Страница:
Продаются метчики в наборах из двух штук (черновой и чистовой) для нарезания резьбы с шагом (расстоянием между нитками-витками) до 3 мм или из трех штук (черновой, средний и чистовой) для нарезания резьбы с шагом свыше 3 мм. На всех метчиках заводской штамповкой указан диаметр. Для вращения метчика при нарезании резьбы используется
вороток(рис. 8, б) который надевается окном на квадрат метчика.
Для нарезания наружной резьбы применяются плашки(рис. 8, в, г) которые могут быть раздвижными (призматическими) и круглыми (лерки).
Раздвижные призматические плашки представляют собой квадрат, состоящий из двух полуплашек. Они изготавливаются для нарезания дюймовой и трубной резьбы диаметром от 1/8 до 2 дюймов, а для нарезания метрической резьбы – от 6 до 52 мм. В комплект, как правило, входит 4–5 пар. При работе раздвижная плашка вставляется в специальный вороток-плашкодержатель. Для того чтобы получить качественную резьбу без перекосов, хорошо иметь плашкодержатель с направляющим кольцом.
Круглые плашки могут быть цельными и разрезными. Стандарт диаметров круглых плашек для нарезания метрической резьбы – от 1 до 26 мм, для нарезания дюймовой и трубной резьбы – от 1/8 до 2 дюймов.
Разрезные круглые плашки имеют боковую прорезь размером от 0,5 до 1,5 мм, что позволяет регулировать диаметр резьбы в пределах 0,1–1,25 мм. Однако вследствие пониженной жесткости таких плашек, нарезаемая ими резьба может иметь неточный профиль. Круглые плашки (подобно раздвижным) во время работы вставляются в специальный вороток-плашкодержатель. Поскольку плашкодержатель для круглых плашек не снабжен направляющим кольцом, в ходе нарезания резьбы нужно следить, чтобы он не создавал перекоса.
Для сверления и обработки всевозможных отверстий понадобится электрическая дрельс набором сверл и других насадок (зенковок, шарошек, разводок).
Однако при сверлении электрической дрелью очень трудно получить качественное отверстие, обычно оно «уходит» в сторону. Избавиться от этого недостатка можно с помощью несложного приспособления, которое легко изготовить в домашней мастерской. Потребуется невысокая втулка с опорным фланцем, имеющая диаметр отверстия чуть больший, чем у сверла, так, чтобы оно вращалось в ней, не задевая стенок втулки.
На втулку нужно навить коническую пружину, широкой стороной оперев ее на фланец, а узкой (вершиной) направив в сторону дрели. Тогда при работе зажимное устройство дрели будет давить на пружину, которая передаст это усилие на фланец и плотно прижмет его к поверхности, где сверлится отверстие. Вероятность перекоса при работе с таким приспособлением сводится к нулю. (Этим же приспособлением можно пользоваться при нарезании внутренней резьбы метчиком.) Если у вас есть такая возможность, нужно обязательно установить в своей мастерской сверлильный станок, ибо качество обработки деталей с его помощью не идет ни в какое сравнение с качеством, полученным при работе дрелью, даже с использованием самых лучших приспособлений.
Практически любая металлическая деталь, изготовленная ручным способом в домашних условиях, требует опиливания, при котором излишний слой металла срезается напильником– стальным бруском с насечкой.
В зависимости от формы сечения напильники могут быть плоские, полукруглые, квадратные, трехгранные, круглые, ромбические (рис. 9).
Рис. 9. Наиболее распространенные напильники и их применение: а – плоский; б – полукруглый; в – квадратный; г – трехгранный; д – круглый.
По размерам различают напильники крупные (до 400 мм) и мелкие – надфили. Кроме того, напильники могут иметь одинарную (простую), двойную, рашпильную и дуговую насечки (рис. 10).
Рис. 10. Напильник: а – элементы напильника; б – способы насечки.
Простая (одинарная) насечка позволяет снимать широкую стружку по всей длине, поэтому основное применение таких инструментов – обработка заготовок из мягких металлов и сплавов (свинца, латуни, бронзы, меди и др.). Помимо этого, такие напильники используются для заточки пил. Напильники с двойной насечкой применяются для обработки стальных, чугунных заготовок и деталей из твердых сплавов.
Рашпильная насечка представляет собой пирамидальные выступы и канавки, расположенные в шахматном порядке, в результате чего образуются довольно крупные и редкие зубья. Напильники с рашпильной насечкой предназначены для черновой обработки мягких материалов.
Дуговая насечка имеет большую, по сравнению с другими, стойкость.
У многих напильников с дуговой насечкой шаг неодинаков, благодаря чему ими можно одновременно снимать крупную и мелкую стружку. Поэтому поверхность заготовки, обработанная таким напильником, получается более чистой. В зависимости от величины насечек и шага между ними, все напильники делятся на шесть номеров.
№ 0 – брусовки – напильники, имеющие очень крупную насечку для грубой обработки со снятием большого слоя металла.
№ 1 – драчевые напильники для менее грубой обработки (спиливание припусков, снятие фасок, заусенцев и т. д.).
№ 2–4 – личные напильники для обработки и отделки металла после применения драчевого напильника.
№ 5 – бархатные напильники для самой точной обработки и доводки поверхностей.
Для удобства работы на хвостовик напильника рекомендуется надеть рукоятку из древесины (березы, ясеня, клена).
Для точных специальных работ применяются напильники с очень мелкой насечкой – надфили. С их помощью выполняют лекальные, граверные, ювелирные работы, зачистку в труднодоступных местах матриц, мелких отверстий, профильных участков изделия и т. п.
Материалом для напильников всех видов является углеродистая инструментальная сталь, начиная с марок У7 или У7А и кончая марками У13 или У13А.
Увеличение срока службы напильника обеспечивается правильным его использованием и уходом за ним. Так, например, нельзя обрабатывать напильником материалы, твердость которых превышает твердость самого инструмента. Новым напильником сначала следует обрабатывать мягкие металлы, а после некоторого затупления – более твердые. Нельзя ударять по напильникам: из-за хрупкости они могут давать трещины и ломаться. Не следует класть напильник на металлические предметы: это может привести к выпадению зубьев.
