Александр Григорьевич Схиртладзе, Борис Васильевич Иванов, Валерий Константинович Корешков, Марк Моисеевич Кане
Системы, методы и инструменты менеджмента качества
Предисловие
Важнейшим условием успешного развития экономики сегодня является производство конкурентоспособной продукции. Основой конкурентоспособности является качество. Опросы потребителей показывают, что среди всех показателей конкурентоспособности (цена, сроки поставки, сервис и др.) качество на 70 % определяет решение о выборе продукции. Справедливость этих положений подтверждает успех развивающихся стран (Южной Кореи, Китая, Турции и др.), продукция которых пользуется популярностью во всем мире из-за высокого уровня ее качества. Процесс глобализации в экономике обостряет конкуренцию, так как расширение рынка позволяет покупателю выбирать товары практически всех мировых производителей. В результате каждый из них соперничает с остальными в определенной области. В таких условиях выживает лишь тот, кто обеспечивает высокое качество при низкой цене.
В последние годы все эти факторы вызвали бурное развитие систем, методов и инструментов менеджмента качества. Их использование позволяет систематизировать работы в области повышения качества, поставить их на научную основу и повысить их эффективность. Они дают возможность объективно оценить пожелания потребителей, преобразовать их в требования к продукции, установить возможности производства, найти слабые места, препятствующие достижению требуемого качества, правильно выбрать корректирующие и предупреждающие действия, оценить удовлетворенность потребителей и других участников данного производства и наметить пути его развития. Только при условии непрерывного улучшения качества продукции предприятие имеет шансы сохранить, а также усилить свои позиции на рынке.
Наряду со знанием систем, методов и инструментов менеджмента качества необходимо учитывать опыт предприятий, достигших успехов в их использовании и добившихся высокого качества продукции. В данной работе такому опыту уделяется большое внимание.
Серьезное значение вопросам качества продукции в машиностроении СНГ начали придавать в конце 1990-х годов. На предприятиях были созданы системы менеджмента качества (СМК), однако, как показывают опросы сотрудников, около 82 % СМК малоэффективны. Причинами этого являются формальный подход к созданию СМК (не ради качества, а ради сертификата, подтверждения ее существования), невнимание руководства предприятия к такой системе и др. Важное место среди этих причин занимает низкая квалификация персонала предприятий в области менеджмента качества, попытки решать новые задачи методом проб и ошибок, силами лишь службы качества. Опыт стран, где эти системы доказали свою эффективность (Япония, Германия, Великобритания, США и др.), показывает, что качества можно достигнуть лишь совместными усилиями всего коллектива при активной позиции руководства и использовании всех современных методов и инструментов менеджмента качества.
Глава 1 подготовлена Б. В. Ивановым и В. Н. Корешковым, главы 2–5 – М. М. Кане. В подготовке главы 2 принял участие А. Г. Схиртладзе. Авторы выражают признательность В. П. Хамицевич, Т. И. Бельской, Н. В. Рудневой, Е. В. Бабовик за компьютерный набор текста и оформление графического материала.
В последние годы все эти факторы вызвали бурное развитие систем, методов и инструментов менеджмента качества. Их использование позволяет систематизировать работы в области повышения качества, поставить их на научную основу и повысить их эффективность. Они дают возможность объективно оценить пожелания потребителей, преобразовать их в требования к продукции, установить возможности производства, найти слабые места, препятствующие достижению требуемого качества, правильно выбрать корректирующие и предупреждающие действия, оценить удовлетворенность потребителей и других участников данного производства и наметить пути его развития. Только при условии непрерывного улучшения качества продукции предприятие имеет шансы сохранить, а также усилить свои позиции на рынке.
Наряду со знанием систем, методов и инструментов менеджмента качества необходимо учитывать опыт предприятий, достигших успехов в их использовании и добившихся высокого качества продукции. В данной работе такому опыту уделяется большое внимание.
Серьезное значение вопросам качества продукции в машиностроении СНГ начали придавать в конце 1990-х годов. На предприятиях были созданы системы менеджмента качества (СМК), однако, как показывают опросы сотрудников, около 82 % СМК малоэффективны. Причинами этого являются формальный подход к созданию СМК (не ради качества, а ради сертификата, подтверждения ее существования), невнимание руководства предприятия к такой системе и др. Важное место среди этих причин занимает низкая квалификация персонала предприятий в области менеджмента качества, попытки решать новые задачи методом проб и ошибок, силами лишь службы качества. Опыт стран, где эти системы доказали свою эффективность (Япония, Германия, Великобритания, США и др.), показывает, что качества можно достигнуть лишь совместными усилиями всего коллектива при активной позиции руководства и использовании всех современных методов и инструментов менеджмента качества.
Глава 1 подготовлена Б. В. Ивановым и В. Н. Корешковым, главы 2–5 – М. М. Кане. В подготовке главы 2 принял участие А. Г. Схиртладзе. Авторы выражают признательность В. П. Хамицевич, Т. И. Бельской, Н. В. Рудневой, Е. В. Бабовик за компьютерный набор текста и оформление графического материала.
Глава 1. Опыт применения и развития систем менеджмента качества
1.1. Развитие систем управления качеством продукции в СССР
Восстановление и развитие промышленности в СССР в 1920-е годы, увеличение масштабов производства поставили задачи совершенствования методов контроля готовой продукции, поэтому с этого времени в СССР начали разрабатываться и внедряться статистические методы контроля, появились специальные контрольные карты и методы выборочного контроля.
