Страница:
Ремонт зубчатых передач и уход за ними
Для того чтобы зубчатая передача работала исправно и не приводила к сбою в работе всего механизма в целом, за ней нужно организовать правильный уход. Что это значит?
При попадании в передачу грязи, абразивной и металлической пыли, при отсутствии или недостаточном количестве смазки зубья колес быстро изнашиваются, на их поверхностях образуются шероховатости, которые могут привести к заклиниванию передачи. Поэтому открытые передачи, которые не имеют защитного кожуха, периодически смазывают кистью или масленкой, одновременно очищая их от пыли и грязи. Закрытые передачи в смазке нуждаются реже, их погружают в масляную ванну или смазывают струей масла, подаваемого под давлением в зону сопряжения зубьев.
В ходе эксплуатации зубья передач периодически осматривают на предмет обнаружения износа: если износ зубьев превышает допустимый, значит, колеса подлежат замене (при этом заменяются оба колеса пары).
Если колеса разборные, то можно ограничиться заменой венца, для чего старый венец срезают, на его место напрессовывают и стопорят новый. Если зубья работают с одной стороны, то колеса можно просто перевернуть, подрезав несимметричную ступицу с одной стороны, а с другой приварив кольцо.
Одной из частых причин выхода из строя передачи является поломка зуба. Отремонтировать «беззубое» колесо (правда, только цилиндрическое) можно заливкой нового зуба по профильному шаблону: на колесе в месте излома на планках и шпильках крепят профильный шаблон, выемку заливают расплавленным металлом, после его остывания профиль зуба обрабатывают, сверяясь с шаблоном (рис. 65).
Рис. 65. Восстановление зубьев цилиндрических колес с помощью профильного шаблона: 1 – зуб цилиндрического колеса; 2 – планка; 3 – новый зуб; 4 – профильный шаблон.
Зуб можно также приварить (наплавить) газовой или электросваркой электродами Э-42 с толстой обмазкой ОММ-5. После наплавки зуб обрабатывают и закаливают.
При попадании в передачу грязи, абразивной и металлической пыли, при отсутствии или недостаточном количестве смазки зубья колес быстро изнашиваются, на их поверхностях образуются шероховатости, которые могут привести к заклиниванию передачи. Поэтому открытые передачи, которые не имеют защитного кожуха, периодически смазывают кистью или масленкой, одновременно очищая их от пыли и грязи. Закрытые передачи в смазке нуждаются реже, их погружают в масляную ванну или смазывают струей масла, подаваемого под давлением в зону сопряжения зубьев.
В ходе эксплуатации зубья передач периодически осматривают на предмет обнаружения износа: если износ зубьев превышает допустимый, значит, колеса подлежат замене (при этом заменяются оба колеса пары).
Если колеса разборные, то можно ограничиться заменой венца, для чего старый венец срезают, на его место напрессовывают и стопорят новый. Если зубья работают с одной стороны, то колеса можно просто перевернуть, подрезав несимметричную ступицу с одной стороны, а с другой приварив кольцо.
Одной из частых причин выхода из строя передачи является поломка зуба. Отремонтировать «беззубое» колесо (правда, только цилиндрическое) можно заливкой нового зуба по профильному шаблону: на колесе в месте излома на планках и шпильках крепят профильный шаблон, выемку заливают расплавленным металлом, после его остывания профиль зуба обрабатывают, сверяясь с шаблоном (рис. 65).
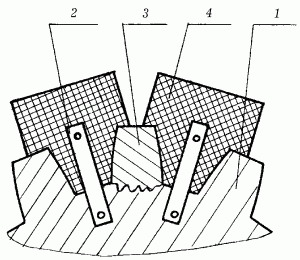
Зуб можно также приварить (наплавить) газовой или электросваркой электродами Э-42 с толстой обмазкой ОММ-5. После наплавки зуб обрабатывают и закаливают.
Сборка цепных передач
О цепных передачах разговор особый, ибо и сами они не совсем обычны: с одной стороны, цепная передача относится к разряду гибких, где цепь представляет собой своеобразный ремень, но, с другой стороны, передача вращающего момента осуществляется не за счет силы трения, а за счет зацепления звеньев цепи за зубья зубчатых колес (звездочек), следовательно, цепная передача является одновременно зубчатой.
Поэтому она обладает достоинствами и у нее отсутствуют недостатки как гибкой, так и зубчатой передач: во-первых, с ее помощью можно передавать вращающие моменты между валами, находящимися на значительном удалении друг от друга – до 8 м (как при ременной передаче); во-вторых, она сохраняет постоянство передаточного числа, то есть отсутствует проскальзывание (как в зубчатых передачах); в-третьих, цепь этой передачи не требует большого натяжения (в отличие от ремня); в-четвертых, она может передавать большие крутящие моменты; в-пятых, КПД цепной передачи достигает 0,98.
Классификация цепных передач производится по двум признакам: по назначению (грузовые – для поднятия грузов, тяговые – для перемещения грузов, приводные – для передачи движения от двигателя к исполнительному механизму) и по конструкции приводных цепей (роликовые, втулочные, зубчатые и т. д.).
Приводная роликовая цепь состоит из переходных (валик с напрессованными наружными пластинами) и соединительных (втулка с насаженным на нее роликом и напрессованными внутренними пластинами) звеньев (рис. 66).
Рис. 66. Цепная передача: а – роликовая цепь.
Рис. 66 (продолжение). Цепная передача: б – втулочная; в – зубчатая цепь; г – узел цепной передачи: 1 – ведущий вал со звездочкой; 2 – ведомый вал со звездочкой; 3 – цепь; 4 – регулировочное приспособление для натягивания цепи со звездочкой.
Ролик в соединительных звеньях насажен на втулку с некоторым зазором, что обеспечивает создание между зубьями звездочек и цепью трения качения. Применяются такие передачи в механизмах, где окружные скорости не превышают 15 м/с.