В процессе слесарных работ (чаще при сборке) сопрягаемые детали для более плотного прилегания друг к другу требуют подгонки плоскостей. Эта операция называется шабрением и выполняется с помощью шаберов(рис. 11).
Рис. 11. Шаберы: а – плоский; б – со вставной пластинкой из твердого сплава; в – трехгранные; г – двухгранные (скребки); д – фасонные.
Они изготавливаются из инструментальных, легированных сталей или твердых сплавов. Рабочая (режущая) часть шабера может быть плоской с радиусом закругления по торцу, трехгранной с боковыми пазами, двухгранной (скребки) или фасонной с выпуклыми радиусами на рабочем профиле. Плоские шаберы применяются для чернового шабрения, фасонные шаберы и шаберы-скребки – для шабрения поверхностей в труднодоступных местах.
Подобно всем рубяще-режущим инструментам, шаберы нуждаются в своевременной заточке на электрокорундовом круге и доводке на абразивных брусках зернистостью 90 и выше (предварительно смазанных машинным маслом) или на чугунной плите с применением пасты из наждачного порошка.
Для чистовой обработки деталей (а также для очистки поверхностей от окалины, краски и пр. перед слесарной обработкой) применяются различные проволочные щетки,изготовленные из проволоки (незакаленной, закаленной, малоуглеродистой стали, цветных металлов) (рис. 12).
Рис. 12. Типы щеток: а – щеточная секция; б – щетка для зачистных операций; в – щетка из отдельных проволочных жгутов.
Диаметр щеток может быть от 30 до 500 мм, причем чем больше диаметр, тем выше окружная скорость, и, соответственно, выше производительность. Ширина рабочей поверхности также различна: от 15 до 300 мм. Неодинакова и толщина проволоки, из которой изготавливается щетка: она варьируется от 0,1 до 0,3 мм. При выборе щетки для конкретного материала следует учитывать, что чем толще проволока, тем грубее получается отделка поверхности.
Для приведения щеток в рабочее состояние (вращение) можно использовать станок для заточки инструмента, заменив абразивный круг щеткой, или переносной шлифовальный станок, или обычную электродрель.
Слесарно-сборочные инструменты
Свойства металлов и сплавов
Железо
Медь и сплавы
Для нарезания наружной резьбы применяются плашки(рис. 8, в, г) которые могут быть раздвижными (призматическими) и круглыми (лерки).
Раздвижные призматические плашки представляют собой квадрат, состоящий из двух полуплашек. Они изготавливаются для нарезания дюймовой и трубной резьбы диаметром от 1/8 до 2 дюймов, а для нарезания метрической резьбы – от 6 до 52 мм. В комплект, как правило, входит 4–5 пар. При работе раздвижная плашка вставляется в специальный вороток-плашкодержатель. Для того чтобы получить качественную резьбу без перекосов, хорошо иметь плашкодержатель с направляющим кольцом.
Круглые плашки могут быть цельными и разрезными. Стандарт диаметров круглых плашек для нарезания метрической резьбы – от 1 до 26 мм, для нарезания дюймовой и трубной резьбы – от 1/8 до 2 дюймов.
Разрезные круглые плашки имеют боковую прорезь размером от 0,5 до 1,5 мм, что позволяет регулировать диаметр резьбы в пределах 0,1–1,25 мм. Однако вследствие пониженной жесткости таких плашек, нарезаемая ими резьба может иметь неточный профиль. Круглые плашки (подобно раздвижным) во время работы вставляются в специальный вороток-плашкодержатель. Поскольку плашкодержатель для круглых плашек не снабжен направляющим кольцом, в ходе нарезания резьбы нужно следить, чтобы он не создавал перекоса.
Для сверления и обработки всевозможных отверстий понадобится электрическая дрельс набором сверл и других насадок (зенковок, шарошек, разводок).
Однако при сверлении электрической дрелью очень трудно получить качественное отверстие, обычно оно «уходит» в сторону. Избавиться от этого недостатка можно с помощью несложного приспособления, которое легко изготовить в домашней мастерской. Потребуется невысокая втулка с опорным фланцем, имеющая диаметр отверстия чуть больший, чем у сверла, так, чтобы оно вращалось в ней, не задевая стенок втулки.
На втулку нужно навить коническую пружину, широкой стороной оперев ее на фланец, а узкой (вершиной) направив в сторону дрели. Тогда при работе зажимное устройство дрели будет давить на пружину, которая передаст это усилие на фланец и плотно прижмет его к поверхности, где сверлится отверстие. Вероятность перекоса при работе с таким приспособлением сводится к нулю. (Этим же приспособлением можно пользоваться при нарезании внутренней резьбы метчиком.) Если у вас есть такая возможность, нужно обязательно установить в своей мастерской сверлильный станок, ибо качество обработки деталей с его помощью не идет ни в какое сравнение с качеством, полученным при работе дрелью, даже с использованием самых лучших приспособлений.
Практически любая металлическая деталь, изготовленная ручным способом в домашних условиях, требует опиливания, при котором излишний слой металла срезается напильником– стальным бруском с насечкой.
В зависимости от формы сечения напильники могут быть плоские, полукруглые, квадратные, трехгранные, круглые, ромбические (рис. 9).
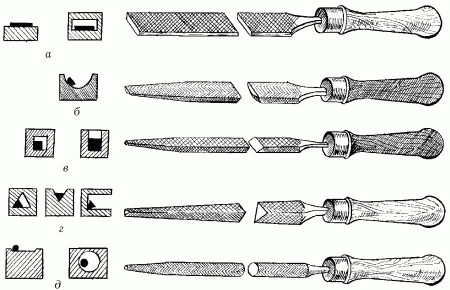
По размерам различают напильники крупные (до 400 мм) и мелкие – надфили. Кроме того, напильники могут иметь одинарную (простую), двойную, рашпильную и дуговую насечки (рис. 10).
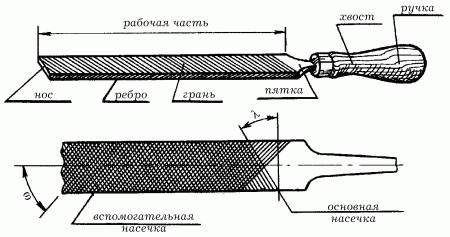
Простая (одинарная) насечка позволяет снимать широкую стружку по всей длине, поэтому основное применение таких инструментов – обработка заготовок из мягких металлов и сплавов (свинца, латуни, бронзы, меди и др.). Помимо этого, такие напильники используются для заточки пил. Напильники с двойной насечкой применяются для обработки стальных, чугунных заготовок и деталей из твердых сплавов.