В 1930-40-е годы новые требования, предъявляемые к качеству продукции, особенно военного назначения, привели к дальнейшему развитию отдельных элементов управления качеством и внедрению более сложных методов его обеспечения. В послевоенный период технический прогресс обусловил необходимость освоения и выпуска высококачественной продукции в короткие сроки. Это привело к созданию техники управления качеством и разработке новых способов его повышения.
Управление качеством в первую очередь внедрялось в отраслях, обеспечивающих научно-технический прогресс, – радиотехнике, химии, авиации, ракетной технике.
Первые успешные попытки организации планомерной работы в обеспечении качества были предприняты в 1950-е годы. Началом системного подхода к управлению качеством продукции в нашей стране считают разработку и внедрение в 1955 году на Саратовском авиационном заводе системы бездефектного изготовления продукции (БИП) и сдачу ее ОТК и заказчикам с первого предъявления (табл. 1.1).
Таблица 1.1. Развитие систем качества в СССР
Внедрению БИП предшествовала сложившаяся система контроля, при которой рабочие, мастера, руководители предприятия несли ответственности за выполнение производственной программы, а не за качество продукции. Ответственность за качество продукции была возложена на ОТК. В связи с этим аппарат ОТК неоправданно разрастался.
Система БИП представляла собой комплекс взаимосвязанных организационных, экономических и воспитательных мероприятий, которые создавали благоприятные условия для изготовления продукции без дефектов в соответствии с требованиями нормативно-технической документации (НТД). В ее основу были положены следующие принципы:
• полная ответственность непосредственного исполнителя за качество выпускаемой продукции;
• строгое соблюдение технологической дисциплины;
• полный контроль качества изделий на соответствие их действующей документации до предъявления службе ОТК;
• сосредоточение технического контроля не только на регистрации брака, но и главным образом на мероприятиях, исключающих появление различных дефектов.
В соответствии с Положением данной системы порядок предъявления продукции ОТК регламентировался рядом документов, составленных ОТК и утвержденных директором предприятия, которые запрещали исполнителю предъявлять ОТК узлы и изделия с отклонениями от НТД.
Внедрение системы способствовало развитию нового движения – работы с личным клеймом. К такой работе допускались исполнители, которые не менее шести месяцев изготовляли продукцию без дефектов и сдавали ее ОТК с первого предъявления.
Главной особенностью и новизной системы БИП было то, что она позволяла проводить количественную оценку качества труда каждого исполнителя, коллективов подразделений и на основе этого осуществлять моральное и материальное стимулирование.
Оценка качества труда отдельных исполнителей проводилась на основе показателей сдачи продукции ОТК с первого предъявления:
где П – процент сдачи продукции ОТК с первого предъявления, А – сумма всех предъявлений исполнителем продукции в ОТК, Б – сумма всех отклонений продукции ОТК после обнаружения первого дефекта.
Эффективность применения этой системы во многом обуславливалась уровнем подготовки кадров. Для повышения этого уровня организовывались школы качества. В системе большое значение придавалось соответствию состояния оборудования, оснастки, инструмента, измерительных приборов и технической документации требованиям технологического процесса. Обязательная научная организация труда и производства, четкие внутрипроизводственные связи, ритмичность работы по выпуску продукции высокого качества способствовали также материальному и моральному стимулированию исполнителя в зависимости от сдачи продукции с первого предъявления.
Использованный в системе БИП механизм управления качеством оказал влияние на структуру управления. На предприятиях создавались постоянно действующие комиссии по качеству, изменились функции ОТК, стали проводиться дни качества.
Система БИП явилась началом комплексного подхода к организации работы по повышению качества продукции. Принципы этой системы нашли применение на многих предприятиях. В ходе внедрения системы БИП ее основные принципы развивались, взаимоизменялись и обогащались применительно к специфике того или иного производства.
Система БИП явилась мощным средством повышения качества продукции. С 1962 года подобные системы начали внедряться в ГДР и ПНР, а также в США, ФРГ, Японии и других странах.
Внедрение системы БИП позволило:
• обеспечить строгое выполнение технологических операций;
• повысить персональную ответственность рабочих за качественные результаты своего труда;
• более эффективно использовать моральное и материальное поощрение рабочих за качество их труда;
• создать предпосылки для широкого развертывания движения за повышение качества продукции.
Моральное стимулирование привело к появлению званий «Мастер „золотые руки“», «Отличник качества» и др. Со временем изменились функции ОТК – контроль велся выборочно, a основным стал самоконтроль. Именно последний выявил дефекты, появившиеся не по вине рабочего, что привело к проведению с участием руководства дней качества и созданию постоянно действующих комиссий по качеству. На ряде предприятий процент сдачи с первого предъявления партий продукции был заменен процентом числа рабочих дней без брака от общего числа рабочих дней.
Однако саратовская система при всех ее достоинствах имела ряд недостатков. Система не позволяла контролировать и управлять уровнем разработок и проектирования продукта, не охватывала другие стадии его жизненного цикла – реализацию и эксплуатацию, она распространялась только на рабочих цехов основного производства.
Система работала по принципу «есть дефект – нет дефекта», не учитывая многообразие недостатков и различную степень их влияния на качество выпускаемой предприятием продукции.
В принципе, БИП воплотилась в зарубежных программах «ноль дефектов» и сохранилась во всех отечественных. Более того, когда отмечалось десятилетие КСУКП (комплексная система управления качеством продукции), она была зарегистрирована только на 30 тыс. предприятий, а БИП к этому времени – на 60 тыс.
