Страница:
Для формовки, собственно литья и хранения топлива необходимо предусмотреть отдельные помещения. Они должны хорошо сообщаться между собой, что облегчает переноску тяжелых форм от одного участка к другому.
Самое просторное помещение отводится для литейной. В центре, подальше от стен, ставится печь. Пол вокруг делается земляным или выкладывается кирпичом.
В стороне ставится невысокий верстак для литейной формы. Уровень расположения литейной чаши не должен быть выше уровня верхней части печи, чтобы при работе ковш не приходилось поднимать.
Одежду литейщика следует делать из прочного материала, хорошо защищающего от тепла. Высокие ботинки на толстой подошве предохраняют ноги во время работы около печи. На руках обязательно должны быть перчатки, а при заливке – рукавицы из двухслойного брезента.
Комната для формовки должна иметь не только хорошее дневное, но и искусственное освещение. Литниковые системы собираются на широком верстаке, за которым должно быть одинаково удобно и сидеть, и стоять. Большие формы заполняются и собираются прямо на полу.
Стол должен иметь жесткую крышку и прочно стоять на ножках, поскольку масса некоторых заполненных форм довольно велика. Вокруг него располагают ящики с инструментами, необходимыми при формовке, и съемными частями литниковых форм.
Многоразовые опоки средних размеров, очищенные от остатков формовочного материала, хранятся в специальном шкафу. Песок и глину держат в больших стационарных ящиках.
Обычно начинающему литейщику доступны два легкоплавких материала – свинец и олово. Пользоваться первым не рекомендуется, несмотря на всю простоту его обработки в домашних условиях. Во-первых, свинец ядовит и дышать его парами опасно. Во-вторых, от неосторожных опытов могут пострадать близкие и соседи.
Инструменты
Материалы
В зависимости от их применения формовочные материалы подразделяются на исходные материалы и смеси, а исходные, в свою очередь, – на основные и вспомогательные. Они имеют также рабочие свойства: природные и технологические. Природные свойства характерны для исходных формовочных материалов – песков и глин. К ним относятся морфологический, зерновой и химический составы материалов.
В зависимости от размера изделия и толщины его стенок в качестве припыла применяют древесноугольный порошок, серебристый или черный графит, цемент и маршаллит.
Залитый в форму металл при кристаллизации и охлаждении уменьшается в объеме, и готовая отливка будет иметь несколько меньшие размеры, чем полость формы. Такое явление называют усадкой отливки.
Литейная форма не должна сопротивляться усадке металла. Иначе в стенках отливки могут образоваться трещины из-за напряжений, возникающих в металле.
Свойство формовочной смеси, характеризующее сопротивление усадке отливки в форме, называется податливостью.
Залитый в форму сплав при охлаждении теряет объем. Это называется усадкой, которая бывает объемной и линейной. Если в отливках возникают внутренние напряжения, вызывающие трещины, пористость, усадочные раковины, то причиной этому стала усадка.
Она также негативно влияет на объем и размеры изготовляемых отливок.
При кристаллизации сплава возникает неоднородность химического состава – это ликвация, которая наиболее выражена в массивных сечениях изделия.
Латунь –это сплав меди с цинком. Иногда добавляют и другие химические элементы. Эти сплавы чаще всего используют при изготовлении отливок со сложной поверхностью, потому что они имеют более плотную структуру и малую газовую пористость.
Техника формовки
Самое просторное помещение отводится для литейной. В центре, подальше от стен, ставится печь. Пол вокруг делается земляным или выкладывается кирпичом.
В стороне ставится невысокий верстак для литейной формы. Уровень расположения литейной чаши не должен быть выше уровня верхней части печи, чтобы при работе ковш не приходилось поднимать.
Одежду литейщика следует делать из прочного материала, хорошо защищающего от тепла. Высокие ботинки на толстой подошве предохраняют ноги во время работы около печи. На руках обязательно должны быть перчатки, а при заливке – рукавицы из двухслойного брезента.
Комната для формовки должна иметь не только хорошее дневное, но и искусственное освещение. Литниковые системы собираются на широком верстаке, за которым должно быть одинаково удобно и сидеть, и стоять. Большие формы заполняются и собираются прямо на полу.
Стол должен иметь жесткую крышку и прочно стоять на ножках, поскольку масса некоторых заполненных форм довольно велика. Вокруг него располагают ящики с инструментами, необходимыми при формовке, и съемными частями литниковых форм.
Многоразовые опоки средних размеров, очищенные от остатков формовочного материала, хранятся в специальном шкафу. Песок и глину держат в больших стационарных ящиках.
Обычно начинающему литейщику доступны два легкоплавких материала – свинец и олово. Пользоваться первым не рекомендуется, несмотря на всю простоту его обработки в домашних условиях. Во-первых, свинец ядовит и дышать его парами опасно. Во-вторых, от неосторожных опытов могут пострадать близкие и соседи.