Рашпильная насечка представляет собой пирамидальные выступы и канавки, расположенные в шахматном порядке, в результате чего образуются довольно крупные и редкие зубья. Напильники с рашпильной насечкой предназначены для черновой обработки мягких материалов.
Дуговая насечка имеет большую, по сравнению с другими, стойкость.
У многих напильников с дуговой насечкой шаг неодинаков, благодаря чему ими можно одновременно снимать крупную и мелкую стружку. Поэтому поверхность заготовки, обработанная таким напильником, получается более чистой. В зависимости от величины насечек и шага между ними, все напильники делятся на шесть номеров.
№ 0 – брусовки – напильники, имеющие очень крупную насечку для грубой обработки со снятием большого слоя металла.
№ 1 – драчевые напильники для менее грубой обработки (спиливание припусков, снятие фасок, заусенцев и т. д.).
№ 2–4 – личные напильники для обработки и отделки металла после применения драчевого напильника.
№ 5 – бархатные напильники для самой точной обработки и доводки поверхностей.
Для удобства работы на хвостовик напильника рекомендуется надеть рукоятку из древесины (березы, ясеня, клена).
Для точных специальных работ применяются напильники с очень мелкой насечкой – надфили. С их помощью выполняют лекальные, граверные, ювелирные работы, зачистку в труднодоступных местах матриц, мелких отверстий, профильных участков изделия и т. п.
Материалом для напильников всех видов является углеродистая инструментальная сталь, начиная с марок У7 или У7А и кончая марками У13 или У13А.
Увеличение срока службы напильника обеспечивается правильным его использованием и уходом за ним. Так, например, нельзя обрабатывать напильником материалы, твердость которых превышает твердость самого инструмента. Новым напильником сначала следует обрабатывать мягкие металлы, а после некоторого затупления – более твердые. Нельзя ударять по напильникам: из-за хрупкости они могут давать трещины и ломаться. Не следует класть напильник на металлические предметы: это может привести к выпадению зубьев.
В процессе слесарных работ (чаще при сборке) сопрягаемые детали для более плотного прилегания друг к другу требуют подгонки плоскостей. Эта операция называется шабрением и выполняется с помощью шаберов(рис. 11).
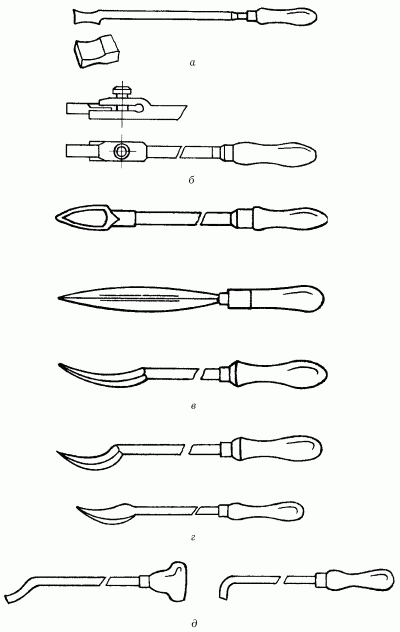
Они изготавливаются из инструментальных, легированных сталей или твердых сплавов. Рабочая (режущая) часть шабера может быть плоской с радиусом закругления по торцу, трехгранной с боковыми пазами, двухгранной (скребки) или фасонной с выпуклыми радиусами на рабочем профиле. Плоские шаберы применяются для чернового шабрения, фасонные шаберы и шаберы-скребки – для шабрения поверхностей в труднодоступных местах.
Подобно всем рубяще-режущим инструментам, шаберы нуждаются в своевременной заточке на электрокорундовом круге и доводке на абразивных брусках зернистостью 90 и выше (предварительно смазанных машинным маслом) или на чугунной плите с применением пасты из наждачного порошка.
Для чистовой обработки деталей (а также для очистки поверхностей от окалины, краски и пр. перед слесарной обработкой) применяются различные проволочные щетки,изготовленные из проволоки (незакаленной, закаленной, малоуглеродистой стали, цветных металлов) (рис. 12).
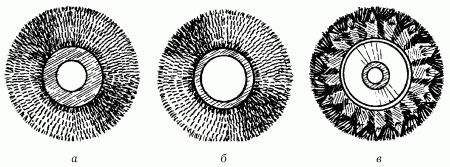
Диаметр щеток может быть от 30 до 500 мм, причем чем больше диаметр, тем выше окружная скорость, и, соответственно, выше производительность. Ширина рабочей поверхности также различна: от 15 до 300 мм. Неодинакова и толщина проволоки, из которой изготавливается щетка: она варьируется от 0,1 до 0,3 мм. При выборе щетки для конкретного материала следует учитывать, что чем толще проволока, тем грубее получается отделка поверхности.
Для приведения щеток в рабочее состояние (вращение) можно использовать станок для заточки инструмента, заменив абразивный круг щеткой, или переносной шлифовальный станок, или обычную электродрель.
Слесарно-сборочные инструменты
Выбор слесарно-сборочного инструмента зависит от вида крепления деталей.
Резьбовые соединения деталей осуществляются с помощью всевозможных ключей и отверток (рис. 13).
Рис. 13. Ручной инструмент для сборки резьбовых соединений. Ключи: а – односторонний; б – двухсторонний; в – накладной; г – разводной; д – накидной открытый для круглых гаек; е – накидной закрытый для круглых гаек; ж – торцовый; з – торцовый шарнирный.
Рис. 13 (продолжение). Ручной инструмент для сборки резьбовых соединений. Ключи: и – коловоротный. Отвертки: к – коловоротная; л – воротковая; м – с направляющей втулкой; н – реверсивная; о – обычная.
Ключи(рис. 13, а-и) служат для завертывания винтов и гаек: одно– и двусторонние, накладные, накидные и коловоротные используются для соединения в доступных местах; торцовые – для труднодоступных мест; разводной ключ используется для соединения труб с помощью сгонов, муфт, уголков и тройников при прокладке трубопроводов и установке сантехнического оборудования. Все ключи имеют свои номера, которые соответствуют размерам завертываемых гаек и диаметрам головок винтов. Для завертывания шурупов и винтов, головки которых имеют прорези (шлицы), применяются отвертки(рис. 13, к-о). Их жало (лезвие) может быть плоским или крестообразным и различным по величине.