Принцип БИП, распространенный затем на функциональные подразделения завода и цеха, на НИИ и КБ, лег в основу системы бездефектного труда – СБТ.
Львовский вариант саратовской системы – система бездефектного труда (СБТ) – впервые был разработан и внедрен на Львовском заводе телеграфной аппаратуры и некоторых других предприятиях г. Львова в начале 1960-х годов.
Цель системы – обеспечить выпуск продукции отличного качества, высокой надежности и долговечности путем повышения ответственности и стимулирования каждого работника предприятия и производственных коллективов за результаты их труда.
Основным критерием, характеризующим качество труда и определяющим размер материального поощрения, является коэффициент качества труда, который вычисляется для каждого работника предприятия, каждого коллектива за установленный промежуток времени (неделя, месяц, квартал) путем учета количества и значимости допущенных производственных нарушений. В системе устанавливается классификатор основных видов производственных нарушений: каждому дефекту соответствует определенный коэффициент снижения. Максимальная оценка качества труда и максимальный размер премии устанавливаются тем работникам и коллективам, которые за отчетный период не имели ни одного нарушения.
Коэффициент качества труда – как отдельных исполнителей, так и коллектива в целом – рассчитывался по формуле:
где Ки – исходный коэффициент качества (принимаемый за 1, 10, 100);Kci. – коэффициент снижения (с) качества за несоблюдение установленного показателя качества труда для i-го задания; пс – количество коэффициентов снижения качества. При этом
Kci = mi zi,
где mi – количество случаев некачественного выполнения однотипного i-го задания; zi – норматив снижения за некачественное выполнение i-го задания.
Недостатком этого метода считалось то, что в нем учитывались только коэффициенты снижения, суммирующие недостатки по всем показателям, а превышения установленных значений показателей качества труда не отражались на коэффициенте качества.
Передовые же предприятия большое внимание уделяли коэффициенту поощрения, поскольку это способствовало повышению творческой активности трудящихся, поиску новых путей и форм повышения качества продукции и эффективности производства.
Принципы организации и функционирования СБТ на различных предприятиях имели свои особенности. Общими являлись следующие элементы: сдача продукции с первого предъявления, коэффициент качества труда, дни оценки качества, строжайший контроль исполнения.
Внедрение СБТ позволило:
• количественно оценить качество труда каждого работника, каждого коллектива;
• повысить заинтересованность и ответственность каждого работника, каждого коллектива за качество своего труда;
• повысить трудовую и производственную дисциплину всех работников предприятия;
• вовлекать в соревнование за повышение качества продукции всех работников предприятия;
• сократить потери от брака и рекламации, повысить производительность труда.
Львовская СБТ, как и саратовская система БИП, распространялась главным образом на стадию изготовления продукции. Известны попытки применения принципов бездефектного труда в научно-исследовательских и проектно-конструктор-ских организациях, однако широкое применение СБТ получила на промышленных предприятиях для оценки и стимулирования качества исполнительского (не творческого) труда.
БИП и СБТ устраняли отрицательные субъективные причины; устранение объективных причин началось со следующих модификаций систем качества.
Система КАНАРСПИ (качество, надежность, ресурс с первых изделий) была разработана и впервые внедрена на машиностроительных предприятиях г. Горького (Нижнего Новгорода) в 1957–1958 годах. В этой системе был сделан упор на повышение надежности изделий за счет улучшения технической подготовки производства, работы КБ и технологов, на долю которых приходилось 60–85 % дефектов, обнаруживаемых при эксплуатации продукции. Создавались опытные образцы узлов, деталей, систем и изделий в целом, и проводились их исследовательские испытания. Значительное развитие получило опытное производство, стандартизация и унификация, общетехнические системы стандартов, такие как Единая система конструкторской документации (ЕСКД) и Единая система технологической подготовки производства (ЕСТПП).
Характерным для системы КАНАРСПИ является то, что она выходит за рамки стадии изготовления продукции и охватывает многие виды работ на стадиях исследования, проектирования и эксплуатации. На стадии исследования и проектирования при изготовлении опытного образца большое внимание уделяется выявлению причин отказов и их устранению в допроизводственный период.
Решение этой задачи осуществляется за счет развития исследовательской и экспериментальной базы, повышения коэффициента унификации, широкого применения методов макетирования и моделирования, ускоренных испытаний, а также кон-структорско-технологической отработки изделий в процессе технологической подготовки производства. Результаты эксплуатации изделий рассматриваются в системе как обратная связь и используются для совершенствования конструкции изделия и технологии его изготовления.
В КАНАРСПИ широко используются принципы бездефектного труда и бездефектного изготовления продукции.
Внедрение системы КАНАРСПИ на ряде предприятий Горьковской области позволило:
• сократить сроки доведения новых изделий до заданного уровня качества в 2–3 раза;
• повысить надежность выпускаемых изделий в 1,5–2 раза и увеличить ресурс в 2 раза;
• снизить трудоемкость и цикл монтажно-сборочных работ в 1,3–2 раза.
Планирование улучшения качества продукции и управления производством по этому критерию, а также распространение внимания к качеству на весь жизненный цикл продукции получили развитие в системе НОРМ (научная организация труда по увеличению моторесурса).
Система НОРМ была разработана и впервые внедрена на Ярославском моторном заводе в 1963–1964 годах. Цель системы – увеличение надежности и долговечности выпускаемых двигателей.