Оборудование для микролитья
Другой металл – олово издавна использовался для отливки небольших предметов быта, а также игрушек. Помните сказку Г. Х. Андерсена «Стойкий оловянный солдатик»? Чтобы сделать фигурку из олова, понадобится большой опыт формовки, но сам металл крайне прост в обращении. Рабочее место оборудовать совсем несложно. Прежде всего необходим просторный стол, за которым можно было бы стоя собирать литейные формы и производить засыпку формовочной смеси. Место должно быть хорошо освещено, поскольку формы для микролитья (именно так называется отливка небольших изделий) по сложности не отличаются от обычных, хотя размеры их гораздо меньше.
Инструменты
Литье – сложный технологический процесс, требующий большого терпения. Для литья различных изделий необходимы специально изготовленные формы-опоки, модели, стержневые ящики для изготовления стержней и разнообразные инструменты. Могут потребоваться также шаблоны (формовочные, скребковые, контрольные) и кондукторы для зачистки стержней.
Все перечисленные приспособления и являются для литейщика специальными инструментами, с помощью которых можно создать в домашних условиях самые разнообразные изделия из металла.
Модель служит для создания отпечатка в литейной форме, именно с ее помощью будущему изделию задаются необходимые контуры. В ручном литье, как правило, используются неразъемные и разъемные деревянные, пластиковые и гипсовые модели.
Чаще всего при ручном литье для изготовления штучных (наиболее сложных) изделий используют деревянные модели, предназначенные для неоднократного применения. Подобную модель несложно изготовить в домашних условиях.
Для этого отбирают наиболее прочные породы деревьев: ольху, сосну, бук. Отдельные детали в разъемных моделях можно изготовить из березовой и буковой фанеры и затем скрепить их с помощью гвоздей, шурупов, болтов, нагелей или просто склеить.
Такие части моделей в процессе формовки очень быстро изнашиваются, и потому их лучше всего готовить из особенно твердых пород деревьев, а также из древесного слоистого пластика ДСП-8, металла или пластмассы. Чтобы предназначенные для затачивания форм и стержней шаблоны служили долго, их предварительно армируют – обвертываютстальной пластиной толщиной 2–5 мм.
Поверхность моделей отливки должна быть достаточно ровной и гладкой. Для того чтобы добиться этого, ее необходимо покрыть двойным слоем модельного лака. Делают это, как правило, после грунтовки и шпатлевки поверхности.
1. Простые (это обычно неразъемные или с разъемом по плоскости модели без отъемных деталей и стержневых знаков).
2. Средней сложности (это модели средние – от 500 до 1500 мм и крупные – от 1501 мм и более, со стержневыми ящиками).
3. Сложные (это разъемные модели крупных размеров, предназначенные для литья таких больших деталей машин, как блок цилиндра внутреннего сгорания, станины металлорежущих станков и др.).
По конструкции все модели отливок разделяют (рис. 161) на:
1. Неразъемные (рис. 161, а). Такие модели часто используют при ручном литье. Их достают из формы, не разделяя на части (хотя в некоторых случаях применяют и состоящие из нескольких мелких деталей шаблоны – рис. 161, в). Причем при формовке они оставляют четкий отпечаток наружного контура требуемой модели.
2. Разъемные (рис. 161, б). Модели подобного типа состоят обычно из нескольких частей, легко отделяющихся друг от друга по плоскости (или по сложной поверхности) детали.
3. Специальные (формовочные шаблоны и скелетные модели). Их часто применяют для формовки штучных изделий из металла.
Рис. 161. Модели отливок: а, в – неразъемные; б – разъемные.
Для предохранения отливки от разрушения необходимо в наиболее прочных местах установить металлические пластины, в которых предварительно проделать отверстия для стержня. Такие пластины могут быть комбинированными, то есть иметь два отверстия: одно для расталкивателя, а другое, с резьбой, для установки в модели подъема.
Бывают также металлические литейные формы. Они называются кокилями и используются при производстве отливок специальными способами литья.
Рис. 162. Литейная форма: а, б – полуформы-опоки; в – крестовины опок; г – штырь; д – литниковая чаша; е – холодильник; ж – полость формы.
Опоки, как правило, заполняют смесью из неорганичеких (кварцевый песок, глина) и органических (уголь, опилки) материалов. На боковой стороне опок необходимо сделать цапфы или небольшие ручки для удобства транспортировки.
Опоки по внешнему виду напоминают деревянные или металлические рамки (рис. 163, 164).
Рис. 163. Деревянная опока для ручной формовки.
Рис. 164. Опока из фасонного проката.
Предназначены они для уплотнения формовочной смеси при ручном изготовлении литейных форм и потому должны быть очень прочными и достаточно легкими.
При ручной формовке рекомендуют использовать небольшие по размерам и массе (до 30 кг – без смеси, до 60 кг – со смесью) опоки, которые впоследствии можно будет достаточно легко перемещать.