Реверсивная отвертка изготавливается, как правило, со сменными насадками, среди которых имеются не только отвертки, но и торцовые ключи. Пантовый зажим на рукоятке такой отвертки позволяет быстро менять рабочий инструмент.
Реверсивной отверткой можно пользоваться не только для завертывания шурупов, винтов, но и для их выкручивания (отсюда и название).
Помимо изображенных на рисунке отверток, существует еще множество их разновидностей: отвертка с держателем, которая удерживает винт или шуруп до завертывания первых нескольких нитей резьбы; отвертка с шарнирно закрепленным лезвием, что облегчает работу в труднодоступных местах, и пр.
Но это довольно специфические инструменты, и в домашней мастерской они могут использоваться достаточно редко.
Для получения неразъемных соединений во время сборки различных механизмов и конструкций применяются такие виды сборки, как заклепочная сварка, пайка и сварка. Соответственно, для выполнения этих операций необходимы следующие приспособления: пневмозаклепочная головка (но для ее работы необходим сжатый воздух, поэтому в домашних условиях для заклепывания можно использовать молоток и специальные обжимки, однако в этом случае получается довольно непрочное соединение); электропаяльник или металлический паяльник с паяльной лампой; сварочный аппарат.
На этом перечень инструментов необходимых домашнему слесарю, можно закончить. Сведения о тех инструментах, которые не попали в этот список, но, возможно, потребуются для выполнения отдельных слесарных операций, можно найти в разделах, посвященных ознакомлению с техникой выполнения отдельных видов работ.
Резьбовые соединения деталей осуществляются с помощью всевозможных ключей и отверток (рис. 13).
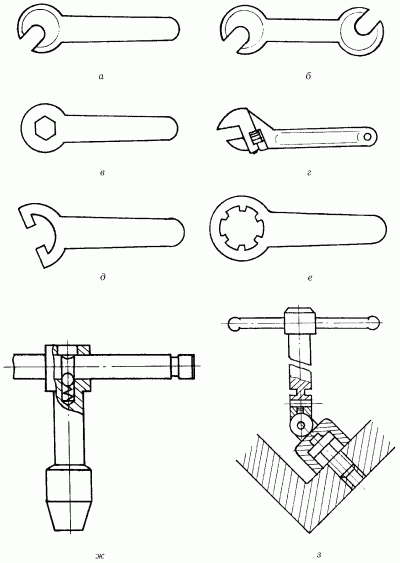
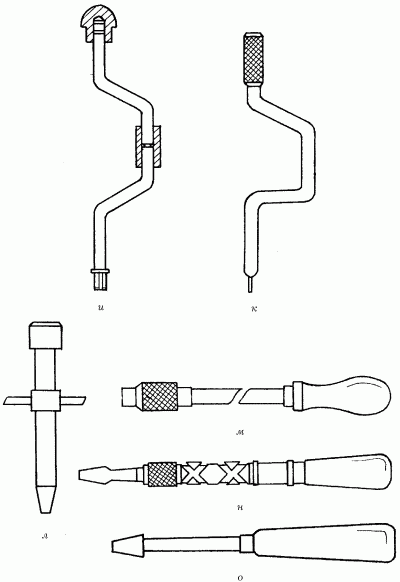
Ключи(рис. 13, а-и) служат для завертывания винтов и гаек: одно– и двусторонние, накладные, накидные и коловоротные используются для соединения в доступных местах; торцовые – для труднодоступных мест; разводной ключ используется для соединения труб с помощью сгонов, муфт, уголков и тройников при прокладке трубопроводов и установке сантехнического оборудования. Все ключи имеют свои номера, которые соответствуют размерам завертываемых гаек и диаметрам головок винтов. Для завертывания шурупов и винтов, головки которых имеют прорези (шлицы), применяются отвертки(рис. 13, к-о). Их жало (лезвие) может быть плоским или крестообразным и различным по величине.
Реверсивная отвертка изготавливается, как правило, со сменными насадками, среди которых имеются не только отвертки, но и торцовые ключи. Пантовый зажим на рукоятке такой отвертки позволяет быстро менять рабочий инструмент.
Реверсивной отверткой можно пользоваться не только для завертывания шурупов, винтов, но и для их выкручивания (отсюда и название).
Помимо изображенных на рисунке отверток, существует еще множество их разновидностей: отвертка с держателем, которая удерживает винт или шуруп до завертывания первых нескольких нитей резьбы; отвертка с шарнирно закрепленным лезвием, что облегчает работу в труднодоступных местах, и пр.
Но это довольно специфические инструменты, и в домашней мастерской они могут использоваться достаточно редко.
Для получения неразъемных соединений во время сборки различных механизмов и конструкций применяются такие виды сборки, как заклепочная сварка, пайка и сварка. Соответственно, для выполнения этих операций необходимы следующие приспособления: пневмозаклепочная головка (но для ее работы необходим сжатый воздух, поэтому в домашних условиях для заклепывания можно использовать молоток и специальные обжимки, однако в этом случае получается довольно непрочное соединение); электропаяльник или металлический паяльник с паяльной лампой; сварочный аппарат.
На этом перечень инструментов необходимых домашнему слесарю, можно закончить. Сведения о тех инструментах, которые не попали в этот список, но, возможно, потребуются для выполнения отдельных слесарных операций, можно найти в разделах, посвященных ознакомлению с техникой выполнения отдельных видов работ.
Свойства металлов и сплавов
В этой главе будет рассказано о металлах, сплавах и их свойствах, что полезно не только для мастеров слесарного дела, но для всех, кто занимается чеканкой, ковкой, художественным литьем (этому посвящены последующие главы).
Металл относится к таким материалам, которые нельзя встретить в природе в готовом виде. Поэтому, чтобы получить его из богатых природных кладовых, нужно иметь большие знания и опыт в столь нелегком деле. Металлы бывают разные. В таблице Менделеева металлические элементы насчитываются десятками; конструкторы, техники могут назвать сотни необходимых им марок сталей, сплавов и т. п.; ученые соединяют широко распространенные и редчайшие металлы в тысячи сочетаний.