В основу системы НОРМ положен принцип последовательного и систематического контроля уровня моторесурса и периодического его увеличения путем повышения надежности и долговечности деталей и узлов, лимитирующих моторесурс; основным показателем в системе является ресурс двигателя до первого капитального ремонта, выраженный в моточасах. Рост этого показателя в системе планируется.
Организация работ в системе построена по принципу цикличности. Каждый новый цикл по повышению моторесурса начинается после достижения в производстве ранее запланированного уровня моторесурса и предусматривает определение его фактического уровня, выявление деталей и узлов, лимитирующих моторесурс, планирование оптимального уровня увеличения моторесурса, разработку и проверку инженерных рекомендаций по обеспечению планируемого уровня моторесурса. Он также предполагает разработку комплексного плана конструкторско-технологических мероприятий по освоению двигателя с новым ресурсом в производстве, проведение комплекса конструкторско-технологи-ческих мероприятий и опытно-исследовательских работ, закрепление достигнутого ресурса в производстве и поддержание достигнутого уровня при эксплуатации.
На стадии производства система НОРМ включает в себя положения систем БИП и СБТ, на стадии проектирования – основные положения системы КАНАРСПИ.
Внедрение системы НОРМ позволило увеличить ресурс ярославских двигателей до первого капитального ремонта с 4 тыс. часов до 10 тыс., увеличить гарантийный срок эксплуатации двигателя на 70 % и снизить потребность в запасных частях более чем на 20 %.
Достижение запланированного уровня качества стало возможным за счет комплексного подхода к УКП путем обобщения опыта предшествующих систем по всем стадиям жизненного цикла продукции.
Все разработанные системы, имея свои особенности, базировались в основном на принципах описанных ранее систем управления качеством продукции, разработанных в 1950-60-х годах передовыми предприятиями страны.
Опыт разработки и внедрения этих систем в ряде случаев оставался достоянием только самих разработчиков, очень медленно внедрялся и недостаточно широко распространялся в промышленности. Однако уже в 1970-е годы возникла необходимость более широкого и эффективного внедрения достижений лучших производственных коллективов в практику работы всей отечественной промышленности.
В начале 1970-х годов специалисты Госстандарта в сотрудничестве с организациями различных министерств и ведомств провели анализ, изучение и обобщение передового опыта предприятий в управлении качеством продукции.
Результатом проведенных исследований стало создание единых принципов построения комплексной системы управления качеством продукции предприятия (КСУКП) на базе его стандартов.
КСУКП – это совокупность мероприятий, методов и средств, при помощи которых целенаправленно устанавливается, обеспечивается и поддерживается на основных стадиях жизненного цикла (планирование, разработка, производство, эксплуатация или потребление) уровень качества продукции, соответствующий потребностям народного хозяйства и населения.
Почему система называется комплексной? Качество продукции зависит от многих факторов и условий: степени прогрессивности конструкторских разработок и добротности применяемого сырья, материалов и комплектующих изделий; совершенства планирования и соблюдения технологической дисциплины; оборудования цехов и гибкости механизма стимулирования, рационального подбора и расстановки кадров; организации труда всего коллектива и качества работы отдельных исполнителей. Метрологическое обеспечение производства, аттестация продукции, организация службы контроля также оказывают воздействие на качество продукции.
Комплексность системы проявляется и в том, что она позволяет управлять качеством на основных стадиях жизненного цикла продукции: стадиях исследования, проектирования и изготовления; в период обращения и реализации; стадии эксплуатации или потребления.
При функционировании КСУКП решались следующие задачи:
• создание и освоение новых видов высококачественной продукции, соответствующих лучшим мировым образцам;
• повышение удельного веса продукции высшей категории качества в общем объеме производства;
• улучшение показателей качества выпускаемой продукции и перевод ее в более высокую категорию качества;
• своевременное снятие, замена или модернизация продукции второй категории;
• планомерное повышение качества работы коллективов и исполнителей;
• обеспечение выпуска продукции в строгом соответствии с требованиями НТД, то есть запланированного, заданного уровня качества.
При построении КСУКП очень важно определить ее основные составляющие, которые обеспечивают выполнение функции управления, а также взаимодействие по вопросам качества с вышестоящими организациями управления, поставщиками и потребителями продукции. Следует помнить также, что для эффективного функционирования систем большое значение имеет выбор организационно-технической основы. В качестве таковой для систем управления качеством продукции была определена Государственная система стандартизации (ГСС).
Широкое внедрение комплексных систем на предприятиях дало мощный импульс развитию заводской стандартизации.
Совершенное высокоразвитое промышленное производство резко увеличило число функций технических и экономических служб, расширило внутрипроизводственные связи, увеличило объем информации в системе управления качеством, что привело к увеличению документооборота, необходимости его упорядочения, соответствия документальной основы управления качеством на предприятиях и объединениях общим нормативно-техническим, регламентирующим и правовым документам.
Все эти вопросы решались применением стандартов предприятий (СТП) как внутренней организационно-методической, регламентирующей и правовой основы функционирования системы управления качеством предприятия.
СТП не только регламентировали показатели качества продукции, но и играли огромную роль в организации деятельности работников предприятий, связи различных подразделений и отдельных исполнителей при выполнении работ и т. п.
Комплекс СТП строился по блочному (модульному) принципу в соответствии с системным подходом к построению КСУКП.
Стандарты предприятия, в отличие от других нормативно-технических документов, сочетали в себе обязательность и возможность учета специфических условий предприятия, передового опыта и последних технических достижений в той или иной области.