При литье в домашних условиях очень важно правильно выбрать опоку необходимого размера, чтобы при ее использовании не произошло разрушения формы. При выборе и установке опоки нужно учитывать следующие параметры:
– расстояние между полостью формы и стенкой мелкой опоки должно составлять 30–50 мм, крупной – от 100 до 150 мм;
– расстояние от стержневого знака до боковой стенки опоки не должно превышать 50 мм;
– расстояние от модели до верхней или нижней поверхности мелкой опоки должно быть 40–60 мм, средней опоки – 60–120 мм, крупной – более 100 мм;
– расстояние от нижнего знака стержня до нижней части опоки может составлять от 20 до 120 мм;
– от верхнего знака стержня до верхней части опоки следует выдерживать расстояние в 50–120 мм;
– при формовке сразу нескольких отливок в одной опоке расстояние между полостями формы должно быть не менее 20–25 мм для тонкостенных и невысоких отливок и 30–50 мм при изготовлении форм с высокими и толстыми стенками.
1. Штырем (рис. 165, а). В данном случае при скреплении деталей используемые металлические штыри вставляют в отверстия ушек верхней опоки.
2. На штырь (рис. 165, б). При этом способе скрепления верхнюю опоку надевают на штыри, предварительно закрепленные на нижней.
Рис. 165. Способы скрепления опок: а – штырем; б – на штырь.
Литейный стержень по внешнему виду напоминает штырь. С его помощью при литье делают необходимые отверстия и задают нужные контуры будущей отливке. В форме его закрепляют на специально сделанном для этого выступе, который в процессе производства отливки входит в соответствующую ему впадину.
Подобная система, как правило, состоит из литниковой чаши (воронки), стояка, шлакоуловителя, питателей и прибылей.
Рис. 166. Виды литниковых воронок: а – простая; б – в форме чаши.
Для изготовления небольших по размеру отливок из алюминия или чугуна в форме проделывают воронку (рис. 166, а). Для литья крупных изделий в форме создают чашу (рис. 166, б). Причем выступ на ее дне служит в качестве своеобразного шлакоуловителя.
Поскольку плотность жидкого металла и шлаков различна, последние быстрее всплывают на поверхность. В остывшем вязком сплаве этот процесс идет медленнее, и мелкие включения не успевают всплывать на поверхность. Поэтому очистку лучше проводить, пока металл еще не успел охладиться.
На рис. 167 представлены различные виды шлакоуловителей.
Рис. 167. Виды шлакоуловителей: а – обычный; б – с удержанием шлака в широком канале; в – с удержанием шлака в высоком канале.
Рис. 168. Прибыли: а – полости для прибылей; б – каналы для выхода воздуха.
Внешние холодильники располагают в различных местах формы: под фланцем отливки, под полкой, в углу стенки, сверху и в углах Т-образной стенки. Такие холодильники, как правило, вклеивают внутрь формы с помощью жидкого клея.
При литье крупных изделий отдельные части холодильника (шпильки, проволочную спираль или металлическую пластину) размещают внутри полости формы, причем при взаимодействии с жидким металлом такой внутренний холодильник должен полностью расплавиться.
С этими же целями в полуформах с помощью длинных игл – душников – проделывают вентиляционые каналы.
Для лучшего сплавления их поверхность рекомендуют покрывать оловом.
Жеребейки бывают самых разнообразных конфигураций. Они должны иметь гладкую и чистую поверхность.
При этом для литья из стали нужно использовать жеребейки из низкоуглеродистой стали, для литья чугунных изделий применяют чугунные жеребейки.
При изготовлении тонкостенных отливок (толщиной не более 10 мм) лучше всего использовать жеребейки из белой жести, а при литье крупных изделий применяют литые.
Рис. 169. Служебный инструмент для ручной формовки: а – сито; б – совковая лопата; в – ручные трамбовки; г – гладилки; д – угловые гладилки; е – крючок; ж – формовочный нож; з – фигурные ложки; и – стальные иглы.
1. Инструменты, предназначенные для заполнения опоки формовочной смесью: прямоугольные или круглые сита с металлической сеткой (рис. 169, а), плоские или совковые лопаты (рис. 169, б).
2. В опоке смесь утрамбовывают с помощью ручных трамбовок (рис. 169, в), которые, в зависимости от назначения, могут быть различными: короткими – для уплотнения смеси в опоках с низкими стенками, длинными – для уплотнения смеси в крупных опоках, с острыми или тупыми концами – для уплотнения смеси, соответственно, в объеме опоки или у ее поверхности.
3. Для контроля поверхностного слоя засыпанной и утрамбованной смеси используют ватерпас, или уровень.
4. Ровную и гладкую поверхность можно создать с помощью гладилки или ланцета (рис. 169, г).
5. Выправлять углы лучше всего угловыми гладилками (рис. 169, д).
6. Упавшие внутрь формы частицы формовочной смеси можно удалить с помощью крючка (рис. 169, е).
7. Для того чтобы избежать разрушения во время извлечения модели из формы, смесь необходимо предварительно увлажнить с помощью кисти.
8. Литниковые каналы лучше всего проделывать специальными ножами (рис. 169, ж).
9. Сгребать формовочную смесь в сито удобнее с помощью скребков и совков.
10. Для выравнивания поверхности литниковых ходов часто используют фигурные ложки (рис. 169, з).
11. Вентиляционные каналы можно проделать с помощью стальных игл разных диаметров (рис. 169, и): 3–5 мм – при изготовлении небольших форм, 7–10 мм – для крупных отливок.