Между тем еще не так уж давно, лет триста назад, по научной классификации насчитывалось всего семь основных металлов: золото, серебро, медь, олово, свинец, ртуть и железо. Именно развитие ремесел было причиной появления новых сплавов, проведения исследований и опытов: умельцам нужны были материалы с определенными свойствами. Кому – твердая и прочная сталь для оружия, кому – мягкие и не теряющие блеска металлы для украшений, которые были бы дешевле золота.
Даже древних фальшивомонетчиков можно считать металлургами. Полученные ими в корыстных целях сплавы меди до сих пор широко используются не только в ювелирном деле, но и в самой современной технике.
Сейчас все металлы принято делить на черные и цветные. Черные – это различные металлические соединения и сплавы железа. Наиболее распространены из них чугун и сталь. Именно черные металлы составляют 95 % всей продукции мировой металлургии. Впрочем, по прогнозам некоторых ученых, эта цифра может существенно уменьшиться: развитие техники может сделать XXI век не «железным», а скорее «алюминиево-титаново-пластиковым». Все большее распространение получают легкие и прочные сплавы, композитные и синтетические материалы. Однако народным умельцам скорее всего и через сто лет придется иметь дело с «железками». Сталь, в зависимости от марок и добавок, может иметь самые различные свойства, достаточно хорошо обрабатывается и не слишком дорого стоит.
Цветные металлы – это все металлы, кроме железа, и их сплавы. Данная группа очень многочисленная, классифицируют ее по различным признакам (залегание в земной коре, химические и физические свойства и т. д.). Но нас интересуют лишь немногие металлы. С благородными, или драгоценными, металлами (золото, серебро, платина и т. д.) в нашей стране имеют дело в основном специалисты-ювелиры. Тугоплавкие металлы (титан, вольфрам, молибден и т. д.) в домашних условиях обработать невозможно. Поэтому наибольший интерес представляют достаточно распространенные: алюминий, медь, свинец и различные сплавы на их основе. Рассмотрим подробнее металлы, с которыми имеют дело те, кто занимается слесарным делом, ковкой, чеканкой, художественным литьем и т. п.
Металл относится к таким материалам, которые нельзя встретить в природе в готовом виде. Поэтому, чтобы получить его из богатых природных кладовых, нужно иметь большие знания и опыт в столь нелегком деле. Металлы бывают разные. В таблице Менделеева металлические элементы насчитываются десятками; конструкторы, техники могут назвать сотни необходимых им марок сталей, сплавов и т. п.; ученые соединяют широко распространенные и редчайшие металлы в тысячи сочетаний.
Между тем еще не так уж давно, лет триста назад, по научной классификации насчитывалось всего семь основных металлов: золото, серебро, медь, олово, свинец, ртуть и железо. Именно развитие ремесел было причиной появления новых сплавов, проведения исследований и опытов: умельцам нужны были материалы с определенными свойствами. Кому – твердая и прочная сталь для оружия, кому – мягкие и не теряющие блеска металлы для украшений, которые были бы дешевле золота.
Даже древних фальшивомонетчиков можно считать металлургами. Полученные ими в корыстных целях сплавы меди до сих пор широко используются не только в ювелирном деле, но и в самой современной технике.
Сейчас все металлы принято делить на черные и цветные. Черные – это различные металлические соединения и сплавы железа. Наиболее распространены из них чугун и сталь. Именно черные металлы составляют 95 % всей продукции мировой металлургии. Впрочем, по прогнозам некоторых ученых, эта цифра может существенно уменьшиться: развитие техники может сделать XXI век не «железным», а скорее «алюминиево-титаново-пластиковым». Все большее распространение получают легкие и прочные сплавы, композитные и синтетические материалы. Однако народным умельцам скорее всего и через сто лет придется иметь дело с «железками». Сталь, в зависимости от марок и добавок, может иметь самые различные свойства, достаточно хорошо обрабатывается и не слишком дорого стоит.
Цветные металлы – это все металлы, кроме железа, и их сплавы. Данная группа очень многочисленная, классифицируют ее по различным признакам (залегание в земной коре, химические и физические свойства и т. д.). Но нас интересуют лишь немногие металлы. С благородными, или драгоценными, металлами (золото, серебро, платина и т. д.) в нашей стране имеют дело в основном специалисты-ювелиры. Тугоплавкие металлы (титан, вольфрам, молибден и т. д.) в домашних условиях обработать невозможно. Поэтому наибольший интерес представляют достаточно распространенные: алюминий, медь, свинец и различные сплавы на их основе. Рассмотрим подробнее металлы, с которыми имеют дело те, кто занимается слесарным делом, ковкой, чеканкой, художественным литьем и т. п.
Железо
Оно было известно уже в древности. А в Средневековье различали не только сталь, железо и чугун, но и различные их марки. Например, клинки оружия могли изготавливаться из обычной стали или из дамасской – знаменитого булата. Кузнецы того времени, конечно же, не знали, что особые свойства железу придает прежде всего различное содержание углерода, но варили сталь с древесным углем.
Сейчас содержание углерода служит одним из основных показателей, по которому определяются сорт и марка черного металла. Различают низко-, средне– и высокоуглеродистые стали. Самая низкоуглеродистая сталь в практике называется железом. В ней меньше 0,1 % углерода, она очень мягкая (по сравнению с другими марками), хорошо поддается ковке, гнется, сваривается кузнечным способом, но закалить ее крайне сложно.
Наилучшей сталью для ручной ковки и изготовления художественных изделий считается низкоуглеродистая (до 0,3 %). Ее называют еще поделочной. Она хорошо куется и сваривается, ее можно закалить для придания прочности изделию.
Конструкционная сталь среднеуглеродистая (до 0,85 %). Она средней твердости, хорошо куется при нагреве и закаливается, но кузнечной сварке поддается плохо.
Высокоуглеродистая сталь наиболее твердая, даже при специальном нагреве куется с трудом и почти не сваривается. Содержание углерода в ней может достигать 1,35 %. Используется она для изготовления различных инструментов и их рабочих частей, поэтому называется также инструментальной.
Чугун – это черный металл с содержанием углерода свыше 2 %. Он твердый, но хрупкий, ковать или варить его нельзя. Чугунные детали изготавливаются литьем, провести которое в условиях обычной домашней мастерской невозможно.