Роликовые цепи могут быть одно– (ПР) и двухрядные (2ПР) – для передачи небольших мощностей, а также трех– (3ПР), четырехрядные (4ПР) цепи с изогнутыми пластинами (ПРИ) и цепи тяжелого типа (ПРТ, 2ПРТ, 3ПРТ, 4ПРТ и 6ПРТ) – для передачи больших мощностей. Многорядные цепи собираются из обычных звеньев с применением удлиненных валиков. Промышленностью выпускаются цепи с шагом определенной величины (соответственно под них выпускаются и звездочки): 8, 9,525, 12,7, 15,875, 19,05, 25,4, 31,75, 38,1, 44,45, 50,8, 63,5 и 76,2 мм.
Приводные втулочные цепи представляют собой подобие роликовых, но ролики не имеют (рис. 66, б). Вследствие этого они значительно легче и ощутимо дешевле роликовых цепей. Однако они больше подвержены износу, поэтому применяются только для передачи малых мощностей в тихоходных механизмах.
Маркировка и роликовых, и втулочных цепей одинакова: на первом месте указывается количество рядов (при маркировке однорядных цепей 1 не указывается), далее идут заглавные буквы, обозначающие тип цепи (ПР – роликовая, ПРИ – роликовая изогнутая, ПРТ – роликовая тяжелая, ПВ – втулочная), следующее число говорит о величине шага звеньев цепи, последнее числовое значение указывает предельно допустимую силу нагрузки.
Конструкция приводной зубчатой цепи состоит из рабочих пластин, соединенных между собой вкладышами качения, и направляющих пластин, которые фиксируют цепь в осевом направлении.
Цепи могут быть однопарными и многопарными в зависимости от назначения. Шаг звеньев цепей 12,7, 15,875, 19,05, 25,4 и 31,75 мм. Такие цепи используют в механизмах, имеющих большие окружные скорости (до 30 м/с) и испытывающих неравномерную загрузку.
Как уже было сказано, цепная передача движения осуществляется за счет зацепления цепи за зубья звездочек. Звездочки изготавливаются из стали, число зубьев может быть от 9 до 22 и 25 (28), 32 (36), 40 (45), 50 (56), 63 (71), 80. Они бывают как цельные, так и разборные (ступица из чугуна или стали, а венец стальной, при этом венец напрессовывается на ступицу и закрепляется болтами или винтами).
Сборка узла цепной передачи состоит из следующих операций:
– звездочки устанавливаются на взаимодействующие валы методом напрессовки прессами или винтовыми приспособлениями и фиксируются во избежание осевого смещения;
– производится проверка их расположения (они должны находиться в одной плоскости) и радиального и торцевого биения (с помощью индикатора);
– подбирается отрезок цепи необходимой длины (при ремонте – по старой цепи, при первичной сборке – согласно техническим условиям на конкретный механизм), надевается на звездочки и натягивается специальным приспособлением;
– замыкается цепь в кольцо. Если цепь состоит из четного количества звеньев, то ее концы соединяются обычным звеном, если число звеньев нечетное, то переходным звеном.
Для нормальной и долговечной работы цепной передачи необходимы два условия:
– во-первых, соблюдение натяжения цепи. Поскольку при работе механизма цепь испытывает постоянные нагрузки на вытягивание, то провисание цепи может увеличиться, цепь начнет болтаться, износ элементов передачи будет ощутимее. Поэтому при вытягивании цепи ее подтягивают либо натяжной звездочкой, если она предусмотрена конструкцией механизма, либо путем удаления звеньев, если это допустимо по техническим условиям, если натяжение откорректировать этими способами нельзя, то устанавливается новая цепь;
– во-вторых, постоянное присутствие смазочного материала.
Если для смазывания сопрягаемых элементов передачи используется пластичный смазочный материал, то цепь перед очередной процедурой смазки промывают в керосине, просушивают, а смазывают ее путем погружения в расплавленную смазку.
Если используется жидкая смазка, то необходимо своевременно пополнять масленки.
Поэтому она обладает достоинствами и у нее отсутствуют недостатки как гибкой, так и зубчатой передач: во-первых, с ее помощью можно передавать вращающие моменты между валами, находящимися на значительном удалении друг от друга – до 8 м (как при ременной передаче); во-вторых, она сохраняет постоянство передаточного числа, то есть отсутствует проскальзывание (как в зубчатых передачах); в-третьих, цепь этой передачи не требует большого натяжения (в отличие от ремня); в-четвертых, она может передавать большие крутящие моменты; в-пятых, КПД цепной передачи достигает 0,98.
Классификация цепных передач производится по двум признакам: по назначению (грузовые – для поднятия грузов, тяговые – для перемещения грузов, приводные – для передачи движения от двигателя к исполнительному механизму) и по конструкции приводных цепей (роликовые, втулочные, зубчатые и т. д.).
Приводная роликовая цепь состоит из переходных (валик с напрессованными наружными пластинами) и соединительных (втулка с насаженным на нее роликом и напрессованными внутренними пластинами) звеньев (рис. 66).
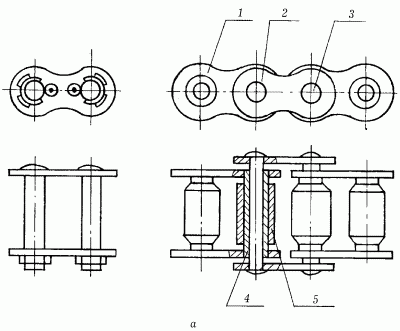
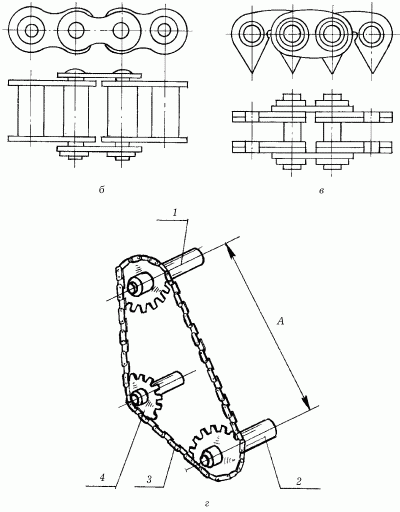
Ролик в соединительных звеньях насажен на втулку с некоторым зазором, что обеспечивает создание между зубьями звездочек и цепью трения качения. Применяются такие передачи в механизмах, где окружные скорости не превышают 15 м/с.