12. Приготовленные модели расталкивают, используя специальные молоточки – киянки.
13. Лишними не окажутся и щетки, которыми можно сметать остатки и ненужные комочки формовочной смеси.
14. Для уплотнения формовочной смеси при изготовлении достаточно больших по размеру и массе форм рекомендуют использовать пневматическую трамбовку.
15. Часто внутри форм, на крестовинах, закрепляют крючки из изогнутой низкоуглеродистой стальной проволоки, которые служат опорой для формовочной смеси. Эти крючки для лучшего сцепления со смесью можно обмазать жидкой формовочной глиной.
16. Для того чтобы лучше зафиксировать формовочную смесь в верхней опоке, в ней устанавливают деревянные колышки.
17. Такие места в форме, как выступающие части, углы, болваны и переходы от тонких сечений к толстым, закрепляют с помощью литейных гвоздей, или шпилек.
18. Проволочные или литые каркасы используют в литье в качестве «скелета» стержней. При этом в небольшие по размерам стержни вставляют каркасы из тонкой проволоки, в более крупных стержнях устанавливают каркасы либо из проволоки диаметром до 9 мм, либо литые из чугуна.
19. Каждому литейщику необходимо всегда иметь под рукой пульверизатор (для нанесения краски на детали) и пневматические сопла (для обдува готовых форм перед сборкой их частей).
Все перечисленные приспособления и являются для литейщика специальными инструментами, с помощью которых можно создать в домашних условиях самые разнообразные изделия из металла.
Модель отливки
Для создания отливки необходимо использовать приготовленную модель.Модель служит для создания отпечатка в литейной форме, именно с ее помощью будущему изделию задаются необходимые контуры. В ручном литье, как правило, используются неразъемные и разъемные деревянные, пластиковые и гипсовые модели.
Чаще всего при ручном литье для изготовления штучных (наиболее сложных) изделий используют деревянные модели, предназначенные для неоднократного применения. Подобную модель несложно изготовить в домашних условиях.
Для этого отбирают наиболее прочные породы деревьев: ольху, сосну, бук. Отдельные детали в разъемных моделях можно изготовить из березовой и буковой фанеры и затем скрепить их с помощью гвоздей, шурупов, болтов, нагелей или просто склеить.
Такие части моделей в процессе формовки очень быстро изнашиваются, и потому их лучше всего готовить из особенно твердых пород деревьев, а также из древесного слоистого пластика ДСП-8, металла или пластмассы. Чтобы предназначенные для затачивания форм и стержней шаблоны служили долго, их предварительно армируют – обвертываютстальной пластиной толщиной 2–5 мм.
Поверхность моделей отливки должна быть достаточно ровной и гладкой. Для того чтобы добиться этого, ее необходимо покрыть двойным слоем модельного лака. Делают это, как правило, после грунтовки и шпатлевки поверхности.
Виды моделей отливок
Модели отливок бывают:1. Простые (это обычно неразъемные или с разъемом по плоскости модели без отъемных деталей и стержневых знаков).
2. Средней сложности (это модели средние – от 500 до 1500 мм и крупные – от 1501 мм и более, со стержневыми ящиками).
3. Сложные (это разъемные модели крупных размеров, предназначенные для литья таких больших деталей машин, как блок цилиндра внутреннего сгорания, станины металлорежущих станков и др.).
По конструкции все модели отливок разделяют (рис. 161) на:
1. Неразъемные (рис. 161, а). Такие модели часто используют при ручном литье. Их достают из формы, не разделяя на части (хотя в некоторых случаях применяют и состоящие из нескольких мелких деталей шаблоны – рис. 161, в). Причем при формовке они оставляют четкий отпечаток наружного контура требуемой модели.
2. Разъемные (рис. 161, б). Модели подобного типа состоят обычно из нескольких частей, легко отделяющихся друг от друга по плоскости (или по сложной поверхности) детали.
3. Специальные (формовочные шаблоны и скелетные модели). Их часто применяют для формовки штучных изделий из металла.
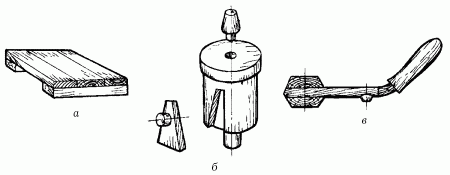
Подъемы
Для того чтобы вытолкнуть получившуюся модель, в форме устанавливают подъемы различных модификаций: остроконечные, вставные (которые часто используют для небольших по массе и размеру моделей), крючковые (также применяемые для мелких и средних моделей), вертикальные полосовые (для крупных по размеру моделей) и болтовые (для моделей с достаточно большой массой).Молотки
При извлечении отливки из формы пользуются молотками и металлическими стержнями. При этом молотком с силой ударяют в различных направлениях по нижней части стержня так, чтобы растолкать модель.Для предохранения отливки от разрушения необходимо в наиболее прочных местах установить металлические пластины, в которых предварительно проделать отверстия для стержня. Такие пластины могут быть комбинированными, то есть иметь два отверстия: одно для расталкивателя, а другое, с резьбой, для установки в модели подъема.