Стандарты предприятий отличались от инструкций, положений и других регламентирующих документов тем, что разрабатывались в соответствии с действующими государственными и отраслевыми стандартами, подлежали обязательному контролю как нормативные документы ГСС, периодическому пересмотру, были обязательны для всех подразделений, взаимосвязаны и не допускали разных толкований.
Стандарты предприятий выполняли организационно-распорядительную функцию. Они устанавливали порядок, очередность действий органов управления и исполнителей для достижений целей в области повышения качества продукции. Это позволяло предприятию влиять на все факторы и условия, от которых зависело качество выпускаемой продукции, планировать и постоянно обеспечивать реализацию планов повышения технического уровня и качества продукции.
Комплексные системы как разновидность организационно-распорядительных методов имели особое значение для инженерно-технических и административных работников предприятий. Само содержание понятий «инженерный труд» и «управленческая деятельность» получили большую конкретность и очевидность. Появилась большая возможность разработать и внедрить методы оценки качества труда для ИТР и служащих.
В 1975 году на передовых предприятиях Львовской области появились комплексные системы управления качеством продукции (КСУКП).
Целью КСУКП было создание продукции, соответствующей лучшим мировым аналогам и достижениям науки и техники. В 1978 году Госстандартом была разработана и утверждена система основных функций УКП. В связи с внедрением на предприятиях КСУКП получили развитие метрологическое обеспечение производства (МОП), многоступенчатый анализ дефектов и статистический контроль качества. Были созданы группы качества, на предприятиях и в объединениях стали разрабатываться программы качества, вводилась аттестация продукции, получила широкое развитие сеть головных и базовых организаций, а также сеть учреждений по повышению квалификации специалистов в области УКП, в вузах были введены в программы обучения курсы по стандартизации и УКП. В 1985 году отмечалось, что за десятилетие с помощью КСУКП удалось создать и успешно реализовать конкурентоспособную продукцию, повысить удельный вес продукции высшей категории качества в 2–3 раза, значительно сократить потери от брака и рекламаций, уменьшить в 1,5–2 раза сроки разработки и освоения новой продукции. Вместе с тем указывалось, что на многих предприятиях при создании систем управления качеством (СУК) нарушались основные принципы комплексного системного подхода, что привело к формализму в этой работе и, по существу, к отсутствию системы. Основные причины этого – экономическая незаинтересованность предприятий в улучшении КП, а следовательно, и в системе, внедрение СУК на предприятиях излишне административными методами. У многих из-за этого сложилось впечатление, что СУК не оправдали себя. Вместе с тем уже при перестройке экономики и переходе на хозяйственный расчет стало ясно, что КП становится основным условием жизнеспособности предприятий, особенно на внешнем рынке.
В 1930-40-е годы новые требования, предъявляемые к качеству продукции, особенно военного назначения, привели к дальнейшему развитию отдельных элементов управления качеством и внедрению более сложных методов его обеспечения. В послевоенный период технический прогресс обусловил необходимость освоения и выпуска высококачественной продукции в короткие сроки. Это привело к созданию техники управления качеством и разработке новых способов его повышения.
Управление качеством в первую очередь внедрялось в отраслях, обеспечивающих научно-технический прогресс, – радиотехнике, химии, авиации, ракетной технике.
Первые успешные попытки организации планомерной работы в обеспечении качества были предприняты в 1950-е годы. Началом системного подхода к управлению качеством продукции в нашей стране считают разработку и внедрение в 1955 году на Саратовском авиационном заводе системы бездефектного изготовления продукции (БИП) и сдачу ее ОТК и заказчикам с первого предъявления (табл. 1.1).
Таблица 1.1. Развитие систем качества в СССР
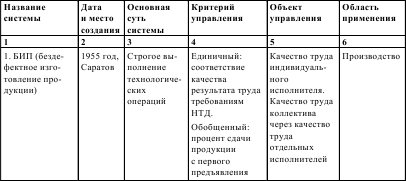
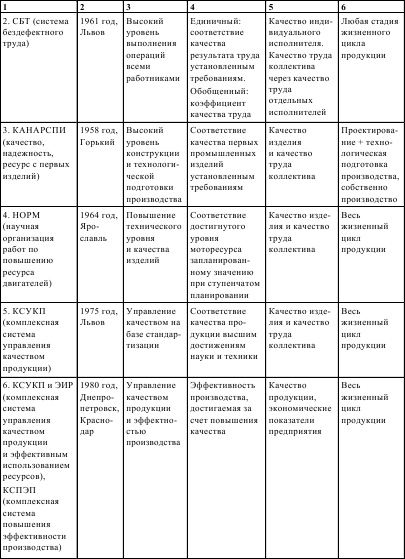
Система БИП представляла собой комплекс взаимосвязанных организационных, экономических и воспитательных мероприятий, которые создавали благоприятные условия для изготовления продукции без дефектов в соответствии с требованиями нормативно-технической документации (НТД). В ее основу были положены следующие принципы:
• полная ответственность непосредственного исполнителя за качество выпускаемой продукции;
• строгое соблюдение технологической дисциплины;
• полный контроль качества изделий на соответствие их действующей документации до предъявления службе ОТК;
• сосредоточение технического контроля не только на регистрации брака, но и главным образом на мероприятиях, исключающих появление различных дефектов.
В соответствии с Положением данной системы порядок предъявления продукции ОТК регламентировался рядом документов, составленных ОТК и утвержденных директором предприятия, которые запрещали исполнителю предъявлять ОТК узлы и изделия с отклонениями от НТД.