Самый распространенный слесарный материал, конечно же, сплав железа и углерода – сталь (удельный вес 7,8 г/см2). Но сталь стали рознь: есть твердые, высокопрочные стали, которые, как правило, не поддаются ручной обработке. (В мастерской такие стали присутствуют в виде инструмента.) А вот мягкие стали, их еще называют ковкими, вполне пригодны для обработки в домашних условиях. Однако следует помнить, что такая сталь особенно сильно подвержена коррозии.
Для домашней обработки наиболее подходит поделочная сталь. Согласно стандарту ГОСТ 380–71 к этому виду относится сталь с маркой от 0 до 6. В профессиональных кругах они называются просто тройкой, пятеркой и т. д. В специальной же литературе обозначаются буквами Ст и номером марки.
Ст 0 (до 0,23 % углерода), Ст 1 (0,07–0,12 %), Ст 2 (0,09–0,15 %) и Ст 3 (0,14–0,22 %) не закаливаются, хорошо свариваются и применяются в виде различных прутков, полос, листов и проволоки. Из них получаются различные кованые, гнутые и чеканные изделия.
Ст 4 (0,18–0,27 % углерода) используется для изготовления заклепок, болтов, труб, уголков, швеллеров и т. п. Она тверже, слабо закаливается, но достаточно хорошо сваривается. Чеканить по ней трудно, однако при должном нагреве ее можно использовать для ковки. Одно из основных ее достоинств в наше время – широкая распространенность и доступность.
Из Ст 5 (содержание углерода 0,28–0,37 %) изготавливаются в основном крупные детали. Она слабо закаливается и хорошо варится.
Ст 6 (0,38–0,50 % углерода) хорошо закаливается, но из-за большой твердости редко употребляется для ручной ковки и других художественных работ.
Заводские заготовки с указанием марки стали на клейме встречаются не так уж часто. Обычно в дело идут какие-то старые, пришедшие в негодность, случайно найденные и т. п. изделия и детали. В этом случае определять сорт стали придется самостоятельно.
Один из самых простых способов определения сорта стали – с помощью зубила. Нужно взять заготовку или деталь, марку стали которой нужно определить, зажать в тисках и попробовать снять зубилом стружку. Если стружка снимается легко, получается длинной и завивается в спираль, то сталь низкоуглеродистая. Чем тверже сталь, тем более короткой и ломкой будет стружка. Инструментальную сталь стругать зубилом почти невозможно.
Малоуглеродистую сталь (Ст 0 – Ст 3) можно определить при закалке. Следует надпилить сталь напильником. После этого нагреть заготовку докрасна и быстро охладить в воде. Если закалки не произошло, пилить будет так же легко, если сталь выше Ст 4 – закалка затруднит надпиливание.
Один из наиболее распространенных способов определения марки стали – по искре от точильного (наждачного) круга. С помощью специальных таблиц можно определить марку довольно точно, но будет достаточно и приблизительного определения пригодности заготовки для намеченного дела.
Надо взять деталь, прижать ее к вращающемуся на большой скорости кругу и наблюдать за искрами (рис. 14).
Рис. 14. Определение сорта стали по искре: а – низкоуглеродистая; б – среднеуглеродистая; в – высокоуглеродистая.
Поделочная сталь образует длинный и светлый пучок, искры прямые, с несколькими утолщениями светлого и темно-красного цвета (рис. 14, а). Среднеуглеродистая сталь даст светлый и короткий пучок искр, распадающихся звездочками после первого утолщения (рис. 14, б). Если искры красноватые, их сноп короткий и широкий, почти сразу же разлетающийся множеством звездочек (такую картину видел каждый, кто затачивал нож или другой инструмент), то деталь из высокоуглеродистой стали (рис. 14, в).
Если необходимо обработать небольшую заготовку из твердой стали, то ее можно несколько размягчить, отпустить. Для этого надо раскалить заготовку добела с помощью газовой горелки или паяльной лампы и дать ей постепенно остыть при комнатной температуре. При необходимости (если заготовка не стала достаточно мягкой) эту операцию можно повторить еще один раз.
В некоторых случаях не обязательно определять марку стали. При занятиях чеканкой, выпиливанием или гравировкой можно просто попробовать заготовку инструментом. Если она поддается, то ее можно пускать в дело. Лучше запомнить, какие изделия изготавливаются из нужной для работы марки, и использовать их в качестве заготовок.
Для чеканки вполне подойдут листы кровельного железа, автомобильная жесть и даже консервные банки. Главное – металл должен быть чистым, без ржавчины, пробоин и трещин. Иногда даже незначительная на первый взгляд царапина способна ослабить заготовку, и при работе с ней материал либо изменит форму не так, как планировалось, либо вообще прорвется в слабом месте. Поделка, на которую до этого было затрачено немало времени и сил, будет безнадежно испорчена.
При гравировании или выпиливании по металлу требования могут быть не такими высокими, но трещин, пробоин и раковин от ржавчины необходимо избегать и в этом случае. При полировке поверхности изделия их обычно не удается зачистить или замаскировать.
Сейчас содержание углерода служит одним из основных показателей, по которому определяются сорт и марка черного металла. Различают низко-, средне– и высокоуглеродистые стали. Самая низкоуглеродистая сталь в практике называется железом. В ней меньше 0,1 % углерода, она очень мягкая (по сравнению с другими марками), хорошо поддается ковке, гнется, сваривается кузнечным способом, но закалить ее крайне сложно.
Наилучшей сталью для ручной ковки и изготовления художественных изделий считается низкоуглеродистая (до 0,3 %). Ее называют еще поделочной. Она хорошо куется и сваривается, ее можно закалить для придания прочности изделию.
Конструкционная сталь среднеуглеродистая (до 0,85 %). Она средней твердости, хорошо куется при нагреве и закаливается, но кузнечной сварке поддается плохо.
Высокоуглеродистая сталь наиболее твердая, даже при специальном нагреве куется с трудом и почти не сваривается. Содержание углерода в ней может достигать 1,35 %. Используется она для изготовления различных инструментов и их рабочих частей, поэтому называется также инструментальной.
Чугун – это черный металл с содержанием углерода свыше 2 %. Он твердый, но хрупкий, ковать или варить его нельзя. Чугунные детали изготавливаются литьем, провести которое в условиях обычной домашней мастерской невозможно.