Литейные формы
С помощью модели отливаемого изделия, различных приспособлений и инструментов из песчаной смеси, называемой формовочной, изготавливают литейную форму. В нее заливают расплавленный металл, который заполняет полость и остывает в ней. После этого образуется отливка, внешне повторяющая очертания модели. В литейную форму можно заливать чугун, латунь, бронзу и другие сплавы.Разовые формы
Литейные формы бывают разовые и многократные. Разовые заливают металлом только один раз. После удаления отливки их разрушают. Основной составляющей формовочных смесей при изготовлении этих форм является кварцевый песок. В качестве связующей добавки используют глину. Разовые формы для художественных отливок могут быть разъемными и неразъемными, цельными и кусковыми, сухими и сырыми.Многократные формы
Прочность и огнеупорность многократных форм позволяет после каждой заливки использовать их повторно, после небольшого ремонта внутренней поверхности. Иногда их применяют до 150 раз. Изготовляют эти формы из огнеупорных материалов (молотый шамот, асбест, графит).Бывают также металлические литейные формы. Они называются кокилями и используются при производстве отливок специальными способами литья.
Опоки (полуформы)
Литейная форма состоит из двух полуформ-опок, служащих для того, чтобы удерживать смесь при ее уплотнении, а также при перемещении и закреплении полуформ (рис. 162).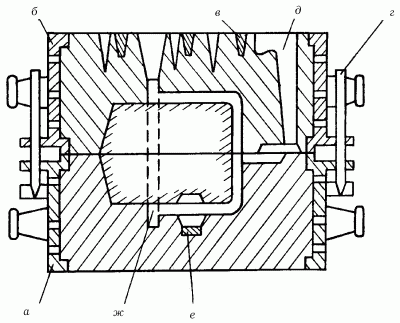
Опоки, как правило, заполняют смесью из неорганичеких (кварцевый песок, глина) и органических (уголь, опилки) материалов. На боковой стороне опок необходимо сделать цапфы или небольшие ручки для удобства транспортировки.
Опоки по внешнему виду напоминают деревянные или металлические рамки (рис. 163, 164).
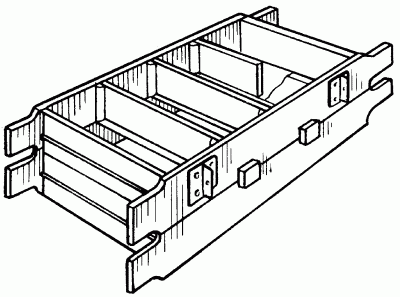
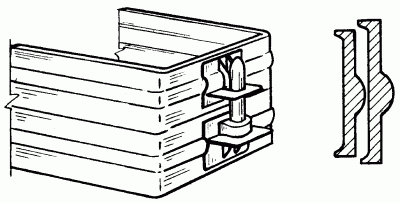
Предназначены они для уплотнения формовочной смеси при ручном изготовлении литейных форм и потому должны быть очень прочными и достаточно легкими.
При ручной формовке рекомендуют использовать небольшие по размерам и массе (до 30 кг – без смеси, до 60 кг – со смесью) опоки, которые впоследствии можно будет достаточно легко перемещать.
При литье в домашних условиях очень важно правильно выбрать опоку необходимого размера, чтобы при ее использовании не произошло разрушения формы. При выборе и установке опоки нужно учитывать следующие параметры:
– расстояние между полостью формы и стенкой мелкой опоки должно составлять 30–50 мм, крупной – от 100 до 150 мм;
– расстояние от стержневого знака до боковой стенки опоки не должно превышать 50 мм;
– расстояние от модели до верхней или нижней поверхности мелкой опоки должно быть 40–60 мм, средней опоки – 60–120 мм, крупной – более 100 мм;
– расстояние от нижнего знака стержня до нижней части опоки может составлять от 20 до 120 мм;
– от верхнего знака стержня до верхней части опоки следует выдерживать расстояние в 50–120 мм;
– при формовке сразу нескольких отливок в одной опоке расстояние между полостями формы должно быть не менее 20–25 мм для тонкостенных и невысоких отливок и 30–50 мм при изготовлении форм с высокими и толстыми стенками.
Скрепление опок
Для скрепления парных опок на их стенках необходимо сделать выступы, или приливы, в которых затем нужно высверлить отверстия, предназначенные для впрессованных стальных втулок. Две опоки можно скрепить двумя способами (рис. 165):1. Штырем (рис. 165, а). В данном случае при скреплении деталей используемые металлические штыри вставляют в отверстия ушек верхней опоки.
2. На штырь (рис. 165, б). При этом способе скрепления верхнюю опоку надевают на штыри, предварительно закрепленные на нижней.
