше ряда плит на 3–4 см. После укладки плит на раствор их нужно осаживать до полного заполнения швов раствором.
Горизонтальность пола проверяется с помощью постоянного перемещения двухметровой рейки. Смежные плиты не должны отличаться по высоте более чем на 1 мм, а просветы под рейкой – на 4 мм.
Полы из крупноразмерных плит
Такие полы устраивают из бетонно-мозаичных плит с отшлифованной лицевой поверхностью. Их стандартные размеры – 400 х 400 х 35 мм. Перед грунтовкой основание под облицовку нужно очистить стальной щеткой, затем тщательно подмести или пропылесосить и затем увлажнить.
Далее основание нужно прогрунтовать цементным молоком. Потом можно приступать к разметке помещения. При его сложной конфигурации лучше всего провести первоначальную раскладку плит насухо. Это позволит точно узнать, сколько потребуется полномерных изделий.
Если нужны неполномерные плиты, то их получают, раскалывая вручную целые плиты. Для этого следует разметить место нанесения разреза на плите с обеих сторон и расколоть плиту надвое с помощью скарпеля и молотка. Арматурную сетку, находящуюся внутри, нужно разрубить зубилом.
Кладку неполномерных плит нужно вести, размещая их краем к стене, чтобы закрыть неровности плинтусом. Для контроля уровня следует разместить на поверхности пола временные плиты-маяки. Они располагаются на расстоянии 2 м друг от друга. По мере продвижения работы маяки нужно постепенно удалять.
Перед укладкой плиты на раствор ее тыльная поверхность смачивается водой. Это предохранит плиту от впитывания излишней влаги из раствора и придаст кладке повышенную прочность.
Кладку плит начинают от стены, противоположной входу, в направлении на себя. Ровные ряды получают, пользуясь шнуром-причалкой. Слой раствора тоже нужно выкладывать по причальному шнуру.
Обычно ширина слоя превышает ширину самих плит на 2–3 см. Его толщина должна составлять 2 см. Добиться выравнивания слоя можно, применяя правку по маячному шнуру или маячным рейкам.
После разравнивания раствора приступают к укладке бетонных плит. Шов между плитами выполняется минимальным.
После укладки плиту осаживают, используя молоток и деревянную прокладку. Ее площадь равняется площади примерно двух плит. Толщина растворного слоя после их осадки не должна превышать 1–1,5 см.
Качество проводимых облицовочных работ должно соответствовать следующим требованиям: толщина швов не долж-на превышать 6 мм, разница в высоте соседних плит – 1 мм. Межплиточные швы нужно заполнять сразу после укладки каждого ряда.
Чтобы повысить прочность пола, швы между плитками нужно заполнять полностью, то есть заподлицо с поверхно-стью покрытия. После укладки мозаично-бетонных плит помещение гаража выдерживают, не приступая к эксплуатации, еще 2–3 дня.
В течение этого времени должно произойти схватывание раствора прослойки и межплиточных швов. Облицованную поверхность покрывают влажными опилками; толщина слоя должна составлять 1,5–2 см. После протирки опилки можно смыть водой.
Далее основание нужно прогрунтовать цементным молоком. Потом можно приступать к разметке помещения. При его сложной конфигурации лучше всего провести первоначальную раскладку плит насухо. Это позволит точно узнать, сколько потребуется полномерных изделий.
Если нужны неполномерные плиты, то их получают, раскалывая вручную целые плиты. Для этого следует разметить место нанесения разреза на плите с обеих сторон и расколоть плиту надвое с помощью скарпеля и молотка. Арматурную сетку, находящуюся внутри, нужно разрубить зубилом.
Кладку неполномерных плит нужно вести, размещая их краем к стене, чтобы закрыть неровности плинтусом. Для контроля уровня следует разместить на поверхности пола временные плиты-маяки. Они располагаются на расстоянии 2 м друг от друга. По мере продвижения работы маяки нужно постепенно удалять.
Перед укладкой плиты на раствор ее тыльная поверхность смачивается водой. Это предохранит плиту от впитывания излишней влаги из раствора и придаст кладке повышенную прочность.
Кладку плит начинают от стены, противоположной входу, в направлении на себя. Ровные ряды получают, пользуясь шнуром-причалкой. Слой раствора тоже нужно выкладывать по причальному шнуру.
Обычно ширина слоя превышает ширину самих плит на 2–3 см. Его толщина должна составлять 2 см. Добиться выравнивания слоя можно, применяя правку по маячному шнуру или маячным рейкам.
После разравнивания раствора приступают к укладке бетонных плит. Шов между плитами выполняется минимальным.