Самый распространенный слесарный материал, конечно же, сплав железа и углерода – сталь (удельный вес 7,8 г/см2). Но сталь стали рознь: есть твердые, высокопрочные стали, которые, как правило, не поддаются ручной обработке. (В мастерской такие стали присутствуют в виде инструмента.) А вот мягкие стали, их еще называют ковкими, вполне пригодны для обработки в домашних условиях. Однако следует помнить, что такая сталь особенно сильно подвержена коррозии.
Для домашней обработки наиболее подходит поделочная сталь. Согласно стандарту ГОСТ 380–71 к этому виду относится сталь с маркой от 0 до 6. В профессиональных кругах они называются просто тройкой, пятеркой и т. д. В специальной же литературе обозначаются буквами Ст и номером марки.
Ст 0 (до 0,23 % углерода), Ст 1 (0,07–0,12 %), Ст 2 (0,09–0,15 %) и Ст 3 (0,14–0,22 %) не закаливаются, хорошо свариваются и применяются в виде различных прутков, полос, листов и проволоки. Из них получаются различные кованые, гнутые и чеканные изделия.
Ст 4 (0,18–0,27 % углерода) используется для изготовления заклепок, болтов, труб, уголков, швеллеров и т. п. Она тверже, слабо закаливается, но достаточно хорошо сваривается. Чеканить по ней трудно, однако при должном нагреве ее можно использовать для ковки. Одно из основных ее достоинств в наше время – широкая распространенность и доступность.
Из Ст 5 (содержание углерода 0,28–0,37 %) изготавливаются в основном крупные детали. Она слабо закаливается и хорошо варится.
Ст 6 (0,38–0,50 % углерода) хорошо закаливается, но из-за большой твердости редко употребляется для ручной ковки и других художественных работ.
Заводские заготовки с указанием марки стали на клейме встречаются не так уж часто. Обычно в дело идут какие-то старые, пришедшие в негодность, случайно найденные и т. п. изделия и детали. В этом случае определять сорт стали придется самостоятельно.
Один из самых простых способов определения сорта стали – с помощью зубила. Нужно взять заготовку или деталь, марку стали которой нужно определить, зажать в тисках и попробовать снять зубилом стружку. Если стружка снимается легко, получается длинной и завивается в спираль, то сталь низкоуглеродистая. Чем тверже сталь, тем более короткой и ломкой будет стружка. Инструментальную сталь стругать зубилом почти невозможно.
Малоуглеродистую сталь (Ст 0 – Ст 3) можно определить при закалке. Следует надпилить сталь напильником. После этого нагреть заготовку докрасна и быстро охладить в воде. Если закалки не произошло, пилить будет так же легко, если сталь выше Ст 4 – закалка затруднит надпиливание.
Один из наиболее распространенных способов определения марки стали – по искре от точильного (наждачного) круга. С помощью специальных таблиц можно определить марку довольно точно, но будет достаточно и приблизительного определения пригодности заготовки для намеченного дела.
Надо взять деталь, прижать ее к вращающемуся на большой скорости кругу и наблюдать за искрами (рис. 14).
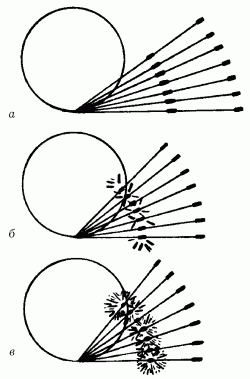
Поделочная сталь образует длинный и светлый пучок, искры прямые, с несколькими утолщениями светлого и темно-красного цвета (рис. 14, а). Среднеуглеродистая сталь даст светлый и короткий пучок искр, распадающихся звездочками после первого утолщения (рис. 14, б). Если искры красноватые, их сноп короткий и широкий, почти сразу же разлетающийся множеством звездочек (такую картину видел каждый, кто затачивал нож или другой инструмент), то деталь из высокоуглеродистой стали (рис. 14, в).
Если необходимо обработать небольшую заготовку из твердой стали, то ее можно несколько размягчить, отпустить. Для этого надо раскалить заготовку добела с помощью газовой горелки или паяльной лампы и дать ей постепенно остыть при комнатной температуре. При необходимости (если заготовка не стала достаточно мягкой) эту операцию можно повторить еще один раз.
В некоторых случаях не обязательно определять марку стали. При занятиях чеканкой, выпиливанием или гравировкой можно просто попробовать заготовку инструментом. Если она поддается, то ее можно пускать в дело. Лучше запомнить, какие изделия изготавливаются из нужной для работы марки, и использовать их в качестве заготовок.
Для чеканки вполне подойдут листы кровельного железа, автомобильная жесть и даже консервные банки. Главное – металл должен быть чистым, без ржавчины, пробоин и трещин. Иногда даже незначительная на первый взгляд царапина способна ослабить заготовку, и при работе с ней материал либо изменит форму не так, как планировалось, либо вообще прорвется в слабом месте. Поделка, на которую до этого было затрачено немало времени и сил, будет безнадежно испорчена.
При гравировании или выпиливании по металлу требования могут быть не такими высокими, но трещин, пробоин и раковин от ржавчины необходимо избегать и в этом случае. При полировке поверхности изделия их обычно не удается зачистить или замаскировать.
Медь и сплавы
Довольно часто домашние слесари отдают предпочтение меди (удельный вес 9,0 г/см2), поскольку ее мягкость и пластичность позволяют добиваться точности и высокого качества при изготовлении всевозможных деталей и изделий.
Чистая (красная) медь – прекрасный материал для различных поделок. Она подходит для ковки (в том числе холодной), чеканки, по ней можно легко гравировать и из нее выпиливать. Ее существенный недостаток – относительная дороговизна, а достать какие-либо бросовые изделия или детали для переработки довольно трудно из-за прокатившейся по России (и не только) волны массовой скупки цветных металлов. При работе с медью необходимо учитывать несколько особенностей этого металла.
Обработка меди резанием затруднена из-за ее пластичности и вязкости. Если необходимо вырезать из медного листа фигуру определенной формы (особенно со сложным контуром или небольших размеров), то лучше воспользоваться дрелью, ножовкой по металлу или напильником. Для тонких листов подойдет лобзик. Зубило или ножницы по металлу сомнут лист и загнут края, восстановить их будет трудно.