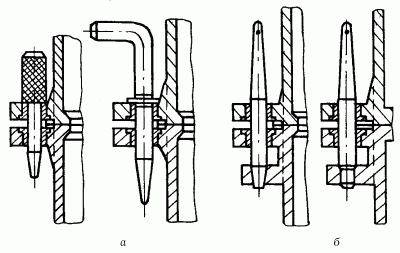
Стержневые ящики и стержни
Стержневые ящики – необходимый инвентарь литейщика. Их используют для изготовления больших партий стержней, чаще делают из песчано-глинистых смесей.Литейный стержень по внешнему виду напоминает штырь. С его помощью при литье делают необходимые отверстия и задают нужные контуры будущей отливке. В форме его закрепляют на специально сделанном для этого выступе, который в процессе производства отливки входит в соответствующую ему впадину.
Литниковая система
Литниковая система устанавливается для обеспечения плавного и равномерного продвижения жидкого металла по каналам формы, а также является своеобразным фильтром для используемого расплава.Подобная система, как правило, состоит из литниковой чаши (воронки), стояка, шлакоуловителя, питателей и прибылей.
Воронка
Из разливочного ковша расплавленный металл наливают в литниковую чашу, или воронку, которая располагается в верхней части формы (рис. 166).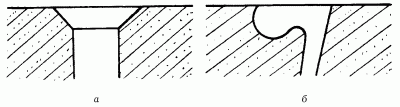
Для изготовления небольших по размеру отливок из алюминия или чугуна в форме проделывают воронку (рис. 166, а). Для литья крупных изделий в форме создают чашу (рис. 166, б). Причем выступ на ее дне служит в качестве своеобразного шлакоуловителя.
Стояк
Из литниковой чаши (или воронки) жидкий сплав попадает в стояк, обычно вертикально расположенный в верхней полуформе под углом 2–4° и имеющий коническую или цилиндрическую форму. Модели стояков лучше всего изготавливать из дерева.Шлакоуловитель
Он является своеобразным передаточным звеном, откуда очищенный от шлаков сплав поступает к питателям. По внешнему виду шлакоуловитель представляет собой горизонтально расположенный канал.Поскольку плотность жидкого металла и шлаков различна, последние быстрее всплывают на поверхность. В остывшем вязком сплаве этот процесс идет медленнее, и мелкие включения не успевают всплывать на поверхность. Поэтому очистку лучше проводить, пока металл еще не успел охладиться.
На рис. 167 представлены различные виды шлакоуловителей.
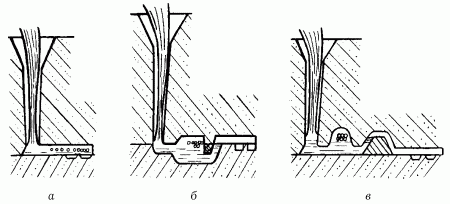
Питатели
Питатели имеют обычно прямоугольную или трапециевидную форму. Они должны легко отделяться от полученного в процессе литья и затем охлажденного изделия. Питатели чаще всего делаются прямоугольной или трапециевидной формы, реже – полукруглой. Из них жидкий металл попадает непосредственно в полость формы.Прибыли
В форме необходимо также расположить прибыли. При охлаждении некоторые металлы дают очень большую усадку, поэтому недостаток металла необходимо компенсировать. Для этого в верхних полуформах создают дополнительные каналы и полости, в которые заливается добавочный металл (рис. 168).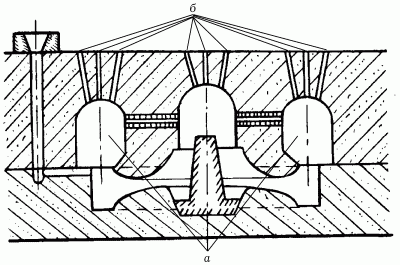
Холодильник
С помощью холодильников можно регулировать процессы охлаждения металла внутри формы. Различают внешние и внутренние холодильники.Внешние холодильники располагают в различных местах формы: под фланцем отливки, под полкой, в углу стенки, сверху и в углах Т-образной стенки. Такие холодильники, как правило, вклеивают внутрь формы с помощью жидкого клея.
При литье крупных изделий отдельные части холодильника (шпильки, проволочную спираль или металлическую пластину) размещают внутри полости формы, причем при взаимодействии с жидким металлом такой внутренний холодильник должен полностью расплавиться.
Выпоры
Для выведения из полости лишнего воздуха и образующихся в процессе литья газов в форме делают выпоры – вертикально расположенные каналы, которые выходят наружу и в полость формы.С этими же целями в полуформах с помощью длинных игл – душников – проделывают вентиляционые каналы.
Жеребейки
Для стержней при отливе необходимо установить дополнительные опоры – жеребейки, которые должны будут сплавиться с жидким металлом.Для лучшего сплавления их поверхность рекомендуют покрывать оловом.
Жеребейки бывают самых разнообразных конфигураций. Они должны иметь гладкую и чистую поверхность.
При этом для литья из стали нужно использовать жеребейки из низкоуглеродистой стали, для литья чугунных изделий применяют чугунные жеребейки.
При изготовлении тонкостенных отливок (толщиной не более 10 мм) лучше всего использовать жеребейки из белой жести, а при литье крупных изделий применяют литые.