Роликовые цепи могут быть одно– (ПР) и двухрядные (2ПР) – для передачи небольших мощностей, а также трех– (3ПР), четырехрядные (4ПР) цепи с изогнутыми пластинами (ПРИ) и цепи тяжелого типа (ПРТ, 2ПРТ, 3ПРТ, 4ПРТ и 6ПРТ) – для передачи больших мощностей. Многорядные цепи собираются из обычных звеньев с применением удлиненных валиков. Промышленностью выпускаются цепи с шагом определенной величины (соответственно под них выпускаются и звездочки): 8, 9,525, 12,7, 15,875, 19,05, 25,4, 31,75, 38,1, 44,45, 50,8, 63,5 и 76,2 мм.
Приводные втулочные цепи представляют собой подобие роликовых, но ролики не имеют (рис. 66, б). Вследствие этого они значительно легче и ощутимо дешевле роликовых цепей. Однако они больше подвержены износу, поэтому применяются только для передачи малых мощностей в тихоходных механизмах.
Маркировка и роликовых, и втулочных цепей одинакова: на первом месте указывается количество рядов (при маркировке однорядных цепей 1 не указывается), далее идут заглавные буквы, обозначающие тип цепи (ПР – роликовая, ПРИ – роликовая изогнутая, ПРТ – роликовая тяжелая, ПВ – втулочная), следующее число говорит о величине шага звеньев цепи, последнее числовое значение указывает предельно допустимую силу нагрузки.
Конструкция приводной зубчатой цепи состоит из рабочих пластин, соединенных между собой вкладышами качения, и направляющих пластин, которые фиксируют цепь в осевом направлении.
Цепи могут быть однопарными и многопарными в зависимости от назначения. Шаг звеньев цепей 12,7, 15,875, 19,05, 25,4 и 31,75 мм. Такие цепи используют в механизмах, имеющих большие окружные скорости (до 30 м/с) и испытывающих неравномерную загрузку.
Как уже было сказано, цепная передача движения осуществляется за счет зацепления цепи за зубья звездочек. Звездочки изготавливаются из стали, число зубьев может быть от 9 до 22 и 25 (28), 32 (36), 40 (45), 50 (56), 63 (71), 80. Они бывают как цельные, так и разборные (ступица из чугуна или стали, а венец стальной, при этом венец напрессовывается на ступицу и закрепляется болтами или винтами).
Сборка узла цепной передачи состоит из следующих операций:
– звездочки устанавливаются на взаимодействующие валы методом напрессовки прессами или винтовыми приспособлениями и фиксируются во избежание осевого смещения;
– производится проверка их расположения (они должны находиться в одной плоскости) и радиального и торцевого биения (с помощью индикатора);
– подбирается отрезок цепи необходимой длины (при ремонте – по старой цепи, при первичной сборке – согласно техническим условиям на конкретный механизм), надевается на звездочки и натягивается специальным приспособлением;
– замыкается цепь в кольцо. Если цепь состоит из четного количества звеньев, то ее концы соединяются обычным звеном, если число звеньев нечетное, то переходным звеном.
Для нормальной и долговечной работы цепной передачи необходимы два условия:
– во-первых, соблюдение натяжения цепи. Поскольку при работе механизма цепь испытывает постоянные нагрузки на вытягивание, то провисание цепи может увеличиться, цепь начнет болтаться, износ элементов передачи будет ощутимее. Поэтому при вытягивании цепи ее подтягивают либо натяжной звездочкой, если она предусмотрена конструкцией механизма, либо путем удаления звеньев, если это допустимо по техническим условиям, если натяжение откорректировать этими способами нельзя, то устанавливается новая цепь;
– во-вторых, постоянное присутствие смазочного материала.
Если для смазывания сопрягаемых элементов передачи используется пластичный смазочный материал, то цепь перед очередной процедурой смазки промывают в керосине, просушивают, а смазывают ее путем погружения в расплавленную смазку.
Если используется жидкая смазка, то необходимо своевременно пополнять масленки.
Сборка передач, основанных на силе трения
Механические передачи, работа которых основана на силе трения, можно разделить на две группы: ременные – используются в том случае, если взаимодействующие валы находятся на некотором удалении друг от друга, и фрикционные – если валы расположены в непосредственной близости.
В ременных передачах движение передается посредством гибкого, замкнутого в кольцо, ремня, надетого на два шкива. Ремни могут быть плоскими, клиновыми и круглыми.
Плоские ремни изготавливаются из кожи, прорезиненных или хлопчатобумажных тканей, шерсти или шелка. Перед установкой такие ремни подвергают растягиванию в течение 3–5 суток, затем концы ремней соединяют склеиванием, сшиванием или с помощью металлических прижимов. Самый лучший способ соединения – склеивание (кожаные – косым швом, прорезиненные – ступенчатым). Для склеивания кожаных ремней используют мездровый, желатиновый, целлюлозный, рыбный клеи, для прорезиненных – резиновые тиуратовые клеи 1-го и 2-го сортов в равных долях. Концы кожаных ремней перед склеиванием тщательно зачищают, наносят два слоя клея с интервалом в 5–6 минут и накладывают ремни друг на друга. Затем клееный шов зажимают между двумя дощечками, которые стягивают болтами, и выдерживают в течение 5–8 часов.
Концы прорезиненных ремней зачищают ножом, затем напильником делают ступенчатые уступы и обезжиривают бензином, наносят 3–4 слоя клея (перед нанесением последующего слоя предыдущий просушивают), после нанесения последнего слоя (без просушки) концы соединяют, зажимают струбцинами между двумя дощечками и выдерживают при температуре 16–20 °C 24 часа (или при температуре 100 °C – 3–4 часа). Используют плоские ремни в передачах со скоростью вращения до 30 м/с.