После укладки плиту осаживают, используя молоток и деревянную прокладку. Ее площадь равняется площади примерно двух плит. Толщина растворного слоя после их осадки не должна превышать 1–1,5 см.
Качество проводимых облицовочных работ должно соответствовать следующим требованиям: толщина швов не долж-на превышать 6 мм, разница в высоте соседних плит – 1 мм. Межплиточные швы нужно заполнять сразу после укладки каждого ряда.
Чтобы повысить прочность пола, швы между плитками нужно заполнять полностью, то есть заподлицо с поверхно-стью покрытия. После укладки мозаично-бетонных плит помещение гаража выдерживают, не приступая к эксплуатации, еще 2–3 дня.
В течение этого времени должно произойти схватывание раствора прослойки и межплиточных швов. Облицованную поверхность покрывают влажными опилками; толщина слоя должна составлять 1,5–2 см. После протирки опилки можно смыть водой.
Полы из гранита
Рисунок пола составляют из различных по величине разноцветных прямоугольных элементов. Для их окончательной подгонки необходим специальный камнерезный станок, на котором можно изготавливать плиты нужной формы и размера.
Камни кладут встык, поэтому очень важна параллельность боковых граней стыкуемых между собой камней. Так как укладка каменного пола – процесс довольно трудоемкий, к нему следует отнестись весьма серьезно, ведь подобный пол рассчитан даже не на десятки, а на сотни лет.
Когда все необходимые инструменты и материалы приготовлены, приступают непосредственно к укладке бетонной стяжки под будущий пол.
Поверх утрамбованного грунта заливают жидкий керамзитобетонный раствор. После того как первый слой застынет, укладывают второй и тщательно выравнивают. Когда стяжка толщиной приблизительно 100–150 мм высохнет и будет готова, приступают к укладке каменных плит.
Природный камень, из многообразия которого чаще всего применяются для облицовки мрамор и гранит, хоть и кажется сверхпрочным, на самом деле – достаточно хрупкий материал и требует к себе деликатного отношения. Поэтому для работы выбирают плиты без трещин и выбоин, от этого напрямую зависит долговечность пола.
Чтобы плита была прочно и ровно уложена, делают специальную растворную подушку из песка и цемента (3 части песка на 3 части цемента). Для приготовления раствора используют просеянный песок. Цемент должен быть однородным и при сжатии его в кулаке как бы просачиваться сквозь пальцы. Воду добавляют в раствор до достижения консистенции густой сметаны, после чего приступают к работе.
Хорошо размешанный, однородный раствор укладывают мастерком на место, где предполагается разместить первую плиту. Начинают от угла помещения. При этом учитывают, что бордюрный стеновой камень должен быть расположен ниже уровня поверхности уложенной плиты. Гранитные плиты кладут впритык к стене.
Уложив первую плиту на подготовленную поверхность подушки, мягким постукиванием резиновой киянкой придают ей идеально горизонтальное положение, проверяя его с помощью уровня. Уложив таким образом несколько плит по двум соседним углам помещения, с помощью шнура, натянутого по верхней плоскости уложенных плит, производят укладку первого ряда.
Первый ряд вдоль стены выкладывают из одинаковых по форме и цвету камней. При работе с последующими рядами обязательно чередуют широкие и узкие прямоугольники и квадраты, чтобы добиться желаемого эффекта. Используя плиты различного цвета и формы, без особого труда составляют любой геометрический рисунок.
Укладку второго и последующих рядов также производят с помощью шнура и уровня. Если плиты имеют большой размер и трудно контролировать процесс укладки, натягивают два или три ряда параллельных шнуров. Это поможет ровнее уложить плиты и подогнать их друг к другу. Расстояние между смежными плитами должно быть минимальным.
На заключительном этапе укладки особенно важно правильно вырезать последние плиты.
Чтобы добиться нужного результата, металлической линейкой тщательно измеряют расстояние между уже уложенными плитами. Исходя из этих размеров, гранитную плитку нужного размера аккуратно отпиливают на станке.
Выложив слой подушки, ее разравнивают в углублении мастерком, закрепляют плиту в полу. Утрамбовывают поверхность плиты резиновой киянкой до строго горизонтального уровня и не наступают на уложенный пол в последующие 2 дня, пока раствор не схватится. После этого приступают к завершающему этапу.
Окончательная доводка пола осуществляется в три этапа.
1-й этап – тонким слоем заливают пол жидким цементным раствором и равномерно распределяют его в щели между плитами шваброй с резиновой насадкой. Необходимое условие – полное заполнение промежутков между плитами. После этого дают полу подсохнуть.