Служебные инструменты
Помимо литейной формы, стержней и модельного комплекта, для ручного литья необходим и другой инвентарь, который условно можно разделить на несколько групп (рис. 169).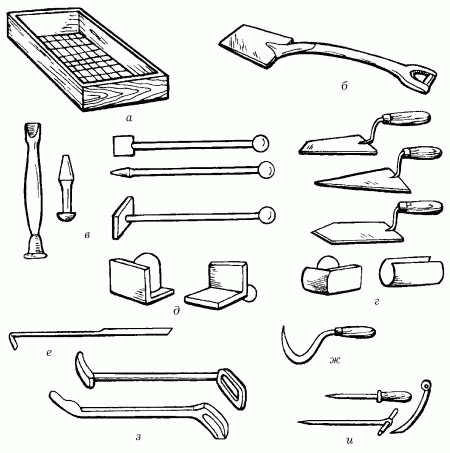
1. Инструменты, предназначенные для заполнения опоки формовочной смесью: прямоугольные или круглые сита с металлической сеткой (рис. 169, а), плоские или совковые лопаты (рис. 169, б).
2. В опоке смесь утрамбовывают с помощью ручных трамбовок (рис. 169, в), которые, в зависимости от назначения, могут быть различными: короткими – для уплотнения смеси в опоках с низкими стенками, длинными – для уплотнения смеси в крупных опоках, с острыми или тупыми концами – для уплотнения смеси, соответственно, в объеме опоки или у ее поверхности.
3. Для контроля поверхностного слоя засыпанной и утрамбованной смеси используют ватерпас, или уровень.
4. Ровную и гладкую поверхность можно создать с помощью гладилки или ланцета (рис. 169, г).
5. Выправлять углы лучше всего угловыми гладилками (рис. 169, д).
6. Упавшие внутрь формы частицы формовочной смеси можно удалить с помощью крючка (рис. 169, е).
7. Для того чтобы избежать разрушения во время извлечения модели из формы, смесь необходимо предварительно увлажнить с помощью кисти.
8. Литниковые каналы лучше всего проделывать специальными ножами (рис. 169, ж).
9. Сгребать формовочную смесь в сито удобнее с помощью скребков и совков.
10. Для выравнивания поверхности литниковых ходов часто используют фигурные ложки (рис. 169, з).
11. Вентиляционные каналы можно проделать с помощью стальных игл разных диаметров (рис. 169, и): 3–5 мм – при изготовлении небольших форм, 7–10 мм – для крупных отливок.
12. Приготовленные модели расталкивают, используя специальные молоточки – киянки.
13. Лишними не окажутся и щетки, которыми можно сметать остатки и ненужные комочки формовочной смеси.
14. Для уплотнения формовочной смеси при изготовлении достаточно больших по размеру и массе форм рекомендуют использовать пневматическую трамбовку.
15. Часто внутри форм, на крестовинах, закрепляют крючки из изогнутой низкоуглеродистой стальной проволоки, которые служат опорой для формовочной смеси. Эти крючки для лучшего сцепления со смесью можно обмазать жидкой формовочной глиной.
16. Для того чтобы лучше зафиксировать формовочную смесь в верхней опоке, в ней устанавливают деревянные колышки.
17. Такие места в форме, как выступающие части, углы, болваны и переходы от тонких сечений к толстым, закрепляют с помощью литейных гвоздей, или шпилек.
18. Проволочные или литые каркасы используют в литье в качестве «скелета» стержней. При этом в небольшие по размерам стержни вставляют каркасы из тонкой проволоки, в более крупных стержнях устанавливают каркасы либо из проволоки диаметром до 9 мм, либо литые из чугуна.
19. Каждому литейщику необходимо всегда иметь под рукой пульверизатор (для нанесения краски на детали) и пневматические сопла (для обдува готовых форм перед сборкой их частей).
Материалы
Формовочные материалы
При наличии всевозможных инструментов и приспособлений, модели и песчаной смеси, которую называют формовочной, можно изготовить литейную форму. В нее заливается металл. Этот процесс и есть получение отливки. Процесс изготовления литейной формы является наиболее продолжительным и трудоемким при производстве литья. Его называют формовкой. Ее подразделяют на формовку по-сырому (когда форму заливают в сыром виде), по-сухому (форму заливают после сушки), по модели, по шаблону, в почве, в опоках, на ручную и машинную в зависимости от сложности и размеров отливок, способа формовки и степени механизации процесса, типа применяемой для изготовления литейной формы формовочной смеси.В зависимости от их применения формовочные материалы подразделяются на исходные материалы и смеси, а исходные, в свою очередь, – на основные и вспомогательные. Они имеют также рабочие свойства: природные и технологические. Природные свойства характерны для исходных формовочных материалов – песков и глин. К ним относятся морфологический, зерновой и химический составы материалов.