Клиновые ремни могут быть кордтканевые или кордшнуровые, с гладким и зубчатым профилем, угол трапецеидальной формы – 40°.
Обладая достаточной гибкостью и большей, по сравнению с плоскими ремнями, прочностью, клиновые ремни используются для передачи мощностей от 0,3 до 75 кВт (в зависимости от профиля и длины ремня). Шкивы для клиноременных передач на ободе имеют канавки клиновидной формы, с углом профиля 34–40°.
Ремни круглого профиля бывают кожаными, хлопчатобумажными, капроновыми или прорезиненными, диаметром от 2 до 20 мм. Область применения та же, что и у плоских ремней. Профиль канавки шкива круглоременной передачи полукруглый, с радиусом, равным радиусу ремня.
Технологический процесс сборки ременной передачи состоит из следующих этапов:
– балансировка шкивов, то есть устранение их неуравновешенности. Она достигается либо путем высверливания части металла из шкива, либо путем нагружения его специальными грузиками;
– установка шкивов на валы. Их напрессовывают и закрепляют шпонкой или шлицем (следует учесть, что для напрессовки шкива на вал нельзя пользоваться ударными инструментами, поэтому ее осуществляют с помощью специальных приспособлений);
– регулирование передачи заключается в создании определенного усилия натяжения ремня. Натяжение проверяют динамометром или гирями, подвешенными за скобу (при воздействии определенной силы от 50 до 100 Н или при определенном весе гирь должен быть такой же прогиб ремня, который задается техническими условиями для каждого конкретного механизма). При слабом натяжении ремень проскальзывает при работе механизма или «бьет» (хлопает), нагревается, что приводит к его быстрому износу; чрезмерное натяжение ремня создает излишнюю нагрузку на подшипники, а также ведет к быстрому износу шеек вала и шкивов. Регулировка натяжения производится перемещением натяжного ролика.
Работоспособность ременной механической передачи характеризуется величиной углов обхвата (угол, образуемый лучами, выходящими из центра шкива и проходящими через крайние точки сопряжения шкива с ремнем). Определяющим является угол обхвата меньшего шкива, он должен быть не менее 120°. Это условие выполняется, если отношение величины диаметра ведущего шкива к величине диаметра ведомого находится в пределах от 1/3 до 3, а межосевое расстояние не меньше удвоенной суммы величин диаметров обоих шкивов. Фрикционные передачи (рис. 67) передают вращательные движения между валами с помощью силы трения.
Рис. 67. Вариант фрикционной передачи: 1 – конический барабан; 2 – винт; 3 – фрикционное колесо; 4 – гайка; 5 – маховик.
Самые распространенные механизмы, в которых используются фрикционные передачи, – фрикционные муфты и тормоза.
Фрикционные муфты, в зависимости от назначения, могут быть сцепными (находящимися в постоянном сцеплении, но при необходимости разъединяющимися), например муфта сцепления в автомобиле, или предохранительными – они предохраняют привод от поломок во время перегрузок.
Название тормоза говорит само за себя: это устройство для уменьшения скорости, вплоть до полной остановки машины. Тормоз любого механизма характеризуется двумя показателями: временем торможения и скоростью, при которой начинается торможение.
Время торможения зависит от контакта тормозной колодки или ленты с вращающимися элементами тормоза, поэтому важно плотное прилегание фрикционного материала к колодке или ленте (без складок, выпучиваний и выступаний головок заклепок), а площадь его контакта с поверхностью торможения должна быть не менее 80 %.
Во время работы механизма, то есть при бездействии тормоза, фрикционный материал не должен соприкасаться с вращающимися деталями, для чего предусмотрен определенный зазор.
Однако если зазор будет очень мал, то это неизбежно приведет к нагреванию поверхностей трущихся пар и быстрому их износу.
Основной деталью фрикционной передачи является фрикционное колесо, которое и передает вращательные движения с одного вала на другой (оно может быть текстолитовым, фибровым, кожаным, деревянным или резиновым). Величина передаваемого крутящего момента зависит от коэффициента трения фрикционных пар, а также от усилия прижима друг к другу отдельных единиц фрикционной передачи. Технологический процесс сборки фрикционных передач аналогичен сборке зубчатых колес.
В ременных передачах движение передается посредством гибкого, замкнутого в кольцо, ремня, надетого на два шкива. Ремни могут быть плоскими, клиновыми и круглыми.
Плоские ремни изготавливаются из кожи, прорезиненных или хлопчатобумажных тканей, шерсти или шелка. Перед установкой такие ремни подвергают растягиванию в течение 3–5 суток, затем концы ремней соединяют склеиванием, сшиванием или с помощью металлических прижимов. Самый лучший способ соединения – склеивание (кожаные – косым швом, прорезиненные – ступенчатым). Для склеивания кожаных ремней используют мездровый, желатиновый, целлюлозный, рыбный клеи, для прорезиненных – резиновые тиуратовые клеи 1-го и 2-го сортов в равных долях. Концы кожаных ремней перед склеиванием тщательно зачищают, наносят два слоя клея с интервалом в 5–6 минут и накладывают ремни друг на друга. Затем клееный шов зажимают между двумя дощечками, которые стягивают болтами, и выдерживают в течение 5–8 часов.
Концы прорезиненных ремней зачищают ножом, затем напильником делают ступенчатые уступы и обезжиривают бензином, наносят 3–4 слоя клея (перед нанесением последующего слоя предыдущий просушивают), после нанесения последнего слоя (без просушки) концы соединяют, зажимают струбцинами между двумя дощечками и выдерживают при температуре 16–20 °C 24 часа (или при температуре 100 °C – 3–4 часа). Используют плоские ремни в передачах со скоростью вращения до 30 м/с.
Клиновые ремни могут быть кордтканевые или кордшнуровые, с гладким и зубчатым профилем, угол трапецеидальной формы – 40°.
Обладая достаточной гибкостью и большей, по сравнению с плоскими ремнями, прочностью, клиновые ремни используются для передачи мощностей от 0,3 до 75 кВт (в зависимости от профиля и длины ремня). Шкивы для клиноременных передач на ободе имеют канавки клиновидной формы, с углом профиля 34–40°.