При длительной ударной обработке (чеканке, ковке) медь может потерять пластичность и начать трескаться. Для восстановления пластичности необходимо обжечь деталь при температуре 200–300 °C, но не выше; при 400–600 °C металл станет хрупким. Для обжига небольших деталей в домашних условиях вполне подойдет духовка газовой плиты со средним огнем.
Следует учитывать, что первоначальный яркий блеск меди вскоре потускнеет, несмотря на полировку. На воздухе изделия из медных пластинок окисляются и приобретают темно-красный цвет. В таком состоянии медь очень устойчива к коррозии, а во влажном воздухе со временем покроется зеленоватым налетом – патиной. С помощью различных химических веществ можно придать меди синий, зеленый и даже черный цвет. При желании сохранить изделие ярко-красным необходимо покрыть его прозрачным (бесцветным) лаком.
Медь является великолепным проводником электрического тока, а медный провод широко используется в работах, связанных с электротехникой.
Широко распространена латунь – сплав меди с цинком золотисто-желтого цвета. Иногда в него добавляется еще и алюминий. Благодаря содержанию цинка латунь прочнее и меньше окисляется, но обладает не столь высокой пластичностью. Ее марки характеризуются различным процентным содержанием меди (например, Л68 – 68 %, Л70 – 70 % и т. д.).
Латунь, в отличие от бронзы, относится к разряду дешевых материалов. Наряду с мягкостью и пластичностью, латунь практически не подвержена коррозии. В слесарных работах на дому чаще всего используется листовая латунь и латунная проволока.
Для поделочных работ рекомендуется использовать сплавы с высоким содержанием меди. Латунь прочнее и тверже меди, ее можно использовать для ажурной чеканки, выпиливания, гравировки, но не для ковки или чеканки с высоким рельефом, потому что могут образоваться трещины. Чтобы этого не произошло при создании плоского рельефа или длительном хранении изделия, надо обжечь латунь при температуре 200–300 °C.
Бронза (сплав меди с другими металлами) – материал не из дешевых, поэтому используется она в основном в декоративных целях. Ее качества зависят от составляющих сплава. Так, алюминиевые бронзы отличаются высокой износоустойчивостью, оловянные – пластичностью, бериллиевые – прочностью. Бронзовые изделия тверже медных (некоторые специальные марки бронзы по прочности превосходят сталь), поддаются ковке и пригодны для литья. Однако бронза дороже и дефицитнее меди, не выпускается в виде тонких листов, поэтому работать с ней в домашних условиях удается редко, только если выплавлять ее самостоятельно.
Благодаря своим декоративным качествам медь (и ее сплавы – латунь, бронза) используется для изготовления предметов украшения, мебельной фурнитуры.
Чистая (красная) медь – прекрасный материал для различных поделок. Она подходит для ковки (в том числе холодной), чеканки, по ней можно легко гравировать и из нее выпиливать. Ее существенный недостаток – относительная дороговизна, а достать какие-либо бросовые изделия или детали для переработки довольно трудно из-за прокатившейся по России (и не только) волны массовой скупки цветных металлов. При работе с медью необходимо учитывать несколько особенностей этого металла.
Обработка меди резанием затруднена из-за ее пластичности и вязкости. Если необходимо вырезать из медного листа фигуру определенной формы (особенно со сложным контуром или небольших размеров), то лучше воспользоваться дрелью, ножовкой по металлу или напильником. Для тонких листов подойдет лобзик. Зубило или ножницы по металлу сомнут лист и загнут края, восстановить их будет трудно.
При длительной ударной обработке (чеканке, ковке) медь может потерять пластичность и начать трескаться. Для восстановления пластичности необходимо обжечь деталь при температуре 200–300 °C, но не выше; при 400–600 °C металл станет хрупким. Для обжига небольших деталей в домашних условиях вполне подойдет духовка газовой плиты со средним огнем.
Следует учитывать, что первоначальный яркий блеск меди вскоре потускнеет, несмотря на полировку. На воздухе изделия из медных пластинок окисляются и приобретают темно-красный цвет. В таком состоянии медь очень устойчива к коррозии, а во влажном воздухе со временем покроется зеленоватым налетом – патиной. С помощью различных химических веществ можно придать меди синий, зеленый и даже черный цвет. При желании сохранить изделие ярко-красным необходимо покрыть его прозрачным (бесцветным) лаком.
Медь является великолепным проводником электрического тока, а медный провод широко используется в работах, связанных с электротехникой.
Широко распространена латунь – сплав меди с цинком золотисто-желтого цвета. Иногда в него добавляется еще и алюминий. Благодаря содержанию цинка латунь прочнее и меньше окисляется, но обладает не столь высокой пластичностью. Ее марки характеризуются различным процентным содержанием меди (например, Л68 – 68 %, Л70 – 70 % и т. д.).
Латунь, в отличие от бронзы, относится к разряду дешевых материалов. Наряду с мягкостью и пластичностью, латунь практически не подвержена коррозии. В слесарных работах на дому чаще всего используется листовая латунь и латунная проволока.
Для поделочных работ рекомендуется использовать сплавы с высоким содержанием меди. Латунь прочнее и тверже меди, ее можно использовать для ажурной чеканки, выпиливания, гравировки, но не для ковки или чеканки с высоким рельефом, потому что могут образоваться трещины. Чтобы этого не произошло при создании плоского рельефа или длительном хранении изделия, надо обжечь латунь при температуре 200–300 °C.
Бронза (сплав меди с другими металлами) – материал не из дешевых, поэтому используется она в основном в декоративных целях. Ее качества зависят от составляющих сплава. Так, алюминиевые бронзы отличаются высокой износоустойчивостью, оловянные – пластичностью, бериллиевые – прочностью. Бронзовые изделия тверже медных (некоторые специальные марки бронзы по прочности превосходят сталь), поддаются ковке и пригодны для литья. Однако бронза дороже и дефицитнее меди, не выпускается в виде тонких листов, поэтому работать с ней в домашних условиях удается редко, только если выплавлять ее самостоятельно.
Благодаря своим декоративным качествам медь (и ее сплавы – латунь, бронза) используется для изготовления предметов украшения, мебельной фурнитуры.