Внедрение системы способствовало развитию нового движения – работы с личным клеймом. К такой работе допускались исполнители, которые не менее шести месяцев изготовляли продукцию без дефектов и сдавали ее ОТК с первого предъявления.
Главной особенностью и новизной системы БИП было то, что она позволяла проводить количественную оценку качества труда каждого исполнителя, коллективов подразделений и на основе этого осуществлять моральное и материальное стимулирование.
Оценка качества труда отдельных исполнителей проводилась на основе показателей сдачи продукции ОТК с первого предъявления:

Эффективность применения этой системы во многом обуславливалась уровнем подготовки кадров. Для повышения этого уровня организовывались школы качества. В системе большое значение придавалось соответствию состояния оборудования, оснастки, инструмента, измерительных приборов и технической документации требованиям технологического процесса. Обязательная научная организация труда и производства, четкие внутрипроизводственные связи, ритмичность работы по выпуску продукции высокого качества способствовали также материальному и моральному стимулированию исполнителя в зависимости от сдачи продукции с первого предъявления.
Использованный в системе БИП механизм управления качеством оказал влияние на структуру управления. На предприятиях создавались постоянно действующие комиссии по качеству, изменились функции ОТК, стали проводиться дни качества.
Система БИП явилась началом комплексного подхода к организации работы по повышению качества продукции. Принципы этой системы нашли применение на многих предприятиях. В ходе внедрения системы БИП ее основные принципы развивались, взаимоизменялись и обогащались применительно к специфике того или иного производства.
Система БИП явилась мощным средством повышения качества продукции. С 1962 года подобные системы начали внедряться в ГДР и ПНР, а также в США, ФРГ, Японии и других странах.
Внедрение системы БИП позволило:
• обеспечить строгое выполнение технологических операций;
• повысить персональную ответственность рабочих за качественные результаты своего труда;
• более эффективно использовать моральное и материальное поощрение рабочих за качество их труда;
• создать предпосылки для широкого развертывания движения за повышение качества продукции.
Моральное стимулирование привело к появлению званий «Мастер „золотые руки“», «Отличник качества» и др. Со временем изменились функции ОТК – контроль велся выборочно, a основным стал самоконтроль. Именно последний выявил дефекты, появившиеся не по вине рабочего, что привело к проведению с участием руководства дней качества и созданию постоянно действующих комиссий по качеству. На ряде предприятий процент сдачи с первого предъявления партий продукции был заменен процентом числа рабочих дней без брака от общего числа рабочих дней.
Однако саратовская система при всех ее достоинствах имела ряд недостатков. Система не позволяла контролировать и управлять уровнем разработок и проектирования продукта, не охватывала другие стадии его жизненного цикла – реализацию и эксплуатацию, она распространялась только на рабочих цехов основного производства.
Система работала по принципу «есть дефект – нет дефекта», не учитывая многообразие недостатков и различную степень их влияния на качество выпускаемой предприятием продукции.
В принципе, БИП воплотилась в зарубежных программах «ноль дефектов» и сохранилась во всех отечественных. Более того, когда отмечалось десятилетие КСУКП (комплексная система управления качеством продукции), она была зарегистрирована только на 30 тыс. предприятий, а БИП к этому времени – на 60 тыс.
Принцип БИП, распространенный затем на функциональные подразделения завода и цеха, на НИИ и КБ, лег в основу системы бездефектного труда – СБТ.
Львовский вариант саратовской системы – система бездефектного труда (СБТ) – впервые был разработан и внедрен на Львовском заводе телеграфной аппаратуры и некоторых других предприятиях г. Львова в начале 1960-х годов.
Цель системы – обеспечить выпуск продукции отличного качества, высокой надежности и долговечности путем повышения ответственности и стимулирования каждого работника предприятия и производственных коллективов за результаты их труда.
Основным критерием, характеризующим качество труда и определяющим размер материального поощрения, является коэффициент качества труда, который вычисляется для каждого работника предприятия, каждого коллектива за установленный промежуток времени (неделя, месяц, квартал) путем учета количества и значимости допущенных производственных нарушений. В системе устанавливается классификатор основных видов производственных нарушений: каждому дефекту соответствует определенный коэффициент снижения. Максимальная оценка качества труда и максимальный размер премии устанавливаются тем работникам и коллективам, которые за отчетный период не имели ни одного нарушения.
Коэффициент качества труда – как отдельных исполнителей, так и коллектива в целом – рассчитывался по формуле:

Kci = mi zi,
где mi – количество случаев некачественного выполнения однотипного i-го задания; zi – норматив снижения за некачественное выполнение i-го задания.
Недостатком этого метода считалось то, что в нем учитывались только коэффициенты снижения, суммирующие недостатки по всем показателям, а превышения установленных значений показателей качества труда не отражались на коэффициенте качества.
Передовые же предприятия большое внимание уделяли коэффициенту поощрения, поскольку это способствовало повышению творческой активности трудящихся, поиску новых путей и форм повышения качества продукции и эффективности производства.
Принципы организации и функционирования СБТ на различных предприятиях имели свои особенности. Общими являлись следующие элементы: сдача продукции с первого предъявления, коэффициент качества труда, дни оценки качества, строжайший контроль исполнения.
Внедрение СБТ позволило:
• количественно оценить качество труда каждого работника, каждого коллектива;
• повысить заинтересованность и ответственность каждого работника, каждого коллектива за качество своего труда;
• повысить трудовую и производственную дисциплину всех работников предприятия;
• вовлекать в соревнование за повышение качества продукции всех работников предприятия;
• сократить потери от брака и рекламации, повысить производительность труда.