Ремни круглого профиля бывают кожаными, хлопчатобумажными, капроновыми или прорезиненными, диаметром от 2 до 20 мм. Область применения та же, что и у плоских ремней. Профиль канавки шкива круглоременной передачи полукруглый, с радиусом, равным радиусу ремня.
Технологический процесс сборки ременной передачи состоит из следующих этапов:
– балансировка шкивов, то есть устранение их неуравновешенности. Она достигается либо путем высверливания части металла из шкива, либо путем нагружения его специальными грузиками;
– установка шкивов на валы. Их напрессовывают и закрепляют шпонкой или шлицем (следует учесть, что для напрессовки шкива на вал нельзя пользоваться ударными инструментами, поэтому ее осуществляют с помощью специальных приспособлений);
– регулирование передачи заключается в создании определенного усилия натяжения ремня. Натяжение проверяют динамометром или гирями, подвешенными за скобу (при воздействии определенной силы от 50 до 100 Н или при определенном весе гирь должен быть такой же прогиб ремня, который задается техническими условиями для каждого конкретного механизма). При слабом натяжении ремень проскальзывает при работе механизма или «бьет» (хлопает), нагревается, что приводит к его быстрому износу; чрезмерное натяжение ремня создает излишнюю нагрузку на подшипники, а также ведет к быстрому износу шеек вала и шкивов. Регулировка натяжения производится перемещением натяжного ролика.
Работоспособность ременной механической передачи характеризуется величиной углов обхвата (угол, образуемый лучами, выходящими из центра шкива и проходящими через крайние точки сопряжения шкива с ремнем). Определяющим является угол обхвата меньшего шкива, он должен быть не менее 120°. Это условие выполняется, если отношение величины диаметра ведущего шкива к величине диаметра ведомого находится в пределах от 1/3 до 3, а межосевое расстояние не меньше удвоенной суммы величин диаметров обоих шкивов. Фрикционные передачи (рис. 67) передают вращательные движения между валами с помощью силы трения.
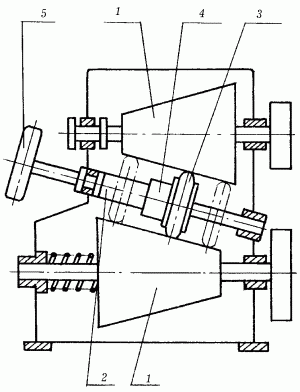
Самые распространенные механизмы, в которых используются фрикционные передачи, – фрикционные муфты и тормоза.
Фрикционные муфты, в зависимости от назначения, могут быть сцепными (находящимися в постоянном сцеплении, но при необходимости разъединяющимися), например муфта сцепления в автомобиле, или предохранительными – они предохраняют привод от поломок во время перегрузок.
Название тормоза говорит само за себя: это устройство для уменьшения скорости, вплоть до полной остановки машины. Тормоз любого механизма характеризуется двумя показателями: временем торможения и скоростью, при которой начинается торможение.
Время торможения зависит от контакта тормозной колодки или ленты с вращающимися элементами тормоза, поэтому важно плотное прилегание фрикционного материала к колодке или ленте (без складок, выпучиваний и выступаний головок заклепок), а площадь его контакта с поверхностью торможения должна быть не менее 80 %.
Во время работы механизма, то есть при бездействии тормоза, фрикционный материал не должен соприкасаться с вращающимися деталями, для чего предусмотрен определенный зазор.
Однако если зазор будет очень мал, то это неизбежно приведет к нагреванию поверхностей трущихся пар и быстрому их износу.
Основной деталью фрикционной передачи является фрикционное колесо, которое и передает вращательные движения с одного вала на другой (оно может быть текстолитовым, фибровым, кожаным, деревянным или резиновым). Величина передаваемого крутящего момента зависит от коэффициента трения фрикционных пар, а также от усилия прижима друг к другу отдельных единиц фрикционной передачи. Технологический процесс сборки фрикционных передач аналогичен сборке зубчатых колес.
Сборка кривошипно-шатунных механизмов
Зачастую домашним слесарям приходится сталкиваться с ремонтом паровых двигателей, двигателей внутреннего сгорания, компрессоров, поршневых насосов.
Работа всех этих механизмов основана на преобразовании поступательного движения поршня во вращательное движение вала, и наоборот: они преобразуют вращательные движения вала в поступательные движения поршня. Называются такие двигатели кривошипно-шатунными механизмами (рис. 68).
Рис. 68. Сборка кривошипно-шатунного механизма: а – кривошипно-шатунный механизм: 1 – поршень; 2 – шатун; 3 – коленчатый вал; 4 – маховик.
Рис. 68 (продолжение). Сборка кривошипно-шатунного механизма: б – шатунно-поршневая группа перед сборкой: 1 – поршень; 2 – поршневые кольца; 3 – поршневой палец; 4 – шатун; 5 – верхний вкладыш; 6 – нижний вкладыш; 7 – болт; 8 – гайка со шплинтом; 9 – крышка нижней головки; 10 – втулка; в – щипцы для монтажа поршневых колец.
Сборочными единицами кривошипно-шатунного механизма являются:
– коленчатый вал (кривошип или кривошипный диск в зависимости от вида двигателя) – наиболее ответственная часть механизма; именно он преобразует поступательные движения поршневой группы во вращательные (и наоборот);
– маховик, имея большую массу и обладая большой инерцией, он облегчает пуск двигателя, делает переход от одной частоты вращений (скорости) к другой наиболее плавным, уменьшает неравномерность вращения вала и выводит поршни во время работы механизма из «мертвых точек»;
– шатун механизма, который соединяет коленчатый вал (кривошип или кривошипный диск) с поршневой группой;
– поршневая группа – этот элемент механизма передает осевое усилие, создаваемое в цилиндре давлением пара или газа (в двигателях внутреннего сгорания и паровых котлах), или, напротив, воспринимает осевые усилия от вращения вала, осуществляя сжатие и подачу воздуха, газа или жидкости (в компрессорах и поршневых насосах).