Вспомогательные формовочные материалы
Они включают в себя различного рода добавки, припылы, краски, натирки, формовочные клеи, разделительный песок и пр.Добавки
Добавки – это опилки, молотый каменный и древесный уголь, конский волос, чугунная дробь. Их используют при изготовлении крупных форм и стержней, подвергающихся сушке перед заливкой металла. Для уменьшения пригара смеси к стенкам отливки добавляют 3–6 % каменноугольной пыли. В производстве крупных архитектурных отливок, во избежание образования трещин, которые появляются при сушке, в формовочную смесь добавляют конский волос. Для быстрого охлаждения массивных частей отливки применяют чугунную дробь, которую добавляют в формовочную смесь.Припылы
Припылы – это порошки, наносимые на внутреннюю поверхность сырой формы. Это делается для того, чтобы расплавленный металл не смачивал стенки формы, и с целью предупреждения образования пригара на отливке.В зависимости от размера изделия и толщины его стенок в качестве припыла применяют древесноугольный порошок, серебристый или черный графит, цемент и маршаллит.
Формовочные смеси и их свойства
Если предстоит получить отливку со сложным рисунком и тонкими стенками, то нужно обратить внимание на качество формовочной смеси при изготовлении литейной формы. Ее свойствами являются прочность, пластичность, газопроницаемость, огнеупорность, податливость, состав зерен, теплопроводность.Залитый в форму металл при кристаллизации и охлаждении уменьшается в объеме, и готовая отливка будет иметь несколько меньшие размеры, чем полость формы. Такое явление называют усадкой отливки.
Литейная форма не должна сопротивляться усадке металла. Иначе в стенках отливки могут образоваться трещины из-за напряжений, возникающих в металле.
Свойство формовочной смеси, характеризующее сопротивление усадке отливки в форме, называется податливостью.
Материалы для отливок
При художественном литье металлы в чистом виде практически никогда не применяют, так как их свойства не соответствуют требованиям, предъявляемым к отливкам. При соединении двух и более химических элементов в определенных пропорциях получаются сплавы. Они бывают нескольких разновидностей: цветные (медь, олово, алюминий, свинец, цинк, магний и т. д.), черные сплавы (чугун и сталь). Наибольшее распространение получили медные сплавы в производстве монументальных отливок, а серый литейный чугун – при отливке малых форм.Залитый в форму сплав при охлаждении теряет объем. Это называется усадкой, которая бывает объемной и линейной. Если в отливках возникают внутренние напряжения, вызывающие трещины, пористость, усадочные раковины, то причиной этому стала усадка.
Она также негативно влияет на объем и размеры изготовляемых отливок.
При кристаллизации сплава возникает неоднородность химического состава – это ликвация, которая наиболее выражена в массивных сечениях изделия.
Употребляемые литейные сплавы
Здесь речь пойдет о сплавах, применяемых при художественном литье. Как уже говорилось выше, их несколько.Медные сплавы
Если изделие будет работать в условиях повышенного трения, во влажной среде (морская вода), то такие детали необходимо изготавливать из медных сплавов. Они имеют хорошие литейные свойства, и их используют при художественном литье. Существует два вида медных сплавов – бронза и латунь. Расскажем немного о каждом. Олово, свинец, марганец, алюминий, добавленные к меди, – это и есть бронза. В свою очередь, бронза бывает двух видов – оловянная и безоловянная. Оловянные бронзы имеют как достоинства (высокое сопротивление износу и действию воды, хорошая жидкотекучесть), так и недостатки (высокая стоимость, низкая прочность при повышенной температуре, склонность к образованию усадочной пористости). Безоловянные бронзы обладают хорошей коррозионной прочностью и стойкостью, недороги, но в то же время отливки из них получаются с усадочными раковинами, не очень плотными.Латунь –это сплав меди с цинком. Иногда добавляют и другие химические элементы. Эти сплавы чаще всего используют при изготовлении отливок со сложной поверхностью, потому что они имеют более плотную структуру и малую газовую пористость.
Алюминиевые сплавы
Они делятся на группы и марки, обладают хорошими литейными свойствами, великолепно обрабатываются, имеют малую плотность и очень прочны. Наибольшее применение имеет группа сплавов кремния с алюминием. Их называют силуминами.Серый чугун
Если учесть дефицитность и высокую стоимость медных сплавов, то лучшей замены им, чем серый чугун, не найти. Он обладает хорошими технологическими свойствами, высокой коррозионной стойкостью и низкой стоимостью. Поэтому широко применяется при изготовлении малых форм.
Техника формовки
Ручная формовка – процесс достаточно трудоемкий, однако терпение и желание создать необычное изделие из металла могут помочь овладеть им. В технологии ручной формовки особенное внимание следует уделять двум основным процессам: наполнению формы и уплотнению формовочной смеси. Недостаточное наполнение и уплотнение смеси часто приводят к различным дефектам на отливках.
Брак на изделиях может появиться в результате чрезмерного наполнения формы смесью, так как при этом нарушается выход газов и воздуха из полости. Наполнять формы и уплотнять смесь нужно равномерно по всему объему так, чтобы при этом не образовывались впадины и излишне плотные места в формовке.
Брак на изделиях может появиться в результате чрезмерного наполнения формы смесью, так как при этом нарушается выход газов и воздуха из полости. Наполнять формы и уплотнять смесь нужно равномерно по всему объему так, чтобы при этом не образовывались впадины и излишне плотные места в формовке.