Львовская СБТ, как и саратовская система БИП, распространялась главным образом на стадию изготовления продукции. Известны попытки применения принципов бездефектного труда в научно-исследовательских и проектно-конструктор-ских организациях, однако широкое применение СБТ получила на промышленных предприятиях для оценки и стимулирования качества исполнительского (не творческого) труда.
БИП и СБТ устраняли отрицательные субъективные причины; устранение объективных причин началось со следующих модификаций систем качества.
Система КАНАРСПИ (качество, надежность, ресурс с первых изделий) была разработана и впервые внедрена на машиностроительных предприятиях г. Горького (Нижнего Новгорода) в 1957–1958 годах. В этой системе был сделан упор на повышение надежности изделий за счет улучшения технической подготовки производства, работы КБ и технологов, на долю которых приходилось 60–85 % дефектов, обнаруживаемых при эксплуатации продукции. Создавались опытные образцы узлов, деталей, систем и изделий в целом, и проводились их исследовательские испытания. Значительное развитие получило опытное производство, стандартизация и унификация, общетехнические системы стандартов, такие как Единая система конструкторской документации (ЕСКД) и Единая система технологической подготовки производства (ЕСТПП).
Характерным для системы КАНАРСПИ является то, что она выходит за рамки стадии изготовления продукции и охватывает многие виды работ на стадиях исследования, проектирования и эксплуатации. На стадии исследования и проектирования при изготовлении опытного образца большое внимание уделяется выявлению причин отказов и их устранению в допроизводственный период.
Решение этой задачи осуществляется за счет развития исследовательской и экспериментальной базы, повышения коэффициента унификации, широкого применения методов макетирования и моделирования, ускоренных испытаний, а также кон-структорско-технологической отработки изделий в процессе технологической подготовки производства. Результаты эксплуатации изделий рассматриваются в системе как обратная связь и используются для совершенствования конструкции изделия и технологии его изготовления.
В КАНАРСПИ широко используются принципы бездефектного труда и бездефектного изготовления продукции.
Внедрение системы КАНАРСПИ на ряде предприятий Горьковской области позволило:
• сократить сроки доведения новых изделий до заданного уровня качества в 2–3 раза;
• повысить надежность выпускаемых изделий в 1,5–2 раза и увеличить ресурс в 2 раза;
• снизить трудоемкость и цикл монтажно-сборочных работ в 1,3–2 раза.
Планирование улучшения качества продукции и управления производством по этому критерию, а также распространение внимания к качеству на весь жизненный цикл продукции получили развитие в системе НОРМ (научная организация труда по увеличению моторесурса).
Система НОРМ была разработана и впервые внедрена на Ярославском моторном заводе в 1963–1964 годах. Цель системы – увеличение надежности и долговечности выпускаемых двигателей.
В основу системы НОРМ положен принцип последовательного и систематического контроля уровня моторесурса и периодического его увеличения путем повышения надежности и долговечности деталей и узлов, лимитирующих моторесурс; основным показателем в системе является ресурс двигателя до первого капитального ремонта, выраженный в моточасах. Рост этого показателя в системе планируется.
Организация работ в системе построена по принципу цикличности. Каждый новый цикл по повышению моторесурса начинается после достижения в производстве ранее запланированного уровня моторесурса и предусматривает определение его фактического уровня, выявление деталей и узлов, лимитирующих моторесурс, планирование оптимального уровня увеличения моторесурса, разработку и проверку инженерных рекомендаций по обеспечению планируемого уровня моторесурса. Он также предполагает разработку комплексного плана конструкторско-технологических мероприятий по освоению двигателя с новым ресурсом в производстве, проведение комплекса конструкторско-технологи-ческих мероприятий и опытно-исследовательских работ, закрепление достигнутого ресурса в производстве и поддержание достигнутого уровня при эксплуатации.
На стадии производства система НОРМ включает в себя положения систем БИП и СБТ, на стадии проектирования – основные положения системы КАНАРСПИ.
Внедрение системы НОРМ позволило увеличить ресурс ярославских двигателей до первого капитального ремонта с 4 тыс. часов до 10 тыс., увеличить гарантийный срок эксплуатации двигателя на 70 % и снизить потребность в запасных частях более чем на 20 %.
Достижение запланированного уровня качества стало возможным за счет комплексного подхода к УКП путем обобщения опыта предшествующих систем по всем стадиям жизненного цикла продукции.
Все разработанные системы, имея свои особенности, базировались в основном на принципах описанных ранее систем управления качеством продукции, разработанных в 1950-60-х годах передовыми предприятиями страны.
Опыт разработки и внедрения этих систем в ряде случаев оставался достоянием только самих разработчиков, очень медленно внедрялся и недостаточно широко распространялся в промышленности. Однако уже в 1970-е годы возникла необходимость более широкого и эффективного внедрения достижений лучших производственных коллективов в практику работы всей отечественной промышленности.
В начале 1970-х годов специалисты Госстандарта в сотрудничестве с организациями различных министерств и ведомств провели анализ, изучение и обобщение передового опыта предприятий в управлении качеством продукции.
Результатом проведенных исследований стало создание единых принципов построения комплексной системы управления качеством продукции предприятия (КСУКП) на базе его стандартов.
КСУКП – это совокупность мероприятий, методов и средств, при помощи которых целенаправленно устанавливается, обеспечивается и поддерживается на основных стадиях жизненного цикла (планирование, разработка, производство, эксплуатация или потребление) уровень качества продукции, соответствующий потребностям народного хозяйства и населения.