Сборка кривошипно-шатунного механизма происходит поэтапно: собирают отдельно поршень, осуществляют предварительную сборку шатуна, сочленяют поршень с шатуном и устанавливают шатунно-поршневую группу на вал.
Сборка поршня начинается с подбора его по гильзам цилиндров, и главное здесь – обеспечить необходимую герметичность (поршень, помимо преобразования одного вида энергии в другую, должен препятствовать проникновению масла из картера в цилиндр, а также отводить в стенки цилиндра и в смазывающий материал теплоту, которая возникает при сгорании топлива; вместе с этим поршень не должно заклинивать и между гильзой цилиндра и поршнем должен находиться смазочный слой). Необходимой герметичности можно достигнуть правильным подбором зазора между стенками цилиндра и поршнем, причем зазор этот должен быть неодинаков по высоте поршня в связи с неравномерным его нагревом (а соответственно, и расширением) во время работы. Наименьший зазор в холодном состоянии должен приходиться на нижнюю часть поршня, именно она центрирующая для поршня. Примерный зазор составляет: для поршней из чугуна – от 0,001 до 0,002 диаметра цилиндра, для поршней из алюминия – от 0,002 до 0,004 диаметра.
В верхней и нижней частях поршня в канавки устанавливают поршневые кольца. Кольца эти должны обладать определенной упругостью (ее принимают за усилие сжатия до касания замка, равное 35–70 Н). К сборке допускаются только качественно обработанные кольца: без трещин, следов обработки, разрушения граней. Для установки колец применяют специальные щипцы (рис. 68, в), разводящие концы колец, но ограничивающие этот развод, так как чрезмерно большой развод является причиной поломки колец или образования на них трещин. При установке колец замки (места стыков концов колец) должны быть сдвинуты относительно замков соседних колец под углом 90, 120 и 180°, величина зазора в замках должна быть в пределах 0,02–0,5 мм.
При предварительной сборке шатуна в его верхнюю головку запрессовывают втулку и производят чистовое развертывание отверстия втулки (поскольку в процессе запрессовки его диаметр уменьшается). Затем подбирают верхний и нижний вкладыши, их внутренняя и наружная поверхности должны быть чистыми, гладкими, без царапин, рисок, вмятин и других дефектов. Вкладыши тщательно протирают салфетками, обдувают, устанавливают на место, закрывают нижней головкой и закрепляют ее болтами с гайкой. Далее проверяют правильность отверстия под подшипники с обеих сторон (на предмет обнаружения эллипсности и конусообразности), для чего используют индикаторный нутромер.
Собранный шатун сочленяют с поршнем поршневым пальцем. Зазор между цилиндрической поверхностью пальца и стенок отверстия втулки шатуна при нагревании во время работы механизма должен находиться в пределах 0,03–0,05 мм, поэтому палец пригоняют к отверстию втулки шатуна с малым зазором или натягом. При запрессовке пальца поршень (без колец) рекомендуется нагреть в масляной ванне до температуры 80–90 °C, а сам палец – смазать маслом. Запрессовку производят деревянным молотком.
При установке шатунно-поршневой группы на коленчатый вал нижнюю головку шатуна разбирают, шатунную шейку вала смазывают тонким слоем смазочного масла, поршень с шатуном вставляют в цилиндр и нижнюю головку вновь собирают, резьбовое соединение гайка-болт стопорят шплинтом.
При установке шатуна на шейку вала между поверхностями шейки вала и вкладышей шатуна необходимо оставить зазор (при диаметре шейки 80–100 мм – не более 0,08–0,14 мм) для смазочного материала. Величину зазора вычисляют как разницу между внутренним диаметром вкладышей шатуна в сборе и наружным диаметром шейки вала.
Этот зазор также позволяет шатуну самоустанавливаться при несовпадении осей цилиндра и шейки вала.
В некоторых случаях для преобразования вращательных движений в поступательные и наоборот использовать кривошипно-шатунный механизм не представляется возможным. В этих случаях применяют его разновидности: эксцентриковый, кривошипно-ползунный, кривошипно-кулисный и пр. Однако эти виды механизмов используются в основном в станкостроении, при производстве промышленного оборудования для металло-, деревообработки и т. д. Для домашнего мастера они вряд ли будут представлять интерес.
Работа всех этих механизмов основана на преобразовании поступательного движения поршня во вращательное движение вала, и наоборот: они преобразуют вращательные движения вала в поступательные движения поршня. Называются такие двигатели кривошипно-шатунными механизмами (рис. 68).
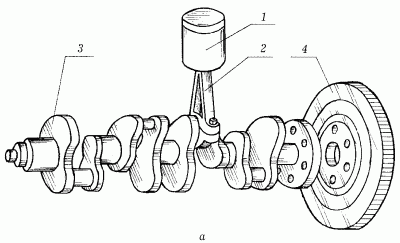
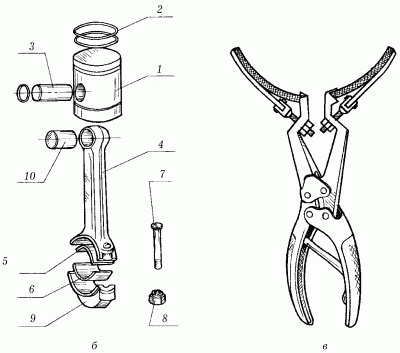
Сборочными единицами кривошипно-шатунного механизма являются:
– коленчатый вал (кривошип или кривошипный диск в зависимости от вида двигателя) – наиболее ответственная часть механизма; именно он преобразует поступательные движения поршневой группы во вращательные (и наоборот);
– маховик, имея большую массу и обладая большой инерцией, он облегчает пуск двигателя, делает переход от одной частоты вращений (скорости) к другой наиболее плавным, уменьшает неравномерность вращения вала и выводит поршни во время работы механизма из «мертвых точек»;
– шатун механизма, который соединяет коленчатый вал (кривошип или кривошипный диск) с поршневой группой;
– поршневая группа – этот элемент механизма передает осевое усилие, создаваемое в цилиндре давлением пара или газа (в двигателях внутреннего сгорания и паровых котлах), или, напротив, воспринимает осевые усилия от вращения вала, осуществляя сжатие и подачу воздуха, газа или жидкости (в компрессорах и поршневых насосах).