2-й этап – полностью очищают поверхность от цемента и грязи водой и опилками, затем сметают опилки обыкновенной щеткой.
3-й этап – отшлифовывают шероховатости, неровности, выступы на каменных плитах шлифовальной машинкой с мелкозернистым полировальным камнем. Это делают и в том случае, если использовались нешлифованные плиты.
Камни кладут встык, поэтому очень важна параллельность боковых граней стыкуемых между собой камней. Так как укладка каменного пола – процесс довольно трудоемкий, к нему следует отнестись весьма серьезно, ведь подобный пол рассчитан даже не на десятки, а на сотни лет.
Когда все необходимые инструменты и материалы приготовлены, приступают непосредственно к укладке бетонной стяжки под будущий пол.
Поверх утрамбованного грунта заливают жидкий керамзитобетонный раствор. После того как первый слой застынет, укладывают второй и тщательно выравнивают. Когда стяжка толщиной приблизительно 100–150 мм высохнет и будет готова, приступают к укладке каменных плит.
Природный камень, из многообразия которого чаще всего применяются для облицовки мрамор и гранит, хоть и кажется сверхпрочным, на самом деле – достаточно хрупкий материал и требует к себе деликатного отношения. Поэтому для работы выбирают плиты без трещин и выбоин, от этого напрямую зависит долговечность пола.
Чтобы плита была прочно и ровно уложена, делают специальную растворную подушку из песка и цемента (3 части песка на 3 части цемента). Для приготовления раствора используют просеянный песок. Цемент должен быть однородным и при сжатии его в кулаке как бы просачиваться сквозь пальцы. Воду добавляют в раствор до достижения консистенции густой сметаны, после чего приступают к работе.
Хорошо размешанный, однородный раствор укладывают мастерком на место, где предполагается разместить первую плиту. Начинают от угла помещения. При этом учитывают, что бордюрный стеновой камень должен быть расположен ниже уровня поверхности уложенной плиты. Гранитные плиты кладут впритык к стене.
Уложив первую плиту на подготовленную поверхность подушки, мягким постукиванием резиновой киянкой придают ей идеально горизонтальное положение, проверяя его с помощью уровня. Уложив таким образом несколько плит по двум соседним углам помещения, с помощью шнура, натянутого по верхней плоскости уложенных плит, производят укладку первого ряда.
Первый ряд вдоль стены выкладывают из одинаковых по форме и цвету камней. При работе с последующими рядами обязательно чередуют широкие и узкие прямоугольники и квадраты, чтобы добиться желаемого эффекта. Используя плиты различного цвета и формы, без особого труда составляют любой геометрический рисунок.
Укладку второго и последующих рядов также производят с помощью шнура и уровня. Если плиты имеют большой размер и трудно контролировать процесс укладки, натягивают два или три ряда параллельных шнуров. Это поможет ровнее уложить плиты и подогнать их друг к другу. Расстояние между смежными плитами должно быть минимальным.
На заключительном этапе укладки особенно важно правильно вырезать последние плиты.
Чтобы добиться нужного результата, металлической линейкой тщательно измеряют расстояние между уже уложенными плитами. Исходя из этих размеров, гранитную плитку нужного размера аккуратно отпиливают на станке.
Выложив слой подушки, ее разравнивают в углублении мастерком, закрепляют плиту в полу. Утрамбовывают поверхность плиты резиновой киянкой до строго горизонтального уровня и не наступают на уложенный пол в последующие 2 дня, пока раствор не схватится. После этого приступают к завершающему этапу.
Окончательная доводка пола осуществляется в три этапа.
1-й этап – тонким слоем заливают пол жидким цементным раствором и равномерно распределяют его в щели между плитами шваброй с резиновой насадкой. Необходимое условие – полное заполнение промежутков между плитами. После этого дают полу подсохнуть.
2-й этап – полностью очищают поверхность от цемента и грязи водой и опилками, затем сметают опилки обыкновенной щеткой.
3-й этап – отшлифовывают шероховатости, неровности, выступы на каменных плитах шлифовальной машинкой с мелкозернистым полировальным камнем. Это делают и в том случае, если использовались нешлифованные плиты.
Особенности устройства полов в зимнее время
Основное требование к цементному раствору: его температура не должна опускаться ниже 5° С. Исходя из этого в холодное время года для приготовления раствора лучше использовать теплую воду. Если это выполнить невозможно, то при работе в холодном помещении лучше применять сухие цементно-песчаные смеси, которые нужно затворить слегка подогретой водой.