Почему система называется комплексной? Качество продукции зависит от многих факторов и условий: степени прогрессивности конструкторских разработок и добротности применяемого сырья, материалов и комплектующих изделий; совершенства планирования и соблюдения технологической дисциплины; оборудования цехов и гибкости механизма стимулирования, рационального подбора и расстановки кадров; организации труда всего коллектива и качества работы отдельных исполнителей. Метрологическое обеспечение производства, аттестация продукции, организация службы контроля также оказывают воздействие на качество продукции.
Комплексность системы проявляется и в том, что она позволяет управлять качеством на основных стадиях жизненного цикла продукции: стадиях исследования, проектирования и изготовления; в период обращения и реализации; стадии эксплуатации или потребления.
При функционировании КСУКП решались следующие задачи:
• создание и освоение новых видов высококачественной продукции, соответствующих лучшим мировым образцам;
• повышение удельного веса продукции высшей категории качества в общем объеме производства;
• улучшение показателей качества выпускаемой продукции и перевод ее в более высокую категорию качества;
• своевременное снятие, замена или модернизация продукции второй категории;
• планомерное повышение качества работы коллективов и исполнителей;
• обеспечение выпуска продукции в строгом соответствии с требованиями НТД, то есть запланированного, заданного уровня качества.
При построении КСУКП очень важно определить ее основные составляющие, которые обеспечивают выполнение функции управления, а также взаимодействие по вопросам качества с вышестоящими организациями управления, поставщиками и потребителями продукции. Следует помнить также, что для эффективного функционирования систем большое значение имеет выбор организационно-технической основы. В качестве таковой для систем управления качеством продукции была определена Государственная система стандартизации (ГСС).
Широкое внедрение комплексных систем на предприятиях дало мощный импульс развитию заводской стандартизации.
Совершенное высокоразвитое промышленное производство резко увеличило число функций технических и экономических служб, расширило внутрипроизводственные связи, увеличило объем информации в системе управления качеством, что привело к увеличению документооборота, необходимости его упорядочения, соответствия документальной основы управления качеством на предприятиях и объединениях общим нормативно-техническим, регламентирующим и правовым документам.
Все эти вопросы решались применением стандартов предприятий (СТП) как внутренней организационно-методической, регламентирующей и правовой основы функционирования системы управления качеством предприятия.
СТП не только регламентировали показатели качества продукции, но и играли огромную роль в организации деятельности работников предприятий, связи различных подразделений и отдельных исполнителей при выполнении работ и т. п.
Комплекс СТП строился по блочному (модульному) принципу в соответствии с системным подходом к построению КСУКП.
Стандарты предприятия, в отличие от других нормативно-технических документов, сочетали в себе обязательность и возможность учета специфических условий предприятия, передового опыта и последних технических достижений в той или иной области.
Стандарты предприятий отличались от инструкций, положений и других регламентирующих документов тем, что разрабатывались в соответствии с действующими государственными и отраслевыми стандартами, подлежали обязательному контролю как нормативные документы ГСС, периодическому пересмотру, были обязательны для всех подразделений, взаимосвязаны и не допускали разных толкований.
Стандарты предприятий выполняли организационно-распорядительную функцию. Они устанавливали порядок, очередность действий органов управления и исполнителей для достижений целей в области повышения качества продукции. Это позволяло предприятию влиять на все факторы и условия, от которых зависело качество выпускаемой продукции, планировать и постоянно обеспечивать реализацию планов повышения технического уровня и качества продукции.
Комплексные системы как разновидность организационно-распорядительных методов имели особое значение для инженерно-технических и административных работников предприятий. Само содержание понятий «инженерный труд» и «управленческая деятельность» получили большую конкретность и очевидность. Появилась большая возможность разработать и внедрить методы оценки качества труда для ИТР и служащих.
В 1975 году на передовых предприятиях Львовской области появились комплексные системы управления качеством продукции (КСУКП).
Целью КСУКП было создание продукции, соответствующей лучшим мировым аналогам и достижениям науки и техники. В 1978 году Госстандартом была разработана и утверждена система основных функций УКП. В связи с внедрением на предприятиях КСУКП получили развитие метрологическое обеспечение производства (МОП), многоступенчатый анализ дефектов и статистический контроль качества. Были созданы группы качества, на предприятиях и в объединениях стали разрабатываться программы качества, вводилась аттестация продукции, получила широкое развитие сеть головных и базовых организаций, а также сеть учреждений по повышению квалификации специалистов в области УКП, в вузах были введены в программы обучения курсы по стандартизации и УКП. В 1985 году отмечалось, что за десятилетие с помощью КСУКП удалось создать и успешно реализовать конкурентоспособную продукцию, повысить удельный вес продукции высшей категории качества в 2–3 раза, значительно сократить потери от брака и рекламаций, уменьшить в 1,5–2 раза сроки разработки и освоения новой продукции. Вместе с тем указывалось, что на многих предприятиях при создании систем управления качеством (СУК) нарушались основные принципы комплексного системного подхода, что привело к формализму в этой работе и, по существу, к отсутствию системы. Основные причины этого – экономическая незаинтересованность предприятий в улучшении КП, а следовательно, и в системе, внедрение СУК на предприятиях излишне административными методами. У многих из-за этого сложилось впечатление, что СУК не оправдали себя. Вместе с тем уже при перестройке экономики и переходе на хозяйственный расчет стало ясно, что КП становится основным условием жизнеспособности предприятий, особенно на внешнем рынке.