Сборка кривошипно-шатунного механизма происходит поэтапно: собирают отдельно поршень, осуществляют предварительную сборку шатуна, сочленяют поршень с шатуном и устанавливают шатунно-поршневую группу на вал.
Сборка поршня начинается с подбора его по гильзам цилиндров, и главное здесь – обеспечить необходимую герметичность (поршень, помимо преобразования одного вида энергии в другую, должен препятствовать проникновению масла из картера в цилиндр, а также отводить в стенки цилиндра и в смазывающий материал теплоту, которая возникает при сгорании топлива; вместе с этим поршень не должно заклинивать и между гильзой цилиндра и поршнем должен находиться смазочный слой). Необходимой герметичности можно достигнуть правильным подбором зазора между стенками цилиндра и поршнем, причем зазор этот должен быть неодинаков по высоте поршня в связи с неравномерным его нагревом (а соответственно, и расширением) во время работы. Наименьший зазор в холодном состоянии должен приходиться на нижнюю часть поршня, именно она центрирующая для поршня. Примерный зазор составляет: для поршней из чугуна – от 0,001 до 0,002 диаметра цилиндра, для поршней из алюминия – от 0,002 до 0,004 диаметра.
В верхней и нижней частях поршня в канавки устанавливают поршневые кольца. Кольца эти должны обладать определенной упругостью (ее принимают за усилие сжатия до касания замка, равное 35–70 Н). К сборке допускаются только качественно обработанные кольца: без трещин, следов обработки, разрушения граней. Для установки колец применяют специальные щипцы (рис. 68, в), разводящие концы колец, но ограничивающие этот развод, так как чрезмерно большой развод является причиной поломки колец или образования на них трещин. При установке колец замки (места стыков концов колец) должны быть сдвинуты относительно замков соседних колец под углом 90, 120 и 180°, величина зазора в замках должна быть в пределах 0,02–0,5 мм.
При предварительной сборке шатуна в его верхнюю головку запрессовывают втулку и производят чистовое развертывание отверстия втулки (поскольку в процессе запрессовки его диаметр уменьшается). Затем подбирают верхний и нижний вкладыши, их внутренняя и наружная поверхности должны быть чистыми, гладкими, без царапин, рисок, вмятин и других дефектов. Вкладыши тщательно протирают салфетками, обдувают, устанавливают на место, закрывают нижней головкой и закрепляют ее болтами с гайкой. Далее проверяют правильность отверстия под подшипники с обеих сторон (на предмет обнаружения эллипсности и конусообразности), для чего используют индикаторный нутромер.
Собранный шатун сочленяют с поршнем поршневым пальцем. Зазор между цилиндрической поверхностью пальца и стенок отверстия втулки шатуна при нагревании во время работы механизма должен находиться в пределах 0,03–0,05 мм, поэтому палец пригоняют к отверстию втулки шатуна с малым зазором или натягом. При запрессовке пальца поршень (без колец) рекомендуется нагреть в масляной ванне до температуры 80–90 °C, а сам палец – смазать маслом. Запрессовку производят деревянным молотком.
При установке шатунно-поршневой группы на коленчатый вал нижнюю головку шатуна разбирают, шатунную шейку вала смазывают тонким слоем смазочного масла, поршень с шатуном вставляют в цилиндр и нижнюю головку вновь собирают, резьбовое соединение гайка-болт стопорят шплинтом.
При установке шатуна на шейку вала между поверхностями шейки вала и вкладышей шатуна необходимо оставить зазор (при диаметре шейки 80–100 мм – не более 0,08–0,14 мм) для смазочного материала. Величину зазора вычисляют как разницу между внутренним диаметром вкладышей шатуна в сборе и наружным диаметром шейки вала.
Этот зазор также позволяет шатуну самоустанавливаться при несовпадении осей цилиндра и шейки вала.
В некоторых случаях для преобразования вращательных движений в поступательные и наоборот использовать кривошипно-шатунный механизм не представляется возможным. В этих случаях применяют его разновидности: эксцентриковый, кривошипно-ползунный, кривошипно-кулисный и пр. Однако эти виды механизмов используются в основном в станкостроении, при производстве промышленного оборудования для металло-, деревообработки и т. д. Для домашнего мастера они вряд ли будут представлять интерес.
Трубопроводные системы
Кран на кухне вышел из строя, лопнула труба центрального отопления, на дачном участке возникла необходимость проложить водопроводную систему орошения... Ремонт и замена элементов различных действующих трубопроводных систем, а тем более конструирование и установка новых также дело слесаря. Конечно же, можно вызвать слесаря из жилищно-коммунального отдела или дачного кооператива или пригласить мастера по объявлению, но лучше сэкономить массу финансов и нервов, если самостоятельно взяться за дело, вооружившись необходимыми знаниями, навыками и соответствующим инвентарем.
Конструктивные особенности трубопроводов
У различных по функциональному назначению коммуникаций – водопровода, газопровода, канализации и отопительной системы – есть нечто общее, что их объединяет. А именно: у всех перечисленных систем имеются последовательно соединенные трубы, то есть трубопроводы, по которым под определенным давлением (или самотеком) перемещаются вода или газ.
Главное требование, которое предъявляется ко всем трубопроводам, – сохранять свою непроницаемость на всем протяжении независимо от увеличения или уменьшения длины, от действия температурных изменений.
Сначала о том, из чего могут монтироваться трубопроводы:
– водопроводная коммуникация представляет собой трубопровод из труб диаметром 3/4 и 1/2 дюйма: из первых монтируются главные линии, вторые нужны для подводки к конкретному прибору-потребителю. Соответственно диаметру труб подбираются фитинги, вентили и краны.
Самым распространенным материалом для изготовления труб являются мягкие сорта обычной стали: они относительно недороги и легко поддаются обработке, но подвержены коррозии.
Поэтому лучше использовать трубы из нержавеющей или оцинкованной стали (срок их службы гораздо дольше, чем у труб из обыкновенной стали, вследствие высокой коррозийной устойчивости);
– для газового трубопровода применяются стальные трубы диаметром 1/2 дюйма, а также фитинги и вентили соответствующего размера (краны в газопровод не монтируются);
– для монтажа отопительной системы нужны: трубы диаметром 60–100 мм (если система отопления двухтрубная) или 3/4 дюйма (если в систему включены излучающие элементы – радиаторы), фитинги подходящего диаметра, вентили, возможно, краны. Если устраивается автономная отопительная система, то потребуется нагревательный прибор (это могут быть котел АОГВ или печь) и расширительный бачок;
– для устройства системы канализационной коммуникации используются чугунные, пластиковые, керамические трубы большого диаметра: около 60 мм – для отвода от раковины, мойки, ванны, душа, около 100 мм – для отвода от унитаза и общей линии. Для подводки к конкретному источнику канализационных сбросов потребуются уголки и тройники из того же материала и соответствующего диаметра. При выборе труб по материалу для канализационной системы необходимо помнить, что: чугунные трубы прочны, но тяжелы и подвержены коррозии; трубы из пластмассы имеют высокую коррозийную стойкость, низкую теплопроводность, гладкую поверхность, хорошо поддаются механической обработке, но вместе с тем обладают большой чувствительностью к механическим повреждениям, хрупкостью при низких температурах, подвержены значительным тепловым деформациям; керамические трубы очень долговечны, если на них не оказываются механические воздействия.
А теперь о некоторых особенностях каждого из многочисленных видов трубопроводов.
Водопровод.В месте подсоединения к магистральной линии централизованного водоснабжения обязательно должен быть установлен запорный вентиль на случай экстренного индивидуального прекращения подачи воды (например, если потребовалось заменить трубы или просто поменять прокладки у крана, то от этого не должны страдать соседи). Желательно, чтобы запорные вентили были также установлены перед каждым прибором-потребителем воды (например, перед смывным бачком, душевой кабиной и пр.). Рабочее положение запорных вентилей – «открыто».
Прокладывая дачный водопровод, в месте подсоединения к магистральной линии (рядом в запорным вентилем) устанавливают кран для слива воды из системы. И хотя этим краном приходится пользоваться только один раз в год, не стоит пренебрегать данным советом: на зимний период оставлять воду в трубах системы нельзя, так как при минусовых температурах вода замерзает и расширяется, в результате чего трубы могут лопнуть. На зиму кран следует оставить в открытом состоянии, а вентиль – в закрытом.
Главное требование, которое предъявляется ко всем трубопроводам, – сохранять свою непроницаемость на всем протяжении независимо от увеличения или уменьшения длины, от действия температурных изменений.
Сначала о том, из чего могут монтироваться трубопроводы:
– водопроводная коммуникация представляет собой трубопровод из труб диаметром 3/4 и 1/2 дюйма: из первых монтируются главные линии, вторые нужны для подводки к конкретному прибору-потребителю. Соответственно диаметру труб подбираются фитинги, вентили и краны.
Самым распространенным материалом для изготовления труб являются мягкие сорта обычной стали: они относительно недороги и легко поддаются обработке, но подвержены коррозии.
Поэтому лучше использовать трубы из нержавеющей или оцинкованной стали (срок их службы гораздо дольше, чем у труб из обыкновенной стали, вследствие высокой коррозийной устойчивости);
– для газового трубопровода применяются стальные трубы диаметром 1/2 дюйма, а также фитинги и вентили соответствующего размера (краны в газопровод не монтируются);
– для монтажа отопительной системы нужны: трубы диаметром 60–100 мм (если система отопления двухтрубная) или 3/4 дюйма (если в систему включены излучающие элементы – радиаторы), фитинги подходящего диаметра, вентили, возможно, краны. Если устраивается автономная отопительная система, то потребуется нагревательный прибор (это могут быть котел АОГВ или печь) и расширительный бачок;
– для устройства системы канализационной коммуникации используются чугунные, пластиковые, керамические трубы большого диаметра: около 60 мм – для отвода от раковины, мойки, ванны, душа, около 100 мм – для отвода от унитаза и общей линии. Для подводки к конкретному источнику канализационных сбросов потребуются уголки и тройники из того же материала и соответствующего диаметра. При выборе труб по материалу для канализационной системы необходимо помнить, что: чугунные трубы прочны, но тяжелы и подвержены коррозии; трубы из пластмассы имеют высокую коррозийную стойкость, низкую теплопроводность, гладкую поверхность, хорошо поддаются механической обработке, но вместе с тем обладают большой чувствительностью к механическим повреждениям, хрупкостью при низких температурах, подвержены значительным тепловым деформациям; керамические трубы очень долговечны, если на них не оказываются механические воздействия.
А теперь о некоторых особенностях каждого из многочисленных видов трубопроводов.
Водопровод.В месте подсоединения к магистральной линии централизованного водоснабжения обязательно должен быть установлен запорный вентиль на случай экстренного индивидуального прекращения подачи воды (например, если потребовалось заменить трубы или просто поменять прокладки у крана, то от этого не должны страдать соседи). Желательно, чтобы запорные вентили были также установлены перед каждым прибором-потребителем воды (например, перед смывным бачком, душевой кабиной и пр.). Рабочее положение запорных вентилей – «открыто».
Прокладывая дачный водопровод, в месте подсоединения к магистральной линии (рядом в запорным вентилем) устанавливают кран для слива воды из системы. И хотя этим краном приходится пользоваться только один раз в год, не стоит пренебрегать данным советом: на зимний период оставлять воду в трубах системы нельзя, так как при минусовых температурах вода замерзает и расширяется, в результате чего трубы могут лопнуть. На зиму кран следует оставить в открытом состоянии, а вентиль – в закрытом.